Назначение токоприемника: Токоприемники
Назначение, устройство и работа токоприемника — Студопедия
ТОКОПРИЁМНИК ТЛ-13У
· Токоприемником называется аппарат, с помощью которого осуществляется передача электрической энергии от контактного провода к электрооборудованию электропоезда.
Токоприемник состоит из следующих узлов:
· основание, выполненное из стального швеллера;
· подвижной системы, состоящей из нижней и верхней трубчатых рам шарнирно соединенных между собой;
· контактной системы, состоящей из кареток и лыжис накладками;
· механизма подъема и опускания, состоящего из подъемных пружин и пневматического привода со встроенными в него опускающими пружинами.
РАБОТА ТОКОПРИЁМНИКА
· ПОДЪЁМ осуществляется с помощью подъемных пружин при введении в цилиндр привода сжатого воздуха.
· Подъёмные пружины, максимально растянутые, получают возможность сократиться и тем самым осуществить поворот главных валов, соединённых между собой тягами.
· ОПУСКАНИЕ: происходит выпуск сжатого воздуха из цилиндра привода, в результате чего опускающая пружина, разжимаясь, не только компенсирует действие подъемных пружин, но и поворачивает главные валы, тем самым, возвращая подвижную систему в начальное положение (токоприемник опущен). Опускающее усилие выбрано с учетом сил трения в цилиндре.
ТЕХНИЧЕСКИЕ ДАННЫЕ
· Нажатие на контактный провод в диапазоне рабочей высоты:
— при подъеме …………………не менее 6 кгс
— при опускании……………….не более 9 кгс
· Разница между наибольшим и наименьшим нажатием приодностороннем
движении токоприёмника………………не более 1кгс
· Разница между характеристиками при подъёме
и опускании……………………………….не более 2 кгс
· Длительно допустимый ток
— при движении………………. 500 А
— при стоянке …………………50 А
· Номинальное давление воздуха…………….5 кгс/см 2
· Минимальное давление воздуха…………. 3,5 кгс/см 2
· Время подъёма……………………………………. 7-10 сек
· Время опускания……………………………….. 3,5-6 сек
· Полный ход каретки…………………………………50 мм
· Величина поворота полоза вокруг оси не менее…. 30°.
· Проверка горизонтальности полоза производится установкой на середину линейки, длиной 1000 мм с уровнем разности высот по концам линейки не должна быть более 20 мм (в эксплуатации).
· Угольные вставки подлежат замене по износу, когда до стального корпуса остаётся 2-3 мм.
· Образующиеся на угольных вставках трещины и сколы не являются браковочными, если количество трещин не превышает 2-х на одну вставку и при этом крепление вставок не ослабляется; скол вставки не превышает 50% её ширины и 20% высоты.
ИССЛЕДОВАТЕЛЬСКАЯ РАБОТА На тему «Техническое обслуживание, устройство и ремонт токоприемников электровоза»
образовательное учреждение
Саратовской области
«Саратовский техникум отраслевых технологий»
ИССЛЕДОВАТЕЛЬСКАЯ РАБОТА
На тему «Техническое обслуживание, устройство и ремонт токоприемников электровоза»
Выполнил: Студент группы № 35 по профессии «Машинист локомотива» Охотников Никита Андреевич
Руководитель: Мастер производственного обучения
Мунаева Светлана Александровна
Саратов 2019
Введение
Железнодорожный транспорт является основной транспортной системой России. Он должен своевременно и качественно обеспечивать потребности населения в грузовых и пассажирских перевозках и транспортных услугах, а также обеспечивать жизнедеятельность всех отраслей экономики страны и безопасности государства. Железнодорожный транспорт играет большую роль в формировании рынка транспортных услуг и позволяет эффективно развивать предпринимательскую деятельность во взаимодействии с другими видами транспорта, составляющими транспортную систему страны. В условиях развивающихся рыночных отношении особенно важным становится его чёткая организованность, ритмичность и надежность работы, качество предлагаемых услуг. При этом должна быть гарантирована полная безопасность движения, обеспечены сохранность грузов и сохранение окружающей среды.
Электровоз — локомотив, приводимый в движение находящимися на нем тяговыми электродвигателями, которые получают электроэнергию от стационарного источника — энергосистемы через тяговые подстанции и тяговую сеть от контактного провода либо от собственных тяговых аккумуляторных батарей. Выпускаются также комбинированные контактно-аккумуляторные электровозы, которые могут работать как от контактной сети, так и от аккумуляторной батареи. Подавляющее большинство находящихся в эксплуатации электровозов магистральных ж. д. являются неавтономными, т. е. не могут работать без контактной сети. На путях промышленных предприятий часто используются автономные электровозы, не зависящие от контактной сети. Для обеспечения маневровых работ наиболее подходящими являются контактно-аккумуляторные электровозы, которые используются также широко для обслуживания горных выработок, где прокладка контактного провода затруднена или невозможна. Таким образом, эксплуатируемые электровозы могут быть классифицированы по назначению, степени автономности, роду тока в тяговой сети; в зависимости от области использования и конструкции имеют ряд различных направлений .
Общие сведения о токоприемнике
1. 1. Назначение токоприемника
Электровоз получает электрическую энергию через токоприемник, который установлен на крыше на изоляторах и при движении электровоза скользит по контактному проводу, обеспечивая надежный съем тока при различных условиях движения. Контактный провод подвешен в отдельных точках и из-за провисания имеет разную высоту. Токоприемник должен успевать следовать за изменением контактного провода без больших изменений нажатия на контактный провод и тем более не отходить от него.
В зависимости от значения снимаемого тока токоприемники выполняют легкого и тяжелого типа.
Токоприёмник предназначен для передачи с помощью скользящего контакта электрической энергии от контактного провода к электрическому оборудованию электровоза.
Токоприемник Т-5М1 (П-5) предназначен для создания подвижного электрического соединения между контактным проводом и электрическими цепями электровоза. Токоприемники типа П-5 эксплуатируются на электровозах серий: ВЛ10, ВЛ10У, ВЛ11, ВЛ11М, ВЛ80, ВЛ82М [2].
Принцип работы токоприемника
Принцип работы токоприемника поясняется рис. 1. Основание токоприемника несет на себе нижние рамы 2, валы 1 которых поворачиваются в подшипниках. С нижними рамами шарнирно соединены верхние рамы 3. В верхней части эти рамы соединены между собой и с кареткой 5, с которой связаны полозы 4, скользящие по контактному проводу.
Рисунок 1 – Принцип работы токоприемника
1-валы;
2-нижние рамы;
3-верхние рамы;
4-полозы;
5-каретка;
6- ушки;
7- тяга;
8-пружина
Валы 1 поворачиваются под действием пружины 8, которая, стремясь сжаться, передает усилие на ушки 6, поднимает рамы и создает нажатие на контактный провод. Синхронность поворота обоих валов и работу рам без перекосов обеспечивает тяга 7, соединенная с ушками 6 [3].
Конструкция токоприемника п-5
На электровозе ВЛ10 установлено два токоприемника П-5. Основание токоприемника 8 (рис. 2) сварено из двух боковых продольных швеллеров и двух поперечных швеллеров, между которыми в средней части проложены и приварены два продольных уголка. К этим уголкам крепят воздушный цилиндр 11 приводного механизма с редуктором 10 и шарнир подъемного рычага. На каждом боковом швеллере укреплено по кронштейну с буфером 12, смягчающим удары подвижных рам при опускании токоприемника, а также по две полуоси 9. На полуось 1 (рис. 3), укрепленную с помощью хомутов 2 на швеллера основания 3, посажен шариковый подшипник 4, находящийся внутри вала 5 нижней рамы. Вал выполняют из трубы с наружным диаметром 89 мм.
Рисунок 2 – Общий вид токоприемника П5
1-полуось;
2-хомуты;
3-швелллера основания;
4-шариковый подшипник;
5-вал;
6-промежуточная тяга;
7-конические трубы;
8-основание токоприемника;
9-полуоси;
10-редуктор;
11-воздушный цилиндр;
12-кроншштейн с буфером;
13-пружины
К валу приваривают два конических кронштейна, на которые надевают конические трубы 7 (см. рис. 2) нижней рамы и закрепляют каждую из них двумя болтами. Кроме того к валам приваривают ушки для крепления пружин 5, тяг 6 и рычагов. Конические трубы изготовляют сваркой; из тонколистовой стали толщиной 1,5 мм. Концы труб меньшего, диаметра нижней рамы соединяют с трубами верхней рамы 4 через шарниры с шариковыми подшипниками. Каждая верхняя рама выполнена из трех тонкостенных стальных труб наружным диаметром 30 мм и толщиной стенки 1 мм. Две трубы — боковые и одна — диагональная соединены между собой стальными хомутами. Верхние шарниры боковых труб через игольчатые подшипники соединены с осями, укрепленными по концам распорки 2, фиксирующей расстояние между боковыми трубами рамы в верхней части.
Рисунок 3 – Узел подшипника нижней рамы
1-каретки;
2-распорки;
3-полозы;
4-рамы;
5-шарниры
По концам этих осей находятся каретки 1 с полозами 3. Каретка обеспечивает небольшое перемещение полозов по вертикали относительно верхней рамы, необходимое для следования полозов за небольшими по величине, но резкими изменениями контактного провода по высоте, при прохождении которых рамы токоприёмников не успевают изменить своего положения вследствие сравнительно большой массы. Каретка состоит из основания (рис. 4), состоящего из двух стальных боковин 1, соединенных втулкой 2 и заклепками 10. В верхних концевых частях основания на шариковых подшипниках установлены рычаги, состоящие из шарниров 5, к которым приварены изогнутые трубы 6 и 9 и держатели 7 кронштейнов 8 полозов. Оба рычага составляют клещевидную конструкцию. Рычаги в верхнем положении находятся под действием пружины 3, укрепленной через ушки 4 к хвостовикам шарниров 5. Своими крайними витками пружина входит в отверстия ушек [3].
Рисунок 4 – Каретка токоприемника
1-стальные боковины;
2-втулка;
3-пружины;
4-ушки;
5-хвостиковые шарниры;
6-изогнутые трубы;
7-кронштейны;
8-полозы;
9-держатели;
10-заклепки
При подъеме токоприемника полозы упираются в контактный провод, но под действием подъемных пружин рама продолжает движение и вызывает просадку полозов с рычагами и растяжение пружины 3. При просадке рычагов относительно основания каретки на 50 мм пружина создает силу 8,5—9,5 юге на полоз. Эту силу можно регулировать изменением длины пружины за счет ввинчивания в отверстия ушек.
Кронштейн полоза укреплен на держателе шарнира и может поворачиваться от горизонтального положения на 5—8°. Каретка удерживается в горизонтальном положении пружинами 13 (см. рис. 2) и имеет возможность поворачиваться на небольшой угол за счет их деформации. Пружину с одной стороны крепят к хомуту, укрепленному на трубе верхней рамы, а с другой — к заклепке основания каретки.
Полоз 3 (см. рис. 2) штампуют из листовой оцинкованной стали толщиной 1,5 мм. На его рабочей поверхности укрепляют сменные контактные пластины, которые скользят по контактному проводу. Материал накладок должен иметь малое электрическое сопротивление, быть устойчивым против действия электрической дуги, износоустойчивым и по возможности меньше изнашивать контактный провод.
В настоящее время находят применение медные пластины, металлокерамические пластины на медной или железной основе, а также угольные вставки. Полозы под медные накладки и под угольные вставки имеют различную конструкцию [2].
Рисунок 5 — Крепление угольных накладок
1-полоз;
2-пластина;
3-угольные вставки;
4-пластина;
5-болты
Пластины крепят к полозу винтами М6Х16 с конической головкой, которая утапливается в коническую рассверловку пластины. Угольные вставки 3 (рис. 5), имеющие в сечении к нижней нерабочей части форму «ласточкина хвоста», укрепляют к полозу 1, зажимая вставку между пластинами 2 и 4 болтами 5 размерами М6Х16. Кронштейны полозов с обеих сторон имеют отверстия и приваренные изнутри гайки М10. В полозе против этих отверстий имеются овальные отверстия для упрощения подгонки деталей. Полозы крепят к кронштейнам четырьмя болтами М10.
Все шарнирные соединения и подшипниковые узлы имеют гибкие медные шунты для прохождения тока и предохранения подшипников от разъедания током и нагрева.
Рамы токоприемника поднимаются двумя подъемными пружинами 5 (см. рис. 2). Концы пружин укрепляют на пружинодержателях, имеющих по наружному диаметру винтообразные канавки, на которые навертывается пружина крайними витками. Во внутреннюю резьбу пружинодержателя ввертывается шпилька шарнира, связывающего пружину с ушками валов нижних рам. Для устранения возможного самоотвертывания пружинодержателя на шпильку ставят контргайки.
Токоприемник поднимают с помощью пневматического привода, включающего в себя цилиндр и систему рычагов и тяг. Внутри цилиндра 7 (рис. 6) находятся поршень 9 с кожаной манжетой и опускающие пружины, показанные на рисунке условно в виде одной пружины 6. Через шток 4 сила сжатого воздуха передается на рычаг 12. Полость цилиндра с левой стороны закрыта от попадания пыли и грязи чулком 5 из пожарного рукава [3].
Рисунок 6 – Система подъема токоприемника П-5
1-кран;
2- воздухораспределитель;
3-винт;
4-шток;
5-чулок;
6-пружины;
7-цилиндр;
8-труба;
9-поршень;
10-тяга;
11-вал нижней рамы;
12-рычаг;
13-шарнир;
14-тяга
При подаче сжатого воздуха в цилиндр по трубе 8 поршень, преодолевая действие пружин 6, начнет перемещаться влево, поворачивая рычаг 12 против часовой стрелки относительно шарнира 13. Тяга 10 сместится вправо и освободит вал нижней рамы 11, который под действием подъемных пружин будет поворачиваться против часовой стрелки, поднимая токоприемник. При поднятом токоприемнике может изменяться высота рам с изменением высоты контактного провода без изменения положения деталей механизма подъема за счет прорези в тяге 10, в которой валик ушка вала и может свободно перемещаться. Если из цилиндра сжатый воздух будет выпущен, то под действием пружин 6 поршень и шток 4 будут перемещаться вправо, а тяга 10 — влево, преодолевая действие подъемных пружин и вызывая поворот вала 11 по часовой стрелке и опускание токоприемника. Три пружины в цилиндре поставлены для повышения надежности опускания токоприемника при выпуске воздуха из цилиндра. Такое опускание должно произойти даже при изломе одной из пружин.
Токоприемник при подъеме не должен сильно ударяться о контактный провод, чтобы не раскачать и не погнуть его. При опускании необходимо резко оторвать полозы от контактного провода с тем, чтобы уменьшить вероятность его пережога в случае опускания токоприемника при включенных вспомогательных цепях электровоза, а затем опускание замедлить, чтобы уменьшить силу удара подвижных частей об амортизатор.
Поэтому токоприемник П-5 снабжен специальным редукционным устройством, состоящим из воздухораспределителя 2, в котором имеется регулируемое винтом 3 отверстие, и крана 1. При опущенном токоприемнике кран 1 перекрывает трубы, по которым воздух может проходить в цилиндр, минуя воздухораспределитель. При подъеме токоприемника воздух медленно наполняет цилиндр, так как проходит через узкое отверстие воздухораспределителя, и подвижные части медленно подводят полозы к контактному проводу. В процессе подъема рычаг 12 поворачивается и через тягу 14 открывает кран 1, соединяя цилиндр в обход воздухораспределителя. За счет этого при опускании воздух из цилиндра выходит быстро и подвижные части токоприемника резко опускаются. Однако при этом перекрывается кран 1 и дальнейшее опускание идет медленно, так как воздух выходит через регулируемое отверстие воздухораспределителя.
Скорость подъема регулируют винтом 3 воздухораспределителя, а скорость опускания — изменением длины тяги 14, а также имеющимися на рычаге 12 регулировочными винтами, изменяющими положение рукоятки крана от угла поворота рычага.
Сила нажатия полозов на контактный провод, с одной стороны, должна быть достаточно большой, чтобы иметь меньшее переходное сопротивление и обеспечить надежный контакт, а с другой, — не вызывать большого износа пластин полозов и контактного провода при движении. Эту силу нажатия регулируют натяжением подъемных пружин 5 (см.рис.2) за счет изменения длины шпилек шарниров, ввертывая их в пружинодержатель или вывертывая. Практически это достигается вращением самих пружин. Одна из шпилек и пружинодержатель имеют правую резьбу М16, а другая шпилька и пружинодержатель — левую того же размера. Поэтому если после ослабления контргаек повернуть пружину с пружинодержателями в одну сторону, то пружинодержатели будут навертываться на шпильки, увеличивая натяжение пружины. Поворот пружины в противоположном направлении приведет к уменьшению натяжения пружин. Для фиксации пружин в отрегулированном положении необходимо завернуть контргайки шпилек.
Для лучшего токосъема нажатие полозов на контактный провод при различной высоте его подвески должно оставаться постоянным. Однако в действительности при скольжении токоприемника по снижающемуся контактному проводу сила нажатия больше, чем при скольжении по поднимающемуся контактному проводу.
При неподвижной раме токоприемника сила нажатия определяется как разность между приведенной к полозу токоприемника силой действия подъемных пружин и весом подвижных частей. Движение рамы вниз (при снижающемся контактном проводе) сопровождается появлением сил трения в шарнирах и подшипниках, а также сил инерции подвижных частей токоприемника.
Эти силы действуют против направления перемещения рам, т. е. вверх, увеличивая нажатие полозов на контактный провод. При подъеме рамы эти силы действуют против силы, создаваемой подъемными пружинами, уменьшая нажатие.
Чтобы уменьшить отклонение сил нажатия на контактный провод, снижают силы трения в шарнирах, используя шариковые и игольчатые подшипники, и снижают массу подвижных частей токоприемника, выполняя ее из тонкостенных труб, обладающих достаточной прочностью при наименьшей массе, и используя работу каретки, обладающей значительно меньшей массой по сравнению с рамами токоприемника; Таким образом, при небольших, но резких изменениях высоты контактного провода, особенно при высоких скоростях движения, рама токоприемника не успевает среагировать, но полозы не отрываются от провода за счет подъема или опускания механизма каретки.
Большие изменения высоты контактного провода, например при подходе к станциям, где провод подвешивают выше, делают плавными, причем при скоростном движении расстояние изменения высоты подвески увеличивают. В этом случае рамы токоприемника успевают изменить свое положение. Нажатие полозов на контактный провод в статическом состоянии определяют динамометром при поднятом токоприемнике и перемещении рам вниз и вверх. Зависимости силы нажатия от высоты токоприемника называют его статическими характеристиками.
Технические характеристики токоприемника п-5
Таблица 1. Технические данные токоприемника Т-5М1 (П-5)
Номинальное напряжение, В3000
Длительный допустимый ток, А:
на стоянке
300
во время движения
2200
Конструктивная скорость движения, км/час
120
Время подъема токоприемника от минимальной рабочей поверхности при номинальном давлении воздуха в цилиндре, с
4–6
Диапазон рабочей высоты, мм
400–1900
Максимальная высота подъема токоприемника, мм
2100
Статическое давление на контактный проводник в пределах рабочей высоты, Н:
активный (при подъеме)
100
пассивный (при опускании)
130
Ход каретки, мм
50
Наименьшее давление сжатого воздуха в цилиндре для нормальной работы пневмопривода, кПа
350
Начальное давление сжатого воздуха в цилиндре для испытания на герметичность, кПа
675
Напряжение переменного тока частотой 50 Гц для испытания изоляции (на электровозе) в течение 1 мин, В
12 000
Масса, кг
269
Технология ремонта токоприемников
2. 1. Система технического обслуживания и ремонта электровозов
Для поддержания электровозов в работоспособном состоянии и обеспечения надежной и безопасной их эксплуатации существует система технического обслуживания и ремонта электроподвижного состава. Она введена приказом «ОАО» «РЖД» России от 30 декабря 1999 г. N ЦТ-725 и положением № 3р от 17.01.2005г.
Предусматривается проведение следующих видов технического обслуживания и текущего ремонта электровозов постоянного тока серий ВЛ:
— технические обслуживания ТО-1, ТО-2, ТО-3 для предупреждения появления неисправностей, поддержания электровозов в работоспособном и надлежащем санитарно-гигиеническом состоянии, обеспечения бесперебойной, безаварийной работы и пожарной безопасности. Техническое обслуживание ТО-3 может быть упразднено начальником железной дороги по согласованию с Департаментом локомотивного хозяйства «ОАО» «РЖД» России;
— техническое обслуживание ТО-4 для обточки бандажей колесных пар без выкатки их из-под электровоза при достижении оптимальных для данного участка эксплуатации или предельных величин проката и толщины гребней бандажей;
— техническое обслуживание ТО-5, выполняемое:
в процессе подготовки электровоза для постановки в запас МПС России и длительного содержания в резерве железной дороги -ТО-5а;
в процессе подготовки электровоза к отправке в недействующем состоянии в капитальный ремонт на заводы или в другие депо, в текущий ремонт в другие депо, передачи на баланс другим депо или передислокации-ТО-5б;
в процессе подготовки электровоза к эксплуатации после постройки, ремонта на заводах или в других депо, после передислокации-ТО-5в;
в процессе подготовки электровоза к эксплуатации перед выдачей из запаса «ОАО» «РЖД» России или РУД-ТО-5г;
— текущие ремонты ТР-1, ТР-2 и ТР-3 для поддержания работоспособности электровозов, восстановления основных эксплуатационных характеристик и обеспечения их стабильности в межремонтный период путем ревизии, ремонта, регулировки, испытаний и замены деталей, узлов, агрегатов. Ремонтный цикл включает последовательно повторяемые виды технического обслуживания и ремонта. Порядок их чередования определяется структурой ремонтного цикла.
Периодичность ремонта магистральных электровозов, т. е. пробеги между техническими обслуживаниями и ремонтами, а также нормы простоя электровозов при этом устанавливаются начальниками дорог с учетом конкретных эксплуатационных условий на основе нормативов приказа ОАО «РЖД» (рис.7).
Рисунок 7 — Нормативы межремонтных пробегов в км
ТО-1 – технический осмотр первого объема, производят на пункте технического осмотра не более 24 часов работы состава на линии. При осмотре ТО-1 слесари-осмотрщики и локомотивная бригада проверяют состояние ходовых частей вагона, токоприемников, автосцепок, отсутствие повреждений подвагонного оборудования, степень нагрева подшипников колесных пар и тяговых двигателей. Производят уборку пассажирского салона.
ТО-2 –технический осмотр второго объема, производят через 10+2 тыс. км пробега вагона. В дополнительно к объему работ ТО-1 производят осмотр электрических приборов, оборудования в кабине машиниста и пассажирском салоне. Проверяют регулировку тормозов.
ТО-3-технический осмотр третьего объема, производят через 30+5 тыс. км. Дополнительно к объему работ ТО-2 производят осмотр состояния тяговых двигателей, проверку некоторых габаритных и регулировочных размеров.
ТО-4 – выполняют при крайне важно эти обточки колёсных пар без выкатки из-под вагона.
Планово-предупредительные деповские ремонты установлены трех видов: ТР-1, ТР-2, ТР-3.
ТР-1-малый периодический ремонт, производят через 60+ 10 тыс. км пробега вагона. Время простоя не более 10 часов.
В ТР-1 дополнительно к объему работ ТО-3 производят расцепку и прокатку вагонов для осмотра поверхности катания колес, осмотра тяговой зубчатой передачи, прослушивания подшипников колесных пар и тяговых двигателей. Открывают, осматривают, зачищают и регулируют все электрические и пневматические приборы.
ТР-2- большой периодический ремонт, производят через 240+ 20 тыс. км пробега. Время простоя в ремонте -двое суток, в данном ремонте дополнительно производят обточку колесных пар на специальных станках (без выкатки из-под вагона) для ликвидации проката и других пороков на поверхности катании колеса, проточку коллекторов тяговых двигателей, производят замену деталей и узлов с износом выше установленных норм, а также проводят регулировку, испытания и частичную модернизацию оборудования.
ТР-3-подьемочный ремонт, производят через 480+20тыс.км. Производят выкатку, полную разборку и ремонт тележек. Ответственные детали проверяют на магнитном и ультразвуковом дефектоскопах. Колесные пары и тяговые двигатели отправляют на полное освидетельствование и в заводской ремонт.
Ремонтируют раздвижные двери и другое оборудование. Контроль качества осмотров осуществляют инженеры технического отдела, бригадиры слесарей и мастера, а также машинисты-инструктора и приемщики электроподвижного состава.
После производства ТР-2 и ТР-3 и осмотра мастером приемку осуществляет приемщик СПС. Далее производят обкатку вагона на ветке деповских путей или на линии в непиковое время в присутствии приемщика и одного из руководителей депо.
Нормы продолжительности технических обслуживаний ТО-4, ТО-5, текущих ремонтов ТР-1, ТР-2 и ТР-3 устанавливаются начальником железной дороги, исходя из технической оснащенности депо, рационального использования ремонтной базы, равномерной загрузки участков по ремонту, обеспечения высокого качества ремонта, проведения испытания и приемки электровозов после ремонта, а также с учетом выполнения установленной нормы деповского процента неисправных электровозов.
Капитальные ремонты (КР-1 и КР-2) являются главным средством «оздоровления» электровозов и предусматривают восстановление несущих конструкций кузова, сложный ремонт рам тележек, колесных пар и редукторов, тяговых двигателей и вспомогательных машин, электрических аппаратов, кабелей и проводов, восстановление чертежных размеров деталей и т. д. Капитальные ремонты электровозов осуществляют на ремонтных заводах [3].
Из всех аппаратов электровоза токоприемники работают в наиболее сложных условиях. Они воспринимают разнообразные динамические нагрузки, подвергаются сильному действию электрического тока, в зимнее время на их работоспособности отрицательно сказывается низкая температура, снегопад, гололед. Конструкция токоприемника отражает противоречивые требования: легкость и прочность, большую подвижность и необходимость сохранения постоянного контакта между полозом и контактным проводом и т. д. На электровозах постоянного тока установлены токоприемники тяжелого типа. По сравнению с токоприемниками электровозов переменного тока и электропоездов они воспринимают значительно большие токи (до 2000 А при продолжительном режиме) и имеют самое большое статическое нажатие.
Из всех повреждений аппаратов электровозов, имевших своим следствием порчи или неплановый ремонт, на долю токоприемников приходится 10—20%. Неисправности приемников приводят к повышенному износу контактного провода, его пережогу, повреждениям воздушных стрелок, фиксаторов и изоляторов контактной сети. Перед разборкой осматривают все узлы и детали и проверяют статическую характеристику, время подъема и опускания при нормальном давлении воздуха в пневматическом приводе. Обнаруженные при этом дефекты определяют в первом приближении характер последующего ремонта и степень разборки агрегатов.
Неисправность верхнего узла токоприёмника и контактной системы, прежде всего кареток, приводят к резкому перекосу полоза и повреждению контактной сети. Осматривая детали кареток, убеждаются в отсутствии изломов, искривлений, трещин и чрезмерной выработки. Трещины в кронштейнах и держателях кареток токоприёмников электровозов обычно возникают в местах концентрации напряжении на резких переходах в верхнем узле нередко наблюдаются износ стенок стакана, продавливание дна, излом шпильки и трещины в местах приварки проушины под полоз.
Начиная разборку, ослабляют пружины для предотвращения удара при самопроизвольном подъёме. Затем отсоединяют гибкие шунты, вынимают валики и снимают полозы. Последовательно демонтируют верхние узлы токоприёмника и снимают каретки. Если детали находятся в исправном состоянии, верхнюю часть не разбирают, пружины, держатели и шунты не снимают, однако обязательно проводят ревизию всех шарнирных узлов. Ещё более ослабив нажатие поднимающих пружин выбивают валики серёг. Затем пружины снимают и выворачивают на них серьги и сердечники. Разбирают шарниры и снимают верхние подвижные рамы. Нижние рамы и основание не разбирают [5].
2.4. Ремонт основных частей Рама основания не должна иметь перекоса болтов. Погнутые швеллеры основания выправляют на плите. Болтовые соединения крепят, а негодные заменяют. Небольшие трещины заваривают, а шов зачищают. Контактную поверхность в месте присоединения наконечников кабелей лудят припоем ПОС 40. Поврежденные или потерявшие эластичность резиновые амортизаторы заменяют. Подшипники при наличии на кольцах, сепараторах, шариках трещин, коррозии, увеличении радиального зазора свыше 0,2 мм заменяют. Специальным шаблоном проверяют расстояние по диагонали между отверстиями для болтов опорных изоляторов. Это расстояние должно соответствовать чертежным размерам; разница расстояний не должна превышать 10 мм. При больших отклонениях производят правку рамы в горячем состоянии.
Опорные изоляторы с трещинами, сколами и глазурью, поврежденной на длине более 10% пути возможного перекрытия электрическим током, заменяют. При ослаблении изоляторов их перезаливают. Разница по высоте изоляторов под один токоприемник не должна превышать 2 мм. Для устранения перекосов устанавливают шайбы между изоляторами и основанием.
При разборке шарниров с игольчатыми подшипниками принимают меры, чтобы не утерять иголки. С шариковых и игольчатых подшипников удаляют смазку и промывают керосином. Подвижные рамы проверяют на специальных стендах-кондукторах. Рама должна входить в кондуктор свободно, без усилий. Если это условно не выполнимо, то ее полностью разбирают. Трубы с трещинами, прожогами, вмятинами, изгибами в заводских условиях заменяют. В депо трещины, прожоги или вмятины глубиной до 3 мм ремонтируют постановкой соединительных муфт не более одной на трубу и не более двух на раму.
Полозы очищают от старой твердой смазки, обстукивая молотком; также можно применять пневматическое зубило. Остатки смазки удаляют вращающейся проволочной щеткой с пневматическим приводом. Проверяют состояние медных накладок или угольных вставок. При их износе, повреждении производят разборку. Полоз устанавливают на стенд, болты накладок срубают или отвертывают пневматическим гайковертом.
Профиль каркаса проверяют по специальному шаблону. На нем же правят каркас, чтобы вогнутости на рабочей поверхности не превышали 2 мм. Каркас должен иметь толщину не менее 1,5 мм. Трещины и прожоги заваривают электросваркой (постоянным током) или газовой сваркой. Разрешается у полозов электропоездов заваривать трещины, прожоги и приваривать накладки толщиной 1,5 мм. Общая длина сварных швов при этом не должна превышать 400 мм. У грузовых электровозов при текущем ремонте ТР-3 каркасы полозов, имеющие трещины, толщину стенок менее 1,3 мм заменяют новыми. При необходимости старые отверстия для накладок заваривают, размечают и сверлят новые. Каркас полоза оцинковывают для предохранения от коррозии и устанавливают медные или металлокерамические накладки или угольные вставки. Новые медные накладки толщиной 5—6 мм размечают по специальному кондуктору. Концы их делают скошенными под углом 45°, чтобы обеспечить плавность перехода контактного провода на стыке двух пластин. Отверстия после сверления зенкуют под угол 60°.
При ремонте редуктора воздушные каналы и, клапаны и их сёдла прочищают заострённой деревянной палочкой с надетой на её концы чистой тканью. Применять металлические предметы нельзя, т.к. ими можно нанести риски на притирочные поверхности. Все детали (кроме кожаных манжет и катушки электромагнитного вентиля КП-17-09) очищают от грязи и ржавчины промывкой в керосине. Работоспособность редукционных клапанов в немалой степени определяется пружиной. Поэтому обязательно проверяют характеристики старой или вновь установленной пружины. После смены деталей привод собирают, клапаны притирают к сёдлам, как при ремонте электромагнитных вентилей [4].
Полиэтиленовые рукава токоприёмников также снимают с электровоза для проверки испытания. Их промывают тёплой водой с мылом и протирают насухо. Влагу из рукава удаляют продувкой сжатым воздухом. Поверхность рукава должна быть гладкой, без трещин, надрывов и вмятин. Трещины чаще всего возникают в местах перегибов. Рукав, имеющий такие дефекты, заменяют. Бурты, имеющие трещины, вмятины или толщину менее 4 мм хотя бы на одном участке по окружности обрезают и формируют с помощью специальной пресс- формы. При этом длина рукава может быть уменьшена против чертёжного размера не более чем на 50 мм. Формируя бурт, на конец шланга надевают обойму, затем разъёмный пуансон.
Конец шланга выводят из пуансона на нужную величину для получения буртика требуемых размеров и опускают в бачок с глицерином, нагретым до 120- 140°С.
Формирование полиэтилена при предварительном нагреве до более высокой температуры значительно затрудняется из-за чрезмерного размягчения. Через 3- 5 минут шланг с пуансоном и обоймой вставляют в корпус в пресс-формы, предварительно нагретой вместе с матрицей до температуры 50- 60С. Буртик формируют лёгким нажатием одновременно на шланг и обойму.
Перед формированием буртиков на втором конце нового воздухопровода на шланг надевают две накидные гайки с уплотнительными прокладками. Если требуется изогнуть шланг, его опускают на 5- 8 минут в воду, нагретую до 100С, а затем укладывают в шаблон. Чтобы избежать смятия стенок шланга при изгибе в него вставляется круглый сплошной резиновый жгут. Готовый шланг испытывают давлением 700 кПа, а затем на электрическую прочность переменным напряжением 9,5 кВ в течение одной минуты.
Приступая к сборке токоприёмника, вновь проверяют по уровню тумбы, на которых установлено его основание, нет ли перекосов. Последовательно монтируют детали и узлы, которые снимали с основания для ремонта: пневматический привод, амортизаторы, пружины, валы и рычаги нижних рам. По мере сборки токоприёмника в шарниры и подшипники закладывают смазку. Устанавливают верхние рамы, в некоторых случаях шарниры собирают с помощью временных валиков, и лишь закончив предварительную работу, приступают к замене временных валиков постоянными. При этом стараются не допускать перекоса рычагов и шарниров. Подготовленные в виде отдельного узла каретки контактной системы собирают в единое целое совместно с верхними рамами и укрепляют в зависимости от токоприёмника один или два полоза. Толщина накладок или угольных вставок на полозах должно соответствовать номинальным значениям. Завершив сборку, перемещением от руки убеждаются в свободном ходе всех подвижных деталей и отсутствии заеданий [5].
2.6. Испытания после ремонта
Проверяют статическую характеристику — нажатие полоза на контактный провод в пределах рабочей высоты при поднятии и опускании токоприёмника. При этом испытании токоприёмник соединяют с воздушной магистралью и поднимают. Затем, зацепив за распорки верхних рам динамометр, плавно, без рывков, опускают токоприёмник, контролируя показания динамометра через 100 — 150 мм. После чего, сдерживая, позволяют ему так же плавно, без ускорения, подняться до предельной высоты, продолжая следить за показаниями динамометра. Испытания редукционного клапана, о чёткости работы которого судят по времени и характеру подъёма и опускания токоприёмника. Включение производят с пульта управления. Плавный подъём должен несколько замедляться в зоне подхода к контактному проводу, чтобы избежать удара о контактный провод. При включении, быстро начав опускаться, пантограф должен плавно замедлить движение при подходе к упорам и без ударов садиться на амортизаторы. Время подъёма и опускания пантографа проверяют хронометром [5].
2.7. Инструмент, оборудование и материалы
При ремонте токоприёмника используются следующие материалы приспособления и инструмент:
Регулируемые тумбы.
Моечная корзина.
Газовая горелка.
Кондуктор.
Ограничители размеров (втулки, валики, прокладки из красной меди).
Шлифовальный станок.
Пресс- форма.
Шаблон.
Уровень, опущенный на линейку.
Электрод (из алюминиевого сплава).
Фтористый натрий.
Бура.
Графитовая смазка СГС-0.
Молоток
Зубила.
Бородки.
Обжимки.
Керна.
Напильники
Отвёртки.
Шаберы.
Гаечные ключи [6]
Работы по ТО и ТР, испытанию и наладке электрического и электронного оборудования ТПС необходимо производить в соответствии с требованиями Правил эксплуатации электроустановок потребителей (ПЭЭП). Правил техники безопасности при эксплуатации электроустановок потребителей (ПТБ) и технологическими процессами [7].
Перед началом ремонта электрооборудования ТПС должны быть обесточены все силовые электрические цепи, отключены выключатели тяговых электродвигателей, крышевой разъединитель поставлен в положение «Заземлено», выпущен воздух и перекрыты краны пневматической системы электроаппаратов. Кроме того, при необходимости ремонта отдельных аппаратов, должны быть вынуты предохранители данного участка, предусмотренные конструкцией.
Внешние электрические сети питания переносных диагностических приборов напряжением более 42 В переменного или 110 В постоянного тока должны быть оборудованы защитным заземлением («занулением» или устройством защитного отключения).
Стенд для диагностики и ремонта электронного оборудования должен иметь защитное заземление («зануление» или устройство защитного отключения).
Испытания электрических машин, аппаратов и счетчиков электрической энергии на электрическую прочность изоляции после ремонта перед установкой на ТПС (кран) должны производиться на специально оборудованной станции (площадке, стенде), имеющей необходимое ограждение, сигнализацию, знаки безопасности и блокирующие устройства.
Перед началом и во время испытаний на станции (площадке) не должны находиться посторонние лица.
Сборка схем на испытательных стендах должна осуществляться при полном снятии напряжения. Питающие кабели для испытания электрических машин и аппаратов высоким напряжением должны быть надежно присоединены к зажимам, а корпуса машин и аппаратов заземлены.
Подачу и снятие напряжения необходимо осуществлять контакторами с механическим или электромагнитным приводом или рубильником, имеющим защитный кожух.
Пересоединение на зажимах испытываемых машин и аппаратов должно производиться после отключения всех источников питания и полной остановки вращающихся деталей.
Измерение сопротивления изоляции, контроль нагрева подшипников, проверка состояния электрощеточного механизма должны производиться после отключения напряжения и полной остановки вращения якоря.
При пайке наконечников на проводе непосредственно на ТПС (кране) должен использоваться надежно закрепленный тигель, исключающий выплескивание из него припоя.
При измерении сопротивления изоляции электрических цепей мегаомметром на напряжение 0,5 и 2,5 кВ выполнение каких-либо других работ на электрооборудовании и электрических цепях ТПС запрещается.
Перед испытаниями высоким напряжением сопротивления изоляции электрических цепей ТПС (крана) все ремонтные работы должны быть прекращены, работники выведены, входные двери на ТПС (кране) закрыты, а с четырех сторон на расстоянии 2 м установлены переносные знаки «Внимание! Опасное место» [7].
Перед подачей высокого напряжения необходимо подать звуковой сигнал и объявить по громкоговорящей связи: «На локомотив (кран), стоящий на такой-то канаве, подается напряжение». Управлять испытательным агрегатом должен руководитель работ, проводить испытания — персонал, прошедший специальную подготовку.
Корпус передвижного трансформатора и рамы испытываемого ТПС необходимо заземлить.
После ремонта «ОАО» «РЖД» подъем токоприемника и опробование электровоза или электросекции под рабочим напряжением должно производить лицо, имеющее право управления, в присутствии проводившего ремонт мастера или бригадира, которые до начала опробования должны убедиться в том, что:
— все работники находятся в безопасных местах, и подъем токоприемника не грозит им опасностью
— закрыты люки машин, двери шкафов управления, щиты стенок ВВК, реостатных помещений, крышки подвагонных аппаратных ящиков;
— в ВВК и под кузовом нет людей, инструментов, материалов и посторонних предметов;
— закрыты двери в ВВК, складные лестницы и калитки технологических площадок для выхода на крышу;
— с машин и аппаратов после их ремонта сняты все временные присоединения;
— машины, аппараты, приборы и силовые цепи готовы к пуску и работе.
После этого работник, поднимающий токоприемник, должен громко объявить из окна кабины локомотива: «Поднимаю токоприемник», подать звуковой сигнал свистком локомотива и поднять токоприемник способом, предусмотренным конструкцией данного электровоза или электросекции.
При поднятом и находящемся под напряжением токоприемнике разрешается:
— заменять перегоревшие лампы в кабине машиниста, в кузове (без захода в ВВК и снятия ограждений), лампы освещения ходовых частей, буферных фонарей, внутри вагонов электросекций при обесточенных цепях освещения;
— протирать стекла кабины внутри и снаружи, лобовую часть кузова, не приближаясь к токоведущим частям, находящимся под напряжением контактной сети, на расстояние менее 2 м и не касаясь их через какие-либо предметы:
— заменять предохранители в обесточенных цепях управления;
— заменять прожекторные лампы при обесточенных цепях, если их смена предусмотрена из кабины машиниста:
— осматривать тормозное оборудование и контролировать выходы штоков тормозных цилиндров: на электровозах типа ЧС — только на смотровой канаве, на электросекциях — не залезая под кузов:
— проверять на ощупь нагрев букс;
— настраивать электронный регулятор напряжения;
— продувать маслоотделители и концевые рукава тормозной и напорной магистралей;
— заправлять песочные бункера электропоездов;
— контролировать подачу песка под колесную пару;
— вскрывать кожух и настраивать регулятор давления. Кроме того, на электровозах дополнительно разрешается:
— обслуживать аппаратуру под напряжением 50 В постоянного тока, которая находится вне ВВК;
— проверять цепи электронной защиты под наблюдением мастера, стоя на диэлектрическом коврике и в диэлектрических перчатках;
— контролировать по приборам и визуально работу машин и аппаратов, не снимая ограждений и не заходя в ВВК;
— включать автоматы защиты;
— обтирать нижнюю часть кузова;
— осматривать механическое оборудование и производить его крепление, не залезая под кузов;
— проверять давление в масляной системе компрессора;
— регулировать предохранительные клапаны воздушной системы;
— производить уборку (кроме влажной) кабины, тамбуров и проходов в машинном отделении.
Другие работы на «ОАО» «РЖД» при поднятом и находящемся под напряжением токоприемнике запрещаются [7].
Заключение
В ходе выполнения работы были рассмотрены вопросы, связанные с изучением устройства, техническим обслуживанием и ремонтом токоприемников. В процессе работы с использованием знаний полученных на практике и специализированной литературы мною получены знания о системе планово-предупредительных ремонтов локомотивов, технологии ремонтно-восстановительных работ, правилам техники безопасности.
Особое внимание в работе обращено на правила разборки, сборки и ремонта токоприемников. Знания, полученные в ходе выполнения работы должны помочь мне в будущей производственной деятельности.
Список используемой литературы
Правила МПС России от 26.05.2000 № ЦРБ-756 «Правила технической эксплуатации железных дорог Российской Федерации».
Алябьев С.А. и др. Устройство и ремонт электровозов постоянного тока. Учебник для технических школ ж.
д. транспорта — М., Транспорт, 2003
Грищенко А.В., Стрекопытов В.В., Ролле И.А. Устройство и ремонт электровозов и электропоездов. М.: Академия, 2008
Дубровский З.М. Электровоз: Управление и обслуживание. М, Транспорт, 2009
Кикнадзе О.А. Электровоз ВЛ-10. — М.: Транспорт, 2010.
Красковская С.Н. и др. Текущий ремонт и техническое обслуживание электровозов постоянного тока. — М.: Транспорт, 2010.
Крутяков В.С. Охрана труда и основы экологии на железнодорожном транспорте. — М.: Транспорт, 2003.
http://www.twirpx.com/file/17179/
http://www.znanius.com/2985.html?L=2
http://referatwork.ru/category/radio/view/397138_tokopriemniki
http://allrefs.net/c2/1tnsn/p1/
Назначение, краткая техническая характеристика и основные составные части штанговых токоприемников. Устройство головки токоприемника. Возможные неисправности токоприемников.
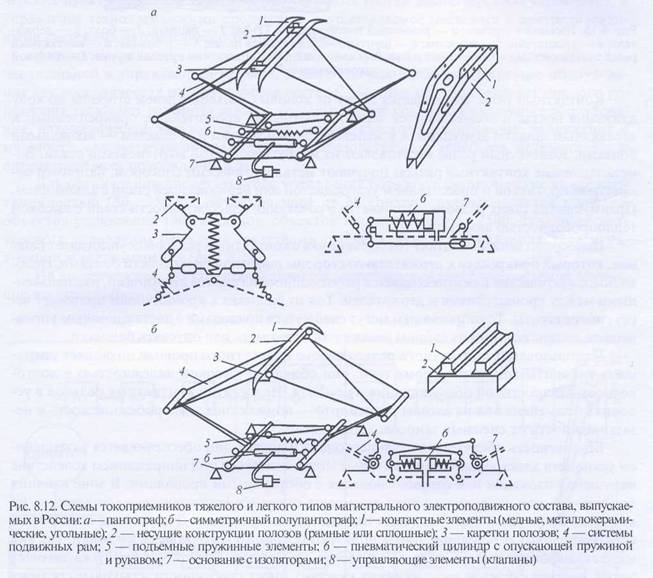
Штанговый токоприемник РТ-6И предназначен для осуществления подвижного электрического соединения между контактным проводом и ТБ как потребителем, а так же для передачи электроэнергии к электрическому оборудованию, установленному на ТБ, как на стоянке, так и во время движения.
Основные требования, предъявляемые к токоприемнику:
· Обеспечить необходимую силу натяжения контактной головки на контактный провод.
· Обеспечить надежный безыскровый токосъем при различной высоте подвески контактных проводов, больших скоростях движения и отклонение ТБ от оси подвески контактных проводов.
· Иметь достаточную механическую прочность, не большую массу подвижных частей, надежную изоляцию их друг от друга и от корпуса ТБ.
Токоприемник РТ-6И предназначен для работы под напряжением 550 V и длительном токе 170 А. Токоприемник крепится к металлическому постаменту на крыше ТБ и изолируется от него фарфоровыми изоляторами. Для изоляции кузова от звуковых колебаний при скольжении контактных вставок по проводам, в местах крепления под постамент устанавливают резиновые прокладки толщиной 20 мм.
Краткая техническая характеристика токоприемника:
· Длинна токоприемника 6400 ± 50 мм.
· Угол поворота корпуса основания на штыре опоры 110°.
· Максимальное отклонение ТБ от оси подвески контактных проводов 4,5 м, что соответствует углу поворота штанг от продольной оси ТБ 60°.
· Токоприемник обеспечивает устойчивый токосъем при скорости движения ТБ до 70 км/час
· Рабочее давление токоприемника на контактные провода от 12 кг до 14 кг при высоте подвески контактного провода 5,8 м.
· Максимальный подъем токоприемника 7,2 м.
· Максимальное опускание токоприемника 2,5 м.
· Масса токоприемника 80 кг.
· Основные составные части токоприемника:
· Основание токоприемника.
· Штангодержатель с пружинами.
· Штанга со штанговым проводом.
· Контактная головка.
Основные составные части контактной головки:
· Стальная втулка с бакелитовым изолятором. Устанавливается и крепится на верхнем конце штанги.
· Разрезная контактная втулка. Насаживается на бакелитовый изолятор стальной втулки. Имеет клемму для подсоединения штангового провода. Крепится на бакелитовом изоляторе с помощью стяжного болта.
· Башмак является основанием для установки и крепления подвижной части контактной головки. Насаживается на разрезную контактную втулку, крепится стяжными болтами.
· Подвижная часть контактной головки.
Основные составные части подвижной части контактной головки:
· Пята, конструкция которой подвижная часть контактной головки крепится к башмаку.
· Сферический держатель.
· Омедненный вкладыш. Крепится 2 винтами к сферическому держателю.
· Латунные щечки с гнездами. С помощью 2 винтов и 2 штифтов крепятся к омедненному вкладышу.
· Контактная вставка («уголек»). Устанавливается в гнездо латунных щечек.
Основные составные части аппаратов кулачкового типа. Устройство кулачковых элементов. В каких аппаратах кулачкового типа применяются кулачковые элементы КЭ-42, КЭ-54 и КЭ-61.Аппараты кулачкового типа – это косвенные многопозиционные выключатели, имеющие механический привод.
Основные составные части аппаратов кулачкового типа:
· Корпус, каркас или рама.
· Кулачковый вал с фигурными шайбами. Фигурные шайбы на кулачковом валу изготовлены из электроизоляционного материала. Боковая поверхность каждой фигурной шайбы представляет собою комбинацию выступов и впадин.
· Кулачковые элементы.
· Привод (ручной привод, педальный привод, электропривод, пневмопривод).
Основные составные части кулачкового элемента:
· Основание, выполненное из электроизоляционного материала
· Неподвижный контакт (контакты)
· Подвижный рычаг с подвижным контактом и роликом
· Пружины (притирающая, включающая)
· Клеммы для подключения внешних проводов
Некоторые типы кулачковых элементов имеют еще 2 составные части:
· Дугогасительное устройство
· Гибкий медный шунт
В контроллере хода и тормозном контроллере используются только кулачковые элементы КЭ-42.
В ГРК работают все типы кулачковых элементов: в цепи управления КЭ-42 и КЭ-54 и в силовой цепи КЭ-61.
Назначение, устройство и регулировка ручного тормоза. Как проверить эффективность действия ручного тормоза?Ручной тормоз обеспечивает длительную стоянку ТБ на уклоне до 10%, фиксирует ТБ на уклоне 23%.
Ручной тормоз состоит из ручного механизма и привода. Механизм расположен на полу кабины, слева от рулевой колонки и крепится к основанию кузова.
Ручной механизм состоит из:
· Кнопка
· Рычаг (внутри рычага отверстие)
· Тяга (проходит внутри рычага). На конце тяги с одной стороны кнопка, а с другой собачка
· Собачка (входит в зацепление с зубчатым сектором)
· Зубчатый сектор (зубчатый сектор и собачка нужны для фиксации рычага)
Привод состоит из:
· Механизм ручного тормоза
· Первичная тяга
· Вал с рычагами и кронштейнами первичный (крепится к основанию кузова)
· Промежуточные тяги
· На конце имеется возвратная пружина (крепится к основанию кузова)
· Вал с рычагами и кронштейнами промежуточный
· Шарнирная вилка
· Коромысло (крепится через палец к шарнирной вилке)
· Вал с рычагами и кронштейнами вторичный
· К нему крепятся тяги со скользящими вилками
· Тормозные рычаги. Скользящие вилки крепятся ко второму (верхнему) отверстию тормозных рычагов.
Регулировка стояночного тормоза:
В скользящей вилке имеется паз, который дает возможность свободно перемещаться тормозному рычагу при перемещении пневматического тормоза. Регулировку стояночного тормоза производят после регулировки ножного пневматического тормоза задних колес. Регулируем ход штока и зазор между накладками и барабаном.
Регулировка:
1. Поставить рычаг ручного тормоза в крайнее нижнее положение (снять с ручника).
2. Привести в действие воздушный тормоз (педаль в пол).
3. Поставить рычаг ручного тормоза в крайнее верхнее положение. При этом паз скользящей вилки должен коснуться соединительного пальца тормозного рычага.
4. Если это не произошло – необходимо отрегулировать длину тяг скользящих вилок.
5. Поставить рычаг ручного тормоза в крайнее нижнее положение и отпустить тормозную педаль.
6. Произвести несколько нажатий ножным пневматическим тормозом и убедиться, что скользящая вилка двигается без заеданий и рывков.
7. Произвести торможение стояночным тормозом, для проверки его работы.
Проверка стояночной тормозной системы:
· Машина должна удерживаться стояночным тормозом при трогании на маневровой позиции
· ТБ должен удерживаться в снаряженном состоянии на уклоне 23%
Компрессор ЭК-4: назначение, устройство, производительность компрессора. Неисправности компрессора.Компрессор ЭК-4В предназначен для получения сжатого воздуха из атмосферы и подачи его в пневмосистему. Компрессор ЭК-4В – двухцилиндровый, одноступенчатого сжатия, расположение цилиндров – горизонтальное.
Производительность 300 , вращение коленвала – 280 , давление нагнетания – 8 атм, передаточное число редуктора – 3,9, вес компрессора 307 кг (без двигателя). Цикл работы – 4 минуты работа, 4 минуты отдых ≈ 8-10 мин. Установлен слева перед задним колесом.
Устройство компрессора:
1. Электродвигатель ДК-408
2. Корпус (картер)
3. Маслоуказатель (щуп)
4. Клапанная коробка
5. Блок цилиндров
6. Шатунно-поршневая группа
7. Подшипники
8. Коленчатый вал
9. Двухступенчатый редуктор
Неисправности компрессора:
· Износ прокладок, компрессионных колец, подшипников, шестерен, бронзовых втулок
· Перекос клапанов
· Недостаток масла
Узнать еще:
Пантограф | Локомотив Вики | Фэндом
Пример пантографа ромбовидной формы или ножничного типа.
Пантограф с одной рукой на Siemens Desiro 360/2.
Высокоскоростной пантограф с одной рукой на синкансэн серии E5.
Пантограф — это устройство для сбора электрического тока для питания электровоза или электропоезда. Система используется для установления контакта с электрифицированным воздушным проводом (кабелем).Пантографы бывают всех форм и размеров в зависимости от скорости локомотива или поезда, требований к питанию, систем электроснабжения и т. Д. Основными частями пантографа являются нижние рычаги, которые поворачиваются относительно крыши, вагона / локомотива. , и прикреплен к плечу (-ям), который, в свою очередь, прикреплен к «головке» или «поддону» коллектора. Головка — единственная часть пантографа, которая касается датчика провода. Ток собирается через металлизированные углеродные полосы на головке.
Низкоскоростные пантографы работают на скорости ниже 125 миль в час (200 км / ч).В этих системах для выполнения большинства операций используются пружины и давление воздуха. В сложенном состоянии до крыши вагона / локомотива «вверх» пружины находятся в растянутом положении. Метод подъема пантографа начинается с впуска воздуха в цилиндр, называемый «рабочий цилиндр», при этом поршень перемещается вперед, тянется управляющий стержень и перемещается щелевое соединение для управления процессом. Затем пружины срабатывают и поднимают головку (с помощью рычага) до контакта с проволокой. Причина наличия воздушного цилиндра заключается в том, чтобы сжать «нижнюю» пружину.Для опускания пантографа воздух выпускается из цилиндра, и «нижняя» пружина воздействует на устройство, опуская головку на крышу каретки / локомотива.
Для локомотивов или поездов с максимальной скоростью выше 125 миль в час (200 км / ч) используется другая система. У них нет пружин (поскольку отскок — проблема), и они поднимаются сжатым воздухом через регулятор. Он установлен для поддержания постоянного усилия на воздушном проводе. Когда высота подвесного провода падает (например, при входе в туннель), воздух удаляется из системы, и воздух добавляется, когда поезд покидает туннель, а высота надземного провода увеличивается.
- Книга: Файл данных железной дороги , опубликованный Silverdale Books. ISBN: 1-85605-499-3.
Что такое пантограф? Как они используются в электрических рельсовых двигателях? | Шубхраншу Мишра
Что такое пантограф? Как они используются в электрических рельсовых двигателях?
Если вы когда-либо видели электрический рельсовый двигатель, вы должны заметить, что двигатель получает питание от воздушных проводов с помощью пантографа. Возникает вопрос, что такое Пантограф?
Пантограф представляет собой набор шарнирных рычагов, прикрепленных к крыше двигателя.Он разворачивается и тянется по вертикальной оси. Горизонтальный конец пантографа называется головкой. Эта голова оснащена углеродной полосой. Их количество и типы зависят от характера и силы передаваемого тока, переменного или постоянного тока. Эти углеродные полосы проходят вдоль контактного провода цепной цепи, таким образом улавливая электричество, необходимое для питания тяговых двигателей двигателя.
Контактная сеть сложнее простого силового кабеля. Он состоит из посыльных кабелей, контактных проводов, капельниц, стабилизаторов и натяжных устройств.Все эти элементы через равные промежутки времени поддерживаются серией мачт. Архитектура контактной сети спроектирована таким образом, что даже на высокой скорости контакт между контактным проводом контактной сети и пантографом остается постоянным и непрерывным.
Кабель воздушной линии настолько тяжелый, что подвешенный между двумя точками, они не образуют прямую линию, а тонут из-за своего веса. Для более высокой скорости и для обеспечения непрерывного контакта между цепной линией и головкой пантографа, что позволяет избежать чрезмерных потерь мощности, контактный провод цепной передачи необходимо поддерживать в горизонтальном положении.Он также должен быть достаточно жестким, чтобы динамически взаимодействовать с пантографом.
Контактный провод поддерживается через равные промежутки времени капельницами. Благодаря этим капельницам и натяжным нагрузкам контактный провод удерживается в горизонтальной оси с контролируемым уровнем жесткости. Эти капельницы имеют переменную длину, рассчитанную в соответствии с несколькими параметрами, такими как растягивающие нагрузки контактных и коммуникационных проводов или их механические характеристики.
с источником питания постоянного тока
1938 IEEE TRANSACTIONS ON POWER POWER, VOL.24, № 4, ОКТЯБРЬ 2009
качки в испытательной установке были намного ниже по сравнению с прокаткой
шт. Таким образом, измерения на движущемся поезде дали бы
более реалистичных результатов, связанных с переходными процессами из-за зигзагообразного движения
. Мы планируем это на более позднем этапе нашей работы.
Было бы интересно увидеть результаты испытаний при других более высоких тяговых напряжениях постоянного тока
(1,5 и 3 кВ), чтобы подтвердить полученные здесь
.В этой испытательной установке пантограф имеет только одну деталь из углеродного волокна,
, тогда как во многих современных поездах используется пантограф, в котором используются две детали из углерода
, разделенные примерно на 10 см, чтобы улучшить качество скользящего контакта и мощность
. Однако эта испытательная установка
является экстремальным условием и определенно улучшает понимание задействованных механизмов
. Поскольку цель
состояла в том, чтобы понять механизмы дугового разряда и влияние различных параметров испытания
, более низкая скорость, один конкретный уровень напряжения
и один пантограф из углеродного куска служили основной цели
этого исследования.Основываясь на нашем обсуждении здесь, мы полагаем, что даже при более высокой скорости, более высоком напряжении и современном графике панто-
мы заметим те же тенденции и характеристики, которые мы обсуждали здесь
, возможно, в другой степени. На более позднем этапе работы с
мы проведем тесты с этими вариантами.
В части II мы обсудим искрение пантографа с напряжением питания переменного тока
. Обратите внимание, что обсуждения, представленные в
Часть I, будут также упомянуты в Части II, если это применимо; Следовательно,
Часть I является основой для дугогасительных механизмов пантографа с системами подачи переменного тока
.
VI. ЗАКЛЮЧЕНИЕ
В этой статье мы представили экспериментальный анализ дуги пантографа
на железных дорогах постоянного тока. Мы обсудили основные параметры
, которые влияют на механизмы искрения. Это относительная скорость
между пантографом и контактным проводом в прямом и боковом (зигзагообразном) направлении
и полярность напряжения питания
, как показано ниже.
Зигзагообразное движение
• Так как зигзагообразное движение пантографа медленнее, чем продольная скорость, по сравнению с продольной скоростью
корень дуги перемещается медленно
по поверхности пантографа.
• Из-за слегка выпуклой поверхности по длине воздушный зазор
увеличивается, когда конец пантографа
контактирует с контактным проводом.
• Этот увеличенный воздушный зазор может вызвать перебои в подаче питания
, а иногда и высокие переходные процессы.
Скорость
• Увеличенная продольная скорость ускоряет благоприятные
точек зажигания дуги; при более низком диапазоне скоростей это может сократить время прерывания подачи питания
.
• Однако увеличение продольной скорости может вызвать более
переходных процессов, особенно когда воздушный зазор больше из-за
зигзагообразного движения.
Полярность питающего напряжения
• Когда пантограф является катодом, становится легче приостановить дугу из-за ее более медленного зигзагообразного движения по сравнению с
в случае, когда это анод.
• Прерывания и переходные процессы, генерируемые напряжением питания —
возрастов также ниже.
• Когда полярность напряжения питания на контактном проводе
отрицательная, может быть больше прерываний питания
на короткие промежутки времени из-за увеличенного воздушного зазора, особенно
, особенно ближе к концу зигзага по сравнению с системой тяги с активной подачей posi-
.
• Таким образом, тяговая система постоянного тока с принудительным питанием лучше с точки зрения дуги
.
БЛАГОДАРНОСТЬ
Авторы хотели бы поблагодарить ABB Corporate Research
за предоставленные помещения, а также L.Лильестранду, Л. Нордину,
и М. Али, ABB Corporate Research, за проектирование и построение испытательной установки
и ценную помощь при выполнении испытаний
. Они также хотели бы поблагодарить S. Shirran, P. Mellberg,
G. Bohlin и N. Theethayi из Bombardier Transportation и
P.-A. Линдебергу и Р. Быстрёму за полезные обсуждения и помощь.
Авторы также выражают особую благодарность команде
OHL ICE.
СПРАВОЧНАЯ ИНФОРМАЦИЯ
[1] Р. Холм, Электрические контакты. Упсала, Швеция: Almqvist and Wik-
sells, 1946.
[2] Э. И. Шоберт, «Скользящие электрические контакты», в Proc. 39-я конференция IEEE Holm
Conf. Электрические контакты, Питтсбург, Пенсильвания, сентябрь 1993 г., стр. 123–134.
[3] PG Slade, Электрические контакты: принципы и применение. New
York: Marcel Dekker, 1999, 10016.
[4] A. Bouchoucha, H. Zaidi, EK Kadiri, and D. Paulmier, «In uence
электрических полей на трибологическом поведении электродинамических медных /
стальных контактов, Электр.Англ. Jpn., Vol. 203–204, стр. 434–441, 1997.
[5] Д. Паульмьер, Х. Заиди, Х. Саллиот, Э. Хункпону, «Влияние электрического тока
и его полярность на поверхности медь и углерод в контакте
»в сб. 11-е евро. Конф. Наука о поверхности, Саламанка, Испания,
, октябрь 1990 г., стр. 769–772.
[6] Х. Заиди, Л. Пан, Д. Полмиер и Ф. Роберт, «Влияние магнитного поля
на износ и поведение трения пары из стали никель / xc 48»,
в Proc. .10-й Int. Конф. Износ материалов. Часть 2, Бостон, Массачусетс,
,, апрель 1995 г., стр. 799–804.
[7] A. Bouchoucha, E. K. Kadiri, F. Robert, H. Zaidi и D. Paulmier,
«Перенос металлов и окисление медно-стальных поверхностей в электрическом контакте скольжения
», в Proc. 22-й Int. Конф. Металлургические покрытия и тонкие пленки
. Часть 2 (из 2), Сан-Диего, Калифорния, апрель 1995 г., стр. 521–527.
[8] Х. Заиди, Э. Чапо, Х. Нери, Д. Полмиер и Т. Матиа, «Изменение коэффициента трения
в динамическом контакте графит-графит, пересекаемом
электрическим током», в Proc. .20-й Int. Конф. Металлургические покрытия
и тонкие пленки. Часть 2 (из 2), Сан-Диего, Калифорния, апрель 1993 г., стр. 388–392.
[9] Э. И. Шоберт, «Углерод, графит и контакты», IEEE Trans. Parts, Hy-
brids, Packag., Vol. PHP-12, нет. 6, pp. 62–74, март 1976.
[10] Д. Борман, С. Мидья и Р. Тоттаппиллил, «Компоненты постоянного тока в дуге пан-
тографа: механизмы и влияние различных параметров», в
Proc. 18-й Int. Цюрих Symp. Электромагнитная совместимость, Мюнхен,
Германия, окт.2007, стр. 369–372.
[11] С. Мидья, Д. Борман, А. Ларссон, Т. Шютте и Р. Тоттаппиллил,
«Понимание дуги пантографа на электрифицированных железных дорогах — влияние
различных параметров» в Proc. IEEE Int. Symp. Совместимость с электромагнитным соединением
, Детройт, Мичиган, август 2008 г., стр. 1–6.
[12] Д. Клапас, Р. Хакэм и Ф. А. Бенсон, «Сбор энергии электрической дуги
для высокоскоростных поездов», Proc. IEEE, т. 64, нет. 12, pp. 1699–1715, декабрь
1976.
[13] С. Мидья и Р. Тоттаппиллил, «Обзор проблем электромагнитной совместимости
в европейской системе управления железнодорожным движением»,
Транспортные исследования, часть C: Новые технологии, 2007.
[14] Т. Бергер , «Обледенение воздушных линий электрифицированных железнодорожных линий — метро-
логические условия», SBB Swiss National Railway, Infrastructure, In-
teroperability, SBB Swiss National Railway, Швейцария, Tech. Rep.,
Мар.2005. [Онлайн]. Доступно: http://www.buhrkall.dk/
[15] Л. Буркалл, «Компоненты постоянного тока из-за льда на контактном проводе
на железных дорогах с электричеством переменного тока», Electrische Bahnen, vol. 103, нет. 8, стр.
380–389, август 2005 г.
[16] Л.Д. Минск, «Обледенение конструкций», Исследование холодных регионов армии США
и инженерная лаборатория, CERL Rep. 80-31, декабрь 1980 г.
Разрешенное лицензионное использование ограничено: ABB AB. Загружено 14 октября 2009 г. в 08:20 с IEEE Xplore.Ограничения применяются.
Разработка активных пантографов для большегрузных автомобилей
Электрификация тяжелого автомобильного транспорта дает огромные социальные выгоды при небольших затратах
Настоящий отчет является продолжением и углублением отчета «Электрические дороги — Услуги электрического дорожного транспорта», проведенного весной 2010 года. Отчет показал, что электрификация тяжелого автомобильного грузового транспорта принесет значительные социальные и климатические преимущества. Эти транспортные средства невозможно электрифицировать с помощью аккумуляторной батареи без необходимости подавать электроэнергию во время путешествия.
Общие цели и условия
Общая цель проекта — внести значительный вклад в транспортный сектор, не зависящий от ископаемых, к 2030 году. Это требует эффективного использования ресурсов общества, поэтому цель проекта — избежать конфликтов с существующей физической инфраструктурой и правилами, такими как создание помех на проезжей части. . Проект основан на существующих, свободно доступных технологиях и существующих стандартах. Эффективная электрификация означает, что некоторые участки дорог, такие как мосты, туннели и проезжие части, не электрифицированы.Для этого требуется «активный пантограф», который можно подключать к кабелепроводу и от него во время движения, а также преодолевать повороты и неровности. На неэлектрифицированных участках гибридный автомобиль питается от аккумулятора или от двигателя внутреннего сгорания с биоуправлением.
Цель и объем проекта
Целью проекта было предоставить рекомендации и спецификации по активному пантографу (интеллектуальный токоприемник) и воздушной проводке для электрификации тяжелых дорожных транспортных средств.В дополнение к этому, проектная группа расширила свой кругозор, а также предоставляет описание:
- Правила и норматив дорожного пространства
- Электроэнергия / электроснабжение
- Конструкция автомобиля
Электрификация сегодня может быть проведена небольшими усилиями
В настоящем отчете показано, что активный пантограф (интеллектуальный токоприемник) в сочетании с традиционной воздушной проводкой позволяет эффективно электрифицировать части шведской дорожной сети.Кроме того, электрические стойки для легковых автомобилей с батарейным питанием могут быть интегрированы и обеспечивать быструю зарядку в местах отдыха. С помощью существующих технологий можно спроектировать, произвести и реализовать активный пантограф (интеллектуальный токоприемник) для использования со стандартизированной технологией воздушной проводки для питания тяжелых гибридных транспортных средств. Активный пантограф позволяет гибридным автомобилям автоматически обрабатывать неэлектрифицированные участки дороги, такие как шоссе, путепровод и туннели. Кроме того, обеспечивается полный электрический контакт при боковых перемещениях и перемещениях по высоте, например, при поворотах и морозе.
В отчете также показано:
- Стандартизированное управление контактами можно адаптировать к существующим дорогам, транспортным средствам и правилам.
- Электричество / электроснабжение возможно с национальной точки зрения.
- Электрические гибридные автомобили включают в себя новые интересные функции, такие как увеличенная грузоподъемность и улучшенная управляемость.
Предложения по продолжению деятельности
Проектная группа предлагает провести следующие мероприятия:
- Физический прототип активного пантографа и тестовая среда для тестирования компонентов
- Пилотный проект для испытания системы
- Постоянное распространение информации об электрификации дорожной сети
Проектная группа надеется, что эти мероприятия могут быть профинансированы и начаты в 2012 году.
49 CFR § 299.435 — Проектирование электрических систем. | CFR | Закон США
§ 299.435 Проектирование электрических систем.
(а) Системы верхнего коллектора.
(1) Пантографы должны быть расположены так, чтобы ими можно было управлять из обычного положения водителя в кабине. Пантографы, которые автоматически поднимаются при отпускании, должны иметь устройство автоматической блокировки, фиксирующее их в нижнем положении.
(2) Каждая подвесная коллекторная система, включая пантограф, должна быть оборудована устройством для электрического заземления любых неизолированных частей для предотвращения риска поражения электрическим током при работе с системой.
(3) Должны быть предусмотрены средства, позволяющие водителю определять, что пантограф находится в самом нижнем положении, и для закрепления пантографа, если это необходимо, без необходимости устанавливать крышу поезда.
(4) Каждый комплект поездов, оборудованный пантографом, работающим на подвесной системе сбора, также должен быть оборудован средствами для безопасного опускания пантографа в случае аварийной ситуации. Если для этой цели используется аварийный столб, та часть столба, с которой можно безопасно обращаться, должна иметь соответствующую маркировку.Этот столб должен быть защищен от влаги и повреждений, когда он не используется. Средства защиты и электроизоляции поврежденного пантографа, когда это не может быть выполнено автоматически, должны быть рассмотрены в правилах эксплуатации железной дороги.
(b) Защита цепи.
(1) Каждая вспомогательная цепь должна быть снабжена автоматическим выключателем или эквивалентными токоограничивающими устройствами, расположенными как можно ближе к точке подключения к источнику питания для этой цепи. Такая защита может отсутствовать в цепях, управляющих критически важными для безопасности устройствами.
(2) Магистральная линия электропередачи на 25 кВ должна быть защищена молниеотводом, автоматическим выключателем и реле перегрузки. Грозовой разрядник должен быть проложен по наиболее прямому пути к земле с заземлением не менее 6 AWG. Эти устройства защиты от перегрузки должны быть размещены в корпусе, специально разработанном для этой цели, с дугогасительной камерой, выходящей непосредственно на внешний воздух.
(3) Вспомогательный источник питания (440 В переменного тока), обеспечивающий распределение мощности, должен быть снабжен защитой от перегрузки и замыкания на землю.
(c) Основная аккумуляторная система.
(1) Основные батареи должны быть изолированы от кабины и мест для сидения пассажиров негорючим барьером.
(2) Если батареи потенциально могут выделять взрывоопасные газы, батареи должны иметь соответствующую вентиляцию для предотвращения накопления взрывоопасных концентраций этих газов.
(3) Зарядные устройства аккумуляторов должны быть спроектированы так, чтобы защищать их от перезарядки.
(4) Цепи аккумуляторных батарей должны включать аварийный выключатель аккумуляторных батарей для полного отключения энергии, накопленной в аккумуляторных батареях, от нагрузки.
(d) Конденсаторы для накопления большой энергии.
(1) Конденсаторы, если они есть, должны быть изолированы от кабины и мест для сидения пассажиров негорючим барьером.
(2) Конденсаторы должны быть спроектированы так, чтобы защищать от перезаряда и перегрева.
(e) Электромагнитные помехи (EMI) и электромагнитная совместимость (EMC).
(1) Железная дорога должна обеспечивать электромагнитную совместимость систем критически важного для безопасности оборудования с окружающей средой.Электромагнитная совместимость может быть достигнута за счет конструкции оборудования или изменения условий эксплуатации.
(2) Электронное оборудование не должно создавать электрические помехи, которые мешают управлению железнодорожной линией и коммуникациям или системам придорожной сигнализации.
(3) Для сдерживания излучения электромагнитных помех подавление переходных процессов должно быть по возможности у источника.
(4) Электрические и электронные системы оборудования должны быть способны работать в присутствии внешних источников электромагнитного шума.
(5) Все электронное оборудование должно быть защищено от повреждений или неправильной эксплуатации, или того и другого, из-за переходных процессов высокого напряжения и долговременных условий перенапряжения или пониженного напряжения. Это включает в себя защиту как от частоты сети, так и от гармонических воздействий, а также защиту от радиочастотных сигналов в диапазоне микроволновых частот.
(f) Изоляция или заземление металлических частей. Все неохраняемые нетоковедущие металлические части, которые могут быть заряжены, должны быть заземлены или тщательно изолированы.
(g) Маркировка высокого напряжения: двери, накладки или барьеры. На наружных поверхностях всех дверей, накладок или барьеров, обеспечивающих прямой доступ к высоковольтному оборудованию, должна быть четко обозначена надпись «ОПАСНО — ВЫСОКОЕ НАПРЯЖЕНИЕ» или слово «ОПАСНО» и нормальное напряжение, передаваемое таким образом защищаемым частям. Этикетки должны быть светоотражающими.
(h) Переключатели с ручным управлением. Все ручные переключатели, пропускающие ток с потенциалом более 150 вольт, которые могут работать под нагрузкой, должны быть закрыты и должны приводиться в действие с внешней стороны крышки.Должны быть предусмотрены средства, показывающие, разомкнуты или замкнуты переключатели. Выключатели, которые не должны работать под нагрузкой, должны иметь заметную и разборчивую маркировку со словами «не должны работать под нагрузкой» и имеющимся напряжением.
(i) проводники; перемычки; кабельные соединения.
(1) Размеры проводников должны выбираться на основе допустимой токовой нагрузки, механической прочности, температуры, требований к гибкости и максимально допустимого падения напряжения. Допустимая нагрузка по току должна быть снижена для группирования и рабочей температуры.
(2) Перемычки и кабельные соединения между модулями поезда должны быть расположены и ограждены, чтобы обеспечить достаточный вертикальный зазор. Они не могут висеть со свободным концом.
(3) Кабельные и перемычки между блоками поездов не могут иметь ни одного из следующих условий:
(i) Сломанная или сильно потёртая изоляция;
(ii) сломанные вилки, розетки, клеммы или штыри железнодорожной линии; и
(iii) Оборванные или выступающие жилы проволоки.
(j) Тяговые двигатели.Все тяговые двигатели должны быть в исправном рабочем состоянии или безопасно отключены.
Как работает пантограф? | блог @ CACM
Герберт Брудерер2 марта, 2020
комментариев
Пантографы (см. Рис. 1–2) широко использовались веками; например, в топографии и вышивке. С помощью этих устройств рисунки можно увеличивать и уменьшать.
Изобретателем считается Кристоф Шайнер из Германии (1603 г.). Однако Герон Александрийский (I век) уже разработал пантограф, который, однако, работал с зубчатым колесом.
Рис. 1: Пантограф.
Немецкая компания Ott в Кемптене была одним из
крупнейших производителей математических инструментов.
Кредит: Vermessungsamt, Аарау, Швейцария
Рис. 2: Пантограф.
Движущимся стилусом можно обвести периметр рисунка.
Чертежное перо одновременно воспроизводит рисунок.
Источник: Исторический музей Тургау, замок Фрауэнфельд, Швейцария
Аналоговый прибор (см. Рис. 3) состоит из подвижного рычага из дерева, металла или пластика. Он представляет собой параллелограмм. Противоположные внутренние углы равны, а сумма двух смежных внутренних углов составляет 180 °. Две диагонали делятся пополам. Стержни соединяются посредством шарнирных соединений.Столб (фиксированный стержень), указатель и перо для рисования лежат на прямой линии.
Рис. 3: Пантограф.
Чтобы уменьшить рисунок A, пантограф закреплен на штанге P. С помощью регулируемых планок определяется заданное соотношение.
Контрольной точкой Т очерчивается контур чертежа А. Ручка для рисования D создает аналогичную фигуру в выбранном масштабе.
Если поменять местами перо для рисования и указатель, фигура увеличится.
Пояснение
Из первой теоремы о перехвате (Фалес Милетский) следует, что:
PJ1: PJ2 = PD: PT
PJ2: PJ1 = PT: PD
PJ1: J1J2 = PD: DT
PJ2: J1J2 = PT: DT.
Пример
PJ1: PJ2 = 6: 12 увеличение вдвое (до 200%)
PJ2: PJ1 = 12: 6 уменьшение вдвое (до 50%).
Примечание
Пантограф Coradi (Цюрих) с длиной шкалы 65 см обеспечивает увеличение и уменьшение от 0,05 до 0,8:
1/20, 1/12, 1/10, 1/8, 1/6, 1/5, ¼, 1/3, 2/5, 2/3, ¾, 4/5, ½, 1/1 , 5/4, 4/3, 3/5, 3/8, 2/3.
Ссылки Bruderer, H . : Meilensteine der Rechentechnik, De Gruyter Oldenbourg, Берлин / Бостон, 2-е издание 2018 г., 2 тома, 1600 страниц, https: // www.degruyter.com/view/product/480555 и https://www.degruyter.com/view/product/503373
Bruderer, H .: Milestones in Analog and Digital Computing, Springer Nature Switzerland AG, Cham, 3-е издание 2020 г., 2 тома, ок. 2000 страниц, https://www.springer.com/de/book/9783030409739
Coradi, G .: Mathematisch-Mechanisches Institut G. Coradi, Цюрих. Verzeichnis über Mathematische Präzisions-Instrumente, Цюрих 1915, 48 страниц
Драхманн А.Г .: Механическая технология греческой и римской античности.Исследование литературных источников, Эйнар Мунксгаард, Копенгаген 1963, 220 страниц
Jordan, W., Eggert, O., and Berroth, A .: Handbuch der Vermessungstechnik, volume 2: Feld- und Landmessung, J. B. Metzlersche Verlagsbuchhandlung, Stuttgart, 10-е издание 1950 г., xvi, 640 страниц
Kronauer, J.H .: Schwebender Pantograph Гольдшмида, в: Schweizerische polytechnische Zeitschrift, том 9, 1864, выпуск 5, страницы 157–158
von Braunmühl, A . : Christoph Scheiner als Mathematiker, Physiker und Astronom, Buchnersche Verlagsbuchhandlung, Bamberg 1891, vi, 92 страницы.
Герберт Брудерер — бывший преподаватель дидактики информатики в ETH Zürich. Совсем недавно он стал историком технологий. [email protected], herbert.bruderer@bluewin.
Записи не найдены
Пантограф Proxxon
Согласно онлайн-словарю Merriam-Webster, пантограф — это «инструмент для копирования чего-либо (например, карты) в заданном масштабе, состоящий из четырех легких жестких полос, соединенных в форме параллелограмма» (см. Иллюстрацию ниже в качестве примера).Использование пантографа для отслеживания и копирования оригинального рисунка произошло еще в 1600-х годах.
Изготовители ножей используют пантографы для различных целей. Поскольку вы зашли на веб-сайт Криса, прочитали его страницы с пантографом и, возможно, посмотрели его видео, вы, вероятно, заинтересуетесь использованием фрезерного станка с пантографом для создания и вставки щитов в весы рукоятки ножа. В зависимости от возможностей станка, на котором вы собираетесь, их также можно использовать для создания простых или сложных кривых на валиках и материалах ручки, чтобы они соответствовали друг другу.Опять же, также в зависимости от машины, вы можете вырезать карманы во встроенных рамах ножей, а также на вставке из материала ручки, которая входит в накладные карманы.
Фрезерные станки с пантографом (фрезерные станки с пантографом) используются для изготовления металлических деталей по рисунку или шаблону. Промышленные модели могут надежно изготавливать как мелкие сложные детали, так и очень большие сверхпрочные детали. Первый промышленный пантограф, который резал металл для дублирования обработанных деталей, был изобретен в 1960-х годах.Одно из преимуществ пантографа заключается в том, что с помощью процесса, который он использует, можно сделать дубликат детали того же размера, большего или меньшего, чем используемый шаблон. Обычно пантограф используется в режиме уменьшения, поскольку любая неровность или несовершенство рисунка будет уменьшена степенью уменьшения, на которую установлен пантограф.
Концепция фрезерных станков с ЧПУ (с ЧПУ) и фрезерных станков с ЧПУ возникла в конце 1940-х годов. Первые надежные производственные машины стали доступны в 1950-х годах.Как и все новые технологии, они были очень дорогими вначале, а также их было трудно научиться программировать и использовать. Со временем цены упали, поскольку требуемые технологии стали более распространенными, а конкуренция снизила цены. Когда технический прогресс и падение цен в конечном итоге сделали их более доступными, станок с ЧПУ был предпочтительнее пантографа, потому что он был намного точнее человека, он мог выполнять заранее запрограммированный набор инструкций и в различной степени его можно было использовать в автоматическом режиме. манера.Оператор мог настроить машину, убедившись, что необходимые инструменты и сырье были доступны, они были разложены там, где они должны были быть (если машина имеет возможность автоматически менять инструменты), а затем нажать кнопку запуска. Станок возьмет на себя управление и автоматически произведет часть или всю деталь.
Поскольку пантографы были по существу заменены фрезерными станками с ЧПУ так давно, сегодня становится все труднее и труднее найти промышленные пантографы. Особенно, если вам нужен дом в хорошем состоянии, со всеми компонентами и достаточно полным набором инструментов.Это не означает, что вы не можете их найти, это просто означает, что вам придется либо заплатить более высокую цену тому, у кого есть опыт, чтобы восстановить их до полезного состояния, либо вам, возможно, придется искать пропавшие без вести. части, чтобы восстановить его самостоятельно. Предполагая, что вы можете найти пантограф в приличном состоянии, вы можете рассчитывать потратить от 1000 до 3000 долларов на станок, запасные части, необходимые, чтобы он снова заработал, и достаточно инструментов для начала.
Если вы хотите узнать больше о том, как работает пантограф, вы можете найти полезную информацию здесь:
ИЗГОТОВЛЕНИЕ ФРЕЗЕРНОГО СТАНКА PANTOGRAPH
Заявленный производителем как гравировальный станок, Proxxon GE20 должен использоваться с профессиональным вращающимся инструментом Proxxon в качестве электроинструмента, который выполняет резку. Другие вращающиеся инструменты (Dremel и т. Д.) Не подходят к воротнику, который крепит инструмент к рычагам пантографа. Итак, как минимум, вам придется купить пантограф Proxxon и его вращающийся инструмент. Я также рекомендую купить два из их наборов зажимов, потому что они имеют правильный размер, чтобы их было легко использовать с ним (один набор включает два зажима; вам понадобится одна пара для копировального стола, а другая пара для рабочего стола).
GE20 включает в себя набор пластиковых шаблонов для надписей и держатель для них, который крепится к копировальному столу с помощью двух зажимов, которые входят в него (они входят в комплект поставки машины).Я использовал функцию гравировки станка только один раз и не был удовлетворен результатом, но это, вероятно, потому, что я недостаточно практиковался, чтобы освоить его, и, вероятно, не имел подходящего наконечника для гравировки. Так что я не могу говорить о его пригодности для этой цели. В какой-то момент в будущем я, вероятно, потрачу больше времени на изучение гравировки и, возможно, предложу дополнительную информацию.
Наконечник иглы, поставляемый с пантографом Proxxon, который отслеживает узор или шаблон, имеет форму конуса и не соответствует диаметру, чтобы быть кратным 1/32 дюймовой концевой фрезы (например, если ваш пантограф настроен на 4: 1, наконечник иглы должен быть в 4 раза больше диаметра концевой фрезы, которую вы собираетесь использовать).Размер концевой фрезы важен, потому что может быть максимальный размер, который поместится в мельчайшие области шаблона и точно вырежет все детали шаблона, который вы используете.
Если вы используете концевую фрезу 1/32 дюйма (0,03125 дюйма), то щуп должен быть в 4 раза больше или 1/8 дюйма (0,125 дюйма). В своем видео Крис рекомендует использовать щуп 0,120 дюйма с концевой фрезой 1/32 дюйма. Использование щупа такого диаметра дает экран примерно на 0,0006 дюйма меньше, чем если бы вы использовали.Щуп размером 125 дюймов, и это приводит к тому, что защитный карман обрезается примерно на 0,0006 дюйма больше, обеспечивая очень плотную, но не слишком тугую посадку (разница в диаметре щупа . 0006 = 0,005 дюйма, деленная пополам, поскольку радиус концевой фрезы это фактическая разница в сделанном разрезе, деленная на коэффициент уменьшения 4). Это гораздо лучший выбор иглы / резака, особенно когда вы работаете над инкрустацией щита из хрупкого или мягкого материала (например, из перламутра или слоновой кости мамонта соответственно), потому что вам не придется прилагать много усилий, чтобы вдавить щит в карман.
Итак, мне пришлось модифицировать наконечник иглы, чтобы сделать его диаметр близким к 0,125 дюйма. Первая попытка сделать это заключалась в том, чтобы купить латунную трубку диаметром 1/8 дюйма, вырезать небольшой участок, чтобы он подходил к наконечнику иглы, с помощью ювелирной пилы, подпилить концы трубки под квадрат и сгладить, расположить ее над наконечником и заполнить зазор между трубкой и наконечником с помощью суперклея — чтобы трубка была центрирована как можно лучше. Хотя эта попытка сработала с точки зрения устойчивости наконечника, прилегание полученного щита и кармана было слишком плотным.
Наконечник стилуса нужно уменьшить до 0,120 дюйма, как это предлагается в видео Криса. Я подумал, что могу закрепить иглу в патроне сверлильного станка и, поворачивая, уменьшить его наждачной бумагой или напильником. Если вы решили попробовать этот метод, следите за тем, чтобы не повредить резьбу на стержне иглы.
Еще я связался с машинистом, который согласился модифицировать стилус для меня. Используя фрезерный станок, он сделал нейлоновый блок с отверстием в нем, достаточно большим, чтобы вдавить в него стержень иглы, но достаточно маленьким, чтобы он мог плотно прилегать.Он надел гайку на стилус как можно ближе к кончику (стилус имеет метрическую резьбу, M10 — 100, гайки были приобретены в магазине товаров для дома Lowe’s), он фрезеровал прорезь в нейлоновом блоке, чтобы она подходила и удерживала надежно закрепите гайку двумя сторонами, наденьте еще одну гайку на другой конец иглы и затяните ее гаечным ключом, пока она не затянется. Теперь он мог удерживать иглу внутри нейлонового блока в своих тисках, не повреждая резьбу на стержне иглы.
На этом этапе он отфрезеровал кончик иглы, просверлил пилотное отверстие точно в центре иглы (используя циферблатный индикатор для определения центра), а затем увеличил пилотное отверстие на кончике иглы, просверлив его с помощью Сверло 1/8 дюйма.Следующим шагом было фрезерование крошечной плоской поверхности на стороне иглы (так, чтобы он не просверливал отверстие для установочного винта в конической головке иглы (над кончиком), а в плоском месте, чтобы сверло немного не блуждал.
Снова, как и прежде, он начал отверстие с помощью центрирующего сверла, а затем просверлил отверстие для установочного винта подходящего размера для нарезания резьбы под винт 0–80. Отверстие проделали, и в него завернули винт.
Он подошел к своему токарному станку и превратил несколько коротких отрезков нержавеющих стержней в хвостовик 1/8 дюйма и повернул концы на несколько разных диаметров.Размер первого наконечника, который он повернул, был примерно на 0,001–0,002 дюйма меньше, чем у оригинального стержня 0,125 дюйма. Он также сделал еще четыре наконечника, уменьшая каждый на 0,001 ”или 0,002”. Я обнаружил, что наконечник .119 дюймов лучше всего работает с шаблонами, которые я купил у Криса.
Список материалов и цен
- Твердосплавный инструмент Источник: твердосплавные шаровые фрезы 1/32 дюйма — 10 шт. По 37,50 долларов США с бесплатной доставкой
- Гравировальное устройство Proxxon GE20: 256 долларов США.25
- Proxxon 38481 Professional Rotary Tool: 108,34 долларов США
- Proxxon 24256 Набор ступенчатых зажимов (рекомендуется 2 пары): 55,00 долларов США (27,50 долларов США за пару)
- Wiha 26430 Прецизионная отвертка с шестигранной головкой и шестигранной головкой 3,0 X 60 мм: 10,67 долларов США
Можно ожидать потратить около 500 долларов, включая несколько шаблонов Криса.
Если вы попросите машиниста модифицировать ваш щуп, стоимость обработки не будет включена в приведенный выше рисунок. Если вы выберете метод латунной трубки, трубка была куплена в Ace Hardware. Трубка длиной 12 дюймов и 1/8 дюйма стоила менее 2 долларов.
(цены указаны на сентябрь 2020 г.)
Рекомендации по установке
Одним из отличий Proxxon от полноразмерного пантографа является размер рабочего стола. Рабочий стол Proxxon имеет размеры приблизительно 2,75 «X 8,375». Поскольку вам нужно оставить место для закрепления изделия на столе, существует практическое ограничение на размер сырья, из которого вы можете вырезать свой щит или вырезать карман для вставки щита.У вас не должно возникнуть проблем с размером материала ручки для большинства папок. Однако вы не сможете использовать бутерброд из стали и микарты такого размера, как Крис в своем видео, потому что Proxxon не вмещает такую большую тарелку. Я сделал для Proxxon «бутерброды» из стали и дерева, из которых можно легко вырезать четыре или пять щитов.
Если вы режете сталь или другой металл, мне удалось последовать совету Криса из его видео. Стальную пластину можно приклеить к основанию из микарты или дерева, а основание можно закрепить на рабочем столе. Если разрезаемый материал не является металлическим, возможно, вы не сможете удалить его с основания с помощью горелки для размягчения клея, поскольку он может сжечь материал экрана. В этом случае мне хорошо подошла двусторонняя ковровая лента. Я прикрепил неметаллический материал к тонкой деревянной основе с помощью ленты. Я не рекомендую использовать ленту с металлом, потому что по мере того, как металл нагревается в результате обработки, лента может ослабнуть, и деталь может сдвинуться, что приведет к испорченной работе (спросите меня, откуда я это знаю!). Одним из нежелательных побочных эффектов использования ленты является то, что клей налипает на концевую фрезу и скапливается на ней, когда вы начинаете прорезать нижнюю часть материала, из которого вы делаете щит.Возможно, вам придется снять концевую фрезу с работы, выключить вращающийся инструмент и удалить клей с наконечника, прежде чем делать последние проходы.
Руководство по эксплуатации, которое поставляется с пантографом Proxxon, ужасно неадекватно. Инструкций на английском языке меньше трех страниц. Итак, вот несколько советов, которые помогут вам начать работу и, надеюсь, помогут вам избежать некоторых ловушек, с которыми я столкнулся в своем подходе проб и ошибок.
Рычаги пантографа (и, следовательно, игла и резак) перемещаются вверх и вниз с помощью двух валов с резьбой.Один из них — это сам стилус, а другой расположен в задней части машины. На обоих валах есть контргайка с накаткой. Плечи пантографа поднимаются и опускаются, ослабляя контргайку, поворачивая вал (валы) и блокируя их, плотно поворачивая контргайку к плечам. Я добился наилучших результатов, выполнив следующие действия:
- Когда режущий инструмент и рычаги пантографа повернуты в сторону, поместите обрабатываемый материал на рабочий стол так, чтобы зажимы были свободно на месте.
- Поместите шаблон или выкройку на стол для копирования, как вы делали материал выше на рабочем столе, но пока не затягивайте зажимы.
- Вам нужно будет переместить столы, шаблон и сырье, чтобы отрегулировать точку, в которой концевая фреза будет резать материал.
При коэффициенте уменьшения 4: 1 расстояние между таблицами составляет около 4 дюймов (плюс или минус место на столах, где вы прикрепляете шаблон и материал, который нужно вырезать). Инструкции по настройке столов можно найти на странице 10 руководства, прилагаемого к пантографу.
- Когда шаблон и обрабатываемый материал отрегулированы и надежно закреплены на своих столах, убедитесь, что рычаги установлены достаточно высоко, чтобы при повороте ножа над материалом он не касался и сломайте концевую фрезу или поцарапайте материал.
- Держа иглу над шаблоном, используя стержень с резьбой в задней части машины, отрегулируйте высоту резака так, чтобы он почти касался поверхности разрезаемого материала.
- Ослабьте контргайку на игле и поворачивайте ее до тех пор, пока плечи пантографа не выровняются, а кончик иглы слегка упирается в шаблон (концевая фреза еще не должна касаться материала). Это гарантирует, что надрез, который вы сделаете в материале, будет перпендикулярно поверхности материала, а не под углом.
Затяните контргайку иглы. Если вы режете тонкий материал или мелкий карман (0,060 дюйма или меньше), вам не нужно изменять высоту иглы.
- Узел рычага пантографа подпружинен на задней части машины.Его можно наклонять вверх и вниз, поднимая или опуская иглу.
- Поднимите иглу над шаблоном, чтобы концевая фреза не касалась разрезаемого материала, включите вращающийся инструмент, отрегулируйте его на полную скорость, ослабьте контргайку на заднем резьбовом валу, опустите резак и затяните контргайку (внимательно прочтите следующие три шага и убедитесь, что вы понимаете их, прежде чем делать первый монтаж).
- Если вы режете металл (нержавеющая сталь, латунь и т. выкройки и выньте резак из работы, приподняв стилус.
При резке более мягкого материала, например микарты, резак можно опускать примерно на ¼ оборота за проход. (Помните, что материал и / или «сэндвич», который вы разрезаете, могут не иметь идеально ровной поверхности для концевой фрезы. Поэтому приближайтесь к поверхности очень медленно и сначала опускайте фрезу все ниже и ниже, пока вы не сделаете контакт с поверхностью.
Обязательно совершайте один полный оборот вокруг всего шаблона перед каждым опусканием стилуса, потому что вы можете сначала коснуться некоторых точек на поверхности раньше других точек, и вы не хотите делать разрез это слишком глубоко и сломает концевую фрезу).
- Если вы вырезаете щит, продолжайте делать последовательные более глубокие проходы через материал, пока не прорвете основание, к которому материал приклеен или приклеен. Перед тем, как прекратить резку и снять «бутерброд» с рабочего стола, убедитесь, что вы прорвали разрезанный материал по всему контуру экрана. Идея здесь состоит в том, чтобы убедиться, что со щита не свисает «чад», потому что будет сложно или невозможно точно удалить его без изменения формы щита (спросите меня, откуда я это знаю).Если вы используете, например, основу из микарты, убедитесь, что концевая фреза прорезает весь материал экрана и хорошо проникает в микарту по всей окружности экрана, прежде чем прекращать выполнение проходов или перемещать работай.
- Если вы прорезаете карман для защиты, продолжайте делать последовательные более глубокие проходы в обрабатываемый материал, пока карман не достигнет желаемой глубины. Помните, что во время каждого прохода вы должны отрезать весь материал внутри кармана; это что-то вроде раскрашивания внутри линий и того, что вы вырезали всю область внутри кармана.
- Убедитесь, что вы поднимаете фрезу и удерживаете ее над разрезаемым материалом, пока вы регулируете задний резьбовой вал для увеличения глубины резания для каждого последующего прохода.
- При разрезании экрана также будьте осторожны, когда вы опускаете резак обратно в материал, так как вы входите в материал далеко за пределы шаблона экрана, потому что вы не хотите разрезать поверхность экрана.
- Аналогичным образом, при разрезании кармана, будьте осторожны, когда вы опускаете резак обратно в материал, чтобы материал хорошо вошел внутрь кармана, чтобы случайно не порезать материал ручки за пределами того места, где расположен карман.
Это может стать настоящей катастрофой, если будет сделан нежелательный разрез на дорогостоящем материале ручки.
Плюсы и минусы
Плюсы:
- Совершенно новый станок
- Относительно низкая стоимость по сравнению с промышленными моделями (если вы даже можете найти промышленный пантограф в сборе и в хорошем состоянии)
- Компактный (занимает намного меньше места, чем промышленная модель)
- Стол, легкий, легко перемещается
- Невероятно легко настроить коэффициент уменьшения (предварительно просверленные и нарезанные отверстия в рычагах пантографа, закрепленные винтами с накатанной головкой)
- Отлично работает с шаблонами пантографа Криса (будьте осторожны, чтобы не перетянуть шаблон при закреплении на копировальном столе он легкий пластик и может треснуть)
Минусы:
- Легкая машина, недостаточно прочная для фрезерования крупных деталей
- Винты с накатанной головкой, которые используются для установки передаточного отношения, могут ослабнуть после прохода или двух — их нужно часто проверять, чтобы убедиться, что они остаются плотными.
Если винты с накатанной головкой ослабнут, вращающийся инструмент может подскочить, что приведет к поломке концевой фрезы и / или выемке на краях разреза. Это не имеет большого значения; вам просто нужно проверять / подтягивать их каждый второй проход по шаблону — всего за секунду или две.
- Руководство по эксплуатации Proxxon оставляет многое для воображения и не является полным руководством по использованию станка в качестве фрезы для вырезания деталей.
Производители промышленных фрезерных станков
Если вы хотите поискать в Интернете информацию о полноразмерных промышленных мельницах, вот список некоторых производителей.Я уверен, что есть много других производителей. Они кажутся наиболее распространенными.
- Александр
- Deckel
- Gorton (P1 — 2 — модель Криса)
- Manek
- Pear
- Sakazaki
- Scripta (Франция, в США была компания Scripta, но они были дистрибьютором в США для Скрипта)
Резюме
В ходе всех моих исследований, продолжавшихся несколько месяцев, я не смог найти другого небольшого настольного пантографа, похожего на Proxxon. Он действительно хорошо сделан, и я настоятельно рекомендую его, если вы не думаете, что когда-либо будете заинтересованы в полноразмерном пантографе или если у вас ограниченный бюджет и вы хотите начать с машины начального уровня хорошего качества. . Proxxon производит отличные инструменты и инструменты. Однако вы можете получить высококачественную оснастку (концевые фрезы, наконечники для гравировки и т. Д.) Из других источников по гораздо более выгодным ценам.
Я доволен Proxxon и в настоящее время не планирую переходить на промышленный токарный стан.Кроме того, у меня нет места в магазине, и нет места для машины побольше.
Возможно, вам стоит рассмотреть возможность заказа на Amazon, потому что вы можете получить все нужные вам товары по одному заказу из одного места (кроме концевых фрез 1/32 дюйма; Крис рекомендует Carbide Tool Source). И при заказе на эту сумму вы, вероятно, получите бесплатную доставку от Amazon.
Несмотря на то, что пантограф поставляется со всеми необходимыми шестигранными ключами, удобно иметь более длинный и прямой 3. Шестигранная отвертка 00 мм, чтобы ослабить и затянуть зажим, удерживающий вращающийся инструмент в гнезде. Если у вас его еще нет, подумайте об этой от Amazon: Прецизионная отвертка Wiha 26430 с шариковой головкой, шестигранник, метрическая 3,0 X 60 мм. Это около 11 долларов.
Пантограф поставляется с шестигранным ключом в виде отвертки, который используется для ослабления и затягивания копировального и рабочего столов. Обе таблицы перемещаются из стороны в сторону и спереди назад.
Рисунок пантографа был создан Inigolv и используется под лицензией Creative Commons Attribution.Изображение пантографа Proxxon было взято с сайта proxxon.com, где его можно купить. Все остальные фотографии были сделаны и предоставлены Стивом Лундом.
.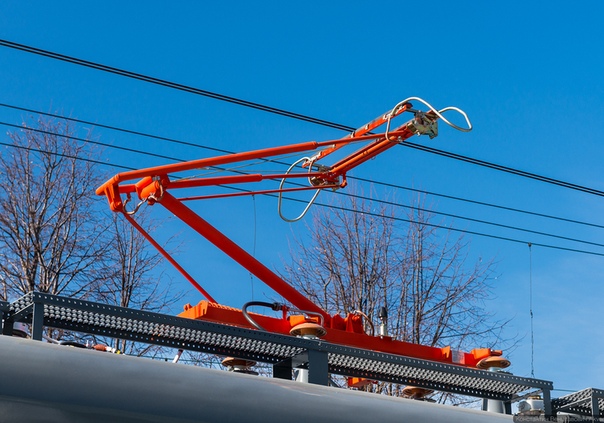