Назначение токоприемника: Токоприёмник — Википедия – 1 Общие сведения о токопримнике
Токоприёмник — Википедия
Материал из Википедии — свободной энциклопедии
Текущая версия страницы пока не проверялась опытными участниками и может значительно отличаться от версии, проверенной 14 мая 2015; проверки требуют 9 правок. Текущая версия страницы пока не проверялась опытными участниками и может значительно отличаться от версии, проверенной 14 мая 2015; проверки требуют 9 правок.Токоприёмник (энергополучатель) — тяговый электрический аппарат, предназначенный для создания электрического контакта электрооборудования подвижного состава с контактной сетью (электропроводом) и, следовательно, токосъёма. Реализует контактный способ токосъёма[1].
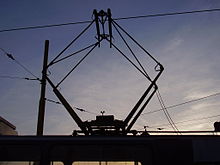
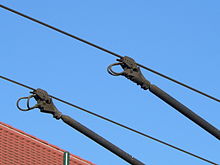
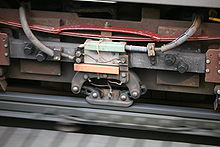
Конструкция токоприёмников и их характеристики определяются мощностью (током нагрузки) и скоростью ЭПС, габаритами подвижного состава и приближения строений, расположением контактных проводов или рельса в плане и по высоте относительно ЭПС, характером изменения расстояния между основанием токоприёмника и контактным проводом или рельсом, условиями управления подъёмом и опусканием токоприёмников. Токоприёмники должны обеспечивать надёжный (без повреждений), экономичный (с минимальным износом контактирующих элементов) и экологичный токосъём.
Комплексы конструктивных элементов, входящих в состав контактных токоприёмников, подразделяют на[1]:
- Базовые элементы, необходимые для участков, электрифицированных как на постоянном, так и на переменном токе
- Система подвижных рам (полностью определяет поперечную жёсткость токоприёмника)
- Подъёмно-опускающий механизм
- Основание
- Управляющие
- Альтернативные специфические элементы для постоянного или переменного тока, а также для электровозов или электропоездов
- Контактирующие
- Полозы
- Каретки — элемент конструкции токоприёмника, обеспечивающий упругое перемещение полоза относительно верхнего шарнира системы подвижных рам, и предназначенный для уменьшения влияния инерции рам в процессе взаимодействия с контактной сетью путём упругого расчленения масс токоприёмника
- Плунжерные
- Вертикальные
- Наклоняемые
- С демпфированием
- Плунжерно-рычажные
- Рычажные
- Рычажно-пружинные
- Пружинные
- С кулисой (направляющей)
- Плунжерные
- Токопроводящие
- Изолирующие
- Дополнительные элементы используют для повышения эксплуатационных свойств токоприёмников — скорости, надёжности, экономичности и экологичности
- Предохранительные
- Аэродинамические — предназначены для улучшения аэродинамических свойств токоприёмников, зависящих от воздействий воздушного потока
- Уменьшающие лобовое сопротивление
- Экранирующие
- Компенсирующие аэродинамическую подъёмную силу
- Демпфирующие — применяют для отбора энергии от колеблющейся системы «токоприёмник — контактная подвеска», снижения амплитуд перемещений и уменьшения колебаний контактных нажатий до допустимых пределов
- Устанавливаемые в верхнем узле токоприёмника
- Устанавливаемые в системе подвижных рам
- Авторегулирующие
- Диагностические
- Сохраняющие
- Для наклона кузова
- Помехоподавляющие
- Шумоподавляющие
- Для обеспечения электробезопасности
- Охлаждающие
- Виброзащищающие
- Гололедозащищающие
- Эрозиозащищающие
Комплексы базовых и альтернативных элементов содержат все токоприёмники отечественного ЭПС.
Безаварийная работа ЭПС и контактной сети в значительной степени зависит от характеристик, определяемых конструкцией подъемно-опускающего механизма (привода) токоприёмника. Привод должен обеспечивать: необходимую величину опускающей силы, требующейся для надёжного опускания токоприёмника (при необходимости) с заданной скоростью за определенное время; определенную величину удерживающей силы, предотвращающей самопроизвольный подъём токоприёмника при высоких скоростях движения; заданное статическое нажатие на контактный провод с возможностью его регулирования как вручную, так и автоматически; достаточно малое время подъёма и опускания токоприёмника без повреждения его элементов и контактной сети при заданных эксплуатационных скоростях движения подвижного состава. Кроме того, привод токоприёмника должен управляться дистанционно. По виду используемой энергии все приводы токоприёмников разделяют на пневматические, электрические и гидравлические
Токоприёмники различают по условиям работы и по конструктивному исполнению:
- Для токосъёма с воздушной контактной сети:
- Пантографный — токоприёмник с подъёмным механизмом в виде шарнирного многозвенника, обеспечивающим вертикальное перемещение контактного полоза[2].
- Штанговый — токоприёмник с подъёмным механизмом в виде рычага-штанги, допускающим вертикальное, а при необходимости и боковое перемещение контактной головки (контактного «башмака») или (реже) полоза. Весьма характерен для троллейбусов (двухштанговый вариант).
- Дуговой — токоприёмник с подъёмным механизмом в виде поворотной рамы, обеспечивающим перемещение полоза по дуге окружности.
- Для токосъёма с контактного рельса:
- ↑ 1 2 3 Михеев В. П. Контактные сети и линии электропередачи: Учебник для вузов ж.-д. транспорта. — М.: Маршрут, 2003.— 416 с. ISBN 5-89035-086-2
- ↑ Сидоров Н.И., Сидорова Н.Н. Как устроен и работает электровоз — М.: Транспорт, 1988. — ISBN 5-277-00191-3. — Тираж 70000 экз. — С. 50.
1 Общие сведения о токопримнике
Министерство транспорта Российской Федерации
Федеральное агентство железнодорожного транспорта
ГОСУДАРСТВЕННОЕ БЮДЖЕТНОЕ ОБРАЗОВАТЕЛЬНОЕ УЧРЕЖДЕНИЕ ВЫСШЕГО ПРОФЕССИОНАЛЬНОГО ОБРАЗОВАНИЯ
«САМАРСКИЙ ГОСУДАРСТВЕННЫЙ УНИВЕРСИТЕТ ПУТЕЙ СООБЩЕНИЯ»
Кафедра «Локомотивы»
Курсовой проект по дисциплине
«ПРОИЗВОДСТВО И РЕМОНТ ПОДВИЖНОГО СОСТАВА»
НА ТЕМУ «РЕМОНТ ТЯГОВОГО ЭЛЕКТРОДВИГАТЕЛЯ»
Вариант
Выполнил: студент 4 курса
группы ПС-17 Попов Мукменов Р.К.
Проверил: ст. преподаватель
Антипова Е. В.
Самара 2015
СОДЕРЖАНИЕ
ВВЕДЕНИЕ
ИСТОРИЯ ОТЕЧКСТВЕННОГО ЭЛЕКТРОВОЗОСТРОЕНИЯ
ЦЕЛЬ РАБОТЫ
1 ОБЩИЕ СВЕДЕНИЯ О ТОКОПРИЕМНИКЕ
1.1 НАЗНАЧЕНИЕ ТОКОПРИЕМНИКА
1.2 ПРИНЦИП РАБОТЫ ТОКОПРИЕМНИКА
1.3 КОНСТРУКЦИЯ ТОКОПРИМНИКА
1.4 ТЕХНИЧЕСКИЕ ХАРАКТРИСТИКИ ТОКОПРИМНИКА
2 ТЕХНОЛОГИЯ РЕМОНТА ТОКОПРИЕМНИКОВ
2.1 СИСТЕМА ТЕХНИЧЕСКОГО ОБСЛУЖИВАНИЯ И РЕМОНТА ЭЛЕКТРОВОЗОВ
2.2 ОСНОВНЫЕ НЕИСПРАВНОСТИ ТОКОПРИЕМНИКОВ
2.3 РАЗБОРКА ТОКОПРИМНИКОВ
2.4 РЕМОНТ ОСНОВНЫХ ЧАСТЕЙ
2.5 ПОСЛЕДОВАТЕЛЬНОСТЬ СБОРКИ
2.6 ИСПЫТАНИЯ ПОСЛЕ РЕМОНТ
2.7 ИНСТРУМЕНТ, ОБРУДОВАНИЕ И МАТЕРИАЛЫ
3 ТРЕБОВАНИЯ ТЕХНИКИ БЕЗОПАСНОСТИ ПРИ РЕМОНТЕ И ИСПЫТАНИИИ ЭЛЕКТРООБОРУДОВАНИЯ
ЗАКЛЮЧЕНИЕ
ЛИТЕРАТУРА
ВВЕДЕНИЕ. ИСТОРИЯ ОТЕЧЕСТВЕННОГО ЭЛЕКТРОВОЗОСТРОЕНИЯ
ЭЛЕКТРОВОЗ — локомотив, приводимый в движение находящимися на нем тяговыми электродвигателями, которые получают электроэнергию от стационарного источника — энергосистемы через тяговые подстанции и тяговую сеть от контактного провода либо от собственных тяговых аккумуляторных батарей. Выпускаются также комбинированные контактно-аккумуляторные электровозы, которые могут работать как от контактной сети, так и от аккумуляторной батареи. Подавляющее большинство находящихся в эксплуатации электровозов магистральных ж. д. являются неавтономными, т. е. не могут работать без контактной сети. На путях промышленных предприятий часто используются автономные электровозы, не зависящие от контактной сети. Для обеспечения маневровых работ наиболее подходящими являются контактно-аккумуляторные электровозы, которые используются также широко для обслуживания горных выработок, где прокладка контактного провода затруднена или невозможна. Таким образом, эксплуатируемые электровозы могут быть классифицированы по назначению, степени автономности, роду тока в тяговой сети; в зависимости от области использования и конструкции имеют ряд различных направлений.
Первые электровозы появились на ж.-д. транспорте в конце 19 в. как локомотивы, альтернативные паровозам. Развитие электротехники позволило создать мощные электродвигатели постоянного тока и двигатели переменного трехфазного тока. Были решены также проблемы генерирования электроэнергии и ее передачи по контактной сети. Идея реализации электрического локомотива с автономным или неавтономным питанием была высказана в первой половине 19 в., но первые практические результаты были получены в 1880 г. В России инженер Ф. А. Пироцкий установил электрический двигатель на пассажирском вагоне и провел первые опыты; в 1880 г. в Санкт-Петербурге был проложен для электровагона рельсовый путь. В том же году Э. В. Сименс в Германии и Т. А. Эдисон в США предложили свои конструкции. Новые локомотивы смогли заменить паровую тягу в специфических условиях эксплуатации ж. д.- в длинных тоннелях и на горных (перевальных) участках с большими уклонами. При этом проявились главные преимущества электровоза — отсутствие выбросов отработанных газов, возможность увеличения силы тяги путем форсировки тяговых электродвигателей на руководящем уклоне, реализация идеи рекуперативного торможения с возвратом энергии в тяговую сеть. Впоследствии область рационального применения электровозов существенно расширилась: их стали использовать и на равнинных участках с интенсивным движением поездов, где решающее значение имел высокий кпд самого электровоза (до 88-91%) и всей системы электрической тяги (до 30% при питании преимущественно от тепловых электростанций и до 50-60% при питании от гидроэлектростанций ).
Первые электровозы на российских ж. д. появились в 1929-1930 гг. в связи с электрификацией Сурамского перевала на Закавказской железной дороге (линия Баку-Батуми). На линии эксплуатировались закупленные в Италии, США, и Германии 6-осные электровозы постоянного тока 3 кВ, получившие обозначение С (с индексом, соответствующим стране-изготовителю). В России было налажено производство электровозов на Коломенском заводе совместно с московским заводом «Динамо», который начал выпускать тяговые электродвигатели и электрооборудование. В 1932 г. был выпущен первый отечественный грузовой электровоз сети Сс, впоследствии — ВЛ19 (цифра 19 указывает осевую нагрузку в т на рельсы). Этот принцип сохранялся в обозначениях электровозов ВЛ22 и ВЛ23, позже перешли к указанию числа осей (постоянного тока ВЛ8), а затем добавили букву «О», которая обозначала род тока (электровозы, работающие на однофазном токе), соответственно 6-осные и 8-осные локомотивы ВЛ60, ВЛ80 (позднее буква трансформировалась в ноль).
Электровозы, имеющие обозначение ВЛ, были предназначены для грузового движения, хотя довольно часто используются и для тяги пассажирских поездов. Конструктивная скорость электровозов ВЛ обычно не превышает 110 км/ч. В 70-е гг. был реализован переход на более мощные 12-осные электровозы на базе двух 6-осных секций, в каждой из которых кузов опирался на три 2-осные тележки (постоянного тока ВЛ15 и переменного тока ВЛ85, ВЛ86). Однако одновременно получила распространение и концепция более гибкого типажного решения, когда выпускались 4-осные секции, из которых можно было формировать тяговые единицы из 2-4 секций (постоянного тока ВЛ11М, переменного тока ВЛ80С). По мере расширения электрификации ж. д. наряду с грузовыми электровозами начался выпуск скоростных электровозов, параметры которых были приспособлены для тяги пассажирских поездов. Первый пассажирский электровоз, получивший наименование ПБ (Политбюро), был выпущен Коломенским заводом в 1934 г. Электровоз имел 6 осей, групповой привод колесных пар. Небольшие партии грузовых электровозов ВЛ19, ВЛ22, ВЛ60 выпускались с измененным передаточным отношением от тяговых двигателей на колесные пары, что позволяло использовать их в пассажирских сообщениях (с дополнительной буквой П, например ВЛ60П).
В начале 90-х гг. произошло значительное снижение перевозочной работы, вследствие чего потребность в сверхмощных электровозах сократилась, имевшийся парк электровозов стал вполне достаточным для выполнения перевозок; выпуск новых электровозов сократился. Электровоз ВЛ85, имевший наиболее отработанную конструкцию, начали выпускать в односекционном исполнении (ВЛ65). Для возможности использования электровоза в пассажирском сообщении было применено опорно-рамное подвешивание тяговых двигателей, в результате чего конструктивная скорость повысилась до 140 км/ч. Было предусмотрено электрическое отопление пассажирского поезда от электровоза. Такой электровоз фактически относится к классу универсальных — грузопассажирских.
Основу эксплуатируемого парка пассажирских локомотивов составляют 6-осные электровозы ЧС2 и ЧС2Т постоянного тока, электровозы ЧС4 и ЧС4Т переменного тока, а также 8-осные электровозы ЧС6, ЧС7 и ЧС200 постоянного тока и с такой же ходовой частью электровозы ЧС8 переменного тока. С середины 90-х гг. на магистральных ж. д. эксплуатируются скоростные пассажирские электровозы (1994 г.), 8-осные односекционные электровозы ЭП200, конструктивную скорость которых предполагалось довести до 250 км/ч, и упрощенная модификация такого электровоза на конструктивную скорость 160 км/ч. В 2001 г. в связи с развитием скоростного движения выпуск электровозов на максимальные скорости 200-250 км/ч увеличился. Основные пассажиропотоки в высокоскоростном пассажирском сообщении реализованы моторвагонными электропоездами. В сер. 90-х гг. были изменены обозначения новых электровозов: в обозначение грузовых электровозов ввели букву Э (например, Э1, Э2, ЭЗ и т.д.), а для пассажирских и универсальных — буквы ЭП, в частности электровоз ВЛ65 получил обозначение ЭП1, электровоз, выполненный на базе его механической части, с возможностью питания от сети как постоянного, так и переменного тока, ЭП10.
ЦЕЛЬ РАБОТЫ
Заданием на письменную экзаменационную работу было предложено изучить назначение, конструкцию и принцип работы и ремонта токоприемника П-5, установленного на электровозе ВЛ-10. Я также должен детально описать технологию ремонта токоприемника, его основные неисправности, разборку, ремонт основных узлов, сборку и испытание, инструмент и оборудование, применяемое при ремонте этого электрического аппарата.
Очень важное значение имеет соблюдение правил техники безопасности, которые я также должен отразить в своей письменной работе..
Теоретическую работу я должен увязать с производственной практикой, ознакомиться, как выполняется ремонт токоприемника, и научиться самостоятельно выполнять технологические операции, соответствующие квалификации слесаря 3 разряда.
1.1 Назначение токоприемника
Электровоз получает электрическую энергию через токоприемник, который установлен на крыше на изоляторах и при движении электровоза скользит по контактному проводу, обеспечивая надежный съем тока при различных условиях движения. Контактный провод подвешен в отдельных точках и из-за провисания имеет разную высоту. Токоприемник должен успевать следовать за изменением контактного провода без больших изменений нажатия на контактный провод и тем более не отходить от него.
В случае отрыва токоприемника от контактного провода между ними возникает электрическая дуга, которая портит контактные поверхности и ухудшает съем тока при последующей работе. Требования постоянства нажатия токоприемника на контактный провод при различной его высоте и при разных скоростях движения выполняются при достаточно сложном конструктивном исполнении.
В зависимости от значения снимаемого тока токоприемники выполняют легкого и тяжелого типа. Токоприемники легкого типа (на ток до 500 А) устанавливают на электровозах переменного тока и электропоездах, тяжелого типа (на длительные токи до 2200 А) — на электровозах постоянного тока. На каждом электровозе устанавливают по два токоприемника: один — рабочий, другой — запасной. Обычно работает второй по ходу движения токоприемник, так как в случае его поломки передний токоприемник остается неповрежденным. При изломе же первого по ходу токоприемника его обломки могут повредить второй.
1.2 Принцип работы токоприемника
Принцип работы токоприемника поясняется рис. 1. Основание токоприемника несет на себе нижние рамы 2, валы 1 которых поворачиваются в подшипниках. С нижними рамами шарнирно соединены верхние рамы 3. В верхней части эти рамы соединены между собой и с кареткой 5, с которой связаны полозы 4, скользящие по контактному проводу.
Рисунок 1 – Принцип работы токоприемника
Валы 1 поворачиваются под действием пружины 8, которая, стремясь сжаться, передает усилие на ушки 6, поднимает рамы и создает нажатие на контактный провод. Синхронность поворота обоих валов и работу рам без перекосов обеспечивает тяга 7, соединенная с ушками 6.
1.3 Конструкция токопримника
На электровозе ВЛ10 установлено два токоприемника П-5. Основание токоприемника 8 (рис. 2) сварено из двух боковых продольных швеллеров и двух поперечных швеллеров, между которыми в средней части проложены и приварены два продольных уголка. К этим уголкам крепят воздушный цилиндр 11 приводного механизма с редуктором 10 и шарнир подъемного рычага. На каждом боковом швеллере укреплено по кронштейну с буфером 12, смягчающим удары подвижных рам при опускании токоприемника, а также по две полуоси 9. На полуось 1 (рис. 3), укрепленную с помощью хомутов 2 на швеллера основания 3, посажен шариковый подшипник 4, находящийся внутри вала 5 нижней рамы. Вал выполняют из трубы с наружным диаметром 89 мм.
Рисунок 2 – Общий вид токоприемника П5
К валу приваривают два конических кронштейна, на которые надевают конические трубы 7 (см. рис. 2) нижней рамы и закрепляют каждую из них двумя болтами. Кроме того к валам приваривают ушки для крепления пружин 5, тяг 6 и рычагов. Конические трубы изготовляют сваркой; из тонколистовой стали толщиной 1,5 мм. Концы труб меньшего, диаметра нижней рамы соединяют с трубами верхней рамы 4 через шарниры с шариковыми подшипниками. Каждая верхняя рама выполнена из трех тонкостенных стальных труб наружным диаметром 30 мм и толщиной стенки 1 мм. Две трубы — боковые и одна — диагональная соединены между собой стальными хомутами. Верхние шарниры боковых труб через игольчатые подшипники соединены с осями, укрепленными по концам распорки 2, фиксирующей расстояние между боковыми трубами рамы в верхней части.
Рисунок 3 – Узел подшипника нижней рамы
По концам этих осей находятся каретки 1 с полозами 3. Каретка обеспечивает небольшое перемещение полозов по вертикали относительно верхней рамы, необходимое для следования полозов за небольшими по величине, но резкими изменениями контактного провода по высоте, при прохождении которых рамы токоприёмников не успевают изменить своего положения вследствие сравнительно большой массы. Каретка состоит из основания (рис. 4), состоящего из двух стальных боковин 1, соединенных втулкой 2 и заклепками 10. В верхних концевых частях основания на шариковых подшипниках установлены рычаги, состоящие из шарниров 5, к которым приварены изогнутые трубы 6 и 9 и держатели 7 кронштейнов 8 полозов. Оба рычага составляют клещевидную конструкцию. Рычаги в верхнем положении находятся под действием пружины 3, укрепленной через ушки 4 к хвостовикам шарниров 5. Своими крайними витками пружина входит в отверстия ушек.
Рисунок 4 – Каретка токоприемника
При подъеме токоприемника полозы упираются в контактный провод, но под действием подъемных пружин рама продолжает движение и вызывает просадку полозов с рычагами и растяжение пружины 3. При просадке рычагов относительно основания каретки на 50 мм пружина создает силу 8,5—9,5 юге на полоз. Эту силу можно регулировать изменением длины пружины за счет ввинчивания в отверстия ушек.
Кронштейн полоза укреплен на держателе шарнира и может поворачиваться от горизонтального положения на 5—8°. Каретка удерживается в горизонтальном положении пружинами 13 (см. рис. 2) и имеет возможность поворачиваться на небольшой угол за счет их деформации. Пружину с одной стороны крепят к хомуту, укрепленному на трубе верхней рамы, а с другой — к заклепке основания каретки.
Полоз 3 (см. рис. 2) штампуют из листовой оцинкованной стали толщиной 1,5 мм. На его рабочей поверхности укрепляют сменные контактные пластины, которые скользят по контактному проводу. Материал накладок должен иметь малое электрическое сопротивление, быть устойчивым против действия электрической дуги, износоустойчивым и по возможности меньше изнашивать контактный провод.
В настоящее время находят применение медные пластины, ме-таллокерамические пластины на медной или железной основе, а также угольные вставки. Полозы под медные накладки и под угольные вставки имеют различную конструкцию.
Рисунок 5 — Крепление угольных накладок
Пластины крепят к полозу винтами М6Х16 с конической головкой, которая утапливается в коническую рассверловку пластины. Угольные вставки 3 (рис. 5), имеющие в сечении к нижней нерабочей части форму «ласточкина хвоста», укрепляют к полозу 1, зажимая вставку между пластинами 2 и 4 болтами 5 размерами М6Х16. Кронштейны полозов с обеих сторон имеют отверстия и приваренные изнутри гайки М10. В полозе против этих отверстий имеются овальные отверстия для упрощения подгонки деталей. Полозы крепят к кронштейнам четырьмя болтами М10.
Все шарнирные соединения и подшипниковые узлы имеют гибкие медные шунты для прохождения тока и предохранения подшипников от разъедания током и нагрева.
Рамы токоприемника поднимаются двумя подъемными пружинами 5 (см. рис. 2). Концы пружин укрепляют на пружинодержателях, имеющих по наружному диаметру винтообразные канавки, на которые навертывается пружина крайними витками. Во внутреннюю резьбу пружинодержателя ввертывается шпилька шарнира, связывающего пружину с ушками валов нижних рам. Для устранения возможного самоотвертывания пружинодержателя на шпильку ставят контргайки.
Токоприемник поднимают с помощью пневматического привода, включающего в себя цилиндр и систему рычагов и тяг. Внутри цилиндра 7 (рис. 6) находятся поршень 9 с кожаной манжетой и опускающие пружины, показанные на рисунке условно в виде одной пружины 6. Через шток 4 сила сжатого воздуха передается на рычаг 12. Полость цилиндра с левой стороны закрыта от попадания пыли и грязи чулком 5 из пожарного рукава.
Рисунок 6 – Система подъема токоприемника П5
При подаче сжатого воздуха в цилиндр по трубе 8 поршень, преодолевая действие пружин 6, начнет перемещаться влево, поворачивая рычаг 12 против часовой стрелки относительно шарнира 13. Тяга 10 сместится вправо и освободит вал нижней рамы 11, который под действием подъемных пружин будет поворачиваться против часовой стрелки, поднимая токоприемник. При поднятом токоприемнике может изменяться высота рам с изменением высоты контактного провода без изменения положения деталей механизма подъема за счет прорези в тяге 10, в которой валик ушка вала И может свободно перемещаться. Если из цилиндра сжатый воздух будет выпущен, то под действием пружин 6 поршень и шток 4 будут перемещаться вправо, а тяга 10 — влево, преодолевая действие подъемных пружин и вызывая поворот вала 11 по часовой стрелке и опускание токоприемника. Три пружины в цилиндре поставлены для повышения надежности опускания токоприемника при выпуске воздуха из цилиндра. Такое опускание должно произойти даже при изломе одной из пружин.
Токоприемник при подъеме не должен сильно ударяться о контактный провод, чтобы не раскачать и не погнуть его. При опускании необходимо резко оторвать полозы от контактного провода с тем, чтобы уменьшить вероятность его пережога в случае опускания токоприемника при включенных вспомогательных цепях электровоза, а затем опускание замедлить, чтобы уменьшить силу удара подвижных частей об амортизатор.
Поэтому токоприемиик П-5 снабжен специальным редукционным устройством, состоящим из воздухораспределителя 2, в котором имеется регулируемое винтом 3 отверстие, и крана 1. При опущенном токоприемнике кран 1 перекрывает трубы, по которым воздух может проходить в цилиндр, минуя воздухораспределитель. При подъеме токоприемника воздух медленно наполняет цилиндр, так как проходит через узкое отверстие воздухораспределителя, и подвижные части медленно подводят полозы к контактному проводу. В процессе подъема рычаг 12 поворачивается и через тягу 14 открывает кран 1, соединяя цилиндр в обход воздухораспределителя. За счет этого при опускании воздух из цилиндра выходит быстро и подвижные части токоприемника резко опускаются. Однако при этом перекрывается кран 1 и дальнейшее опускание идет медленно, так как воздух выходит через регулируемое отверстие воздухораспределителя.
Скорость подъема регулируют винтом 3 воздухораспределителя, а скорость опускания — изменением длины тяги 14, а также имеющимися на рычаге 12 регулировочными винтами, изменяющими положение рукоятки крана от угла поворота рычага.
Сила нажатия полозов на контактный провод, с одной стороны, должна быть достаточно большой, чтобы иметь меньшее переходное сопротивление и обеспечить надежный контакт, а с другой, — не вызывать большого износа пластин полозов и контактного провода при движении. Эту силу нажатия регулируют натяжением подъемных пружин 5 (см. рис. 2) за счет изменения длины шпилек шарниров, ввертывая их в пружинодержатель или вывертывая. Практически это достигается вращением самих пружин. Одна из шпилек и пружинодержатель имеют правую резьбу М16, а другая шпилька и пружинодержатель — левую того же размера. Поэтому если после ослабления контргаек повернуть пружину с пружинодержателями в одну сторону, то пружинодержатели будут навертываться на шпильки, увеличивая натяжение пружины. Поворот пружины в противоположном направлении приведет к уменьшению натяжения пружин. Для фиксации пружин в отрегулированном положении необходимо завернуть контргайки шпилек.
Для лучшего токосъема нажатие полозов на контактный провод при различной высоте его подвески должно оставаться постоянным. Однако в действительности при скольжении токоприемника по снижающемуся контактному проводу сила нажатия больше, чем при скольжении по поднимающемуся контактному проводу.
При неподвижной раме токоприемника сила нажатия определяется как разность между приведенной к полозу токоприемника силой действия подъемных пружин и весом подвижных частей. Движение рамы вниз (при снижающемся контактном проводе) сопровождается появлением сил трения в шарнирах и подшипниках, а также сил инерции подвижных частей токоприемника.
Эти силы действуют против направления перемещения рам, т. е. вверх, увеличивая нажатие полозов на контактный провод. При подъеме рамы эти силы действуют против силы, создаваемой подъемными пружинами, уменьшая нажатие.
Чтобы уменьшить отклонение сил нажатия на контактный провод, снижают силы трения в шарнирах, используя шариковые и игольчатые подшипники, и снижают массу подвижных частей токоприемника, выполняя ее из тонкостенных труб, обладающих достаточной прочностью при наименьшей массе, и используя работу каретки, обладающей значительно меньшей массой по сравнению с рамами токоприемника; Таким образом, при небольших, но резких изменениях высоты контактного провода, особенно при высоких скоростях движения, рама токоприемника не успевает среагировать, но полозы не отрываются от провода за счет подъема или опускания механизма каретки.
Большие изменения высоты контактного провода, например при подходе к станциям, где провод подвешивают выше, делают плавными, причем при скоростном движении расстояние изменения высоты подвески увеличивают. В этом случае рамы токоприемника успевают изменить свое положение. Нажатие полозов на контактный провод в статическом состоянии определяют динамометром при поднятом токоприемнике и перемещении рам вниз и вверх. Зависимости силы нажатия от высоты токоприемника называют его статическими характеристиками.
Назначение и общее устройство токоприёмников — Мегаобучалка
Лабораторная работа №7
«Изучение конструкц ии, проверка действия и нажатия полозов асимметричного токоприёмника»
Цель работы: наружным осмотром и по пособию изучить конструкцию токоприёмника ТА-160-3200; проверить его состояние, действие, соответствие техническим данным и измерить нажатие.
Назначение и общее устройство токоприёмников
Токоприёмники служат для создания надёжного скользящего контакта между контактным проводом и высоковольтными электрическими цепями электроподвижного состава. Конструкция токоприёмников определяется: расположением контактного провода относительно Э.П.С., величиной тока нагрузки, скоростью движения подвижного состава, характером изменения высоты подъёма, климатическими условиями, условиями управления токоприёмником.
На электроподвижном составе выпуска конца ХХ века, как правило, применяются симметричные токоприёмники (пантографы). Такие токоприёмники обеспечивают надёжный контакт с контактным проводом при больших (до 160 км/ч) скоростях и больших (до 2500 А) токах, не требуют перестановки при изменении направлении движения, удобны для дистанционного управления.
В последнее время на электровозах и электропоездах всё чаще применяются асимметричные токоприёмники (полупантографы), которые имеют ряд существенных преимуществ:
— меньшая, чем у симметричных, масса подвижных частей;
— лучшие динамические и аэродинамические характеристики;
— позволяют развивать скорости свыше 200 км/ч;
— занимают меньше места на крыше электровоза.
Применяемые токоприёмники довольно сильно отличаются друг от друга, но все они в основном состоят из одних и тех же элементов (см. рис.1):
— основания на опорных изоляторах;
— валов;
— нижних и верхних шарнирных рам;
— кареток;
— одного или двух полозов с контактными пластинами;
— механизма подъёма и опускания.
Для дистанционного управления токоприёмники снабжают пневматическими приводами: поршневыми у симметричных токоприёмников и резинокордными гофрированными баллонами – у несимметричных. Данная практическая работа посвящена изучению одного из несимметричных токоприёмников, применяемых на электровозах 2ЭС6 и 2ЭС10.
Рисунок 1 – Электровоз с симметричными токоприёмниками
Рисунок 2 – Электровоз с асимметричными токоприёмниками
Рисунок 3 – Общий вид токоприёмника ТА-160-3200
![]() |
Рисунок 4 –Кинематическая схема асимметричного токоприёмника ТА-160
Технические данные токоприёмника электровоза 2ЭС6 (ТА-160-3200)
Наименование параметра | Значение |
Скорость движения электровоза, км/ч, не более | 160 |
Высота подъема от сложенного положения, мм — рабочая минимальная — рабочая максимальная — максимальная | 190 1790 2100 |
Время подъема до максимальной высоты, с, не более | 10 |
Время опускания с максимальной высоты, с, не более | 6 |
Максимальная сила тока протекающего через токоприемник, А — при движении — при стоянке | 3200 260 |
Контактное нажатие ТП, Н — при движении — при стоянке | 120 (12) 80 (8) |
Двойное трение в шарнирах, Н, не более | 25 |
Рабочий ход каретки, мм | 60-90 |
Привод подъема и опускания | пневматический |
Токоприемник ТЛ13У1
содержание .. 1 2 3 4 5
ДЕПАРТАМЕНТ ОБРАЗОВАНИЯ И НАУКИ КОСТРОМСКОЙ ОБЛАСТИ
Областное государственное бюджетное профессиональное образовательное учреждение
«Буйский техникум железнодорожного транспорта Костромской области»
КОНТРОЛЬНАЯ РАБОТА
По дисциплине: Конструкция
На тему : Токоприемник ТЛ13У1
Введение
Токоприемниками согласно стандарту называют тяговые электрические аппараты, предназначенные для создания электрического контакта электрооборудования подвижного состава с контактной сетью. Конструкция токоприемника должна обеспечивать съем тока заданного значения при максимальной скорости движения, на которую рассчитан электроподвижной состав.
На советских и зарубежных электрифицированных железных дорогах эксплуатируются токоприемники разнообразных конструкций. Объясняется это тем, что электрификация железных дорог осуществляется как на постоянном, так и на переменном токе, а применяемый электроподвижной состав имеет различную мощность и конструкционную скорость. Наибольшее распространение получили пантографные токоприемники (пантографы).
В Советском Союзе на электровозах и электросекциях переменного тока установлены токоприемники ТЛ-13У. На электровозах постоянного тока наибольшее применение получили токоприемники П-3, П-5 и 10РР, на электросекциях постоянного тока — ТЛ-13У или ТЛ-13М, используют также токоприемники П-1 и ДЖ-5. Токоприемники ТЛ-13У и ТЛ-14М (рис. 8.1) различаются только типами полоза (соответственно с угольными вставками и металлокерамическими пластинами). За рубежом имеются токоприемники с незамкнутой (асимметричной) системой подвижных рам, а также с перекрещивающимися нижними рамами.
Назначение токоприемников
Токоприемники служат для создания электрического соединения между контактным проводом или контактным рельсом и электрическими цепями э.п.с. Конструкция токоприемников определяется расположением контактного провода или рельса относительно локомотива, током нагрузки, скоростью движения подвижного состава, характером изменения расстояния между основанием токоприемника и контактным проводом, условиями управления подъемом и опусканием токоприемников. При верхнем или верхнем и боковом контактных проводах применяют пантографные, дуговые, штанговые и боковые токоприемники; при контактном рельсе-рельсовые токоприемники. На магистральном электроподвижном составе применяют токоприемники пантографного типа. На каждом электровозе установлено по два токоприемника: в работе обычно находится только один, задний по ходу токоприемник. Второй токоприемник является запасным, его поднимают в тех случаях, когда необходимо уменьшить искрение между полозом и контактным проводом при трогании или во время гололеда. Пантографные токоприемники обеспечивают надежный контакт с контактным проводом при больших скоростях движения и токах, не требует перестановки в случае изменения направления движения, удобны для дистанционного управления.
Технические данные токоприемника следующие:
Номинальное напряжение в сети 25 кВ Длительно допустимый ток:
при движении — 500 А
при стоянке 50 А Статическое нажатие на контактный провод в диапазоне рабочей высоты:
активное (при подъеме), не менее — б кгс
пассивное (при опускании), не более — 9 кгс
Максимальная скорость движения — 160 км/ч
Наибольшая высота подъема от сложенного состояния,
не менее — 2100 мм
Рабочая высота:
наибольшая 1900 мм наименьшая 400 мм Длина в сложенном состоянии 3280 мм Ширина (по концам полоза) 2260 мм Опускающая сила в диапазоне рабочей высоты, не менее 11 кгс Разница между наибольшим и наименьшим нажатием при одностороннем движении токоприемника в диапазоне рабочей высоты, не более 1 кгс Двойное трение в шарнирах, приведенное к верхнем) узл\, не более 2 кгс Время подъема до наибольшей рабочей высоты при номинальном давлении сжатого воздуха ~—Ю с Время опускания с наибольшей рабочей высоты при номинальном давлении сжатого воздуха 3,5—6 с Давление сжатого воздуха:
номинальное — 0,5 МПа
(5 кгс/см2)
наименьшее — 0,35 МПа
(3,5 кгс/см2)
Полный ход каретки — 50 мм
Масса токоприемника:
без изоляторов — 290 кг
с изоляторами -315 кг
Устройство токоприемника Л-13У1
Токоприемник Л-13У1 состоит из основания, нижней и верхней подвижных рам, двух кареток, полоза, а так же поъемно-опускающего механизма.
Основание — сварное из двух продольных и двух поперечных швеллеров .Оно укреплено на крыше кузова электровоза на четырех опорных изоляторах.
Нижняя рама — состоит из двух главных валов в виде труб,цапфы которых закреплены в шарикоподшипниках продольных швеллеров основания. Главные валы связаны друг с другом синхронизирующей тягой , которая обеспечивает их одновременное и синхронное вращение. К каждому главному валу в средней части жестко прикреплена Т-образная цилиндрическая труба, на конце которой приварена короткая труба для крепления с трубами верхней рамы.
Верхняя рама — состоит из четырех продольных и двух диагональных труб для жесткости конструкции. Трубы верхней рамы соединены с трубами нижней рамы и между собой шарнирно валиками с шарикоподшипниками.
Все шарниры токоприемника зашунтированы гибкими медными шунтами для уменьшения сопротивления току и для предотвращения заваривания шарниров от дуги.
Каретка — состоит из ряда отдельных штампованных облегченных деталей, шарнирно соединенных друг с другом .На каретке сверху шарнирно укреплен кронштейн для крепления полоза , а внутри каретки находится сжатая пружина.
Каретки позволяют полозу поворачиваться в обе стороны и перемещаться до 50 мм без поворота труб рамы. Это необходимо для улучшения токосъёма при движении на неровностях контактной сети а также для быстрой реакции на изменение высоты подвески провода.
Полоз — выполнен штампованным из стали толщиной 2,5 мм в виде швеллера. Концы полоза загнуты под углом 45 градусов для предотвращения захлестывания контактного провода на воздушных стрелках (общая длина полоза 2260 мм , длина рабочей части полоза 1270мм).
Сверху на полозе укреплены з ряда угольных накладок( 11 угольных накладок общей длиной 1200 мм).
Толщина новых угольных накладок — 25 мм , их износ допускается до толщины 11 мм. Продолжением угольных накладок служат алюминиевые накладки на концах полоза.
Подъемный механизм — состоит из двух крайних растянутых подъёмных пружин,пневматического цилиндра с двумя поршнями со штоками и двумя сжатыми опускными пружинами , двух поперечных рычагов , двух продольных тяг с роликами на концах, которые через кронштейн соединяются с главными валами.
Концы двух подъёмных растянутых пружин через шайбы и шпильки с левой и правой резьбой шарнирно соединены с рычагами главных валов , которые закреплены сверху главных валов как хомуты с помощью регулировочных болтов для регулирования плеча.
Работа токоприемника
Для подъёма токоприемника в его пневматический цилиндр посередине подается сжатый воздух давлением 3,5 — 5 кгс/см2, через электропневматический клапан ЭВТ- 54А.Тогда оба поршня со штоками раздвигаются сжимая обе впускающие пружины в цилиндре. При этом штоки поршней поворачивают оба поперечных рычага наружу , за счет чего обе продольные тяги сдвигаются к середине и ролики на их концах отходят от кронштейнов двух главных валов. разблокирую их . В результате происходит освобождение двух крайних растянутых пружин,которые сжимаются и поворачивают через рычаги оба главных вала с трубами нижней и верхней рам вовнутрь, что приводит к подъёму полоза токоприемника до упора в контактный провод.
Для опускания токоприемника катушка его электропневматического вентиля (245) теряет питание и происходит выпуск воздуха из пневматического цилиндра в атмосферу. Тогда обе съжатые пружины разжимаются и сдвигают оба поршня со штоками к середине цилиндра. При этом оба поперечных рычага за счет штоков поршней поворачиваются во внутрь, а обе продольных тяг проходят зазоры и нажимают на кронштейн сверху главных валов и разворачивают оба главных вала наружу вместе с трубами нижней и верхней рам. При этом полоз токоприемника опускается на амортизаторы основания, так как сила двух опускных пружин плюс вес полоза и подвижных частей токоприемника больше силы двух подъемных пружин не менее чем на 12кгс — это и есть опускающее усилие токоприемника.
Опускание токоприемника происходит неравномерно, в начале происходит быстрый отрыв полоза с целью разрыва дуги, а затем плавное опускание на амортизаторы для избежания удара. Такая неравномерность достигается регулировкой электропневматического вентиля токоприемника ЭВТ-54А.
Техническое обслуживание токоприемников, инструмент и оборудование при его проведении
токоприемник провод рельс
ТО-1.Осмотр крышевого оборудования с «земли». Проверка свободности перемещения рам токоприёмника путем включения и выключения кнопок токоприемников.
ТО-2.(Выписка из Временного руководства по техническому обслуживанию, текущему и среднему ремонтам электровозов постоянного тока взамен правил ремонта ЦТ № 725). При ТО-2 выполняются следующие работы:
Осматривается всё крышевое оборудование. Загрязненные изоляторы очищаются. Изоляторы с трещинами, сколами, свыше 20 % пути возможного перекрытия напряжением, заменяются. Токопроводящие шины и шунты, имеющие следы нагрева и обрыв жил более 15% заменяются
Проверяется крепление токоприемников к опорным изоляторам, состояние основания, рам, полоза, кареток, шарнирных соединений, шунтов, деталей привода
Проверяется вручную работа токоприемников на подъем и опускание. Деформация рам, заедание в шарнирах токоприемников не допускается. В зимний период рамы и полоз токоприемника должны быть очищены от снега и льда. В гололёдный период на подвижные рамы, пружины и скосы полозов токоприемников наносится противогололёдная смазка.
Осматриваются металлокерамические накладки. Они должны быть прочно закреплены на полозе и располагаться на одном уровне. Пластины не должны иметь острых и выступающих углов. Производится запиловка (зачистка) подгоревших пластин. Полозы с изношенными металлокерамическими пластинами или угольными вставками и с прожогами каркаса заменяются.
Проверяется состояние сухой графитовой смазки (СГС-О) полоза с металлокерамическими накладками. Трещины и места выкрашивания смазки заполняются дополнительной графитовой смазкой (СГС-Д).
Проверяется состояние подводящих воздухопроводных труб и полиэтиленовых рукавов. Полиэтиленовые рукава со следами электроожогов и трещин заменяются.
В зимних условиях работы проверяется статическая характеристика токоприемников, в летнее время характеристика проверяется при замене полозов, медленном подъеме (опускании) токоприемника или по записи машиниста.
Браковочные размеры в эксплуатации:
• толщина металлокерамических пластин…………… менее 2,5 мм.
• тоже самое для угольных вставок…………….. .. менее 10 мм.
• зазор в стыке между металлокерамическими
накладками……………………………………………. более 1 мм.
• тоже самое для угольных вставок…………………… более 0,8 мм.
• отклонение полоза от горизонтали на длине 1 метр………………. более 20 мм.
• смещение центра полоза относительно центра основания…………….более 30 мм.
• вогнутость полоза на длине 1 м прямолинейной части……………………более 2 мм
Давление полоза на контактный провод, согласно откорректированного приказа 92Н, для электровозов ВЛ11 и ВЛ11М при подъёме не менее 10 кг/см2, при опускании не более 13 кг/см2, как в зимний, так и в летний период времени.
СМАЗКИ ТОКОПРИЁМНИКА
•СГС-О. Сухая, графитовая смазка-основная. Представляет из себя смесь 35% кумарановой смолы с 65% графита. При изготовлении полозов или при их ремонте эта смесь, разогретая до температуры 180-190° наноситься на разогретые полозы в пространство меду накладками и после остывания превращается в твердую массу тёмно-серого цвета;
•СГС-Д. Сухая, графитовая смазка-дополнительная. Имеет тот же состав, но с добавлением растворителя бензолового происхождения. Применяется для подмазки трещин и отколов в основной смазке СГС-О.
•ЖТ-79Л. Смазка привода с резиновыми манжетами. При замерзании её в цилиндр добавляют 3/5 антифриза Левер: смесь спирта и глицерина в равных долях.
•ЖТКЗ-65 или ЦИАТИМ-201. Смазки привода с кожаными манжетами шарниров. Перед постановкой манжеты пропитываются в прожировочном составе №12: разогретая смесь касторового масла с пчелиным воском;
•ЦНИИ-КЗ. Смазка противогололёдная. Наноситься на подъёмные пружины, подвижные рамы и фартуки полозов слоем 1-2 мм при получении команды «Гололёд»
Применяемая спецодежда и средства защиты:
Жилет сигнальный 2 класса защиты
Комплект «Механик-Л»
Перчатки с полимерным покрытием
Ботинки юфтевые .на МБС подошве
Головной убор сигнальный
Каска защитная
Костюм от пониженных температур «Механик»
Валенки
Галоши на валенки
Очки защитные открытые
Подшлемник
Рукавицы утепленные
№ п.п. |
Наименование работ |
Технические требования |
Инструмент и приспособления |
Исполнитель |
1. |
Осмотреть полозы и угольные вставки на отсутствие прожогов, трещин, исправность каркасов. При наличии трещин и прожогов на полозе заварить электросваркой. Оплавленные поверхности обработать напильником. |
Сварочные работы производить согласно инструкционным указаниям № 251/ЦТ Теп. |
Напильник 2820-0069 (№ 1-4) ГОСТ 1465-80, трансформатор ТС-400. |
Слесарь по осмотру и ремонту крышевого оборудования |
2. |
Убедиться, что ни одна вставка или накладка не имеют качения. Проверить наличие и качество крепления токосъёмных материалов к полозу токоприёмника. При необходимости следует подтянуть ослабшие винты. Изломанные элементы — заменить. Убедиться, что токосъёмный материал соответствует техническим требованиям, и не достиг предельного износа. Износ угольных вставок контролировать, используя риски. |
Полозы с изношенными угольными вставками заменяются. Вогнутость полоза на длине 1 м прямолинейной части должна быть не более 2 мм. Угольные вставки толщиной менее 11 мм заменить. Толщина угольной вставки от верхнего уровня бортовой полосы, служащей для крепления угольных вставок, должна быть не менее 2 мм летом и 3 мм – зимой. Сколы на одной из угольных вставок более 15 мм по ширине и более 6 мм по высоте заменить. Запиловку (зачистку) местной выработки производить под углом не более 20 град. До плавного сопряжения с остальной контактной поверхностью. Допускается не более одной трещины на одну угольную вставку и сколы не более 50% её ширины и 20% высоты, если при этом не ослабляется крепление вставки. Продольные трещины на боковой поверхности вставки не допускаются. Зазор между вставками должен быть не более 0,8 мм. |
Набор щупов №4 ТУ2-034-0221197-011-97, линейка контрольная НО-9-000-000 ТЧ-9, ключ гаечный 7811-0021 (12х14) ГОСТ 2839-80Е, уровень УС-2-11, линейка метал. измерит. (0-150) мм ЦД 1мм ГОСТ 427-75, штангенциркуль ШЦ-1 125-0,1 ГОСТ 166-89, шаблон НО-10-000-000 ТЧ-9, напильник 2820-0069 (№ 1-4) ГОСТ 1465-80, набор щупов №2 ТУ2-034-0221197-011-97. |
Слесарь по осмотру и ремонту крышевого оборудования |
3. |
При ремонте короба полоза очистить его от грязи и ржавчины, особенно в месте крепления угольных вставок. После правки полоза произвести контроль ширины короба и расстояние между отверстиями для винтов, крепящих полоз к корешкам. |
Ширина коробов должна быть равна 148 мм, расстояние между отверстиями для винтов, крепящих полоз равна 1260 мм. Сопряжение боковых дюралюминиевых и стальных средних накладок на криволинейных частях (рогах) полоза должно быть плавным, без уступов и выемок. Головки винтов для крепления дюралюминиевых накладок должны быть запилены. Все кромки деталей тонколистовой стали для полоза и его отдельных элементов не должны иметь заусениц и коробление в прямой его части. Расстояние между концами рогов не должно отличаться от номинального более чем на 15 мм, а высота боковых отбортовок в средней части полоза – более 2 мм. Короб следует править так, чтобы вогнутость полоза на длине 1 м прямолинейной части не превышала 2 мм и 0,5 мм – при измерении по ширине полоза. Наклон рога к горизонтали не должен превышать 45 градусов. Не разрешается на одном коробе заваривать более одной поперечной и двух продольных трещин в средней части (короб не должен иметь более 3 заваренных трещин). Во избежание заметного утяжеления полоза длина сварного шва допускается не более 400 мм. |
Линейка метал. измерит. (0-150) мм ЦД 1мм ГОСТ 427-75.Напильник 2820-0069 (№ 1-4) ГОСТ 1465-80.Линейка метал. измерит. (0-150) мм ЦД 1мм ГОСТ 427-75. Линейка метал. измерит. (0-500) мм ЦД 1мм ГОСТ 427-75. |
Слесарь по осмотру и ремонту крышевого оборудова-ния |
4. |
При необходимости выправить планки (корытца) или бортовую полосу, служащую для крепления угольных вставок. |
|
Молоток 200 гГОСТ2310-77. |
Слесарь по осмотру и ремонту крышевого оборудова-ния |
5. |
Окисленную поверхность медной подложки зачистить металлической щёткой, затем очистить пастой, приготовленной из мела и нашатырного спирта или специальными пастами для очистки меди. После очистки пасту тщательно удалить, а поверхность медной подложки смазать техническим вазелином. |
|
Металлическая щётка, паста, техн. вазелин. |
Слесарь по осмотру и ремонту крышевого оборудова-ния |
6. |
При монтаже вставок на полозе подогнать их друг к другу и к боковым контактным пластинам. |
Зазор между вставками на отремонтированном полозе не должен превышать 0,8 мм. Новые вставки внутреннего ряда следует размещать на одном уровне со вставками наружных рядов или ниже их на 1,5 мм. Для обеспечения надёжного закрепления вставок при сборке следует подогнать корытце. Если какое-либо корытце не перекрывает стыка вставок нормальной длины, заменить его на удлинённое. Корытце при сборке следует подогнать и закрепить так, чтобы исключить возможность перемещений и качений вставок на смонтированном полозе. Запиливать вставки в стыках друг с другом следует так, чтобы переход контактного провода был плавным. По ширине контактные поверхности запиливать так, чтобы в контакте участвовало 3/4 ширины вставок, т.е. суммарная ширина запиленной поверхности каждой вставки составляла не менее 22 мм. Концы внутреннего ряда вставок запиливаются с каждой стороны на 5-6 мм по длине и на 3 мм — по высоте. |
|
Заключение
В ходе выполнения данной работы мною были изучены вопросы:
1.Назначение токоприемника
2.Устройство токоприемника
3.Принцип работы при подъёме и опускании токоприемнтка
4.Виды технического обслуживания , инструмент используемый при обслуживании и требования к ним.
Назначение, устройство токоприемника Л-13У1 (Л-14М1) — Мегаобучалка
Напряжение от тяговой подстанции к электровозу подается по своеобразной двухпроводной линии электропередачи. Одним проводом являются рельсы, а другим — контактная сеть, точнее контактный провод. Электровоз имеет непрерывный электрический контакт с рельсами (через колеса). Поэтому в нормальных условиях потенциал корпуса электровоза, как и потенциал рельсов, равен потенциалу земли. Таким образом, для силовой цепи электровоза одним полюсом является контактный провод, а вторым — корпус. Переменный ток из контактного провода в цепи электровоза поступает через пантографный токоприемник (пантограф). При движении электровоза такой токоприемник скользит по контактному проводу, осуществляя токосъем.
Особенности работы скользящего контакта предъявляют к конструкции пантографного токоприемника определенные требования. Токоприемник должен быть легким, чтобы во время скольжения его полоза по контактному проводу, высота подвески которого изменяется, он успевал «следить» за ней — не отрывался от контактного провода при увеличении высоты подвески и не создавал сильных ударов по проводу при уменьшении высоты. Контактная поверхность полоза токоприемника должна быть гладкой, что уменьшает износ контактного провода и обеспечивает хороший контакт во время движения, так и во время стоянки электровоза (на стоянке электровоз может потреблять значительный ток для цепей отопления поезда и цепей собственных нужд). Необходимо, чтобы пружинный механизм обеспечивал примерно одинаковое нажатие токоприемника на провод независимо от высоты контактного провода. Кроме того, токоприемник должен иметь высокую механическую прочность, надежную изоляцию от заземленных частей электровоза, малое трение в шарнирных соединениях подвижной системы и достаточную боковую устойчивость ее против колебаний и вибраций.
Токоприемник выполняют обтекаемым, так как при этом он имеет удовлетворительные аэродинамические характеристики, особенно полоз. Это требование обусловлено тем, что при большой скорости движения электровоза нажатие токоприемника на контактный провод не должно изменяться в больших пределах и совершенно недопустим отрыв его от контактного провода. Кроме того, характеристика токоприемника должна быть такой, чтобы даже при очень сильном ветре не могло произойти его самопроизвольного подъема. Необходимо также, чтобы механизм подъема — опускания был прост и надежен в работе. Предусматривается возможность дистанционного управления подвижной системой при всех условиях работы.
На электровозах переменного тока при опускании токоприемника всегда возникает дуга между полозом и контактным проводом. Даже при отключенном главном выключателе через поднятый токоприемник протекают небольшие емкостные токи. Роль конденсаторов (емкостей) здесь играют шины 25 кВ и помехоподавляющий дроссель, расположенный вблизи заземленной крыши электровоза.
Длительность горения дуги, возникающей при опускании токоприемника, по возможности должна быть минимальной. Поэтому необходимо, чтобы в начале опускание происходило быстро, а затем во избежание удара медленно. Все токоприемники электровозов имеют один и тот же принцип действия. Подвижная система связана с системой спиральных пружин, часть которых действует в направлении подъема, а другая — в направлении опускания токоприемника. Усилия опускающих пружин всегда превосходят усилия подъемных, и токоприемник при отсутствии внешних воздействий находится в опущенном положении. Для подъема его предусмотрено специальное устройство, приводимое в действие сжатым воздухом; управляют им из кабины машиниста.
Независимо от типа и конструктивных особенностей все токоприемники состоят из четырех основных узлов (рис.1): основания, выполненного в виде рамы, укрепленной на опорных изоляторах; подвижной системы, состоящей из подвижных рам, шарнирно соединенных друг с другом и с основанием; контактной системы, представляющей собой совокупность кареток и одного или двух полозов с контактными вставками; механизма подъема — опускания, состоящего из подъемных и опускающих пружин, системы рычагов и приводного воздушного цилиндра.
Рисунок 1 – Общий вид токоприемника Л-13У
1- верхняя рама; 2 – полоз; 3 – каретка; 4 – нижняя рама
На полозе токоприемника укреплены токосъемные угольные вставки (раньше были медные накладки). Медные накладки необходимо было систематически смазывать, так как только при обильной смазке они работали хорошо, не вызывая повышенного износа контактного провода. При недостаточной смазке (например, после сильного дождя) на трущихся поверхностях медной накладки и провода появлялись задиры, неровности, увеличивающие износ контактного провода и ухудшающие токосъем.
Угольные вставки (рис. 2) выгодно отличаются от медных. Они не требуют смазки. Благодаря слоистой структуре графита при скольжении вставки по проводу происходит самосмазывание. Все неровности контактного провода заполняются графитом, провод шлифуется. При угольных вставках износ контактного провода в несколько раз меньше, чем при медных. Поэтому угольные вставки получили практически повсеместное распространение на электровозах переменного тока