Изготовление стеклопластика своими руками: Как в домашних условиях сделать стеклопластик своими руками и детали из него
Как в домашних условиях сделать стеклопластик своими руками и детали из него
Согласитесь, не каждый поклонник тюнинга имеет возможность приобрести оригинальные предметы интерьера в соответствующих магазинах. Но, честно говоря, это вовсе не обязательно — превратить обычный автомобиль в предмет искусства можно и самостоятельно, если научиться правильно делать стеклопластик своими руками.
Собственно, стеклопластик представляет собой полиэфирную смолу, которая изготавливается примерно следующим образом: материалу придают необходимую форму, армируют стекловолокном и затем полимеризуют.
Само собой разумеется, что тягаться с фирменными предметами гаражного тюнинга мы не намерены. Но если необходимые детали имеют незначительные размеры, то сделать их может практически каждый. Но начинать подобную практику лучше всего с примитивных деталей, имеющих самые простые очертания.
Их установка не должна требовать от вас какой-либо сверхъестественной аккуратности.
Учимся быть аккуратными.
1. На начальном этапе изготовления нам необходимо сделать болванку. Стоит отметить, что форма болванки должна в точности имитировать будущую деталь. По этой причине самой главной заботой будет именно правильность всех изгибов, симметрия, и максимально чистая поверхность.
Еще один не менее важный момент — это материал, из которого будет сделан наш пуансон. К примеру, если деталь будет иметь большие габариты (такие, как бампер), то болванку для нее лучше изготавливать из пенопласта.
Основание, полученное таким образом, после завершения процесса можно даже не удалять. Для меньших деталей следует использовать глиняные или пластилиновые детали (но, честно говоря, нюансы обработки подобных материалов могут вас несколько смутить).
Нередко в качестве пуансона используют древесину. Хотя ее предварительная обработка, связанная с придачей формы, и кажется на первый взгляд сложной, но последующая обработка наждачкой станет для вас сущим пустяком.
Помимо этого, на данном этапе мы должны определиться, каким именно образом готовое изделие будет сниматься с болванки. Если есть возможность, то мы ее попросту снимаем. Но в отдельных случаях вам придется распиливать болванку на две части, дабы извлечь изделие.
Как бы то ни было, но перед извлечением изделия вам в любом случае понадобится специальное смазывающее вещество, которым нужно будет обработать стенки матрицы. Хотя, если планируется использование пенопласта, то подобные манипуляции не потребуются.
Этап второй.
Смола, используемая при изготовлении стеклопластика, превращается в пластик только после того, как в нее добавят отвердитель. Также существует специальная инструкция, в соответствии с которой смешиваются необходимые компоненты.
При наличии минимального опыта вы сможете самостоятельно контролировать процедуру отвердения. Так, если вам нужно ускорить процесс, то массу следует немного нагреть. Примерно такой же эффект достигается, если увеличить количество отвердителя. Но и в первом, и во втором случае полученная масса будет не слишком уж крепкой.
Еще один важный момент — это прокаливание ткани, можно даже на открытом огне. Когда перестанет идти дым, мы прекращаем процедуру: все защитные вещества, в том числе и парафин, уже испарились, а пустоты между тканями заполнились нашей смолой.
Когда начнем пропитывать стеклоткань, то лучше положить ее на стекло, так смола распределится максимально равномерно. Также для этого можно использовать железную линейку, сильно придавив ее к поверхности.
Ткань помещается на болванку как целиком, так и несколькими отдельными лоскутами (в данном случае все будет зависеть от особенностей конкретной модели и от ваших умений). Разумеется, что разделение ткани на лоскуты (если такое потребуется) произойдет еще до начала пропитки.
Роль стеклоткани
Когда готовая стеклоткань будет помещаться на болванку, то нужно позаботиться о максимальном ее прилегании, исключив разнообразные складки.
Примерно так же удаляются воздушные пузыри. Также стоит отметить, что зачастую одного слоя ткани не хватает, минимальное количество — три-четыре. Каждый слой мы укладываем по очереди, но без длительных задержек. В противном случае предыдущий слой может высохнуть.
Убираем болванку
Когда затвердеет смола (это примерно 3-4 суток), мы удаляем болванку. К слову, это крайне ответственный процесс и повреждение «скорлупы» в нем — нередкое явление. Если это произошло, не отчаивайтесь, ведь поврежденную поверхность можно подклеить посредством той же смолы.
В итоге хотелось бы добавить, что практически каждое изготовление детали тюнинга осуществляется по данной схеме. Но если будет несколько экземпляров, то процедура значительно усложнятся. «Скорлупу» при этом необходимо укрепить дополнительными слоями. Подобные матрицы можно неоднократно использовать, но все детали, вышедшие из нее, потребуют хорошей чистки.
А если необходимо сделать более прочный стеклопластик, то изделие на этапе затвердения помещают в вакуум (то есть, в полиэтиленовый мешочек с откачанным воздухом). Тогда все слои ткани уплотнятся и, соответственно, существенно уплотнится вся поверхность готового материала.
Видео урок — матрица из стеклопластика своими руками
[Всего: Средний: /5]Изделия из стеклопластика. Изготовление деталей из стеклопластика. Москва.
Не всегда нам, тюнингистам приходится придумывать новые детали и изготавливать их из стеклопластика. Часто меня просят повторить и размножить заводские изделия из стеклопластика. А вот в этот раз вообще копировал полипропиленовый воздуховод из стеклопластика .
Поменять серийный руль на руль с тюнингом (анатомия + кожа)
Технология изготовления деталей из стеклопластика позволяет нам тиражировать изделия в небольших количествах.
Фото 01. Передо мной непростая, сборная из двух частей деталь. Без применения сложных технологических приемов, стеклопластиком невозможно повторить сразу обе стороны корки изделия. Значит, буду копировать лицевые поверхности, а крепеж, который на заводской детали находится на внутренней стороне, сделаю другими средствами. Можно, конечно было бы и защелки повторить из стеклопластика, но тогда изделие будет более сложным в изготовлении.
Фото 02. Думаю, что вас уже не удивляет мое стремление максимально, где можно использовать пластилин. Покажу теперь, как делать из пластилина разъемы для матрицы. Разъем должен находиться на детали в самом широком ее сечении. А сечение это проходит не только по плоскости моего изделия, а хитро изгибается. Разъем должен точно повторять сечение со всеми его изгибами, иначе изделие из стеклопластика не захочет по-хорошему выходить из матрицы. Пластилин лучше немного согреть, потом раскатать «колбасками» и расплющить. Одним торцом полоски пластилина прилепить к линиям сечения детали. Неровности пластилина можно грубо разровнять скребком или линейкой.
Фото 03. Черновая матрица из стеклопластика (а я буду клеить быструю, грубую, одноразовую матрицу) не требует первого слоя гелькоута, но для примера я одну полуматрицу намажу гелькоутом, а вторую нет. Такое изделие из стеклопластика как черновая матрица, не требует тщательной формовки, но в качестве тренировки я всегда стараюсь аккуратно затягивать модель стекловолокном. Обычно, для такой задачи можно использовать обрывки стекломата любого размера, которых много остается в процессе работы со стеклопластиком.
Фото 04. Половинка матрицы затвердела, и я продолжил мастерить свое грубое изделие из стеклопластика. Пластилин легко отделяется от стеклопластика матрицы. Нависшие за края пластилина стекловолокна опиливаю и слегка зашкуриваю наждачной бумагой.
Фото 05. Вторую половинку матрицы склею без гелькоута, чтобы можно было сравнить поверхности обеих половинок матрицы. И решить потом: а нужно ли тратить время на гелькоут, стоит ли затрат материалов и времени это якобы преимущество в качестве гелькоутированной поверхности. Хотя для себя я этот вопрос давно решил в пользу упрощения и экономии — все равно, единичные изделия из стеклопластика приходится шпаклевать, грунтовать и красить.
Фото 06. Почему-то всегда боюсь забыть просверлить крепежные отверстия во фланцах полуформ матрицы. Этот этап можно легко пропустить, в эйфории разнимая готовые половинки. А между тем, изготовление деталей из стеклопластика часто требует сборных конструкций матриц. Поэтому вначале просверливаю отверстия под саморезы (для черновой матрицы этого достаточно), а уже потом заглядываю внутрь, что получилось.
Фото 07. Вот вам и разница поверхности матрицы без гелькоута и с ним. На поверхности, где геля не было, можно заметить микро пузырьки и раковинки размером с игольное отверстие. А так, в целом, загущенная аэросилом полиэфирка (вместо гелькоута) дает довольно плотный верхний рабочий слой матрицы. По крайней мере, изготовить единственное изделие из стеклопластика по такой поверхности можно без лишней последующей доработки детали.
Саму деталь буду клеить со слоем гелькоута. В этот раз, это полиэфирная смола с алюминиевой пудрой.
Фото 08. Поскольку внутренняя поверхность воздуховода имеет значение, выкладываю корки цельными кусками стекломата и проформовываю насухо полиэфиркой. Качественные изделия из стеклопластика должны и с изнаночной стороны выглядеть аккуратно. На этом примере хочу обратить внимание на то, что края стекломата не завалены на фланцы матрицы, а стоят вертикально. Это чтобы не образовывались пузыри на кромке изделия из стеклопластика.
Фото 09. С моим разделителем затвердевшие корочки легко выходят из матрицы. Опиливаю и подравниваю края деталей. Из стеклопластика изделия более жесткие чем из полипропилена. Но это для нас и к лучшему, так как не приходится делать стоечки от провисания поверхностей между деталями как на заводской.
Фото 10. Пустотелые, замкнутые детали из стеклопластика делают из нескольких частей склеенных между собой той же смолой. В моем случае частей две и к внутренней полости имеется доступ (хоть и узкий, но пролезть маленькой рукой можно). Это я к тому, что после склейки половинок, шов изнутри можно будет размазать и выровнять.
Склеиваются изделия из стеклопластика специальным составом на основе полиэфирки, который называется «престакол», а в просторечии «склейка». Я намешал свою склейку из полиэфирки, аэросила и стекловолокон, на моем лексиконе – «волосатая каша». Накладываю этой каши по краям деталей, вложенных в полуформы матрицы. Каши не жалею – наваливаю и на фланцы тоже.
Фото 11. Сильно затягивать с намазыванием каши не стоит, все равно, на фланцах она выдавится, а внутри нашего изделия из стеклопластика размажется после сборки матрицы. Аккуратно, чтобы не сместилась корочка стеклопластика, переворачиваю одну половинку матрицы и совмещаю по фланцам с другой. Изготовление деталей из стеклопластика с замкнутым объемом, достигается склеиванием двух или более деталей. После свинчивания половинок матрицы мои две детали склеятся в единую форму. Как я предполагал, моя рука в перчатке пролезла в отверстия матрицы и разгладила изнутри стыки по контуру изделия из стеклопластика.
Фото 12. Новорожденное изделие из стеклопластика кажется грубым и неаккуратным. Облой стеклопластика по фланцам и с торцов детали выглядит безобразно. Но я не могу скрыть радости от того, что деталь готова. Стоит только опилить и ошкурить, а если еще и покрасить, так ее будет не узнать (в хорошем смысле).
Фото 13. После опиливания и ошкуривания, как я обещал, это совсем другое дело! Изготовление деталей из стеклопластика это поэтапное, постепенное движение от замысла к готовому изделию из стеклопластика. От принятия решения по способу изготовления и применению материалов, до финишной доводке формы снаружи, а если нужно, то изнутри.
Фото 14. А так выглядит законченная конструкция в собранном состоянии. Маленький козырек, который пристыковывается к воздуховоду, изготавливается отдельной деталью из стеклопластика по совсем простой матрице. Для крепления козырька, который в заводском исполнении фиксируется на защелках, я использовал винтовой крепеж. Гайку приформовал к стеклопластику корки самого воздуховода (пример смотреть http://bosscar.ru/archives/653 фото 13-16).
В таком примерно виде изделия из стеклопластика попадают в малярку. До малярных работ желательно приставить изготовленную из стеклопластика деталь на место установки и прокачать, как говориться.
Статьи о тюнинге своими руками.
Автор: Михаил Романов
Сайт: http://bosscar.ru
При копировании статьи поставьте, пожалуйста, «кликабельную» ссылку на мой блог.
Как сделать капот из стеклопластика?
Самый дешёвый, относительно быстрый и доступный способ как сделать капот – использование стекловолокна и специальной смолы. Стекловолокно много лет успешно используется в автомобильной индустрии, как в производстве, так и при тюнинге.
Углеволокно (карбон) также популярно из-за своего особого внешнего вида, прочности и лёгкого веса. По соотношению прочности к весу оно превосходит как стеклопластик, так и металл. Однако, карбон не так доступен, как стекловолокно и работа с ним сложнее, поэтому применяется реже.
В этой статье подробно рассмотрим, как сделать капот из стеклопластика (стекловолокна и ламинирующей смолы).
Причиной изготовления собственного капота из стекловолокна может быть копирование дорогостоящего капота, создание капота с индивидуальным дизайном, облегчение веса автомобиля. Возможно, автолюбитель хочет полностью изучить процесс, чтобы в дальнейшем заниматься изготовлением панелей из стеклопластика. Изучив информацию из этой статьи, можно сделать капот из стеклопластика высокого качества.
Преимущества капота из стеклопластика
- Для изготовления капота из стеклопластика не требуется обладать специальными навыками. Главное соблюдать последовательность этапов изготовления и сушить слои нужное количество времени.
- Можно сделать капот, имеющий индивидуальный дизайн, которого нет ни у кого.
- Капот из стеклопластика имеет лёгкий вес (обычно в 3 раза легче, чем стальной капот), при этом не страдает его структурная устойчивость. Это облегчает общий вес автомобиля.
- Стекловолокно, смола и другие сопутствующие материалы (рассмотрим ниже) имеют приемлемую стоимость. Таким образом, капот, сделанный своими руками не будет стоить дорого.
- Панели из стекловолокна имеют хорошую устойчивость к перепадам температуры.
- Капот из стекловолокна и смолы не мнётся и не ржавеет.
Мастерская
Очень важны условия мастерской при создании матрицы и панелей из стеклопластика. Температура должна быть между 18–22 градусами по Цельсию. Нужно избегать прямого попадания солнечных лучей. Любой обогрев мастерской должен быть направлен в сторону от рабочей зоны. Влажность должна быть нормальной и постоянной. Всё это важно, так как сушка панелей из стеклопластика должна быть постепенной и равномерной. Лучше, чтобы изделие сохло медленно, естественным путём. Это предотвратит искажения формы стеклопластикового капота.
В мастерской нужно обеспечить вентиляцию, так как смола даёт токсичные испарения.
Способы изготовления капота из стекловолокна
Давайте рассмотрим, как можно изготовить капот из стекловолокна. Есть всего два способа:
- Изготовление капота из стекловолокна и смолы без применения матрицы
- Изготовление капота из стекловолокна и смолы при помощи матрицы
Изготовление капота из стекловолокна и смолы без применения матрицы
Стекловолокно со смолой наносятся на внешнюю (лицевую) поверхность оригинального капота. Усилители с обратной стороны могут быть также сделаны из стекловолокна со смолой по шаблону оригинального капота, а потом приклеены к первой части. Другой вариант усиления на внутренней стороне – создание их формы из любого материала (монтажной пены, пенопласта, картона) по месту, а потом нанесение стекломата со смолой поверх них с нахлёстом, на обратной стороне капота. Таким образом, получается однородная обратная сторона с усилителями из стекловолокна.
Недостатки:
- Недостатком является грубая лицевая часть, которая требует дополнительного выравнивания (шпаклёвкой и шлифованием), что потребует дополнительного времени, утяжелит капот и сделает его толще.
- Если панель копируется напрямую с оригинала, без матрицы, то её форма может немного искажаться при отвердевании.
Это также потребует дополнительного выравнивания. Поэтому, важно, чтобы отвердевание происходило постепенно, без скачков температуры.
- Форма (в данном случае капот), изготовленная без матрицы получается немного большего размера, чем оригинал, так как делается поверх него. Это может потребовать дополнительной подгонки капота по месту.
Форму (капот) без применения матрицы можно изготавливать, когда не нужно делать множество копий оригинала или не требуется высокого качества лицевой стороны. Как было написано выше, высокого качества лицевой части можно достичь дополнительным выравниванием после полного отвердевания капота из стекловолокна. Если захотите использовать этот способ, то принцип можете использовать такой же, что и при создании капота по матрице. Он будет подробно описан ниже. Исключением является то, что слои стекловолокна со смолой кладутся на оригинальный капот (донор), а не внутрь матрицы и не наносится слой gel coat (гелькоута), так как смысл в нём теряется.
Изготовление капота из стекловолокна и смолы при помощи матрицы
Если требуется сделать несколько копий оригинала (или созданного полномасштабного макета), а также требуется высокое качество лицевой стороны капота, то перед изготовлением капота из стекловолокна необходимо сначала сделать матрицу.
Капот, изготовленный по матрице, будет наиболее точной копией капота, по которому эта матрица была сделана. Способ изготовления капота из стекловолокна при помощи матрицы можно считать единственным правильным способом получения высококачественного изделия. Если матрица была сделана правильно, то Вы получите капот, который не потребует дополнительного выравнивания, будет точно такого же размера, что и оригинал (в отличие от капота, изготовленного без матрицы).
Недостатки:
- Изготовление капота при помощи матрицы требует дополнительных затрат на большее количество материалов (чем изготовление капота без матрицы), а также это займёт больше времени.
Опять же, отличное качество полученной копии при помощи матрицы, не потребует дополнительных трудозатрат и материалов на выравнивание капота (как в случае с капотом, сделанном без применения матрицы).
- Если требуется изготовить всего одну копию капота, то матрицу придётся выбросить, отдать или продать кому-нибудь, либо хранить до момента, когда она может снова пригодиться.
Как сделать капот? Подробный разбор процесса изготовления
Изготовление капота представляет собой многоэтапный процесс. Давайте разберём каждый этап подробно. Будем рассматривать процесс создания капота из стеклопластика при помощи матрицы. Как было сказано ранее, это самый правильный вариант, в результате которого можно получить идентичную копию металлического капота, которую не нужно будет дополнительно выравнивать, а можно сразу подготавливать к покраске и красить.
Понадобится:
- Стекловолокно.
Стекломат (CSM – chopped strand mat), плотностью 225 и 450 gsm.
- Специальные валики, чтобы выгонять пузырьки воздуха и разравнивать стекловолокно, пропитанное смолой. Более дешёвый вариант — малярный валик с секцией трубы PVC поверх ролика.
- 4 литра gel coat. Gel coat (в России часто пишут русскими буквами без перевода «гелькоут») – это специальная полиэфирная смола, которая идёт как начальный слой при создании матрицы или копии. В его составе есть добавка для повышенной эластичности, чтобы улучшить устойчивость к ударам, повышенной износостойкости. Также эта смола имеет свойство не стекать с вертикальных поверхностей.
- 4 литра ламинирующей смолы
- Разделительное вещество. Воск (Parting Wax) и PVA (water/alcohol-based polyvinyl alcohol)
- Кисти с натуральной щетиной, шириной 10–12 см. Лучше использовать кисточки с короткой щетиной или отрезать щетину до 3 см в длину.
- Контейнеры для смешивания смолы с отвердителем.
- Рабочая одежда. Лучше надеть рабочих халат.
- Ацетон (для чистки). Он хорошо отмывает прилипшую смолу.
- Латексные перчатки
- Шлифовальная бумага (P120-P240), шпаклёвка.
Создание матрицы
- Матрицу нужно сделать по оригинальной детали в качестве шаблона. Матрица для капота является точной копией нужной формы в перевёрнутом наизнанку виде. Стекловолокно ламинируется внутри матрицы. На оригинальный капот, перед созданием матрицы, могут быть добавлены дополнительные элементы, либо может быть кардинально изменена форма (для этого можно использовать глину для лепки, полиуретановую пену с шпаклёвкой, картон и т. д.). Таким образом, можно получить капот с индивидуальным дизайном.
- Матрица должна быть толще (обычно в 3–5 раз) и прочнее, чем вылитая по ней будущая форма. Это предотвратит искажение матрицы и повреждение формы.
- При создании матрицы нужно учесть, как Вы будете извлекать залитую в неё форму. Фактор, который нужно учитывать – угол конусности отливки. Это угол краёв панели, по которой изготавливается матрица. Залитую форму легче вытащить из матрицы с позитивным углом. То есть, нужно, чтобы края донора (или матрицы) были немного скошены, чтобы отлитая форма могла легко отделиться.
- Оригинальный капот, перед созданием матрицы должен быть идеально ровным. Все неровности и несовершенства оригинального капота отпечатаются на создаваемой матрице. Поэтому, если в этом есть необходимость, нужно сделать косметический ремонт капота перед переходом к созданию матрицы.
- Капот нужно тщательно вымыть и высушить.
- Мы будем рассматривать способ создания матрицы, который предполагает заливку матрицы на лицевой стороне капота и её отвердевание, потом переворачивание капота и изготовление матрицы другой стороны капота (усилителя), отвердевание и разделение этих половинок.
Этот способ предполагает предварительное изготовление барьера из плотного материала, который приклеивается на край обратной стороны, перед созданием матрицы на лицевой части капота. Этот барьер послужит основанием для создания угла конусности из глины для лепки или специального воска (скошенный угол по периметру края капота, для облегчения отделения отвердевшей матрицы). Также барьер не даст смоле затекать на обратную сторону капота и послужит основанием для запаса стекловолокна со смолой по краю то есть ламинироваться стекловолокно будет как на капоте, так и на приклеенном барьере (получится кромка). Эта кромка придаст дополнительную жёсткость матрице, а также обеспечит более безопасное отдёление двух половин матрицы после их готовности. Расщеплять края можно будет любым плоским инструментом, не боясь повредить оригинальный капот (его край будет вдали от края залитых половин матриц).
- Барьер можно сделать из поликарбоната или плотного пластикового листа. Сначала нужно использовать малярную ленту, чтобы сделать шаблон вокруг краёв капота. Потом можно будет перенести форму шаблона на плотный пластик и вырезать из него барьер. Малярная лента наклеивается по периметру капота шириной 10 см. Нужно отметить места среза, чтобы получить отдельные сегменты, которые будет удобно наклеить. Сегменты барьеров нужно пометить, чтобы их было легко приклеить в нужное место. Перед приклеиванием барьера к капоту нужно приклеить маскировочную ленту, чтобы барьер было легко отклеить. Малярная лента наклеивается на край обратной стороны капота. На эту ленту наносится горячий клей. Потом приклеивается барьер. Между стыками сегментов барьера наклеивается скотч, чтобы герметизировать стыки.
- Далее нужно использовать глину для лепки или специальный воск, чтобы сделать угол конусности вокруг края капота между капотом и барьером.
Этот угол не даст смоле затечь под капот, иначе это помешает разъединению отлитой формы. Таким образом, когда матрица будет готова, она легко отделится, и не будет зацепляться за край капота.
- Далее, на поверхность капота (и на приклеенный барьер) наносится разделяющее вещество (mould release / separating agent). Оно необходимо, чтобы смола не приклеивалась на поверхность оригинального капота. Во-первых, это поможет не испортить оригинальный капот, во-вторых, разделяющее вещество необходимо, чтобы залитая форма без особых проблем отделилась от поверхности. В качестве разделяющего средства чаще всего используют комбинацию воска и PVA (Parting Wax и PVA Release Film).
Нужно сначала нанести воск в матрицу. Для нанесения воска нужно использовать чистую материю или специальный аппликатор. Дайте воску подсохнуть в течение часа. Далее распыляется (или наносится кистью) слой PVA.
- После высыхания разделительного вещества наносится gel coat. Для этого можно использовать как специальный краскопульт, так и кисть. Можно нанести 2 тонких слоя или один толстый (0.8 мм). Для капота среднего размера понадобиться примерно 700 грамм gel coat. Дайте этому слою подсохнуть и отвердеть, но чтобы он всё ещё прилипал при касании.
- Далее наносится соединительный слой (coapling coat). Соединительный слой делается также, как обычное ламинирование стекловолокна. Для этого слоя может использоваться специальная смола (в линейке производителя), которая служит соединительным (переходным слоем) между gel coat и основной смолой. На поверхность наносится смола, потом кладётся стекломат и пропитывается смолой.
Нужно использовать стекломат плотностью 225 gsm или менее плотный. Сделайте вырезы на стекломате, если это необходимо, чтобы он повторял форму капота. Из-за того, что стекломат менее плотный, это позволяет ему хорошо повторить все контуры капота и хорошо прилегать. Это гарантирует, что не останется никаких пустот между слоем gel coat и первым слоем стекловолокна, пропитанного смолой. После пропитывания стекломата, его нужно прокатать валиком, чтобы окончательно убрать пузырьки воздуха. Этот слой должен просохнуть в течение 3 часов. Он должен стать твёрдым, но оставаться липким.
- Теперь нужно использовать стекломат плотностью 450 gsm. Сначала наносится смола, потом кладётся стекломат и снова пропитывается смолой. Далее кладётся второй слой стекломата и снова пропитывается смолой. Всё прокатывается валиком, чтобы разровнять слои и выгнать пузырьки воздуха.
- Большинство матриц, использующих стекломат (chopped strand mat) состоят из 8–10 слоёв. Более толстая стеклоткань (Woven Roving, Tooling Fabric) может быть добавлена после третьего слоя стекломата для более быстрого увеличения толщины и прочности матрицы. Изменяйте положение волокон слоёв, чтобы прочность была равномерной. Не наносите более 3–4 слоёв за один раз, так как из-за формирования тепла может искажать матрицу.
- На больших матрицах (как в нашем случае) добавляется усиление с обратной стороны, для дополнительной жёсткости. Для этого можно сделать распорки (из пвх труб) и нанести 2 слоя стекломата со смолой поверх них. Эти усиления должны проходить как по центру, так и по краям матрицы, где постоянное количество напряжения будет возрастать от воздействия залитой формы.
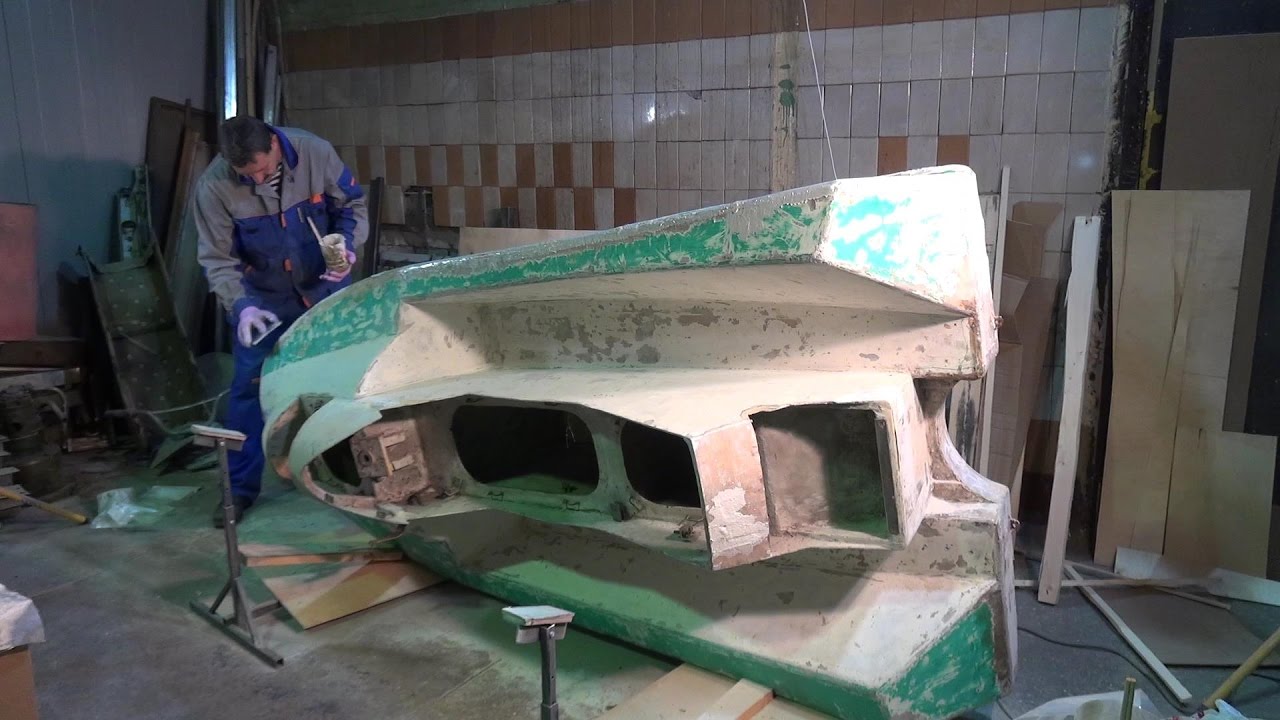
- После отвердевания матрицы, сделанной на лицевой части, нужно перевернуть капот, не отделяя затвердевшую стеклопластиковую часть. Далее можно начать делать форму для внутренней части капота (усиления). На этом этапе можно удалить барьеры из пластикового листа, приклеенные к краю капота. После удаления пластикового барьера останется кромка из стеклопластика.
Обратная сторона капота
- Чтобы подготовить обратную сторону к нанесению смолы и стекловолокна, нужно заклеить все швы и отверстия. Когда будет наноситься смола, она не должна просочиться в какие-либо щели и отверстия, так как это помешает отделению формы. Мелкие швы можно заделать глиной для лепки, а большие отверстия – скотчем или специальной липкой лентой (flash/release tape).
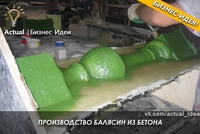
- Также нужно добавить глины к краям усилителей, чтобы смола не попала под них.
- Как и при изготовлении лицевой стороны капота, по краям капота (между барьером, который теперь сделан из стеклопластика и краем) нужно создать угол конусности. То есть, сделать скошенный край из глины для лепки.
- Теперь нужно нанести и распределить воск и распылить или намазать кистью PVA mold release (разделяющее вещество) на внутреннюю часть капота.
- Теперь вся поверхность обильно промазывается gel coat при помощи кисти (или наносится распылением). Слой должен получиться достаточно толстым (0.8 мм). Этот слой должен оставаться немного липким перед нанесением стекловолокна со смолой.
- Далее намазывается смола и кладётся стекломат 225 gsm. На не до конца просохший слой смолы и стекломата наносится второй стекломата плотностью 450 gsm и пропитывается смолой.
Всего должно получиться минимум 4 слоя 450 gsm. Всё тщательно прокатывается валиком. Нанесённые слои должны просохнуть в течение суток.
Отделение матрицы от капота
После полного отвердевания матрицы, её нужно высвобождать. Для этого существуют специальные клинья разных размеров и разной твёрдости. Эти пластиковые клинья удобно использовать, так как они не повредят край, в отличие от отвёрток, шпателей и прочих инструментов. В нашем случае не слишком важно не повредить края, так как у нас есть дополнительная кромка по периметру капота. Нужно срезать несколько сантиметров этой кромки, чтобы стык двух половин матриц был чётко виден. Сначала нужно отметить линию среза по всему периметру капота. Для обрезания используется электролобзик. Используйте вольфрамовое карбидное лезвие (tungsten carbide blade). Вставьте клинья или любой другой плоский инструмент вокруг периметра матрицы и аккуратно протолкните внутрь. Так нужно делать постепенно, двигаясь по периметру. Иногда может потребоваться использовать молоток, чтобы немного простукивать клинья или другой инструмент.
Большие панели и матрицы иногда сложно разделять, даже после разъединения краёв. На это влияет небольшая адгезия отлитой формы и статика. При сложности в разъединении можно применить сжатый воздух или напор воды под давлением в щель между матрицей и макетом, чтобы помочь отсоединить матрицу.
В таком виде матрицу можно использовать как есть, но чтобы придать дополнительную гладкость поверхности, нужно отшлифовать поверхность шлифовальной бумагой P1200 с водой. Этот этап уберёт мелкие несовершенства на поверхности и сделает поверхность идеально гладкой. Таким образом, залитая в этой матрице форма не отпечатает на себе мелкие неровности поверхности матрицы.
Как сделать капот из стеклопластика по матрице
- Процесс изготовления копии капота похож на создание матрицы. При создании окончательной копии капота не нужно использовать много смолы, в отличие от матрицы. Достаточно будет, чтобы стекловолокно было пропитано смолой, но не залито.
- Нанесите 3 слоя разделяющего вещества (mold release paste wax) на поверхность матрицы, потом несколько слоёв жидкого разделяющего вещества PVA.
- После высыхания разделяющего вещества наносится 3 толстых слоя gel coat. Этот слой обеспечит гладкую лицевую поверхность будущего капота. Если сразу нанести смолу, а потом стекломат и пропитать его, то лицевая часть будет иметь неровности в виде выпирающих волокон стекловолокна (в особенности, если используется толстый стекломат), поры.
- После нанесения gel coat, нужно выждать от 2–4 часа.
- Далее наносится смола. Для создания капота производитель может рекомендовать смолу Vinyl Ester Resin, которая лучше по свойствам, чем более дешёвая полиэфирная.
- Кладётся слой стекломата и пропитывается смолой. Стекловолокно должно немного заходить за края матрицы. Смолы наносится столько, чтобы полностью пропитать стекловолокно. При этом избегайте нанесения излишнего количества смолы, чтобы не увеличивать вес капота. Прочность от излишней смолы тоже не увеличивается. Смола наносится на поверхность от центра к краям.
- Нужно нанести 4 слоя стекломата. Кладите слои стекломата так, чтобы волокна располагались под разными углами относительно разных слоёв. Это увеличивает прочность во всех направлениях.
- После нанесения и разравнивания первого слоя нужно подождать примерно 40 минут, потом класть 2 слой стекломата. Нужно, чтобы первый слой был твёрдым, но всё ещё липким, перед нанесением второго слоя.
- С 3–4 слоями будет примерно 2.5 — 3 мм толщиной, что соответствует толщине заводских капотов из стеклопластика.
- Раскатайте валиком нанесённый слой, чтобы убрать пузырьки воздуха. Если останутся пузырьки, то в этом месте верхний слой с лицевой стороны может треснуть.
- В отливаемой форме искажения (коробление, скручивание) можно избежать, позволяя каждому слою отвердеть (до состояния липкости поверхности), перед нанесением следующего слоя.
- Сушите смолу медленно. Чем быстрее сохнет панель из стекловолокна и чем выше температура сушки, тем более хрупкой будет панель.
Обрезание лишнего стеклопластика и приклеивание креплений
Нужно срезать излишек по краям двух частей нового капота и вырезать проёмы между усилителями на части капота, которая относится к обратной его стороне. Для обрезания излишков стеклопластика удобно использовать dremel. Обрезая края, нужно следовать линии края, отпечатавшейся от оригинального капота. Нужно срезать с небольшим отступом от линии края капота, так как края нужно будет дорабатывать шлифованием. Перед началом работы не забывайте про средства защиты. Используйте респиратор, защитные очки и перчатки. После обрезания краёв используйте напильник или шлифовальную бумагу на бруске, чтобы подровнять края (P120-P240).
Далее нужно просверлить отверстия для крепления шарниров. Для этого нужно пометить нужные места, в соответствии с местами на оригинальном капоте. Используйте дрель и сверло нужного размера. Место в передней части капота, которое соединяется с замком, нужно вырезать при помощи dremel, а края обработать напильником. Для приклеивания креплений используется двухкомпонентный эпоксидный клей. Этот клей хорошо прилипает как к композитным материалам (в данном случае стекловолокно), так и к металлу. Пока две половины капота (лицевая часть и усилители) не склеены вместе, крепления можно легко приклеить к обратной стороне усилителей.
Соединение двух частей капота
Перед склеиванием двух половин, нужно отшлифовать места соединения, чтобы они были плоскими.
Для склеивания двух половин можно использовать 3М fiberglass panel adhesive, который специально для этого предназначен, либо полиуретановый клей-герметик. Клей нужно нанести на край по периметру, потом разровнять, чтобы получилось примерно 3 мм толщины и 4 мм ширины. Далее половины капота соединяются и прижимаются зажимами на 24 часа. Если используете зажимы, то старайтесь избегать прогибов на краях.
Для склеивания двух половин капота (полотно капота и усилитель) вместе можно использовать матрицу, из которой отливалась лицевая часть капота. Это нужно для того, чтобы лицевая часть не искажалась при склеивании. Берём полотно капота (лицевую часть) и кладём обратно в матрицу, наносим клей и прижимаем вторую половину (усилитель). Поверх усилителя нужно положить груз в нескольких местах. При этом способе склеивания можно обойтись без зажимов.
Как подготовить капот из стеклопластика к покраске?
Прежде всего, нужно знать, что панель из стеклопластика должна как следует высохнуть и затвердеть. Сколько времени только что изготовленный капот должен сохнуть? Чем дольше, тем лучше. Минимальное время 48 часов, а максимальное – вплоть до недели. Полное отвердевание особенно важно, если деталь будет окрашиваться в чёрный или другой тёмный цвет. Так как тёмные оттенки впитывают тепло, на солнце на не просохшем капоте могут возникнуть пузыри или даже искажение формы.
После отвердевания нужно поставить капот на автомобиль и проверить все зазоры. Возможно, нужно будет где-то подрезать панель и подшлифовать, чтобы все зазоры были ровными. При шлифовании панелей из стеклопластика обязательно используйте респиратор, а также работайте в защитной робе.
После подгонки нужно тщательно вымыть панель из стекловолокна. Это нужно, чтобы убрать разделяющее вещество, которое используется для облегчения извлечения капота из матрицы. Если это вещество убрать не полностью, то во время покраски могут возникнуть дефекты «рыбий глаз».
Во многом, подготовка капота из стекловолокна и смолы схожа с подготовкой металлической панели (см. статью “подготовка к покраске”). Важно убрать все неровности шпаклеванием, шлифованием и грунтованием, если они остались.
Каким грунтом покрыть капот из стеклопластика? Здесь может быть несколько вариантов. Можно использовать эпоксидный грунт (см. статью о свойствах и применении эпоксидного грунта). Далее уже можно нанести акриловый грунт, подготовить его и красить.
Ещё одно большое отличие капота из стекловолокна от стального в том, что обычный капот имеет одинаковую поверхность с обеих сторон, в то время как лицевая сторона капота из стекловолокна гладкая, а обратная сторона грубая и неровная. На обратную сторону капота можно нанести полиуретановую краску раптор или аналог, предварительно подготовив поверхность. Это добавит износоустойчивости капоту, а также улучшит внешний вид.
Установка капота из стеклопластика и его эксплуатация
- При установке капота из стекловолокна нужно учитывать конструкцию крепления оригинального капота. К примеру, если использовались пружины в механизме шарниров или замка, то они могут привести к повреждению капота из стекловолокна. То же самое относится к пневматическим упорам капота. В этом случае нужно изменить конструкцию креплений, чтобы капот из стекловолокна не подвергался излишнему напряжению.
- В отличие от закрывания тяжёлого металлического капота, капот из стеклопластика не достаточно просто отпустить, чтобы он хлопнул и закрылся. Нужно убедиться, что замок защёлкнулся. Для этого нужно аккуратно потянуть за край капота вверх и проверить.
- Капоты из стеклопластика толще, чем оригинальные металлические капоты. Поэтому необходимо настроить их по высоте резиновыми регулировочными отбойниками. Отбойники может потребоваться подрезать или убрать полностью.
- Капот из стеклопластика жестче, чем оригинальный из стали. Стальной капот может немного сгибаться по линии крыльев, даже если одно из крыльев расположено ниже, чем другое. Поэтому, после установки капота из стекловолокна может понадобиться скорректировать положение прилегающих панелей.
- Капот из стекловолокна получается лёгким и гибким, поэтому, если автомобиль, на котором установлен капот из стекловолокна, используется для вождения на высоких скоростях, то должны быть установлены специальные крепления для капота (hood pins) на его передние углы для предотвращения его подъёма на скорости.
Печатать статью
Ещё интересные статьи:
Стеклопластик своими руками | Dvamolotka.
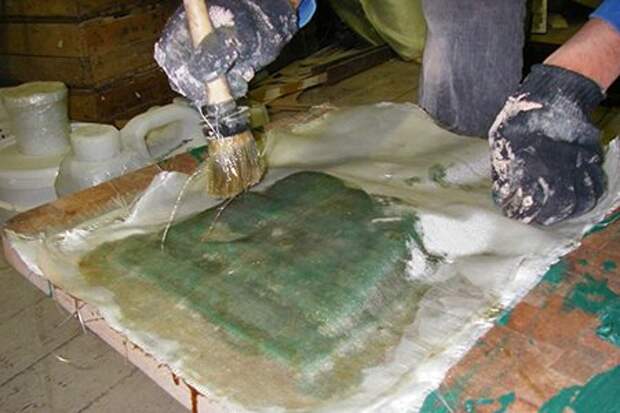
Статья рассказывает о том, какими свойствами обладает стеклопластик и насколько он применим в строительстве и в быту. Вы узнаете, какие компоненты нужны для изготовления этого материала и их стоимость. В статье приведены пошаговые видео и рекомендации к применению стеклопластика.
С момента открытия эффекта быстрого окаменения эпоксидной смолы под действием кислотного катализатора стеклопластик и его производные стали активно внедрять в бытовые изделия и детали машин. На практике он заменяет или дополняет исчерпаемые природные ресурсы — металл и дерево.
Что такое стеклопластик
Принцип действия, заложенный в основу прочности стеклопластика, аналогичен железобетону, а по виду и структуре ближе всего к армированным слоям современной «мокрой» отделки фасадов. Как правило, вяжущее — композитный, гипсовый или цементный раствор — имеет свойство ссыхаться и трескаться, не удерживая нагрузку, а иногда даже не сохраняя целостности слоя. Чтобы этого избежать, в слой внедряют армирующий компонент — стержни, сетки или холст.
В результате получается уравновешенный слой — вяжущее (в высохшем или полимеризованном виде) работает на сжатие, а армирующий компонент работает на растяжение. Из таких слоёв на основе стекловолокна и эпоксидной смолы можно создать объёмные изделия, либо дополнительные усиливающие и защитные элементы.
Компоненты стеклопластика
Армирующий компонент*. Для изготовления бытовых и вспомогательных строительных элементов обычно используется три типа армировочного материала:
- Стеклосетка. Это сетка из стекловолокна с ячейкой от 0,1 до 10 мм. Поскольку эпоксидный раствор — агрессивная среда, для изделий и строительных конструкций настоятельно рекомендована сетка с пропиткой. Ячейку сетки и толщину нити следует подбирать, исходя из назначения изделия и требований к нему. Например, для армирования нагруженной плоскости стеклопластиковым слоем подойдёт сетка с ячейкой от 3 до 10 мм, толщиной нити 0,32–0,35 мм (усиленная) и плотностью от 160 до 330 г/куб. см.
- Стеклохолст.
Это более совершенный вид основы стекловолокна. Он представляет собой очень густую сетку, изготовленную из «стеклянных» (кремниевых) нитей. Его применяют для создания и ремонта бытовых изделий.
- Стеклоткань. Имеет те же свойства что и материал для одежды — мягкий, гибкий, податливый. Этот компонент очень разнообразен — он различается по прочности на разрыв, толщине нити, густоте плетения, спецпропиткам — все эти показатели ощутимо влияют на конечный результат (чем они выше, тем прочнее изделие). Главный показатель — плотность, в пределах от 17 до 390 г/кв. м. Такая ткань значительно крепче даже знаменитого военного сукна.
* Описанные виды армировки применяются и для других работ, но в паспорте изделия обычно указывается их совместимость с эпоксидной смолой.
Таблица. Цены на стеклоткань (на примере продукции компании «Интеркомпозит»)
Плотность | Цена, у. е.![]() |
17 | 4,6 |
25 | 3 |
48 | 3,2 |
80 | 2,8 |
110 | 2,8 |
160 | 3 |
200 | 3 |
280 | 4,3 |
390 | 5,2 |
Вяжущее. Это и есть эпоксидный раствор — смола, смешанная с отвердителем. По отдельности компоненты могут храниться годами, но в смешанном виде состав твердеет от 1 до 30 мин, в зависимости от количества отвердителя — чем его больше, тем быстрее твердеет слой.
Таблица. Наиболее распространённые марки смолы
Наименование | Производитель | Назначение | Цена, у. е./кг |
ЭД-16 | Россия, Китай | Ремонтные работы и слои в защищённых местах | 4,6 |
ЭД-20 | Россия, Китай | Ремонтные работы и слои на открытых местах | 6,3 |
LR1100 | Саудовская Аравия | для бытовых нужд, бижутерии | 2,5 |
Популярные отвердители:
- ЭТАЛ-45М — 10 у.
е./кг.
- ХТ-116 — 12,5 у. е./кг.
- ПЭПА — 18 у. е./кг.
Дополнительным химическим компонентом можно назвать смазку, которую иногда наносят для того, чтобы защитить поверхности от проникновения эпоксида (для смазывания форм).
В большинстве случаев баланс компонентов мастер изучает и подбирает самостоятельно.
Как применить стеклопластик в быту и в строительстве
В частном порядке этот материал чаще всего применяется в трёх случаях:
- для ремонта стержней;
- для ремонта инвентаря;
- для усиления конструкций и плоскостей и при герметизации.
Ремонт стержней из стеклопластика
Для этого потребуется рукав из стеклоткани и высокопрочная марка смолы (ЭД-20 или аналог). Технически процесс подробно описан в этой статье. Стоит отметить, что углеволокно значительно прочнее стекловолокна, а значит, второе не подойдёт для ремонта ударного инструмента (молотков, топоров, лопат). При этом из стеклопластика вполне можно изготовить новую ручку или рукоятку для инвентаря, например, крыло мотоблока.
Полезный совет. Стеклопластиком можно усовершенствовать свой инструмент. Оберните пропитанным волокном рукоять рабочего молотка, топора, отвертки, пилы и сожмите в руке через 15 минут. Слой идеально примет форму вашей руки, что заметно отразится на удобстве в работе.
Ремонт инвентаря
Герметичность и химическая стойкость стеклопластика позволяют ремонтировать и герметизировать следующие изделия из пластика:
- Канализационные трубы.
- Строительные вёдра.
- Пластиковые бочки.
- Дождевые отливы.
- Любые пластиковые детали инструмента и техники, не испытывающие больших нагрузок.
Ремонт при помощи стеклопластика — пошаговое видео
У «самодельного» стеклопластика есть одно незаменимое свойство — он точно обрабатывается и хорошо держит жёсткость. Это значит, что из холста и смолы можно восстановить безнадёжно испорченную пластиковую деталь, либо изготовить новую.
Усиление строительных конструкций
Стеклопластик в жидком виде имеет прекрасную адгезию к пористым материалам. Иными словами, он хорошо сцепляется с бетоном и деревом. Этот эффект можно реализовать при монтаже деревянных перемычек. Доска, на которую нанесён жидкий стеклопластик, приобретает дополнительно 60–70% прочности, а значит, для перемычки или перекладины можно использовать доску вдвое тоньше. Если усилить этим материалом дверную коробку, она станет более устойчивой к нагрузкам и перекосам.
Герметизация
Ещё один способ применения — герметизация стационарных ёмкостей. Резервуары, каменные цистерны, бассейны, покрытые изнутри стеклопластиком, приобретают все положительные свойства пластиковой посуды:
- нечувствительность к коррозии;
- гладкие стены;
- сплошное монолитное покрытие.
При этом создание такого покрытия обойдётся около 25 у. е. за 1 кв. м. О прочности изделий красноречиво говорят реальные испытания продукции одного из частных мини-заводов.
На видео — испытания стеклопластика
Особо стоит отметить возможность починки кровли. Правильно подобранным и нанесённым эпоксидным составом можно отремонтировать шифер или черепицу. С его помощью можно моделировать сложные светопрозрачные конструкции из оргстекла и поликарбоната — навесы, уличные светильники, скамейки, стенки и многое другое.
Пошаговое видео производства матрицы из стеклопластика
Как мы выяснили, стеклопластик становится простым и понятным ремонтно-строительным материалом, который удобно применять в быту. При развитом навыке из него можно создавать интересные изделия прямо в собственной мастерской.
Как сделать стеклопластик в домашних условиях – АвтоТоп
Стеклопластик это материал, состоящий из двух основных компонентов. Это материал из стекловолокна (стекловолокно, стеклоткань, стекломат), который служит для армирования (усиления) изделия, и смолы, являющейся связующим.
Материалы для изготовления стеклопластика.
Смола
Смола является связующим материалом и поэтому к выбору смолы надо подойти наиболее ответственно, особенно при отсутствии опыта изготовления стеклопластиковых изделий. Если при выборе стеклоткани или стекломата можно довольствоваться рекомендациями специалистов, т.к. этим выбором определяются, в основном, механические свойства готового изделия, то разная смола требует разных технологических процессов.
Для начинающих мы рекомендуем эпоксидную смолу. Эпоксидная смола менее привередлива в работе и имеет большее время застывания и поэтому у вас будет больше времени для исправления возможных ошибок. Эпоксидную смолу также рекомендуется использовать при ремонте изделий (лодок, бамперов…). Она хорошо склеивается с пластиком, деревом, металлом.
Полиэфирная смола, в основном, используется для изготовления цельных деталей
Хотим также напомнить, что на свойства смол и на их рабочие параметры довольно сильно влияют температурные характеристики помещения, в котором производятся работы, и его проветриваемость. Порой для лучшего застывания матрицу с изделием помещают в специальную сушильную камеру. Это помогает значительно ускорить процесс получения готового изделия. Самые прочные изделия изготавливаются в автоклавах под большим давлением и при высокой температуре.
Сама смола достаточно хрупкая, и именно стекломатериал придает ей необходимую прочность и гибкость
Материалы из стекловолокна
Для изготовления стеклопластиков используется стекловолокно, ровинг, стекломат, стеклоткань и другие стекломатериалы.
Самые распространенные это ровинг, стекломат и стеклоткань.
Ровинг
Ровинг это стекловолокно собранное в пучок и намотанное на бобину. Ровинг похож на некрученую стеклонить. Укладка ровинга производится специальным пистолетом, в который, во время работы, подается еще смола и катализатор.
Стекломат
Стекломат состоит из хаотично расположенных волокон, а стеклоткань выглядит как обычная ткань. Наибольшее упрочнение дают стеклоткани. Стекломаты дают меньшую прочность, но они более легки в обработке и по сравнению со стеклотканью лучше повторяют форму матрицы.
Стекломат может быть очень тонким, а бывает толстым, как одеяло. Стекломаты различаются по толщине и плотности, но разделяют их по весу одного квадратного метра материала в граммах: 300, 450, 600. Чем тоньше мат, тем более сложную поверхность он позволяет вывести, с большим количеством граней и резких переходов. Толстый мат (600 или 900) позволяет набрать толщину изделия и добиться необходимой прочности. При создании толстых изделий работа проходит в несколько этапов. Выкладывается несколько листов для получения первого слоя и дается время на застывание. Затем дополнительно, уже на твердую поверхность, укладываются дополнительные листы мата для придания необходимой толщины. Если попытаться уложить сразу все слои, то велика вероятность, что готовое изделие покоробится, стянется.
Стеклоткань
Стеклоткани бывают разной толщины. Стеклоткани также используются для придания жесткости и объема готовому изделию. Как и любая ткань, стеклоткань неодинаково работает при разнонаправленном растяжении. Поэтому для придания необходимой жесткости стеклоткань укладывается под разными углами. Стекловолокно в стеклоткани играет немаловажную роль. Оно должно хорошо пропитываться смолой и удерживать ее между волокнами. На это свойство пропитываемости в стеклоткани влияет наличие в ней и количество парафина. На ответственные изделия желательно выбирать стеклоткани без парафина. Парафин также можно выжигать перед применением.
К слову о прочности. Как это ни странно прозвучит, но чем меньше смолы в стекловолокне (при условии его полной пропитки и отсутствии пузырьков), тем прочнее будет готовое изделие и тем меньше окажется и его вес.
Гелькоут (gelcoat)
Для придания цвета готовой детали , а также для защиты от внешних воздействий используется особый материал гелькоут (gelcoat – гелевое покрытие). Можно сказать, что гелькоут это та-же смола, но с добавлением красителя. Его можно подобрать по цвету или создать свой оттенок колеровочными составами. Кроме того, слой гелькоута увеличивает срок службы изделия, защищает от воздействий окружающей среды и скрывает структуру стеклопластика. Готовое изделие будет иметь ровную (зависит от качества матрицы) поверхность, нужного цвета.
Гелькоуты бывают внутренними и внешними (topcoat).
Внутренний гелькоут наносится первым слоем в матрицу. После того как гелькоут затвердел, укладывается стекловолокно и смола. В этом процессе кроется один важный момент. Если слой гелькута будет в одном месте слишком тонкий, то может случиться следующее: или в этом месте будет просвечивать структура стекловолокна, или гелькоут может вообще отойти и сморщиться. Поэтому крайне важно пользоваться правильными материалами и следовать технологии. Для равномерного нанесения гелькоута часто используют не кисти, а краскопульты. Так удается значительно сократить количество брака и уменьшить расход материала. Но для распыления гелькоут должен быть более жидким, чем для ручного нанесения. В настоящее время в продаже имеются готовые гелькоуты для нанесения кистью и для напыления.
Внешний гелькоут (topcoat) наносится после того, как изделие вынули из матрицы. Здесь он выполняет роль краски. Благодаря присутствию в составе топкоута парафина поверхность после отверждения не остается липкой, хорошо шкурится и полируется. Топкоут можно изготовить самим на базе гелькоута или смолы, добавив раствор парафина в стироле.
Макет и матрица
Для изготовления изделия из стеклопластика первое, что необходимо, – создать его макет. В некоторых случаях макетом может являться уже существующее изделие, которое Вы хотите размножить. Например: бампер автомобиля. Для еще не существующих изделий макет может быть изготовлен различными способами: фанера, пластилин, пенопласт и т. д. От того, насколько правильно сделан макет, будет зависеть качество будущих изделий. Более того, если необходимо, чтобы у детали, которая будет затем создаваться, была идеально ровная поверхность, над ее качеством придется поработать уже на макете. Чем более гладким и ровным будет макет, тем меньше работы потребуется потом, при изготовлении и доведении матрицы.
Еще до создания макета необходимо понять, можно ли изготовить деталь целиком или нет. Дело в том, что при работе со стеклопластиками и другими подобными материалами необходимо, чтобы готовую деталь после застывания можно было вытащить из матрицы, ничего не повредив при этом. Возможно, деталь будет иметь такую форму, что ее придется изготавливать из нескольких частей, а затем скреплять их друг с другом.
Матрица создается по макету. Это самый ответственный момент. Прежде всего макет покрывается тонким слоем воска. Эту процедуру можно сравнить с полировкой автомобиля. После того как макет подготовлен, на него наносится слой специального матричного гелькоута. Это покрытие в дальнейшем позволит вывести поверхность матрицы практически до зеркального блеска. Матричный гелькоут гуще, чем обычный, и ложится более толстым слоем.
После того как встанет этот слой, начинается укладывание стекломатериала. Сначала более тонкого (стекловуаль, …). Он позволит точно повторить все изгибы и контуры макета. Далее желательно дать подсохнуть первому слою. Затем уже можно выложить еще несколько слоев более толстого материала (мат, стеклоткань), но сразу набирать толщину не стоит, иначе матрицу может повести (изогнуть и покоробить). При создании матриц на простые детали можно упростить процедуру.
Если матрица будет разъемной, то при ее изготовлении делаются специальные перегородки вокруг макета, разделяющие его на сегменты. Выложив основной, после его застывания перегородки вынимаются и, обработав кромки первого сегмента матрицы, выкладываются остальные. Для правильного позиционирования сегментов друг относительно друга в первом при формовании делаются специальные ямки. Когда будут формоваться следующие сегменты, эти ямки будут заполнены смолой и стекловолокном, и появятся бугорки. Эти пары и позволят при будущем использовании правильно скрепить различные части матрицы воедино. Для скрепления сегментов матрицы в ребрах всех отдельных частей сверлятся отверстия под крепежные болты.
Для того чтобы матрица была прочной и хорошо держала форму, после ее изготовления, прежде чем вынуть макет, к матрице приформовывают ребра жесткости. В зависимости от ее размеров это может быть прочный стальной каркас или небольшие фанерные или деревянные ребра.
Готовая матрица, если макет был изготовлен аккуратно, может и не потребовать дополнительной обработки, но зачастую приходится выводить поверхности, шлифовать и полировать матрицу до блеска. Только тогда можно получить идеальную деталь. А к кузовным элементам вообще нужно особое внимание.
Затем начинается долгий процесс вощения. Матрицу приходится тщательно натирать воском несколько раз с перерывами. Воск нужно не просто намазывать, а растирать до получения тонкой, гладкой, невидимой пленки. Если этого не сделать, то поверхность готового изделия будет не гладкой, а шершавой.
После, а порой и вместо вощения иногда используют специальные жидкости, которые, высыхая, создают пленочное покрытие, предотвращающее попадание смолы или гелькоута на матрицу, чего никак нельзя допускать. Как нельзя и царапать ее поверхность. В противном случае смола может намертво прирасти к матрице, и тогда процедуру шлифовки, полировки и вощения придется повторять снова. Порой используют особые составы, обработав которыми матрицу можно снимать с нее до 100 изделий, но старый добрый воск всегда остается самым понятным и надежным средством.
Процесс создания матрицы, описанный выше, является довольно распространенным вариантом, используемым в большинстве фирм, но существуют и другие, более сложные технологии.
Собственно, далее можно приступать к изготовлению деталей. Слой гелькоута в принципе не обязателен, но, во-первых, он придает более законченный вид готовому изделию, а будучи цветным, позволяет сэкономить на покраске или вообще от нее отказаться, а во-вторых, он защищает матрицу от стекловолокна, которое на самом деле очень даже абразивно, т. е. царапает.
Технологии
Технологий производства изделий из стекловолокна существует несколько. Стоит сразу оговориться, что эти методы используются и при работе с другими армирующими материалами, такими, как карбон, кевлар, другие тканые материалы и их сочетания.
Ручное (контактное) формование. Этот способ самый простой и дешевый (если не считать затрат на квалифицированную рабочую силу). Пропитка стекловолокна осуществляется валиком или кистью, которые должны быть стойкими к смолам. Волокно или сразу укладывается в форму, или уже после пропитки. Обработка стекловолокна разбивочными валиками способствует лучшему распределению смолы между волокнами. Затем укаточными валиками производят окончательную укатку стеклоткани, выдавливая пузырьки воздуха и равномерно распределяя смолу по всему объему. Крайне важно не допустить, чтобы под слоем стеклоткани оставались пузырьки воздуха. Если изделие застынет с таким браком, это место будет ослаблено вплоть до возможного сквозного продавливания. Такие брачки также могут помешать дальнейшей обработке изделия, потребовать его восстановления или полной замены. В любом случае будут затрачены дополнительные материалы, труд, а также деньги.
Ручной метод может быть несколько механизирован. Существуют смесители, подающие смолу с катализатором через валик, и иные приспособления. Но укатывать все равно приходится своими руками.
Достоинство ручного метода вполне очевидно: просто и дешево. Но любая экономия может иметь и обратную сторону. Качество готовых изделий очень сильно зависит от квалификации рабочих. И условия труда при таком подходе довольно вредные. Кроме того, очень сложно добиться большой производительности. Однако для небольших фирм и малых объемов работы этот метод самый подходящий.
Метод напыления рубленого ровинга. Этот подход куда более технологичен. В нем используется не стекловолокно, а стеклонить, которая подается в измельчитель специального пистолета, где рубится на короткие волокна. Затем пистолет «выплевывает» их вместе с порцией смолы и катализатора. В воздухе все смешивается и наносится на форму. Но после этой процедуры все равно массу необходимо прикатать, чтобы удалить пузырьки. Далее отвердевание происходит как обычно.
Такой способ выглядит очень заманчиво и просто. Казалось бы, стой и поливай из шланга. Но есть один существенный недостаток, из-за которого этот способ не столь популярен, – слишком большой расход смолы. Изделие получается очень тяжелым, и, так как волокна не переплетены друг с другом, механические свойства такого стеклопластика несколько хуже. Кроме того, к вредным парам смол подмешивается взвесь мелких частиц стекла от измельчителя, очень вредных для легких человека.
Метод намотки. Этот специфический метод предназначен для изготовления пустотелых круглых или овальных секционных компонентов, типа труб или резервуаров. Таким образом делаются парусные мачты, удочки, рамы велосипедов, глушители автомобилей и т. д. Стекловолокна пропускаются через ванну со смолой, затем через натяжные валики, служащие для натяжения волокна и удаления излишков смолы. Волокна наматываются на сердечник с необходимым сечением, угол намотки контролируется отношением скорости движения тележки к скорости вращения. Как намотка нитки на шпульку швейной машинки. В результате получаются крепкие и легкие изделия.
Метод препрегов. В данном случае используются не отдельные смола и ткань, а так называемые препреги – предварительно пропитанная смолами стеклоткань. Стекловолокно предварительно пропитывается предкатализированной смолой под высокой температурой и большим давлением. При низких температурах такие заготовки могут храниться недели и даже месяцы. При этом смола в препрегах находится в полутвердом состоянии. При формовании препреги укладываются в матрицу и закрываются вакуумным мешком. После нагрева до 120 -1800°C смола переходит в текучее состояние, и препрег под действием вакуума принимает нужную форму. При дальнейшем повышении температуры смола застывает.
Вся проблема этого метода в необходимости нагревательного оборудования, особенно автоклава. По этой причине изготавливать большие детали очень сложно. Но и плюсы очевидны. Использование вакуума позволяет значительно снизить вероятность появления воздушных пузырьков и существенно сократить долю смолы в готовом изделии.
Существуют и иные технологии – пултрузия, RFI, RTM и др. – практически на все случаи жизни. Выбор той или иной технологии зависит от необходимых объемов, сложности изделия и количества денег.
Согласитесь, не каждый поклонник тюнинга имеет возможность приобрести оригинальные предметы интерьера в соответствующих магазинах. Но, честно говоря, это вовсе не обязательно — превратить обычный автомобиль в предмет искусства можно и самостоятельно, если научиться правильно делать стеклопластик своими руками.
Собственно, стеклопластик представляет собой полиэфирную смолу, которая изготавливается примерно следующим образом: материалу придают необходимую форму, армируют стекловолокном и затем полимеризуют.
Само собой разумеется, что тягаться с фирменными предметами гаражного тюнинга мы не намерены. Но если необходимые детали имеют незначительные размеры, то сделать их может практически каждый. Но начинать подобную практику лучше всего с примитивных деталей, имеющих самые простые очертания.
Их установка не должна требовать от вас какой-либо сверхъестественной аккуратности. Постепенно, день за днем, мы будем приобретать нужный нам опыт и когда-то сможем приступить к гораздо более сложным изделиям.
Учимся быть аккуратными.
На начальном этапе изготовления нам необходимо сделать болванку и для этого, скажу я вам, нам придется попотеть. Стоит отметить, что форма болванки должна в точности имитировать будущую деталь. По этой причине самой главной заботой будет именно правильность всех изгибов, симметрия и максимально чистая поверхность.
Еще один не менее важный момент — это материал, из которого будет сделан наш пуансон. К примеру, если деталь будет иметь большие габариты (такие, как бампер), то болванку для нее лучше изготавливать из пенопласта.
Основание, полученное таким образом, после завершения процесса можно даже не удалять. Для меньших деталей следует использовать глиняные или пластилиновые детали (но, честно говоря, нюансы обработки подобных материалов может вас несколько смутить).
Нередко в качестве пуансона используют древесину. Хотя ее предварительная обработка, связанная с придачей формы, и кажется на первый взгляд сложной, но последующая обработка наждачкой станет для вас сущим пустяком.
Помимо этого, на данном этапе мы должны определиться, каким именно образом готовое изделие будет сниматься с болванки. Если есть возможность, то мы ее попросту снимаем. Но в отдельных случаях вам придется распиливать болванку на две части, дабы извлечь изделие.
Как бы то ни было, но перед извлечением изделия вам в любом случае понадобится специальное смазывающее вещество, которым нужно будет обработать стенки матрицы. Хотя, если планируется использование пенопласта, то подобные манипуляции не потребуются.
Смола, используемая при изготовлении стеклопластика, превращается в пластик только после того, как в нее добавят отвердитель. Также существует специальная инструкция, в соответствии с которой смешиваются необходимые компоненты.
При наличии минимального опыта вы сможете самостоятельно контролировать процедуру отвердения. Так, если вам нужно ускорить процесс, то массу следует немного нагреть. Примерно такой же эффект достигается, если увеличить количество отвердителя. Но и в первом, и во втором случае полученная масса будет не слишком уж крепкой.
Еще один важный момент — это прокаливание ткани, можно даже на открытом огне. Когда перестанет идти дым, мы прекращаем процедуру: все защитные вещества, в том числе и парафин, уже испарились, а пустоты между тканями заполнились нашей смолой.
Когда начнем пропитывать стеклоткань, то лучше положить ее на стекло, так смола распределится максимально равномерно. Также для этого можно использовать железную линейку, сильно придавив ее к поверхности.
Ткань помещается на болванку как целиком, так и несколькими отдельными лоскутами (в данном случае все будет зависеть от особенностей конкретной модели и от ваших умений). Разумеется, что разделение ткани на лоскуты (если такое потребуется) произойдет еще до начала пропитки.
Роль стеклоткани
Когда готовая стеклоткань будет помещаться на болванку, то нужно позаботиться о максимальном ее прилегании, исключив разнообразные складки. Но если вы что-то там недоглядели и они все же образовались, то мы аккуратно удаляем их кончиком ножа.
Примерно так же удаляются воздушные пузыри. Также стоит отметить, что зачастую одного слоя ткани не хватает, минимальное количество — три-четыре. Каждый слой мы укладываем по очереди, но без длительных задержек. В противном случае предыдущий слой может высохнуть.
Убираем болванку
Когда затвердеет смола (это примерно 3-4 суток), мы удаляем болванку. К слову, это крайне ответственный процесс и повреждение «скорлупы» в нем — нередкое явление. Если это произошло, не отчаивайтесь, ведь поврежденную поверхность можно подклеить посредством той же смолы.
В итоге хотелось бы добавить, что практически каждое изготовление детали тюнинга осуществляется по данной схеме. Но если будет несколько экземпляров, то процедура значительно усложнятся. «Скорлупу» при этом необходимо укрепить дополнительными слоями. Подобные матрицы можно неоднократно использовать, но все детали, вышедшие из нее, потребуют хорошей чистки.
А если необходимо сделать более прочный стеклопластик своими руками, то изделие на этапе затвердения помещают в вакуум (то есть, в полиэтиленовый мешочек с откачанным воздухом). Тогда все слои ткани уплотнятся и, соответственно, существенно уплотнится вся поверхность готового материала.
Видео урок — матрица из стеклопластика своими руками
Изготовление стеклопластика своими руками
Если же рассматривать вопрос про изготовление стеклопластика своими руками, то из всех существующих технологий, предпочтение лучше отдать так называемому методу ручного формирования. О том, как сделать стеклопластик в домашних условиях и какие материалы для этого понадобятся в первую очередь, будет рассказано ниже.
Что такое стеклопластик
Стеклопластик представляет собой одну из разновидностей композитных материалов, очень широко используемых сегодня как в промышленности, так и в быту. Основными элементами стеклопластика, являются: полимерная смола, специальный наполнитель, стеклоткань и армирующие элементы.
Стеклопластик имеет относительно небольшой вес, около 300-900 грамм на 1 м², хотя во многом данный показатель зависит от толщины изделия. Как было сказано выше, для изготовления стеклопластика своими руками, предпочтительней применение метода ручного формирования, без использования дорогостоящего оборудования для этих целей.
Сам процесс изготовления стеклопластика, таким образом, выглядит так:
- Сначала производится подборка и раскрой стеклоткани;
- Затем изготавливается разделительный слой в матрице;
- Создаётся покровный слой и укладка материала в подготовленную для этих целей матрицу;
- Наносится полимерный состав;
- Производится сушка материала.
Заключительным этапом изготовления стеклопластика в домашних условиях, является обработка изделия после его сушки.
Изготовление стеклопластика своими руками
Итак, рассмотрим первый этап изготовления стеклопластика, который начинается с выбора материалов для матрицы. При одноразовом изготовлении стеклопластикового изделия, матрицу для этих целей можно вылить, например, из гипсового раствора. Если же нужно сделать большое количество стеклопластиковых деталей, то лучше всего использовать для этого стальную матрицу.
Теперь что касается полимерной смолы, поскольку её состав может быть также различным. Здесь всё во многом зависит от таких характеристик полученного изделия, как его:
- Цвет;
- Водонепроницаемость;
- Рабочая температура и невосприимчивость к ультрафиолету;
- Уровень мягкости, хрупкости и ударопрочности;
- Подверженность к воздействию химических веществ.
Укладку стеклоткани в матрицу производят после её предварительного раскроя. Если матрица имеет сложную форму, то допускается использование отдельных элементов стеклоткани, для равномерного формирования слоя в матрице.
Далее производится нанесение формировочного слоя на поверхность матрицы, для удобства извлечения высохшего изделия из неё. Материалом для разделительного слоя может служить, например автомобильный воск или тефлоновый гель.
После подготовки матрицы вышеописанным способом, в неё заливается первый слой (покровный) стеклопластика. Покровный слой состоит из состава полиэфирной или эпоксидной смолы. С его использованием медлить не стоит, поскольку применять смолу нужно в течение 15 минут.
Как клеить стеклоткань
Итак, после того как покровный слой уложен, а его толщина должна варьироваться в пределах 0,4 мм, можно приступать к укладке стеклоткани в матрицу. В первую очередь укладывается самый тонкий слой стеклоткани, не более 300 г/м². При этом нужно следить, чтобы в матрице не образовались пустоты и воздушные пузыри.
Количество и толщина приклеиваемой стеклоткани в матрицу, зависит в первую очередь от того, какую прочность должно иметь изделие из стеклопластика. Последний укладываемый слой в матрицу, состоит либо из отделочной стеклоткани, либо из стекловойлока.
Когда залитый состав наберёт свою прочность, а это примерно 12-24 часа, готовое стеклопластиковое изделие извлекается из формы. Далее следует заключительный этап обработки, во время которого производится шлифовочные и полировочные работы.
из стеклопластика, фанеры или пенопласта?
Желание, хоть ненадолго, стать капитаном пусть даже самого маленького судна, очевидно, живет в нас с раннего детства. Оно не уплывает в бумажной лодочке по весеннему звонкому ручью, не растворяется в детских снах о дальних морских путешествиях. А если рядом есть водоем, по которому вы можете периодически совершать пусть не дальние и не морские, но вполне водные путешествия, то можно сделать лодку, например из стеклопластика, своими руками — эта статья для вас. Причем молоток, либо вообще не потребуется, либо почти не потребуется.
Какую лодку будем строить
Здесь решающим фактором может стать не только глубина вашего кошелька, но и глубина, а также ширина и соленость близлежащего водоема, а значит и правила судоходства на нем. Мы, конечно же, не будем строить морскую яхту, а поговорим об материалах, приемах и способах сооружения небольших весельных лодок и лодок, на которые можно установить небольшой двигатель, т.е. о конструкциях достаточно легких и не особо больших.
И даже в этом сегменте судостроительства, конструкций, технологий и подходов такое количество, что мы возьмем за основу наиболее, на наш взгляд простые и действенные. В конце 70-х годов прошлого века на многочисленные водоемы Советского Союза вышли в большое плавание распашные прогулочные лодки, изготовленные целиком из стеклопластика. Новый «корабль» был значительно легче, маневреннее своей тяжелой деревянной предшественницы, поэтому на лодочных станциях разбирался в первую очередь. К тому же, такая шлюпочка и ремонтировалась легко, и служила не меньше деревянной. Что мешает просто взять и повторить эту технологию в удобных для себя размерах. Да ничего, а вот надо ли – разберемся в процессе описания процесса.
Изготовление лодки из стеклопластика своими руками
Делается такая лодка, независимо от сложности, по одной схеме:
- изготавливаем макет;
- наносим разделительный слой;
- укладываем стеклоткань (или стекловолокно) со связующим (эпоксидная или полиэфирная смола, полиуретановый компаунд) необходимой толщины;
- обрабатываем и устанавливаем оборудование, узлы, элементы прочее.
При выборе такой технологии изготовления лодки, нужно учесть два момента, а именно то, что изготовление макета для производства одной единственной лодки – выбрасывание на ветер денег, а толщина стеклопластика для прочности и жесткости судна должна достигать 10 – 15 мм, что еще более затратно.
Жесткость подобным суднам придают за счет дополнительных конструктивных элементов. Поэтому в индивидуальном производстве в чистом виде эта технология почти не используется, а используется в соединении с другими конструкционными материалами, такими как фанера.
Самодельная лодка из фанеры
Очень многие создатели самодельных лодок предпочитают работать именно с этим материалом, так как он общедоступен, легко обрабатывается и, главное, при небольших толщинах – гнется. Если мы ведем речь об индивидуальной рыбацкой лодочке из фанеры, которая будет использоваться на ближайшем пруду, без риска повредить днище об острые прибрежные камни, то вполне достаточно будет фанеры толщиной 6 – 8 мм. Да и выкроить такую лодочку можно из одного листа фанеры.
Для соединения между собой элементов лодки используют тонкую медную проволоку, продетую через отверстия, просверленные по краю друг напротив друга с шагом приблизительно 150 мм. Борта и транец ставят на днище.
Стыки изнутри и снаружи проклеивают тремя слоями стеклоткани с увеличением по ширине от внутреннего к наружному. Поверху приклеивают обносную рейку (буртик), уширения под уключины, упоры для сиденья и обязательно на дно несколько реек для жесткости. Можете все скручивать на саморезы, которые потом нужно будет обязательно выкрутить, а в оставшиеся отверстия вбить деревянные нагеля на эпоксидной смоле. В отверстия для уключин лучше вклеить трубки из нержавейки, на худой конец – из латуни. Если на днище приклеить килевую рейку – лодка будет лучше вести себя на воде. В принципе, прокрасив это сооружение в несколько слоев пентафталевой краской, можно отправляться в заплыв. Но если всю конструкцию оклеить в 2 – 3 слоя стеклотканью на одном из вышеупомянутых связующих, то срок службы вашего судна увеличится как минимум вдвое и вполне может составить лет эдак с тридцать. Если вы сделаете это, то не поскупитесь и на покупной гелькоут или сделайте его, добавив в эпоксидку краситель. Нужно помнить, что со временем это покрытие стоит обновлять.
Весла можете купить готовые, а можете сделать сами, лучше из клееной древесины. Длина их не должна быть меньше 2 м, оптимальный размер – 2,2 м. Для лопасти использовать фанеру толщиной 6 мм.
По такому принципу можно построить и достаточно большую лодку, усилив корпус шпангоутами и другими необходимыми элементами. Конечно же, и фанера берется потолще. Предварительно изготовьте макет судна из плотного картона. Масштабировав элементы, получите чертежи деталей. А вообще-то в интернете достаточно чертежей лодок и катеров на любой вкус, также есть журнал «Катера и яхты» в котором тоже публикуются интересные проекты.
Лодка из пенопласта
Пожалуй, проще этого метода постройки лодки и не сыщешь. Достаточно большой кусок пенопласта – сам по себе лодка. Крепи уключины, ставь весла и в путь. Естественно, это слегка упрощенный вариант водного транспортного средства, но масса простеньких суденышек-катамаранов построено именно по такому принципу:
- берут два пенополистирольных блока, при помощи нихромовой проволоки и зарядного автомобильного устройства придают им форму поплавков катамарана;
- приклеивают килевые рейки, оклеивают несколькими слоями стеклоткани с усилением носовой и хвостовой части;
- сооружают деревянную или металлическую платформу;
- обеспечивают плавсредство любым движителем (от гребного колеса до легкого движка).
И все. А если все же говорить о лодке или небольшом катере, то пенополистирол может сослужить роль несъемной модели, повысив, к тому же, живучесть судна.
Все, как в случае с изготовлением чисто стеклопластиковой лодки, но модель делается из пенопласта толщиной 5 – 10 см и плотности 35 – 50 кг/см2, который склеивается между собой на полиуретановый клей. О способах придания пенополистиролу необходимой формы, кроме уже упоминавшегося, говорить не будем, их достаточно и все они вполне просты. Тем более что форму и сложность конфигурации своего корабля вы выбираете сами.
Так вот, когда ваше пенопластовое судно радует глаз своими плавными обводами, вы можете просто оклеить его многими слоями стеклоткани до требуемой ее толщины, вклеив все узлы, нуждающиеся в усиленном креплении или предусмотрев места их крепежа. И дальше – по схеме: шпаклевка, шлифовка, гелькоут и шампанское…
Хотя, нет. С шампанским мы погорячились. Наша лодка легка, достаточно прочна для эксплуатации длительное время, но об ее корпус бутылку с шампанским разбить вряд ли получится. А вот если до стеклоткани оклеить пенопластовую модель хотя бы в самых ответственных местах (днище, нос, корма, выступающие элементы) всего лишь 4-мм фанерой, то прочность судна увеличится значительно.
Все это не более чем приемы работы с материалом, а какие из них использовать – решать вам. Наша задача показать, что такая работа вам по силам и может сэкономить существенные финансовые ресурсы.
Уважаемые читатели, если у вас остались вопросы, задавайте их, используя форму ниже. Мы будем рады общению с вами 😉
Рекомендуем другие статьи по теме
Изделия из стеклопластика под заказ, масштабные объемы!
Изготовление деталей из стекловолокна
Стеклопластик – это композитный материал, который уже успел покорить рынок и вытеснить многие другие материалы. По своей сути, стеклопластик представляет собой стекловолокно, которое по специальным технологиям обрабатывается эпоксидной или полиэфирной смолой. В результате, получается сложный материал, обладающий уникальными физическими, химическими и эксплуатационными характеристиками. Изготовление деталей из стекловолокна – это достаточно трудоемкий процесс, который требует наличия:
- специального оборудования;
- качественных материалов;
- владения инновационными технологиями;
- квалифицированного труда высококлассных профессионалов и т.д.
Все это, и многие другое, есть в компании Голд Арт Лайн, которая занимается многими видами работ по выполнению декоративных элементов, в том числе – и изделий из стеклопластика для интерьера и экстерьера. Впрочем, не только декоративные элементы из стеклопластика производят наши специалисты. Мы предлагаем изготовление деталей из стеклопластика людям, у которых имеются катера и другие плавстредства, а также матрицы, которые используются в различных сферах деятельности. Выбор стеклопластика в качестве материала для изготовления декоративных элементов и различных деталей позволяет получить изделия с высокой эстетикой, но и дополнительные преимущества, обусловленные качественными характеристиками самого материала. Детали из стеклопластика используются во многих сферах деятельности и производственных процессах, а потому они востребованы и популярны. Компаний, которые занимаются производством таких изделий, сегодня появилось достаточно много, но не все производители соблюдают технологические процессы, от чего страдает качество изделий и их эксплуатационные свойства. Компания Голд Арт Лайн предлагает вам обширное портфолио изделий из стеклопластика, с которым вы можете ознакомиться на страницах нашего сайта.
Преимущества стеклопластиковых изделий
Главное преимущество деталей и готовых изделий из стеклопластика заключается в их относительно малом весе, в сравнении с деталями и конструкционными частями из металлов и их сплавов. Кроме того, используя такие детали можно получить ряд дополнительных преимуществ:
- В ходе эксплуатации различные конструктивные части изделий и декоративные элементы из стеклопластика могут подвергаться механическим воздействиям и , как следствие – повреждениям.
Преимущество заключается в том, что стеклопластик имеет свойство возвращаться в исходную форму, если не имеет места разрушение элементов.
- Если те или иные детали из стекловолокна сильно повреждены, то их можно восстановить, уложив в имеющуюся матрицу.
- Износ материала является минимальным, а потому изделия из стеклопластика имеют практически неограниченный срок эксплуатации.
Стоимость изделий нельзя назвать дешевой, но это компенсируется их высоким качеством и неограниченными возможностями. Компания Голд Арт Лайн – это компания международного уровня, у которой есть достаточно внушительные производственные мощности и все необходимое технологическое оборудование, чтобы производить высококачественные детали из стекловолокна на заказ и готовые изделия из стеклопластика. Такие изделия широко применяются как строительной сфере, так и в сфере современного судостроительства.
Если вам нужно изготовить пластиковую деталь, то вы можете заказать у нас любые изделия, которые вам необходимы. Мы выполняем все работы в точно обозначенные сроки и в соответствии с договорными обязательствами. В сравнении с конкурентами, наши цены более чем демократичны, а условия сотрудничества – приемлемы и ориентированы на потребности заказчика. За более подробной информацией обращайтесь по телефонам, которые вы найдете в разделе нашего сайта «Контакты». Мы всегда рады новым проектам и плодотворному сотрудничеству.
У вас есть вопросы по изделиям из стеклопластика? Позвоните нам, мы сможем Вам помочь!
Простые методы формования стекловолокна и углеродного волокна: 4 шага (с изображениями)
Я использовал этот метод для модификации существующего кузова гоночного автомобиля Mazda Ralt R5 CSR. Его новая шина / колесо приводило к тому, что передние шины ударяли по существующему кузову, поэтому он изменил его, вырезав отверстия в крыльях, а затем прикрутив несколько пластин с проставками, чтобы передние шины очистились, когда подвеска была полностью сжата. Модификации были довольно уродливыми и неаэродинамичными (не говоря уже о том, что шины все равно иногда натирались), поэтому он попросил меня сделать новые части крыльев, которые можно было бы прикрепить к существующему кузову, чтобы ему не пришлось покупать все новые кузова для перед его гоночной машиной.Я внес эти изменения несколько лет назад, поэтому у меня нет фотографий всей последовательности, поэтому я сделал рисунки, чтобы заполнить пробелы.
Первое, что я сделал, — это выяснил, насколько я хочу приподнять линию крыла, а затем вырезал шаблон, который будет использоваться для разрезания синей пены. Затем синюю пену разрезают с помощью кусачка для горячей проволоки и кладут на имеющееся крыло для проверки посадки.
Затем поролон приклеивается к крылу с помощью прозрачной упаковочной ленты — лента не дает полиэфирной смоле расплавить пену при наложении стекловолокна.Затем я сделал несколько вентиляционных отверстий для нового крыла, используя деревянную лепнину — она приклеена горячим клеем на проклеенную пену.
Пенопласт, обмотанный лентой, затем покрывается смазкой для форм.
Теперь ткань из стекловолокна смачивается полиэфирной смолой и накладывается на пену. Для этого можно использовать тканую ткань из стекловолокна или коврик из рубленых прядей. Если вы используете CSM, вы должны использовать полиэфирную смолу — полиэфирная смола плавит стирольное связующее в CSM. Эпоксидная смола только создаст огромный беспорядок.
При использовании тканой ткани я делаю один трюк: предварительно разрезаю ткань и приклеиваю ее к выкройке с помощью цемента для распыления 3M Super77, а затем смачиваю ткань смолой, используя кисть с короткой щетиной. Если ткань (или CSM) необходимо накладывать секциями, убедитесь, что секции перекрываются как минимум на один дюйм.
Как только смола затвердеет, вы можете вытащить форму из стекловолокна из пены.
Чтобы вылепить позитив из углеродного волокна из формы из стекловолокна, сначала нанесите воск для смазки формы на форму из стекловолокна.
Затем начните смачивать углеродную ткань смолой и укладывать ее внутрь формы из стекловолокна. При смачивании смолы используйте кисть с короткой щетиной и нанесите «точечный» эффект, чтобы убедиться, что смола полностью проникла в угольную ткань, помещенную в форму. Я предпочитаю использовать эпоксидную смолу при ламинировании углеродной ткани, так как она дает гораздо более жесткий конечный продукт.
Я обычно накладываю слои углеродной ткани с попеременным расположением под углом 45/90 градусов. Это связано с тем, что тканая углеродная ткань имеет жесткость только в направлении ориентации ее волокон.
До того, как смола полностью затвердеет, вы можете обрезать излишки материала по краям формы ножницами — позже это сделать гораздо сложнее.
Как только смола полностью затвердеет, деталь можно вынуть из формы.
После завершения процесса формования все, что мне нужно было сделать, это приклеить новые углеродные секции к существующему кузову и смешать их с некоторым наполнителем.
Как сделать форму из стекловолокна Инструкции
Мы начнем с изготовления формы для люка фюзеляжа, таким образом мы создадим образец для люка и будем использовать образец штриховки, чтобы рисунок фюзеляжа идеально подходил к люку.Применяя смазку для пресс-формы к выкройке, важно нанести как смазку для пресс-формы Partall, так и жидкую смазку для пресс-формы Coshops. Восковая эпиляция повторяется; количество раз зависит от поверхности. Если поверхность потенциально пористая, необходимо нанести несколько слоев. Эти слои воска заполнят мелкие дефекты поверхности. Если у вас есть сомнения, добавьте еще несколько слоев воска. Если они не заполнены полностью, эпоксидная смола заблокирует эти недостатки. Затем на воск наносится смазка для пресс-формы Liquid Coshops.
Комбинезон можно наносить качественной малярной кистью, воду можно использовать для очистки малярной кисти после каждого слоя. Нанесите тонкий ровный слой, стараясь удалить лишнюю жидкость или потеки. Дайте этому слою высохнуть и нанесите второй слой, чтобы обеспечить полное равномерное покрытие.
Пыль и грязь могут улавливаться смазкой для формы, когда она высыхает и становится частью поверхности формы. Если у вас есть какие-либо дефекты в смазке для пресс-формы, удалите слой водой и бумажным полотенцем и повторно нанесите смазку для пресс-формы Комбинезон.Поверхность, которую вы видите в пресс-форме, будет той поверхностью, которую вы увидите в пресс-форме и деталях. После формования детали смазку для формы необходимо удалить из формы, а деталь с помощью воды и бумажного полотенца и нанести повторно перед следующей операцией формования.
Теперь вы готовы приступить к нанесению слоев эпоксидной смолы и стеклоткани. Используйте следующие эпоксидные продукты West System:
105 Смола — это смола с низкой вязкостью, которая легко смачивает ткань и оставляет минимальные пузырьки воздуха между слоями ткани.
205 Fast Hardener дает достаточно времени для смачивания каждого слоя, а затем быстро загустевает, так что процесс создания формы может быть завершен за несколько часов.
406 Коллоидный диоксид кремния используется для загущения эпоксидной системы для облегчения нанесения эпоксидной смолы на вертикальные поверхности, заполнения углов и деталей в форме.
423 Графитовый порошок используется для придания механическому слою покрытия формы черного цвета и более твердой и прочной поверхности.
Стекловолоконная форма, знакомство с заглушками
Изготовление форм для стекловолокна — заглушки
Первым шагом в изготовлении пресс-формы из стекловолокна является изготовление заглушки. Заглушка для пресс-формы из стекловолокна или композитного материала, как правило, представляет собой представление готовой детали и может быть реальной деталью или макетом детали. При планировании пресс-формы необходимо учитывать определенные факторы; чистота поверхности, углы уклона, поднутрения и способ изготовления.Композитная форма, которая будет использоваться для процессов вакуумной инфузии или закрытого формования, потребует больших фланцев. Детали с поднутрением или отрицательной осадкой необходимо будет изготовить в двухкомпонентных формах, чтобы их можно было извлечь из формы. Композитные формы, которые предназначены для использования с деталями из углеродного волокна, часто необходимо изготавливать из углеродного волокна, чтобы обеспечить соответствие коэффициента теплового расширения, особенно если в процессе формования деталь и форма будут нагреваться до отверждения, а затем охлаждаться до demold, я.е. детали из препрега. Если форма должна выдерживать высокие температуры и требуется дополнительное отверждение заглушки, то ваш выбор материалов изменится.
Заглушки, изготовленные с нуля, можно изготавливать из самых разных материалов с помощью самых разных методов. Мы разместили здесь пример изготовления вилки с нуля и полного ее изготовления. В этом примере мы использовали пенопласт для изготовления корпуса, прикрепили его к фанере, чтобы сделать фланец, и застеклили поверх него, чтобы обеспечить стабильную поверхность, над которой можно обтекать. Мы использовали МДФ для изготовления заглушек, пенопласта высокой плотности, пенополистирола, наполнителя для кузова и других материалов. Для крупных деталей часто строится каркас, который затем покрывается пеной, стекловолокном и наполнителем кузова перед грунтованием и отделкой.
Для того, чтобы сделать из стекловолокна формы из существующей детали, мы обычно смонтировать часть на опорной доске какой-то.Вообще говоря, мы строим все наши формы с фланцами, предполагая, что в какой-то момент мы захотим использовать их в процессе закрытого формования или вакуумной инфузии. Гораздо легче встроить фланцы в форму из стекловолокна с самого начала, чем делать это позже. Фланцы пресс-формы должны быть минимум 6 дюймов, предпочтительно 8 дюймов. Установите часть на опорной доске любыми доступными средствами и необходимыми. Горячий клей — одно из наших предпочтений, поскольку он быстро схватывается и обычно снимается, однако, если вы имеете дело с повышенными температурами, горячий клей не подойдет.После того, как часть установлена на сытости Задник и скругления любые пробелы или переходы между частью и опорной доски так, чтобы ваша вилка один блок. Качество поверхности вилки и ваша опорной доска будет отражено в гелькоуте формы. Лучше не станет, только хуже. Прежде чем продолжить, доведите поверхность до желаемого уровня готовой композитной детали. Для заглушек этого типа мы обычно рекомендуем использовать восковую пасту и ПВА в качестве смазки для форм.ПВА создает физический барьер между пробкой и гелькоутом стекловолоконной формы. Это обеспечивает дополнительную защиту готовой детали, которую вы используете в качестве вилки.
После того, как заглушка доведена до желаемой чистоты поверхности и нанесена смазка для пресс-формы, пора приступить к изготовлению пресс-формы из стекловолокна. Обычно для этого используются следующие материалы: гелькоут, полиэфирная смола (изо-инструментальная смола), стеклоткань или стекловолоконный мат. При изготовлении формы из углеродного волокна вы будете использовать: углеродное волокно, эпоксидное покрытие и эпоксидную смолу. В этой статье мы дадим краткий обзор этапов создания формы из стекловолокна с гелевым покрытием.
Сначала нанесите гелькоут (желательно с помощью пистолета-распылителя до толщины 20 мил мокрого (0,020 дюйма)) на поверхность заглушки.Дайте гелькоуту застыть, пока он не станет твердым, но липким на ощупь. Затем нанесите один слой мата из стекловолокна на всю поверхность формы с полиэфирной смолой поверх гелькоута, соблюдая особую осторожность, чтобы удалить весь воздух и убедиться, что ламинат не имеет пустот. Дайте этому слою полностью высохнуть, чтобы свести к минимуму любую возможность деформации поверхности. После того, как этот слой затвердеет, нанесите 2-3 слоя стекловолокна за раз, пока не получите желаемую толщину. Например, 9-10 слоев по 1.Стекловолоконный мат на 5 унций даст вам толщину формы около 0,38 дюйма (что для небольшой формы вполне приемлемо). На более крупных формах из стекловолокна может быть более практичным добавить материалы сердцевины, чтобы довести форму до желаемого уровня жесткости.
Для получения дополнительной информации о конкретных материалах перейдите по этой ссылке
Одноразовая конструкция из стекловолокна поверх пены
Обзор того, как работать со стекловолокном поверх пены
Роберт К.Райли Применение композитов FRP / пены в автомобилестроении было впервые предложено в 1970-х годах бывшей дизайнерской фирмой автора Quincy-Lynn Enterprises, Inc. Мы использовали многослойную полиэфирную смолу и стеклоткань поверх сердцевины из жесткого пенополиуретанового картона (стекловолокно поверх пенопласта). В современных вариациях иногда используется эпоксидная смола или винилэфирная смола и ткань из углеродного волокна поверх уретановой пены, как композит, используемый для создания экспериментального легкового автомобиля GM Ultralite. Материалы из углеродного волокна намного дороже, и сомнительно, соответствует ли эта стоимость дополнительным расходам.Несмотря на преимущество новых материалов в соотношении прочности к весу, ничто не сравнится с исходным композитом полиэфир-смола / стеклоткань / пенополиуретан для быстрого производства прочного и легкого продукта по минимальным ценам. И это удивительно простая система в использовании.
Из этого композита можно сделать практически все, от кузова автомобиля до лодки. Следующее описание шаг за шагом проведет вас через создание композитного стекловолокна / пены на кузове автомобиля. Чтобы проиллюстрировать этот процесс, мы включили фотографии, сделанные на разных этапах строительства Tri-Magnum; высокопроизводительный трицикл, планы на который доступны на этом сайте. Однако эти методы будут одинаково хорошо работать и в других приложениях. И планы Tri-Magnum включают гораздо больше деталей, чем показано в этом обзоре.
Если вы хотите продолжить работу над индивидуальным проектом (не обязательно Tri-Magnum) и просто хотите знать, как это сделать, гибридные планы XR3 на диске обеспечивают максимальную детализацию, плюс часа- длинное видео , показывающее, как применяется и укрепляется стекловолокно. (См. Рамку внизу этой страницы.) Если вы планируете проект из композитного стекловолокна / пены, план XR3 на диске даст вам гораздо более глубокое понимание при минимальных затратах.Планы также охватывают дизайн петель, приспособлений и остекления, что позволяет создавать собственные петли и приспособления и правильно закреплять их в стеклопластике. Этот композитный процесс также хорошо работает для изготовления заглушки для традиционной формы из стекловолокна. Или вы можете заказать видео для мгновенной загрузки
Недорогой и щадящий материал
Типичный автомобильный кузов потребует фанеры, уретановой пены и стандартного полиэфирного стекловолокна на сумму около 900 долларов (тот же материал, который используется для изготовления лодок, машин и серийных корветов). Корпус сначала изготавливается из недорогого пенопласта (обычно это панели размером 4 x 8 футов из материала толщиной 1 дюйм), цементируемые на месте над формирователями станций. Пенопласт или бак также могут служить недорогим полноразмерным макетом для укладки. Изложите около 250 долларов на достаточно фанеры и пенопласта и около трех-четырех дней на сборку, чтобы построить типичный автомобильный кузов из пенопласта.
Если конструкция не подходит для трех измерений, ее можно изменить, уложив дополнительную пену и изменив ее форму. Или вы можете отказаться от первой попытки и начать заново с минимальными потерями в стоимости материалов.А сборка практически безболезненна. Используя бритвенный нож, уретановая пена режет, как масло, и шлифуется так легко, что вы можете потереть две части вместе и наблюдать, как она тает. Стекловолокно применяется для герметизации пены только после того, как конструкция будет полностью доработана. Разглаживание стекловолокна для подготовки его к покраске — самая трудоемкая часть процесса. Но даже здесь современные пластиковые наполнители для кузова и наносимые распылением грунтовки / покрытия, такие как «Featherfil» и «Eliminator», значительно упрощают работу, чем первоначальный метод шлифовки и гелькоута, использовавшийся при первой разработке системы.
Начните с прикрепления формовочных станков из фанеры
Кузовной проект начинается с шасси, поддерживаемого по высоте. Обычно колеса необходимо снимать, чтобы они не мешали гладкой кривизне пенопласта. Затем в соответствующих местах по всей длине прикрепляются фанерные каркасы станций. Правильное размещение и количество подстанций будет зависеть от конструкции кузова и расположения удобных точек крепления на шасси. Формирователи станций обычно становятся частью готового кузова, где они служат переборками кабины, противопожарной перегородкой и / или точками крепления кузова к шасси. Щелкните фотографии справа от страницы, чтобы увидеть ее в большом размере.
Установите формирователи станции : Tri-Magnum потребовалось всего четыре формирователя станции для плавного переноса контуров тела спереди назад. Как правило, перед установкой пенопласта необходимо снять колеса. Формирователи станций прикручены болтами, поэтому корпус можно будет снять позже.
Использование стрингеров для отслеживания формы вспененных панелей
Некоторые строители могут предпочесть рассчитывать форму пенопластов по чертежам.Более быстрый практический метод — прикрепить временные стрингеры к формам станции на каждом изломе формы (чтобы они стали точками стыковки пенопласта). Затем панели кузова могут быть нанесены непосредственно на пену, используя стрингеры в качестве направляющих. Вырежьте пенопластовые панели большего размера, затем придайте им форму по мере установки. Используйте контактный цемент на основе растворителя, чтобы приклеить пену к соседним панелям (цементы на водной основе плохо подходят для уретановой пены). Лучше всего носить респиратор для твердых частиц при работе с незащищенной уретановой пеной (до того, как она будет покрыта стекловолокном), чтобы избежать вдыхания частиц в воздухе, вызванных шлифовкой. На коммерческих объектах эти респираторы от пыли требуются OSHA
Укладка пенопласта : Используя фетровый маркер, обведите края стрингеров, чтобы очертить панели на пенопласте. Срежьте пену бритвенным ножом. Обычно стыковые кромки необходимо отшлифовать и придать им форму, чтобы они хорошо прилегали к прилегающим панелям.
Сборка пенопластовых панелей в очевидной последовательности
Правильная последовательность сборки будет зависеть от вашей конкретной конструкции. Корпус из пенопласта Tri-Magnum начинается с продольных панелей, установленных в самом широком месте корпуса.В случае других конструкций может быть лучше сначала установить паркетную доску и двигаться вверх. Там, где внутренние конструкции имеют важное значение для прочности, установите их и закрепите швы с помощью стекловолоконного мата с внутренней стороны. В Tri-Magnum большая часть пассажирского салона была собрана и покрыта стекловолокном до установки панели крыши. Однако часто детали интерьера легче установить после того, как кузов был покрыт стекловолокном. Идея состоит в том, чтобы построить каркас кузова и закрепить его стекловолокном, прежде чем заняться всеми деталями.Правильная последовательность строительства зависит от конструктивных особенностей и от того, какие элементы будут недоступны в дальнейшем.
Установите панели из пеноматериала : Соберите панели в очевидной последовательности. Отрежьте пенопласт, затем отшлифуйте и сформируйте края, чтобы они подходили к соседним панелям. Закрепите пенопластовые панели контактным цементом на основе растворителя. Не используйте клей на водной основе. Клеи на водной основе плохо сочетаются с пенополиуретаном.
Детализируйте зону обитания : Детализируется пассажирский салон Tri-Magnum до закрытия кузова.Центр был вырезан из второй бывшей станции, чтобы освободить место для ног пассажиров. Пенопласт в центре временный. Он используется для сохранения выпуклой кривизны кровельной панели. Без этой временной панели панель крыши провисла бы в области лобового стекла. Снимите временную пенопластовую панель после того, как снаружи будет стекловолокно.
Закройте крышу : Последняя панель на крыше закрывает кузов. Обратите внимание, что панель крыши свисает сбоку.Этот лишний материал можно быстро удалить бритвенным ножом или подпилить напильником. Обработка блоков по швам приведет к тому, что панели будут заподлицо.
Добавить детали к пенопласту
По мере добавления деталей пенопласт начинает больше походить на готовый продукт. Картон из пенопласта толщиной в один дюйм обеспечивает много материала для глубокого закругления углов, чтобы избежать панельного вида. Уретановой пене легко придать форму с помощью пилки Surform или шлифовального блока. Некоторые детали при установке могут потребовать усиления слоем стекловолокна.Например, брови Tri-Magnum были чрезвычайно тонкими и простирались довольно далеко от тела. Следовательно, они были усилены стекловолокном, чтобы они сохраняли свою форму и выдерживали случайные атаки падающего инструмента.
Create Wheel Well Eyebrows : Брови Tri-Magnum изготовлены из вспененных панелей толщиной 1/2 дюйма, которые приклеиваются на место. Укладка коврика сверху защищает легко повреждаемые брови. Используйте эту технику усиления пенопласта с накладкой из стекловолокна в любой точке, которая требует усиления.
Деталь Колодцы задних фонарей : На соседней фотографии рабочий добавляет галтели из пенопласта для отделки внутренней части отсека для задних фонарей. Хотя следует избегать образования воздушных карманов внутри пенопласта, в этом случае небольшой карман будет существовать между галтелем, установленным на фотографии, и панелью из пенопласта на внешней стороне корпуса.
Обведите двери и окна фетровым маркером, затем зашлифуйте углубления и линии разреза в пену с помощью шлифовального блока. Окна остаются нетронутыми, чтобы избежать ослабления напряжения, которое могло бы удерживать кривизну в соседних панелях. Сложная детализация, возможная с пенополиуретаном, видна на следующих фотографиях.
Зашлифуйте оконные фланцы в корпус : Утопленные стыковочные фланцы для остекления (окон) и аксессуаров, а также линии отделки двери / козырька зашлифованы на поверхность пенопласта до того, как он будет покрыт стекловолокном.
Деталь задней части : С уретановой пеной возможны глубокие совки, длинные обтекатели и замысловатые формы.И даже на этом этапе элементы укладки все еще можно модифицировать, наложив дополнительный поролон и изменив форму поверхности.
Нанесите оболочку из стекловолокна для герметизации пены Слои стекловолокна превращают хрупкий пенопласт в настоящий автомобильный кузов. Накладка стекловолокна на внешнюю и внутреннюю поверхности пенопласта создает жесткую многослойную структуру, которая намного прочнее и легче, чем обычная одностенная оболочка из стекловолокна. Типичная внешняя укладка состоит из двух слоев стекловолоконной ткани весом 6 унций и полиэфирной смолы для ламинирования, которые наносятся по одному за раз.Во избежание неровностей поверхности не используйте мат снаружи. Нанесите аналогичные слои (две ткани) стекловолокна на заднюю сторону, чтобы полностью покрыть пену. Дополнительные слои ткани и усиление мата можно использовать на обратной стороне, вдоль внутренних углов и на участках, где пена была отшлифована особенно тонко. Когда стеклопластик будет сделан, вырежьте из кузова люки, двери и окна, а затем детализируйте интерьер.
Нанесите слои из стекловолокна : Используйте недорогую кисть со щетиной, чтобы нанести катализированную смолу на стеклоткань.Стекловолокно можно делать секциями, как показано на фото слева. Пена полностью покрыта двумя слоями стекловолокна. Другими словами, не должно быть открытых участков из пенопласта или фанеры.
Вырезать навес из кузова : Используйте переносную сабельную пилу, чтобы вырезать двери, люки и окна из кузова. Купол раскладушки Tri-Magnum стабилизирован за счет остекления стального каркаса изнутри. Каркас застекляют перед тем, как отделить купол от тела.Если купол не был стабилизирован стальным каркасом, он не будет сохранять свою форму после того, как будет отрезан от тела.
Добавить возврат, желоба и приспособления для навесного оборудования после облицовки стекловолокном снаружи
Дойти до этого уровня можно немногим больше, чем за три-четыре уик-энда. Теперь, однако, прогресс, похоже, замедлится, поскольку в кузов встроены такие детали, как гайки, фланцы, водосточные желоба и другие элементы интерьера.
Отделка салона и водосточные желоба : Сиденья и водосточные желоба Tri-Magnum встроены в кузов путем цементирования пены, придания ей формы и затем стекловолокна.Толщина пены не должна быть одинаковой по всему телу. В одних областях он может быть толще, в других — тоньше.
Создание фланцев вокруг заднего люка : Чтобы создать выступ вокруг отверстия, приклейте вощеный мазонит к задней части стеклопластика, а затем нанесите стекловолокно на вощеную поверхность. Когда стекловолокно схватится, удалите мазонит и нанесите стекловолокно на заднюю сторону, чтобы укрепить фланец и изолировать любую открытую пену. Обязательно удалите остатки воска со стекловолокна, отшлифуя его и протерев ацетоном.Если на стекловолокне останутся отложения воска, последующие слои не будут хорошо держаться и могут расслоиться позже.
Разгладьте поверхность и нанесите краску
Процесс выравнивания и разглаживания кузова из стеклопластика является наиболее трудоемкой частью строительства. В литературе по стекловолокну описываются различные методы получения отделки гелькоутом. Однако в Quincy-Lynn вместо этого мы использовали обычные методы ремонта кузовов и наполнители. Корпус из стекловолокна сначала обрабатывается напильником Surform, чтобы удалить большие потеки из стекловолокна и неровности поверхности.Затем он покрывается легким пластиковым наполнителем для тела (например, «Bondo») и выравнивается с использованием традиционных методов работы с телом.
Катализируйте небольшое количество наполнителя для тела, затем нанесите и разгладьте пластиковым ракелем. Покройте за раз примерно два квадратных фута. Подождите, пока заполнитель не схватится, затем выровняйте поверхность с помощью напильника Surform, прежде чем переходить к прилегающей зоне. Лучше всего подходят маленькие полукруглые напильники. Не ждите, пока материал полностью затвердеет. Используйте файл Surform, когда наполнитель для тела еще достаточно мягкий, чтобы он мог легко врезаться в наполнитель, образуя небольшие скрученные полоски материала.Если наполнитель гранулируется или стирается (вместо чистой резки), он еще недостаточно твердый. Если основная пилка проскакивает по поверхности, не врезаясь в материал, значит, основной наполнитель стал слишком твердым. После полного затвердевания поверхность необходимо выровнять шлифовальной машиной, что является гораздо более медленным и трудоемким процессом. Сразу после того, как поверхность была выровнена напильником (до полного затвердевания материала), используйте шлифовальный блок с зернистостью 36, чтобы удалить следы напильника. После застывания шпатлевки зачистить поверхность наждачной бумагой зернистостью 100–120.
Выровненное тело затем обрабатывается полиэфирной грунтовкой / грунтовкой, например Featherfil или Eliminator. Затем его можно покрасить любой из традиционных автомобильных красок. Покрытие из полиэстера не так сложно, как традиционное покрытие гелькоутом. Однако результаты приходят гораздо быстрее.
Кузов приближается к стадии окраски : На фото справа показан корпус Tri-Magnum после того, как он был заполнен и выровнен. На этапе, показанном на фото, кузов практически готов под покраску.Темные участки нижней части тела уже обработаны Eliminator. Перед нанесением грунтовки элиминатор необходимо отшлифовать.
Дополнительная информация и одночасовое видео
В вышеприведенной статье используется Tri-Magnum, чтобы проиллюстрировать технику одноразового строительства из стекловолокна поверх пены. Фактический план Tri-Magnum обеспечивает гораздо более глубокое обсуждение и более 130 фотографий и иллюстраций с высоким разрешением. Если вам нужно видео процесса, подумайте о покупке тарифных планов XR3 Hybrid.Хотя планы XR3 специально ориентированы на XR3 Hybrid, в действительности они представляют собой кладезь информации о том, как построить практически любую форму или структуру из пенопласта и стекловолокна, включая кузова автомобилей, суда на воздушной подушке и лодки. Руководство по XR3 включает в себя множество технической информации и более 200 иллюстраций и фотографий, сделанных во время постройки XR3. Планы XR3 также включают одночасовое видео на DVD, в котором показаны различные этапы и методы сборки всего кузова автомобиля. Когда вы посмотрите видео, вы поймете, как использовать эту удобную систему для создания любых ваших специальных проектов.Планы также касаются конструкции из углеродного волокна ручной укладки. Щелкните здесь, чтобы увидеть изображение пакета «Планы на диске».
XR3 представлены в трех вариантах. Для тех, кто хочет использовать планы для получения общей информации, пакет «Планы на диске» предоставляет всю необходимую информацию по минимально возможной цене, включая видео на DVD. Щелкните здесь, чтобы приобрести планы XR3 Hybrid.
Как сделать форму из стекловолокна
Изготовление формы из стекловолокна
Заглушка
Чтобы иметь форму, по которой можно разработать форму, вы должны либо построить изделие с нуля, используя дерево, гипс, полиэфирную замазку, формику, листовой металл и т. Д.или у вас должна быть под рукой готовая статья, которую вы хотите продублировать. Последний, конечно, самый быстрый метод. Вилка — это, как правило, мужская модель, во всех деталях точно такая же, как предмет, который вы хотите изготовить. Если заглушка не имеет уклона (конуса), вам будет сложно снимать детали. Если вилка имеет обратные изгибы, как у многих каноэ, вам нужно будет сделать разъемную форму, которую можно раздвигать или разбирать.
Если на поверхности пробки есть мягкие материалы, такие как штукатурка, дерево или шпатлевка, то ее необходимо покрыть лаком или смолой для заполнения пор. Если используется штукатурка, ее необходимо высушить в духовке, а затем герметизировать.
Чтобы форма не прилипала к пробке, пробка должна быть покрыта пластиковой пленкой, известной как «ПВА». Это пластик, растворенный в спирте, зеленого цвета. Его можно нанести кистью или распылением, но лучше всего нанести три тонких слоя, первый из которых будет «туманным слоем». Тогда внешний вид будет зеленым. Каждый слой должен высохнуть в течение получаса или около того, и на нем не должно быть луж или капель, которые могли бы испортить поверхность плесени.Для максимально легкого разделения, перед нанесением PVA, нанесите мягкий воск (TR Mold Release) , разработанный для использования с PVA. После высыхания третьего слоя ПВА на него можно аккуратно нанести покрытие из этого воска для легкого разделения.
Форма
Первым шагом является нанесение гелькоута , который будет поверхностью формы. Гелькоут должен быть «наружным гелькоутом» (без воска). Если необходимо снять много деталей с формы, желательно использовать гелькоут , который предназначен для увеличения срока службы формы.Цвет гелькоута должен контрастировать по цвету с поверхностью детали, которую вы будете делать. Поскольку большинство деталей имеют светлый цвет, обычно используется черный гелькоут . Это облегчает нанесение светлого гелькоута равномерной толщины, так как черный будет виден сквозь тонкие пятна.
Если гелькоут наносится кистью, необходимо нанести два слоя, и первый слой должен затвердеть за несколько часов до нанесения второго слоя. Лучшее средство для нанесения гелькоута — это простой пистолет для гелькоута , предназначенный для этой цели и простой в очистке.Желательно давление воздуха от 80 до 90 фунтов. Гелькоут необходимо наносить толщиной не менее 15 мил или кварту на каждые 25 квадратных футов поверхности. Если заглушка была шероховатой, так что потребуется значительная шлифовка гелькоута, нанесите дважды. Перед нанесением гелькоута его, конечно же, необходимо катализировать пероксидным отвердителем MEKp, используя от одного до двух процентов. Все гелькоуты из Bottom Paint Store включают MEKp.
Когда гелькоут затвердеет и его нельзя будет поцарапать ногтем на краю формы, что занимает от 2 до 4 часов до ночи в прохладную или влажную погоду, вы готовы к «кожному покрову».«Это слой ¾ или 1 унция. мат из стекловолокна , достаточно тонкий, чтобы вы могли видеть и удалять все пузырьки воздуха, захваченные смолой, когда вы «смачиваете» мат. Смолу следует наносить мохеровым валиком или кистью до тех пор, пока не исчезнут белые волокна. Затем пузырьки воздуха удаляются с помощью рифленого пластикового или металлического валика для ламинирования. Используемая полиэфирная смола должна быть «смолой для укладки», не содержащей воска. Будьте осторожны, чтобы не перебрать катализатор при укладке стекла. При температуре выше 75 ° F обычно достаточно одного 10-15 куб. См отвердителя на литр. Ниже 70 ° F, 20 куб. См на кварту. Не работайте при температуре ниже 65 ° F.
При укладке стекловолоконной формы можно избежать деформации, позволяя каждому слою «оттолкнуться» или загустеть перед переходом к следующему слою. На большую плесень хорошо наносить всего один слой в день. После «кожного покрова» можно использовать 1½ унции. мат из стекловолокна для более быстрого наращивания. Как правило, тканый ровинг не используется в формах, поскольку рисунок переносится через форму на гелькоут.Если для прочности в большой форме необходимо использовать тканый ровинг из стекловолокна, его наносят после полного затвердевания мата толщиной в 3 или 4 слоя. Толщина, необходимая для изготовления формы, зависит от размера и формы, а также от количества снимаемых деталей. Чтобы использовать форму для лодки всего несколько раз, достаточно четырех слоев мата.
Удаление формы с пробки
По возможности дайте плесени застыть в течение нескольких дней, чтобы она сохранила свою форму. Первый шаг — обрезать лишний ламинат до формованного края.Это легко делается сабельной пилой и полотном для резки металла. Края тщательно отшлифовать до тех пор, пока не станет видна линия между формой и заглушкой. Затем между формой и заглушкой проталкивается заостренный «язычок», чтобы разделить края. Затем стержень вытягивают вокруг заглушки до тех пор, пока все края не станут свободными и не останется мостиков. Избегайте использования для этой цели металлических инструментов, так как они поцарапают поверхность формы. Затем форма должна вырваться из пробки. В противном случае детали можно согнуть или осторожно постучать резиновым молотком.При необходимости воздух или вода могут быть нагнетены под давлением между пробкой и формой. Для этого в интерфейсе можно просверлить отверстие. ПВА водорастворим, что облегчает расставание под давлением воды.
Полировка формы
В зависимости от состояния поверхности формы ее, возможно, придется отшлифовать зерном 220, обрабатывая до 600, влажным или сухим. Затем на поверхность наносится обычная чистовая отделочная смесь, предназначенная для работы со стекловолокном. Наилучших результатов можно достичь, используя специальные составы, такие как 3M Finesse-It Marine Paste Compound , чтобы добиться зеркального блеска.
Перед использованием формы необходимо дать ей застыть в течение недели или более, если возможно. Обязательно используйте разделительную пленку ПВА и мягкий воск для первых 3-х или 4-х частей, после чего можно использовать карнаубский воск.
Проблемы с гелькоутом
Аллигаторство или сморщивание может возникнуть в результате:
1. Гелькоут местами слишком тонкий
2. Недостаточное количество отвердителя или отвердитель недостаточно смешан.
3. Гелькоут не затвердел до укладки мата.
4. Ацетоновый очиститель капает с валика или кисти во время укладки мата.
Оригинальный технический товар предоставлен Fiberglass Coatings.
Литье из стекловолокна | Фибер Гласт
Фото предоставлено IStock Photo.
Проверьте свои навыки формовки стекловолокна
Примите участие в викторине по формованию стекловолокна!
- Фото предоставлено IStock Photo. Композиты
открывают огромные возможности для изготовления деталей после понимания нескольких основных концепций. Ключ кроется в понимании различных доступных материалов, их применения и наилучших способов обращения с ними.
Этот технический документ представляет собой общий обзор изготовления композитов с упором на изготовление деталей в формах. Широкий охват этого технического документа ограничивает количество деталей, содержащихся в основных основах и конструкции пресс-формы.Fiber Glast Developments предлагает официальные документы, в которых более подробно рассматриваются конкретные аспекты этих областей.
Терминология
Лучшее место для начала изучения композитных материалов — это понимание словаря, используемого в этой области. При описании процесса изготовления композита часто используются следующие термины:
Штука: Готовый продукт, который вы изготавливаете.
Заглушка: Фактический предмет, который должен быть продублирован из стекловолокна или других композитных материалов, который используется для создания формы.Заглушка может быть собственно частью или изготовлена по индивидуальному заказу практически из любого материала.
Форма: Изделие, из которого будет изготовлено изделие. Есть два основных типа слепков: мужские и женские. Патрубок идентичен дублируемому изделию, и деталь изготавливается поверх формы. Матричная или полая форма — это обратная сторона дублируемого изделия, и деталь изготавливается внутри формы. Это слово также можно использовать для описания процесса изготовления композита: формование детали.
Ламинат: Прочная деталь, изготовленная из комбинации смолы и армирующей ткани. Этот термин также можно использовать для описания процесса укладки детали: ламинирование детали.
Гелевое покрытие (или поверхностное покрытие): Термин гелевое покрытие часто используется в общем для описания любого поверхностного покрытия на основе смолы, но с технической точки зрения этот термин применяется к материалам на основе полиэфира. Термин «поверхностное покрытие» может использоваться для описания эпоксидных или полиэфирных материалов.Поверхностные покрытия представляют собой специально разработанные загущенные версии смол, которые можно наносить на поверхность формы или детали в качестве косметического и защитного покрытия.
Разделительный агент: Любой из ряда материалов, нанесенных на поверхность формы перед изготовлением детали, чтобы способствовать высвобождению детали из формы. Это могут быть воски, масла или специальные антиадгезионные покрытия, такие как ПВА.
Фланец / разделительная перемычка: Временное приспособление, прикрепляемое к заглушке при сборке составных форм.Как правило, это создает поверхность для формованных материалов, перпендикулярную плоскости симметрии разделения. Фланец помогает зажимать или скреплять секции формы вместе, а также служит точкой крепления во время операций вакуумной упаковки.
Материалы
Когда вы знаете «ключевые слова» композитов, следующим шагом будет изучение различных вариантов смол и армирования, доступных при работе с композитами. Первая часть этого раздела касается трех основных смол, используемых для большинства композитных конструкций, а вторая часть посвящена наиболее распространенным армирующим материалам.
Смолы
Композитная структура состоит из термореактивной смолы, используемой в сочетании с некоторыми типами армирования, такими как тканая ткань из стекловолокна. Три основных типа смол, отверждаемых при комнатной температуре, используемых в производстве композитов, — это полиэфирные, винилэфирные и эпоксидные смолы.
Полиэфирная смола — это смола общего назначения, подходящая для самых разных применений. Перекись метилэтилкетона (МЕКП) должна использоваться в качестве катализатора для начала процесса отверждения. Скорость катализа можно варьировать с помощью полиэфирных смол, чтобы приспособиться к различным условиям окружающей среды. В тонких слоях или при напылении гелькоута в качестве верхнего покрытия поверхность может оставаться липкой и не затвердеть должным образом, если оставить ее на воздухе. Для полного отверждения тонкие ламинаты или верхние покрытия должны содержать либо раствор стирольного воска, либо слой раствора поливинилового спирта (ПВА), нанесенный на них для герметизации воздуха. В первом случае воск «всплывает» на поверхность по мере отверждения смолы, действуя как барьер для воздуха.После отверждения стирольный воск необходимо отшлифовать, а ПВА можно смыть теплой водой.
Эпоксидные смолы не так просты в измерениях, как полиэфирные смолы, но эпоксидные смолы обеспечивают большую прочность и стабильность размеров. Они также лучше прилипают к другим материалам, чем полиэфирные смолы. Соотношение отвердителя эпоксидной смолы не может быть изменено, и во время процесса отверждения необходимо поддерживать соответствующую температуру (не менее 70 градусов по Фаренгейту). Системы на основе эпоксидных смол, как правило, стоят дороже, чем полиэфирные смолы, но они практически необходимы в некоторых случаях ремонта, например, при использовании листового формованного компаунда (SMC).Эпоксидные смолы также настоятельно рекомендуются для использования с Kevlar® и углеродным волокном.
Третий тип смолы, винилэфирная смола, по своим свойствам по большей части находится между полиэфирными и эпоксидными смолами. Однако он превосходит оба в области коррозионной стойкости, термостойкости (хорошо до 300 градусов по Фаренгейту) и прочности. Обычно используется для ремонта корпуса лодки, строительства полного резервуара и облицовки резервуаров для хранения химикатов. Как и полиэфирная смола, она катализируется МЕКП, но виниловый эфир имеет более короткий трехмесячный срок хранения.
Примеры продукции
Товар | Описание | |
---|---|---|
Полиэфирная смола | Полиэфирные смолы — это наиболее широко используемые смолы в композитной промышленности.![]() | |
Винилэфирная смола | Смола на основе сложного винилового эфирасчитается гибридом полиэфира и эпоксидной смолы, что означает, что ее рабочие характеристики, свойства и цена обычно уступают двум другим. Виниловый эфир отличается высокой устойчивостью к коррозии, температуре и растяжению. | |
Эпоксидная смола | Для композитных деталей, требующих максимальной прочности, изготовители будут использовать эпоксидную смолу.Помимо улучшенных прочностных свойств, эпоксидные смолы обычно превосходят полиэфир и сложный виниловый эфир по стабильности размеров и улучшенному сцеплению с другими материалами. | |
MEKP | Перекись метилэтилкетона или МЕКП требуется для всех полиэфирных смол, гелькоутов и винилэфирных смол.![]() | |
PVA | Поливиниловый спирт, или ПВА, распыляется на тонкие ламинаты или верхние слои, чтобы изолировать воздух во время отверждения детали. После этого ПВА можно смыть теплой водой. | |
Стироловый воск | Стироловый воск — еще одно решение, позволяющее не допускать попадания воздуха на детали в процессе отверждения. В отличие от ПВА, воск будет «плавать» на поверхности смолы по мере ее отверждения.После отверждения стирольный воск необходимо отшлифовать. |
Ткани
Существует множество армирующих тканей, которые используются с обсуждаемыми смолами. Чаще всего используются три типа армирующих тканей: стекловолокно, кевлар® (арамейд) и углеродное волокно (графит). Каждый из них обладает разными качествами и преимуществами. Все три обычно доступны в виде жгутов или ровниц, вуалей и тканых материалов. Кроме того, стекловолокно доступно в виде мата из рубленых прядей, который состоит из коротких случайно ориентированных волокон, скрепленных связующим веществом.
Углеродное волокно стоит дороже всего, но оно обеспечивает исключительно высокую прочность и жесткость, будучи чрезвычайно легким. Кевлар® также легкий и обеспечивает отличную стойкость к истиранию. Однако его трудно разрезать и смочить смолой. В целях отделки производители часто используют поверхностный слой из легкой стекловолоконной ткани в ламинатах Kevlar®, потому что после отверждения Kevlar® практически невозможно шлифовать. В большинстве универсальных приложений используется ткань из стекловолокна.Несмотря на то, что ему не хватает легкого и высокопрочного углеродного волокна или Kevlar®, его приобретение значительно дешевле. Ткань из стекловолокна бывает самых разных стилей и веса, что делает ее идеальной для многих областей применения. Доступны стили высокопрочного переплетения, и их можно рассматривать как экономически эффективную альтернативу более современным тканям.
Примеры продукции
Товар | Описание | |
---|---|---|
Стекловолокно | Стекловолокно — основа композитной промышленности.Он легкий, имеет умеренную прочность на разрыв и прост в обращении. Производители будут использовать стекловолокно в широком спектре проектов в отрасли. | |
Углеродное волокно | Углеродное волокно используется везде, от автогонок до авиакосмической отрасли. Хотя он дороже, чем стекловолокно и кевлар, он может похвастаться самой высокой прочностью на растяжение, сжатие, изгиб и изгиб в отрасли. Углеродное волокно обычно используется для проектов, требующих более высокого уровня прочности, таких как несущие детали. | |
Кевлар | Кевлар — одно из первых высокопрочных синтетических волокон, получивших признание в промышленности армированных волокнами пластмасс.![]() |
Конструкция пресс-формы
Фото предоставлено IStock Photo. Первый шаг в изготовлении пресс-формы состоит из изготовления и / или подготовки пробки. Пробка может быть изготовлена практически из чего угодно, если ее поверхность может быть обработана достаточно хорошо, чтобы получить подходящую поверхность формы. Как указывалось ранее, заглушка может быть либо существующим изделием, либо чем-то, изготовленным специально для процесса изготовления пресс-формы. Некоторые из материалов, обычно используемых при строительстве заглушек, включают дерево, гипс, металл и пенополиуретан. Последний выпускается либо в виде предварительно сформованных листов, либо в виде двухкомпонентной системы смешивания и заливки, которая химически реагирует с образованием пены. Пена «смешай и налей» будет соответствовать форме любой полости, в которую наливаются ингредиенты.
Поверхность заглушки должна быть обработана по крайней мере так же, как желаемая поверхность изготавливаемой детали. В большинстве случаев предпочтительной поверхностью заглушки будет идеально гладкая и полированная поверхность класса «А». Если на готовой детали требуется особая текстура или узор, их можно включить в поверхность заглушки. Высококачественная шлифуемая грунтовка для поверхностей, такая как Duratec Grey Surfacing Primer (# 1041-B), хорошо работает в качестве финишного покрытия на пробке.На этом этапе установите на заглушку фланцы и любые необходимые разделительные перегородки (см. «Особые рекомендации по конструкции пресс-формы»).
Перед началом изготовления формы на заглушку необходимо нанести разделительный состав. Это самый важный шаг в процессе, потому что, если разделительный агент не действует, форму нельзя удалить, не повредив ее и заглушку. Немного дополнительных усилий на этом этапе лучше, чем часы, потраченные на попытки исправить повреждение пробки и формы. Разделительный агент может представлять собой комбинацию разделительного воска и ПВА или одностадийного разделительного агента, такого как FibRelease.
При использовании воска нанесите четыре слоя с выдержкой в час между вторым и третьим слоями. После полировки последнего воскового покрытия нанесите три тонких слоя тумана ПВА и дайте ему высохнуть в течение 30-45 минут. FibRelease можно протереть или намочить на вилке и дать высохнуть в течение 30 минут. Обязательно нанесите разделительный состав на поверхность всех фланцев и разделительных перегородок.
Контрольный список продукта
Товар | Описание | |
---|---|---|
Листы пенополиизоцианурата | Листы из вспененного полиизоцианурата лучше всего подходят для создания моделей без форм, где изоляция является важным фактором. Его легко разрезать и придать форму острым ножом и наждачной бумагой. Fiber Glast имеет как 2-фунтовые, так и 6-фунтовые разновидности.![]() | |
Полиуретановая смесь и пена для заливки | Эта пенная смесь поставляется в наборе из двух частей, который создает систему с закрытыми ячейками, то есть отдельные ячейки пены улавливают воздух и не пропускают жидкости. После отверждения этой пене можно придать форму и вырезать ее для изготовления форм. Fiber Glast имеет варианты весом 2 и 6 фунтов. | |
Серая грунтовка для поверхностей | Duratec Surfacing Primer обеспечивает быстрое отверждение даже при нанесении тонких слоев.Он отличается высокой температурой теплового искажения и легко шлифуется до зеркального блеска класса А. | |
Разделительный воск | Partall Paste Wax — это не содержащий силикона зеленый воск, специально разработанный для создания прочной, долговечной и блестящей поверхности. Он будет предлагать отличные характеристики выпуска.![]() | |
PVA | PVA, или поливиниловый спирт, сочетается с разделительным воском, чтобы создать легкое разделение для форм.PVA устойчив к растворителям в любой системе смол, но он растворим в воде. Его нельзя использовать с продуктами, выделяющими воду во время отверждения. | |
FibRelease | В качестве альтернативы разделительному воску и ПВА производители могут сэкономить время, деньги и силы с помощью FibRelease. FibRelease — это раствор на водной основе, не содержащий вредных растворителей, летучих органических соединений или силиконов. |
Для большинства форм, полиэфирная смола и 1.5 унций / кв. футов мата из рубленого волокна дают удовлетворительные результаты. Прочность и толщину формы можно увеличить быстрее, добавив тканый ровинг или инструментальную ткань. В случае форм из полиэстера первым шагом в изготовлении формы является нанесение гелевого покрытия для инструментов, которое отличается ярко-оранжевым или глубоким черным цветом. Перед нанесением обязательно нанесите гелькоут в нужном соотношении. Для достижения наилучших результатов гелькоут для оснастки следует распылять на заглушку с помощью пистолета для гелькоута за три прохода от семи до восьми мил каждый, нарастая до общей толщины 20-25 мил.
Поверхностное покрытие должно быть стабилизировано начальным слоем мата в течение полутора-пяти часов, чтобы предотвратить усадку гелевого покрытия или отрывание поверхности заглушки. Нанесите слой смолы на поверхность и положите мат в смолу. Используя щетинную щетку, нанесите смолу на мат, придавая мату различные контуры вилки. Нанесение мазка гораздо эффективнее рисования, поскольку длинные мазки тянут коврик.
Все воздушные карманы должны быть обработаны так, чтобы мат плотно прилегал к поверхности пробки и был равномерно пропитан смолой.Пузырьки воздуха и сухие участки будут казаться молочными на фоне гелевого покрытия инструмента. Используйте валик со щетиной, чтобы выдавить воздушные карманы из мата, и валик для насыщения с канавками, чтобы уплотнить ламинат. Следите за тем, чтобы волокна не перекрывали (поднимались) на острых углах и в текстурированных областях. Любые пузырьки воздуха, оставшиеся после геля из смолы, необходимо аккуратно вырезать с помощью острого канцелярского ножа и наклеить на место спичку.
После того, как начальный слой затвердеет, слегка отшлифуйте его для подготовки к нанесению дополнительных слоев, следуя той же процедуре, что и с начальным слоем.В большинстве форм используется 8-10 слоев, но не следует наносить более трех-четырех слоев за раз, чтобы минимизировать тепловыделение (экзотермический эффект). После третьего слоя мата можно добавить слой тканого ровинга или инструментальной ткани для более быстрого наращивания толщины. Как правило, пресс-форма должна быть как минимум в два раза больше толщины детали, которую она должна изготовить.
Дайте готовой форме высохнуть в течение как минимум 24 часов, прежде чем пытаться удалить. Любые опорные конструкции должны быть прикреплены к задней части формы до ее отсоединения от заглушки. Отжимные клинья могут быть вставлены по периметру формы, между формой и заглушкой, и постепенно вставлены на место. Клинья для впрыска воздуха, которые прикрепляются к воздушному компрессору, можно использовать для разделения устойчивых участков.
После освобождения формы смойте остатки разделительного состава теплой водой и осмотрите поверхность. Любые дефекты необходимо зачистить и отремонтировать. После этого вы готовы начать подготовку формы для производства деталей.
Контрольный список продукта
Товар | Описание | |
---|---|---|
Полиэфирная смола | Для большинства форм полиэфирная смола дает удовлетворительные результаты. Полиэфирные смолы дешевле, чем альтернативы, при этом обладают умеренными прочностными свойствами и просты в обращении. | |
Мат из рубленого волокна | Мат из рубленых прядей чаще всего используется для придания толщины деталям между слоями ткани.![]() | |
Тканый ровинг | Тканый ровинг обеспечивает недорогое средство ламинирования больших площадей в процессе создания формы. Волокна объединяются в теплые и заполняющие нити, которые проходят под углом 0 и 90 градусов, обеспечивая твердую прочность в двух направлениях для готовой детали. | |
Гель-покрытие для инструментов | Обладая характерным ярко-оранжевым или глубоким черным цветом, гелькоуты для инструментальной оснастки представляют собой стойкие к истиранию гелевые покрытия для изготовления форм, где ключевыми факторами являются сохранение блеска, твердость, устойчивость к образованию трещин и минимальное искажение. | |
Пистолеты для гелькоута | Пистолеты можно использовать для эффективного распыления гелькоутов, ПВА и разделительной пленки, а также широкого выбора грунтовок.![]() | |
Выжимные клинья | Разъединяющие клинья можно использовать для снятия формы с заглушки, избегая при этом ненужного повреждения поверхности формы. Клинья для впрыска Iar могут использоваться для разделения особо устойчивых участков. |
Обслуживание пресс-формы
Фото предоставлено IStock Photo. Перед тем, как какую-либо деталь можно будет изготовить в новой форме, ее необходимо отшлифовать и отполировать до класса «А». Постепенно смачивайте форму наждачной бумагой с зернистостью 400, 600 и, наконец, 1000. Не забудьте сменить воду в ведре и промыть поверхность формы при переходе на более тонкую бумагу, чтобы не осталось более крупной зернистости. Для полировки Fiber Glast Development Co. рекомендует использовать двухступенчатую полировальную пасту и высокоскоростной буфер. Первый этап удаляет шлифовальные царапины, а второй полирует поверхность до желаемого результата.
После полировки формы нанесите на нее смазку, следуя процедурам, описанным для подготовки пробки. На новую форму часто наносят дополнительный слой разделительного агента в качестве дополнительной страховки. Если деталь не высвобождается должным образом и повреждает форму, потребуется ремонт. Любой незакрепленный или поврежденный материал необходимо удалить шлифованием или шлифованием, и на эту область следует нанести новый инструментальный гель-слой. Слой ПВА или вощеной бумаги, наложенный поверх ремонта, будет необходим для надлежащего отверждения.После отверждения ремонт можно отшлифовать и отполировать, как описано ранее.
Контрольный список продукта
Товар | Описание | |
---|---|---|
Наждачная бумага | Новые формы требуют гладкой поверхности или отделки класса «А», чтобы их можно было использовать при создании деталей.![]() | |
Двухступенчатая полировка для пресс-форм | После шлифовки вам необходимо отполировать форму, чтобы удалить все шлифовальные царапины, появившиеся после очистки наждачной бумагой. Двухступенчатая полировальная паста обеспечит впечатляющий блеск, в то время как ее состав разработан для производителей, которым требуется только половина материала других полировальных смесей |
Особенности конструкции пресс-формы
Формы для многокомпонентных изделий
В некоторых случаях форма пробки может потребовать составной формы, так что форма может быть снята с пробки, а последующие части удалены из формы.При изготовлении многокомпонентной формы начните с создания временной перегородки на заглушке вдоль желаемой линии разъема. Эта плотина может быть построена из мазонита или подобного материала и удерживаться на месте с помощью глины. На той части, которую нужно формовать в первую очередь, необходимо сохранить острый угол без радиуса. К разделительной перемычке должны быть добавлены установочные шпонки или дюбели для перестановки деталей формы. При использовании форм, состоящих из нескольких частей, сконструируйте всю форму перед тем, как снимать какую-либо часть формы, чтобы избежать проблем с переналадкой.После того, как первая часть формы застынет, удалите временную перегородку и используйте готовую часть фланца, чтобы сформировать разделительную перегородку для следующей половины. Нанесите разделительный состав на эту поверхность, прежде чем продолжить конструирование формы.
Альтернативные методы строительства
Если прочность и стабильность размеров являются важными факторами в конструкции пресс-формы, вместо полиэфирной смолы можно использовать эпоксидную смолу. Процедура для этого во многом такая же, как и с полиэфирной смолой, за исключением того, что мат нельзя использовать с эпоксидной смолой, поскольку связующее, которое скрепляет мат, несовместимо с эпоксидными смолами. Начните с ткани весом 2–4 унции, чтобы минимизировать сквозные отпечатки узора. Затем перейдите на ткань плотностью 7-10 унций. Обязательно разместите несколько слоев под углом 45 градусов для хорошей жесткости. Для достижения наилучших результатов эпоксидные покрытия следует нанести щеткой на заглушку. Поскольку эпоксидные смолы менее склонны к усадке, чем полиэфирные материалы, немедленное нанесение стабилизирующего армирующего слоя на поверхностное покрытие не является критическим.
Если требуются исключительно жесткие формы, вместо стеклоткани можно использовать углеродное волокно.Мы рекомендуем использовать эпоксидную смолу с углеродным волокном, а гибкий резиновый ракель лучше всего подходит для распределения смолы по ткани.
Контрольный список продукта
Товар | Описание | |
---|---|---|
Эпоксидная смола | При работе с формой, требующей повышенной прочности и стабильности размеров, обычно рекомендуются эпоксидные смолы.![]() | |
Стекловолокно | Рубленый мат нельзя использовать с эпоксидной смолой из-за несовместимости продукта. По этой причине рекомендуется начать с более легкой ткани, например, ткани весом 2–4 унции, а затем перейти на более плотную ткань. | |
Ткань из углеродного волокна | Ткань из углеродного волокна может использоваться почти так же, как стекловолокно при создании вашей формы.Изготовители обычно выбирают углеродное волокно, когда их форма требует исключительной жесткости. | |
Ракели | При конструировании формы важно сохранить и равномерно распределить смолу по всей ткани. Такие инструменты, как гибкий резиновый ракель, помогут равномерно распределить ткань по поверхности, сводя к минимуму возможные осложнения.![]() |
Выбор материалов для формования деталей
После того, как форма будет должным образом отполирована и покрыта разделительным составом, можно приступать к изготовлению деталей! Первым этапом процесса формования деталей является определение того, какая смола и арматура будут использоваться.Обсудив ранее достоинства трех основных смол, мы сосредоточимся на особенностях выбора арматуры.
После выбора типа армирования наиболее важными факторами являются выбор стиля (переплетения) и веса ткани, наиболее подходящей для конкретного применения. Три основных стиля ткани — это полотняное переплетение, саржевое переплетение и атласное переплетение. Кроме того, стекловолокно доступно в унциях на квадратный ярд, за исключением мата, который выражается в унциях на квадратный фут.
Когда ткань ткется, волокна скручиваются в пряжу под углом 0 (основная пряжа) и 90 (пряжа наполнителя). В простом переплетении используется узор «сверху-снизу», в то время как при атласном переплетении одна пряжа с наполнителем плавает над тремя-семью нитями основы перед сшиванием под другой нитью основы, а саржевое переплетение — это узор «2×2». Обычное переплетение — наименее дорогостоящие и хорошие ткани общего назначения, но они не обладают такой же прочностью, как атласное и саржевое переплетение, но одинаково прочны во всех направлениях.
Чем легче ткань, тем легче она будет драпироваться по контурам и тем меньше смолы потребуется для ее смачивания. Легкие ткани чаще всего используются для отделки поверхностей и хобби для радиоуправления (R / C). При ремонте и пошиве чаще всего используются ткани средней плотности. Самые тяжелые ткани обычно используются для быстрого наращивания толщины, например, для изготовления корпусов лодок и форм. Ткани продаются на складах, как правило, шириной 38, 50 и 60 дюймов, хотя не все ткани будут доступны со всей этой шириной.Для данного проекта выберите ширину, которая максимально приближена к ширине детали, которую нужно сделать. Идея состоит в том, чтобы использовать как можно меньше отдельных кусков ткани для каждого слоя. Необходимое количество смолы будет зависеть от веса выбранной ткани. Соотношение ткани и смолы для большинства тканых стекловолокон и Kevlar® составляет примерно 50:50, а углеродного волокна — 60:40. Мат из стекловолокна потребует примерно вдвое больше смолы, чем тканый стекловолокно для надлежащего насыщения. Дополнительную прочность можно придать деталям за счет конструкции сэндвич-сердечника.Этот процесс включает использование материала сердцевины, такого как бальзовое дерево с торцевыми волокнами, пенополиуретан, виниловая пена или соты, между двумя слоями ламината. Некоторые материалы сердцевины бывают разной толщины в зависимости от потребностей конкретного применения. Прочность и жесткость детали можно значительно увеличить, добавив к ней очень небольшой дополнительный вес.
Процесс изготовления
Фото предоставлено IStock Photo. Выбрав ткань и смолу, вы готовы приступить к лепке детали.Как указывалось ранее, при первом использовании формы добавьте дополнительное покрытие разделительного агента, чтобы обеспечить надлежащее разделение. Пока разделительный состав высыхает, найдите время, чтобы обрезать арматуру до нужного размера и количества частей и сложить стопку рядом с рабочей зоной. Если вы используете коврик, вместо того, чтобы разрезать его, разорвите его на куски подходящего размера. Изношенные края деталей будут смешиваться друг с другом при помещении в форму, обеспечивая более прочное соединение, чем при стыковании двух обрезанных краев. В случае тканых материалов определите, где должна быть наибольшая прочность детали, и соответствующим образом сориентируйте волокна.При использовании тканей с полотняным переплетением более равномерная прочность может быть достигнута путем чередования ориентации волокон от 0/90 до 45/45 градусов.
Процесс изготовления детали аналогичен этапам изготовления пресс-формы. При работе с охватывающей формой начните с нанесения соответствующего поверхностного покрытия на поверхность формы. Этот шаг не является абсолютно необходимым при изготовлении деталей, но гораздо лучший косметический вид готовой детали будет достигнут, если он будет использоваться. Нанесение первого слоя смолы и ткани непосредственно на поверхность формы может привести к неровностям поверхности, проколам и сквозной печати рисунка тканевого переплетения, если используется более тяжелая ткань.Эти недостатки можно исправить после того, как деталь будет извлечена из формы, но для этого потребуется утомительное шлифование и заполнение. Использование легкой ткани, например, двух или четырех унций, в качестве первого слоя может свести к минимуму эти проблемы, если не используется гелькоут или поверхностное покрытие. В качестве альтернативы гелевому покрытию грунтовку Duratec Surfacing Primer можно распылить в форму, обеспечивая прочную отделку поверхности.
Гель-коуты из полиэстера бывают белого или прозрачного цвета, которые окрашены в различные цвета.Прозрачные гелькоуты очень точно воспроизводят цвета, а белые гелькоуты дают пастельные тона. Поверхность эпоксидной смолы белого цвета, также может быть пигментирована.
Контрольный список продукта
Товар | Описание | |
---|---|---|
Полиэфирные гелькоуты | Полиэфирные гелевые покрытия отличаются высокой прочностью и обычно считаются отраслевым стандартом при формовании.Fiber Glast имеет белый, прозрачный и нейтральный цвет геля. | |
Эпоксидные покрытия поверхности | Это эпоксидное покрытие, предназначенное для создания прочной и прочной поверхности на узорах, приспособлениях и эпоксидных формах, легко наносится и распределяется по детализированным поверхностям, не задерживая пузырьков воздуха. | |
Duratec Surfacing Primer | Duratec Surfacing Primer обеспечивает быстрое отверждение даже при нанесении тонких слоев.Он отличается высокой температурой теплового искажения и легко шлифуется до зеркального блеска класса А. |
При нанесении гелькоута на форму наилучшие результаты будут достигнуты при распылении неразбавленного гелькоута с помощью пистолета-распылителя, почти таким же образом, как гелькоут на оснастке наносится в конструкции формы. Медленно нанесите гелькоут за три прохода до толщины 15-20 мил. Измеритель толщины гелькоута — лучший инструмент для определения толщины.Проверьте несколько мест на детали, чтобы убедиться, что слой наносится ровно. Слишком много или слишком мало на некоторых участках может вызвать образование складок или деформацию при застывании гелькоута. При использовании эпоксидного покрытия поверхность следует нанести щеткой в форму.
Придерживаясь указаний в разделе о конструкции пресс-формы на белой бумаге, нанесите гелькоут с начальным стабилизирующим слоем армирования. Если вы пигментировали гелькоут и хотите, чтобы он был одинакового цвета по всей детали, смолу также можно пигментировать.
При укладке армирования старайтесь использовать один неразрезанный кусок ткани для каждого слоя. К сожалению, это не всегда возможно. Иногда часть слишком велика, чтобы ее можно было покрыть одним куском ткани, поэтому необходимо использовать два или более куска. Когда две отдельные детали должны быть соединены вместе в форме, лучше всего перекрывать их на полдюйма или один дюйм, а не стыковать детали более жестко. Соединяйте две детали вместе, чтобы получился шов, только если необходимо поддерживать постоянную толщину.
Фото предоставлено IStock Photo. Контуры и формы детали также могут затруднить получение хорошей адгезии при использовании одного куска ткани. В частности, проблемы такого рода представляют вмятины и острые углы. Композитам можно придавать самые разные формы, но очень трудно получить острые углы (90 градусов и более) с непрерывными кусками ткани. Ткань будет подниматься в этих местах, что приводит к образованию пузырьков воздуха и слабых мест в ламинате.Если в детали требуется острый угол, лучший способ приблизиться к нему — это соединить вместе два отрезанных куска ткани на повороте. Для дополнительной прочности стыковых соединений смешайте небольшое количество смолы с измельченными стекловолокнами, чтобы получить структурный шпатлевочный наполнитель. Нанесите его на шов перед тем, как положить на ткань. В случае углублений лучше вырезать меньший кусок ткани, чтобы он соответствовал углублению, чем пытаться вдавить в него более крупный кусок ткани.
Как и в случае с пресс-формой, используйте валики и ракель для тщательного пропитывания ткани, вытесните воздушные карманы из ламината и максимально уплотните слои.Это поможет избежать слабых мест и проблем с расслоением готовой детали. Поскольку слои армирования помещаются в форму, обратите внимание на ориентацию волокон при использовании тканого полотна, чередуя ориентацию слоев, чтобы увеличить прочность детали.
Если планируется использовать многослойную конструкцию сердечника, определите, какой тип материала сердечника лучше всего подходит для данной области применения. Пенополиуретан очень жесткий и плохо повторяет контуры, в то время как пенополиуретан можно нагреть и придать ему самые разные формы.Бальза, которая обычно состоит из небольших блоков волокон на концах, скрепленных холстом ткани, может иметь мягкие изгибы. Материалы сотового заполнителя очень гибкие и могут принимать самые разные формы.
Необходимо предпринять несколько шагов для подготовки материала сердцевины, чтобы получить прочную деталь. После вырезания и придания формы сердцевине материала контурам детали скосите края сердцевины по периметру под углом 45 градусов, чтобы сгладить переход ткани. Смешайте часть смолы со стеклянными микросферами до консистенции суспензии и используйте ее для заполнения любых зазоров, а также для сращивания нескольких частей или материала сердцевины вместе.Предварительно обработайте пенопласты с открытыми ячейками и сотовые заполнители этой суспензионной смесью, чтобы заполнить открытые ячейки чем-то более легким, чем чистая смола. Как только эти шаги будут завершены, сердечник можно прикрепить на место.
При работе с многокомпонентными формами почти всегда собирайте детали формы перед тем, как собирать деталь. Укладка детали, а затем сборка деталей формы затруднит получение хорошей связи между деталями и гладкой косметической отделки. Исключением из этого правила будет закрытый предмет, такой как топливный бак, который было бы невозможно складывать, если бы форма была собрана заранее.
Если используется пресс-форма, другая половина пресс-формы может быть прижата к первой половине после того, как все армирующие слои будут на своих местах. Если пресс-форма не используется, но желательна гладкая поверхность с обеих сторон детали, поверх последнего слоя армирования можно нанести поверхностное покрытие. Когда ламинат достигнет стадии «кожистого» полуотверждения, обрежьте края острым канцелярским ножом. Выполнение этого сейчас значительно сократит время чистовой обработки и позволит сократить образование пыли в будущем.
После того, как деталь затвердела, выньте ее из формы почти так же, как она была снята с заглушки. Любые остатки разделительного агента можно смыть с детали и обработать любым способом. Отделка обычно включает шлифование швов и шлифовку краев детали.
Осмотрите форму на предмет повреждений или потускнения поверхности формы. Если все в порядке, повторно нанесите агент выпуска, когда будете готовы построить следующую деталь.Если требуется ремонт или полировка, выполните эти операции, как описано выше.
Тщательно следуя рекомендациям в этом и других наших официальных документах, вы можете производить формы и готовые детали, которые соответствуют вашим ожиданиям или превосходят их. Если что-то пойдет не так, можно устранить практически любые повреждения или проблемы. Помните, что работа с композитами похожа на любой другой новый навык, который вы изучаете: чем больше вы над этим работаете и оттачиваете свои способности, тем лучше будут результаты.После того, как вы освоите основы, а затем отточите эти навыки, станет возможным практически все.
DIY Лист стекловолокна | Тест Flite
Предупреждение: в этой статье подробно описано использование опасных веществ. Прочтите все инструкции к материалам, которые вы используете, и придерживайтесь их. Они могут отличаться от материалов, которые я использовал. Несмотря на то, что я не ношу перчатки в процессе, я предлагаю вам сделать это, так как стекло рамки может иметь острые края, и вы не хотите, чтобы смола попала на руки.
Я собираюсь начать сборку своего Tricopter v2.5, и как бы сильно я не хотел покупать обрезные доски Davids с ЧПУ, я подумал, что попробую сделать свою собственную.
К сожалению, я не могу найти легкодоступный лист стекловолокна, поэтому делаю свой собственный. Эта статья предназначена для тех, кто также хотел бы сделать свою собственную плиту из стекловолокна и отметить, что ее конечное использование не ограничивается только сборками Tricopter.
Необходимые материалы и инструменты:
Это список всего, что вам понадобится, чтобы сделать свой собственный лист из стекловолокна.
- Смола и активатор из стекловолокна
- Ткань / мат из стекловолокна (я предпочитаю внешний вид тканой ткани, а не мат)
- 2 стеклянные панели больше, чем размер листа, который вы хотите (достаньте их из дешевых рам для картин в магазине со скидками )
- Лезвия для бритв / универсального ножа
- Прямоугольник и обрамляющий квадрат
- Маркер Sharpie
- Скребок для краски
- Малярная кисть (дешевые — вы не сможете использовать ее повторно)
- Малярный валик (тоже дешевый)
- Палочки для весла
- Старая стеклянная чашка / банка
- Автомобильный воск (например, черепаший воск)
- Старая футболка / полотенце
- Что-то тяжелое (например,грамм. Пластины со штангой 2,5-5 кг)
Разложите ткань FG на плоской чистой поверхности, по которой вы можете разрезать. Используя маркер Sharpie, отметьте квадратным или прямым краем, как вы собираетесь резать его. Так как это ламинированный лист, я вырезал половину кусков по одной линии с листом, а вторую половину под углом 45 градусов к нему. Для рамы трикоптера я делаю лист размером 120 x 170 мм, это дает мне некоторое пространство, чтобы края ткани двигались на этапе сборки.Будьте осторожны при перемещении ткани, так как она очень хрупкая.
Примечание. Обязательно мойте руки после работы с тканью, так как волокна очень раздражают глаза и другие чувствительные части тела.
Используя прямую кромку, чтобы удерживать ткань (это не позволяет ножу испортить переплетение), аккуратно вырежьте куски.
После того, как вы вырежете все части, сложите их в две стопки. Один для квадратной ориентации, а другой для 45deg.
Подготовьте форму для остекления
Если вы ее уже сделали, вам нужно будет удалить излишки смолы со стороны стекла, на котором вы будете строить доску.С помощью лезвия универсального ножа соскребите всю старую смолу, чтобы поверхность стала гладкой и чистой.
После того, как поверхности станут гладкими и чистыми, пора надеть вашего Karate Kid и сказать: «Нанесите воск, удалите воск!»
Равномерно нанесите воск на обе части стекла, затем отполируйте.
Воск на …
Воск на …
Собираем вместе
Для 7-слойного листа размером 120 мм x 170 мм потребуется примерно 100 мл стекловолоконной смолы.Чтобы измерить его, я наполнил старый стакан 100 мл воды и отметил внешнюю сторону, затем вылил воду и полностью высушил стакан. Это позволило мне наполнить мой старый стакан 100 мл смолы.
Осторожно: Следующие шаги следует выполнять в хорошо вентилируемом помещении / на открытом воздухе. Смешайте смолу, как указано на упаковке.
Примечание. В более жарком климате вам потребуется меньше активатора, чем в более холодных.
Используя дешевую кисть, нанесите толстый слой на нижнюю панель вашей «формы» на область, чуть большую, чем ваша ткань FG.(Для перемешивания использовалась лопаточная палочка)
Работая разумно быстро, но не торопясь, начинаем укладывать ткань. Сначала я использую одну из моих 45-градусных деталей.
Нанесите еще немного смолы поверх этого, но не чистите его, используя вытирающие движения, чтобы убедиться, что вы не двигаете плетение.
Выдавите пузырьки воздуха из волокон с помощью малярного валика. Возможно, вам придется добавить еще немного смолы, так как валик немного заберет ее.
Повторите описанный выше процесс, укладывая каждый слой. Если вы решите использовать две разные ориентации плетения, обязательно чередуйте ориентацию между слоями. например 45 градусов — квадрат — 45 градусов — квадрат — …
После того, как вы положили и свернули каждый из слоев, у вас должно получиться нечто похожее на то, что показано ниже. Примерно через 10 минут сборки обратите внимание на то, как эпоксидная смола начала полимеризоваться (на это указывает изменение цвета). Смола также действует как растворитель на маркере и распределяет чернила вокруг 🙁
Чтобы сделать доску заданной толщины, используйте распорки по краю стеклянной панели.Например, палка для весла, изображенная ниже. В конце концов, я решил не использовать распорки.
Примечание: если вы хотите сделать доску сплошного цвета, попросите в магазине оборудования / краски смешать примерно 5% цветного пигмента через смолу.
Поместите вторую стеклянную панель, восковой стороной вниз, сверху и осторожно приложите несколько грузов, чтобы сжать все вместе (я использовал 7,5 кг). Затем оставьте на ночь, чтобы она застыла.
Извлечение из формы
После отверждения в течение ночи вы готовы снять лист FG со стекол.Для этого осторожно снимите одно из оконных стекол с помощью скребка. Будьте осторожны, медленно двигайтесь вперед, делая понемногу за раз. Используйте здесь слишком большое давление, и стекло наверняка расколется.
Затем вы можете использовать лезвие универсального ножа, чтобы начать поднимать лист с другой стеклянной панели.
После запуска вы можете вернуться к скребку для краски, чтобы быстро и легко удалить оставшуюся часть листа.
После того, как лист FG был снят со стекла, вы можете использовать свой универсальный нож и квадратный / прямой край, чтобы отрезать излишки смолы.Я рекомендую сделать несколько проходов с каждой стороны доски, прежде чем загибать пропил, чтобы отломать лишнее. Любые волокна, которые все еще удерживают доску, можно обрезать канцелярским ножом.
Возможно, стоит дать ему отвердеть в течение еще 24 часов после извлечения из формы, чтобы доска приобрела максимальную прочность, прежде чем вы станете ее обрабатывать или подвергнете ее испытаниям в воздухе.