Ферритная сталь что это такое: Нержавеющие стали – Ферритные свойства и применение нержавеющей стали 2020
Нержавеющие стали
Нержавеющая сталь, (сложнолегирована сталь) является стойкой против появления ржавчины в атмосферных условиях и коррозии в агрессивных средах. Главный легирующий элемент нержавеющей стали — Cr (содержание 12-20%). Кроме того, нержавеющая сталь содержат элементы, которые сопутствуют железу в его сплавах (С, Si, Mn, S, Р) и элементы, вводимые в сталь для придания ей нужных физико-механических свойств и коррозионной стойкости (Ni, Mn, Ti, Nb, Co, Mo). Чем выше содержание Cr в стали, тем выше ее сопротивление коррозии и жаропрочность; при содержании Cr 12% и более сплавы являются нержавеющими в обычных условиях и в слабоагрессивных средах, 17% и более — коррозионностойкими и в более агрессивных окислительных и других средах, в частности в азотной кислоте крепостью до 50%. Коррозионная стойкость нерж. стали объясняется тем, что на поверхности контакта хромсодержащего сплава со средой образуется тончайшая защитная пленка окислов либо др. нерастворимых соединений. Немаленькое значение при этом имеют однородность металла, которое соответствует состояние поверхности, отсутствие у стали склонности к межкристаллитной коррозии. В сильных кислотах (соляной,
По химическому составу нержавеющие стали подразделяются на хромоникелевые, хромистые и хромомарганцевоникелевые (более 100 марок). По структуре хромистые нерж. стали подразделяются на полуферритные, мартенситные и ферритные . Наилучшую стойкость против коррозии имеют хромистые Н. с. мартенситного типа в полированном состоянии. Хромистые нерж. стали находят применение в качестве конструкционного материала для клапанов гидравлических прессов, которые турбины лопаток, арматуры крекинг-установок, режущего инструмента, пружин, предметов быта.
Нержавеющие стали обычно делятся на 3 немаленькие группы, в зависимости от их структуры:
♦ аустенитные стали обычно содержат 16-25% хрома, 6-14% никеля, кое-когда 2-6% молибдена и маленькое число иных элементов. Стали это группы — максимально широко используемые и представляют 60-70% мирового потребления. Область их применения довольно-таки широка.
♦ мартениститные нержавеющие стали применяются в специальных случаях, когда требуется высокая твердость и прочность. Дальше будут рассматриваться по большей части аустенитные марки. Области применения аустенитных нержавеющих сталей.
Различают аустенитные нерж. стали, которые не склонны к межкристаллитной коррозии, так называемые стабилизированные — с добавками Ti и Nb. Резкое понижение склонности нерж. стали к межкристаллитной коррозии достигается также сокращением содержания углерода (до 0.03%). Стабилизированные аустенитные нерж. стали применяются для изготовления сварной аппаратуры, которая работает в агрессивных средах (при этом после сварки термическая обработка не обязательна). В качестве жаропрочного и жаростойкого материала данные стали используются для изготовления изделий, которые подвергаются воздействию температур 550-800 °С. Стали, которые склоны к межкристаллитной коррозии, после сварки, обычно, подвергаются термической обработке (для деталей, которые сварены роликовой или точечной сваркой, термическая обработка не требуется). Хромомарганцевоникелевые и Хромоникелевые нерж. стали находят широкое применение в промышленности и быту. Для высоконагруженных элементов конструкций, которые работают при повышенных температурах (до 550 °С), применяются так называемые мартенситно-стареющие нерж. стали аустенитно-мартенситного типа, которые обладают значительной прочностью (sb = 1200-1500 Мн/м2, либо 120-150 кгс/мм2), высокой вязкостью и отличной свариваемостью.
В последнее время на рынке дымоотводящих труб и газоходов стали появляться случаи использования нержавеющих сталей не аустенитного, а ферритного класса.
Основные недостатки нержавеющих сталей ферритного класса (AISI 430, 439, 409, аналоги по Российской классификации 08Х17Т, 15Х25Т, 08Х13, 08Х18Т1) по сравнению со сталями аустенитного класса (AISI 304, 321, 316, аналоги по Российской классификации 08Х18Н10, 12Х18Н10Т, 10Х17Н13М2Т, 20Х23Н18) следующие:
♦ Неупрочняемые при термообработке.
♦ Ферритные стали склонны к охрупчиванию при длительном использовании в диапазоне температур от 300 до 600.
♦ Вязкость может быть до некоторой степени ограничена при низких температурах и в заготовках крупного сечения (переход пластичность-хрупкость).
ВНИМАНИЕ:
Срок службы дымоходных труб, изготовленных из ферритных нержавеющих сталей, толщиной 0,5 мм от 1 года составляет менее 2-х лет!
ВНИМАНИЕ:
Сварка швов ферритных нержавеющих сталей должна производиться с особой осторожностью.
ВНИМАНИЕ:
Рекомендуемая максимальная температура применения в течение длительного времени (до 10 000 час) до 800°С установлена только для нержавеющих сталей аустенитного класса. Для ферритных нержавеющих сталей данные условия использования категорически запрещены!
ВНИМАНИЕ:
Отличить ферритную сталь от аустенитной можно с помощью магнита — ферриная сталь обладает магнитными свойствами в отличии от аустенитной.
Ферритные нержавеющие стали – это нержавеющие стали, в которых основным легирующим элементом является хром. Содержание этого элемeнта в сплаве колеблется от 11 до 30%. Хорошей новостью является то, что ферритные стали (серия-400), имея достаточно низкую и стабильную цену и хорошие технические характеристики ждут за кулисами, готовые выйти на сцену и оказаться превосходными как альтернативный материал для многих практических приложений, где на первый взгляд могут справиться «только аустенитные» стали. Ферритные нержавеющие стали представляют собой в основном железо и хромовые сплавы (10,5% мин.), они не содержат дорогой никель. Цена на хром, элемент, который делает нержавеющую сталь особенно устойчивой к коррозии, исторически относительно стабильна. Некоторые ферриты содержат легированные добавки, такие как молибден, что позволяет улучшить характеристики. Ферритные нержавеющие стали разделяет большую часть механических свойств и характеристик коррозионной стойкости с их кузинами – более дорогими, аустенитными сталями и даже превышают их по некоторым параметрам. Зачем платить никель, если вам он не нужен? Те кто ищут альтернативное решение дорогой аустенитной стали могут вздохнуть с облегчением. Ферриты представляют собой технически идеальное и доступное решение чтобы в полной мере использовать уникальные характеристики нержавеющей стали. Используемые ФЕРРИТНЫЕ марки сталей:
Производство продукции из других марок сталей и сплавов осуществляется по запросу. | ![]() ООО «MАРЧЕГАЛИЯ РУ» г. ВЛАДИМИР |
Ферритные стали
Ферритные стали обязаны своим названием ферриту. Так называется фазовая составляющая сплавов железа. При ближайшем рассмотрении это оказывается твердый раствор легирующих элементов и углерода, находящийся в α-железе. Одна из его особенностей – наличие кубической объемоцентрированной решетки. Часто феррит выступает как составляющая и других структур.
Современные ферритные нержавеющие стали выделяются своей устойчивостью к коррозии. Они лучше всего показывают себя при использовании в тех средах, которые не содержат ионов хлора. При использовании в таких средах, они остаются качественными и во многом не уступают хромоникелевым аналогам. Существует ряд сред, в которых такого типа стали превосходят описанные аналоги и показывают лучшую устойчивость, в том числе к коррозийному растрескиванию.
Такая разновидность продукции хорошо поддается дополнительному легированию. Это помогает улучшать характеристики состава и расширять границы его использования.
В таблице ниже представлены химические свойства сталей такого типа в зависимости от использования различных легирующих элементов:
Таблица 1. Хромистые ферритные стали: химический состав.
Марка стали | C | Si | Mn | Cr | Mo | S | P | прочих элементов |
08X13 | ≤0,08 | ≤0,8 | 12,0..14,0 | — | ≤0,025 | ≤0,030 | ≥6(C+N) Ti | |
08Х17Т | 16,0…18,0 | ≤0,035 | 0,50…0,80 Ti | |||||
08Х23С2Ю | 1,5… 1,8 | 0,4…0,7 | 22,0…24,0 | ≤0,015 | ≤0,030 | Не регламентируется | ||
04Х14Т3Р1Ф (ЧС-82) | 0,02…0,06 | ≤0,6 | ≤0,5 | 13,0…16,00 | 0,020 | 0,025 | 2,3 …3,5 Ti, 1,1 … 1,8 V | |
ЭП 882-ВИ | ≤0,015 | ≤0,5 | 16,5…18,5 | 1,5…2,0 | ≤0,020 | ≤0,025 | 0,15…0,35 Nb | |
ЭП 904-ВИ | ≤0,012 | ≤0,3 | 18 | — | 0,1 …0,4 Nb, 2,2 …3,5 А1 | |||
15Х25Т | ≤0,08 | ≤0,8 | ≤0,8 | 29,0…27,0 | ≤0,025 | ≤0,035 | 0,5 …0,9 Ti |
Центральные свойства и особенности использования материала
При использовании такой разновидности продукции потребуется учитывать ряд значимых особенностей, накладывающих ограничения или расширяющих возможности применения. Среди таких особенностей можно выделить:
- Высокая стойкость к коррозии. Как уже было отмечено, особенно такая стойкость проявляется в условиях, когда в среде не присутствуют ионы хлора. Еще один показатель – возможность сохранения стабильных характеристик использования при воздействии азотной кислоты. Такого типа материал хорошо выдерживает язвенную коррозию, а также растрескивание и коррозийное повреждение под высоким напряжением. Специалисты называют оптимальной коррозийную стойкость стали после медленного охлаждения и после отжига при повышенных температурах.
- Сталь выдерживает достаточно высокий нагрев, так как закаляется при повышенных температурах.
- При обработке образует достаточно уязвимые сварные швы. Потому к варке потребуется подходить с осторожностью (об этом будет дополнительно рассказано ниже).
- Материал отличается высокой прочностью и хорошо переносит механическое воздействие.
Центральные области применения
Описанные выше возможности объяснили обширную область применения ферритных сталей. В зависимости от конкретной марки стали, она может использоваться при создании деталей высокотемпературного оборудования, внутренних элементов химических аппаратов. Не менее значимая область использования – создание змеевиков пиролиза, а также различного рода контейнеров и емкостей.
Использование определяется при анализе технических характеристик конкретной марки. Для того чтобы читатель получил лучшее представление о таких механических свойствах, мы собрали их в рамках отдельной таблицы, приведенной ниже:
Таблица 2. Хромистые ферритные стали: механические свойства, не менее.
Марка стали | σв, МПа | σ0,2,МПа | δ5, % | ψ,% | KCU, Дж/см2 | Примеры использования |
08Х13 | 590 | 410 | 20 | 60 | 10 | Внутренние устройства химических аппаратов |
08Х17Т | 372 | — | 17 | — | — | |
08Х23С2Ю | 490 | 10 | 60 | Змеевики пиролиза | ||
04Х14Т3Р1Ф | 500 | 320 | 15 | 20 | 10 | Стеллажи ядерного топлива, контейнеры |
ЭП 882-ВИ | 372 | 245 | 22 | — | 60 | Заменитель Сг — Ni аустенитных сталей |
ЭП 904-ВИ | 440 | 323 | 24 | Детали высокотемпературного оборудования | ||
15Х25Т | — | 14 | 20 | Внутренние устройства химических аппаратов |
Особенности сварки
О том, можно ли сваривать ферритные стали, что получается в итоге и какие характеристики имеют получаемые швы, существует масса противоречивых сведений.
Свариваемость таких типов стали напрямую зависит от их состава. При ограничении в составе C и N удается добиться хороших показателей свариваемости. Также во многом параметры отличаются в зависимости от уровня содержания углерода. К примеру, если углерода и азота ~0,020 %, материал приобретает хорошую пластичность и высокую ударовязкость, а при сваривании не становится хрупким. Показатель хрупкости сварных соединений хромистых ферритных сталей связан содержанием в твердом растворе примесей внедрения.
Также стоить обратить внимание на то, что при правильном выборе материала сварные соединения хромистых ферритных сталей будут устойчивы к коррозии. Это актуально также при использовании в агрессивных средах. Одной из возможностей повышения качества шва, является легирование с использованием титана или ниобия. Это дополнительно повышает стойкость к появлению межкристаллической коррозии. Причем такая стойкость остается неизменной и после термической обработки.
В таблице ниже собраны основные рекомендации по тепловому режиму сваривания такого типа стали. Их соблюдение гарантирует, что материал будет оставаться прочным и получит высокий уровень устойчивости к различного рода внешним типам воздействия.
Таблица 3. Рекомендации по тепловому режиму сварки хромистых ферритных сталей.
Марка стали | Температура подогрева, оС | Продолжительность хранения до термической обработки, ч | Термическая обработка |
08Х13 | 150…250 | Не ограничено | Отпуск при 680…700оС |
08Х13 (плакирующий слой биметалла) | без подогрева | Не регламентируется | |
08Х17Т, 15Х25Т | 150…200 | ||
08Х17Т, 15Х25Т (плакирующий слой биметалла) | без подогрева | ||
08Х23С2Ю | 200 …250 | Не допускается | Отжиг при 900оС |
ЭП 882-ВИ, ЭП 904-ВИ | без подогрева | Не регламентируется |
Помимо этого, при работе с ферритными сталями от специалистов требуется использовать правильное оборудование и нужный способ сварки. Предусмотрена возможность сварки с использованием ручного дугового, электронно-лучевого и лазерного метода. Вопрос выбора зависит от того, какая марка стали используется вами на данный момент.
Подробности выбора определенного типа воздействия в зависимости от марки стали приведены в таблице ниже:
Таблица 4. Способы сварки, сварочные материалы и механические свойства свариых соединеиий хромистых ферритных сталей.
Марка стали | Способ сварки, сварочные материалы | Механические свойства сварных соединений | |
σв, МПа | KCU, Дж/см2 | ||
08Х13 | Ручная дуговая сварка: — электроды Э-10Х25Н13Г2 ОЗЛ-6, ЦЛ-25, Э-10Х25Н13Г2Б ЦЛ-9, Э-08Х20Н15ФБ АНВ-9, Э-10Х20Н15Б АНВ-10 | 540 | 5 |
— электроды Э-2Х13 УОНИ-13НЖ, АНВ-1, ЦЛ-51 | 590 | ||
АДС: проволока Св-07Х25Н12Г2Т, Св-06Х25Н12ТЮ, Св-06Х25Н12БТЮ, флюс АН-26с, АНФ-14, ОФ-6, АН-18 | 540 | ||
АрДС: проволока CB-06X25Н12Т, Cв-06Х25Н12БТЮ, Cв-07X25Н12Г2Т, аргон | |||
08Х17Т | РДС: электроды Э-10Х25Н13Г2Б ЦЛ-9, УОНИ-10Х17Т. АДС: проволока Св-10ХI7Т, флюсы АНФ-6, ОФ-6 | 440 | |
08Х23С2Ю | РДС: электроды ЦТ-33, ЦТ-38 | 500 | |
04Х14Т3Р1Ф | Электронно-лучевая и лазерная сварка | ||
ЭП 882-ВИ | РДС: электроды Э-10Х25Нl3Г2 ЦЛ-25, ЦТ-45, ЭА-400/10Т. АрДС: проволока Св-02ХI8М2Б-ВИ, аргон | 372 | |
ЭП 904-ВИ | РДС: электроды ЦТ-52 | 390 | — |
АрДС: проволока Св-02Х19Ю3Б-ВИ, аргон | 372 | 5 | |
15Х25Т | РДС: электроды 3иО-7, ЭА-48М/22, АНВ-9, АН9-10. АрДС: проволока Св-07Х25Н 13, аргон АДС: проволока Св-07Х25Н13, флюсы АН-26с, АНФ-14, ОФ-6, АН-16 | 440 | 5 |
Правильное использование сварки, а также точный расчет области применения в зависимости от марки способны обеспечить долговременное использование сталей ферритного типа.
Сегодня такая разновидность получила большое распространение в промышленности, часто встречается в различных областях производства материалов. При использовании материала и работе с ним рекомендуем ориентироваться на приведенные в тексте таблицы. Они помогут избежать распространенных ошибок, изменения свойств стали и поддержания высокого качества конечного продукта при его сварке, нагреве или охлаждении.
Классификация нержавеющих сталей — аустенитная, ферритная, дуплексная, мартенситная.
АУСТЕНИТНАЯ НЕРЖАВЕЮЩАЯ СТАЛЬ
Аустенитная нержавеющая сталь содержит значительное количество хрома и достаточное для образования «аустенитной» микроструктуры количество никеля и марганца, которые и придают этим маркам стали хорошую формуемость, пластичность и коррозионную стойкость (а также делают сталь немагнитной). Типичный состав аустенитной стали содержит 18% хрома и 8% никеля, что соответствует популярной «нулевой» («0») марки, согласно определению Американского института чугуна и стали (AISI). Данная марка известна в России как AISI 304, DIN 1.4301 и соответствует российскому аналогу 08Х18Н9. Аустенитные марки стали отличаются высокой прочностью, имеют коррозионную стойкость в широком диапазоне агрессивных сред и отличаются хорошей технологичность и свариваемостью.
ФЕРРИТНАЯ НЕРЖАВЕЮЩАЯ СТАЛЬ
Ферритные марки нержавеющей стали сходны по свойствам с низкоуглеродистой сталью, но обладают более высокой коррозионной стойкостью. Наиболее распространённые марки ферритной стали содержат в среднем 11% и 17% хрома. Первые обычно применяются в производстве выхлопных систем автомобилей, а вторые – в производстве кухонных приборов, стиральных машин, и архитектурного декора интерьеров.
АУСТЕНИТНО-ФЕРРИТНАЯ НЕРЖАВЕЮЩАЯ СТАЛЬ (ДУПЛЕКСНАЯ)
Стали аустенитно-ферритного класса характеризуются высоким содержанием хрома (18-22%) и пониженным (экономным) содержанием никеля (4-6%, в отдельных случаях до 2%). Дополнительные легирующие элементы – молибден, медь, титан, ниобий. Химический состав этих сталей таков, что соотношение аустенита и феррита после оптимальной термической обработки составляет примено 1:1. Данный класс сталей имеет ряд преимуществ по сравнению с аустенитным сталями: более высокая (в 1,5-2 раза) прочность при удовлетворительной пластичности и сопротивляемости действию ударных нагрузок, большая стойкость против межкристаллитной коррозии и коррозионного растрескивания. Они в основном используются в обрабатывающей промышленности, строительстве и в изделиях, контактирующих с морской водой.
МАРТЕНСИТНАЯ НЕРЖАВЕЮЩАЯ СТАЛЬ
Мартенситные, как и ферритные марки, содержат в среднем от 12% до 17% хрома, однако имеют более высокое содержание углерода. Эти стали применяют преимущественно в термически обработанном состоянии, часто с тщательно шлифованной, а иногда и полированной поверхностью. Они используются при производстве лопастей турбин, столовых приборов и бритвенных лезвий.
Таблица взаимного соответствия нержавеющих аустенитных сталей, специфицированных по стандартам JIS, W.-nr., DIN, BS, EN, AFNOR, UNI, UNE, SS, AISI/SAE (ANSI/ASTM), GB.
Таблица взаимного соответствия нержавеющих ферритных и мартенситных сталей, специфицированных по стандартам JIS, W.-nr., DIN, BS, EN, AFNOR, UNI, UNE, SS, AISI/SAE (ANSI/ASTM), GB.
Таблица взаимного соответствия легированных сталей, специфицированных по стандартам JIS, W.-nr., DIN, BS, EN, AFNOR, UNI, UNE, SS, AISI/SAE (ANSI/ASTM), GB.
Таблица взаимного соответствия жаропрочных сталей, специфицированных по стандартам JIS, W.-nr., DIN, BS, EN, AFNOR, UNI, UNE, SS, AISI/SAE (ANSI/ASTM), GB.
Нержавеющие стали: феррит, мартенсит, аустенит
Нержавеющие стали ценят за их высокое сопротивление коррозии. Все по-настоящему нержавеющие стали содержат не менее 11 % хрома. Такое содержание хрома обеспечивает образование тонкого защитного поверхностного слоя из карбида хрома при взаимодействии стали с кислородом.
Влияние хрома на коррозионную стойкость стали
Именно хром делает сталь нержавеющей. Кроме того, хром является элементом, повышающим устойчивость феррита. Рисунок 1 иллюстрирует влияние хрома на диаграмму состояния железо-углерод. Хром заставляет аустенитную область сжаться тогда, как ферритная область увеличивается в размерах. При высоком содержании хрома и низком содержании углерода феррит является единственной фазой вплоть до температуры ликвидуса.
Рисунок 1 – Влияние 17 % хрома на диаграмму состояния железо-углерод. При низком содержании углерода феррит является устойчивым при всех температурах. Буква «М» обозначает «металл», например, хром или железо, а также другие легирующие элементы.
Различают несколько видов нержавеющих сталей, основанных на различиях кристаллической структуры и упрочняющих механизмов.
Ферритные нержавеющие стали
Ферритные нержавеющие стали содержат до 30 % хрома и не более 0,12 % углерода. Благодаря своей объемноцентрированной кристаллической структуре (ОЦК) ферритные стали имеют хорошую прочность и приличную пластичность , которые достигаются за счет упрочнения твердого раствора и деформационного упрочнения. Ферритные стали являются ферромагнитными или, говоря по-простому, «магнитят». Они не поддаются термической обработке. Ферритные стали имеют отличную коррозионную стойкость, обладают умеренной способностью поддаваться обработке давлением и являются относительно дешевыми.
К ферритным нержавеющим сталям относятся стали 08Х13, 12Х17, 08Х17Т, 15Х25Т, 15Х28 по ГОСТ 5632-72.
Из рисунка 1 видно, что сталь с 17 % хрома и 0,5 % углерода при нагреве до 1200 ºС образует 100 %-ный аустенит, который превращается в мартенсит при закалке стали в масле. Мартенсит затем отпускают для получения высокой прочности и твердости стали (рисунок 2).
Рисунок 2 – Мартенситная нержавеющая сталь. Содержит крупные первичные карбиды и мелкие карбиды, которые образовались при отпуске.
Содержание хрома в мартенситных сталях обычно не более 17 %, так как в противном случае аустенитная область на диаграмме состояния становится слишком маленькой. Это приводит к тому, что в нее становится технологически трудно попасть: требуется жесткий контроль содержания углерода и температуры аустенитизации. Более низкое содержание хрома позволяет расширить содержание углерода от 0,1 до 1,0 %, что дает возможность получать мартенсит различной твердости. Комбинация высокой твердости, прочности и коррозионной стойкости делает эти стали подходящим для изготовления таких изделий как высококачественные ножи и шариковые подшипники.
К мартенситным нержавеющим сталям относятся стали 20Х13, 30Х13, 40Х13, 14Х17Н2 по ГОСТ 5632-72.
Никель является элементом, который повышает устойчивость аустенита. Присутствие никеля в стали увеличивает размер аустенитной области, тогда как феррит почти полностью изчезает из железо-хромово-углеродистых сплавов (рисунок 3).
Рисунок 3 – Сечение диаграммы состояния железо-хром-никель-углерод при 18 % хрома и 8 % никеля. При низком содержании углерода аустенит является устойчивым при комнатной температуре.
Если содержание углерода становиться ниже 0,03 %, то карбиды в стали вообще не образуются и сталь является полностью аустенитной при комнатной температуре (рисунок 4).
Рисунок 4 – Аустенитная нержавеющая сталь
Аустенитные нержавеющие стали обладают высокой пластичностью, способностью обработке давлением и коррозионной стойкостью.
Термическая обработка нержавеющих сталей аустенитного класса заключается в закалке в воде с температуры 1050-1100 °С. Такой нагрев вызывает растворение карбидов хрома, а быстрое охлаждение фиксирует состояние пресыщенного твердого раствора. Очень важно отметить, что в результате закалки твердость этих сталей не повышается, а снижается. Поэтому для аустенитных нержавеющих сталей закалка является смягчающей термической операцией.
Свою прочность аустенитная нержавеющая сталь получает за счет холодного наклепа — нагартовки. Аустенитные стали могут получать деформационное упрочнение до значительно более высоких величин, чем ферритные нержавеющие стали. При деформациях порядка 80-90 % предел текучести достигает 980-1170 МПа, а предел прочности — 1170-1370 МПа. Ясно, что такого наклепа можно достичь только при изготовлении таких видов изделий, как тонкий лист, лента, проволока.
Аустенитные нержавеющие стали являются немагнитными, что дает им преимущество во многих применениях.
Представителями аустенитных нержавеющих сталей являются стали 12Х18Н9 и 17Х18Н9, 12Х18Н10Т и 12Х18Н9Т, 08Х18Н10Т, 08Х18Н12Б, 03Х18Н11 по ГОСТ 5632-72.
Дисперсионно твердеющие нержавеющие стали
Эти стали называют также высокопрочными нержавеющими сталями. Дисперсионно твердеющие нержавеющие стали содержат алюминий, ниобий или тантал и получают свои свойства за счет закалки, деформационного упрочнения, упрочнения старением и мартенситного превращения. Сталь сначала нагревают и закаливают с превращением аустенита в мартенсит. Повторный нагрев вызывает выделение из мартенсита упрочняющих частиц, таких как NiAl3. Высокая прочность этих сталей достигается даже при низком содержании углерода.
К дисперсионно твердеющим сталям относятся стали 07Х16Н6, 09Х15Н8Ю, 08Х17Н5М3, 04Х25Н5М2, ХН40МДТЮ по ГОСТ 5632-72.
Двухфазные нержавеющие стали
В некоторых случаях в структуре нержавеющих сталей намеренно получают смесь различных фаз. При соответствующем контроле химического состава и режимов термической обработки получают сталь с содержанием, например, 50 % феррита и 50 % аустенита. Такая комбинация фаз в структуре стали обеспечивает ей такое уникальное сочетание механических свойств, коррозионной стойкости, способности к обработке давлением и свариваемости, которое невозможно достичь в никаких других нержавеющих сталях. Иногда их называют по-зарубежному — дуплексные стали.
К двухфазным нержавеющим сталям относятся стали 08Х22Н6Т, 03Х23Н6, 08Х21Н6М2Т, 03Х22Н6М2, 08Х18Г8Н2Т, 03Х24Н6М3 по ГОСТ 5632-72.
Источник: D. Askeland, P. Fulay, W. Wright – The Science and Engineering of Materials, 2011
Аустенитная нержавеющая сталь — Википедия
Материал из Википедии — свободной энциклопедии
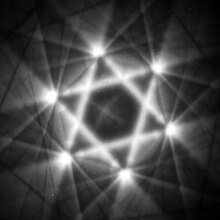
Аустенитная нержавеющая сталь — особый тип нержавеющей стали . Нержавеющие стали могут быть классифицированы по их кристаллической структуре на четыре основных типа: аустенитная, ферритная , мартенситная и дуплексная[1]. Аустенитные нержавеющие стали имеют аустенит в качестве своей первичной кристаллической структуры (гранецентрированная кубическая). Эта кристаллическая структура аустенита достигается достаточным добавлением аустенитных стабилизирующих элементов никеля, марганца и азота. Из-за специфической кристаллической структуры аустенитные стали не увеличивают твёрдость при тепловой обработке и не обладают магнитными свойствами.[2]
Есть две подгруппы аустенитной нержавеющей стали. Нержавеющие стали серии 300 достигают своей аустенитной структуры в основном за счет добавления никеля, в то время как нержавеющие стали серии 200 заменяют никель марганцем и азотом, хотя небольшое содержание никеля все еще остается.
Нержавеющая сталь серии 300 — большая подгруппа. Наиболее распространенной аустенитной нержавеющей сталью и самой распространенной из всех нержавеющих сталей является тип 304, также известный как 18/8 или A2. Тип 304 широко используется в таких предметах, как кухонная посуда, столовые приборы и кухонное оборудование. Тип 316 является следующей наиболее распространенной аустенитной нержавеющей сталью. Некоторые серии 300, такие как тип 316, также содержат некоторое количество молибдена для повышения устойчивости к кислотам и повышения устойчивости к локальным воздействиям (например, точечной и щелевой коррозии). Более высокое добавление азота в серии 200 дает им более высокую механическую прочность, чем в серии 300. [3]
Другими известными аустенитными нержавеющими сталями являются типы 309 и 310, [4] которые используются в средах с температурой выше 800 °C.
Сплав 20 (Карпентер 20) представляет собой аустенитную нержавеющую сталь, обладающую превосходной стойкостью к горячей серной кислоте и многим другим агрессивным средам, которые могут легко воздействовать на нержавеющую сталь типа 316. Этот сплав обладает превосходной стойкостью к коррозионному растрескиванию при кипении в 20–40% серной кислоты. Сплав 20 обладает превосходными механическими свойствами, а присутствие ниобия в сплаве сводит к минимуму выпадение карбидов во время сварки.
Аустенитная нержавеющая сталь может быть испытана путем неразрушающего контроля с использованием метода проникающего красителя, но не методом магнитного контроля частиц. Вихретоковые испытания также могут быть использованы.
Публикация «Коррозионностойкие аустенитно-ферритные стали» — ЗАО «Балтийская нержавеющая сталь» Санкт-Петербург
Коррозионно-стойкие аустенитно-ферритные стали, в дальнейшем условно называемые дуплексными коррозионностойкими (ДКС), состоят из двух основных фаз — аустенита и феррита примерно в равных количествах (но не менее 30% каждой).
Обе эти фазы вследствие высокого содержания в них хрома являются коррозионностойкими. Преимущества ДКС перед аустенитными коррозионностойкими сталями (АКС) — более высокие прочность (без снижения вязкости) и коррозионная стойкость, а также пониженная стоимость стали из-за сравнительно низкого содержания никеля. ДКС могут применяться в средах, где стандартные АКС имеют недостаточную стойкость, например, в хлоридсодержащих растворах. Вследствие низкого содержания углерода и наличия никеля ДКС обладают хорошей свариваемостью. Однако из-за возможности выделения при нагреве нежелательных избыточных фаз и снижения порога хладноломкости в зоне термического влияния сварных соединений они имеют ограниченный температурный интервал эксплуатации от -40 до 300°С. Легирование современных ДКС азотом стабилизирует аустенит, и в этом отношении азот заменяет никель. Кроме того, азот повышает прочность и сопротивление питтингу и улучшает структуру сварного шва.
ДКС имеют высокую прочность, поэтому из них можно изготавливать изделия с гораздо меньшей массой, чем, например, из АКС. В результате снижается их металлоемкость и экономятся дорогие и дефицитные материалы.
Вследствие уникального сочетания высокой прочности, вязкости, коррозионной стойкости, свариваемости и экономичности ДКС можно успешно использовать в различных отраслях промышленности, особенно для изделий, эксплуатирующихся в Сl-содержащих средах (химическая, нефтехимическая, нефтегазовая разведка и добыча, в том числе с морского дна и из глубинных кислых Н2-содержащих скважин), целлюлозно- бумажная, пищевая, фармацевтическая, текстильная промышленность, атомная энергетика и др.). Установлена также их биологическая совместимость, и они могут имплантироваться в человеческий организм.
Английский филиал шведской фирмы Sandvik Steel на выставке «Побережье Европы-91» в г. Абердине (Шотландия) объявил о полном освоении любых профилей из супер SAF 2507 для надводного и подводного использования в сильно коррозионных средах.
Отечественная ДКС 03Х23Н6 производится в виде толстого (4-20 мм) и тонкого (0,8-3,6 мм) листа и сорта до диаметра 200 мм, сталь 03Х22Н6М2 — в виде толстого и тонкого листа, а супер ДКС 03X24H6M3 — в виде толстого листа (4-11 мм) и сорта. Области их применения: сталь 03Х23Н6 (ЭИ68) — сварное емкостное оборудование, работающее в производстве минеральных удобрений, серной кислоты и др.; сталь 03Х22Н6М2 (ЭИ67) предназначена для изготовления оборудования, работающего в средах производства сложных минеральных удобрений; сталь Avesta 2205 используется в качестве материала для наливных судов, предназначенных для транспортировки фосфорной и серной кислот с температурой 30-50°С.
Ниже рассматриваются ДКС третьего поколения, которые содержат около 25% Сr, до 4 % Мо и до 0,3 N и имеют очень высокую коррозионную стойкость, выражаемую так называемым эквивалентом сопротивления питтингу:
ЭСП = (%Сг+3,3%Мо+16%N)>40%, что соответствует критической температуре питтингообразования >60°С. Некоторые марки современных наиболее распространенных деформируемых ДСК приведены в табл.1.
Таблица 1
Группа ДКС | ЭСП, % | Обозначение стали, данное разработчиком | Условная марка стали | Разработчик |
с 18-23% Cr | 23-25 |
ЭИ-68 ЭИ-67 SAF2304 Uranus 35N 3RE60 Uranus45N SAF2205 FALC223 AF22 VS22 |
03X23H6 03X22H6M2 03X23Ah5 03X23Ah5 03X18H5M3C2 03X21H5AM3 03X22H5AM3 03X22H5AM3 03X22H5AM3 03X22H5AM3 |
ЦНИИЧЕРМЕТ ИМ.И.П. Бородина ЦНИИЧЕРМЕТ ИМ.И.П. Бородина2 Sandvik, Avesta Creusot-Loire Sandvik, Avesta Creusot-Loire Sandvik, Avesta Krupp Stahl Mannesmann Valinox |
Фазовый состав ДКС зависит от химического состава и термической обработки и ориентировочно определяется соотношением Сг- и Ni -эквивалентов (в %) по известной диаграмме Шеффлера. Для литого состояния Сгэкв = %Cr + 2%Si +1,5%Мо + 5%V + 5,5%Аl + 1,5%Тi + 1,75%Nb + 0,75%N; Niэкв = %Ni + %Со + 30%С + 25%N + 0,5%Мn + 0,3%Сu. Все ДКС затвердевают через феррит. В интервале температур 1200-1000°С, характерном для пластической деформации, термодинамически стабильны феррит (Ф) и аустенит (А). При 900°С стабильна σ-фаза, при 800°С стабильны нитриды хрома типа Cr2N(e) и χ-фаза, а ниже 800°С — еще и R-фаза.
При использовании азота как легирующего элемента в ДКС в интервале 700-900°С возможно выделение нитрида Cr2N, которое протекает преимущественно внутри зерен при быстром охлаждении от высоких температур и оказывает отрицательное влияние на свойства этих сталей. Следует отметить, что количество вводимого азота должно обеспечивать его сохранение в твердом растворе, так как только в этом случае обеспечивается высокая коррозионная стойкость стали.
После термической обработки на твердый раствор (закалка от 1000-1100°С в воде или на воздухе, в зависимости от сечения изделий) ДКС должны иметь оптимальное количество Ф и А в структуре. В этом случае они в наибольшей степени приближаются к АКС по пластичности и вязкости (табл. 2) и к ферритным коррозионностойким сталям по сопротивлению коррозии.
Предел текучести ДКС в 2-3 раза выше, чем АКС типа Х18Н9, так как феррит в соответствии с законом аддитивности упрочняет аустенитную матрицу. ДКС обычно имеют более мелкое зерно, чем АКС, что вносит дополнительный вклад в упрочнение. В ДКС, легированных азотом, он концентрируется в аустените до такой степени, что аустенитная фаза может быть прочнее феррита. Современные супер ДКС дополнительно упрочнены за счет повышенного содержания Сг и Мо в твердом растворе.
Супер ДКС в состоянии поставки (обработка на твердый раствор с ускоренным охлаждением) имеют весьма высокую прочность при относительном удлинении до 20-30%, ударной вязкости до 200-300 Дж/см2 и вязкости разрушения К1с до 3140 Н/мм3/2. Ударная вязкость ДКС после обработки на твердый раствор весьма высока, что обусловлено наличием аустенита, тормозящего рост трещин в зернах феррита. Температура перехода ДКС в хрупкое состояние Ткр<-60°С. Вязкость разрушения в растворах хлоридов К15СС у ДКС в несколько раз выше, чем у АКС и аустенитно-мартенситных коррозионностойких сталей.
ДКС имеют два температурных интервала охрупчивания: 600-900°С (σ-фаза и др.) и 500°С (475-градусная хрупкость). Для избежания распада пересыщенного твердого раствора охлаждение после нагрева при термической обработке должно быть достаточно быстрым.
ДКС имеет высокое сопротивление коррозионной усталости: предел выносливости при испытании в синтетической морской воде почти в 2 раза выше, чему АКС. Сопротивление усталости ДКС в коррозионных средах (водопроводная и синтетическая морская вода, 0,1 Н раствор HCl) не ниже, чем при испытании на воздухе.
Физические свойства ДКС после обработки на твердый раствор, а также для сравнения — свойства АКС и ферритных коррозионностойких сталей (ФКС) приведены в табл. 3. ДКС по физическим свойствам, как и по механическим, занимают промежуточное положение между аустенитными и ферритными сталями.
Горячая обработка давлением проводится в интервале температур 1280- 850°С. После окончательной деформации обязательно проводится отжиг ДКС, заключающийся в обработке на твердый раствор при 1000-1100°С с последующим ускоренным охлаждением. Выделения σ-фазы снижают горячую пластичность ДКС при 900-1200°С, однако эта фаза достаточно быстро диссоциирует при температурах >1000°С. В промышленной практике прокатки целесообразен перегрев слитков из ДКС до 1250-1280°С. Образующееся при этом большое количество феррита вновь уменьшается в результате обратного δ-γ-превращения, протекающего при деформации в интервале более низких температур. Феррит снижает горячую прочность ДКС, что способствует уменьшению усиления их деформирования.
Если горячая пластическая деформация является конечной операцией при изготовлении металлоконструкции или изделия, после нее проводят закалку от 1000-1100°С с охлаждением в воде или на воздухе.
Для повышения механических свойств и коррозионной стойкости разработаны специальные режимы термомеханической обработки ДКС, включающие нагрев до ферритного состояния (1250°С), быстрое охлаждение и прокатку ниже температуры рекристаллизации (500-800°С) с обжатием ≈30%, рекристаллизацию в двухфазной области (900-1150°С 0,5-20 ч) с последующим быстрым охлаждением (возможно дополнительное старение или холодная деформация).
В холодном состоянии ДКС могут деформироваться всеми известными способами: гибкой, штамповкой, глубокой вытяжкой, выдавливанием, раскаткой, волочением и т.п.
Применение ДКС марки 05Х20Н5АМЗ в холоднодеформированном состоянии позволяет получить σв>1760 Н/мм2, относительную магнитную проницаемость ≈ 8-9 и удовлетворительную стойкость против охрупчивания в среде хлоридов, насыщенной h3S.
Режимы термической обработки оказывают большое влияние на структуру и свойства изделий из ДКС. Снижение скорости охлаждения при пониженном содержании аустенитообразующих элементов приводит к уменьшению пластичности, а при повышенном — и к уменьшению прочности металла. Температура нагрева под закалку в зависимости от состава ДКС выбирается в пределах 1000-1100°С (иногда до 1150°С). Высокие температуры нагрева способствуют более полному растворению избыточных фаз и повышению коррозионной стойкости стали. Время нагрева под закалку устанавливается из расчета 1-3 мин. на 1 мм толщины изделия. При закалке в воде изделий с большой или переменной толщиной от температур ≈1100°С возможно образование закалочных трещин вследствие выделения по границам зерен частиц меди или s-фазы. Во избежание этого рекомендуется промежуточное охлаждение (подстуживание) в печи до 1040-950°С с последующей закалкой в воде, масле или на воздухе. Варьированием температуры нагрева и скорости охлаждения при закалке можно изменять в широких пределах количество феррита (от 50 до 100%) и соответственно физические и механические свойства стали.
ДКС привлекают к себе внимание не столько высокими механическими свойствами, сколько коррозионной стойкостью. Наиболее опасной является локальная (питтинговая) коррозия, так как при ее развитии создаются места зарождения усталостных трещин или коррозионного растрескивания под напряжением (КРН).
Высокие служебные свойства ДКС обеспечиваются их высокой стойкостью против общей и локальной коррозии, поэтому во многих агрессивных средах они могут заменять не только высоко-никелевые АКС, но и некоторые цветные сплавы. ДКС имеют высокую коррозионную стойкость в растворах солей, кислот и щелочей, органических соединениях, а также хорошо противостоят эрозионной коррозии, в том числе под воздействием высокоскоростных потоков жидкостей.
Двухфазная структура лучше противостоит коррозионному воздействию даже при наличие пор и раковин, образующихся в литых изделиях. Предполагает, что аустенит и феррит гальванически взаимно защищают друг друга. Введение азота в ДКС уменьшает различие концентрации хрома в Ф и А и этим повышает коррозионную стойкость аустенитной фазы, приближая ее к стойкости Ф.
При эксплуатации ДКС в морской воде вредное влияние оказывают бактерии, отложения которых могут вызвать щелевую коррозию. Для уменьшения активности бактерий рекомендуется непрерывное или периодическое хлорирование морской воды.
Питтинговая коррозия наиболее часто зарождается на межфазных границах Ф/А вследствие возможной сегрегации легирующих элементов, но поскольку современные ДКС являются чистыми сплавами (0,002% S), влияние сегрегации в них считается несущественным, и гораздо большую опасность представляют выделения нежелательных фаз, таких как s- фаза и вторичный аустенит.
Для эксплуатации в проточной морской воде могут применяться и АКС. Однако в неподвижной морской воде при наличии конструктивных зазоров (щелей) АКС подвергаются воздействию питтинговой и щелевой коррозии. В этих условиях отлично ведут себя ДКС. В установках, охлаждаемых морской водой, ДКС имеют более высокую коррозионную стойкость, чем АКС, алюминиевая бронза и Cu-Ni-сплавы. Идеальную стойкость показала супер ДКС Zeron 100 (Х25Н7АМ4ДВ), незначительную коррозию претерпели супер ДКС SAF2507 (Х25Н7АМ4), сплав Nicrofer 6020 hMO (X22H64M9B3Fe2) и АКС 254 SMO (Х20Н18АМ6Д), остальные стали и сплавы L (AISI316L, AISI904L, Sanicro 28, AISI 317LN, SAF 2205, Nicrofer 4221) признаны непригодными для работы в морской воде тропических широт.
Анализ результатов многочисленных исследований показывает, что обычные АКС по своей природе более склонны к КРН, чем ДКС, при сопоставимом содержании Сг и Мо.
Сенсибилизация, приводящая к межкристаллитной коррозии, в ДКС выражена меньше, чем в АКС, так как при выделении зернограничных карбидов хром поставляется в эти участки ферритом, в котором диффузия протекает намного быстрее, чем в аустените.
В слабо окислительных кислотах (серная кислота, загрязненная и незагрязненная фосфорная кислота, органические кислоты) стойкость супер ДКС превосходит стойкость АКС. И наоборот, в сильно окислительных кислотах (кипящая азотная кислота) высокое содержание феррита в ДКС является вредным.
ДКС легко свариваются всеми известными способами ручной и автоматической электросварки: дуговой, плазменной, электронно-лучевой и др.). В отличие от однофазных АКС они обладают меньшей склонностью к образованию горячих зернограничных трещин даже при большой толщине сварного шва, более высокой прочностью и коррозионной стойкостью шва.
Для обеспечения высокой коррозионной стойкости и достаточной пластичности содержание феррита в сварном шве должно составлять 30-70%. Это указывает на необходимость использования присадочного металла, состав которого сходен с основным металлом, но содержит не более 30% Ф. При сварке разнородных материалов (сварка с простыми углеродистыми или легированными сталями или с другими коррозионностойкими сталями) рекомендуется использовать проволоку типа PHYWELD625 или 82. В других случаях ДКС можно сваривать при тех же условиях, что и стандартные АКС: без предварительного подогрева, с охлаждением шва между проходами до температуры <120°С, с зачисткой до и после сварки, без термической обработки и регенерации (восстановления) структуры после сварки ДКС в отожженном (закаленном) состоянии. Однако при использовании сплавов в упрочненном состоянии после сварки нужно проводить отжиг (закалку) и упрочняющую обработку.
Травление ДКС для удаления окалины после термической обработки проводят в водном растворе 10-20% HNО3 (плотностью 36°В) с 1,5-5% 65%-ной HF. Время погружения составляет несколько часов при комнатной температуре. Оно может быть сокращено до 20 мин. при нагреве ванны до 60°С.
ДКС обрабатываются резанием труднее, чем стандартные АКС, вследствие более высокой прочности и низкого содержания углерода и неметаллических включений (в супер ДКС).
Обзор подготовили: Литвак В. А. Белокопытов Н. П.
Информационно-справочное издание «Балтийские металлы» июнь 1998, № 2.