Получение стали: получение стали, процесс и способы. Технология получения стали
Производство стали: способы, технология и сырье
Сталь – это прочный материал и основной конструкционный материал для машиностроения. Он представляет сплав железа с углеродом, содержание которого в структуре составляет 0,01–2,14%. В состав также входят в незначительных количествах кремний, марганец и сера. Этот материал обладает исключительными механическими свойствами: твердостью и ковкостью, благодаря им он считается основным конструкционным материалом в машиностроении. Трудно представить, что могло бы заменить материал. Но активное развитие производство стали и других металлов. Из стали изготавливаются самые разнообразные изделия – от канцелярских скрепок до станин многотонных прессов и обшивки корпусов морских судов.
Процесс производства
Производится сталь плавкой. Исходным сырьем служат чугун, лом самой стали или чугуна, окатыши, флюсы и ферросплавы.
Сам чугун по природе – недостаточно твердый и хрупкий материал, поэтому имеет ограниченное применение.
Однако, он незаменим в качестве сырья для получения стали. Суть плавки состоит, в случае применения передельного чугуна, в снижении процентного содержания углерода в нем до требуемого уровня.
Выводятся не предусмотренные в конечной рецептуре примеси. Традиционный состав шихты представляет 55% чугуна и 45% стального лома (скрапа). Существует также рудный процесс, когда к компонентам добавляется рудный материал или скрап-процесс для переработки отходов машиностроительного производства.
Чтобы в процессе плавки примеси и углерод легче выводился из состава компонентов, они переводятся в газы и шлак. В первую очередь при взаимодействии чугуна с кислородом железо окисляется, образуя закись железа FeO.
Одновременно окисляются C, Si, Mn и P, при этом происходит отдача кислорода оксидом железа химически активным примесям. К массе шихты добавляют флюс для лучшего растворения металла: известняк или известь, боксит. В качестве топлива используют каменноугольную пыль, жидкий мазут, природный или коксовый газ.
Особенности процесса
Процесс производства стали происходит последовательно в три этапа.
Первый этап – расплавление породы. На этапе его проведения формируется расплав в ванне и окисляется металл, отдавая одновременно кислород кремнию, фосфору и марганцу.
Одна и главных задач этого этапа – удаление фосфора. Для ее осуществления требуется сравнительно невысокая температура и присутствие в достаточном количестве FeO. При взаимодействии ингредиентов фосфорный ангидрид образует с оксидом железа нестойкое соединение (FeO)3 + P2O5.
Присутствие в шлаке более стойкого основания СаО вызывает замещение FeO. В результате оно связывает фосфорный ангидрит в другое соединение (CaO)4 х P2O5 + 4 Fe, чего и требовалось добиться.
Чистый Fe высвободился в расплаве, а фосфор образовал шлак, который удаляется с зеркала металла и утилизируется за ненадобностью. Поскольку фосфорный ангидрид преобразует состав шлака, процесс должен идти непрерывно.
Поэтому FeO должен непрерывно пополняться за счет загрузки новых партий железной руды и окалины, наводящих в расплаве железистый шлак.
Особенности второго этапа
Технология производства стали на втором этапе называется кипением стали. Основное назначение заключается в процентном снижении содержания углерода за счет окисления. FeO + C = CO + Fe.
Реакция окисления происходит более интенсивно при кипении и сопровождается поглощением тепла. Поэтому необходимо создавать постоянный приток тепла в ванну, а также для выравнивания температуры в расплаве.
При такой реакции окисления интенсивно выделяется газ оксида углерода CO, что вызывает бурное кипение в жидком агрегатном состоянии, по этой причине процесс называют кипением. Чтобы излишки углерода интенсивнее преобразовывались в окись, производство качественной стали предусматривает вдувание чистого кислорода и добавление в расплавленную структуру окалины. Поэтому таким важным является качество сырья для производства стали. Все исходные материалы проходят щепетильную проверку.
Немаловажным на этом этапе является вывод серы, благодаря чему повышается качество конечной стали. Используемая в компонентах сера, присутствует не в прямом виде, а в форме сульфида железа FeS.
При высоких температурах компонент также взаимодействует с оксидом СаО, образуя сульфид кальция CaS, который растворяется в шлаке, не соединяясь с железом. Это позволяет беспрепятственно выводить сульфид за пределы ванны.
Конвертерное производство стали
Раскисление
Третий этап – раскисление металла. После добавления кислорода (на предыдущем этапе) требуется снизить его содержание в чистой стали. Использованием О2 удалось добиться окисления примесей, но его остаточное присутствие в конечном продукте снижает качественные характеристики металла. Требуется удалить или преобразовать окислы FeO, связав кислород с другими металлами.
Для этого существуют два метода раскисления:
- диффузионное;
- осаждающее.
При диффузионном методе в расплавленный состав вводят добавки: алюминий, ферромарганец и ферросилиций. Они восстанавливают оксид железа и переводит в шлак. В шлаке оксид распадается и высвобождает чистое железо, которое поступает в расплав. Второй высвободившийся элемент – кислород улетучивается в окружающую среду.
Осаждающий метод предусматривает введение добавок, имеющих большее сродство с кислородом, чем Fe. Происходит замещение этими веществами железа в окисле. Они, как менее плотные, всплывают и выводятся вместе со шлаком.
Процесс раскисления продолжается при затвердевании слитка, в кристаллической структуре которого оксид железа и углерод взаимодействуют. В результате чего вместе с пузырьками азота, водорода он выводится.
Чем больше при раскислении выводится включений различных металлов, тем выше ковкость получаемой стали. Для проверки раскаленный кусок металла подвергают ковке, на нем не должны образовываться трещины. Такая проверка пробы говорит о правильном проведении процесса раскисления.
В зависимости от степени раскисления специалисты могут получить:
- спокойную сталь полного раскисления;
- кипящую раскисленную не полностью сталь, когда процесс выведения пузырьков угарного газа СО продолжается в ковше и изложнице.
Для получения легированных сталей с добавками некоторых металлов в расплавленный металл добавляются ферросплавы или чистые металлы. Если они не окисляются (Ni, Co, Mo), то такие добавки могут вводиться на любом этапе плавки. Более чувствительные к окислению металлы Si, Mn, Cr, Ti добавляют в ковш или, что обычно и происходит, в форму для отливки металла.
Существуют основные способы получения стали в сталеплавлении.
Мартеновский способ
Этот способ применяется для производства сталей высокого качества, применяемых в особо ответственных деталях машинах и точных механизмах.
В свое время он заменил трудоемкие и малопроизводительные тигельную и пулдинговую плавки, применявшиеся ранее.
Емкость загрузки одной отражательной печи, используемой при этом методе, достигает 500 тонн. Особенностью мартеновского способа является возможность переплавки не только передельного чугуна, но и металлургических отходов, металлического лома.
Температура нагрева жидкой стали достигает 2 тыс. градусов. Этот результат достигается специальной конструкцией мартеновской печи:
- применением дополнительного тепла регенераторов, получаемого сжиганием коксовального или доменного газа в струе горячего воздуха;
- отражения от свода закачиваемого газа в результате сгорание топлива в нем происходит над ванной с металлом, что способствует быстрому нагреву содержимого;
- применением реверсирования нагревающего потока.
Мартеновская печь состоит из следующих элементов:
- рабочего пространства с огнеупорной футеровкой стенок и завалочными окнами;
- подины (основания) из магнезитового кирпича;
- свода печи;
- головки печи;
- шлаковика для выведения пыли;
- регенератора с перекидными клапанами.
Процесс плавки занимает от 4 до 12 часов. С целью ускорения процесса плавки объем закачиваемого кислорода превышает потребности, что повышает производительность плавки на 20–30%.
Конвертерный метод
В конверторах выплавляют сорта стали для производства автомобильного листа, инструментальной стали сварных конструкций и других стальных заготовок. По качеству они уступают мартеновскими применяются для изготовления менее ответственных изделий.
В них содержится больше примесей, чем при мартеновском изготовлении. Благодаря высокому объему загрузки одной печи до 900 тонн, способ считается самым производительным, поэтому получил широкое распространение.
Производство стали и другого вида металла этим методом основано на продувке жидкого чугуна воздухом или кислородом под давлением 0,3–0,35 МПа, при этом металл разогревается до 1600 градусов. Плавка скоротечна и длится до 20 минут. За это время происходит окисление углерода, кремния и марганца, содержащихся в сырье, которые извлекаются из ванны с расплавом шлака.
Конвертер представляет сосуд ретортообразной (грушевидной) формы, состоящий из стальных листов с футеровкой изнутри. Для заливки чугуна и выпуска готовой стали используется одно отверстие, в него также загружается чугун и скрап.
Рождение стали
Особенности процесса
Вместе с ними загружаются шлакообразующие вещества: известь и бокситы. Корпус охвачен опорным кольцом, прикрепленным к поворотным цапфам. С их помощью сосуд наклоняется и через это отверстие – летку выливается готовая сталь. Нижняя продувка осуществляется через сквозные отверстия (фурмы), сделанные в днище печи.
Исторически повелось, что используемый везде способ называется томасовским, бессемеровским. В прошлом веке преобладающим стал мартеновский процесс. Нагрев регенератора осуществляется продувкой печных газов, после чего он нагревается холодный воздух, поступающий на расплав.
В современных конструкциях чаще применяют верхний способ, при котором продувка на огромной скорости осуществляется через опускаемые к поверхности металла сопла. В России преимущественно используется именно верхняя продувка печей.
Находясь под струей воздуха, чугун интенсивно окисляется в зоне контакта. Поскольку его концентрация значительно больше других примесей, преимущественно образуется оксид железа. Но он растворяется в шлаке. Поэтому металл обогащается выделяемым кислородом.
Окисляются C, Cr и Mn, снижая процентное содержание в структуре металла. Окисление сопровождается выделением тепла. Благодаря присутствию шлаков СаО и FeO до разогрева происходит выведение фосфора в самом начале продувки.
Шлак с ним сливается и наводится новый. Производство стали сопровождается экспресс-анализами и контролем текущих изменений приборами контроля, вмонтированных в печь. Содержание фосфора в чугуне не должно превышать 0,075%.
Кислородно-конвертерный способ получения стали
Производство стали сегодня осуществляется в основном этим способом. На долю кислородно-конверторного производства совсем недавно приходилось до 60% мирового производства стали.
Однако, этот процент снижается в связи с появлением электродуговых печей (ЭДП). Продувка печей осуществляется чистым кислородом (99,5%) под высоким давлением.
Продукт кислородно-конвертерной печи представляет сталь с заданными химическими свойствами. Она поступает в машину непрерывного литья заготовок (МНЛЗ), где материал застывает в форме блюма или плиты. Для получения определенных жестких параметров металл подвергается вторичной переработке.
Электросталеплавильный способ
Производство стали электрической плавкой обладает рядом неоспоримых преимуществ. Этот способ считается основным при выплавке высококачественных легированных сталей.
Достигаемая при этом высокая температура позволяет выплавлять стали, содержащие тугоплавкие металлы:
- молибден;
- вольфрам;
- ванадий.
Высокое качество достигается практическим отсутствием в сталях фосфора, серы и кислорода. Этот способ также применяется для производства широкой номенклатуры строительных сталей.
Выделение тепла не связано с потреблением окислителя, а происходит в результате преобразования электрической энергии в тепловую. Она выделяется при прохождении электрической дуги или наведения вихревых токов. В зависимости от принципа работы печи подразделяются на электродуговые и индукционные.
Электродуговая печь способна принять одновременно от 3,5 до 270 тонн сырья:
- жидкой стали из конвертеров;
- скрапа;
- железной руды.
Она имеет несколько электродов из графитосодержащего материала, к которым подводится электрическое напряжение. Время плавки составляет до 1,5 часа, при этом температура дуги достигает 6 тыс. градусов.
Особенности электроиндукционных печей
В электроиндукционных печах сталь выплавляют в небольших по объему (4,5–60 тонн) емкостях, именуемых огнеупорными тиглями. Вокруг тигля располагается индуктор, состоящий из большого количества витков провода.
При прохождении переменного тока внутри индуцируются вихревые токи большой силы, вызывающее плавление содержимого тигля. Электромагнитные силы одновременно перемешивают расплав стали. Продолжительность плавки в таких печах не превышает 45 мин.
Электросталеплавильный способ производит мало дыма, пыли и меньше излучает световой энергии. Однако, высокая стоимость электрооборудования при малой вместительности ограничивает применение этого способа.
Схема электросталеплавильной печи
Помимо рассмотренных вариантов, существуют не только основные способы производства стали. В современном сталеплавлении используется плавка в вакуумных индукционных печах и обогащение процентного содержания железа в окатышах плазменно-дуговым переплавом.
Виды получаемых сталей по химическому составу
Производимая этими методами сталь делится, в зависимости от химического состава, на две большие группы:
- углеродистую;
- легированную.
Процентное содержание элементов в углеродистой стали:
Наименование | Fe | С | Si | Mn | S | P |
Содержание в процентах | до 99,0 | 0,05–2,0 | 0,15–0,35 | 0,3–0,8 | до 0,06 | до 0,07 |
В углеродистых сталях прочность недостаточно сочетается с пластичностью. Недостаток устраняется введением добавок других металлов, такая сталь называется легированной.
Согласно ГОСТ 5200 выделяют три группы легированных сталей с допустимым содержанием примесей:
- низколегированная не более 2,5%;
- среднелегированная в диапазоне 2,5–10%;
- высоколегированная свыше 10%.
С каждым годом способы плавки усовершенствуются благодаря вводу в строй нового высокотехнологичного оборудования. Это позволяет получать в сталелитейной промышленности высококачественные стали с оптимальным содержанием добавок и металлов.
Видео по теме: Производство чугуна и стали
Способы производства стали
Технологический процесс производства углеродистой стали можно разделить на два этапа. Сначала из руды выплавляется чугун, который на следующем этапе перерабатывается в сталь. При сокращении в расплавленном чугуне вкраплений углерода и иных примесей, которые в процессе плавления сгорают или отделяются в форме шлака. В качестве исходного сырья для изготовления стали используется чугун, металлолом, железные руды, также в расплавленный металл могут быть добавлены флюсы и ферросплавы. Существуют три принципиально отличающихся технологии выпуска: электрическое плавление, конвертерный метод и плавка в мартеновских печах, последний способ на сегодняшний день считается наиболее эффективным и распространенным, а производимая сталь по своему качеству выше, чем при конверторной плавке.
Мартеновский способ.
Масса загрузки мартеновских печей доходит до тысячи тонн, внутреннее пространство выполняется в виде камеры, вытянутой по горизонтальной оси и обкладывается специальным выдерживающим высокую температуру кирпичом. В верхнем отделении проложены каналы, связывающие камеру с теплообменными устройствами (регенераторами). Нижняя часть конструкции, имеет форму ванны и называется подом. Для усиления эффекта в регенераторах производится подогрев газа. В мартеновской печи плавится твердый или жидкий чугун с добавлением железной руды или стального металлолома. Углерод сгорает под воздействием высокой температуры, окисляющиеся под воздействием кислородного дутья примеси преобразуются в шлак и удаляются с поверхности расплавленного металла, сера удаляется при помощи содержащего известь флюса. За время плавления, занимающее от четырех до восьми часов, имеется возможность добавления в состав металла дополнительных компонентов, для получения на выходе легированной стали. В процессе плавления производится отбор образцов металла для химического анализа, при получении желаемых параметров расплавленная сталь выпускается в ковш, откуда разливается формам. Из стали произведенной по этому методу производят монорельсовые и подкрановые балки, фермы мостов и цеховых перекрытий, железнодорожные рельсы и арматуру.
Конверторный способ.
Печь конвертерная представляет вращающийся относительно горизонтальной оси стальной футерованный корпус грушевидной формы. При помощи ковша внутренняя часть конвертера наполняется расплавленным чугуном, через отверстия в корпусе под давлением нагнетается воздушно кислородная смесь образуя в сплаве закись железа, взаимодействующую с нежелательными в сплаве элементами, преобразовывает их в шлак или выгорающие оксиды. Метод считается экономичным и отличается высокой производительностью, занимает от пятнадцати до тридцати минут, емкость конвертерных печей достигает до шестисот тонн, полученный металл используется для производства стальных листов, балок, швеллеров, катанки и проволоки.
Электроплавка.
Электроплавильные дуговые или индукционные печи служат для получения сталей высокого качества, в печь загружают руду, скрап или стальной сплав после конвертера или из мартеновской печи, в процессе добавляются легирующие металлы. Для нагрева используется электрическая дуга между расплавом и специальными электродами. Выплавка по этой технологии позволяет получать сталь очень хорошего качества, но имеет высокую себестоимость и низкую производительность, как правило, применяются печи до двухсот тонн. В связи с этим часто применяются разные типы печей, сначала сплав готовят в конвертерной печи или мартене, а затем подается в электропечь, где доводится до более высокого качественного уровня.
Читать далее.
Уважаемые партнеры, клиенты, заказчики. Для оперативной обработки вашей заявки указывайте в заказе каким образом необходимо подготовить металл к отгрузке. Нужно ли порезать его для транспортировки, на какую длину? Если заказываете доставку нашими силами, укажите по какому адресу и в какой город, какой транспортной компанией или каким отдельным видом транспорта необходимо произвести отправку приобретаемого вами металла.
Способы производства стали
С момента изобретения стали, менялись и совершенствовались способы ее производства. В настоящее время существует несколько приоритетных способов производства стали. К ним относятся кислородно-конвертерный, мартеновский и электросталеплавильный способы производства (или плавления) стали. В основе всех этих способов лежит окислительный процесс, направленный на снижение в чугуне некоторых веществ. Давайте остановимся на каждом способе более подробно и рассмотрим их отличия.
Кислородно-конвертерный способ
Первое использование кислородно-конвертерного способа приходится на пятидесятые годы двадцатого столетия. В процессе производства стали, чугун продувают в конвертере чистым кислородом. При этом, процесс происходит без затраты топлива. Для того, чтобы переработать 1 тонну чугуна в сталь требуется около 350 кубометров воздуха. Стоит отметить, что кислородно-конвертерный способ получения стали является наиболее актуальным на сегодняшний день. При этом, процесс не ограничивается на одном способе вдувания кислорода. Различают кислородно-конвертерный процесс с комбинированной, верхней и нижней поддувкой. Конвертерный способ производства стали с комбинированной поддувкой является наиболее универсальным.
Для осуществления этого метода необходим конвертер. Подача кислорода осуществляется через водоохлаждаемую фурму под давлением. В данном случае, процесс окисления является наиболее значимым. Окисление чугуна происходит под воздействием дутья. В результате окисления выделяется тепло, что способствует снижению примесей и повышению температуры металла. далее происходит так называемое раскисление металла.
Мартеновский способ
В процессе производства стали мартеновским способом, участвует специальная отражательная печь. Для того чтобы нагреть сталь до нужной температуры (2000 градусов), в печь вводят дополнительное тепло с помощью регенераторов. Это тепло получают за счет сжигания топлива в струе нагретого воздуха. Обязательное условие – топливо должно полностью сгорать в рабочем пространстве. Особенностью мартеновского способа производства стали является то, что количество кислорода, подаваемого в печь, превышает необходимый уровень. Это позволяет создать воздействие на металл окислительной атмосферы. Сырье (чугун, железный и стальной лом) погружается в печь, где подвергается плавлению в течение 4 – 6 часов. В процессе плавления есть возможность проверять качество металла, путем взятия пробы. В мартеновской печи возможно получать специальные сорта стали. Для этого в сырье вводят необходимые примеси.
Электросталеплавильный способ
В результате электросталеплавильного способа, получают сталь высокого качества. Процесс этот происходит в специальных электрических печах. Основной принцип электросталеплавильного способа производства стали – использование электроэнергии для нагрева металла. Механизм производства следующий: в результате горения нагревательного элемента, выделяется тепло, за счет преобразования электроэнергии в тепловую энергию. Важно отметить, что процесс выплавки связан с выработкой шлаков. Качество получаемой стали во многом зависит от количества и состава шлаков. Основной причиной образования шлаков, в процессе производства стали, является окисление шихты из оксидов.
Благодаря шлакам, происходит связь оксидов, которые образуются в процессе окисления чугуна, а так же удаление ненужных примесей. Кроме этого, шлаки являются передатчиками тепла и кислорода. Присутствие шлаков в процессе производства стали оказывает благотворное влияние на качество стали. Определенное соотношение количества шлаков выводит из стали ненужные вредоносные вещества, например, фосфор. Кроме вышеперечисленных способов производства стали, известны и такие способы, как производство стали в вакуумных индукционных печах, плазменно-дуговая сварка.
Давайте подробнее остановимся на способе производства особо чистой стали, а так же жаропрочных сплавов. Суть способа состоит в выплавке в вакуумных печах. После такой выплавки, сталь дополнительно переплавляют вакуумным дуговым переплавом. Что дает возможность получения качественной однородной стали. Такая сталь применяется, в основном, в авиакосмической промышленности, атомной энергетике и других важных отраслях. Мы рассмотрели основные способы производства стали. Выбор способа всегда зависит от поставленных задач, удобства применения оборудования, необходимого качества полученной стали и от других факторов. Естественно, что каждый способ имеет свои преимущества и свои недостатки.
Вся эта сталь применяется для производства металлопроката и спец сталей, на нашей металлобазе Вы можете найти широкий выбор и того и другого.
Первый этап
На этом этапе идет расплавление шихты и нагрев жидкого металла. Температура металла невысока. Начинается интенсивное окисление железа, так как оно содержится в наибольшем количестве в чугуне и по закону действующих масс окисляется в первую очередь. Одновременно начинает окис-лятся примеси Si, P, Mn. Образующийся оксид железа (FeO) при высоких температурах растворяется в железе и отдает свой кислород более активным элементом (примесям в чугуне), окисляя их. Чем больше оксида железа содержится в жидком металле, тем активнее окисляются примеси. Для ускорения окисления примесей в сталеплавильную печь добавляют железную руду, окалину, содержащие оксиды же-леза.
Скорость окисления примесей зависит не только от их концентрации, но и от температуры металла и подчиняется принципу, в соответствии с которым хи-мические реакции, выделяющие теплоту, протекают интенсивнее при более низких температурах, а реакции поглощающие теплоту, протекают активнее при высоких температурах. Поэтому в начале плавки, когда температура металла невысока, интенсивнее идут процессы окисления кремния, фосфора, марганца, протекающие с выделением теплоты, а углерод интенсивно окисляется только при высокой температуре металла.
Наиболее важной задачей этого этапа является удаление фосфора. Для этого необходимо проведение плавки в основной печи, в которой можно использовать основной шлак, содержащий СаО, применяемый для удаления фосфора. В ходе плавки фосфорный ангидрид Р2О5 образует с оксидом железа нестойкое соединение (FeO)3⋅Р2О5. Оксид кальция СаО более сильное основание, чем оксид железа. Поэтому при невысоких температурах он связывает ангидрид Р2О5 в прочное соединение , (CaO)⋅Р2О5 переводя его в шлак. Для удаления фосфора из металла шлак должен содержать достаточное количество оксида железа FeO. Для повышения содержания FeO в шлаке в сталеплавильную печь в этот период плавки добавляют железную руду, окалину, наводя железистый шлак. По мере удаления фосфора из металла в шлак содержание его в шлаке возрастает. В соответствии с законом распределения, когда вещество растворяется в двух несмешивающихся жидкостях, распределение его между этими жидкостями происходит до установления определенного соотношения постоянного для данной температуры. Поэтому удаление фосфора из металла замедляется и для более полного удаления фосфора из металла шлак, содержащий фосфор удаляют, и наводят новый со свежими добавками (CaO).
Второй этап
Этап начинается по мере прогрева металлической ванны до более высоких температур, чем на первом этапе. При повышении температуры более интенсивно протекает реакция окисления углерода, проходящая с поглощением тепла. Для окисления углерода на этом этапе в металл вводят зна-чительное количество руды, окалины или вдувают кислород.
Образующийся в металле оксид железа реагирует с углеродом и пузырьки оксида углерода СО выделяются из жидкого металла, вызывая кипение ванны. При кипении ванны:
- уменьшается содержание углерода в металле;
- выравнивается температура и состав ванны;
- удаляются частично неметаллические включения в шлак.
- Все это способствует повышению качества металла.
В этот же период создаются условия для удаления серы из металла. Сера в ванне находится в виде сульфида железа, растворенного в металле [FeS] и шла-ке (FeS). Чем выше температура, тем большее количество FeS растворяется в шлаке или больше серы переходят из металла в шлак. Сульфид железа, раство-ренный в шлаке, взаимодействует с оксидом кальция СаО, также растворенным в шлаке, образуя соединение CaS, которое растворимо в шлаке, но не растворя-ется в металле. Таким образом сера удаляется в шлак.
Третий этап
Этот этап является завершающим, в котором производится раскисление и, если требуется, легирование стали. Раскисление представляет собой технологическую операцию, при которой растворенный в металле кислород переводится в нерастворимое соединение и удаляется из металла. При плавке повышенное содержание кислорода в металле необходимо для окисления примесей. В готовой же стали кислород является нежелательной примесью, так как понижает механические свойства стали, особенно при высоких температурах.
Для раскисления стали используют элементы-ракислители, обладающие большим сродством к кислороду, чем железо. В качестве раскислителей используют марганец, кремний, алюминий. Существует несколько способов раскисления стали. Наиболее широко применяются:
- осаждающий способ;
- диффузионный.
Осаждающий способ
Раскисление по этому способу осуществляют введением в жидкую сталь раскислителей (ферромарганца, ферросилиция, алю-миния), содержащих Mn, Si, Al. В результате раскисления образуются оксиды MnO, SiO2, Al2O3, которые имеют меньшую плотность, чем сталь, и удаляются в шлак. Однако часть оксидов не успевает всплыть и удалится из металла, что понижает его свойства. Этот способ называют иногда глубинным, так как рас-кислители вводятся в глубину металла.
Диффузионный способ
По этому способу раскисление осуществляют раскислением шлака. Ферромарганец, ферросилиций и другие раскислители загружают в мелкоизмельченном виде на поверхность шлака. Раскислители, восстанавливая оксид железа, уменьшают его содержание в шлаке. В соответс-твии с законом распределения оксид железа, растворенный в стали, начнет пе-реходить в шлак. Образующиеся при таком способе раскисления оксиды остаю-тся в шлаке, а восстановленное железо переходит в сталь, что уменьшает в ней содержание неметаллических включений повышает ее качество.
Ввиду того, что скорость процесса перемещения кислорода из металла в шлак определяется скоростью его диффузии в металле, этот способ имеет и не-которые недостатки. Из-за малой скорости диффузии кислорода в металле про-цесс удаления кислорода идет медленно, возрастает продолжительность плавки. В зависимости от степени раскисленности различают стали:
- кипящие;
- спокойные;
- полуспокойные.
Кипящая сталь
Это сталь, выплавленная без проведения операции рас-кисления. При разливке такой стали и при ее постепенном охлаждении в излож-нице будет протекать реакция между растворенными в металле кислородом и углеродом
[O]+[C]=COг
Образующиеся при этом пузырьки оксида углерода СО будут выделятся из кристаллизующегося слитка, и металл будет бурлить. Такую сталь называют кипящей. Кипящая сталь практически не содержит неметаллических включений, представляющих продукты раскисления. Поэтому она обладает хорошей пластичностью.
Спокойная сталь
Это сталь, полученная после проведения операции рас-кисления. Такая сталь при застывании в изложнице ведет себя спокойно, из нее не выделяются газы. Такую сталь называют спокойной.
Полуспокойная сталь. Сталь имеет промежуточную раскисленность между спокойной и кипящей. Раскисление ее проводят частично, удаляя из нее не весь кислород. Оставшийся кислород вызывает кратковременное кипение металла в начале его кристаллизации. Такую сталь называют полуспокойной.
Легированные стали
Легированием называют процесс присадки в сталь специальных (легирующих) элементов с целью получить так называемую леги-рованную сталь с особыми физико-химическими или механическими свойствами. Легирование осуществляют введением ферросплавов или чистых металлов в необходимом количестве в сплав. Легирующие элементы, сродство к кислороду которых меньше, чем у же-леза (Ni, Cu, Co, Mo), при плавке и разливке практически не окисляются и по-этому их вводят в печь в любое время плавки. Легирующие элементы, у которых сродство к кислороду больше, чем у железа (Si, Mn, Al и др.), вводят в металл после или одновременно с раскислением.
ПОДЕЛИСЬ ИНТЕРЕСНОЙ ИНФОРМАЦИЕЙ
Выплавка стали: технология, способы, сырье
Железную руду получают привычным способом: открытой или подземной добычей и последующей транспортировкой для первоначальной подготовки, где материал измельчается, промывается и перерабатывается.
Руду засыпают в доменную печь и подвергают струйной обработке горячим воздухом и теплом, который превращает ее в расплавленное железо. Далее оно извлекается из нижней части печи в формы, известные как свиньи, где происходит остывание для получения чугуна. Он превращается в кованое железо или перерабатывается в сталь несколькими способами.
Что такое сталь?
Вначале было железо. Оно является одним из наиболее распространенных металлов в земной коре. Его можно встретить почти везде, в сочетании со многими другими элементами, в виде руды. В Европе начало работы с железом датируется 1700 г. до н.э.
В 1786 году французские ученые Бертолле, Мондж и Вандермонде точно определили, что разница между железом, чугуном и сталью обусловлена различным содержанием углерода. Тем не менее сталь, изготовленная из железа, быстро стала самым важным металлом промышленной революции. В начале XX века мировое производство стали составило 28 миллионов тонн — это в шесть раз больше, чем в 1880 году. К началу Первой мировой войны ее производство составляло 85 миллионов тонн. В течение нескольких десятилетий она практически заменила железо.
Содержание углерода влияет на характеристики металла. Существует два основных вида стали: легированная и нелегированная. Сплав стали относится к химическим элементам, отличным от углерода, добавленного к железу. Таким образом, для создания нержавеющей стали используется сплав 17 % хрома и 8 % никеля.
В настоящее время существует более 3000 каталогизированных марок (химических составов), не считая тех, которые созданы для удовлетворения индивидуальных потребностей. Все они способствуют превращению стали в наиболее подходящий материал для решения задач будущего.
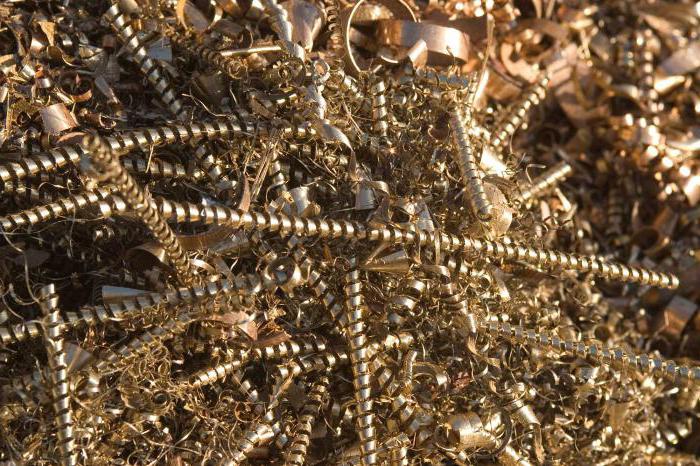
Сырье для выплавки стали: первичное и вторичное
Выплавка данного металла с использованием многих компонентов – самый распространенный способ добычи. Шихтовые материалы могут быть как первично используемые, так и вторично. Основной состав шихты, как правило, составляет 55 % чугуна и 45 % оставшегося металлолома. Ферросплавы, переделанный чугун и технически чистые металлы используются как основной элемент сплава, ко вторичным, как правило, относят все виды черного металла.
Железная руда является самым важным и основным сырьем в черной металлургии. Для производства тонны чугуна требуется около 1,5 тонны этого материала. Для производства одной тонны чугуна используется около 450 тонн кокса. Многие металлургические заводы применяют даже древесный уголь.
Вода — важное сырье для черной металлургии. Она в основном используется для закалки кокса, охлаждения доменных печей, производства пара в дверях угольной печи, работы гидравлического оборудования и удаления сточных вод. Для производства тонны стали требуется около 4 тонн воздуха. Флюс используется в доменной печи для извлечения загрязнений из плавильной руды. Известняк и доломит объединяются с экстрагированными примесями с образованием шлака.
Как дутьевые, так и стальные печи, облицованы огнеупорами. Они используются для облицовочных печей, предназначенных для плавки железной руды. Диоксид кремния или песок используется для формования. Для производства стали различных марок применяют цветные металлы: алюминий, хром, кобальт, медь, свинец, марганец, молибден, никель, олово, вольфрам, цинк, ванадий и др. Среди всех этих ферросплавов марганец широко используется в выплавке стали.
Железные отходы, полученные из демонтированных конструкций заводов, механизмов, старых транспортных средств и т. д., перерабатываются и широко используются в этой отрасли.
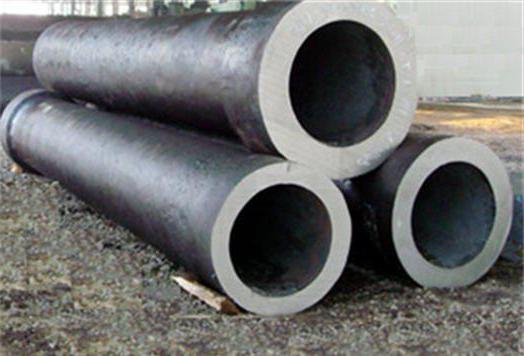
Чугун для стали
Выплавку стали с использованием чугуна производят гораздо чаще, чем с другими материалами. Чугун — это термин, который обычно относится к серому железу, однако он также идентифицирован с большой группой ферросплавов. Углерод составляет примерно от 2,1 до 4 мас.%, тогда как кремний составляет обычно от 1 до 3 мас.% в сплаве.
Выплавка чугуна и стали проходит при температуре плавления между 1150 и 1200 градусов, что примерно на 300 градусов ниже, чем температура плавления чистого железа. Чугун также демонстрирует хорошую текучесть, отличную обрабатываемость, устойчивость к деформации, окислению и отливке.
Сталь также является сплавом железа с переменным содержанием углерода. Содержание углерода в стали составляет от 0,2 до 2,1 мас.%, И это наиболее экономичный легирующий материал для железа. Выплавка стали из чугуна полезна для различных инженерных и конструкционных целей.
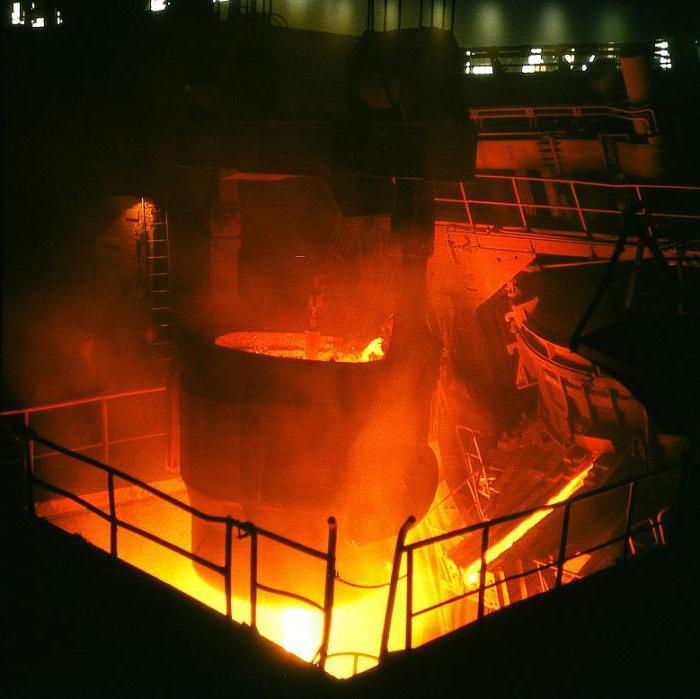
Железная руда для стали
Процесс выплавки стали начинается с переработки железной руды. Породу, содержащую железную руду, измельчают. Руду добывают с использованием магнитных роликов. Мелкозернистая железная руда перерабатывается в крупнозернистые комки для использования в доменной печи. Уголь очищается от примесей в коксовой печи, что дает почти чистую форму углерода. Затем смесь железной руды и угля нагревают для получения расплавленного железа или чугуна, из которого производится сталь.
В основной кислородной печи расплавленная железная руда является основным сырьем и смешивается с различными количествами стального лома и сплавов для производства различных марок стали. В электродуговой печи переработанный стальной лом расплавляется непосредственно в новую сталь. Около 12% стали изготовлено из переработанного материала.
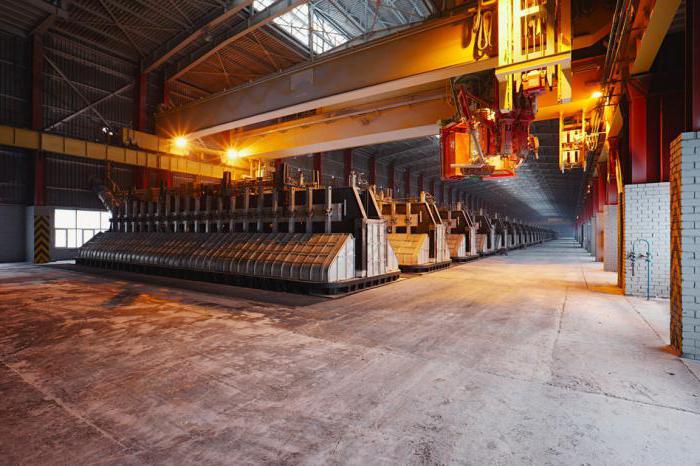
Технология выплавки
Плавление — процесс, посредством которого металл получают либо в виде элемента, либо как простое соединение из его руды путем нагревания выше температуры плавления обычно в присутствии окислителей, таких как воздух, или восстановителей, таких как кокс.
В технологии выплавки стали металл, который сочетается с кислородом, например оксидом железа, нагревается до высокой температуры, и оксид образуется в сочетании с углеродом в топливе, выходящим как монооксид углерода или диоксид углерода.
Другие примеси, все вместе называемые жилами, удаляются добавлением потока, с которым они объединяются, образуя шлак.
В современных плавках стали используется отражательная печь. Концентрированная руда и поток (обычно известняк) загружаются в верхнюю часть, а расплавленный штейн (соединение меди, железа, серы и шлака) вытягивается снизу. Вторая термообработка в конвертерной печи необходима для удаления железа из матовой поверхности.
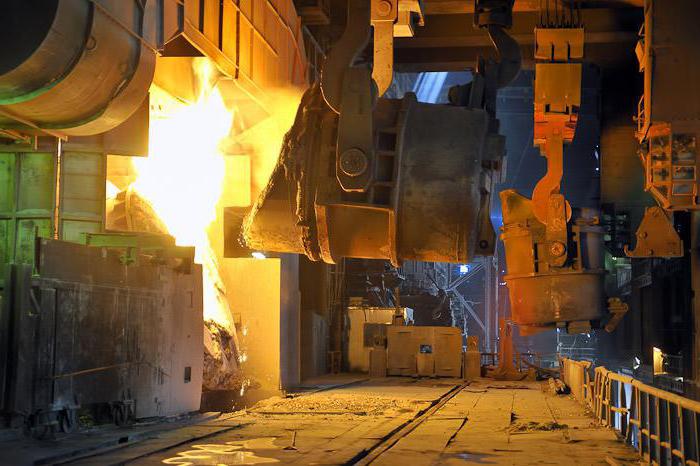
Кислородно-конвекторный способ
Кислородно-конвертерный процесс является ведущим процессом сталеплавильного производства в мире. Мировое производство конвертерной стали в 2003 году составило 964,8 млн тонн или 63,3 % от общего производства. Производство конвертера является источником загрязнения окружающей природной среды. Основными проблемами этого являются снижение выбросов, сбросов и уменьшение отходов. Суть их заключается в использовании вторичных энергетических и материальных ресурсов.
Экзотермическое тепло генерируется реакциями окисления во время продувки.
Основной процесс выплавки стали с использованием собственных запасов:
- Расплавленный чугун (иногда называемый горячим металлом) из доменной печи выливается в большой огнеупорный футерованный контейнер, называемый ковшом.
- Металл в ковше направляется непосредственно для основного производства стали или стадии предварительной обработки.
- Высокочистый кислород под давлением 700-1000 килопаскалей вводится со сверхзвуковой скоростью на поверхность ванны железа через охлаждаемую водой фурму, которая подвешена в сосуде и удерживается в нескольких футах над ванной.
Решение о предварительной обработке зависит от качества горячего металла и требуемого конечного качества стали. Самые первые конвертеры со съемным дном, которые могут быть отсоединены и отремонтированы, все еще используются. Были изменены копья, используемые для дутья. Для предотвращения заклинивания фурмы во время продувки применялись щелевые манжеты с длинным сужающимся медным наконечником. Кончики наконечника после сгорания сжигают CO, образующийся при выдувании в CO2, и обеспечивают дополнительное тепло. Для отвода шлака используются дротики, огнеупорные шарики и шлаковые детекторы.
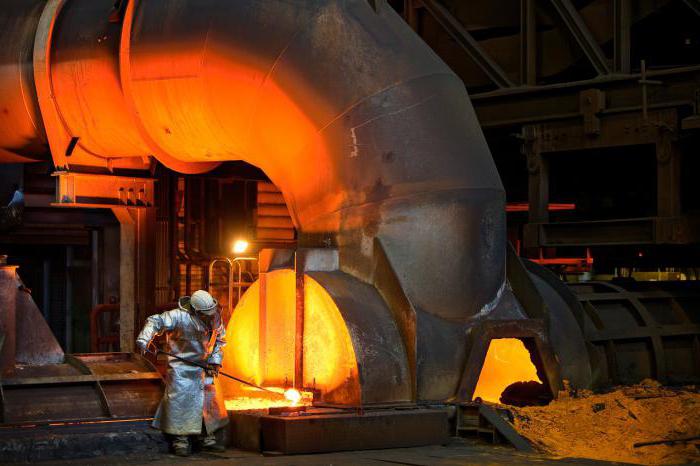
Кислородно-конвекторный способ: достоинства и недостатки
Не требует затрат на оборудование по очищению от газа, так как пылеобразование, т. е. испарение железа, снижено в 3 раза. За счет снижения выхода железа наблюдается рост выхода жидкой стали в 1,5 — 2,5 %. Преимуществом стало и то, что интенсивность продувки в таком способе увеличивается, что дает возможность повысить производительности конвертера на 18 %. Качество стали выше, потому что температура в зоне продувки снижена, что приводит к уменьшению образования азота.
Недостатки данного способа выплавки стали привели к снижению спроса на потребление, так как повышается уровень потребления кислорода на 7 % из-за большого расхода на сжигание топлива. Наблюдается повышенное содержание водорода в переработанном металле, из-за чего приходится некоторое время после окончания процесса вести продувку при помощи кислорода. Среди всех способов кислородно-конвертерный обладает самым повышенным шлакообразованием, причиной является невозможность следить за процессом окисления внутри оборудования.
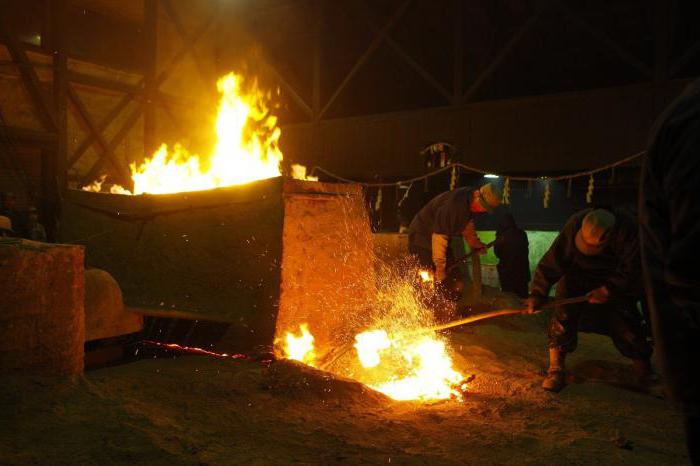
Мартеновский способ
Мартеновский способ на протяжении большей части 20-го века составлял основную часть обработки всей стали, изготовленной в мире. Уильям Сименс в 1860-х годах искал средства повышения температуры в металлургической печи, воскресив старое предложение об использовании отработанного тепла, выделяемого печью. Он нагревал кирпич до высокой температуры, затем использовал тот же путь для ввода воздуха в печь. Предварительно нагретый воздух значительно увеличивал температуру пламени.
Природный газ или распыленные тяжелые масла используются в качестве топлива; воздух и топливо нагреваются до сгорания. Печь загружается жидким доменным чугуном и стальным ломом вместе с железной рудой, известняком, доломитом и флюсами.
Сама печь изготовлена из высокоогнеупорных материалов, таких как магнезитовый кирпич для очагов. Вес мартеновских печей достигает 600 тонн, и их обычно устанавливают группами, так что массивное вспомогательное оборудование, необходимое для зарядки печей и обработки жидкой стали, может быть эффективно использовано.
Хотя мартеновский процесс практически полностью заменен в большинстве промышленно развитых стран основным кислородным процессом и электродуговой печью, им изготавливают около 1/6 всей стали, произведенной во всем мире.
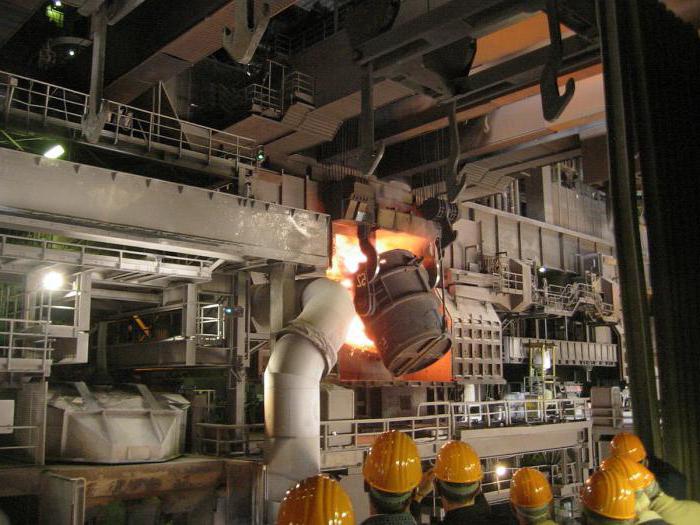
Достоинства и недостатки данного способа
К преимуществам относят простоту использования и легкость в получении легированной стали с примесью различных добавок, которые придают материалу различные специализированные свойства. Необходимые добавки и сплавы добавляют непосредственно перед окончанием выплавки.
К недостаткам можно отнести сниженную экономичность, по сравнению с кислородно-конверторным способом. Также качество стали более низкое, по сравнению с остальными методами выплавки металла.
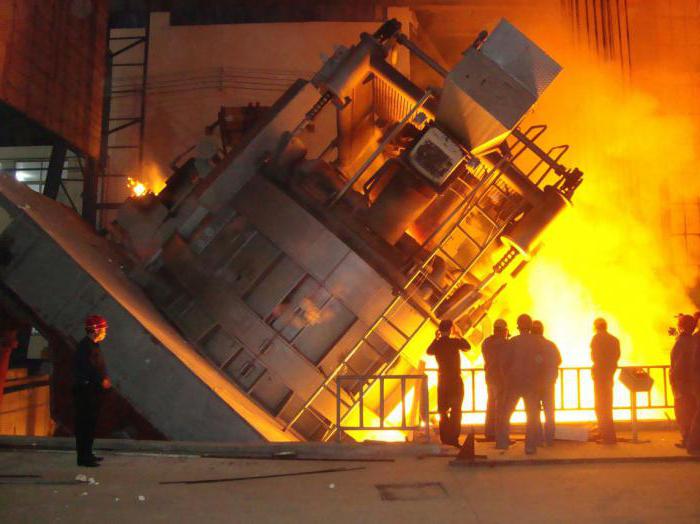
Электросталеплавильный способ
Современный способ выплавки стали с использованием собственных запасов представляет собой печь, которая нагревает заряженный материал с помощью электрической дуги. Промышленные дуговые печи имеют размеры от небольших единиц грузоподъемностью около одной тонны (используются в литейных цехах для производства чугунных изделий) до 400 тонн единиц, применяемых для вторичной металлургии.
Дуговые печи, используемые в исследовательских лабораториях, могут иметь емкость всего несколько десятков граммов. Промышленные температуры электрической дуговой печи могут составлять до 1800 °C (3,272 °F), в то время как лабораторные установки могут превышать 3000 °C (5432 °F).
Дуговые печи отличаются от индукционных тем, что зарядный материал непосредственно подвергается воздействию электрической дуги, а ток в выводах проходит через заряженный материал. Электрическая дуговая печь используется для производства стали, состоит из огнеупорной футеровки, обычно водоохлаждаемой, больших размеров, покрыта раздвижной крышей.
Печь в основном разделена на три секции:
- Оболочка, состоящая из боковых стенок и нижней стальной чаши.
- Очаг состоит из огнеупора, который вытягивает нижнюю чашу.
- Крыша с огнеупорной футеровкой или водяным охлаждением может быть выполнена в виде секции шара или в виде усеченного конуса (коническая секция).
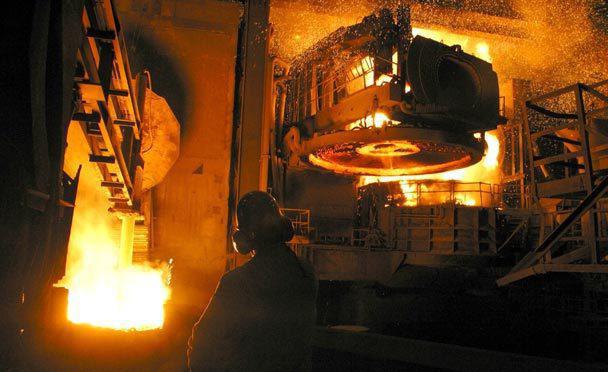
Достоинства и недостатки способа
Данный способ занимает лидирующие позиции в области производства стали. Метод выплавки стали применяется для создания высококачественного металла, который либо совсем лишен, либо содержит незначительное количество нежелательных примесей, таких как сера, фосфор и кислород.
Главным плюсом метода является использование электроэнергии для нагревания, благодаря чему можно легко контролировать температуру плавления и достичь невероятной скорости нагревания металла. Автоматизированная работа станет приятным дополнением к прекрасной возможности качественной переработки различного металлического лома.
К недостаткам можно отнести большое энергопотребление.
Основные способы производства стали
Категория:
Автомобильные эксплуатационные материалы
Публикация:
Основные способы производства стали
Читать далее:
Основные способы производства стали
Сталь представляет собой сплав железа с углеродом, причем углерода содержится от сотых долей до двух целых четырнадцати сотых процента. В состав стали могут входить также в определенном процентном соотношении и другие элементы.
По своим механическим свойствам и химическому составу сталь значительно отличается от чугуна. Она обладает высокой вязкостью, пластичностью, легко поддается механической и термической обработкам.
Производство стали осуществляется из передельного чугуна, стального лома, металлизированных окатышей, в специальных печах. Процесс получения стали основан на окислении в чугуне избытка углерода и других примесей с помощью твердых окислителей или газообразного кислорода.
Рекламные предложения на основе ваших интересов:
В настоящее время применяют главным образом конверторный, мартеновский и электросталеплавильный процессы выплавки стали.
Процесс получения стали в бессемеровском конверторе заключается и заполнении конвертора жидким чугуном и продувке его воздухом через днище. Основное преимущество итого способа и дальнейших его аналогов состоит в высокой производительности и отсутствии потребности в дополнительном топливе.
Современный кислородно-конверторный способ имеет примерно ту же технологию, что и бессемеровский способ. Отличием является конструкция конвертора с глухим дном (рис. 20) и применение для продувки технически чистого кислорода.
Кислород подают в конвертор через вертикальную трубчатую водоохлаждаемую фурму, не доходящую до металлической ванны. Из-за этого кислород не вдувается в толщу металла, как в старых конверторах, а подается на поверхность металла. При этом развивается высокая температура, что дает возможность перерабатывать чугун практически любого химического состава, а также добавлять в чугун скрап (железный лом).
Началом плавки считается загрузка в конвертор железного лома. После этого заливают жидкий чугун, опускают фурму, подают в нее технический кислород и загружают шлакообразующие материалы. Весь процесс выжигания примесей и избыточного углерода, включая слив шлака, занимает 50—60 мин, а продувка кислородом продолжается 18—26 мин.
Выплавка стали в кислородном конверторе отличается достаточно высокой точностью получения заданного содержания углерода при низком содержании вредных добавок фосфора и серы.
Недостатком кислородно-конверторного способа получения стали является большое пылеобразование, что требует применения дорогих пылеочистительных установок.
Мартеновский способ выплавки стали предложен в 1865 г. французским инженером П. Мартеном, который использовал для этой цели пламенную печь с регенерацией тепла отходящих газов для подогрева, топлива -и воздуха.
По этому принципу строятся и работают современные сталеплавильные мартеновские печи. Они отапливаются обычно смесью природного газа и мазута, имеют два-четыре регенератора.
Рабочее пространство печи ограничено снизу подом, сверху сводом, а с боков — стенками. Внутренняя полость печи имеет головки, сообщающиеся каналами с регенераторами.
В передней стенке мартеновской печи расположены рабочие окна 9, ЧеРез которые загружают материал для плавки и ведут за нею контроль. Под печи наклонен в сторону задней стенки, где расположена летка для выпуска стали.
Рис. 1. Кислородный конвертор на 130 т: 1 — станина; 2 — опорный подшипник; з — корпус конвертора; 4 — механизм наклона; г — выпускное отверстие для стали; в — водоохлаждаемая форма, 7 — днище конвертора
Рис. 2. Схемы мартеновской печи (а) и регенератора (б)
В печь загружают жидкий или в виде чушек чугун и стальной лом в разных соотношениях в зависимости от разновидности мартеновского процесса.
Серьезным недостатком мартеновского процесса получения стали является его продолжительность (7—10 ч) и значительный расход топлива. С целью совершенствования и ускорения мартеновского процесса применяют кислород для обогащения воздушного дутья или непосредственного введения его в ванну с металлом через свод печи. На некоторых заводах комбинируют способы применения кислорода и даже разрабатывают для этого двухванные печи.
Получение стали в электрических печах основано на плавлении шпхты при использовании электрической энергии. Отсутствие окислительного пламени и доступа воздуха в электрических печах позволяют лучше управлять процессом плавки и получать сталь точно заданного состава.
В нашей стране этот способ применяют для выплавки высококачественных углеродистых и легированных сталей, сплавов на основе никеля и кобальта.
По принципу преобразования электрической энергии в тепловую электрические печи делятся на дуговые и индукционные. Для наклона и слива металла и шлака печь оборудована роликами с электроприводом.
В дуговых электрических печах плавят отходы сталеплавильного прокатного производства, а также привозной стальной лом. В зависимости от состава сырья и материала, а также футеровки печей процесс плавки может носить основной или кислый характер.
Выплавка стали в индукционных печах применяется реже, чем в дуговых. Такая печь состоит из индуктора в виде катушки, окружающей огнеупорный тигель, куда загружают металл для плавки. При включении электрического тока в катушке образуется магнитное силовое поле, пронизывающее металл. За счет поля в металле индуктируются вихревые токи, которые нагревают и плавят его.
В индукционных печах получают легированные стали с малым содержанием углерода и различные сложные сплавы.
Рис. 3. Схемы дуговой (а) и индукционной (б) электрических печей
Металл, залитый в ковш, выдерживают в течение 10 мин для выравнивания его состава и выделения газов и неметаллических включений. После этого ковш подают на разливку.
Изложницы представляют собой чугунные или стальные сосуды определенной формы, позволяющие получать слитки квадратного, прямоугольного, многоугольного или круглого сечения в зависимости от назначения получаемых слитков. Изложницы заполняют жидким металлом из ковша сверху через центральный литник по каналам или снизу (сифонная разливка). Разливкой сверху получают крупные слитки массой до 35—45 т для прокатки.
Сифонная разливка применяется для получения слитков массой до 14—16 т высокого качества.
При непрерывной разливке сталь из разливочного ковша через промежуточный ковш равномерной струей заливается в кристаллизатор, представляющий короб, охлаждаемый проточной водой. Здесь быстро формируются стенки слитка, откуда он вытягивается валками с определенной скоростью, равной скорости кристаллизации. Ниже валков слиток полностью отвердевает и от него кислородной горелкой отрезаются заготовки-необходимой длины, которые автоматически направляются на транспортные тележки.
Непрерывная разливка стали обеспечивает высокое качество слитков, уменьшает потери металла и повышает производительность труда.
Качество стали повышается при разливке за счет применения ее вакуумирования. Этот метод заключается в удалении из стали растворенных газов путем вакуумной обработки стали в ковшах перед ее разливкой в изложницы и разливочную машину. В результате сталь становится более пластичной и прочной.
Разливка стали в вакууме применяется для получения высококачественных и легированных марок сталей. Этот способ требует применения дополнительного сложного оборудования.
—
Сталью называется сплав железа с углеродом и другими примесями (марганец, сера, фосфор, кремний и др.) при содержании углерода до 2%. Сталь по своим свойствам значительно отличается от чугуна. Она лучше поддается механической и термической обработке, хорошо куется, прокатывается и т. д. Детали машин, изготовленные из стали, более прочны по сравнению с чугунными деталями.
Сталь получают из чугуна или из смеси чугуна со стальным ломом при переработке их в мартеновских печах, в конвертерах и в электропечах. Сущность этих способов получения стали заключается в удалении углерода и других примесей до пределов, определяемых маркой стали. Удаление примесей происходит в результате окисления их при высоких температурах расплавленного металла с последующим переводом окислов в шлак. Удаляются примеси также в виде газообразных продуктов сгорания.
Мартеновское производство стали
Наиболее широкое применение находит производство стали в мартеновских печах. Крупнейшие в мире мартеновские печи построены в СССР. Емкость каждой из них составляет 900 т.
Сырьем служит твердый или жидкий чугун и стальной или чугунный лом. В качестве флюсов применяют: известняк, плавиковый шпат, бокситы. Топливом служит мазут, генераторный газ, смесь доменного и коксового газов, а также природный газ. Устройство мартеновской печи показано на рис. 2. Шихтусостоящую из расплавленного чугуна, холодного чугуна и флюсов, подают в рабочее пространство печи через завалочные окна. Газ и воздух поступают в рабочее пространство печи, пройдя через нагретые газовый и воздушный регенераторы (на рис. 2 — через левые).
В настоящее время широко применяют обогащение кислородом воздуха, поступающего в мартеновскую печь. Это ускоряет процесс горения, кроме того, обогащение воздуха кислородом облегчает процесс окисления примесей.
Регенераторы представляют собой камеры с насадками2 из огнеупорного кирпича. Насадки нагреваются за счет тепла отходящих из рабочего пространства газов. После того как насадки левых регенераторов достаточно охладятся газом и воздухом, а насадки правых регенераторов нагреются отходящими продуктами сгорания, клапаны 1 и шиберы 2, приводимые в движения электрическими лебедками, изменят направление газа, воздуха и продуктов сгорания на обратное, В результате газ и воздух будут нагреваться, проходя через правые, регенераторы, а левые регенераторы нагреваются отходящими продуктами сгорания.
Таким образом, применение регенераторов позволяет в результате предварительного подогрева газа и воздуха получить достаточно высокую температуру в рабочем пространстве печи и частично использовать тепло отходящих газов.
Рис. 4. Устройство мартеновской печи:
1 — клапаны; 2 — шиберы; 3 — левые регенераторы; 4 — правые регенераторы; 5 — рабочее пространство печи; 6 — дымовая труба
Подача жидкого чугуна из доменного цеха в мартеновский производится в ковшах на четырехосных чугуновозных тележках. В мартеновском цехе расплавленный чугун сливают при помощи мостового крана в миксер, который представляет собой футерованный огнеупорным кирпичом цилиндр емкостью 1,3 • 10 кг (1300 г) жидкого чугуна. Миксер обеспечивает работу мартеновских печей независимо от времени выпуска чугуна в доменном цехе и, кроме того, позволяет выравнивать состав и температуру жидкого чугуна.
В мартеновских цехах при помощи заливочных кранов заливают жидкий чугун в печь; при помощи завалочных кранов или напольных завалочных машин производят завалку в печь твердых составляющих шихты; разливочными кранами поднимают и переносят разливочные ковши и производят разливку стали в изложницы; остывшие слитки вынимают из изложниц при помощи кранов для раздевания слитков, снабженных специальным механизмом для выталкивания слитков из изложниц. Таким образом, в мартеновских цехах краны непосредственно участвуют в технологическом потоке.
Кроме перечисленных кранов, мартеновский цех, его шихтовый двор и уборочный пролет обслуживают магнитогрейферные краны и краны общего назначения. Всего в современном мартеновском цехе насчитывается 25-—30 мостовых кранов.
Производство стали в конвертерах
В современном отечественном производстве начинают применять 100-г и проектируют 250 и 500-г конвертеры.
Раньше производство стали в конвертерах заключалось в продувке воздуха через расплавленный чугун. Во время продувки сначала окисляется железо, при этом выделяется большое количество тепла, за счет которого поддерживают необходимую температуру в течение всего процесса. Образующееся за-кисное железо растворяется в металле и раскисляет содержащиеся в чугуне примеси.
Сталь, полученная по описанному способу, содержит большое количество шлаковых включений и газы (азот, кислород), что ухудшает механические качества стали и ограничивает область применения конвертерного метода .производства стали, так как по этому методу можно было получать сталь только из руд определенного состава.
В настоящее время при конвертерном производстве широко практикуют продувку через чугун, смеси воздуха с кислородом или чистого кислорода. При этом процесс идет значительно быстрей, появляется возможность использовать руды любого состава и .получать сталь то качеству такую же, как и при мартеновском способе производства. Отличительной чертой конвертерного производства является его высокая производительность: на 1 г емкости конвертера приходится более 60 т выплавленной стали в сутки.
В конвертерах, предназначенных для продувки жидкого чугуна воздухом, последний подается через керамические фурмы, расположенные в днище конвертера. Применение для продувки кислорода вместо воздуха позволяет отказаться от неудобных в эксплуатации керамических фурм, заменив их более долговечными водоохлаждаемыми подвесными фурмами.
Продувку жидкого чугуна кислородом производят сверху, для чего подвесную фурму на время продувки опускают в горловину конвертера. Для слива шлака и стали конвертер поворачивают при помощи механизма с электрическим приводом.
Для слива шлака и стали конвертер поворачивается в цапфах. Механизм поворота конвертера состоит из двух электрических двигателей, червячного редуктора и цилиндрического редуктора. Слив происходит через специальное отверстие в верхней части конвертера.
Скорость поворота конвертера регулируется в широких пределах. Максимальная скорость поворота равна приблизительно одному обороту в минуту.
Учитывая высокую производительность конвертеров на кислородном дутье и высокое качество стаЛи, выплавляемой при этом процессе, правительство Советского Союза взяло курс на значительное развитие конвертерного производства стали.
Производство стали в электрических печах
В современном отечественном сталеплавильном производстве самыми крупными являются 80-т электрические печи. В настоящее время в СССР проектируют электрические печи емкостью 120 т.
Электрические печи для выплавки стали разделяют на дуговые и индукционные.
В дуговых электропечах тепло для расплавления сообщается шихте электрической дугой, возбужденной между угольными электродами
Рис. 5. Конвертер на кислородном дутье (общий вид)
В индукционных печах металл плавится электрическим током, наведенным в шихте индукционным путем. Классическим примером индукционной печи является печь, где ванна для металла выполнена в виде кольца вокруг магнитопровода трансформатора. В этом случае ванна является коротко-замкнутой вторичной обмоткой трансформатора.
Производство стали в электропечах является самым совершенным. Но вследствие относительно высокой стоимости электрической энергии в дуговых электрических печах выплавляют только качественные, высококачественные и легированные стали и их сплавы. Индукционные же печи применяют в сравнительно редких, специальных случаях для выплавки сталей с улучшенной структурой.
Современный уровень развития техники предъявляет высокие требования к качеству стали.
С целью получения наиболее высококачественных сталей применяют вакуумирование стали. Вакуумированием жидкой стали удается в значительной степени уменьшить содержание в ней вредных газов (особенно водорода), ухудшающих ее качество.
Одной из новинок, позволяющей увеличить коэффициент использования жидкой стали, является непрерывная разливка. При этом способе жидкая сталь поступает в кристаллизатор с одного конца и, затвердевая, выходит слитком на другом конце кристаллизатора. Процесс происходит непрерывно. При непрерывной разливке стали значительно сокращаются потери металла, неизбежные при обычном способе разливки вследствие образования усадочных раковин.
Независимо от способа получения стали ее химический состав контролируют специальные лаборатории на протяжении всего технологического процесса, в результате чего стали присваивают марку, обозначающую ее химический состав и механические свойства.
Рекламные предложения:
Читать далее: Основные марки сталей и чугунов, применяемых при производстве и ремонте автомобилей
Категория: — Автомобильные эксплуатационные материалы
Главная → Справочник → Статьи → Форум
Для массового производства стали в современной металлургии основными исходными материалами являются передельный чугун и стальной скрап (лом). По химическому составу сталь отличается от передельного чугуна меньшим содержанием углерода, марганца, кремния и других элементов. Поэтому выплавка стали — передел чугуна (или же чугуна и скрапа(металлолома)) в сталь — сводится к проведению окислительной плавки для удаления избытка углерода, марганца и других примесей. При выплавке легированных сталей в их состав вводят соответствующие элементы.
Первыми способами получения стали из чугуна были кричный способ (XII—XIII вв.) и затем пудлинговый способ (конец XVIII в.). Продуктом плавки были крицы — небольшие куски — комья сварившихся между собой зерен металла. Получение плотного металла — сварочного железа — происходило при последующей ковке или прокатке. Во второй половине XIX в. появились и получили наибольшее развитие высокопроизводительные способы: бессемеровский (1856 г.) и томасовский процессы (1878 г.). Их недостатками являются, невысокое качество стали и ограниченность сырьевой базы, так как можно было использовать лишь некоторые чугуны (с определенным содержанием Si, S, Р). Поэтому примерно с начала нынешнего столетия основную массу стали выплавляли мартеновским способом (появился в 1864 г.) — менее производительным, но позволяющим выплавлять более качественную сталь. Кроме того, для выплавки мартеновской стали, используется наиболее распространенный чугун (непригодный для бессемеровского и томасовского передела) и огромное количество вторичного металла — стального скрапа.
В 50-х годах XX в. появился новый, прогрессивный способ выплавки стали — кислородно-конверторный процесс. Благодаря значительным технико-экономическим преимуществам этот способ быстро получил очень широкое применение, вытесняя мартеновский способ в массовом производстве стали.
В настоящее время в мировом производстве около 40 % стали выплавляют кислородно-конверторным способом и около 40 % мартеновским способом; при этом за последнее время доля кислородно-конверторной стали непрерывно возрастает, а доля мартеновской стали сокращается.
Выплавка качественных сталей в электрических дуговых и индукционных печах началась в конце XIX- начале XX вв. Электросталь стоит дороже, но превосходит по качеству кислородно-конверторную и мартеновскую сталь; ее производство – около 20 % от всей массы стали – непрерывно возрастает. В связи с возрастающими требованиями к стали все большее применение получает внепечное ваккумирование, рафинирование синтетическими шлаками в ковше и другие новые прогрессивные технологические способы.
Сталь особо высокого качества выплавляют в вакуумных электрических печах, а также путем электрошлакового, плазменного переплава и других новейших методов.
Сущность процесса получения сталиОсновными исходными материалами для производства стали являются передельный чугун и стальной лом (скрап). Сравнения химических составов передельного чугуна и стали показывает, что содержание углерода и примесей в стали существенно ниже, чем в чугуне (см. таблицу).
Состав передельного чугуна и низкоуглеродистой стали
Материал | Состав, % | ||||
Углерод | Кремний | Марганец | Фосфор | Сера | |
Передельный чугун Низкоуглеро- дистая сталь | 4,0 – 4,4 0,14 – 0,22 | 0,76 – 1,26 0,12 – 0,3 | До 1,75 0,4 – 0,65 | 0,15 – 0,3 0,05 | 0,03 – 0,07 0,055 |
Таким образом, для передела чугуна в сталь необходимо снизить содержание углерода и примесей. Поэтому сущностью любого металлургического передела чугуна в стальявляется снижение содержания углерода и примесей путем их избирательного окисленияи перевода в шлак и газы в процессе плавки. В результате окислительных реакций, осуществляемых на первом этапе передела чугуна в сталь, углерод соединяется с кислородом, образуя СО, который удаляется в атмосферу печи. Кремний, марганец, фосфор, сера образуют окислы или другие соединения, нерастворимые или малорастворимые в металле (SiO2, МnО, СаS и др.), которые в процессе плавки частично удаляются в шлак.
Однако в полной мере окислить примеси не удается, так как, несмотря на их значительно большее сродство к кислороду, чем у железа, по мере снижения содержания примесей в соответствии с законом действующих масс начинает окисляться железо. Окислы железа растворяются в железе, насыщая металл кислородом. Сталь, содержащая кислород, непригодна для обработки давлением — ковки, прокатки, так как в ней образуются трещины при деформации в нагретом состоянии.
Для уменьшения содержания кислорода в стали в процессе плавки ее раскисляют, т. е. вводят в нее элементы с большим сродством к кислороду, чем у железа. Взаимодействуя с кислородом стали, эти элементы образуют нерастворимые окислы, частично всплывающие в шлак. Для раскисления стали используют ферросплавы — ферросилиций, ферромарганец, а также алюминий. Раскисление является завершающим этапом выплавки стали.
Чугун переделывают в сталь в различных по принципу действия металлургических агрегатах. Основными их них являются кислородные конвертеры, мартеновские печи и электропечи. Соотношение между способами производства стали непрерывно изменяется. Объем производства стали, выплавляемой в высокопроизводительных агрегатах- кислородных конвертерах и крупных электропечах, возрастает, а стали, выплавляемой в мартеновских печах, постепенно уменьшается.
сталь | Состав, свойства, виды, марки и факты.
Металлы недрагоценные: железо
. Изучение производства и структурных форм железа от феррита и аустенита до легированной стали. Железная руда является одним из самых распространенных элементов на Земле, и одно из ее основных применений — производство стали. В сочетании с углеродом железо полностью меняет характер и становится легированной сталью. Encyclopædia Britannica, Inc. Просмотреть все видео этой статьиОсновным компонентом стали является железо, металл, который в чистом виде не намного тверже меди.Пропуская очень крайние случаи, железо в твердом состоянии, как и все другие металлы, является поликристаллическим, то есть состоит из множества кристаллов, которые соединяются друг с другом на своих границах. Кристалл — это упорядоченное расположение атомов, которое лучше всего представить как сферы, соприкасающиеся друг с другом. Они упорядочены в плоскостях, называемых решетками, которые проникают друг в друга особым образом. Для железа расположение решетки может быть лучше всего визуализировано единичным кубом с восемью атомами железа по углам. Для уникальности стали важна аллотропия железа, то есть его существование в двух кристаллических формах.В объемно-центрированном кубическом расположении в центре каждого куба есть дополнительный атом железа. В гранецентрированной кубической (ГЦК) схеме имеется один дополнительный атом железа в центре каждой из шести граней единичного куба. Важно, что стороны гранецентрированного куба или расстояния между соседними решетками в ГЦК-расположении примерно на 25 процентов больше, чем в ОЦК-расположении; это означает, что в ГЦК больше места, чем в структуре ОЦК, для хранения чужих ( i. легирующих) атомов в твердом растворе.
Железо имеет ОЦК-аллотропию ниже 912 ° C (1674 ° F) и от 1394 ° C (2,541 ° F) до температуры плавления 1538 ° C (2800 ° F). Называемый ферритом, железо в его ОЦК-образовании также называют альфа-железом в более низком температурном интервале и дельта-железом в высокотемпературной зоне. Между 912 и 1394 ° С железо находится в своем ГЦК-порядке, который называется аустенит или гамма-железо. Аллотропное поведение железа сохраняется за редким исключением в стали, даже когда сплав содержит значительное количество других элементов.
Существует также термин бета-железо, которое относится не к механическим свойствам, а скорее к сильным магнитным характеристикам железа. Ниже 770 ° C (1420 ° F) железо является ферромагнитным; температура, выше которой он теряет это свойство, часто называется точкой Кюри.
Получите эксклюзивный доступ к контенту из нашего первого издания 1768 года с вашей подпиской. Подпишитесь сегодняВ чистом виде железо мягкое и, как правило, не используется в качестве инженерного материала; основной метод его укрепления и превращения в сталь заключается в добавлении небольшого количества углерода.В твердой стали углерод обычно встречается в двух формах. Либо он находится в твердом растворе в аустените и феррите, либо в виде карбида. Карбидной формой может быть карбид железа (Fe 3 C, известный как цементит), или он может быть карбидом легирующего элемента, такого как титан. (С другой стороны, в сером железе углерод появляется в виде чешуек или скоплений графита из-за присутствия кремния, который подавляет образование карбидов.)
Влияние углерода лучше всего иллюстрируется диаграммой равновесия железо-углерод.Линия A-B-C представляет точки ликвидуса (, то есть — температуры, при которых расплавленное железо начинает затвердевать), а линия H-J-E-C представляет точки солидуса (в которых завершение затвердевания). Линия A-B-C показывает, что температуры затвердевания снижаются по мере увеличения содержания углерода в расплаве железа. (Это объясняет, почему серое железо, которое содержит более 2 процентов углерода, обрабатывается при гораздо более низких температурах, чем сталь.) Расплавленная сталь, содержащая, например, содержание углерода 0.77 процентов (показано вертикальной пунктирной линией на рисунке) начинает затвердевать при температуре около 1475 ° C (2660 ° F) и полностью твердо при температуре около 1400 ° C (2550 ° F). С этого момента все кристаллы железа находятся в аустенитном — , то есть ГЦК — расположении и содержат весь углерод в твердом растворе. При дальнейшем охлаждении происходит резкое изменение при температуре около 727 ° C (1341 ° F), когда кристаллы аустенита превращаются в тонкую пластинчатую структуру, состоящую из чередующихся пластин феррита и карбида железа.Эта микроструктура называется перлит, а изменение называется эвтектоидным превращением. Жесткость алмазной пирамиды (DPH) составляет приблизительно 200 кг на квадратный миллиметр (285 000 фунтов на квадратный дюйм) по сравнению с DPH, равной 70 кг на квадратный миллиметр для чистого железа. Охлаждение стали с более низким содержанием углерода (, например, , 0,25 процента) приводит к микроструктуре, содержащей около 50 процентов перлита и 50 процентов феррита; это мягче, чем перлит, с DPH около 130.Сталь с содержанием углерода более 0,77%, например 1,05%, содержит в своей микроструктуре перлит и цементит; он тверже перлита и может иметь DPH 250.
Диаграмма равновесия железоуглерод. Encyclopædia Britannica, Inc. .о производстве стали из чугуна и стального лома в печах металлургических заводов. Производство стали является важным этапом в общем производственном цикле черной металлургии, другими являются производство чугуна в доменных печах и прокатка стальных слитков и полуфабрикатов. Два основных технологических процесса производства стали — плавка и разливка.
В современной металлургии основными методами выплавки стали являются основной кислородный процесс, мартеновский процесс и электропечь.Относительная важность этих процессов меняется; в начале 1950-х годов на мартеновский процесс приходилось примерно 80 процентов мирового производства, но к середине 1970-х годов основной процесс с кислородом стал преобладающим, составив более половины мирового производства.
Сталь, полученная в печи, передается в ковш, из которого она затем разливается либо в металлические формы, либо в формы, либо в машины, используемые при непрерывной разливке. Только около 2 процентов всей производимой стали используется для изготовления фасонных отливок.Отверждение металла приводит к получению слитков и полуфабрикатов, которые затем обрабатываются механическим способом, например, путем прокатки или ковки. Хотя непрерывное литье дает очевидные преимущества по сравнению с разливкой стали в формы, большая часть металла все еще производится по последней технологии. Разливка является критическим этапом в производстве стали, и используемый процесс в значительной степени определяет качество готового металла и количество отходов при последующем восстановлении стальных слитков.
Печи, используемые в основном кислородном процессе, обычно имеют вместимость 100-350 тонн.Ассортимент марок стали, полученных этим способом, постоянно увеличивается, а качество легированной стали, получаемой с помощью основного кислородного процесса, находится на одном уровне с качеством, полученным с помощью мартеновского процесса, и электротехнической стали той же марки. Из соображений экономии и качества рекомендуется использовать базовые кислородные печи для производства определенных низколегированных сталей. Таким образом, сталь, которая должна быть подвергнута холодной обработке, особенно автомобильная листовая сталь, производится на металлургических заводах по всему миру в основном в кислородных печах.Высоколегированные стали теперь также производятся в кислородных печах. В настоящее время опытно-конструкторские работы по этому процессу сосредоточены на интенсификации процесса плавления, в частности, на раздуве, увеличении сопротивления футеровки печи, использовании компьютеров для управления процессом и разработке новых вариантов процесса. Сочетание основного кислородного процесса с методами очистки, которые проводятся вне печи, обещает будущее.
Несмотря на резкое снижение роли мартеновского процесса в мировом производстве, этот процесс все еще занимает видное место в черной металлургии многих стран.Использование кислорода, природного газа и высококачественных огнеупоров позволяет значительно повысить производительность процесса. Тем не менее, новые мартеновские печи больше не производятся, и то, что сейчас кажется многообещающим, — это преобразование существующих печей в печи с двумя ваннами.
Во второй половине 20-го века произошло заметное развитие производства стали с использованием электрических печей, развитие которого поощряется многочисленными преимуществами процесса электропечи по сравнению с другими методами производства стали.В СССР в настоящее время работают 200-тонные дуговые печи, а печи мощностью 400 тонн находятся в стадии проектирования. Самая большая в мире электропечь мощностью 360 тонн в настоящее время (1975 г.) работает в Соединенных Штатах. Ведутся работы по строительству печей грузоподъемностью 500–600 тонн с использованием шести электродов. Важной тенденцией в процессе производства электропечи является значительное увеличение мощности на тонну печей, с 250–300 до 500–600 киловольт-ампер на тонну и более.В некоторых странах был введен предварительный нагрев шихты, что позволяет сократить время, необходимое для плавления, а также потребление электроэнергии и электродов. Рабочие характеристики дуговых печей таковы, что печи могут эффективно использоваться при производстве не только легированной стали, но и обычной стали. Таким образом, обычная сталь составляет 70 процентов производства сталеплавильных сталелитейных заводов в Соединенных Штатах и 50 процентов производства аналогичных прокатных станов в Федеративной Республике Германии.Толчком к развитию электрометаллургии стали станет широкое использование прямого восстановления железной руды, что позволяет производить высококачественное сырье для электрических печей. Использование металлизированных загрузок, например, металлизированных окатышей, при электроплавлении снижает капитальные вложения, необходимые для строительства сталеплавильного завода с электропечью, и повышает производительность дуговых печей.
Перспективным развитием сталелитейного производства является улучшение качества стали за счет процессов рафинирования, проводимых вне печи.Процессы, имеющие наибольшее промышленное значение, включают барботирование инертных газов или окислительных смесей через металл в ковше или в специальном аппарате, вакуумную обработку и обработку стали синтетическими шлаками.
В середине 1960-х годов началось интенсивное развитие электрометаллургических процессов, которые в целях рафинирования включают переплавку полуфабрикатов, полученных из обычных сталеплавильных агрегатов, обычно дуговых или индукционных печей. Среди процессов — плавление в дуговых вакуумных печах, вакуумно-индукционная плавка, электрошлаковая плавка, электронно-лучевая плавка и плавка в плазменных печах.В результате рафинирующего переплава неметаллические включения и другие нежелательные материалы эффективно удаляются из металла, однородность структуры и плотность увеличиваются, а многие свойства стали улучшаются.
Что касается разливки, то наблюдается непрерывное увеличение процента металла, производимого в результате непрерывной разливки, и к середине 1970-х годов в эксплуатации было более 500 машин непрерывной разливки. Самая большая такая машина, способная получиться 1.9 миллионов тонн стали в год эксплуатируется в США (1975). Тип машины непрерывного литья заготовок изогнутой формы является наиболее распространенным. Выход готового продукта на лучших машинах непрерывного литья достигает 96–99 процентов. Как при непрерывной разливке, так и при обычной разливке хорошие технические и экономические результаты были получены путем замены заглушек на золотниковые клапаны, которые надежны и безопасны и позволяют точно регулировать скорость разливки. Использование экзотермических шлакообразующих смесей приводит к улучшению поверхности слитка, и потери металла могут быть значительно уменьшены при использовании теплоизоляционных и экзотермических горячих поверхностей.
Тенденция в производстве стали, как и в черной металлургии в целом, заключается в концентрации производства и более широком использовании непрерывных производственных процессов. Существует также тенденция к специализации отдельных предприятий. Эти разработки позволяют снизить удельные затраты, улучшить качество стали, повысить степень механизации и автоматизации всего металлургического процесса, а также облегчить внедрение компьютеров и систем автоматического управления. В ряде стран ведется работа по разработке непрерывного процесса производства стали, и производственные единицы для этого процесса имеют большие перспективы для производства стали.
Мировое производство стали в 1974 году превысило 700 миллионов тонн, из которых 136 миллионов тонн было произведено в СССР. Производство стали на душу населения в промышленно развитых странах составляет 400–600 кг; в СССР этот показатель превышает 500 кг. По некоторым прогнозам, к 2000 году мировое производство этого важнейшего металла современной эпохи достигнет 2 миллиардов тонн.
ЛИТЕРАТУРА
Сталеплавильное производство: Справочник , тт. 1-2.Под редакцией А. М. Самарина. М., 1964.Явойский, В. И. Теория процессов производства, киоск , 2-е изд. М., 1967.
Лемпицкий В. В., Голиков И. Н., Склокин Н. Ф.. Прогрессивные способы повышения качества ларька . Москва, 1968.
Перспективы развития технологии черной металлургии . Москва, 1973.
Электрометаллургический киоск иферросплавов . М., 1974.
Калинников, Е. С. Черналская металлургия: реальность и тенденции .М., 1975.
Баптизманский, В. И. Теория клородно-конверторного процесса . Москва, 1975..
Топ сталелитейных компаний 2019 | worldsteel
Это рейтинг 50 ведущих компаний-производителей стали.
Расширенный список ведущих производителей стали на 2017-2019 гг. Можно найти в PDF под этой таблицей.
Этот список обновляется каждый год в мае / июне.
Тоннаж выражается в миллионах тонн (Мт).
РАНГ | КОМПАНИЯ | ТОННАЖ 2019 |
1 | ArcelorMittal (1) | 97.31 |
2 | Китай Baowu Group (2) | 95,47 |
3 | Nippon Steel Corporation (3) | 51,68 |
4 | HBIS Group (4) | 46,56 |
5 | POSCO | 43.12 |
6 | Shagang Group | 41,10 |
7 | Ansteel Group | 39.20 |
8 | Jianlong Group | 31,18 |
9 | Tata Steel Group (5) | 30,1517 |
10 | Shougang Group | 29,34 |
11 | Shandong Steel Group | 27,58 |
12 | JFE Steel Corporation | 27,35 |
13 | Валин Групп | 24.31 |
14 | Nucor Corporation | 23.09 |
15 | HYUNDAI Steel Company | 21,56 |
16 | IMIDRO (6) | 16,79 |
17 | JSW Steel Limited | 16,26 |
18 | Steel Authority of India Ltd. (SAIL) | 16,18 |
19 | Benxi Steel | 16.18 |
20 | Fangda Steel | 15,66 |
21 | Новолипецкий Сталь (НЛМК) | 15,61 |
22 | Baotou Iron & Steel (Group) Co., Ltd. | 15,46 |
23 | Китайская Стальная Корпорация | 15,23 |
24 | Techint Group (7) | 14,44 |
25 | Лючжоу Сталь | 14.40 |
26 | Rizhao Steel | 14.20 |
27 | Стальная корпорация США | 13,89 |
28 | ЕВРАЗ | 13,81 |
29 | CITIC Pacific | 13,55 |
30 | Gerdau S.A. | 13.13 |
31 | Jingye Steel | 12.58 |
32 | Магнитогорский металлургический комбинат (ММК) | 12,46 |
33 | Шэньси Сталь | 12,45 |
34 | Саньмин Сталь | 12.40 |
35 | thyssenkrupp | 12,25 |
36 | Зенит Сталь | 11,93 |
37 | Северсталь | 11.85 |
38 | Циншань Нержавеющая сталь | 11,40 (е) |
39 | Нанкин Сталь | 10,97 |
40 | Тайюань Сталь | 10,86 |
41 | Аньян Сталь | 10,54 |
42 | Метинвест Холдинг, ООО | 9,58 |
43 | Xinyu Steel | 9.47 |
44 | Donghai Special Steel | 8,90 |
45 | Jinxi Steel (также известная как Китайская Восточная) | 8,73 |
46 | ERDEMIR Group | 8,61 |
47 | Steel Dynamics, Inc. | 8,59 |
48 | Куньмин Сталь | 7,73 |
49 | SSAB | 7.62 |
50 | Jiuquan Steel | 7,48 |
(е) оценка
Примечания:
- Включает акции AM / NS Индия и Китай Oriental
- Включает тоннаж Maanshan Steel и Chongqing Steel
- Включает тоннаж корпорации Nippon Steel из нержавеющей стали, Sanyo Special Steel, Ovako AB, а также доли в AM / NS India и USIMINAS
- Включает тоннаж сербского железа и стали d.o.o. Белград и МАКСТИЛЬ А.Д. в Македонии
- Совмещенный тоннаж Mobarrakeh Steel, Esfahan Steel, Khuzestan Steel и NISCO.
Примечания о владении компанией и расчетах тоннажа:
Для членов Worldsteel данные были получены из их официальных деклараций тоннажа. Для китайских компаний использовалась официальная публикация тоннажа CISA, если не указано иное. Цифры представляют собой консолидированный тоннаж, заканчивающийся 31 декабря 2019 года, включая доли в дочерних и совместных предприятиях.
сталь | Состав, свойства, виды, марки и факты.
Металлы недрагоценные: железо
. Изучение производства и структурных форм железа от феррита и аустенита до легированной стали. Железная руда является одним из самых распространенных элементов на Земле, и одно из ее основных применений — производство стали. В сочетании с углеродом железо полностью меняет характер и становится легированной сталью. Encyclopædia Britannica, Inc. Просмотреть все видео этой статьиОсновным компонентом стали является железо, металл, который в чистом виде не намного тверже меди.Пропуская очень крайние случаи, железо в твердом состоянии, как и все другие металлы, является поликристаллическим, то есть состоит из множества кристаллов, которые соединяются друг с другом на своих границах. Кристалл — это упорядоченное расположение атомов, которое лучше всего представить как сферы, соприкасающиеся друг с другом. Они упорядочены в плоскостях, называемых решетками, которые проникают друг в друга особым образом. Для железа расположение решетки может быть лучше всего визуализировано единичным кубом с восемью атомами железа по углам. Для уникальности стали важна аллотропия железа, то есть его существование в двух кристаллических формах.В объемно-центрированном кубическом расположении в центре каждого куба есть дополнительный атом железа. В гранецентрированной кубической (ГЦК) схеме имеется один дополнительный атом железа в центре каждой из шести граней единичного куба. Важно, что стороны гранецентрированного куба или расстояния между соседними решетками в ГЦК-расположении примерно на 25 процентов больше, чем в ОЦК-расположении; это означает, что в ГЦК больше места, чем в структуре ОЦК, для хранения чужих ( i. легирующих) атомов в твердом растворе.
Железо имеет ОЦК-аллотропию ниже 912 ° C (1674 ° F) и от 1394 ° C (2,541 ° F) до температуры плавления 1538 ° C (2800 ° F). Называемый ферритом, железо в его ОЦК-образовании также называют альфа-железом в более низком температурном интервале и дельта-железом в высокотемпературной зоне. Между 912 и 1394 ° С железо находится в своем ГЦК-порядке, который называется аустенит или гамма-железо. Аллотропное поведение железа сохраняется за редким исключением в стали, даже когда сплав содержит значительное количество других элементов.
Существует также термин бета-железо, которое относится не к механическим свойствам, а скорее к сильным магнитным характеристикам железа. Ниже 770 ° C (1420 ° F) железо является ферромагнитным; температура, выше которой он теряет это свойство, часто называется точкой Кюри.
Получите эксклюзивный доступ к контенту из нашего первого издания 1768 года с вашей подпиской. Подпишитесь сегодняВ чистом виде железо мягкое и, как правило, не используется в качестве инженерного материала; основной метод его укрепления и превращения в сталь заключается в добавлении небольшого количества углерода.В твердой стали углерод обычно встречается в двух формах. Либо он находится в твердом растворе в аустените и феррите, либо в виде карбида. Карбидной формой может быть карбид железа (Fe 3 C, известный как цементит), или он может быть карбидом легирующего элемента, такого как титан. (С другой стороны, в сером железе углерод появляется в виде чешуек или скоплений графита из-за присутствия кремния, который подавляет образование карбидов.)
Влияние углерода лучше всего иллюстрируется диаграммой равновесия железо-углерод.Линия A-B-C представляет точки ликвидуса (, то есть — температуры, при которых расплавленное железо начинает затвердевать), а линия H-J-E-C представляет точки солидуса (в которых завершение затвердевания). Линия A-B-C показывает, что температуры затвердевания снижаются по мере увеличения содержания углерода в расплаве железа. (Это объясняет, почему серое железо, которое содержит более 2 процентов углерода, обрабатывается при гораздо более низких температурах, чем сталь.) Расплавленная сталь, содержащая, например, содержание углерода 0.77 процентов (показано вертикальной пунктирной линией на рисунке) начинает затвердевать при температуре около 1475 ° C (2660 ° F) и полностью твердо при температуре около 1400 ° C (2550 ° F). С этого момента все кристаллы железа находятся в аустенитном — , то есть ГЦК — расположении и содержат весь углерод в твердом растворе. При дальнейшем охлаждении происходит резкое изменение при температуре около 727 ° C (1341 ° F), когда кристаллы аустенита превращаются в тонкую пластинчатую структуру, состоящую из чередующихся пластин феррита и карбида железа.Эта микроструктура называется перлит, а изменение называется эвтектоидным превращением. Жесткость алмазной пирамиды (DPH) составляет приблизительно 200 кг на квадратный миллиметр (285 000 фунтов на квадратный дюйм) по сравнению с DPH, равной 70 кг на квадратный миллиметр для чистого железа. Охлаждение стали с более низким содержанием углерода (, например, , 0,25 процента) приводит к микроструктуре, содержащей около 50 процентов перлита и 50 процентов феррита; это мягче, чем перлит, с DPH около 130.Сталь с содержанием углерода более 0,77%, например 1,05%, содержит в своей микроструктуре перлит и цементит; он тверже перлита и может иметь DPH 250.
Диаграмма равновесия железоуглерод. Encyclopædia Britannica, Inc. .