Как сделать шестерню своими руками из металла: Как сделать шестерню своими руками из металла. Изготовление пластиковой шестерни (обучающий видео урок) Как сделать шестеренку из пластика своими руками
Как сделать шестерню своими руками из металла. Изготовление пластиковой шестерни (обучающий видео урок) Как сделать шестеренку из пластика своими руками
Для изготовления шестерен используют такие материалы: железо, чугун, бронза, сталь простая углеродистая, специальные составы стали с примесью хрома, никеля, ванадия. Помимо металлов применяют смягчающие материалы: кожу, фибру, бумагу, они смягчают и обесшумливают зацепление. Но и металлические шестерни могут работать бесшумно, если их профиль выполнен с точностью. Для грубых передач производят «силовые» зубчатые колеса, их изготовляют литьем из чугуна и стали без последующей обработки. «Рабочие» зубчатые колеса для быстроходных передач изготовляются на фрезерных или зуборезных станках, с последующей термической обработкой – цементацией, которая предает зубьям твердость и устойчивость к износу. После цементации шестерни подвергаются обработке на шлифовальных станках.
Метод обката
Метод обката самый распространённый вариант изготовления шестерен, так как этот способ наиболее технологичный.
Метод обката с использованием долбяка
Для изготовления шестерен используется зубодолбёжный станок со специальным долбяком (шестерня оснащенная режущими кромками). Процедура изготовления шестерен происходит в несколько этапов, так как срезать за один раз весь лишний слой металла не возможно. При обработке заготовки, долбяк выполняет возвратно-поступательное движение и после каждого двойного хода, заготовка и долбяк проворачиваются на один шаг, как бы «обкатываются» друг по другу. Когда заготовка шестеренки сделает полный оборот, долбяк выполняет движение подачи к заготовке. Этот цикл производства выполняется, пока не будет удалён весь необходимый слой металла.
Метод обката с использованием гребёнки
Гребенка — режущий инструмент, его форма аналогична зубчатой рейки, но одна сторона зубьев гребенки заточена. Заготовка изготавливаемой шестерни производит вращательное движение вокруг оси. А гребёнка выполняет поступательное движение перпендикулярно оси шестерни и возвратно-поступательное движение параллельного оси колеса (шестеренки). Таким образом гребенка снимает лишний слой по всей ширине обода шестерни. Возможен другой вариант движения режущего инструмента и заготовки шестерни относительно друг друга, например, заготовка выполняет сложное прерывистое движение, скоординированное с движением гребенки, как будто совершается зацепление профиля нарезаемых зубьев с контуром режущего инструмента.
Этот метод позволяет изготовить шестерню при помощи червячной фрезы. Режущим инструментом в данном методе служит червячная фреза, которая совместно с заготовкой зубчатого колеса производят червячное зацепление.
Одна впадина шестеренки нарезается дисковой или пальцевой фрезой. Режущая часть фрезы, выполненная в виде формы этой впадины, нарезает шестерню. А при содействии делительного устройства нарезаемая шестеренка поворачивается на один угловой шаг и процесс нарезания повторяется.
Горячее и холодное накатывание
В этом способе производства шестерен применяется зубонакатный инструмент, который нагревает определенный слой заготовки до пластического состояния. После этого, нагретый слой деформируют для получения зубьев. А далее обкатывают зубья, изготавливаемого зубчатого колеса, до приобретения ними точной формы.
Изготовление конических шестерен
Для изготовления конических колес (конических шестеренок) применяют вариант обкатки в станочном зацеплении заготовки с воображаемым производящим колесом. Режущие кромки инструмента в процессе главного движения срезают припуск, таким образом, образовывают боковые поверхности будущей шестерни (шестеренки).
В сегодняшнее время, вокруг нас работают очень много механизмов где используются пластмассовые шестеренки. Причем, это могут быть как и игрушечные машинки, так и вполне серьезные вещи, к примеру, антенный подъемник в автомобиле, редуктор спиннинга, и тп. Причины поломки шестеренок могут быть разные, конечно большинство из них связаны с неправильной эксплуатацией, но сейчас не об этом. Если уж вы попали в такую ситуацию и у вас сломало пару зубьев шестерни, то выход есть как не платить за дорогостоящую деталь, а восстановить ее простым способом.
Понадобится для восстановления
- Ненужная зубная щетка.
- Моющее средство.
- Двухкомпонентный эпоксидный клей — холодная сварка для пластика.
Восстановление пластмассовой шестеренки
Подготовка
Первомым делом необходимо подготовить поверхность шестеренки. Промываем ее многократно в теплой воде с моющим средством, активно работая зубной щеткой.
После того как обезжировка проведена, высушите ее насухо.
Готовим клей
Теперь подготовим клей. Смешаем на небольшом кусочке картона компоненты в пропорции как в инструкции. Хорошо перемешаем.Вообще, перед открыванием клея, рекомендую тщательно ознакомиться с его инструкцией, особенно с временем полного и частичного затвердевания, так как у разных производителей эти данные могут кардинально отличаться.
Если консистенция получилась жидкая — дайте ей немного постоять, пока она начнет отвердевать.
Восстановление зубьев
В моем случае сточено несколько зубьев, ситуация исправима. Мажем клей на то место, которое нужно восстановить. Клей должен быть очень густым, но пластичным.Делаем такой своеобразный бугорок.
Кладем шестеренку на импровизированную подставку, для того чтобы клей ещё больше загустел. Все опять же индивидуально, мне понадобилось лично минут 20, чтобы консистенция заметно загустела.

Ускорить реакцию и уменьшить время загустения можно нагреванием. К примеру взять фен и начать нагревать клей на шестеренке.
Восстановление зубьев
Теперь самый ответственный момент — прокатка зубьев. Узел где эксплуатировалась шестерня, а именно другая шестеренка с которой непосредственно контактировала наша сломанная, нужно обильно смазать смазкой, солидолом или литолом.Устанавливаем сломанную шестерню и прокатываем несколько раз по другой.
В результате другая шестеренка прокатает след на густом клее.
Теперь вы понимаете, что прежде чем прокатывать зубья, эпоксидный клей на шестеренке должен затвердеть до консистенции твердого пластилина.
Благодаря смазке клей не прилипнет на другую шестеренку.
Затвердевание
Аккуратно извлекаем восстановленную делать из механизма и оставляем ее для окончательного затвердевания, обычно на сутки.Вот таким несложным способом можно довольно просто восстановить сломанные шестерни.

Чем заменить эпоксидный клей?
Если вы не нашли клей, я могу вам порекомендовать сделать немного похожий состав.Для этого понадобится:
- Эпоксидная смола с отвердителем.
- Цемент сухой.
В пропорции указанной в инструкции, смешиваем компоненты для получения нужного количества клея. Добавляем цемент. Только не цементно-песчаную смесь, а именно чистый цемент. Пропорции примерно два к одному. То есть две части клея и одна цемента. И все очень тщательно перемешиваем. Клей готов, а дальше все как по инструкции выше.
Постарался изложить максимально простым языком.
Недавно друг, который занимался продажей шоколадных фонтанов в Питере обратился с необычным предложением. Ему вернули фонтан, где не крутился винт, поднимающий шоколад. Я люблю подобные задачи, когда мало кто может (или хочет браться) за

После разборки стало ясно, что дело в редукторе. Одна шестерня буквально расплавилась на валу (качество компонентов было просто на высоте. Скорей всего шестерня проскальзывала долгое время, потом нагрелась. Фонтан выключили, шестерня снова прилипла к валу со смещенным центром. Потом его снова включили и несколько зубъев, не выдержав нагрузки, отломилось). Точно такую же шестерёнку не найти, поэтому из оказавшегося под боком оборудования решил изготовить новую.
Вариантов создания шестерёнок очень много, я расскажу лишь про один из них. На мой взгляд он самый простой и эффективный.
Шаг 1. Разработка чертежа шестерни
Вам понадобится:
- любой векторный редактор
- штангенциркуль
- генератор шестеренок (я использовал этот онлайн сервис)
Итак, считаем количество зубцов поломавшейся шестерни. Вводим все параметры, проводим замеры.
Качаем файл чертёж. Внутреннюю звёздочку я чертил сам в кореле, т.к. нужного параметра не нашел.
Шаг 2. Изготовление шестерни
Материал новой шестерни — прозрачное оргстекло. Просто ищете в поисковике лазерную резку в вашем городе и отправляетесь туда. Лучше нарезать несколько с разными параметрами сразу. Думаю, одна порезка как у меня не должна выйти более $ 6.
Шаг 3. Запуск и тест фонтана
Вообще соседние шестерни принято делать из материалов немного разной плотности. Так они дольше прослужат. Скорей всего производитель просто пренебрег этим.
Смазываем, запускаем, радуемся!
Удачи в вашем труде!
Как сделать шестерню своими руками из металла. Как сделать шестерню своими руками из металла Как изготовить маленькие шестерни самостоятельно
В сегодняшнее время, вокруг нас работают очень много механизмов где используются пластмассовые шестеренки.
Понадобится для восстановления
- Ненужная зубная щетка.
- Моющее средство.
- Двухкомпонентный эпоксидный клей — холодная сварка для пластика.
Восстановление пластмассовой шестеренки
Подготовка
Первомым делом необходимо подготовить поверхность шестеренки.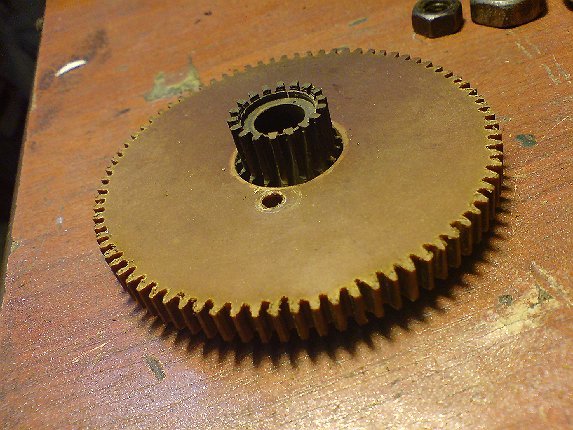
После того как обезжировка проведена, высушите ее насухо.
Готовим клей
Теперь подготовим клей. Смешаем на небольшом кусочке картона компоненты в пропорции как в инструкции. Хорошо перемешаем.Вообще, перед открыванием клея, рекомендую тщательно ознакомиться с его инструкцией, особенно с временем полного и частичного затвердевания, так как у разных производителей эти данные могут кардинально отличаться.
Если консистенция получилась жидкая — дайте ей немного постоять, пока она начнет отвердевать.
Восстановление зубьев
В моем случае сточено несколько зубьев, ситуация исправима. Мажем клей на то место, которое нужно восстановить. Клей должен быть очень густым, но пластичным.Делаем такой своеобразный бугорок.
Кладем шестеренку на импровизированную подставку, для того чтобы клей ещё больше загустел.

Ускорить реакцию и уменьшить время загустения можно нагреванием. К примеру взять фен и начать нагревать клей на шестеренке.
Восстановление зубьев
Теперь самый ответственный момент — прокатка зубьев. Узел где эксплуатировалась шестерня, а именно другая шестеренка с которой непосредственно контактировала наша сломанная, нужно обильно смазать смазкой, солидолом или литолом.Устанавливаем сломанную шестерню и прокатываем несколько раз по другой.
В результате другая шестеренка прокатает след на густом клее.
Теперь вы понимаете, что прежде чем прокатывать зубья, эпоксидный клей на шестеренке должен затвердеть до консистенции твердого пластилина.
Благодаря смазке клей не прилипнет на другую шестеренку.
Затвердевание
Аккуратно извлекаем восстановленную делать из механизма и оставляем ее для окончательного затвердевания, обычно на сутки.
Вот таким несложным способом можно довольно просто восстановить сломанные шестерни.
Чем заменить эпоксидный клей?
Если вы не нашли клей, я могу вам порекомендовать сделать немного похожий состав.Для этого понадобится:
- Эпоксидная смола с отвердителем.
- Цемент сухой.
Данный материал есть общее руководство по проектированию и печати на послойном 3D-принтере пластиковых шестеренок.
Выключатель света на шестеренках — хитрый пример того, что можно будет спроектировать самостоятельно после прочтения этой статьи.
Оптимальные материалы для пластиковых шестеренок
Какой же материал самый лучший? Короткий ответ в плане качества готовых шестеренок выглядит следующим образом:
Nylon (PA) > PETG > PLA > ABS
- Пожалуйста, обратите внимание, на лицензию «Только для личного пользования», т.е. результат нельзя распространять, продавать, менять и т.д.
- В собранном виде конструкция имеет 15,87 см в диаметре. Самая большая напечатанная деталь — 14,92 см в диаметре
Распечатайте все детали с не менее чем 3 периметрами по всем сторонам и снизу, 15% заполнения. Рекомендуем толщину слоя не более 0,3 мм. Работать будет любой материал — пока удастся избежать перекосов деталей, что приведет устройство в негодность.
Деталь ручки — единственная, для которой потребуются поддержки.
Инструкция по сборке (прочесть до начала работы)
- Почистите с помощью лезвия зубцы шестеренок, чтобы они хорошо совмещались, затем установите их на пластину с тем же направлением вращения, в котором они печатались (штырек центральной шестеренки справа, зацепка ведомой — сверху по центру).
- Закрепите основную шестеренку, попав штырьками в отверстия.
- Нанесите немного сухого клея (хорошо подойдет клеящий карандаш) на рабочий конец рычага и установите рычаг с той стороны, с которой он совпадает по штырькам. Клей нужен для того, чтобы закрепить рычаг на штырьки. Рычаг также прижимает к конструкции основную шестеренку.
- Нагрейте и размягчите зажимы. Этого довольно, чтобы их раскрыть. Выровняйте края зажимов по отверстиям с задней стороны пластины и обожмите шестеренку по кругу. (Отверстия на обороте пластины могут потребовать чистки — нож в помощь, все зависит от того, насколько хорош у вас принтер). Прижимайте зажимы до застывания. Это гарантирует, что все будет надежно держаться.
Особые преимущества послойной печати и примеры использования шестеренок
Итак, в чем же преимущество 3D-печати шестеренок перед традиционными методами их изготовления, и насколько прочными получаются шестеренки?
Напечатанные пластиковые шестеренки дешевы, процесс быстр, можно без труда получить специализированный результат. Сложные шестеренки и 3D-вариации печатаются без проблем. Процесс прототипирования и создания проходит быстро и чисто. Самое главное то, что 3D-принтеры достаточно распространены, так что набор STL-файлов из интернета может обеспечить тысячи людей.
Конечно, печатать шестеренки распространенным пластиком — это компромисс по качеству поверхности и износостойкости, если сравнивать с литыми или обработанными пластиковыми шестернями. Но если правильно все спроектировать, напечатанные шестеренки могут оказаться достаточно эффективным и разумным вариантом, а для некоторых решений — идеальным.
Большинство рабочих приложений выглядят наподобие редуктора , как правило, для небольших электродвигателей, ручек и заводных ключей. Это потому, что электродвигатели отлично работают на высоких скоростях, но у них возникают проблемы с резким снижением оборотов, и обойтись без шестереночной передачи в таком случае проблематично. Вот примеры:
Специфические проблемы послойной печати
- Напечатанные шестеренки перед использованием обычно требуют небольшой постобработки.
Будьте готовы к «червоточинам» и к тому, что зубцы нужно будет обработать лезвием.
Уменьшение диаметра центрального отверстия — очень распространенная беда даже на дорогих принтерах. Это результат множества факторов. Отчасти это — температурное сжатие охлаждающегося пластика, отчасти — потому что отверстия проектируются в виде многоугольников с большим числом углов, которые стягиваются по периметру отверстия. (Всегда экспортируйте STL-файлы шестеренок с большим числом сегментов).
Слайсеры тоже вносят свой вклад, поскольку некоторые из этих программ могут выбирать разные точки для обхода отверстий. Если внутренний край отверстия будет рисовать внутренний край экструдируемого пластика, то реальный диаметр отверстия будет иметь небольшую усадку, и чтобы в это отверстие потом что-нибудь вставить, может понадобиться определенное усилие. Так что слайсер может вполне намеренно делать отверстия меньше.
Кроме того, любое расхождение слоев или расхождение по ширине предполагаемого и реального экструдирования могут оказывать довольно заметный эффект, «уплотняя» отверстие.
Бороться с этим можно, например, моделируя отверстия диаметром примерно на 0,005 см больше. По аналогичным причинам, и чтобы напечатанные шестеренки помещались друг рядом с другом и могли работать, рекомендуется оставлять в модели зазор между зубцами примерно в 0,4 мм. Это некоторый компромисс, зато напечатанные шестеренки не будут застревать.
- Другая распространенная проблема — получить сплошное заполнение, что довольно трудно для маленьких шестеренок. Щели между маленькими зубчиками — довольно обычное явление, даже если в слайсере выставлено заполнение 100%.
Некоторые программы относительно успешно справляются с этим в автоматическом режиме, а вручную решить эту проблему можно, увеличив перекрытие слоев. Эта задача отлично задокументирована на RichRap, и в блоге приведены различные ее решения.
- Тонкостенные детали получаются хрупкими, нависающие части нуждаются в подпорках, прочность детали значительно меньше по оси Z. Рекомендуемые для печати шестеренок настройки не отличаются от обычных.
На основе уже проведенных тестов можно порекомендовать прямоугольное заполнение и не менее 3 периметров. Желательно также печатать как можно более тонким слоем — насколько позволяет оборудование и терпение, потому что тогда зубцы получаются более гладкими.
- Однако же, пластик недорог, а время дорого. Если проблема критична или нужно заменить огромную сломавшуюся шестерню, можно печатать и сплошным заполнением, чтобы не оставить шанса на какую-нибудь другую засаду, кроме износа.
Наиболее распространенные причины отказа напечатанных шестеренок
- Стачивание зубцов (от длительного использования, см. Шаг 10 про смазку).
- Проблемы с насаживанием на ось (см. Шаг 7 про насаживание).
- Поломка тела или спицы (это редкие поломки, которые возникают обычно, если шестеренка плохо напечатана, с недостаточным заполнением, например, или спроектирована со слишком тонкими спицами).
О важности эвольвенты
Плохой способ изготовления шестеренок
Довольно часто в любительских сообществах можно встретить неправильно спроектированные шестеренки — моделирование шестеренок дело не такое уж и простое. Как нетрудно догадаться, плохо спроектированные шестеренки плохо сцепляются, имеют избыточное трение, давление, отдачу, неравномерную скорость вращения.
Эвольвента (инволюта) — это определенного рода оптимальная кривая, описываемая по какому-либо контуру. В технике эвольвенту окружности используют как профиль зубца для колес зубчатой передачи. Это делается для того, чтобы скорость вращения и угол сцепления оставались постоянными. Хорошо разработанный набор шестеренок должен передавать движение исключительно через вращение, с минимальным проскальзыванием.
Моделирование эвольвентной шестеренки с нуля — дело довольно нудное, так что перед тем, как за него браться, имеет смысл поискать шаблоны. Ссылки на некоторые из них будут даны ниже.
Тонкости моделирования зубца. Оптимальное количество зубцов
Подумайте вот о чем: если вам нужно передаточное число 2:1 для линейного механизма — сколько зубцов должно быть на каждой шестеренке? Что лучше — 30 и 60, 15 и 30 или 8 и 17?
Каждое из этих соотношений даст один и тот же результат, но комплект шестеренок в каждом случае будет при печати сильно отличаться.
Большее количество зубцов дает более высокий коэффициент сцепления (количество одновременно зацепленных зубцов) и обеспечивает более плавное вращение. Увеличение количества зубцов приводит к тому, что каждый из них должен быть меньше — чтобы уместиться на тот же диаметр. Мелкие зубцы более хрупкие, их сложнее точно напечатать.
С другой стороны, уменьшение количества зубцов дает больше объема для увеличения прочности.
Печатать на 3D-принтере меленькие шестеренки — это как раскрашивать в раскраске тонкие линии толстой кисточкой. (Это на 100% зависит от диаметра сопла и разрешения принтера по горизонтальной плоскости. Разрешение по вертикали не играет роли в ограничении по минимальным размерам).
Если вы хотите испытать свой принтер в деле печатания мелких шестеренок, можете воспользоваться этим STL:
Протестированный нами принтер все выполнил на высшем уровне, но при диаметре от примерно полудюйма зубцы стали выглядеть как-то подозрительно.
Совет заключается в том, чтобы делать зубцы как можно больше, избегая при этом предупреждения от программы о слишком малом их количестве, а также избегая пересечений.
Есть еще один момент, на который следует обратить внимание при выборе количества зубцов: простые числа и факторизация.
Числа 15 и 30 оба делятся на 15, так что при таком количестве зубцов на двух шестеренках одни и те же зубцы будут постоянно встречаться друг с другом, образуя точки износа.
Более правильное решение — 15 и 31. (Это ответ на вопрос в начале раздела).
При этом не соблюдается пропорция, зато обеспечивается равномерный износ пары шестеренок. Пыль и грязь будут распределяться по всей шестеренке равномерно, износ тоже.
Опыт показывает, что лучше всего, если соотношение количества зубцов двух шестеренок лежит в интервале примерно от 0,2 до 5. Если требуется большее передаточное число, лучше добавить в систему дополнительную шестеренку, иначе может получиться механический монстр.
Мало зубцов — это сколько?
Такую информацию можно найти в каком-нибудь Справочнике механика. 13 — минимальная рекомендация для шестеренок с углом давления 20 градусов, 9 — рекомендованный минимум для 25 градусов.
Меньшее число зубцов нежелательно, потому что они будут пересекаться, что ослабит сами зубцы, да и в процессе печати придется решать проблему перекрытия.
Тонкости моделирования зубца. Угол давления, и Как сделать прочные зубцы
Угол давления 15, угол давления 35
Угол давления? Зачем мне это знать?
Это угол между нормалью к поверхности зубца и диаметром окружности. Зубцы с большим углом давления (более треугольные) прочнее, но хуже сцепляются. Их проще печатать, но при работе они создают высокую радиальную нагрузку на несущую ось, издают больше шума и склонны к отдаче и проскальзыванию.
Для 3D-печати хорошим вариантом является 25 градусов, что обеспечивает плавную и эффективную передачу в шестернях размером с ладонь.
Что еще можно сделать для укрепления зубцов?
Просто сделайте шестерню толще — это, очевидно, укрепит и зубцы. Удвоение толщины дает удвоение прочности. Хорошее общее правило гласит: толщина должна быть от трех до пяти раз больше шага зацепления шестеренки.
Прочность зубца шестеренки можно приблизительно оценить, если рассматривать его как небольшую консольную балку. При таком подходе ясно, что добавление перекрывающей сплошной стенки для уменьшение неподдерживаемой площади значительно укрепляет прочность зубцов шестеренок. В зависимости от применения, такая техника расчетов может быть использована также для уменьшения числа точек зацепления.
Методы крепления на ось
Тугая насадка на ось с насечками. Этот самый простой метод встречается не слишком часто. Здесь надо быть внимательным со перекосом пластика, что с течением времени ухудшит передачу момента. Такая конструкция является также неразборной.
Ось на фиксирующем винте в плоскости шестерни. Фиксирующий винт проходит сквозь шестерню и упирается в плоский участок на оси. Фиксирующий винт обычно направляется непосредственно в тело шестерни или через утопленную гайку через квадратное отверстие. У каждого метода есть свои риски.
Если направлять винт напрямую, можно сорвать хрупкую пластиковую резьбу. Метод с утопленной гайкой решает эту проблему, но, если не проявить достаточно аккуратности и приложить при креплении слишком большое усилие, тело шестерни может сломаться. Делайте шестерню потолще!
Добавление специальных ввинчивающихся термовставок, существенно улучшит прочность насадки на ось.
Утопленный шестигранник — шестиугольная врезка, в которой сидит шестиугольная гайка под шестиугольный винт. Вокруг шестиугольника нужно напечатать достаточно сплошных слоев, так чтобы винту было за что держаться. При этом тоже полезно использовать фиксирующий винт, особенно если речь идет о высоких оборотах.
Клин встречается в мире любительской 3D-печати нечасто.
Ось как единое целое с гайкой. Такое решение хорошо противостоит нагрузкам на скручивание. Его, однако, очень трудно добиться на принтере, потому что шестерни приходится печатать перпендикулярно к поверхности стола, а любые оси при таком решении имеют слабое место по оси Z, что проявляется при высоких нагрузках.
Некоторые типы шестеренок
Внешние и внутренние прямозубые шестерни, параллельные спиральные (косозубые), двойные спиральные, реечные, конические, винтовые, плосковершинные, червячные
Спиральное зубчатое колесо (елочка). Его обычно можно увидеть в экструдерах принтеров, они сложны в работе, но имеют свои преимущества. Они хороши большим коэффициентом сцепления, самоцентровкой и самовыравниванием. (Самовыравнивание бесит, потому что отражается на работе всей конструкции). Этот тип шестеренок также непрост в изготовлении на обычном оборудовании, вроде любительских принтеров. 3D-печать знает значительно более простые методы.
Червячная шестерня. Легко моделируется, есть большой соблазн ее использовать. Следует отметить, что передаточное число такой системы равно числу зубцов шестеренки, поделенному на количество проемов червяка. (Надо посмотреть с торца червяка и посчитать количество начинающихся спиралей. В большинстве случаев получается от 1 до 3).
Реечная шестерня. Преобразует вращательное движение в линейное и наоборот. Здесь речь идет не о вращении, а о расстоянии, которое проходит рейка с каждым поворотом вала шестерни. Тут очень просто вычислять плотность зубцов: надо лишь умножить их плотность на рейке на пи и на диаметр шестерни. (Или умножить количество зубцов на рейке на плотность зубцов на шестерне).
Смазка 3D-напечатанных шестеренок
Если устройство работает при малых нагрузках, на малых скоростях и частотах, о смазке пластиковых шестеренок можно не беспокоиться. Но если нагрузки высоки, то можно попробовать продлить срок службы, смазывая шестерни и уменьшая трение и износ. В любом случае все функции шестеренок более эффективны при наличии смазки, а сами шестерни служат дольше
Для таких объектов, как шестеренки экструдера 3D-принтера, можно порекомендовать плотную смазку. Для этого отлично подойдут литол, PTFE или смазки на силиконовой основе. Смазку надо наносить, слегка протирая деталь туалетной бумагой, чистым бумажным полотенцем или не пыльной тканью, равномерно распределяя лубрикант, несколько раз провернув шестеренку.
Любая смазка лучше, чем никакой, но надо убедиться в ее химической совместимости с данным пластиком. А еще всегда надо помнить, что смазка WD-40 — отстой. Хотя она и прилично чистит.
Инструментарий для изготовления шестеренок
Высококачественные шестеренки можно делать на одних лишь бесплатных программах. То есть, существуют платные программы для очень оптимизированных и совершенных шестереночных соединений, с тонко настраиваемыми параметрами и оптимальной производительностью, но от добра добра не ищут. Просто надо сделать так, чтобы в одном и том же механизме использовались шестеренки, изготовленные одним и тем же инструментом, чтобы соединения сцеплялись как надо. Шестеренки лучше моделировать парами.
Вариант 1. Найти имеющуюся модель шестеренки, модифицировать или масштабировать ее под свои нужды. Вот перечень баз данных, где можно найти готовые модели шестеренок.
- McMaster Carr : обширный массив 3D-моделей, проверенных решений
- GrabCAD : гигантская база данных присланных пользователями моделей .
- GearGenerator.com генерирует SVG-файлы прямозубых шестеренок (Эти файлы могут быть конвертированы в импортируемые . Впрочем, некоторые программы, такие как Blender, умеют импортировать SVG напрямую, без танцев с бубнами).
- https://inkscape.org/ru/ — бесплатная программа векторной графики с интегрированным генератором шестеренок. Приличное руководство по созданию шестеренок на Inkscape — и .
Редакторы STL-файлов
Большинство генераторов шаблонов шестеренок дают на выходе STL-файлы, что может раздражать, если вам требуются особенности, которых генератор не предлагает. STL-файлы — это PDF мира 3D, они изощренно сложны для редактирования, однако редактирование возможно.
TinkerCAD. Хорошая элементарная браузерная CAD-программа, простая и быстрая в освоении, одна из немногих программ 3D-моделирования, которая умеет модифицировать STL-файлы. www.Tinkercad.com
Meshmixer. Хорошая программа для масштабирования исходных форм. http://meshmixer.com/
Не-FDM 3D-печать
Большинство людей, даже убежденные любители, не имеют непосредственного доступа к другим технологиям 3D-печати для изготовления шестеренок. Между тем такие сервисы существуют и могут помочь.
SLA — отличная технология для профессионального прототипирования шестеренок. Печатаемые слои не видны, в результате процесса можно получать очень мелкие детали. С другой стороны, детали получаются дорогими и несколько хрупкими. Если вы используете этот процесс для прототипирования будущей литой модели, проблем с ее извлечением не возникнет. Делайте деталь сплошной, а то она непременно сломается!
SLS — очень точный процесс, в результате которого получаются прочные детали. Технология не требует подпорок для нависающих структур. Можно создавать сложные и подробные изделия, лучше со стенками толщиной до четверти дюйма. Слои печати также почти невидимы… НО, шершавая поверхность (потому что технология основана на порошковой печати) крайне склонна к износу. Требуется очень мощная смазка, и многие вообще не рекомендуют SLS-шестеренки для приложений длительного пользования.
Технология BinderJet хороша для детализированных и точных многоцветных декоративных или не конструкционных деталей. Подойдет для получения деталей безумных цветов, впрочем, очень хрупких и зернистых, так что это не то, что требуется для функциональных шестеренок.
Здравствуйте уважаемые посетители. Предлагаем Вам ознакомиться с обучающим видео уроком по изготовление пластиковой шестерни. Как Вы знаете многие шестерни в бытовой и офисной техники изготавливаются из пластика, а так же происходит поломка данной шестеренки. Вы сможете узнать как сделать новую по образцу которая имеется.
В этом уроке Вы узнаете как изготовить сломанную шестеренку из кухонного комбайнера. Как Вы понимаете такие шестеренки не возможно купить в магазинах, в ремонтных мастерских могут просто не найти подходящую шестеренку. Изготовление металлической шестеренки будет дороговато для данной модели кухонного комбайна.
Для создания новой пластиковой шестеренки, нам нужно использовать сломанную часть, но в начале нам необходимо будет её склеить. При собрании сломанной шестеренки, у нас могут возникнуть не большие трудности — это появление небольших дефектов, возможно не доставание мелки деталей.
Все это склеиваем обычным суперклеем, так как в сверхпрочности нам нет никакой необходимости. Нужно сделать все имеющие детали в одно подобие шестеренки. При склеивании мы видим небольшие дефекты которые имеются у нас. Мелкие части просто разлетелись, когда сломалась шестеренка. Соответственно нам необходимо будет все восполнить и все это будет делать воском. Заполняем все там где не достают данные детальки, кусочки пластика воском и до моделируем так как у нас выглядела бы не достающая деталька. Если эта часть детали выпуклая то будем моделировать как выпуклая, а если плоская то как плоская.
При восстановлении шестеренки нужно постараться сделать таким каким он был изначально кухонном комбайне. Конечно при выполнении воском мы не сможем сделать точную копию шестеренки, но постараемся сделать более или менее точную копию. При использовании таких шестеренок в кухонных комбайнах, там нет таких сверх точный посадок, так как постоянно снимается и одевается.
Данный процесс моделирования воском занимает в среднем пару часов. После моделирования до нужного состояния можно смело приниматься к процессу изготовление пластиковой шестерни. В обучающем видео Вы сможете более подробно посмотреть весь процесс создания такой шестеренки. Желаем Вам удачи.
Одной из самых сложных и, тем не менее, распространенных механических систем является зубчатая передача. Это отличный способ передачи механической энергии из одного места в другое и способ увеличения или уменьшения мощности (крутящего момента), а также увеличения или уменьшения скорости чего-либо.
Как сделать шестеренку своими руками? Проблема всегда заключаются в том, что для создания эффективных зубчатых колес требуется достаточно много навыков рисования и знание математики, а также умение создавать сложные детали.
Для любительского нет необходимости иметь максимальную эффективность, поэтому мы можем получить намного более легкую в изготовлении систему, даже с подручными инструментами.
Шестерня — это ряд зубьев на колесе. (Обратите внимание на диаграмму выше, они пометили неправильное количество зубьев на шестернях — извините)
Шаг 1: Формулы и расчеты
Формулы для рисования и изготовления зубьев зубчатых колес в избытке можно найти в интернете , но для новичка они кажутся очень сложными.
Я решил упростить задачу, и решение очень хорошо работает как в больших, так и в малых масштабах. В небольших масштабах это лучше всего подходит для машинной резки с помощью лазерных резаков, например, очень маленькие зубчатые колеса могут быть успешно изготовлены таким образом.
Шаг 2: Простой способ
Итак, форма зубца, если говорить просто, может представлять собой полукруг.
Шаг 3: Определяем размеры
Теперь мы можем определить параметры, чтобы сделать шестерню:
- Насколько большими / маленькими будут зубья шестерни (диаметр) — чем меньше шестерня, тем меньше должны быть зубья.
- Все зубья, которые собираются в сцепление (соединяются), должны быть одинакового размера, поэтому сначала нужно рассчитать меньшую шестерню.
Давайте начнем с зубьев размером 10 мм.
Я хочу шестерню с 5 зубьями, чтобы круг был 10х10 мм (в окружности) = 100 мм.
Чтобы нарисовать этот круг, мне нужно найти диаметр, поэтому я использую математику и калькулятор и делю окружность (100 мм) на Pi = 3,142.
Это дает мне диаметр 31,8 мм, и я могу нарисовать этот круг с помощью циркуля, а затем нарисовать с помощью циркуля на его окружности ровно 10 кругов диаметром 10 мм.
Если у вас есть такая возможность, то проще сделать все с помощью программного обеспечения для рисования. Если вы используете программное обеспечение, вы должны иметь возможность вращать круги зубьев вокруг основного круга, и вам нужно будет знать, как далеко повернуть каждый зуб. Это легко рассчитать: делите 360 градусов на количество кругов. Таким образом, для наших 10 кругов 360/10 = 36 градусов для каждого зуба.
Шаг 4: Делаем зубчатую форму
Удалите верхнюю часть одного круга и нижнюю часть следующего круга. Чтобы сделать это, у вас должно быть четное количество зубьев
У нас есть первая шестерня. Она может быть вырезана из дерева или металла с помощью базовых подручных инструментов, пил и напильников.
Этот процесс легко повторить для любого количества шестеренок, которое вам нужно. Держите размер круга по образцу, и они будут соответствовать друг другу.
Шаг 5: Получите шестерёнку
Поскольку такие полукруглые шестеренки легко вырезать, вы можете сделать их с помощью подручного инструмента и лобзика или пилы.
Раньше я делал шаблон из 9 или 10 зубьев на фанере и использовал его в качестве ориентира для моего ручного фрезера и без проблем вырезал шестерни.
Если у вас есть доступ к лазерному резцу, они могут быть вырезаны из акрила 3 или 5 мм толщины и быть очень маленьких размеров.
Здравствуйте) Сегодня, в процессе размышлений над смыслом всего сущего, я задался вопросом изготовления зубчатой рейки в домашних условиях. Я думаю некоторые уже сталкивались с этой проблемой — найти готовую зубчатую рейку весьма трудно, а выпиливать каждый зуб натфилем дело очень муторное (выдержать постоянный профиль и шаг довольно сложно). Конечно если модуль зуба не сликом мал, а длина рейки необходима небольшая, то можно и поморочится)) Но что делать если модуль например 0,5 мм (высота зуба 1,125 мм) и менее, а длина относительно большая? В серийном производстве такие рейки изготовляют на зубофрезерных или зубодолбежных станках (иногда штамповкой), в единичном на универсальных фрезерных станках пальцевой или дисковой профилированной фрезой. Для домашних условий предлагаю следующий способ (наверное для многих это не будет новостью, но может быть кому-то пригодится).
Итак, у нас имеется зубчатое колесо (m=0,35мм; высота зуба соответственно h=0,7875мм)
К сожалению будет необходимо кое чем пожертвовать((Жертвой выступит любое другое колесо с таким же модулем (Ну или хотя бы близким к нему). Диаметр здесь особой роли не играет, главное соответствие модуля. Вот две жертвы.
Проверяем. Подходят идеально)
Далее заготовка для будущей рейки, ею послужила пластина из часового механизма (хорошо видно, что на ней я уже тренировался).
Отжигаем ее и закрепляем в тисках.
Далее чеканим ее нашей жертвой. Для начала легкими ударами молотка по шестерне делаем метки.
Ну а потом лупим что есть мочи! неспеша и аккуратно вычеканиваем на высоту зуба.
Шаг при этом будет совпадать идеально. Профиль, конечно, не совершенен, но не думаю, что такой метод будет использован для реек в каких-нибудь очень ответственных механизмах))
После того, как мы прочеканили заготовку на необходимую глубину, дорабатываем натфилем. В результате получаем участок с профилем очень даже неплохого качества)
Контроль.
После этого можно спокойно вырезать саму рейку с уже готовым профилем)) Таким образом можно получать мелкомодульные рейки из нетвердых металлов. Было потрачено: две шестеренки, пол-часа времени (+ два эксперемента). Спасибо за внимание)
Изготовление шестерен — как легко сделать шаблон?
Одной из самых сложных и, тем не менее, распространенных механических систем является зубчатая передача. Это отличный способ передачи механической энергии из одного места в другое и способ увеличения или уменьшения мощности (крутящего момента), а также увеличения или уменьшения скорости чего-либо.
Как сделать шестеренку своими руками? Проблема всегда заключаются в том, что для создания эффективных зубчатых колес требуется достаточно много навыков рисования и знание математики, а также умение создавать сложные детали.
Для любительского нет необходимости иметь максимальную эффективность, поэтому мы можем получить намного более легкую в изготовлении систему, даже с подручными инструментами.
Шестерня — это ряд зубьев на колесе. (Обратите внимание на диаграмму выше, они пометили неправильное количество зубьев на шестернях — извините)
Шаг 1: Формулы и расчеты
Формулы для рисования и изготовления зубьев зубчатых колес в избытке можно найти в интернете, но для новичка они кажутся очень сложными.
Я решил упростить задачу, и решение очень хорошо работает как в больших, так и в малых масштабах. В небольших масштабах это лучше всего подходит для машинной резки с помощью лазерных резаков, например, очень маленькие зубчатые колеса могут быть успешно изготовлены таким образом.
Шаг 2: Простой способ
Итак, форма зубца, если говорить просто, может представлять собой полукруг.
Шаг 3: Определяем размеры
Теперь мы можем определить параметры, чтобы сделать шестерню:
- Насколько большими / маленькими будут зубья шестерни (диаметр) — чем меньше шестерня, тем меньше должны быть зубья.
- Все зубья, которые собираются в сцепление (соединяются), должны быть одинакового размера, поэтому сначала нужно рассчитать меньшую шестерню.
Давайте начнем с зубьев размером 10 мм.
Я хочу шестерню с 5 зубьями, чтобы круг был 10х10 мм (в окружности) = 100 мм.
Чтобы нарисовать этот круг, мне нужно найти диаметр, поэтому я использую математику и калькулятор и делю окружность (100 мм) на Pi = 3,142.
Это дает мне диаметр 31,8 мм, и я могу нарисовать этот круг с помощью циркуля, а затем нарисовать с помощью циркуля на его окружности ровно 10 кругов диаметром 10 мм.
Если у вас есть такая возможность, то проще сделать все с помощью программного обеспечения для рисования. Если вы используете программное обеспечение, вы должны иметь возможность вращать круги зубьев вокруг основного круга, и вам нужно будет знать, как далеко повернуть каждый зуб. Это легко рассчитать: делите 360 градусов на количество кругов. Таким образом, для наших 10 кругов 360/10 = 36 градусов для каждого зуба.
Шаг 4: Делаем зубчатую форму
Удалите верхнюю часть одного круга и нижнюю часть следующего круга. Чтобы сделать это, у вас должно быть четное количество зубьев
У нас есть первая шестерня. Она может быть вырезана из дерева или металла с помощью базовых подручных инструментов, пил и напильников.
Этот процесс легко повторить для любого количества шестеренок, которое вам нужно. Держите размер круга по образцу, и они будут соответствовать друг другу.
Шаг 5: Получите шестерёнку
Поскольку такие полукруглые шестеренки легко вырезать, вы можете сделать их с помощью подручного инструмента и лобзика или пилы.
Раньше я делал шаблон из 9 или 10 зубьев на фанере и использовал его в качестве ориентира для моего ручного фрезера и без проблем вырезал шестерни.
Если у вас есть доступ к лазерному резцу, они могут быть вырезаны из акрила 3 или 5 мм толщины и быть очень маленьких размеров.
Отливаем самодельную шестерню из алюминия вместо пластмассовой
Данный мастер-класс научит вас делать копии несложных деталей из алюминия. В нашем случае сломалась приводная шестеренка для откатных ворот. В заводском исполнении она сделана из пластика. Ей и займемся.
Нам понадобятся:
- Секундный клей.
- Пластилин.
- Желатин.
- Глицерин.
- Воск.
- Гипс.
- Самоклеящийся уплотнитель.
- Алюминий (в виде любого ненужного лома).
Все необходимое покупается в хозяйственном, продуктовом и строительном магазинах. Стоит не дорого и всегда есть в наличии. Из инструментов и прочего нужны различные металлические емкости или кастрюли, газовая плита и горн.
Процесс изготовления
Приступим к самому процессу. Берем части расколотой шестеренки и склеиваем секундным клеем.
Все технические полости в ней заполняем пластилином, чтобы проще было отливать деталь.
Затем высыпаем в кастрюлю желатин и разбавляем его глицерином. Растапливаем на водной бане до однородной массы. Когда желатин готов, помещаем деталь в небольшую емкость и заливаем получившейся массой.
Даем некоторое время на застывание. Далее делаем небольшие надрезы, чтобы извлечь шестерню. Первая форма готова.
Теперь необходимо расплавить воск и отлить из него деталь.
Когда деталь готова обязательно сравните ее размер с исходной.
У нас вышла чуть меньше, чем должна быть. Вопрос был решен оконным уплотнителем. Нужно наклеить его на зубья шестерни и срезать лишнее.
Дальше повторяем предыдущие шаги. Плавим желатиновую форму и опять заливаем деталь, извлекаем ее и заливаем воск. Теперь получилось точно по размеру.
Следующим шагом разводим гипс и в металлической емкости и заливаем им деталь из воска. Даем гипсу застыть и прокаливаем емкость в горне, чтобы убрать из нее воск.
Мы пробовали выплавить воск из гипса в духовке, но до конца это сделать не получилось, что плохо сказалось на качестве конечной детали.
Когда гипсовая форма готова, плавим алюминий в горне.
Расплавленный метал заливаем в гипс, охлаждаем в воде и получаем готовую деталь.
В целом выглядит неплохо, но требует небольших доработок.
Для этого достаточно напильника и ножовки по металлу.
Токарный станок облегчит обработку, но его наличие не обязательно.
Все что осталось сделать после обработки детали, это установить шестерню на свое место.
Не забывайте смазывать движущиеся и трущиеся детали механизма. Так они прослужат намного дольше.
Важный момент! При заливке металла в гипсовую форму будьте предельно осторожны. Если гипс высох не до конца, то при сильном разогреве от заливаемого металла вода начнет быстро испаряться. Это приведет к тому, что форма начнет «плеваться» паром и мелкими капельками раскаленного метала.
Заключение
В наши дни зачастую используются пластиковые детали в высоконагруженных механизмах. Это хитрый маркетинговый ход, который вынуждает нас раскошелиться на дорогостоящие детали. Новая шестерня из алюминия проста в изготовлении, прослужит намного дольше и существенно сбережет ваш бюджет.
Смотрите видео
Шестеренка в домашних условиях. Как сделать шестерню своими руками из металла
Одной из самых сложных и, тем не менее, распространенных механических систем является зубчатая передача. Это отличный способ передачи механической энергии из одного места в другое и способ увеличения или уменьшения мощности (крутящего момента), а также увеличения или уменьшения скорости чего-либо.
Как сделать шестеренку своими руками? Проблема всегда заключаются в том, что для создания эффективных зубчатых колес требуется достаточно много навыков рисования и знание математики, а также умение создавать сложные детали.
Для любительского нет необходимости иметь максимальную эффективность, поэтому мы можем получить намного более легкую в изготовлении систему, даже с подручными инструментами.
Шестерня — это ряд зубьев на колесе. (Обратите внимание на диаграмму выше, они пометили неправильное количество зубьев на шестернях — извините)
Понадобится для восстановления
- Ненужная зубная щетка.
- Моющее средство.
- Двухкомпонентный эпоксидный клей — холодная сварка для пластика.
Клей холодная сварка должен быть жидкий, в тюбиках. Обязательно смотрите на упаковке, чтобы он подходил для склеивания пластмассовых и пластиковых деталей. Такой двухкомпонентный клей можно купить как в магазине автозапчастей, так и в строительном магазине. Если у вас возникнут затруднения и вы не сможете найти такой, в конце статьи я расскажу как сделать похожий аналог.
Восстановление пластмассовой шестеренки
Подготовка
Первомым делом необходимо подготовить поверхность шестеренки. Промываем ее многократно в теплой воде с моющим средством, активно работая зубной щеткой. Наша задача обезжирить и удалить смазку со всех граней. После того как обезжировка проведена, высушите ее насухо.
Готовим клей
Теперь подготовим клей. Смешаем на небольшом кусочке картона компоненты в пропорции как в инструкции. Хорошо перемешаем. Вообще, перед открыванием клея, рекомендую тщательно ознакомиться с его инструкцией, особенно с временем полного и частичного затвердевания, так как у разных производителей эти данные могут кардинально отличаться. Если консистенция получилась жидкая — дайте ей немного постоять, пока она начнет отвердевать.
Восстановление зубьев
В моем случае сточено несколько зубьев, ситуация исправима. Мажем клей на то место, которое нужно восстановить. Клей должен быть очень густым, но пластичным. Делаем такой своеобразный бугорок. Кладем шестеренку на импровизированную подставку, для того чтобы клей ещё больше загустел. Все опять же индивидуально, мне понадобилось лично минут 20, чтобы консистенция заметно загустела. Ускорить реакцию и уменьшить время загустения можно нагреванием. К примеру взять фен и начать нагревать клей на шестеренке.
Восстановление зубьев
Теперь самый ответственный момент — прокатка зубьев. Узел где эксплуатировалась шестерня, а именно другая шестеренка с которой непосредственно контактировала наша сломанная, нужно обильно смазать смазкой, солидолом или литолом. Устанавливаем сломанную шестерню и прокатываем несколько раз по другой. В результате другая шестеренка прокатает след на густом клее. Теперь вы понимаете, что прежде чем прокатывать зубья, эпоксидный клей на шестеренке должен затвердеть до консистенции твердого пластилина. Благодаря смазке клей не прилипнет на другую шестеренку.
Затвердевание
Аккуратно извлекаем восстановленную делать из механизма и оставляем ее для окончательного затвердевания, обычно на сутки. Вот таким несложным способом можно довольно просто восстановить сломанные шестерни.
Чем заменить эпоксидный клей?
Если вы не нашли клей, я могу вам порекомендовать сделать немного похожий состав. Для этого понадобится:
- Эпоксидная смола с отвердителем.
- Цемент сухой.
Покупаем обычную прозрачную или желтоватую эпоксидную смолу с отвердителем. Эти два компонента зачастую продаются вместе. В пропорции указанной в инструкции, смешиваем компоненты для получения нужного количества клея. Добавляем цемент. Только не цементно-песчаную смесь, а именно чистый цемент. Пропорции примерно два к одному. То есть две части клея и одна цемента. И все очень тщательно перемешиваем. Клей готов, а дальше все как по инструкции выше.
Здравствуйте) Сегодня, в процессе размышлений над смыслом всего сущего, я задался вопросом изготовления зубчатой рейки в домашних условиях. Я думаю некоторые уже сталкивались с этой проблемой — найти готовую зубчатую рейку весьма трудно, а выпиливать каждый зуб натфилем дело очень муторное (выдержать постоянный профиль и шаг довольно сложно). Конечно если модуль зуба не сликом мал, а длина рейки необходима небольшая, то можно и поморочится)) Но что делать если модуль например 0,5 мм (высота зуба 1,125 мм) и менее, а длина относительно большая? В серийном производстве такие рейки изготовляют на зубофрезерных или зубодолбежных станках (иногда штамповкой), в единичном на универсальных фрезерных станках пальцевой или дисковой профилированной фрезой. Для домашних условий предлагаю следующий способ (наверное для многих это не будет новостью, но может быть кому-то пригодится).
Итак, у нас имеется зубчатое колесо (m=0,35мм; высота зуба соответственно h=0,7875мм)
К сожалению будет необходимо кое чем пожертвовать((Жертвой выступит любое другое колесо с таким же модулем (Ну или хотя бы близким к нему). Диаметр здесь особой роли не играет, главное соответствие модуля. Вот две жертвы.
Проверяем. Подходят идеально)
Далее заготовка для будущей рейки, ею послужила пластина из часового механизма (хорошо видно, что на ней я уже тренировался).
Отжигаем ее и закрепляем в тисках. Далее чеканим ее нашей жертвой. Для начала легкими ударами молотка по шестерне делаем метки.
Ну а потом лупим что есть мочи! неспеша и аккуратно вычеканиваем на высоту зуба.
Шаг при этом будет совпадать идеально. Профиль, конечно, не совершенен, но не думаю, что такой метод будет использован для реек в каких-нибудь очень ответственных механизмах))
После того, как мы прочеканили заготовку на необходимую глубину, дорабатываем натфилем. В результате получаем участок с профилем очень даже неплохого качества)
Контроль.
После этого можно спокойно вырезать саму рейку с уже готовым профилем)) Таким образом можно получать мелкомодульные рейки из нетвердых металлов. Было потрачено: две шестеренки, пол-часа времени (+ два эксперемента). Спасибо за внимание)
Данный материал есть общее руководство по проектированию и печати на послойном 3D-принтере пластиковых шестеренок.
Выключатель света на шестеренках — хитрый пример того, что можно будет спроектировать самостоятельно после прочтения этой статьи.
Мешок шестеренок для ремонта игрушек
Приветствую! У вас есть дети? А игрушки, которым дети поломали шестеренки играя без пульта? Есть? То-то же
Тогда у меня для вас есть решение. Прошу под кат. Быстрообзор Предыстория. Ездил я когда-то в командировку и привез сыну игрушку с Р/У. Отдал, кстати, не мало денег т.к. это какой-то бренд был. Ребенку она сильно нравилась так что он ей играл постоянно и с пультом и без. Кстати вот и она. Правда симпатичная?
В один прекрасный день сломал зуб в шестерне. Ну и просит починить. Я тут уже думал на принтере ее печатать, но как оказалось там столько нюансов, что просто жуть. Не знаю в какой момент мне пришла в голову мысль поискать на али шестеренки, но я был поражен выбору. Пришлось разобрать машинку, найти нужную шестерню, пересчитать количество зубов, собрать и отдать хозяину
Вроде не так и много. Высыпаем и раскладываем. Я сделал несколько фото чтобы проще можно было разглядеть шестерни. Не получилось поймать так чтобы все было видно.
Мой вольный перевод: A — плотная посадка (-0.05 mm от диаметра) B — свободная посадка (+0.05 mm к диаметру) Диаметр шестерни: (Штук зубов+2) * модуль= Диаметр шестерни Модуль: 0.5 Внутреннее отверстие: 1.5/2/2.5/3 Шпиндельная шестерня(9 видов): 8-1.5A 9-2A 8-2A 10-2A 12-2A 14-2A 16-2A 18-2.5A 18-3A Корончатая шестерня(10 видов): C20-2.5A C20-2A C20-3A C2410-2A C2410-2B C2810-2B C28-2A C3010-2B C30-3A C3610-2B Одиночная шестерня(18 видов): 20-2A 26-2A 24-2.5A 28-2A 30-2A 36-2A 38-2A 38-3A 40-2A 42-2A 44-2A 44-2.5A 46-2.5A 48-2A 50-3A 52-2.5A 56-2A 56-3A Двойная шестерня(18 видов): 1810-2A 4812-2.5A 2210-2B 2410-2B 2610-2B 2808-2B 4610-2B 2810-2B 3010-2B 3210-2B 3212-2B 3412-2B 3610-2B 3808-2B 4410-2B 4810-2B 5010-2B 5610-2A Червячная шестерня(2 вида): 6 * 6-2A 6 * 8-2A Шестерня-шкив(1 вид): 6*6-2A
Я не спец в названиях шестеренок, но похоже что «Шпиндельная шестерня» это под напрессовку на ось. С остальными вроде все понятно. Так что если вам лень считать зубья — меряйте диаметр и считайте на калькуляторе
Ладно, мы тут машинку собирались чинить Переворачиваем и крутим 6 саморезов:
Открывается богатый внутренний мир, и крутим еще 6 винтов:
А я то думал что шестеренки посыплются.
Отпаиваем провода и аккуратно отщелкиваем защелки. Наконец-то видим шестерни:
Минус моторчик:
А вот и та самая шестерня.
Ищем такую же новую:
Китаец не обманул — она таки есть в мешке
Плюсы:
— Ребенок изучил внутренний мир машинки — Понял что лучше не возить туда-сюда машинку на Р/У — Помог крутить винты и весело провел время — Папа сэкономил на новой машинке
Минусы:
— не обнаружено
Подводя итог хотелось бы показать что можно не выбрасывать старые вещи, порой их ремонт не стОит дорого и приносит еще и пользу. Спасибо что дочитали, и не ломайтесь
Оптимальные материалы для пластиковых шестеренок
Какой же материал самый лучший? Короткий ответ в плане качества готовых шестеренок выглядит следующим образом:
Nylon (PA) > PETG > PLA > ABS
- Пожалуйста, обратите внимание, на лицензию «Только для личного пользования», т.е. результат нельзя распространять, продавать, менять и т.д.
- В собранном виде конструкция имеет 15,87 см в диаметре. Самая большая напечатанная деталь — 14,92 см в диаметре
Распечатайте все детали с не менее чем 3 периметрами по всем сторонам и снизу, 15% заполнения. Рекомендуем толщину слоя не более 0,3 мм. Работать будет любой материал — пока удастся избежать перекосов деталей, что приведет устройство в негодность.
Деталь ручки — единственная, для которой потребуются поддержки.
Инструкция по сборке (прочесть до начала работы)
- Почистите с помощью лезвия зубцы шестеренок, чтобы они хорошо совмещались, затем установите их на пластину с тем же направлением вращения, в котором они печатались (штырек центральной шестеренки справа, зацепка ведомой — сверху по центру).
- Закрепите основную шестеренку, попав штырьками в отверстия.
- Нанесите немного сухого клея (хорошо подойдет клеящий карандаш) на рабочий конец рычага и установите рычаг с той стороны, с которой он совпадает по штырькам. Клей нужен для того, чтобы закрепить рычаг на штырьки. Рычаг также прижимает к конструкции основную шестеренку.
- Нагрейте и размягчите зажимы. Этого довольно, чтобы их раскрыть. Выровняйте края зажимов по отверстиям с задней стороны пластины и обожмите шестеренку по кругу. (Отверстия на обороте пластины могут потребовать чистки — нож в помощь, все зависит от того, насколько хорош у вас принтер). Прижимайте зажимы до застывания. Это гарантирует, что все будет надежно держаться.
Шестерёнка своими руками
«Копался» в интернете и ни где не нашёл как можно сделать шестерёнку без компьютерных программ и станков.
Оказалось всё просто. У любого мастера под рукой найдётся:
кусок фанеры, карандаш, линейка, ножовка по металлу или лобзик (у меня циркулярная пила в помощь), 2 сверла (у меня 8 и 3 мм), диск пилы или отрезной диск по камню (главное, что бы были зубцы), ручная или электрическая дрель, напильник с крупной насечкой.
Для начала возьмём квадратный кусок фанеры, найдём середину проведя 2 диагонали.
Накладываем пильный диск так, что бы зубцы совпадали с диагоналями
И сверлим отверстия выбрав «шаг» для будущих зубцов шестерни.
Рассверлим полученные отверстия до 8 мм. и с помощью лобзика (я делал на циркулярке) выпилим правильный круг.
Нанесём линии проходящие через центр круга, соединяя противоположные стороны 8и мм. отверстий и выпилим заштрихованные сектора.
С помощью лобзика или циркулярки подравняем полученные зубцы до нужной длинны.
Нанеся линии (чёрные) на полученную заготовку, подрезаем зубцы шестерни.
Далее подработав напильником получаем готовый продукт
Так же мне нужна ещё и маленькая шестерёнка, для «привода». Её я делал аналогично большой, но использовал отрезной круг по камню.
Если большая шестерня у меня на 20 зубьев, то малая на 9 зубьев. Определив центра на основании получил шестерёнчатую передачу, которую собираюсь употребить в другом изделии. Удачи в делах и изысканиях!
Становитесь автором сайта, публикуйте собственные статьи, описания самоделок с оплатой за текст. Подробнее здесь.
Особые преимущества послойной печати и примеры использования шестеренок
Итак, в чем же преимущество 3D-печати шестеренок перед традиционными методами их изготовления, и насколько прочными получаются шестеренки?
Напечатанные пластиковые шестеренки дешевы, процесс быстр, можно без труда получить специализированный результат. Сложные шестеренки и 3D-вариации печатаются без проблем. Процесс прототипирования и создания проходит быстро и чисто. Самое главное то, что 3D-принтеры достаточно распространены, так что набор STL-файлов из интернета может обеспечить тысячи людей.
Конечно, печатать шестеренки распространенным пластиком — это компромисс по качеству поверхности и износостойкости, если сравнивать с литыми или обработанными пластиковыми шестернями. Но если правильно все спроектировать, напечатанные шестеренки могут оказаться достаточно эффективным и разумным вариантом, а для некоторых решений — идеальным.
Большинство рабочих приложений выглядят наподобие редуктора
, как правило, для небольших электродвигателей, ручек и заводных ключей. Это потому, что электродвигатели отлично работают на высоких скоростях, но у них возникают проблемы с резким снижением оборотов, и обойтись без шестереночной передачи в таком случае проблематично. Вот примеры:
Специфические проблемы послойной печати
- Напечатанные шестеренки перед использованием обычно требуют небольшой постобработки. Будьте готовы к «червоточинам» и к тому, что зубцы нужно будет обработать лезвием.
Уменьшение диаметра центрального отверстия — очень распространенная беда даже на дорогих принтерах. Это результат множества факторов. Отчасти это — температурное сжатие охлаждающегося пластика, отчасти — потому что отверстия проектируются в виде многоугольников с большим числом углов, которые стягиваются по периметру отверстия. (Всегда экспортируйте STL-файлы шестеренок с большим числом сегментов).Слайсеры тоже вносят свой вклад, поскольку некоторые из этих программ могут выбирать разные точки для обхода отверстий. Если внутренний край отверстия будет рисовать внутренний край экструдируемого пластика, то реальный диаметр отверстия будет иметь небольшую усадку, и чтобы в это отверстие потом что-нибудь вставить, может понадобиться определенное усилие. Так что слайсер может вполне намеренно делать отверстия меньше.
Кроме того, любое расхождение слоев или расхождение по ширине предполагаемого и реального экструдирования могут оказывать довольно заметный эффект, «уплотняя» отверстие. Бороться с этим можно, например, моделируя отверстия диаметром примерно на 0,005 см больше. По аналогичным причинам, и чтобы напечатанные шестеренки помещались друг рядом с другом и могли работать, рекомендуется оставлять в модели зазор между зубцами примерно в 0,4 мм. Это некоторый компромисс, зато напечатанные шестеренки не будут застревать.
- Другая распространенная проблема — получить сплошное заполнение, что довольно трудно для маленьких шестеренок. Щели между маленькими зубчиками — довольно обычное явление, даже если в слайсере выставлено заполнение 100%.
Некоторые программы относительно успешно справляются с этим в автоматическом режиме, а вручную решить эту проблему можно, увеличив перекрытие слоев. Эта задача отлично задокументирована на RichRap, и в блоге приведены различные ее решения. - Тонкостенные детали получаются хрупкими, нависающие части нуждаются в подпорках, прочность детали значительно меньше по оси Z. Рекомендуемые для печати шестеренок настройки не отличаются от обычных. На основе уже проведенных тестов можно порекомендовать прямоугольное заполнение и не менее 3 периметров. Желательно также печатать как можно более тонким слоем — насколько позволяет оборудование и терпение, потому что тогда зубцы получаются более гладкими.
- Однако же,
пластик недорог, а время дорого. Если проблема критична или нужно заменить огромную сломавшуюся шестерню, можно печатать и сплошным заполнением, чтобы не оставить шанса на какую-нибудь другую засаду, кроме износа.
О важности эвольвенты
Плохой способ изготовления шестеренок
Довольно часто в любительских сообществах можно встретить неправильно спроектированные шестеренки — моделирование шестеренок дело не такое уж и простое. Как нетрудно догадаться, плохо спроектированные шестеренки плохо сцепляются, имеют избыточное трение, давление, отдачу, неравномерную скорость вращения.
Эвольвента (инволюта) — это определенного рода оптимальная кривая, описываемая по какому-либо контуру. В технике эвольвенту окружности используют как профиль зубца для колес зубчатой передачи. Это делается для того, чтобы скорость вращения и угол сцепления оставались постоянными. Хорошо разработанный набор шестеренок должен передавать движение исключительно через вращение, с минимальным проскальзыванием.
Моделирование эвольвентной шестеренки с нуля — дело довольно нудное, так что перед тем, как за него браться, имеет смысл поискать шаблоны. Ссылки на некоторые из них будут даны ниже.
Тонкости моделирования зубца. Оптимальное количество зубцов
Подумайте вот о чем: если вам нужно передаточное число 2:1 для линейного механизма — сколько зубцов должно быть на каждой шестеренке? Что лучше — 30 и 60, 15 и 30 или 8 и 17?
Каждое из этих соотношений даст один и тот же результат, но комплект шестеренок в каждом случае будет при печати сильно отличаться.
Большее количество зубцов дает более высокий коэффициент сцепления (количество одновременно зацепленных зубцов) и обеспечивает более плавное вращение. Увеличение количества зубцов приводит к тому, что каждый из них должен быть меньше — чтобы уместиться на тот же диаметр. Мелкие зубцы более хрупкие, их сложнее точно напечатать.
С другой стороны, уменьшение количества зубцов дает больше объема для увеличения прочности.
Печатать на 3D-принтере меленькие шестеренки — это как раскрашивать в раскраске тонкие линии толстой кисточкой. (Это на 100% зависит от диаметра сопла и разрешения принтера по горизонтальной плоскости. Разрешение по вертикали не играет роли в ограничении по минимальным размерам).
Если вы хотите испытать свой принтер в деле печатания мелких шестеренок, можете воспользоваться этим STL:
Протестированный нами принтер все выполнил на высшем уровне, но при диаметре от примерно полудюйма зубцы стали выглядеть как-то подозрительно.
Совет заключается в том, чтобы делать зубцы как можно больше, избегая при этом предупреждения от программы о слишком малом их количестве, а также избегая пересечений.
Есть еще один момент, на который следует обратить внимание при выборе количества зубцов: простые числа и факторизация.
Числа 15 и 30 оба делятся на 15, так что при таком количестве зубцов на двух шестеренках одни и те же зубцы будут постоянно встречаться друг с другом, образуя точки износа.
Более правильное решение — 15 и 31. (Это ответ на вопрос в начале раздела).
При этом не соблюдается пропорция, зато обеспечивается равномерный износ пары шестеренок. Пыль и грязь будут распределяться по всей шестеренке равномерно, износ тоже.
Опыт показывает, что лучше всего, если соотношение количества зубцов двух шестеренок лежит в интервале примерно от 0,2 до 5. Если требуется большее передаточное число, лучше добавить в систему дополнительную шестеренку, иначе может получиться механический монстр.
Мало зубцов — это сколько?
Такую информацию можно найти в каком-нибудь Справочнике механика. 13 — минимальная рекомендация для шестеренок с углом давления 20 градусов, 9 — рекомендованный минимум для 25 градусов.
Меньшее число зубцов нежелательно, потому что они будут пересекаться, что ослабит сами зубцы, да и в процессе печати придется решать проблему перекрытия.
Инструкция и чертёж по созданию реечного дровокола при помощи своих собственных рук
Современным дачникам часто приходится решать проблему, с которой наши предки сталкивались ещё с глубокой древности. Также эту проблему приходится решать и некоторым другим людям в некоторых других условиях даже в современном мире. Речь идёт о колке дров своими руками.
Это довольно важное занятие в условиях холодной территории проживания и холодного климата было неотъемлемым способом для выживания раньше. Сегодня ситуация несколько изменилась, цивилизация шагнула вперёд и будет шагать дальше обязательно.
Но вопрос о том, как колоть дрова в местах, где нет городов и дрова реально нужны, остался.
Вот только технические приспособления весьма упростили этот процесс и то, что нашим предкам казалось сложным — сегодня вопрос техники и уже реальность.
Также это вопрос денег, а в некоторых случаях и просто свободного времени для работы и создания необходимого чудесного оборудования своими руками. Итак, позвольте представить — дровокол. Можете увидеть его на фото.
Типы дровоколов
Чертежи этого инструмента достаточно просты и их можно найти во всемирной сети, допустим . По ним можно понять, что создать такое оборудование своими руками не так сложно.
Особенно относительно других технических инструментов современности.
Тем более что «аппаратура», требующаяся для сотворения колуна не столь редка, да и в целом сама схема его проста.
В особенности будет интересно отметить, что дровоколы бывают разных вариаций, видов. Можно найти конусные, можно винтовые, есть гидравлические, реечные также. Колуны — достаточно полезная штука, и во многих из них могут соединяться необходимые элементы и детали разных видов. Хороши и эффективны гидравлические модели.
Винтовой колун, к примеру, состоит из конусного сверла, которое превосходно и позволяет резать ( так сказать, колоть ) дрова достаточно легко.
Допустим, что вы не поняли из предыдущего описания насколько это простое занятие — колка дров — сегодня .
Тонкости моделирования зубца. Угол давления, и Как сделать прочные зубцы
Угол давления 15, угол давления 35
Угол давления?
Зачем мне это знать?
Это угол между нормалью к поверхности зубца и диаметром окружности. Зубцы с большим углом давления (более треугольные) прочнее, но хуже сцепляются. Их проще печатать, но при работе они создают высокую радиальную нагрузку на несущую ось, издают больше шума и склонны к отдаче и проскальзыванию.
Для 3D-печати хорошим вариантом является 25 градусов, что обеспечивает плавную и эффективную передачу в шестернях размером с ладонь.
Что еще можно сделать для укрепления зубцов?
Просто сделайте шестерню толще — это, очевидно, укрепит и зубцы. Удвоение толщины дает удвоение прочности. Хорошее общее правило гласит: толщина должна быть от трех до пяти раз больше шага зацепления шестеренки.
Прочность зубца шестеренки можно приблизительно оценить, если рассматривать его как небольшую консольную балку. При таком подходе ясно, что добавление перекрывающей сплошной стенки для уменьшение неподдерживаемой площади значительно укрепляет прочность зубцов шестеренок. В зависимости от применения, такая техника расчетов может быть использована также для уменьшения числа точек зацепления.
Схема изготовления реечного дровокола в домашних условиях — Жми!
Современный рынок отопительного оборудования насыщен всевозможными технологическими агрегатами нового поколения, с помощью которых достаточно эффективно можно осуществлять обогрев жилища. Но, несмотря на это, многие загородные и сельские дома обогревают с помощью дровяных печей, каминов и котлов.
Дрова также являются прекрасным сырьем для обогрева бань и саун. Однако, ни для кого не секрет, что заготовка дров является весьма трудоемким процессом. Чего только стоит нарубить большое количество поленьев!
Поэтому, чтобы облегчить этот тяжелый труд, люди начали придумывать и использовать различные механические приспособления, к которым смело можно отнести и реечный дровокол. Стоит также отметить, что конструкция реечного дровокола достаточно простая, а принцип действия несложный и понятный.
Исходя из этого, смело можно сделать утверждение, что такой вид устройства для рубки дров вполне можно сделать своими руками. В этой статье мы расскажем о том, как изготовить реечный дровокол своими руками, а также дадим рекомендации, касающиеся выбора необходимых для этого материалов.
Устройство, в котором бревно раскалывается на чурки путем механического воздействия на него колуна, называется дровоколом. Отличительной особенностью реечного вида этого агрегата является то, что колун прикреплен на специальной направляющей рейке.
Конструкция реечного дровокола состоит из следующих основных компонентов:
- мощная станина;
- двигатель, который приводит в действие механизм;
- зубчатая рейка и шестерня;
- режущий элемент в виде колуна;
- шкивы, которые находятся на первичном и вторичном валах;
- рычаг управления устройством.
Как сделать винтовой дровокол своими руками: https://6sotok-dom.com/instrumenty/vintovoj-drovokol.html
Как функционирует
Принцип действия этого вида устройства заключается в следующих важных моментах:
- запускается привод двигателя;
- бревно подается по желобу на режущую поверхность;
- нажимая рычаг, зубчатая шестерня сцепляется с направляющей рейкой и начинает двигать толкатель бревна к колуну;
- бревно раскалывается на поленья;
- нарубленный пиломатериал убирается;
- рычаг управление возвращается в исходное положение.
Совет: чертеж можно подобрать в зависимости от наличия материалов.
После выполнения этого цикла операций реечный дровокол готов к следующей рубке.
Технология изготовления своими руками
Чертеж дровокола (нажмите, чтобы увеличить)
Как видно из описания конструкции и принципа работы, дровокол этого вида вполне можно смонтировать своими руками.
Но чтобы выполнить качественно работу, результатом которой станет эффективный агрегат, прежде всего, необходимо придерживаться следующего ряда рекомендаций:
1. Выбор чертежа. На сегодняшний день существует множество схем конструкции реечного агрегата. Благодаря такому источнику как интернет, можно подобрать себе чертеж, который будет оптимально подходить вам.
2. Подготовка материалов. После детального изучения схемы дровокола нужно приготовить все необходимые материалы. Для этого нужно осмотреть все, что есть в наличии в домашнем хозяйстве, а недостающие материалы необходимо докупить.
Как изготовить ручной садовый бур своими руками: https://6sotok-dom.com/instrumenty/ruchnoj-bur-svoimi-rukami.html
3. Сборка станины реечного дровокола. Важным конструктивным элементом реечного агрегата является несущая рама, поэтому к ее монтажу нужно отнестись достаточно внимательно и ответственно.
Наиболее оптимальными материалами для рамы являются следующие виды металлических изделий:
- двутавр;
- швеллер;
- уголок необходимой толщины;
- профильная труба.
Совет: если вы рассчитываете, что дровокол должен быть передвижным, то нужно позаботиться о том, чтобы в конструкции были предусмотрены колеса, а также их надежная фиксация.
Реечное зацепление
4. Монтаж конструктивных элементов дровокола. Следующим этапом монтажа является установка толкательного механизма бревна. При этом важно понимать, что его установка должна происходить строго в соответствии с выбранным чертежом.
Для удобства использования реечного дровокола можно установить следующие дополнительные элементы:
- тепловое реле для агрегатов, для которых приводом является электродвигатель;
- защитная муфта для повышения уровня безопасности;
- колун лучше выбирать четырехрезцовой формы, таким образом, бревно сразу же можно будет разделять на четыре чурки.
Описание разновидностей садовых измельчителей: https://6sotok-dom.com/instrumenty/sadovyj-izmelchitel.html
Совет: желательно оборудовать реечный дровокол горизонтальным механизмом укладки, который представлен в виде желоба. Благодаря этому, можно достичь, оптимальное передвижение бревна к колуну, или, наоборот, в зависимости от выбранной конструкции.
И в заключение хочется отметить еще один немаловажный момент: при работе с реечным дровоколом всегда нужно соблюдать технику безопасности, в противном случае, можно навредить себе, и серьезно вывести из строя только созданный агрегат.
В этой статье мы попытались изложить максимальное количество рекомендаций и советов для того, чтобы созданный вами агрегат для рубки дров значительно облегчил ваш труд.
Надеемся, что информация, изложенная в статье, будет для вас достаточно полезной.
Ниже, мы предлагаем Вам посмотреть видео о том, как сделать реечный дровокол своими руками:
Источник: https://6sotok-dom.com/instrumenty/reechnyj-drovokol.html
Методы крепления на ось
Тугая насадка на ось с насечками.
Этот самый простой метод встречается не слишком часто. Здесь надо быть внимательным со перекосом пластика, что с течением времени ухудшит передачу момента. Такая конструкция является также неразборной.
Ось на фиксирующем винте в плоскости шестерни.
Фиксирующий винт проходит сквозь шестерню и упирается в плоский участок на оси. Фиксирующий винт обычно направляется непосредственно в тело шестерни или через утопленную гайку через квадратное отверстие. У каждого метода есть свои риски.
Если направлять винт напрямую, можно сорвать хрупкую пластиковую резьбу. Метод с утопленной гайкой решает эту проблему, но, если не проявить достаточно аккуратности и приложить при креплении слишком большое усилие, тело шестерни может сломаться. Делайте шестерню потолще!
Добавление специальных ввинчивающихся термовставок, существенно улучшит прочность насадки на ось.
Утопленный шестигранник —
шестиугольная врезка, в которой сидит шестиугольная гайка под шестиугольный винт. Вокруг шестиугольника нужно напечатать достаточно сплошных слоев, так чтобы винту было за что держаться. При этом тоже полезно использовать фиксирующий винт, особенно если речь идет о высоких оборотах.
Клин
встречается в мире любительской 3D-печати нечасто.
Ось как единое целое с гайкой.
Такое решение хорошо противостоит нагрузкам на скручивание. Его, однако, очень трудно добиться на принтере, потому что шестерни приходится печатать перпендикулярно к поверхности стола, а любые оси при таком решении имеют слабое место по оси Z, что проявляется при высоких нагрузках.
Реечный домкрат: основные характеристики, изготовление своими руками, особенности эксплуатации
Домкраты принято использовать в процессе ремонта автомобилей, хотя такое устройство оказывается незаменимым и при сооружении мостов, а также прокладке электролиний.
Чтобы такое оборудование оказалось максимально эффективным, следует отдать предпочтение реечной модели. При наличии базовых знаний и опыта ее можно сделать своими руками.
Виды и принцип работы
Все реечные домкраты могут быть электрическими или с ручным приводом. Несмотря на такое различие, принцип работы устройства сохраняется.
Так, происходит взаимодействие храпового механизма с рейкой. Корпус поднимают и перемещают по рейке. Здесь предусмотрена опора и рычаг.
Также есть механический кожух, защищающий все детали от возможного загрязнения.
Реечные модели делятся на две группы:
- зубчатые – здесь предусмотрена рукоятка с шестеренками;
- рычажные – такие домкраты приводят в движение благодаря рычагу.
Самое простое оборудование поднимает вес, не превышающий 8 т. В продаже встречаются особые модели, предназначенные для выполнения различных строительных работ.
Благодаря сложной конструкции они способны выдерживать вес около 10 т. Этот показатель у одноступенчатых разновидностей составляет 15 т, а у трехступенчатых – 20 т.
Причем удастся перемещать груз по горизонтали и вертикали.
Инструмент работает при приложении определенного усилия на соответствующий механизм. При необходимости удается даже поднимать груз непосредственно с земли. Этому способствует низкий подхват.
Главным недостатком всех реечных домкратов считаются их внушительные габариты. Так, оборудование, предназначенное для работы с грузами в 5 т, имеют вес около 40 кг. Соответственно, использовать их в бытовых условиях не всегда удобно.
Важные технические характеристики
Чтобы приобрести или сделать своими руками надежный домкрат, стоит учитывать несколько основных параметров. Именно они влияют на эффективность и безопасность выполнения различных работ.
- Грузоподъемность принято указывать в кг либо т. Этот показатель определяется на основании веса груза, который переносят максимально часто.
- Соответствие опорной площадки всем принятым нормам. Такой элемент обеспечивает упор оборудования в землю. Площадка должна быть устойчивой и не двигаться во время выполнения работ. Это возможно благодаря правильной форме основания.
- Высота подхвата, то есть подъемного кронштейна, признана еще одним важным параметром. Стоит отметить, что такой элемент может иметь разную форму, однако это не влияет на его эффективность и качество.
- Важно всегда учитывать высоту подъема. Речь идет о расстоянии от подхвата до опорной площадки.
- Усилие, прикладываемое при подъеме любых грузов, зависит от максимально допустимой массы. Этот параметр может отличаться для разных механизмов.
- На устойчивость всей конструкции влияет качество и прочность фиксации опорной площадки. Если изделие будет аккуратно собрано своими руками, груз не будет съезжать.
Самостоятельное изготовление домкрата
Практически каждый человек может сделать своими руками домкрат при наличии соответствующего опыта и всех необходимых деталей.
Стоит отметить, что самостоятельная сборка на практике всегда выходит дешевле покупки готового оборудования.
При создании такого устройства можно использовать различные схемы, хотя в целом выполнение работ остается одинаковым.
- Сначала необходимо сварить пару реечных труб так, чтобы они визуально напоминали усеченную пирамиду.
- После этого из листа стали толщиной в 5 мм создается верхнее и нижнее основание.
- В верхней части подготавливается отверстие, где будет впоследствии приварена гайка. Подобное отверстие делают и в нижнем основании, однако туда вставляют механический пруток, необходимый для вращения.
Стоит отметить, что для создания домкрата своими руками лучше брать детали, выполненные из закаленной стали. Если говорить о винте, то оптимальным решением станет изделие с трапецеидальной резьбой.
Правильно изготовленное устройство можно смело применять при ремонте автомобилей и выполнении строительных работ. Если подсоединить сюда металлический трос, то домкрат сможет заменить собой лебедку.
Подобное устройство поднимет груз весом в 5–20 т.
Особенности эксплуатации оборудования
Чтобы домкрат был эффективным, надежным и долговечным, нужно правильно его использовать. Так, в процессе разворачивания опорную «пятку» аккуратно задвигают вглубь. Благодаря этому устройство будет ровным и устойчивым. В противном случае оно немного наклонится, а значит, груз может сдвинуться или вовсе выпасть.
Как только устройство займет нужную позицию, следует переместить выключатель в верхнее положение, а затем потянуть рычаг вверх, чтобы «пятка» уперлась в груз. Только после этого этапа можно приступать к подъему.
Во время работы с домкратом следует помнить о технике безопасности. Стоит находиться по левую сторону от инструмента и держать рычаг правой рукой.
Его дополнительно берут левой рукой, располагая сбоку большой палец. При этом следует убедиться, что пальцы не дотрагиваются до реек, а голова не находится между рычагом и рейкой.
Если не соблюдать такие рекомендации, возможно травмирование пальцев и сотрясение мозга.
Сам рычаг аккуратно раскачивают вверх-вниз. Если в процессе работы кажется, что домкрат слегка перекосился, следует переустановить его и начать все заново. После поднятия груза рычаг фиксируют в соответствии со схемой.
Стоит отметить, что опускание груза считается более травмоопасной процедурой, потому ее выполняют очень аккуратно и медленно. К возможным повреждениям обычно приводит выход шпонки. Чтобы избежать этого, важно крепко держать рычаг до тех пор, пока груз не коснется земли.
Реечный домкрат незаменим для каждого автомобилиста. Такое оборудование несложно сделать своими руками, используя несколько стальных труб, листов и крепежей. Готовое изделие нужно периодически очищать от грязи, поливая водой из шланга. Такого простого ухода достаточно для правильного функционирования конструкции.
- Александр Романович Чернышов
- Распечатать
Некоторые типы шестеренок
Внешние и внутренние прямозубые шестерни, параллельные спиральные (косозубые), двойные спиральные, реечные, конические, винтовые, плосковершинные, червячные
Спиральное зубчатое колесо (елочка).
Его обычно можно увидеть в экструдерах принтеров, они сложны в работе, но имеют свои преимущества. Они хороши большим коэффициентом сцепления, самоцентровкой и самовыравниванием. (Самовыравнивание бесит, потому что отражается на работе всей конструкции). Этот тип шестеренок также непрост в изготовлении на обычном оборудовании, вроде любительских принтеров. 3D-печать знает значительно более простые методы.
Червячная шестерня.
Легко моделируется, есть большой соблазн ее использовать. Следует отметить, что передаточное число такой системы равно числу зубцов шестеренки, поделенному на количество проемов червяка. (Надо посмотреть с торца червяка и посчитать количество начинающихся спиралей. В большинстве случаев получается от 1 до 3).
Реечная шестерня.
Преобразует вращательное движение в линейное и наоборот. Здесь речь идет не о вращении, а о расстоянии, которое проходит рейка с каждым поворотом вала шестерни. Тут очень просто вычислять плотность зубцов: надо лишь умножить их плотность на рейке на пи и на диаметр шестерни. (Или умножить количество зубцов на рейке на плотность зубцов на шестерне).
Основные способы изготовления
Заготовки для рассматриваемых изделий получаются методом ковки или литьем, в некоторых случаях при применении технологии резания. Технологический процесс изготовления зубчатого колеса довольно сложен, так как нужно получить рабочую поверхность сложной формы с определенными геометрическими параметрами. Проводится нарезание косозубых колес и других изделий при использовании двух основных технологий:
- Метод копирования предусматривает фрезерование, при котором прорез между впадинами зубьев образуются при применении, дисковых, модульных или концевых фрез. После образования каждой впадины заготовка поворачивается ровно на один зуб. Сред особенностей подобной технологии можно отметить то, что форма применяемого режущего инструмента повторяет форму впадины.
- Метод обкатки сегодня встречается намного чаще. В этом случае механическая обработка предусматривает имитирование зацепления зубчатой пары, одним элементом которой становится червячная фреза. При изготовлении инструмента используется металл повышенной прочности, за счет чего и происходит резка. Обработка методом копирования предусматривает применение не только червячной фрезы, но также и долбяка и гребенки.
Довольно большое распространение получили червячные фрезы. Подобный инструмент представлен рейкой, на момент работы заготовка вращается вокруг своей оси. Применяется инструмент для изготовления исключительно шестерен с внешним расположением зубьев.
Гребенки используются для нарезания прямых и косых зубьев с большим модулем зацепления. Стоит учитывать, что поверхность инструмента может быстро изнашиваться.
Технология накатывания используется для получения больших зубчатых колес, а также крупных партий. В подобном случае проводится горячее накатывание, за счет нагрева степень обрабатываемости материала повышается. Венец получается методом выдавливания. Для существенного повышения точности может проводится механическая обработка.
Смазка 3D-напечатанных шестеренок
Если устройство работает при малых нагрузках, на малых скоростях и частотах, о смазке пластиковых шестеренок можно не беспокоиться. Но если нагрузки высоки, то можно попробовать продлить срок службы, смазывая шестерни и уменьшая трение и износ. В любом случае все функции шестеренок более эффективны при наличии смазки, а сами шестерни служат дольше
Для таких объектов, как шестеренки экструдера 3D-принтера, можно порекомендовать плотную смазку. Для этого отлично подойдут литол, PTFE или смазки на силиконовой основе. Смазку надо наносить, слегка протирая деталь туалетной бумагой, чистым бумажным полотенцем или не пыльной тканью, равномерно распределяя лубрикант, несколько раз провернув шестеренку.
Любая смазка лучше, чем никакой, но надо убедиться в ее химической совместимости с данным пластиком. А еще всегда надо помнить, что смазка WD-40 — отстой. Хотя она и прилично чистит.
Инструментарий для изготовления шестеренок
Высококачественные шестеренки можно делать на одних лишь бесплатных программах. То есть, существуют платные программы для очень оптимизированных и совершенных шестереночных соединений, с тонко настраиваемыми параметрами и оптимальной производительностью, но от добра добра не ищут. Просто надо сделать так, чтобы в одном и том же механизме использовались шестеренки, изготовленные одним и тем же инструментом, чтобы соединения сцеплялись как надо. Шестеренки лучше моделировать парами.
Вариант 1.
Найти имеющуюся модель шестеренки, модифицировать или масштабировать ее под свои нужды. Вот перечень баз данных, где можно найти готовые модели шестеренок.
- McMaster Carr : обширный массив 3D-моделей, проверенных решений
- GrabCAD : гигантская база данных присланных пользователями моделей
- GearGenerator.com генерирует SVG-файлы прямозубых шестеренок (Эти файлы могут быть конвертированы в импортируемые . Впрочем, некоторые программы, такие как Blender, умеют импортировать SVG напрямую, без танцев с бубнами).
- https://inkscape.org/ru/ — бесплатная программа векторной графики с интегрированным генератором шестеренок. Приличное руководство по созданию шестеренок на Inkscape — и .
.
Редакторы STL-файлов
Большинство генераторов шаблонов шестеренок дают на выходе STL-файлы, что может раздражать, если вам требуются особенности, которых генератор не предлагает. STL-файлы — это PDF мира 3D, они изощренно сложны для редактирования, однако редактирование возможно.
TinkerCAD.
Хорошая элементарная браузерная CAD-программа, простая и быстрая в освоении, одна из немногих программ 3D-моделирования, которая умеет модифицировать STL-файлы. www.Tinkercad.com
Meshmixer.
Хорошая программа для масштабирования исходных форм. https://meshmixer.com/
Изготовление конических шестерен
Для изготовления конических колес (конических шестеренок) применяют вариант обкатки в станочном зацеплении заготовки с воображаемым производящим колесом. Режущие кромки инструмента в процессе главного движения срезают припуск, таким образом, образовывают боковые поверхности будущей шестерни (шестеренки).
Владельцы домашних мастерских имеют много приспособлений и устройств, которые значительно облегчают ручной труд и повышают эффективность работы. Одним из таких механизмов является понижающий редуктор.
В основном он используется для того, чтобы скорость вращения выходного вала изменялась в меньшую сторону или повышался на нем крутящий момент. По своей конструкции это устройство может быть комбинированным, червячным или шестеренным, а также одно- и многоступенчатым.
Понижающий редуктор многие изготавливают своими руками.
Что такое редуктор?
Этот механизм представляет собой передаточное звено, которое располагается между вращательными устройствами электродвигателя или двигателя внутреннего сгорания к конечному рабочему агрегату.
Основными характеризующими показателями редуктора являются:
- передаваемая мощность;
- количество ведущих и ведомых вращательных валов.
К вращательным устройствам этого механизма неподвижно закрепляют зубчатые или червячные передачи
, которые передают и регулируют движение от одного к другому. В корпусе имеются отверстия с подшипниками, на которых располагаются валы.
Необходимые материалы и инструменты
Чтобы изготовить редуктор могут потребоваться следующие материалы и инструменты:
- гаечные ключи и отвертки разнообразных форм и размеров;
- надфили, сверла;
- прокладки из резины;
- шайбы, обрезки труб, шестерни, болты, подшипники, шкивы, валы;
- инвертор;
- штангенциркуль, линейка;
- плоскогубцы;
- тиски, молоток;
- каркас от старого редуктора или стальные листы.
Как сделать редуктор своими руками?
Самой важной деталью понижающего редуктора считается его корпус. Он должен быть спроектирован и изготовлен правильно своими руками, так как от этого зависит взаимное положение валов и осей, соосность гнезд под опорные подшипники и зазоры между шестернями.
Корпусы промышленных редукторов изготавливают в основном методом литья из алюминиевых сплавов или чугуна
, однако, в домашних условиях сделать это совершенно невозможно. Поэтому под свои нужды можно подобрать или доделать уже готовый корпус либо сварить из стального листа. Только в этом случае следует помнить, что в процессе сварки металл может «повести», и поэтому для сохранения соосности валов необходимо оставлять припуск.
Многие мастера делают по-другому. Чтобы не заморачиваться с расточными работами, они корпус начинают сваривать полностью, а вместо гнезд для опорных подшипников применяют отрезки трубы
, которые выставляют в необходимом положении и только после этого окончательно закрепляют на месте при помощи сварки или болтами. Для облегчения обслуживания редуктора необходимо у корпуса сделать съемной верхнюю крышку, а снизу — сливное отверстие, которое будет использоваться для стока отработанного масла.
Опорой для шестеренок служат оси и валы редуктора. Обычно в одноступенчатом механизме используют только валы, имеющих жесткое крепление шестерен. Обе шестеренки в этом случае вращаются вместе со своими валами. Ось используют тогда, когда в редуктор необходимо вставить промежуточную шестеренку.
Она начинает свободно вращаться на своей оси с минимальным зазором
, а чтобы не смещалась вбок, ее фиксируют гайкой, упорным буртиком или стопорными разрезными шайбами.
Валы следует изготавливать из стали, обладающей хорошей прочностью и замечательно поддающейся механической обработке.
Опорами для валов служат подшипники в редукторе. Они воспринимают нагрузки, возникающие в процессе работы механизма. Надежность и работоспособность редуктора целиком зависит от того, насколько правильно были подобраны подшипники.
Для механизма своими руками лучше всего подобрать подшипники закрытого типа
, для которых требуется минимальное обслуживание. Они смазываются консистентной смазкой. Тип подшипников напрямую зависит от вида нагрузки.
При использовании прямозубых шестерен будет достаточно обыкновенных одно- или двухрядных шариковых подшипников.
Если в механизме присутствуют косозубые шестерни или червячные передачи, то на вал и подшипники начинает передаваться осевая нагрузка, что требует наличия шарикового или роликового радиально-упорного подшипника.
Другой довольно важной деталью редуктора являются шестерни. Благодаря им можно изменять частоту вращения выходного вала. Чтобы изготовить шестерни, необходимо специальное металлорежущее оборудование, поэтому для экономии можно использовать готовые детали со списанных устройств.
Очень важно в процессе монтажа шестерен выставить правильно зазор между ними, потому что от этого зависит уровень шума, возникающего во время работы редуктора и нагрузочная способность. Смазывать шестерни лучше всего жидким индустриальным маслом, которое заливают таким образом, чтобы оно покрыло зубья нижней шестерни. Смазка остальных деталей осуществляется при помощи разбрызгивания масла по внутренней полости механизма.
Сальниковые уплотнители валов предотвращают просачивание масла наружу из редуктора. Устанавливают их на выходах валов и закрепляют в подшипниковых крышках.
Чтобы предотвратить аварийное разрушение деталей механизма от больших нагрузок используют предохранительную муфту. Она бывает в виде сильфона, подпружиненных фрикционных дисков или срезаемого штифта.
Процесс монтажа очень сильно облегчают крышки подшипников
, которые бывают сквозными или глухими. Подбирают их из готовых деталей или вытачивают на токарном станке.
Сфера применения редуктора
Этот механизм является незаменимым помощников в различных сферах деятельности человека. Обычно он применяется:
- в промышленности;
- в автомобильных коробках передач;
- в электрооборудовании и бытовой техники;
- в газодобывающей промышленности и многих других отраслях.
В промышленности этот механизм используется очень широко. В различных обрабатывающих станках он применяется как вращательная передающая деталь
, повышающая скорость оборотов.
А вот в автомобильных коробках передач редуктор, наоборот, понижает частоту вращения двигателя. От того, насколько правильно отлажена его регулировка, зависит плавность и мягкость хода транспорта.
Это понижающее обороты устройство используется также в бытовой технике и электрооборудовании, имеющих электродвигатели. Это могут быть миксеры, стиральные машины, дрели, кухонные комбайны, болгарки.
Редукторы являются незаменимой частью вентиляционного оборудования, очистных сооружений, насосных систем. Они способствуют поддержанию оптимального давления газа
в газопламенных установках.
Газодобывающая промышленность также не может обойтись без этого механизма. Транспортировка и хранение газов является довольно опасным процессом, поэтому используют редуктор, с помощью которого перекрывают доступ газа или открывают ему выход, регулируя напор.
Сборка редуктора своими руками из подручных средств – дело довольно хлопотное, но не слишком трудное. С его помощью уменьшается вращение выходного вала и увеличивается его крутящий момент. Производительность устройств или машины полностью зависит от этой детали. Используется этот механизм в самых разнообразных отраслях деятельности человека.
- Фёдор Ильич Артёмов
- Распечатать
В сегодняшнее время, вокруг нас работают очень много механизмов где используются пластмассовые шестеренки. Причем, это могут быть как и игрушечные машинки, так и вполне серьезные вещи, к примеру, антенный подъемник в автомобиле, редуктор спиннинга, и тп. Причины поломки шестеренок могут быть разные, конечно большинство из них связаны с неправильной эксплуатацией, но сейчас не об этом. Если уж вы попали в такую ситуацию и у вас сломало пару зубьев шестерни, то выход есть как не платить за дорогостоящую деталь, а восстановить ее простым способом.
Не-FDM 3D-печать
Большинство людей, даже убежденные любители, не имеют непосредственного доступа к другим технологиям 3D-печати для изготовления шестеренок. Между тем такие сервисы существуют и могут помочь.
SLA —
отличная технология для профессионального прототипирования шестеренок. Печатаемые слои не видны, в результате процесса можно получать очень мелкие детали. С другой стороны, детали получаются дорогими и несколько хрупкими. Если вы используете этот процесс для прототипирования будущей литой модели, проблем с ее извлечением не возникнет. Делайте деталь сплошной, а то она непременно сломается!
SLS —
очень точный процесс, в результате которого получаются прочные детали. Технология не требует подпорок для нависающих структур. Можно создавать сложные и подробные изделия, лучше со стенками толщиной до четверти дюйма. Слои печати также почти невидимы… НО, шершавая поверхность (потому что технология основана на порошковой печати) крайне склонна к износу. Требуется очень мощная смазка, и многие вообще не рекомендуют SLS-шестеренки для приложений длительного пользования.
Технология BinderJet
хороша для детализированных и точных многоцветных декоративных или
не конструкционных
деталей. Подойдет для получения деталей безумных цветов, впрочем, очень хрупких и зернистых, так что это не то, что требуется для функциональных шестеренок.
Как сделать шестерню своими руками
Привет. Хочу поделиться опытом быстрого создания шестерёнок. Кратко расскажу как проектировать шестерни и как изготавливать.
Постарался изложить максимально простым языком.
Недавно друг, который занимался продажей шоколадных фонтанов в Питере обратился с необычным предложением. Ему вернули фонтан, где не крутился винт, поднимающий шоколад. Я люблю подобные задачи, когда мало кто может (или хочет браться) за починку единичных вещей и нужно поломать немного голову как изготовить редкие запчасти своими руками.
После разборки стало ясно, что дело в редукторе. Одна шестерня буквально расплавилась на валу (качество компонентов было просто на высоте. Скорей всего шестерня проскальзывала долгое время, потом нагрелась. Фонтан выключили, шестерня снова прилипла к валу со смещенным центром. Потом его снова включили и несколько зубъев, не выдержав нагрузки, отломилось). Точно такую же шестерёнку не найти, поэтому из оказавшегося под боком оборудования решил изготовить новую.
Вариантов создания шестерёнок очень много, я расскажу лишь про один из них. На мой взгляд он самый простой и эффективный.
Шаг 1. Разработка чертежа шестерни
Вам понадобится:
- любой векторный редактор
- штангенциркуль
- генератор шестеренок (я использовал этот онлайн сервис)
Итак, считаем количество зубцов поломавшейся шестерни. Вводим все параметры, проводим замеры.
Качаем файл чертёж. Внутреннюю звёздочку я чертил сам в кореле, т.к. нужного параметра не нашел.
Рассчитывая внутренний диаметр шестерёнки нужно соблюсти тонкий баланс между прокручиванием и растрескиванием от сильного натяга.
Шаг 2. Изготовление шестерни
Материал новой шестерни — прозрачное оргстекло. Просто ищете в поисковике лазерную резку в вашем городе и отправляетесь туда. Лучше нарезать несколько с разными параметрами сразу. Думаю, одна порезка как у меня не должна выйти более $ 6.
Шаг 3. Запуск и тест фонтана
Вообще соседние шестерни принято делать из материалов немного разной плотности. Так они дольше прослужат. Скорей всего производитель просто пренебрег этим.
Смазываем, запускаем, радуемся!Удачи в вашем труде!
Как сделать шестеренки из металла. Изготовление пластиковой шестерни (обучающий видео урок)
Постарался изложить максимально простым языком.
Недавно друг, который занимался продажей шоколадных фонтанов в Питере обратился с необычным предложением. Ему вернули фонтан, где не крутился винт, поднимающий шоколад. Я люблю подобные задачи, когда мало кто может (или хочет браться) за починку единичных вещей и нужно поломать немного голову как изготовить редкие запчасти своими руками.
После разборки стало ясно, что дело в редукторе. Одна шестерня буквально расплавилась на валу (качество компонентов было просто на высоте. Скорей всего шестерня проскальзывала долгое время, потом нагрелась. Фонтан выключили, шестерня снова прилипла к валу со смещенным центром. Потом его снова включили и несколько зубъев, не выдержав нагрузки, отломилось). Точно такую же шестерёнку не найти, поэтому из оказавшегося под боком оборудования решил изготовить новую.
Вариантов создания шестерёнок очень много, я расскажу лишь про один из них. На мой взгляд он самый простой и эффективный.
Шаг 1. Разработка чертежа шестерни
Вам понадобится:
- любой векторный редактор
- штангенциркуль
- генератор шестеренок (я использовал этот онлайн сервис)
Итак, считаем количество зубцов поломавшейся шестерни. Вводим все параметры, проводим замеры.
Качаем файл чертёж. Внутреннюю звёздочку я чертил сам в кореле, т.к. нужного параметра не нашел.
Рассчитывая внутренний диаметр шестерёнки нужно соблюсти тонкий баланс между прокручиванием и растрескиванием от сильного натяга.
Шаг 2. Изготовление шестерни
Материал новой шестерни — прозрачное оргстекло. Просто ищете в поисковике лазерную резку в вашем городе и отправляетесь туда. Лучше нарезать несколько с разными параметрами сразу. Думаю, одна порезка как у меня не должна выйти более $ 6.
Шаг 3. Запуск и тест фонтана
Вообще соседние шестерни принято делать из материалов немного разной плотности. Так они дольше прослужат. Скорей всего производитель просто пренебрег этим.
Смазываем, запускаем, радуемся!
Удачи в вашем труде!
Для изготовления шестерен используют такие материалы: железо, чугун, бронза, сталь простая углеродистая, специальные составы стали с примесью хрома, никеля, ванадия. Помимо металлов применяют смягчающие материалы: кожу, фибру, бумагу, они смягчают и обесшумливают зацепление. Но и металлические шестерни могут работать бесшумно, если их профиль выполнен с точностью. Для грубых передач производят «силовые» зубчатые колеса, их изготовляют литьем из чугуна и стали без последующей обработки. «Рабочие» зубчатые колеса для быстроходных передач изготовляются на фрезерных или зуборезных станках, с последующей термической обработкой – цементацией, которая предает зубьям твердость и устойчивость к износу. После цементации шестерни подвергаются обработке на шлифовальных станках.
Метод обката
Метод обката самый распространённый вариант изготовления шестерен, так как этот способ наиболее технологичный. В этом способе изготовления применяются такие инструменты: долбяк, червячная фреза, гребенка.
Метод обката с использованием долбяка
Для изготовления шестерен используется зубодолбёжный станок со специальным долбяком (шестерня оснащенная режущими кромками). Процедура изготовления шестерен происходит в несколько этапов, так как срезать за один раз весь лишний слой металла не возможно. При обработке заготовки, долбяк выполняет возвратно-поступательное движение и после каждого двойного хода, заготовка и долбяк проворачиваются на один шаг, как бы «обкатываются» друг по другу. Когда заготовка шестеренки сделает полный оборот, долбяк выполняет движение подачи к заготовке. Этот цикл производства выполняется, пока не будет удалён весь необходимый слой металла.
Метод обката с использованием гребёнки
Гребенка — режущий инструмент, его форма аналогична зубчатой рейки, но одна сторона зубьев гребенки заточена. Заготовка изготавливаемой шестерни производит вращательное движение вокруг оси. А гребёнка выполняет поступательное движение перпендикулярно оси шестерни и возвратно-поступательное движение параллельного оси колеса (шестеренки). Таким образом гребенка снимает лишний слой по всей ширине обода шестерни. Возможен другой вариант движения режущего инструмента и заготовки шестерни относительно друг друга, например, заготовка выполняет сложное прерывистое движение, скоординированное с движением гребенки, как будто совершается зацепление профиля нарезаемых зубьев с контуром режущего инструмента.
Этот метод позволяет изготовить шестерню при помощи червячной фрезы. Режущим инструментом в данном методе служит червячная фреза, которая совместно с заготовкой зубчатого колеса производят червячное зацепление.
Одна впадина шестеренки нарезается дисковой или пальцевой фрезой. Режущая часть фрезы, выполненная в виде формы этой впадины, нарезает шестерню. А при содействии делительного устройства нарезаемая шестеренка поворачивается на один угловой шаг и процесс нарезания повторяется. Этот способ изготовления шестерен использовался еще в начале ХХ века, он является не точным, впадины произведенного зубчатого колеса получаются разными, не идентичными.
Горячее и холодное накатывание
В этом способе производства шестерен применяется зубонакатный инструмент, который нагревает определенный слой заготовки до пластического состояния. После этого, нагретый слой деформируют для получения зубьев. А далее обкатывают зубья, изготавливаемого зубчатого колеса, до приобретения ними точной формы.
Изготовление конических шестерен
Для изготовления конических колес (конических шестеренок) применяют вариант обкатки в станочном зацеплении заготовки с воображаемым производящим колесом. Режущие кромки инструмента в процессе главного движения срезают припуск, таким образом, образовывают боковые поверхности будущей шестерни (шестеренки).
Здравствуйте уважаемые посетители. Предлагаем Вам ознакомиться с обучающим видео уроком по изготовление пластиковой шестерни. Как Вы знаете многие шестерни в бытовой и офисной техники изготавливаются из пластика, а так же происходит поломка данной шестеренки. Вы сможете узнать как сделать новую по образцу которая имеется.
В этом уроке Вы узнаете как изготовить сломанную шестеренку из кухонного комбайнера. Как Вы понимаете такие шестеренки не возможно купить в магазинах, в ремонтных мастерских могут просто не найти подходящую шестеренку. Изготовление металлической шестеренки будет дороговато для данной модели кухонного комбайна.
Для создания новой пластиковой шестеренки, нам нужно использовать сломанную часть, но в начале нам необходимо будет её склеить. При собрании сломанной шестеренки, у нас могут возникнуть не большие трудности — это появление небольших дефектов, возможно не доставание мелки деталей.
Все это склеиваем обычным суперклеем, так как в сверхпрочности нам нет никакой необходимости. Нужно сделать все имеющие детали в одно подобие шестеренки. При склеивании мы видим небольшие дефекты которые имеются у нас. Мелкие части просто разлетелись, когда сломалась шестеренка. Соответственно нам необходимо будет все восполнить и все это будет делать воском. Заполняем все там где не достают данные детальки, кусочки пластика воском и до моделируем так как у нас выглядела бы не достающая деталька. Если эта часть детали выпуклая то будем моделировать как выпуклая, а если плоская то как плоская.
При восстановлении шестеренки нужно постараться сделать таким каким он был изначально кухонном комбайне. Конечно при выполнении воском мы не сможем сделать точную копию шестеренки, но постараемся сделать более или менее точную копию. При использовании таких шестеренок в кухонных комбайнах, там нет таких сверх точный посадок, так как постоянно снимается и одевается.
Данный процесс моделирования воском занимает в среднем пару часов. После моделирования до нужного состояния можно смело приниматься к процессу изготовление пластиковой шестерни. В обучающем видео Вы сможете более подробно посмотреть весь процесс создания такой шестеренки. Желаем Вам удачи.
Одной из самых сложных и, тем не менее, распространенных механических систем является зубчатая передача. Это отличный способ передачи механической энергии из одного места в другое и способ увеличения или уменьшения мощности (крутящего момента), а также увеличения или уменьшения скорости чего-либо.
Как сделать шестеренку своими руками? Проблема всегда заключаются в том, что для создания эффективных зубчатых колес требуется достаточно много навыков рисования и знание математики, а также умение создавать сложные детали.
Для любительского нет необходимости иметь максимальную эффективность, поэтому мы можем получить намного более легкую в изготовлении систему, даже с подручными инструментами.
Шестерня — это ряд зубьев на колесе. (Обратите внимание на диаграмму выше, они пометили неправильное количество зубьев на шестернях — извините)
Шаг 1: Формулы и расчеты
Формулы для рисования и изготовления зубьев зубчатых колес в избытке можно найти в интернете , но для новичка они кажутся очень сложными.
Я решил упростить задачу, и решение очень хорошо работает как в больших, так и в малых масштабах. В небольших масштабах это лучше всего подходит для машинной резки с помощью лазерных резаков, например, очень маленькие зубчатые колеса могут быть успешно изготовлены таким образом.
Шаг 2: Простой способ
Итак, форма зубца, если говорить просто, может представлять собой полукруг.
Шаг 3: Определяем размеры
Теперь мы можем определить параметры, чтобы сделать шестерню:
- Насколько большими / маленькими будут зубья шестерни (диаметр) — чем меньше шестерня, тем меньше должны быть зубья.
- Все зубья, которые собираются в сцепление (соединяются), должны быть одинакового размера, поэтому сначала нужно рассчитать меньшую шестерню.
Давайте начнем с зубьев размером 10 мм.
Я хочу шестерню с 5 зубьями, чтобы круг был 10х10 мм (в окружности) = 100 мм.
Чтобы нарисовать этот круг, мне нужно найти диаметр, поэтому я использую математику и калькулятор и делю окружность (100 мм) на Pi = 3,142.
Это дает мне диаметр 31,8 мм, и я могу нарисовать этот круг с помощью циркуля, а затем нарисовать с помощью циркуля на его окружности ровно 10 кругов диаметром 10 мм.
Если у вас есть такая возможность, то проще сделать все с помощью программного обеспечения для рисования. Если вы используете программное обеспечение, вы должны иметь возможность вращать круги зубьев вокруг основного круга, и вам нужно будет знать, как далеко повернуть каждый зуб. Это легко рассчитать: делите 360 градусов на количество кругов. Таким образом, для наших 10 кругов 360/10 = 36 градусов для каждого зуба.
Шаг 4: Делаем зубчатую форму
Удалите верхнюю часть одного круга и нижнюю часть следующего круга. Чтобы сделать это, у вас должно быть четное количество зубьев
У нас есть первая шестерня. Она может быть вырезана из дерева или металла с помощью базовых подручных инструментов, пил и напильников.
Этот процесс легко повторить для любого количества шестеренок, которое вам нужно. Держите размер круга по образцу, и они будут соответствовать друг другу.
Шаг 5: Получите шестерёнку
Поскольку такие полукруглые шестеренки легко вырезать, вы можете сделать их с помощью подручного инструмента и лобзика или пилы.
Раньше я делал шаблон из 9 или 10 зубьев на фанере и использовал его в качестве ориентира для моего ручного фрезера и без проблем вырезал шестерни.
Если у вас есть доступ к лазерному резцу, они могут быть вырезаны из акрила 3 или 5 мм толщины и быть очень маленьких размеров.
Владельцы домашних мастерских имеют много приспособлений и устройств, которые значительно облегчают ручной труд и повышают эффективность работы. Одним из таких механизмов является понижающий редуктор.
В основном он используется для того, чтобы скорость вращения выходного вала изменялась в меньшую сторону или повышался на нем крутящий момент. По своей конструкции это устройство может быть комбинированным, червячным или шестеренным, а также одно- и многоступенчатым.
Понижающий редуктор многие изготавливают своими руками.
Что такое редуктор?
Этот механизм представляет собой передаточное звено, которое располагается между вращательными устройствами электродвигателя или двигателя внутреннего сгорания к конечному рабочему агрегату.
Основными характеризующими показателями редуктора являются:
- передаваемая мощность;
- количество ведущих и ведомых вращательных валов.
К вращательным устройствам этого механизма неподвижно закрепляют зубчатые или червячные передачи , которые передают и регулируют движение от одного к другому. В корпусе имеются отверстия с подшипниками, на которых располагаются валы.
Необходимые материалы и инструменты
Чтобы изготовить редуктор могут потребоваться следующие материалы и инструменты:
- гаечные ключи и отвертки разнообразных форм и размеров;
- надфили, сверла;
- прокладки из резины;
- шайбы, обрезки труб, шестерни, болты, подшипники, шкивы, валы;
- инвертор;
- штангенциркуль, линейка;
- плоскогубцы;
- тиски, молоток;
- каркас от старого редуктора или стальные листы.
Как сделать редуктор своими руками?
Самой важной деталью понижающего редуктора считается его корпус. Он должен быть спроектирован и изготовлен правильно своими руками, так как от этого зависит взаимное положение валов и осей, соосность гнезд под опорные подшипники и зазоры между шестернями.
Корпусы промышленных редукторов изготавливают в основном методом литья из алюминиевых сплавов или чугуна , однако, в домашних условиях сделать это совершенно невозможно. Поэтому под свои нужды можно подобрать или доделать уже готовый корпус либо сварить из стального листа. Только в этом случае следует помнить, что в процессе сварки металл может «повести», и поэтому для сохранения соосности валов необходимо оставлять припуск.
Многие мастера делают по-другому. Чтобы не заморачиваться с расточными работами, они корпус начинают сваривать полностью, а вместо гнезд для опорных подшипников применяют отрезки трубы , которые выставляют в необходимом положении и только после этого окончательно закрепляют на месте при помощи сварки или болтами. Для облегчения обслуживания редуктора необходимо у корпуса сделать съемной верхнюю крышку, а снизу — сливное отверстие, которое будет использоваться для стока отработанного масла.
Опорой для шестеренок служат оси и валы редуктора. Обычно в одноступенчатом механизме используют только валы, имеющих жесткое крепление шестерен. Обе шестеренки в этом случае вращаются вместе со своими валами. Ось используют тогда, когда в редуктор необходимо вставить промежуточную шестеренку.
Она начинает свободно вращаться на своей оси с минимальным зазором , а чтобы не смещалась вбок, ее фиксируют гайкой, упорным буртиком или стопорными разрезными шайбами.
Валы следует изготавливать из стали, обладающей хорошей прочностью и замечательно поддающейся механической обработке.
Опорами для валов служат подшипники в редукторе. Они воспринимают нагрузки, возникающие в процессе работы механизма. Надежность и работоспособность редуктора целиком зависит от того, насколько правильно были подобраны подшипники.
Для механизма своими руками лучше всего подобрать подшипники закрытого типа , для которых требуется минимальное обслуживание. Они смазываются консистентной смазкой. Тип подшипников напрямую зависит от вида нагрузки.
При использовании прямозубых шестерен будет достаточно обыкновенных одно- или двухрядных шариковых подшипников.
Если в механизме присутствуют косозубые шестерни или червячные передачи, то на вал и подшипники начинает передаваться осевая нагрузка, что требует наличия шарикового или роликового радиально-упорного подшипника.
Другой довольно важной деталью редуктора являются шестерни. Благодаря им можно изменять частоту вращения выходного вала. Чтобы изготовить шестерни, необходимо специальное металлорежущее оборудование, поэтому для экономии можно использовать готовые детали со списанных устройств.
Очень важно в процессе монтажа шестерен выставить правильно зазор между ними, потому что от этого зависит уровень шума, возникающего во время работы редуктора и нагрузочная способность. Смазывать шестерни лучше всего жидким индустриальным маслом, которое заливают таким образом, чтобы оно покрыло зубья нижней шестерни. Смазка остальных деталей осуществляется при помощи разбрызгивания масла по внутренней полости механизма.
Сальниковые уплотнители валов предотвращают просачивание масла наружу из редуктора. Устанавливают их на выходах валов и закрепляют в подшипниковых крышках.
Чтобы предотвратить аварийное разрушение деталей механизма от больших нагрузок используют предохранительную муфту. Она бывает в виде сильфона, подпружиненных фрикционных дисков или срезаемого штифта.
Процесс монтажа очень сильно облегчают крышки подшипников , которые бывают сквозными или глухими. Подбирают их из готовых деталей или вытачивают на токарном станке.
Сфера применения редуктора
Этот механизм является незаменимым помощников в различных сферах деятельности человека. Обычно он применяется:
- в промышленности;
- в автомобильных коробках передач;
- в электрооборудовании и бытовой техники;
- в газодобывающей промышленности и многих других отраслях.
В промышленности этот механизм используется очень широко. В различных обрабатывающих станках он применяется как вращательная передающая деталь , повышающая скорость оборотов.
А вот в автомобильных коробках передач редуктор, наоборот, понижает частоту вращения двигателя. От того, насколько правильно отлажена его регулировка, зависит плавность и мягкость хода транспорта.
Это понижающее обороты устройство используется также в бытовой технике и электрооборудовании, имеющих электродвигатели. Это могут быть миксеры, стиральные машины, дрели, кухонные комбайны, болгарки.
Редукторы являются незаменимой частью вентиляционного оборудования, очистных сооружений, насосных систем. Они способствуют поддержанию оптимального давления газа в газопламенных установках.
Газодобывающая промышленность также не может обойтись без этого механизма. Транспортировка и хранение газов является довольно опасным процессом, поэтому используют редуктор, с помощью которого перекрывают доступ газа или открывают ему выход, регулируя напор.
Сборка редуктора своими руками из подручных средств – дело довольно хлопотное, но не слишком трудное. С его помощью уменьшается вращение выходного вала и увеличивается его крутящий момент. Производительность устройств или машины полностью зависит от этой детали. Используется этот механизм в самых разнообразных отраслях деятельности человека.
- Фёдор Ильич Артёмов
- Распечатать
Узнайте, как легко изготовить свои собственные шестерни
В 2010 году мы попросили Дастин Робертс, в то время преподававшую в программе интерактивных телекоммуникаций (ITP) Нью-Йоркского университета, под названием «Механизмы и вещи, которые движутся», внести свой вклад в создание собственных механизмов для нашей темы «Физика и механика». Дастин только что написал книгу под названием «Заставить вещи двигаться», и мы хотели показать некоторые виды контента, которые можно в ней найти. — Гарет
Шестерни легко понять, изготовить и использовать, если вы знаете терминологию и можете расположить шестерни на правильном расстоянии друг от друга.Что хорошо в зубчатых колесах, так это то, что если вы знаете о них какие-либо две вещи — скажем, внешний диаметр и количество зубцов — вы можете использовать несколько простых уравнений, чтобы найти все остальное, что вам нужно знать, включая правильное межцентровое расстояние между ними. Во-первых, изучите анатомию цилиндрической зубчатой пары на рисунке 1 и словарях ниже.
- Число зубцов (N)
- Диаметр шага (D): Круг, на котором две шестерни эффективно зацепляются, примерно на полпути через зуб.Шаговые диаметры двух шестерен будут касаться друг друга, если центры расположены правильно.
- Диаметральный шаг (P): количество зубьев на дюйм окружности делительного диаметра. Думайте об этом как о плотности зубьев — чем больше число, тем меньше и ближе друг к другу зубья на шестерне. Обычные диаметральные шаги для проектов любительского размера — 24, 32 и 48. Диаметральный шаг всех зацепляющих шестерен должен быть одинаковым.
- Шаг по окружности (p) = pi / P: длина дуги между центром одного зуба и центром соседнего зуба.Это просто число пи (€ = 3,14), деленное на диаметральный шаг (P). Хотя этот параметр редко используется для идентификации стандартных шестерен, вам может понадобиться этот параметр при моделировании шестерен в программном обеспечении 2D и 3D, как мы делаем здесь. Как и в случае диаметрального шага , круговой шаг всех зацепляющих шестерен должен быть одинаковым.
- Внешний диаметр (Do): самый большой круг, касающийся краев зубьев шестерни. Вы можете измерить это с помощью штангенциркуля, такого как # TOL-00067 на Sparkfun.com.
Примечание. Шестерни с четным числом зубьев легче всего измерить, поскольку у каждого зуба есть другой зуб прямо напротив шестерни.На шестерне с нечетным числом зубьев, если вы проведете линию от центра одного зуба прямо через центр через шестерню, линия будет проходить между двумя зубьями. Так что просто будьте осторожны с использованием внешнего диаметра в своих расчетах, если вы рассчитали его для шестерни с нечетным числом зубьев. - Межосевое расстояние (C): половина делительного диаметра первой шестерни плюс половина делительного диаметра второй шестерни будет равняться правильному межосевому расстоянию. Этот интервал имеет решающее значение для обеспечения плавного хода шестерен.
- Угол давления : угол между линией действия (как точка контакта между зубьями шестерни перемещается при их вращении) и линией, касательной к делительной окружности. Стандартные углы давления по какой-то причине составляют 14,5 ° и 20 °. Угол давления 20 ° лучше для малых шестерен, но это не имеет большого значения. Не важно понимать этот параметр, просто нужно знать, что угол сжатия всех зубчатых колес должен быть одинаковым.
Все эти параметры зубчатой передачи связаны друг с другом простыми уравнениями.Уравнения в таблице ниже взяты из превосходного (и бесплатного) руководства по проектированию, опубликованного Boston Gear [PDF].
Самостоятельное изготовление
Этот проект адаптирован из записи в блоге, которую студент сделал на моем первом курсе «Механизмы и вещи, которые движутся» в ITP Нью-Йоркского университета. Мы спроектируем и изготовим прямозубые цилиндрические зубчатые колеса с помощью бесплатного программного обеспечения (Inkscape) и интернет-магазина (Ponoko.com), который выполнит индивидуальную лазерную резку по доступным ценам из различных материалов. Если у вас есть доступ к лазерному резаку в местной школе или в хакерской среде, даже лучше! Вы также можете распечатать шаблон и прикрепить его к картону или дереву, чтобы вырезать шестеренки вручную.
- Загрузите и установите Inkscape из Inkscape. Это бесплатная программа для рисования векторных изображений с открытым исходным кодом, аналогичная Adobe Illustrator. Он хорошо работает с большинством современных операционных систем Windows, Mac и Linux (подробности см. В FAQ).
- Зайдите в Ponoko и загрузите их стартовый комплект Inkscape. Это даст вам руководство по изготовлению (файл PDF) и три шаблона, которые относятся к размерам материалов Ponoko. Разархивируйте файл и сохраните его в удобное для вас место.
- Откройте новый файл в Inkscape.В меню файла перейдите в Свойства документа, чтобы открыть окно, показанное на рисунке 2. Измените единицы измерения по умолчанию в верхнем правом углу на дюймы. Вернувшись в главное окно, измените линейки с пикселей на дюймы на панели инструментов. Ваш экран должен выглядеть так, как показано на рисунке 2. После настройки выйдите из этого окна.
- А теперь займемся шестеренками! Перейдите на панель инструментов и выберите Extensions -> Render -> Gear. Появится небольшое окно шестерни, в котором вы найдете три варианта: количество зубцов, круговой шаг, пиксели и угол прижима.Оставьте угол давления в покое — значение по умолчанию 20 ° является стандартным для серийных шестерен, так что это хорошее место для начала. На рисунке 3 вы можете видеть, что я выбрал 28 зубцов с круговым шагом 24. Нажмите «Применить», затем «Закрыть». Примечание относительно шага окружности. В Inkscape шаг окружности указывается в пикселях, а не в дюймах, как мы привыкли использовать в уравнениях в приведенной выше таблице. Вы можете получить разные передаточные числа, просто выбирая круговой шаг, который выглядит хорошо, и варьируя количество зубьев, но если вы хотите сделать шестерни, которые взаимодействуют с шестернями, уже имеющимися в продаже, вам нужно уделить немного больше внимания.По умолчанию в Inkscape 90 пикселей на 1 дюйм. Итак, если вы установите круговой шаг на 24 пикселя в инструменте шестерни, как это было сделано выше, он округлится до 0,267 дюйма (24/90 = 0,2666…). Поскольку диаметральный шаг (P) = € / круговой шаг (p), диаметральный шаг (P) в дюймах составляет = € / 0,267 = 11,781. Вы не найдете готовых шестерен с диаметральным шагом 11,781. Как упоминалось ранее, наиболее распространенными диаметральными шагами являются 24, 32 и 48. Поэтому, если вы планируете сделать так, чтобы шестерни хорошо играли со стандартными шестернями, начните с диаметрального шага вашей готовой шестерни и используйте уравнения в таблице, чтобы работайте в обратном направлении до того, каким должен быть ваш круговой шаг в пикселях в Inkscape.
- Теперь, поскольку шестерни сами по себе не приносят удовольствия, повторите шаги 4 и 5 еще раз, чтобы сделать еще хотя бы одну шестерню. Вторая шестерня, показанная на рисунке 30, имеет 14 зубьев. Помните: угол давления и шаг окружности должны быть одинаковыми для зацепления шестерен — измените только количество зубьев!
- Используйте инструмент круга и удерживайте кнопку CTRL (на ПК), чтобы нарисовать круг внутри большой шестеренки. Круг по умолчанию отображается черным цветом. Если нужно, увеличьте масштаб.Убедитесь, что переключатель со стрелкой активен, и щелкните кружок. Убедитесь, что на панели инструментов выбраны дюймы и кнопка блокировки выглядит заблокированной. Введите 0,250 в поле W на панели инструментов, нажмите клавишу ВВОД и посмотрите, как поле H изменится автоматически. Размер вашего круга изменится до 0,250 дюйма в диаметре, и ваш экран должен выглядеть, как показано на рисунке 4.
- Щелкните и перетащите рамку вокруг большой шестеренки, маленькой шестеренки и круга, чтобы выделить их все. В строке меню выберите «Объект» -> «Заливка и обводка».Должно появиться окно, похожее на рисунок 5.
- На вкладке Заливка нажмите кнопку X, чтобы не рисовать.
- На вкладке Stroke paint нажмите кнопку рядом с X, чтобы получить однородный цвет. Оставьте пока цвет по умолчанию (черный).
- На вкладке Stroke style измените ширину на 0,030 мм и нажмите Enter. Это то, что Поноко хочет, чтобы толщина линии была для лазерной резки. При необходимости отрегулируйте, если вы используете другой лазерный резак. Закройте окно.
- Теперь нам нужно, чтобы этот круг находился точно в центре шестеренки. Убедитесь, что переключатель со стрелкой активен. Щелкните и перетащите рамку вокруг большой шестеренки и круга, чтобы выбрать их обоих. В строке меню перейдите в Объект -> Выровнять и распределить. Нажмите кнопку «центрировать объект по горизонтали», выделенную на рисунке 6, затем кнопку справа под ней — «центрировать объекты по вертикали». Теперь у вас есть шестерня с идеально отцентрованным отверстием! Скопируйте и вставьте этот круг и повторите этот шаг, чтобы центрировать круг на другой шестерне.
- Теперь, когда у нас есть шестерни, давайте создадим основу с отверстиями, расположенными на правильном расстоянии друг от друга, чтобы мы могли установить шестерни деревянными дюбелями 1/4 дюйма и заставить их вращаться.
- Во-первых, нам нужно вычислить, какое центральное расстояние (CD) наших шестерен, используя уравнения из таблицы. Обе шестеренки имеют круговой шаг 24 пикселя и угол давления 20 °. У большой шестерни 28 зубьев, а у маленькой 14. В примечании к шагу 4 мы преобразовали круговой шаг в пикселях в диаметральный шаг в дюймах, равный 11.781. Если мы посмотрим на таблицу, все, что нам понадобится, это это число и количество зубьев на двух зацепляющих шестернях, чтобы найти межосевое расстояние (CD). Используйте уравнение CD = (N1 + N2) / 2P, и вы обнаружите, что CD = 1,783.
- Теперь скопируйте один из кругов внутри шестеренок и вставьте два из них на расстоянии двух дюймов друг от друга в нижнюю часть шаблона. Выберите крайний левый и измените координату X на панели инструментов на 3 дюйма, затем нажмите Enter. Ваш экран должен выглядеть как на Рисунке 7.
- Используйте ту же процедуру, чтобы разместить второй круг справа от первого с координатой X, равной 4.783. Это центральное расстояние, которое мы вычислили выше (1,783), добавленное к координате X первого круга (3.000).
- Теперь нарисуйте прямоугольник вокруг двух кругов, чтобы завершить основу. Совместите прямоугольник с двумя кругами, как показано на рисунке 8.
- Теперь нам нужно подготовить файл для загрузки и заказа на Ponoko.com.
- Ponoko использует цвета, чтобы указать, как они должны обращаться с файлами — например, синий 0.Линия 030 мм означает прорезание насквозь. Итак, выберите все, что вы нарисовали, перейдите к образцам цвета в нижней части экрана и, удерживая кнопку Shift, нажмите на синий.
- Откройте шаблон P1.svg, который вы скачали ранее. Выделите все, что вы уже нарисовали, скопируйте и вставьте в этот шаблон, как показано на рисунке 9. Не беспокойтесь о оранжевой рамке и словах — Поноко умеет вырезать только синие контуры.
- Сохраните файл и перейдите в Ponoko.com, чтобы создать бесплатную учетную запись, загрузить ее, выбрать материал и получить его! Я выбрал светлый бамбук, как показано на рисунке 10, и общая стоимость составила всего 4,13 доллара (плюс доставка). Примечание. После того, как вы откроете бесплатную учетную запись, перейдите в «Мои учетные записи» -> «Настройки», чтобы указать в качестве узла доставки Поноко — США (или ближайшее к вам место). Мой был случайно отправлен в Новую Зеландию, поэтому мои расходы на доставку были на удивление высокими, пока я не выяснил это.
- Ваш заказ Ponoko должен прибыть через пару недель, если вы не укажете срочность.Пока вы ждете, купите деревянный дюбель 1/4 дюйма в местном хозяйственном или ремесленном магазине (или, конечно, McMaster). Отрежьте две секции диаметром 2 дюйма ножом для хобби и подпилите концы сколов.
- Шестерни входят в квадратный шаблон с бумажными протекторами с каждой стороны. Снимите бумагу, вытащите шестерни и поместите две шестерни над отверстиями в основании. Вставьте деревянные дюбели и вуаля!
BIO: Дастин Робертс — инженер с традиционным образованием и нетрадиционными представлениями о том, как преподавать инженерное дело.Она начала свою карьеру в Honeybee Robotics в качестве инженера в проекте системы манипуляции образцами для миссии NASA Mars Science Laboratory, запуск которой запланирован на 2011 год. После консультаций с двумя художниками во время их резидентуры в Eyebeam Art + Technology Center в Нью-Йорке в 2006 году, она основал Dustyn Robots (www.dustynrobots.com) и продолжает заниматься консультационной работой, начиная от анализа походки и заканчивая проектированием управляемых парашютных систем. В 2007 году она разработала курс для программы интерактивных телекоммуникаций Нью-Йоркского университета (ITP) под названием «Механизмы и вещи, которые движутся», в результате чего была написана книга «Заставить вещи двигаться: механизмы для изобретателей, любителей и художников», которые выйдут осенью 2010 года.Дастин имеет степень бакалавра в области механической и биомедицинской инженерии в Университете Карнеги-Меллона, степень магистра в области биомеханики и движений в Университете Делавэра, и в августе этого года поступит в аспирантуру по машиностроению в NYU-Poly. Освещение ее работы в СМИ появилось в Time Out New York, IEEE Spectrum и других местных организациях. Она живет в Нью-Йорке со своим партнером Лореной и котом Симбой.
Больше:
Как построить электрическую лебедку из металлолома
Нужна лебедка? Тогда сделайте свой собственный дом с нуля из металлолома.
Если видеоплеер не работает, вы можете щелкнуть по этой альтернативной ссылке на видео.
Нужен новый подъемник? Зачем покупать такой, если его можно сделать из металлолома?
Узнайте, как …
Источник: Интересные разработки / YouTubeКак и в любом проекте подобного рода, вам сначала нужно собрать воедино некоторые материалы и инструменты.
Теперь, когда у вас все под рукой, пора приступить к сборке. Однако имейте в виду, что вам понадобится некоторый опыт сварки и использования электроинструментов, например токарного станка.
Сначала возьмите утилизированную червячную передачу и закрепите ее на запасной металлической пластине, как показано на видео.
Источник: Интересные разработки / YouTubeСогните другие части стального листа, чтобы охватить червячную передачу, и приварите к опорной плите. Смотрите видео, чтобы узнать больше об этом.
Источник: Интересные разработки / YouTubeЗатем возьмите два больших шарикоподшипника, разметьте отверстия, просверлите и прикрепите их к основанию червячной передачи, как показано на видео. Также убедитесь, что вы добавили главную шестерню, прежде чем надежно закрепить ее болтами.
Источник: Интересные разработки / YouTubeПеред тем, как двигаться дальше, проверьте снаряжение. Он должен двигаться свободно с некоторым сопротивлением.
Отшлифуйте под углом один конец осей червячной передачи и прикрепите шкив подходящего размера, как показано на видео. Плотно закрепите.
Источник: Интересные разработки / YouTubeТеперь возьмите еще один кусок металлического листа и свой асинхронный двигатель. Закрепите двигатель на металлическом листе, как показано. Кроме того, прикрепите основной механизм лебедки к тому же стальному листу, как показано.
Источник: Интересные разработки / YouTubeСоедините двигатель и лебедку в сборе с помощью резинового ремня ГРМ. Перед закреплением лебедки на месте убедитесь, что ремень натянут.
Возможно, вам потребуется разметить и просверлить отверстия для болтов.
Источник: Интересные разработки / YouTubeВключите двигатель и проверьте, плавно ли вращается механизм лебедки. При необходимости отрегулируйте.
Затем возьмите кусок металлического стержня и просверлите отверстие посередине на токарном станке.
Источник: Интересные разработки / YouTubeДиаметр отверстия должен быть таким же, как диаметр выступающей оси червячного зубчатого колеса лебедки в сборе. При необходимости закрепите его плотно гайкой (возможно, потребуется просверлить отверстие через ось и длину трубы).
Источник: Интересные разработки / YouTubeТеперь возьмем два стальных диска и еще одну длинную трубку с широким отверстием. Эти колеса будут использоваться для удержания подъемного троса. Соберите, как показано на видео — потребуется механическая обработка и сварка.
Источник: Интересные разработки / YouTubeЗатем вставьте и приварите трубку, которую вы сделали ранее, к центру держателя подъемного троса. Сваривайте надежно, как показано на видео.
Источник: Интересные разработки / YouTubeУстановите его на место и надежно закрепите на главном механизме лебедки. Создайте и прикрепите крепежную пластину (с шарикоподшипником) для другой стороны троса подъемного механизма.
Источник: Интересные разработки / YouTubeЕще раз убедитесь, что все движущиеся части свободно перемещаются.При необходимости приварите компоненты к опорной плите. Используйте несколько L-образных металлических полос, чтобы построить монтажные рельсы для всей сборки.
Приварите к основанию, как показано.
Источник: Interesting Engineering / YouTubeПри необходимости добавьте поперечины для увеличения прочности между монтажными рельсами. Теперь обмотайте стальной кабель вокруг держателя кабеля, как показано на видео. Убедитесь, что он надежно закреплен.
Чтобы облегчить эту задачу, возьмитесь за кабель за один конец и включите двигатель на малой скорости, чтобы намотать кабель.
Источник: Интересные разработки / YouTubeПрисоедините шкив подъемника и зацепите за свободный конец троса (если к тросу не прилагается). Теперь сделайте подпружиненную прижимную пластину троса подъемника, используя запасные металлические пластины и пружину.
Приварите к опорной плите.
Источник: Интересные разработки / YouTubeНа этом ваш подъемник фактически готов.
Теперь просто настройте свой подъемник, убедитесь, что он надежно закреплен, и начните тестирование пределов его грузоподъемности.Тот, что на видео, поднимает вес более 396 фунтов (180 кг).
Счастливого подъема!
Interesting Engineering является участником партнерской программы Amazon Services LLC и различных других партнерских программ, поэтому в этой статье могут быть партнерские ссылки на продукты. Нажимая ссылки и делая покупки на партнерских сайтах, вы не только получаете необходимые материалы, но и поддерживаете наш сайт.
Как анодировать алюминий в домашних условиях — сделать его из металла
В одном магазине, в котором я работал, мы регулярно отправляли вещи на термообработку, анодирование, оцинковку, гальванизацию и так далее.Если вы хотели, чтобы что-то было сделано для личного проекта, просто отложите это в кучу и наберитесь терпения.
К сожалению, я больше не работаю в этом магазине. Там, где я сейчас нахожусь, на самом деле довольно редко можно получить что-то анодированное. Так что для моих собственных небольших проектов я провел небольшое исследование, как я могу осуществить это дома, в моем гараже.
Я обнаружил, что информация действительно разрознена. Вот почему я собрал все, что узнал, в эту статью. Это должно быть все, что вам нужно для начала.
В этом посте я расскажу о том, что я узнал о том, как добиться успеха, а также дам несколько советов и приемов, которые помогут вам в этом.
Заявление об ограничении ответственности: У меня есть , которые сделали это профессионально, но делать это дома — совсем другое дело. Ожидайте, что потребуется несколько попыток, прежде чем вы сделаете процесс правильным.
Что делает анодированный алюминий?
Вероятно, неплохо было бы начать это руководство с того, чтобы понять, в чем заключается процесс.Это поможет вам понять, что происходит и почему это важно, по мере прохождения этапов.
Для чего нужен анодированный алюминий? Анодирование алюминия создает тонкий слой оксида алюминия на металле. Этот защитный оксидный слой имеет более грубую поверхность, что позволяет красителям или краскам прилипать к металлу. Он тверже алюминия, поэтому обеспечивает определенную защиту. Это также придает алюминию коррозионную стойкость. Поскольку это такой тонкий слой, который окисляется, его можно наносить на прецизионные детали с минимальным влиянием на геометрию.
Это также обычно делается для косметики, даже если детали не подлежат окрашиванию или окрашиванию. Анодирование придает алюминию матовый светло-серый цвет. Он также не подвергнется коррозии от таких вещей, как соль на ваших руках, и со временем оставит мутные пятна, похожие на яркий алюминий.
Что вам нужно
Сам процесс анодирования не так уж и сложен, и его не так дорого наладить (я знаю, все относительно).
Это то, что вам нужно для анодирования алюминия:
- Источник питания с соединениями
- Кислота
- Дистиллированная вода
- Катод
- Емкость
- Краситель (нужен только в том случае, если вы хотите сделать его другого цвета)
- Алюминиевая или титановая проволока
- Обезжириватель
- Кислотный нейтрализатор
- Мешалка (опция)
- Защитное снаряжение
- Вентилируемое место для работы
Многое из этого можно убрать, но некоторые вещи работают лучше, другие.Я рассмотрю несколько вариантов того, что можно использовать здесь, чтобы помочь вам установить бюджет. По крайней мере, вы будете знать, чего ожидать, и не будете тратить деньги на то, что не сработает.
Установка для мелкомасштабного анодирования
Если анодирование — это то, что вы хотите делать довольно часто и не возражаете потратить немного денег, то это то, что имеет смысл.
Полные комплекты бывает сложно найти в Интернете, иногда их нужно покупать отдельно.
Вот краткий обзор того, что доступно.Если это не то, что вас интересует, просто переходите к следующему разделу, посвященному более самостоятельному подходу. Спойлер: маршрут «Сделай сам» даст вам очень неоднозначные результаты.
Примечание: Онлайн-цены колеблются, поэтому я мог бы написать эту статью сегодня, а завтра они будут другими. Я изо всех сил старался дать довольно хорошее представление о том, для чего нужны эти штуки, но в этом случае не упираюсь в огонь! Бюджет находится в конце раздела передач.
Источник питания
В общем, вы ищете что-то, способное выдавать около 18 В и выше.
Сила токаважна в зависимости от площади поверхности детали, которую вы хотите анодировать. Однако это немного легче сбалансировать, поскольку вы можете компенсировать это, просто бегая на нем дольше. В любом случае вам, вероятно, понадобится хотя бы один усилитель для небольших декораций и виджетов.
Вы можете найти приличные источники питания в Интернете по цене от 60 до 100 долларов. Плюс в том, что эти источники питания универсальны — вы можете использовать их и для других вещей, например для покрытия.
Это тот, который я бы порекомендовал забрать.Он рассчитан на 30 вольт и 5 ампер, поэтому он подойдет для большинства проектов, площадь которых составляет около одного квадратного фута. В нем также есть несколько красивых зажимов из крокодиловой кожи, которые облегчают жизнь для таких проектов.
Как правило, вам нужно примерно от 0,02 до 0,03 ампер на квадратный дюйм площади поверхности детали.
Если вы хотите использовать MacGyver в своей настройке, возможно, вам удастся обойтись без автомобильного зарядного устройства большего размера. Преимущество этого в том, что у вас уже может быть такой, который будет работать.Недостатком является то, что у вас нет почти такого же контроля над мощностью, вам будет сложно настроить процесс, чтобы все было правильно. Анодирование может быть непростым делом.
Кислота
Самая распространенная кислота, которую вы встретите в гаражах, — это серная кислота. Обычно вы можете найти его примерно за 40 долларов за полтора галлона.
Совет от профессионала: Аккумуляторная кислота — это, по сути, серная кислота, но, вероятно, она также имеет несколько присадок.Для наших целей это прекрасно работает. Обычно вы можете получить его немного дешевле, чем лабораторный. Вот пример того, что будет работать на Amazon.
Это необязательно, но использование действительно сильной кислоты может быть хорошим способом подготовить алюминий и удалить любой оксид, который может быть на нем. Щелок отлично работает, и он дешевый. Вам не нужно много этого.
Краситель
Многие интернет-ресурсы говорят, что просто используйте краситель для ткани, если вы хотите покрасить анодированную деталь.Исходя из моего опыта, этот обычно работает как надо, , но не всегда. Иногда цвета действительно нечеткие — синий может выглядеть фиолетовым, фиолетовый может выглядеть розовым и т. Д.
Но если вы не слишком привередливы, краска для одежды стоит довольно дешево. Обычно вы можете получить его за несколько долларов в Интернете.
Если вы хотите убедиться, что это работает должным образом, просто возьмите подходящий краситель для анодирования. Вот пример того, что отлично подойдет. Хороший краситель обычно стоит около 20 долларов за бутылку, в зависимости от того, где вы его купите.
Катод
Технически для этого можно было бы просто использовать кусок алюминия, но свинец работает лучше и служит долго. Я получил наилучшие результаты, используя листовой свинец, так как он имеет такую большую площадь поверхности.
Вы можете просто взять свинцовую огранку в домашнем центре или взять листок на Amazon. По сути, это будет разовая покупка, так как качество свинца на самом деле не ухудшается.
Контейнер
Пластиковые контейнеры отлично работают.Не нужно обдумывать это. Для деталей среднего или большего размера используйте красивое и чистое ведро из полиэтилена высокой плотности на 5 галлонов. Для действительно мелких вещей вы можете использовать контейнер для посуды или даже стеклянную банку.
Просто выберите что-нибудь, что не проводит электричество и может сопротивляться кислоте.
Стеллажи для проволоки
Для фиксации детали можно использовать алюминиевую или титановую проволоку. Я очень предпочитаю использовать титан. Вот почему.
Стеллажи должны надежно проводить электричество.Оксид алюминия не проводит электричество.
Это означает, что если вы используете алюминиевую проволоку, она также будет анодирована. Титан — нет. Таким образом, титановый провод можно не только использовать повторно, но и с меньшей вероятностью потерять соединение во время процесса.
В любом случае оба провода будут работать, и они не будут стоить много. Можно подобрать титановую проволоку (чуть дороже) или алюминиевую (дешевле). Честно говоря, если вы планируете анодировать несколько деталей, просто возьмите титановую проволоку.
Обезжириватель
Здесь нет ничего лишнего, просто что-то, что удалит жир или масло с детали, чтобы сделать ее красивой и чистой. Возможно, в вашем гараже уже есть что-то хорошее. Это будет отлично работать.
Кислотный нейтрализатор
Используйте пищевую соду. Работает как шарм.
Мешалка
Это необязательно, но это хорошая идея. В основном это предотвращает прилипание пузырьков к детали во время анодирования и оставление небольших следов.Если вы хотите, чтобы детали выглядели безупречно, есть простой, но чрезвычайно эффективный прием.
Используйте воздушный насос аквариума. Если вы не можете «одолжить» одну из аквариума вашего ребенка какое-то время, вы можете проверить текущую цену на Amazon здесь.
Защитное снаряжение
Это важно. Вам понадобятся средства защиты глаз, респираторная маска от химикатов и перчатки.
Я видел, как многие люди используют простую респираторную маску, когда делают подобные вещи. Я бы действительно не рекомендовал это, поскольку маски от пыли не задерживают дым, а только частицы.
Это маска, которая работает хорошо, она не слишком дорогая и поможет избавиться от паров. В комплекте также есть защитные очки на случай, если у вас их еще нет. Кислота в глаза — отстой.
Дело не в том, что пары слишком токсичны, но лучше не вдыхать их.
Вам также понадобятся перчатки. Я предпочитаю нитрил, и вы можете получить коробку совсем недорого. Это сделано не только для защиты рук от кислотных ожогов, но и для предотвращения попадания масла на детали.Если прикоснуться к детали голыми руками, после анодирования останутся постоянные следы пальцев.
Разное Handy Stuff
Есть несколько вещей, которые необязательны, но действительно помогают вам делать хорошую работу.
Шарики для пинг-понга могут плавать над кислотной смесью. Это довольно хорошо устраняет кислотный туман, который вы получите, когда в резервуаре начнут пузыриться во время процесса. Вы можете купить в Интернете упаковку из 50 штук, которой хватит на весь срок службы анодирования.
ПодушечкиScotch brite — хороший способ сделать поверхность красивой даже до анодирования. Не требуется, но если вы анодируете обработанные детали, все отметки будут видны. Это просто придает детали более профессиональный вид. Вы можете купить большую их упаковку, которая прослужит вам некоторое время с отличным соотношением цены и качества. Я все время использую этот материал для разных проектов, поэтому у меня всегда есть запас на полке.
Чайник для разогрева краски (если вы хотите раскрасить детали).Большинство красителей должны иметь температуру около 120-140 F или около того, когда вы окунаете деталь, и использование электрического чайника делает этот шаг действительно простым. Вы можете купить дешевый на Amazon. Только не используйте его после заваривания чая.
Обогреватель аквариума позволит вам регулировать температуру в аквариуме. Вы хотите, чтобы он был как можно ближе к 70F. Если вы делаете это в помещении с контролируемой температурой, это не критично. Если вы делаете это в неотапливаемом гараже, я очень рекомендую. Вы можете узнать цену на Amazon здесь.
Термометр для мяса позволит вам быть уверенным в своей температуре. Это также очень удобно для проверки температуры красок. Не обязательно, но хорошая идея. Вы можете получить его по дешевке в Интернете.
Всего
Скорее всего, у вас в гараже есть немало этих вещей, или вы можете поискать. Но если вам нужно покупать абсолютно все новое, вот разбивка того, чего ожидать, если вы платите за все довольно среднюю цену.
Источник питания | 80 долларов США | |||
Серная кислота | 40 долларов США | |||
Щелок | 5 долларов США | |||
Краситель | 9040 Gallon 9040 9040 Gallon | |||
$ 25 | ||||
Титановая проволока | $ 10 | |||
Обезжириватель | $ 15 | |||
Пищевая сода | $ 2 | $ 25 | ||
Коробка нитриловых перчаток | $ 10 | |||
Шарики для пинг-понга | $ 10 | |||
Пакет подушечек Scotch Brite | $ 20 | |||
Чайник | ||||
Нагреватель | $ 15 | |||
Термометр | $ 2 904 02 | |||
Дистиллированная вода (местного производства) | 5 долларов | |||
ИТОГО | 317 долларовРазумное количество этого материала не является обязательным, и вы также можете купить его в меньших количествах, если хотите. Но начиная с нуля, это установка, которая позволит вам сделать действительно качественное анодирование прямо в вашем гараже. Многие парни используют подобные установки для изготовления деталей, которые они продают в Интернете. После того, как вы все настроите, обслуживание вашей системы станет совсем не дорогим. Вам нужно будет долить кислоту, щелок, краситель, обезжириватель, пищевую соду, перчатки и скотч-брайт, но вы действительно не так много используете.Этого хватит на время. Анодирование — не дорогой процесс, если у вас есть оборудование. Как анодировать алюминий своими рукамиИтак, как только у вас будет все необходимое, вот пошаговые инструкции, как это сделать. Имейте в виду, что все настройки индивидуальны, и вам нужно будет точно настроить свой процесс, чтобы получить желаемые результаты. Не ждите, что первые несколько раз все получится идеально. Скотч-Брайт АлюминийЭто даст красивую, ровную поверхность, которая будет хорошо выглядеть после анодирования.Это не обязательно, но серьезно делает деталь более профессионально выглядящей. Если не использовать скотч-брайт, следы обработки будут хорошо видны. Деталь будет блестящей на участках с более красивой обработкой поверхности и тусклой на участках, где она не идеальна. Просто после анодирования он становится более заметным. Надень шестеренкуДержите респиратор под рукой. Наденьте защитные очки. Самое главное на этом этапе надеть перчатки !!! Если вы не наденете перчатки, на вашей стороне останутся отпечатки пальцев, и ваше анодирование будет выглядеть ужасно. Очистите деталиДостаньте обезжириватель и чистую тряпку. Поверхность детали должна быть идеально чистой. Когда закончите, промойте часть дистиллированной водой. Протравить деталиДостаньте щелок и смешайте его с дистиллированной водой. Соотношение составляет примерно 3-5 столовых ложек чистого щелока на 1 галлон воды. Убедитесь, что на этом этапе вы надели респиратор и защитные очки, щелок может быть неприятным. Дайте детали впитаться в течение 3-5 минут, затем смойте дистиллированной водой. Проверка чистотыНа этом этапе вы можете провести тест воды на детали, чтобы убедиться, что она очищена должным образом. При правильной очистке вода должна плавно стекать с поверхности детали. Если вы напортачили, вода брызжет на поверхность. Это потому, что на поверхности все еще есть масла. В этом случае повторите процесс очистки. Этот шаг действительно важен. Анодирование подействует только на действительно чистую деталь. Совершенно необходимо, чтобы на этом этапе вы не позволяли детали соприкасаться с чем-либо грязным.Надевайте перчатки на протяжении всего процесса и не кладите деталь на грязную поверхность. Стеллаж для деталейЗакрепите детали на алюминиевой или титановой проволоке. Имейте в виду, что там, где провод контактировал с деталью, останется неанодированная отметка. Большинству парней нравится использовать внутреннюю часть отверстия в качестве точки контакта, чтобы ее не было видно. Один из приемов заключается в том, чтобы скрутить конец проволоки и воткнуть ее в отверстие. Пружинность проволоки проделает отверстие в детали, и на анодированной поверхности не останется видимых следов. Важно одно: вам нужно хорошее соединение. Если соединение ненадежно, процесс гарантированно завершится неудачно. Поскольку оксид алюминия не проводит электричество, вам придется вытащить деталь, отшлифовать анодированную поверхность и перезапустить процесс. Какая боль. Налейте ваннуПоместите контейнер в хорошо проветриваемое место. Анодирование работает лучше всего, когда оно проводится при температуре около 70 F. При необходимости дайте жидкости время для акклиматизации. Анодирование при температуре более 75 градусов не даст очень хороших результатов. Сначала налейте в емкость дистиллированную воду. Затем добавьте серную кислоту. Соотношение составляет 1 часть кислоты на 3 части воды. Я знаю, что другие сайты говорят, что нужно делать половину или половину. Они ошибаются. Кислота не должна быть такой сильной. Эта концентрация работает лучше и дешевле. Всегда добавляйте кислоту в воду, а не воду в кислоту. Ожоги могут быть неприятными, если вы все испортите. Настройте GearПоместите свинцовый катод в ванну. Очень важно, чтобы он не касался деталей.Мне нравится, когда им оборачивают внутреннюю часть ведра, чтобы получить красивый, ровный оксидный слой на детали. Понятия не имею, действительно ли это имеет значение или нет, но я этим занимаюсь. Поместите воздушный насос прямо под то место, где будут находиться детали. Чем больше волнений вокруг деталей, тем лучше. Поместите нагреватель и термометр в резервуар. Перед тем, как начать, убедитесь, что температура в ванне максимально приближена к температуре 70 ° F. Подвесьте детали в бак. Обычно я просто кладу кусок плоского стержня на ведро и подвешиваю к нему детали. Убедитесь, что они ничего не трогают! Если вы решили получить шары для пинг-понга, вы можете добавить их сюда. Добавьте достаточно, чтобы покрыть поверхность кислотной смесью. Добавить мощностьНастройте блок питания. Присоедините положительный полюс к проводу на ваших деталях. Присоедините отрицательную сторону к свинцовому катоду. Подсказка: детали — это ваш анод, свинец — это катод. Анодирование = детали — аноды. Детали всегда положительные. Когда все будет выглядеть безопасным, пора включить блок питания.Вот где это становится суетливым. Вы хотите установить силу тока в зависимости от общей площади поверхности ваших деталей. Использование 0,03 ампера на квадратный дюйм даст хорошую твердую поверхность, использование 0,02 ампера на квадратный дюйм даст более мягкую поверхность, но при этом потребуется больше краски. В любом случае, нужно немного поэкспериментировать, чтобы добиться того, чтобы он выглядел именно так, как вы хотите. Попробуйте запустить для запуска при напряжении 16 В. На самом деле, есть целый ряд вычислений, которые вы можете проделать, чтобы получить это теоретически совершенное, но это руководство для новичков.Это достаточно близко, чтобы начать. Кроме того, есть несколько других переменных, которые влияют на расчеты, которые на самом деле сложно добиться с одной из этих домашних настроек. Итак, вот действительно упрощенный калькулятор, который я придумал, и он хорошо мне подходит, когда я делаю это дома. Имейте в виду, что это , а не , который я использую на работе для профессионального управляемого аэрокосмического анодирования, но он, похоже, неплохо работает для этих более домашних установок. Хорошая идея (по крайней мере, хорошая практика) — медленно увеличивать громкость.Это то, чем мы занимаемся профессионально — довольно часто при запуске партии мы увеличиваем скорость на 5 или 10 минут. Вам не нужно действовать так медленно, но просто не включайте мощность мгновенно — не торопитесь, повернув ручку вверх. Установите таймер для любого числа, которое вам дал калькулятор, и сделайте перерыв на кофе! Pro Tip: Если вы анодируете несколько деталей или одну большую деталь, следите за температурой ванны. Он может согреться, если будет усерднее работать. Если вы видите, что температура достигает 75 F или выше, попробуйте сделать что-нибудь, чтобы было прохладнее. Вы также должны убедиться, что он не опускается ниже 60 F. Вот где вам действительно пригодится нагреватель для аквариума. Нагрейте красительДостаньте чайник и разогрейте краситель, проверяя температуру термометром для мяса. Это может быть немного суетливый шаг. Большинство красителей хорошо работают при температуре около 140 F, но некоторые цвета работают немного лучше при более низкой температуре, например, 120 F. Я бы рекомендовал попробовать первую партию при 140 F, а если вы не довольны результатами, попробуйте следующую. немного круче. Подготовьте ваннуХорошо, на этом этапе мы собираемся установить пару ванн. Я знаю, что другие люди могут подойти к этому шагу по-другому, но это то, что мне подходит. Установите одну ванну с дистиллированной водой. Хорошо, если он будет немного больше, чем детали. Например, если у вас есть деталь размером с кулак, используйте как минимум полгаллона дистиллированной воды. Налейте немного дистиллированной воды в распылитель. Не обязательно, но удобно. Затем установите один бак со смесью пищевой соды и дистиллированной воды.Это нейтрализует кислоту и повысит вероятность того, что на деталях не останется никаких пятен. Обычно я использую соотношение 3 столовые ложки пищевой соды на литр воды. За этим нет ничего научного, это просто то, что я делаю. Вам не понадобится тонна этой смеси, ее достаточно, чтобы покрыть части, чтобы они могли впитаться в течение нескольких минут. Затем откройте крышку чайника с краской. Вы можете просто окунуть детали напрямую. Частичное погружениеВыключите питание резервуара для анодирования.Частично приподнимите детали из резервуара и несколько раз обрызгайте их дистиллированной водой. Я распыляю прямо в резервуар, чтобы не было беспорядка. Теперь прополощите детали в баке с дистиллированной водой. Вы просто хотите смыть как можно больше кислоты. Затем поместите детали в емкость для пищевой соды. Слегка взболтайте и оставьте на 5 минут. Теперь снова промойте детали в дистиллированной воде. Будьте внимательны. Дважды проверьте температуру красителя и при необходимости отрегулируйте. Окуните детали в краситель. Размешайте его достаточно энергично, чтобы сбить пузырьки с деталей, но не создавайте большого беспорядка. Этот материал очень сложно чистить. Вы должны увидеть, как детали сразу начинают окрашиваться. Если процесс не сработал, краска просто стечет. Если это сработало, деталь начнет менять цвет. Дайте деталям впитаться в краситель на 10-15 минут. Позже вы можете точно настроить время выдержки в зависимости от желаемой глубины цвета. УплотнениеЭта часть действительно проста. Как только краска пропитается, варите детали около 15 минут. Здесь пригодится либо дополнительный чайник, либо плита, на которой можно вскипятить кастрюлю с водой. Это только сделает краску более жесткой и уменьшит вероятность того, что краска обесцветится или легко оторвется. Даже если вы не красили детали, это хорошая идея. Готово, процесс завершен! В целом, мне очень нравится анодировать дома.Вероятно, потребуется немного практики, чтобы получить детали, которые должным образом анодированы и не имеют дефектов, но это действительно крутой процесс. Также очень весело настраивать и настраивать то, как вы это делаете, чтобы вы могли получить именно тот вид, который хотите — существует множество переменных, и каждая из них влияет на внешний вид детали в конечном итоге. Анодирование пробовали? Каковы были ваши результаты, и отличается ли ваш процесс от моего? Или есть вопросы? Размещайте их в комментариях! Связанные вопросыЧто такое твердое анодирование? Жесткое анодирование — это процесс, в котором используется более высокий ток и выполняется при более низкой температуре.В результате получается значительно более толстый оксидный слой, часто около 0,002 дюйма. Этот слой чрезвычайно твердый и может значительно повысить износостойкость и коррозионную стойкость алюминия. Требования к этому процессу намного выше, и не все отделочные предприятия имеют такую возможность. При твердом анодировании следует учитывать то обстоятельство, что из-за большой толщины оксидного слоя это вызовет заметные изменения размеров прецизионных компонентов. Сколько стоит профессиональное анодирование? Чтобы получить что-то профессионально анодированное, потребуется минимальная плата, цена за квадратный дюйм площади и, возможно, плата за стеллаж.Конечно, это будет сильно варьироваться в зависимости от местоположения и объекта, но вы можете ожидать от 75-125 долларов за меньшую партию. Хорошее эмпирическое правило для определения «небольшой партии» — это все, что вы можете носить в коробке. Truckload = наверное не маленькая партия. City Scrap Metal Inc. | МеталлоломCOVID-19 Обновление Мы понимаем, что находимся на Lees Summit, но используем рекомендации Core 4 и KCMO. Мы принимаем все меры, чтобы обеспечить безопасную среду для наших сотрудников и клиентов. Мы внедрили следующую Политику по обеспечению социального дистанцирования в 6 футов между сотрудниками и клиентами:
Алюминиевая банка для напитков Процедура Клиенты будут извлекать алюминиевые банки для напитков из своих пакетов или других контейнеров, используемых для доставки алюминиевых банок для напитков.Клиентам рекомендуется приносить собственные маски для лица, резиновые перчатки, защитные очки и любые другие средства индивидуальной защиты. Клиенты помещают свои собственные алюминиевые банки для напитков в предоставленную пустую и продезинфицированную корзину для банок для проверки и взвешивания. Клиенты удаляют все загрязнения из своих алюминиевых банок для напитков. City Scrap Metal предоставит клиентам продезинфицированный механический захват для удаления загрязнений из алюминиевых банок для напитков. Только пустые алюминиевые банки для напитков могут находиться в корзине перед взвешиванием и выгрузкой.Ни фольги, ни стальных банок, ни пластиковых бутылок, ни мусора. Только пустые алюминиевые банки из-под напитков. Дезинфицирующее средство для рук будет предоставлено клиентам для мытья рук после того, как они поместят свои алюминиевые банки для напитков в специальные корзины и удалят загрязнения. После того, как алюминиевые банки для напитков прошли проверку, корзина будет взвешена, и будет составлен билет, показывающий вес нетто (вес брутто за вычетом веса корзины для банок) алюминиевых банок для напитков клиентов. Этот билет можно обменять на деньги в зависимости от текущего рынка использованных алюминиевых банок для напитков за вычетом наших затрат и прибыли. При условии, что корзины для консервных банок будут сбрасываться в контейнер для скатывания с помощью шеста, чтобы руки не касались банок или корзины для консервных банок. Любые банки, выпавшие из рулона, будут подбираться механическим захватом без помощи рук. Сразу после сброса; корзина, механический захват и шест будут продезинфицированы, прежде чем другой клиент или сотрудник сможет воспользоваться корзиной, механическим захватом или шестом. Сотрудники City Scrap Metal всегда должны следовать всем рекомендациям CDC по правильному мытью рук и другим необходимым шагам, чтобы оставаться здоровыми. В City Scrap Metal Inc. мы увлечены нашей Землей и ценными ресурсами, из которых она состоит. Создание более экологичного мира является движущим фактором в нашей переработке цветных и черных металлов. Наша миссия — продлить срок службы ресурсов Земли и обеспечить конкурентоспособные цены и качественные услуги, при этом безопасность и окружающая среда являются приоритетом во всем, что мы делаем. City Scrap Metal Inc. — компания по переработке металлолома. Берем мелкие и крупные партии цветных и черных металлов.Затем мы разделяем, очищаем и упаковываем материал, получая сырье для предприятий по производству первичного и вторичного металла в США и за рубежом. Звоните, чтобы узнать подробности! Как начать сварку1. Выберите свой методНе существует единого процесса сварки, подходящего для всех областей применения, поэтому вам необходимо учитывать следующие факторы: тип и толщина металла, который вы свариваете, насколько велика работа, выполняете ли вы сварка в помещении или на открытом воздухе, внешний вид сварных швов и ваш бюджет. На сегодняшний день наиболее широко используемой формой сварки является электродуговая сварка, при которой электрическая дуга плавит электрод (например, сварочную проволоку) и частично плавит основной металл. Когда расплавленный металл остывает, детали соединяются. Существуют разные виды дуговой сварки, но мы сосредоточимся на MIG (металлический инертный газ). Сварка с подачей проволоки — самый простой в освоении вид, особенно если вы учитесь сами. Металлический инертный газ (MIG) Использует сварочный пистолет, который непрерывно подает проволоку с катушки, когда оператор нажимает на спусковой крючок.Сварочный пистолет одновременно с проволокой подает защитный газ, защищающий металл от загрязнений в воздухе. MIG дает более чистые и качественные сварные швы, чем сварка штучной сваркой. Дуговая сварка порошковой проволокой (FCAW) Аналогично MIG, за исключением того, что здесь нет отдельного защитного газа, потому что проволочный электрод имеет флюс в его сердечнике, который создает свой собственный экран при плавлении проволоки. Эта ветрозащитная установка делает FCAW хорошим методом сварки на открытом воздухе. 2. Купить оборудованиеСварщик Сварщик — это ваши самые большие расходы, поэтому не обманывайте себя — дешевый сварщик только расстроит вас и затруднит обучение. Сварочный аппарат с механизмом подачи проволоки использует обычный бытовой ток для получения очень горячей электрической дуги высокой энергии. Внутри аппарата находится небольшая катушка сварочной проволоки (электрод) с приводом от двигателя. Проволока подается по шлангу к пусковой горелке.Когда оператор соприкасается проволокой с основным металлом, дуга плавит проволоку и частично плавит основание. При сварке MIG, пока спусковой крючок нажат, горелка продолжает подавать проволоку и газ. Lincoln Electric Power MIG 210 (вверху) — это новая технология по отличной цене: при напряжении 120 или 230 В он позволяет амбициозному новичку выполнять сварку MIG, TIG и сваркой стержнем. Стоит он 999 долларов. Миллерматик 141 (ниже) по цене 767 долларов — хороший начальный вариант. Это сварочный аппарат с подачей проволоки на 120 В, который можно использовать для сварки тонкого алюминия и стали толщиной от 24 до 3/16 дюйма. Совет: у вашего сварщика также выходит рабочий провод. Это электрический кабель с зажимом на конце, который крепится к основному металлу и замыкает электрическую цепь, необходимую для сварки. Если грязь, ржавчина или краска мешают контакту свинца, качество сварного шва ухудшится. Проволока сварочная Проволока относительно недорогая. Простое практическое правило — использовать тонкую сварочную проволоку на тонком листовом материале и увеличивать диаметр проволоки по мере увеличения толщины материала.Сварщик берет проволоку как минимум двух диаметров.
В руководстве по эксплуатации машины указано, что для этого нужно, и обычно инструкции находятся на откидной панели сбоку машины. Все это на удивление интуитивно понятно. Газ Выбор подходящего защитного газа важен, поэтому убедитесь, что вы знаете, какой тип работы вы планируете выполнять. Вы можете получить многоразовый баллон с газом у местного поставщика сварочных материалов.Пси будет варьироваться в зависимости от типа горелки, которую вы используете, и глубины сварных швов, но обычно вы будете придерживаться значений от 15 до 25. Что касается газовой смеси, домашний любитель со сварочным аппаратом с подачей проволоки может это сделать. Обычно обходятся 100-процентным защитным газом CO2. Для получения более чистого сварного шва используйте 75 процентов CO2 и 25 процентов аргона. Сварочная тележка : Сварочные аппараты с механизмом подачи проволоки могут весить до 75 фунтов, поэтому сделайте или приобретите сварочную тележку, чтобы повысить портативность. Шиловая или твердосплавная палочка : для разметки линий реза. Угловая шлифовальная машина : для шлифования, снятия фаски и правки сварных швов, а также для подготовки поверхности. Зажим под углом или магнитный квадрат : для фиксации стыков. Отбойный молоток и проволочная щетка : для очистки от шлака и брызг. Сварочные клещи : для обрезки сварочной проволоки и удаления брызг с сопла сварочной горелки. Почему вам нужен шлем с автоматическим затемнением : Свет, генерируемый любым процессом дуговой сварки, невероятно яркий, и он обожжет вам глаза, если вы не наденете шлем.В течение многих лет традиционные сварочные шлемы имели постоянно затемненную шторку для обзора, но это означало, что вам приходилось поднимать маску, когда вы не выполняли сварку. Новые шлемы с автоматическим затемнением защищают от вредного излучения света, автоматически затемняя их прозрачные линзы до предварительно выбранного оттенка за миллисекунды, используя технологию ЖК-дисплея в их стекле. У каждого шлема также есть элементы управления для индивидуальной настройки. Сварочный шлем Antra AH6-660-0000 с автоматическим затемнением на солнечной энергии, показанный выше, предлагает множество опций, от 45 до 109 долларов, в зависимости от размера линзы. 3. Подготовка сварного шваПодготовьте металлы Используйте проволочную щетку и ацетон для удаления масел и грязи. Если вам нужно разрезать металл, наметьте линию шилом или твердосплавной палочкой и обрежьте ее отрезной пилой по металлу, ножовкой или болгаркой с отрезным кругом. Отшлифуйте кромки Но только те, которые вы планируете соединить, и используйте угловую шлифовальную машину. Это называется снятием фаски. Фаска — это скос между смежными краями двух кусков материала, обычно под углом 45 градусов.Это создает пространство для наполнителя и обеспечивает большую структурную целостность сварного шва. Это особенно полезно для стыковых швов.
Разместите металлы С помощью углового зажима или магнитного угольника закрепите соединения, чтобы металлические части оставались в одной плоскости, прежде чем начинать сварку. Совет : вы имеете дело с искрами, огнем и расплавленным металлом, поэтому не начинайте сварку, не надев сварочную куртку или фартук, кожаные перчатки и шлем.Если вы хотите сэкономить, качественную хлопковую рабочую рубашку с длинным рукавом можно заменить курткой для сварщиков. Не забудьте рабочие ботинки (без кроссовок) и снимите украшения с запястий и шеи. При шлифовании надевайте защитные очки и маску, закрывающую все лицо. Также держите поблизости огнетушитель ABC. 4. Создание слоев сварного шваПоложение тела и рук Думайте о сварочных движениях как о качелях для гольфа — вам нужно как можно меньше движущихся частей, и вы хотите, чтобы движение было плавным и повторяемым.По возможности держите сварочный пистолет двумя руками или используйте запястье другой руки, чтобы направить руку, держащую сварщика (представьте себе бильярдный удар). Выключив сварщика, сделайте пробный запуск, чтобы убедиться, что вы правильно расположили его. Чем устойчивее ваши руки, тем лучше сварной шов. Прихваточная сварка Перед запуском проверьте пистолет. Проволочный электрод должен выступать от 1/4 до 3/8 дюйма. Убедитесь, что на сопле нет брызг и кончик проволоки чистый.Затем сделайте несколько прихваточных швов, достаточных для соединения основных металлов вдоль стыка. Последний валик После того, как вы закрепили металлы на месте, вы можете уложить последний валик сварного шва. Держа сварочный пистолет под углом примерно 75 градусов к основанию, медленно двигайтесь слева направо (если вы правша), затрачивая одну-две секунды на укладку каждого валика и поддержание постоянной длины дуги. Не зацикливайтесь на яркой дуге. Посмотрите на край сварочной ванны, и когда вы дойдете до конца сварного шва, оттяните электрод от металла и дайте ему остыть. 5. Шлифовка сварного шваЕсли вам все равно, как выглядит ваш сварной шов, или если он находится на куске металла, который не будет виден, когда ваш проект будет завершен, вы можете пропустить этот шаг, потому что все готово. Поздравляю, вы сделали первые сварные швы. Работайте над совершенствованием своей техники на металлоломе. Сварка во многом похожа на игру на гитаре: немного сделать это несложно, но чтобы стать профессиональным, вам нужна практика, практика, практика. Сварные швы, шлифование заподлицо Для получения гладкой поверхности используйте шлифовальный круг с зернистостью 36, прикрепленный к угловой шлифовальной машине, чтобы шлифовать вдоль пути сварки, а не поперек, для однородности. Иди медленно. Если вы шлифуете сварной шов, вам придется начинать заново. При шлифовании должны быть видны только оранжевые искры. Синий означает, что вы слишком сильно нажимаете. Когда вы закончите, возьмите циркониевый лепестковый диск для точной формовки и отделки. Благодаря Майклу Дэниелу из Майкл Дэниэл Metal Design , Нико Хуаресу из Хуарес Custom и Стивену Сомплу из Empire Metal Finishing . Эта история опубликована в июньском номере журнала Popular Mechanics за 2015 год. Этот контент создается и поддерживается третьей стороной и импортируется на эту страницу, чтобы помочь пользователям указать свои адреса электронной почты. Вы можете найти больше информации об этом и подобном контенте на пианино.io Получите снаряжение и что надеть для занятий Little League®Старая поговорка «практика делает совершенство» столь же верна в Малой лиге, как и везде. Для новых родителей из Little League® подготовка игроков к тренировкам поможет убедиться, что они готовы к игре. Что надетьНезависимо от того, тренируется ли ваша команда в помещении или на улице, важно, чтобы дети носили удобную спортивную одежду и выглядели как игроки в бейсбол или софтбол. Для тренировок в начале сезона, когда температура во многих частях все еще остается низкой, убедитесь, что ваш Little Leaguer® носит рубашки с длинными рукавами или толстовку с капюшоном, особенно во время тренировок на открытом воздухе. С переменчивой погодой может возникнуть соблазн надеть шорт на вашего члена Малой лиги. Тем не менее, с учетом того, что дети могут попрактиковаться в скольжении, а дети будут пачкаться, играя наземными мячами и всплывающими окнами, рекомендуется всегда одевать вашего члена Маленькой лиги либо в спортивные штаны, либо в бейсбольные штаны. Убедитесь, что ваш игрок одет в соответствующую возрасту одежду.Не должно быть «заявительной» одежды и, без сомнения, ни одна часть практического набора не должна иметь никакого отношения к алкоголю или табаку. Многие родители одевают своего ребенка в старые форменные футболки или футболку / майку своей любимой команды Высшей бейсбольной лиги. При тренировках на свежем воздухе участники Малой лиги должны носить шипы и помнить, что использование металлических шипов или металлических шипов на младших уровнях запрещено. Обувь с формованными шипами следует носить на уровнях Tee Ball, Minor и Major. Essential GearДля игр бейсболисты должны быть в шляпе или козырьке, поэтому рекомендуется потренироваться в одном или другом.Когда ваш член младшей лиги получает свою командную шляпу, он или она должны носить ее на большинстве, если не на всех тренировках. Игроки в софтбол не обязаны носить шляпу или козырек во время игры, но многие так и поступают. Игроки в софтбол должны надевать на тренировку то, что они будут носить во время игры. Убедитесь, что перчатка вашего игрока Little Leaguer имеет соответствующий размер и правильно сломана, чтобы помочь при игре на поле. Если у вас есть вопросы о размере и способах ослабления перчатки, проконсультируйтесь с официальным представителем лиги. У менеджера вашей маленькой лиги могут быть командные ракетки.Если нет, убедитесь, что размер ракетки вашего игрока соответствует размеру. Важно отметить, что с 1 января 2018 года бейсбольная бейсбольная команда младшей лиги будет соответствовать новому стандарту бейсбольной биты США. Никакие летучие мыши, ранее одобренные для использования в играх Малой лиги (бейсбольной младшей лиги и ниже), не будут разрешены для использования в любых играх или тренировках Малой лиги, а также в других функциях, мероприятиях или мероприятиях Малой лиги. Вы можете узнать больше о новом стандарте на LittleLeague.org/BatInfo. Все игроки должны приносить на каждую тренировку шлем ватина.Некоторые лиги предлагают командные шлемы. Если ваша малая лига предпочитает носить собственный шлем, убедитесь, что он одобрен Национальным операционным комитетом по стандартам на спортивное снаряжение (NOCSAE). Мальчики должны носить спортивные шорты или компрессионные шорты под тренировочными штанами и бейсбольными штанами. Если ваш сын ловец, он обязательно должен носить защитный стаканчик. Если дать вашим игрокам из младшей лиги время попрактиковаться с снаряжением, которое они будут использовать в своих играх, они почувствуют себя комфортно и будут готовы к игре.Существует также множество дополнительных элементов защитного снаряжения, от каппы до защиты лица и рукавов, которые родители и игроки могут носить, но не являются обязательными. Поэтому не забудьте посетить местный магазин, например, DICK’S Sporting Goods, до начала сезона Малой лиги, чтобы ваш игрок был готов к сезону. В то время как Маленькая лига рекомендует игрокам носить соответствующую одежду для тренировок и снаряжения, мы уделяем еще больше внимания тому, чтобы младшие игроки веселились и заводили новых друзей от первой тренировки до последней.Удачного сезона в Малой лиге! Интервью с Дэниелом Мелвиллом: каково это — иметь бионическую руку Metal Gear SolidПовысьте уровень технологий и стратегии корпоративных данных на Transform 2021 . Дэниел Мелвилл родился без правой руки. Но 29-летний мужчина из Рединга в Соединенном Королевстве готов сделать несколько «дай пятерок» теперь, когда у него появилась новая бионическая рука. И это не просто бионическая рука. Это настоящий протез, напечатанный на 3D-принтере по мотивам серии видеоигр Metal Gear Solid. Open Bionics и издатель Metal Gear Solid Konami объединились, чтобы создать бионическую руку Venom Snake для Мелвилла, который несколько лет был послом Open Bionics. Я разговаривал с Мелвиллом еще в 2018 году. Компания создала протез на основе персонажа Адама Дженсена из научно-фантастической игры Deus Ex: Mankind Divided. Но это было не так уж и функционально. Это действительно выглядело круто. Новый протез отличается — он позволяет Мелвиллу использовать мышцы руки для активации бионической руки.Он может заставить его делать такие вещи, как поднимать кубик Лего и складывать его. И Мелвилл может использовать новую руку, чтобы играть в некоторые компьютерные игры. Прогресс, достигнутый всего за пару лет, показывает, как мы движемся в мир, в котором сочетаются органические и искусственные объекты, в точности как дизайнеры и писатели, представленные в Deus Ex. Эта игра представляет собой будущее, в котором люди будут дополнять себя искусственными частями тела, такими как мощные бионические конечности. Дженсен помогает искоренить заговор против «аугсов» или улучшенных людей, которых дискриминируют «натуралы».” Мелвилл — первый спикер, который мы наняли для нашего мероприятия GamesBeat Summit 2021, которое состоится 28 и 29 апреля 2021 года. Модератором сессии будет Кейша Ховард, основатель Sugar Gamers. Вот отредактированная стенограмма нашего интервью. Вверху: Даниэль Мелвилл имеет бионическую руку от Konami и Open Bionics. Кредит изображения: Konami / Open Bionics GamesBeat: Как у вас рука? Мне было любопытно, добились ли руки прогресса за то время, когда мы впервые их увидели. Дэниел Мелвилл: Если честно, все сильно изменилось. The Deux Ex one, вы говорили об этом с Крисом? Оригинальный Deus Ex one, когда я был участником этого проекта, был рассчитан только на мою руку. С ними вы можете менять обложки, и это долгий путь. Все это, электроника, датчики и все такое, находится в руке. Раньше все было там, но мне все время приходилось отключать от сети. Он не мог использовать разные схемы захвата и тому подобное. У него было только открытое и закрытое.Это было не так ловко, как сейчас. GamesBeat: Как это работает? В определенный момент вы меняете то, что делаете с рукой, и это помогает вам контролировать это. Melville: Это пульс в руке, мышцы руки. Как бы вы это сделали, я бы его закрыл. Если бы вы так напрягли мышцы, она раскрылась. Это не совсем связано с моим мозгом. Все дело в ваших мышцах. Он читает внутри — датчики здесь. Каждый раз, когда ваши мышцы пульсируют, он определяет то, что вы пытаетесь сделать, а когда дело доходит до реального захвата, вы просто меняете его на другой режим захвата, и он будет знать, что вы делаете что-то новое. GamesBeat: Что это дает вам практически? Melville: Для меня это было много разных вещей. Взять, например, ручку. Я могу этим рисовать. Я выкладываю в свой Instagram видео с произвольными рисунками, как Адам Дженсен. Просто случайные вещи. Мне нравится смотреть, что вы можете с этим сделать. Это довольно ловко. Я могу забрать Лего. Я построил из него конструктор Лего. Это очень полезно для подобных вещей. Он хорош для игр на ПК, но не подходит для игр на консолях.Многие спрашивают об этом. Вы можете держать мышь и все такое, но с контроллером у него нет вращения запястья. На данный момент это вращение вручную. Вот где я хотел бы увидеть это дальше, больше движений запястьями. Было бы здорово увидеть это вместо того, чтобы менять его. Вверху: у Дэниела Мелвилла дома есть 3D-принтер. Кредит изображения: Red Bull GamesBeat: Как они усовершенствовали датчики, считывающие сигналы от ваших мышц? Мелвилл: Честно говоря, я не знаю всех тонкостей.Поскольку большая часть этого состоит из коммерческих секретов, я не знаю всего. Но все изменилось за последние шесть лет — через две недели будет шесть лет с тех пор, как я начал им помогать. В основном это связано с датчиками и двигателями в руке. Я могу держать яйцо, и оно не просто разобьется. Он знает, когда остановиться. GamesBeat: Выглядит неплохо, даже зная, что он напечатан на 3D-принтере. Похоже, что-то изготовленное. 3D-печать прошла долгий путь. Мелвилл: О, массово.У меня нет оригинальной руки Deus Ex. У Open Bionics есть это в своей коллекции. Но у меня здесь одна из моих старых рук. Вы можете увидеть, как менялись обложки. Ничто из этого не имеет значения в том, как вы его используете, но он отлично подходит для тех, кто хочет показать свою индивидуальность. У них есть от Marvel, как у Железного человека. У них есть несколько «Звездных войн». Для кого-то вроде меня, лет за двадцать, иметь руку, связанную с видеоигрой, которую я люблю, — это здорово, но они также подходят для пользователей старшего возраста. GamesBeat: Вы упомянули компьютерные игры.С ним можно управлять мышью? Мелвилл: Да, неплохо. Я уже давно не играю на ПК, потому что стараюсь вести себя хорошо во время блокировки и играть в игры, которые были на моей PlayStation целую вечность. Это немного похоже на все. Чем больше вы практикуетесь, тем лучше у вас получается. Чем больше я использую мышь, тем лучше у меня получается. Но временами это сложно. Я к этому привыкаю. GamesBeat: Как вы раньше управляли консольными играми? Вы использовали что-то вроде адаптивного контроллера Microsoft? Melville: Адаптивный контроллер Xbox был потрясающей идеей, и я удивлен, что PlayStation не сделала этого сама.Но я вырос с отцом, играя в компьютерные игры. В молодости я больше увлекался компьютерными играми. Однако мои друзья собирались покупать консоли, и поэтому — как ни странно, мои родители выиграли PlayStation в тот день, когда она вышла, и они ее продали, потому что у меня есть старший брат. Они думали, что было бы несправедливо, если бы он мог им воспользоваться, а я — нет. Но потом они увидели, как я играю в клубе после уроков. Как это работает — не могу никому показать, пока не сниму это на видео. Но по сути я должен использовать свое колено.Проведя на планете 29 лет, я научился пользоваться контроллером консоли. Он просто адаптируется, разрабатывает, как с этим можно поиграть. На чердаке, в ящике памяти, у меня есть контроллер, предназначенный только для людей с одной рукой. У него были все кнопки на одном контроллере, но он был действительно громоздким. Я подумал: «Какой в этом смысл?» Так что я просто адаптировался. Это одна из тех вещей, где вам просто нужно иметь решимость сделать это. Вверху: Даниэль Мелвилл опробовала бионическую руку Deus Ex: Mankind Divided в 2018 году. Кредит изображения: Red Bull GamesBeat: Как вы играли в компьютерные игры до этого? Были ли у вас другие способы использования клавиатуры? Melville: Когда я начал играть в компьютерные игры, это были больше похожие на кликабельные игры, такие как Theme Hospital, Command & Conquer. Игры, для которых вам не нужны дополнительные элементы управления. В первую игру, в которую я играл, все это было необходимо, мне это показалось довольно сложной. Я использовал левую руку для мыши без привязки, а затем для клавиатуры с тем, что у меня есть.Я играл в Tomb Raider на ПК, и это показалось мне трудным, но чем больше я играл, тем лучше становился. Я просто нашел способ, как это сделать. GamesBeat: Я знаю, что некоторые игры добились успехов. Была ли для вас «Последние из нас, часть 2» более доступной? Melville: Как ни странно, я кое-что сделал для PlayStation Access, касаясь специальных возможностей и прочего. Я не знал, пока не начал этим заниматься, что у них есть отключенный доступ, встроенный в игры вроде этой или Человека-паука.Я просто играл в игру как обычно и получил платину. А потом я подумал: «Вот дерьмо, есть ли для меня более простой способ сделать это?» Я не знал этого до тех пор, пока не начал проводить тестирование. Я играл в игры, как и любой другой человек, и так и остался. Немного странно переходить на Access. Для меня это слишком странно. GamesBeat: Интересно, сколько еще таких людей, как вы, играет в игры и просто выясняет, как это сделать. Я помню, как Microsoft говорила что-то вроде того, что в любой момент времени 20 процентов людей могут столкнуться с проблемой доступности тем или иным образом. Melville: У меня довольно много друзей с отсутствующими конечностями, особенно верхними, и почти каждый из них, которого я знаю, нашел свой собственный способ играть на консоли или ПК. Мой друг Джо, у него тоже есть рука от Open Bionics, и он действительно хорош в ПК. Он в той же ситуации, что и моя рука, но ему не хватает левой, а не правой. Допустим, у вас есть гоночная игра. Он может нажать на курок R намного быстрее, чем я, потому что мне приходится использовать свое колено.Или в стрелялке они могут нажимать R2 намного проще. С другой стороны, в «Человеке-пауке» мне легче играть, потому что с левой стороны нужно делать больше, чем с правой. GamesBeat: Есть ли что-нибудь, что вы хотели бы, чтобы игровая индустрия делала больше в плане улучшения доступности? Мелвилл: Едем. Я чувствую, что PlayStation должна делать немного больше, но опять же, повторюсь, я провел некоторое тестирование в этом отношении некоторых вещей.Что касается доступности, я думаю, что у Xbox все правильно с адаптивным контроллером. Я подумал, что это действительно круто, так почему же PlayStation этого не делает? Надеюсь, они туда пойдут. Вы слышали о компании под названием Special Effects? Я люблю этих парней. Пару лет назад мы вместе с другими людьми устроили игровой джем. Это было тогда, когда я занимался игровым дизайном, до того, как перешел на 3D-печать. Мы устроили 48-часовой игровой джем и собрали много денег на спецэффекты. Я считаю, что это прекрасное дело. Вверху: Даниэль Мелвилльд надела свою бионическую руку нарядом Адама Дженсена из Deus Ex в 2018 году. Кредит изображения: Red Bull GamesBeat: Да, они здесь довольно известны. Melville: До тех пор, пока я не сделал это для них, я никогда о них не слышал, но теперь я проповедую всем, кто не знает о доступности. Если вы думаете, что я могу играть в игры, вы должны увидеть этих людей, которые находятся в гораздо худшем положении, чем я. Это одна из тех вещей, где — если вам бросают вызов, вы пытаетесь.Я лично чувствую, что мы приближаемся к этапу, когда они значительно упрощают доступ к играм для всех, с любым типом инвалидности. GamesBeat: Насколько вы активны в играх? Melville: Было время, когда я думал о том, чтобы заняться Twitch и всем остальным, потому что у меня здесь небольшой бизнес, который я люблю. Я хотел бы больше узнать об этом. Но я и мои партнеры потеряли много бизнеса из-за COVID. Мы все играем в игры, но бывают случаи, когда я прохожу через фазы и просто не прекращаю играть в игры.Я просто не могу перестать играть. А иногда бывают случаи, когда я сильно отдыхаю от этого. В настоящий момент я медленно возвращаюсь к этому. Я бы сказал, что я меньше киберспортсмен. Я нахожу их очень интересными, и я люблю их смотреть. Но я играю онлайн только с друзьями. Я не буду играть в Call of Duty онлайн со случайными людьми. Я просто злюсь. Я из тех, кто предпочитает сюжетные игры. Это больше мое. GamesBeat: Вы заказывали какие-нибудь новые приставки? Мелвилл: Нет, я видел цену и подумал — нет, я подожду.Даже когда PS4 только вышла, я отдал ей полтора года. На момент запуска игр было немного, да и в этот раз не так уж много. Но в первых играх, которые вышли, я подумал: «Вау, это меняет правила игры». Они использовали эти аспекты для первой волны игр, которые вышли на консоли, но никогда больше не использовали их. Что-то вроде Infamous: Second Son, где у вас была аэрозольная краска? Это был отличный способ использовать контроллер, но они больше им не пользуются. Я не понимаю, почему они добавляют вещи, которые никогда не будут использовать. Другая компания, которая, как мне кажется, нуждается в большей доступности, теперь, когда вы заставили меня задуматься над ней, на самом деле является Nintendo. Я не думаю, что они много делают для людей с ограниченными возможностями. Что касается меня, играя в Switch с этим, я буквально нажимаю кнопки. Я один из лучших игроков в Super Smash среди своих друзей, но не могу — мне нравится GameCube. Это моя самая любимая консоль. Кнопки мне идеально подошли, поэтому, когда я играю в Smash, мне приходится использовать те адаптивные, которые они использовали.Я играю на своем Switch с помощью контроллера GameCube, потому что в противном случае кнопки слишком маленькие. Но да, я бы сказал, что Nintendo нужно немного активизировать. GamesBeat: Я помню документальный фильм CNN, который вышел примерно во времена Deus Ex. По этому поводу тоже была конференция. Они продвигали идею дополненных людей, и мне интересно, как далеко это продвинулось за последние несколько лет. Вы вообще за этим следили? Мелвилл: У меня есть. Я их не виню.Я действительно думаю, что это не за горами в ближайшем будущем, что люди, возможно, — добрых пять или десять лет, но мы приближаемся к этому. Но я действительно волнуюсь. У меня есть люди — особенно вчера, когда пошла волна Metal Gear Solid. У меня на телефоне есть цитаты, которые немного беспокоят. Люди говорят что-то вроде: «Ой, я бы за это отрубил себе руку». Конечно, я не собираюсь бросать им вызов, но это не самое лучшее, что нужно слышать. Если бы я родился с моими руками, моим первым выбором было бы не отрезать их.Но это потому, что мне не хватает конечности. Может, иначе я бы передумал. Но это одна из тех вещей — я действительно думаю, что в будущем люди будут совершенствоваться. Боюсь это сказать, но думаю, что это может случиться. Вверху: предыдущая бионическая рука Дэниела Мелвилла не могла реально управлять вещами. Кредит изображения: Red Bull GamesBeat: Интересно, сможете ли вы нанести довольно хороший сокрушительный удар рукой Metal Gear. Мелвилл: Наверное, смог бы, но, наверное, сломал бы и руку.Через пять или десять лет я мог бы быть Адамом Дженсеном, пробивающим колодец. Он дойдет до этой стадии. В наши дни 3D-принтеры прогрессируют все больше и больше. Я вижу, как это происходит. Open Bionics хочет, чтобы это было удобно для всей семьи и чтобы люди не занимались подобными вещами, а другие компании? Думаю, это случится в будущем. У вас также может быть ракетный удар из Metal Gear. Одна игра, над которой мне бы хотелось увидеть сотрудничество Open Bionics, — это Capcom с Devil May Cry V.Крушитель дьявола Неро. Это такая классная рука. Это еще одна игра, которую я люблю, потому что — не знаю, отмечает ли она ее, но вы чувствуете себя хорошо, зная, что у этого человека в игре крутая бионическая рука. Это только самая новая игра в серии, в которой появился этот персонаж, и я просто влюбился в нее, потому что в ней так много вариаций. Overwatch была еще одной игрой, в которой были крутые дополненные персонажи, такие как МакКри. Наверное, это была единственная игра, в которую я играл онлайн самостоятельно, Overwatch, хотя она немного умерла, пока не вышла Overwatch 2.Там довольно много всего. GamesBeat: Если игровые компании умеют создавать более антиутопический взгляд на предмет, как Deus Ex, что было бы противоположным, более утопическим взглядом на то, где могут развиваться технологии? Где бы вы хотели, чтобы это применялось таким образом, чтобы помогать людям? Интересно, что эти мощные технологические компании видят это на своем радаре и думают об этом, как Microsoft со своим адаптивным контроллером. Если они дойдут до версии 5.0 или 10.0 этого контроллера, возможно, это будет намного более полезно для людей, когда они играют в игры. Melville: Рука Open Bionics в целом, как я уже сказал, — было бы здорово увидеть, как она адаптируется к консольным играм. Я немного удивлен, что Илон Маск ничего не сделал с подобными вещами. Когда я увидел, что он сравнивает себя с Дж. Си Дентоном, я подумал: «О, боже мой». Но я мог видеть подобные вещи, происходящие с крупными компаниями. GamesBeat: Вы спрашивали кого-нибудь о том, думают ли они, что смогут научиться управлять мелкой моторикой для таких, как вы? Движение отдельных пальцев и так далее. Melville: Я разговаривал раньше с несколькими компаниями или людьми, которые проводят исследования по статьям, студентам университетов. Люди, желающие обратной связи. Я не помню имени этого парня, но у него был протез конечности, которым он мог управлять своим разумом. Я представляю, как смешать это с Open Bionics и объединить вместе, и вы сможете что-то делать — когда вышло Mankind Divided и было снято это видео, представьте, было ли это реальным с точки зрения ловкости, возможности играть на пианино и тому подобного.Я вижу, как это происходит. Я также разговаривал с несколькими людьми из университетов и других мест, которые работали над тактильной обратной связью. Допустим, я пожал тебе руку, верно? Я этого не чувствовал. Было бы полезно знать, что я не собирался сокрушать вас, получая какую-то обратную связь. Open Bionics и другие компании занимаются этим, но это не так просто, как думают люди. Если бы это было так просто, все бы этим занимались. Это довольно сложно. Но для меня это было бы следующим этапом получения этой обратной связи.И, в стиле Люка Скайуокера, он может использовать всю руку. Очевидно, у него есть свои пределы. Но меньше, чем раньше. GamesBeat: Сколько новых версий обычно выходит Open Bionics? Это происходит раз в несколько лет или вы видите более частые обновления? Melville: Поскольку я был тестировщиком с первого дня, я лично испытал столько разных версий, что мне никогда не удавалось их сохранить. Они его постоянно обновляют.Но когда вышла Hero Arm, они сказали: «Хорошо, теперь она вышла», и отпустили ее. За последние два с небольшим года после его выхода было намного больше изменений. Не только новые обложки, но и настоящая рука. В нем есть другой мотор. Я покажу вам одну большую разницу. Это новая версия его внутренней части. Это другой тип материала, который используется на 3D-принтерах. Намного более высокая температура. Тот, который у меня здесь, тоже немного отличается. Это более низкая температура.Изменилось одно: раньше он был липучкой, а теперь стал магнитным. Хотя это может показаться незначительной разницей, для меня это огромная разница. Скажем, я ношу поверх него свитер. Если у меня есть липучка, она зацепится за меня по всему телу. Но я бы сказал, что каждый год у них есть новое обновление для руки. Даже большой палец, для кого-то вроде меня, который тестировал это в течение нескольких лет, вы не заметите особой разницы, но есть некоторые различия с точки зрения положения большого пальца, места и способа нажатия.Вот они — не отпечатки пальцев, но и не слишком жесткие и не слишком мягкие. Они стараются максимально приблизиться к ощущениям настоящего пальца. Когда вы берете в руки ручку или что-то в этом роде, теперь это легко и приятно, тогда как с оригиналом было немного сложнее. Он постоянно развивается. Я начал заниматься 3D-печатью шесть лет назад благодаря Open Bionics, Ultimaker и тому подобному, и они тоже сильно изменились. Они становятся доступнее для людей.Одна вещь, которую я хотел бы увидеть в будущем, было бы круто, если … скажем, я сломаю палец. Они могли сказать: «О, мы просто пришлем вам файл, и вы сможете распечатать его и исправить сами». Было бы здорово починить это дома. Вверху: Однажды Даниэль Мелвилл надеется, что он сможет контролировать мелкую моторику пальцев с помощью протеза. Кредит изображения: Red Bull GamesBeat: О каком малом бизнесе вы упомянули? Мелвилл: Я занимаюсь 3D-печатью.Я делаю дизайн для других людей, много разных вещей. Ничего общего с рукой. Я просто вдохновлен Open Bionics. Я использую компьютер, на котором сейчас работаю. У нас есть несколько принтеров. До COVID я проводил семинары, рассказывая о руке, о 3D-печати, о том, что могут сделать дети и взрослые. Это был мой доход, но теперь он перевернулся с ног на голову. На данный момент мне пришлось изменить то, как я все делаю. Вместе со своей второй половинкой, Харриет, я начал искать способ утилизировать отходы от 3D-печати. Мы потеряли много бизнеса из-за того, что делала она.Немного скучно, но мы все переплавляем и перепечатываем. Это все мои отходы. Мы превращаем их в кастрюли и тому подобное и продаем в Интернете, потому что я просто ненавижу расточительство. GamesBeat: Есть ли у вас что-то, что помогает вам с интерфейсом, например голосовое управление? Мелвилл: Нет, я использую его как обычный человек. Думаю, это потому, что я родился в 90-х. Я родился в сфере технологий. Мои родители пытались относиться ко мне так нормально, как считали возможным, стараясь делать все, что делал бы нормальный человек.Если бы я писал, я бы предпочел диктофон. Но когда дело доходит до простых вещей, таких как проектирование, я просто использую мышь. Я действительно не думаю об этом. Теперь, когда вы упомянули все эти вещи, я действительно был слишком строг к себе, делая это слишком сложно. Я сильно отстаю в этих вещах. Но обычно я просто отправляю электронные письма или использую мышь и проектирую. Если бы я писал эссе — большую часть времени я заставлял бы мою половину писать огромные электронные письма. Она в этом хороша. Когда я пошел в школу, я был первым ребенком с ограниченными возможностями до верхней конечности.Так что они подумали: «Что, черт возьми, нам делать?» Они давали мне все это, но я просто хотел делать то, что делают все остальные. Я до сих пор об этом не думал. GamesBeat: Это довольно модно, в стиле Metal Gear. Мелвилл: Мне с ним очень повезло. Я все время говорил Сэмми и всем остальным, а также другим пользователям. «Мы действительно должны попытаться заставить Konami что-то делать рукой». Другие люди спрашивали не о Адаме Дженсене, а о чем-то другом, и я их постоянно беспокоил.Наконец они сказали: «Мы связались с ними, вам будет интересно?» Да, конечно! Я люблю Deus Ex, но это то, о чем большинство людей хотели со мной поговорить. Я хотел начать говорить о других играх. Я предпочитаю быть известным как человек-геймер, а не как человек из Deus Ex. Будем надеяться, что следующим этапом станет еще одно направление видеоигр. GamesBeat: Это фильм из «Звездных войн» с Люком Скайуокером. Мелвилл: Наконец-то получили обложки BB-8 и R2-D2.Никогда не знаешь, когда у них может появиться что-нибудь еще. Мне нравится тот факт, что Open Bionics расширяет горизонты с точки зрения того, что интересует людей. У вас есть игры, фильмы. Я пытаюсь придумать, что еще могло бы быть, когда люди сказали бы: «Мне нужна эта рука из этого, что-то, созданное из этого». GamesBeat: Вы знаете, сколько из этих Open Bionics получают доступ к людям? Мелвилл: На данный момент не знаю. До COVID все было хорошо, но с тех пор стало немного — вы бы хотели задать Крису этот вопрос, потому что у него было бы больше понимания.Я бываю там довольно часто, но не знаю. Думаю, теперь они снова вернулись в нужное русло. Но для всех это был странный год. GamesBeatКредо GamesBeat при освещении игровой индустрии — «там, где страсть встречается с бизнесом». Что это значит? Мы хотим рассказать вам, как новости важны для вас — не только как человека, принимающего решения в игровой студии, но и как фаната игр. Читаете ли вы наши статьи, слушаете наши подкасты или смотрите наши видео, GamesBeat поможет вам узнать об отрасли и получить удовольствие от взаимодействия с ней.Как ты это сделаешь? Членство включает доступ к:
|