Сталь вики: Сталь — Википедия – Нержавеющая сталь — Википедия
Электротехническая сталь — Википедия
Материал из Википедии — свободной энциклопедии
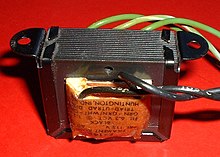
Электротехни́ческая сталь, также имеет названия динамная сталь, трансформаторная сталь, кремнистая электротехническая сталь — сплав железа обычно с кремнием, иногда легированный алюминием, готовый продукт выпускается в виде тонких листов толщиной от 0,05 до 2 мм.
Магнитомягкий ферромагнитный материал. Имеет улучшенные ферромагнитные свойства для применения в знакопеременных магнитных полях.
Используется при изготовлении магнитопроводов различного электротехнического оборудования — электромагнитов, трансформаторов, генераторов, электродвигателей, дросселей, магнитопроводов реле, феррорезонансных стабилизаторов напряжения и др.
В зависимости от требуемых свойств, электротехническая сталь содержит различное количество кремния. В зависимости от технологии производства электротехнические стали разделяют на холоднокатаные (изотропные или анизотропные; количество кремния до 3,3 %) и горячекатаные (изотропные; количество кремния до 4,5 %). Нередко в качестве легирующей добавки в электротехнической стали может содержаться алюминий (до 0,5 %). Иногда электротехнические стали условно разделяют на динамную (изотропную), трансформаторную (анизотропную), релейную (изотропную, нелегированную).
Электромагнитные свойства[править | править код]
Как правило, электротехнические стали стараются выполнить:
Относительная магнитная проницаемость μ/μ0 электротехнической стали сильно зависит от величины приложенного поля. К примеру, сталь электротехническая сернистая Э43 в слабых полях имеет μ/μ
Электротехническая сталь выпускается в виде листов (часто в рулонах) и узкой ленты толщиной 0,05—1 мм. Качество электротехнической стали характеризуется электромагнитными свойствами (удельными потерями, коэрцитивной силой и индукцией), изотропностью свойств (разницей в значениях свойств металла вдоль и поперёк направления прокатки), геометрическими размерами и качеством листов и полос, механическими свойствами, а также параметрами покрытия. Снижение удельных потерь в стали обеспечивает уменьшение потерь энергии, а повышение максимальной индукции стали позволяет уменьшить габариты, снижение анизотропии свойств улучшает характеристики устройств с вращающимися магнитопроводом. Электротехническая сталь обычно поставляется в отожжённом состоянии. Для снятия механических напряжений, возникающих при изготовлении деталей, проводят дополнительный кратковременный отжиг при 800—850°С. Некоторые электротехнические стали поставляются в неотожжённом виде; в этом случае для обеспечения заданного уровня свойств после механической обработки необходимо проводить термическую обработку деталей.
Для изотропной тонколистовой электротехнической стали в различных странах приняты следующие стандарты: ГОСТ 21427.2-83, ASTM A677/A677M-89, EN 10106-96.
- Лит.: Дубров Н. Ф., Лапкин Н. И., Электротехнические стали, М., 1963; Дружинин В. В., свойства электротехнической стали, 2 изд., М., 1974.
- Электротехническая сталь — статья из Большой советской энциклопедии.
- ГОСТ 3836-83 Сталь электротехническая нелегированная тонколистовая и ленты. Технические условия.
- ГОСТ 21427.1-83 Сталь электротехническая холоднокатаная анизотропная тонколистовая. Технические условия.
- ГОСТ 21427.2-83 Сталь электротехническая холоднокатаная изотропная тонколистовая. Технические условия
- Дружинин В. В. Магнитные свойства электротехнической стали/В. В. Дружинин. — М.: Энергия, 1974—240 с.
- Казаджан Л. Б. Магнитные свойства электротехнических сталей и сплавов / Под. ред. В. Д. Дурнева. — М.: ООО «Наука и технологии», 2000—224 с.
Дамасская сталь — Википедия
Клинок (нож), имитация дамасской сталиДама́сская сталь (или просто дама́ск) — вид стали с видимыми неоднородностями на стальной поверхности, чаще всего в виде узоров, получаемых различными способами. Различается два рода стали, которые именуются общим термином «дамаск»: сварочный дамаск (при многократной перековке стального пакета, состоящего из сталей с различным содержанием углерода) и

Тигельные булаты (он же вуц, англ. wootz), где узоры появляются за счёт образования крупных карбидов, как результат высокого содержания углерода и методов медленного охлаждения, к дамасским сталям не относятся.
Рафинированная сталь или харалуг, только номинально относится к дамаскам, так как целью кузнечной сварки крицы является очистка от остатков шлака и получение относительно однородной стали с приемлемым содержанием углерода. Цель процесса была не вывести какой-либо узор, а добиться очистки и равномерного распределения углерода в заготовке
Комбинируя стальные заготовки с разным содержанием углерода с последующей сваркой, складыванием и проковкой, кузнецы добивались контроля над свойствами получаемого материала. Железо, как правило, мягко и легко поддаётся деформации, высокоуглеродистая сталь же тверда и (при надлежащей термообработке) упруга. Комбинируя железо и высокоуглеродистую сталь, получали материал, который восполнял недостатки обеих исходных сталей. Так возникало чередование слоёв металла с очень высоким и очень низким содержанием углерода. Первые при закалке приобретали большую твёрдость, а вторые, напротив, не закаливались вовсе и служили амортизирующей подложкой. Мягкие железные слои не давали металлу быть слишком хрупким, а высокоуглеродистые слои придавали нужную упругость и остроту. Диффузия углерода также усредняла в какой-то мере его распределение в заготовке.
Основным и немаловажным недостатком дамасской стали является ее низкая коррозионная стойкость, обусловленная большим содержанием углерода в компонентах поковки и практически полным отсутствием легирующих элементов.
По более прогрессивной технике, принятой в арабских странах, раннесредневековой Европе или в Китае, проковывался пучок заранее заготовленной проволоки или ленты с определённым содержанием углерода. Так тратилось меньше времени и железа. Уже в III веке до н. э. согласно археологическим находкам европейские кельты изготавливали сварные дамаски. В первые века нашей эры вошёл в моду так называемый кручёный харалуг; бруски из разнородных сталей сваривались, перекручивались спиралью, снова проковывались и соединялись вместе с такими же заготовками в один брус. Большое количество германских, позднеримских и франкских мечей старше X века, дошедшие до наших дней, имеют сложную харалужную дамаскировку.
Узоры на поверхности этого вида дамаска — оптический эффект неравномерного распределения углерода в связи с неоднородностью материала. Этот эффект часто усиливался специальными методами полировки и травлением поверхности кислотами. Сам же узор изначально является не главной целью изготовления сварных харалугов, а всего лишь побочным явлением.
Когда упоминают «легендарную дамаскую сталь», то обычно имеют в виду любую старинную сталь с узором, смешивая как сварные композиты-дамаски с собственно булатами — булатами, сваренными в тигле и имеющими значительно более высокое содержание углерода по сравнению с дамасками. На западе до сих пор распространенно мнение, что дамаски и булаты по сути одно и то же, в отличие от восточных и русскоговорящих стран, где допускают чёткое деление, на дамаски — сварные композиты, и булаты — композиты, полученные без использования многократной сварки.
Последнее время на западе имеется тенденция называть тигельную сталь вуутцами, что так же не является правильным, поскольку слово вуутц применимо к любой тигельной стали. Последние исследования одного из булатных клинков из исторического музея города Берн в Швейцарии, проведённые группой учёных из Дрезденского технического университета в 2006 году под руководством профессора Петера Пауфлера, обнаружили в булатной стали УНТ. После закалки и отпуска в булате образуется композит из цементитов в трооститно-сорбитной матрице, армированной однослойными УНТ, наполненными цементитом.
Настоящие булаты имеют повышенные механические свойства по сравнению с дамасками или обычными углеродистыми сталями с аналогичным количеством углерода. Булатная сталь закаливалась, но после закалки тело клинка обязательно подвергалось высокому отпуску, а лезвие низкому. В результате оружие приобретало выдающиеся прочностные характеристики. Правильно изготовленный булатный клинок спокойно надрубает (оставляет засечки) на закалённом, более твёрдом небулатном клинке, но при этом сам не страдает.
Выдающийся горный инженер Павел Петрович Аносов воссоздал секрет булата и доказал необычайно высокие свойства этой стали. Высокая температура — до 500 градусов цельсия — для булата была не страшна, он не терял своих свойств в отличие от любой другой нелегированной клинковой стали. Высокий перегрев, значительно выше 600-650 градусов, приводил к полному отжигу, и сталь теряла прочностные свойства, а перегрев выше 900 градусов приводил к растворению цементитов и потере узора, а иногда и к полному уничтожению булатной структуры, в зависимости от содержания углерода в металле.
Булат ни в коем случае не надо путать с дамасской сталью, полученной при помощи сварки. Уже во времена П.П. Аносова дамасская сталь считалась сварочным или ложным булатом, поскольку кроме узора не предъявляла никаких выдающихся свойств. П. П. Аносов так же ввёл новый термин, а именно термин «Литой булат». Таким образом булаты разделились на два класса. На булаты тигельные, полученные длительной варкой булата в тигле, охлаждении вместе с тиглем и последующей расковкой полученного сплавка в полосу. И булаты литые, полученные из литой стали путём длительного отжига в определённых условиях. То есть тигельная сталь с содержанием углерода около одного процента разливалась в изложницы, расковывалась и затем подвергалась длительному отжигу. Такой литой булат показывал узоры и значительно более высокое качество стали даже по сравнению с передовой на то время тигельной сталью английского производства. «Литой булат» П.П. Аносов называл мягким из-за низкого содержания углерода, а тигельные булаты — твёрдыми, поскольку содержание углерода в его тигельных булатах доходило до 5%, по утверждениям самого Павла Петровича Аносова. Необходимую информацию можно найти в опубликованных работах Павла Петровича Аносова «О булатах» и в работе профессора Петера Пауфлера “Carbon nanotubes in an ancient Damascus sabre.”
Рафинированная сталь употреблялась почти сразу после овладения людьми процесса изготовления кричного железа, так как продукт сыродутной печи в чистом виде был непригоден для выделки. Около 1300 лет до н. э. соответствующая технология появилась в Передней Азии, около 800 до н. э. проникла в Европу, а в Китае археологами доказана самостоятельная редукция руды с помощью сыродутной печи примерно в VII—VI веках до н. э. Сваривание разных сортов стали и целенаправленное изготовление сварных дамасков было разработано в большинстве случаев независимо друг от друга. Уже в первых веках до н. э. подобные материалы были известны и в Европе, и в Китае. Есть сведения[2], что в III веке н. э. римляне уже знали оружие из дамасской стали. Находка из Нидама[2] содержит много мечей с очень сложной сваркой наравне с клинками, гораздо более простыми в конструкции.[3]
Впервые индийская тигельная сталь упоминается около 300 года до н. э.[4] В Иран дамаск попал ещё в VI веке. На территории Киевской Руси узорчатый булат был известен, хотя и редок, ещё в домонгольский период и назывался булатом или «красным железом». Более существенных масштабов применение дамасского оружия на Руси достигло только в XV веке, но вплоть до начала XVIII века немногочисленные дамасские и булатные клинки ввозились из Персии. Сведений о местном производстве дамасских и булатных сталей нет, однако есть об их импорте. В домонгольской Руси был известен сварной харалуг,[5] технология изготовления которого была утрачена и восстановлена только в конце XX века. Первым упоминанием об этой технологии можно считать сведения Аль-Бируни:[6]
Русы выделывали свои мечи из , а долы посредине их из , чтобы придать им прочность при ударе, предотвратить их хрупкость. не выносит холода их зим и ломается при ударе. Когда они познакомились с , то изобрели для долов плетенье из длинных проволок (изготовленных) из обеих разновидностей железа — и . И стали получаться у них на сварных плетениях при погружении (в травитель) вещи удивительные и редкостные, такие, какие они желали и намеревались получить. же не получается соответственно намерению при изготовлении и не приходит по желанию, но он случаен.
А «харалуг» упоминается в «Слове о полку Игореве».
Яръ туре Всеволодѣ! стоиши на борони, прыщеши на вои стрѣлами, гремлеши о шеломы мечи харалужными.
В то же время однозначного толкования термина «харалуг» нет.
В настоящее время в СМИ существует много теорий о превосходстве так называемой «настоящей дамасской стали» (то есть тигельного булата или вуца) над всеми другими видами металла. Это мнение, по-видимому, появилось в начале XIX века, и было распространено главным образом через романтическую литературу, такую, как «Талисман» и «Айвенго» Вальтера Скотта. Собственно исторически и металлургически миф об абсолютном превосходстве тигельного булата не обоснован, также и как его предпочтение всеми народами. До сих пор археологами не найден ни один ближневосточный клинок старше XV века на территории западной Европы, состоящий из тигельного булата, хотя, следуя соответствующему мифу, рыцари их покупали на «вес золота», потому что они якобы «резали кольчугу как масло». Никаких исторических доказательств этому до сих пор не существует. Также Римская Империя имела обширные торговые связи с Древним Востоком (персы, индийцы) и по словам Плиния Старшего лучшая сталь привозилась оттуда.[7] Хотя индийскую тигельную сталь, предположительно, знали ещё во времена Александра Македонского, до сих пор науке не известны римские доспехи, спаты или гладиусы, состоящие из «того самого» узорчатого булата. Напротив, именно сварные харалуги часто встречаются среди находок римской эпохи[источник не указан 2390 дней].
Также тигельный булат упоминается в исторических источниках только с XIII века, когда крестовые походы уже были на исходе. Сабля является оружием режущим, а чисто с физической точки зрения и согласно материаловедению термообработанная и отпущенная сталь на твёрдость 55-58 HRC не может быть разрезана точно такой же сталью. Мифы о разрубании пластинчатых доспехов и других мечей на самом деле являются продуктами XIX и XX веков и не соответствуют исторической действительности. Что касается легенды о том, что ближневосточные народы легко расправлялись с тяжелобронированными крестоносцами[8] с помощью кривых сабель, то она также не имеет исторических доказательств. Хотя наличие импортных среднеазиатских сабель (которые как правило не имели с персидскими и индийскими булатами ничего общего) неоспоримо, один из самых ранних «исламских» ближневосточных кривых клинков датируется концом XIII века.[9] Начиная с VIII[10] века до XVI[11] на Востоке одновременно с саблей ходили и прямые мечи, кои и применялись против кольчуги, в которую были одеты рыцари эпохи Крестовых Походов. Утверждение, что ближневосточные народы не пользовались прямыми клинками в эпоху Крестовых Походов, следовательно необоснованно, также как и использование рыцарями «тяжёлых двуручных мечей» (что ошибочно предполагал Вальтер Скотт в своих трудах). Сабли из тигельного булата появились лишь в XIII веке (см. выше), а клыч и ятаган, которые часто приписывают «сарацинам» популярные источники, — только спустя 200 лет после окончания Крестовых Походов в конце XV века.
К тому же металлургические исследования до сих пор не доказали, что тигельный узорчатый булат обладал какими-то необычайными свойствами, выходящими за пределы дозволенного законами физики.[12]
Само название «дамасская сталь» часто ставится под сомнение[источник не указан 2390 дней], так как город Дамаск (от имени которого и произошло наименование стали) никогда не славился кузнечным делом и мастерами. Большинство сохранившихся булатных клинков происходят из Сирии, Персии и Индии, как правило не из регионов, связанных непосредственно с Дамаском. Есть предположение[источник не указан 2390 дней], что в Дамаске существовал обширный рынок оружия, где булатные клинки предлагались в большой массе — отчего их и назвали дамасскими. Второе предположение[источник не указан 2390 дней], что первый клинок из такой стали был найден как раз таки в окрестностях Дамаска, в связи с чем и был назван дамасским.
- Аносов П. П. О булатах. Кн. 1—2 // Горный журнал. — 1841. — № 2. — С. 157—318.
- Belaiew N. T. Damascene steel, part 1 // The Journal of the Iron and Steel Institute. — 1918. — Vol. 97. — № 1. — P. 417—439.
- Belaiew N. T. Damascene steel, part 2 // The Journal of the Iron and Steel Institute. — 1921 — Vol. 104. — № 1. — P. 181—184.
- Zschokke B. Du damasse et des lames de Damas // Revue de métallurgie. — 1924. — № 21. — P. 635—669.
- Panseri C. Damascus Steel in Legend and Reality // Gladius. — 1965. — Vol. 4. — P. 5—66.
- Sherby O. D. Damascus Steel Rediscovered? // Transactions of the Iron and Steel Institute of Japan. — 1979. — Vol. 19. — № 7. — P. 381—390.
- Wadsworth J., Sherby O. D. On the bulat-damascus steels revisited // Progress in Materials Science. — 1980. — Vol. 25. — P. 35—68.
- Sherby O. D., Wadsworth J. Damascus Steels — Myths, Magic and Metallurgy // The Stanford Engineer. — Fall/winter 1983—1984. — P. 27—37.
- Verhoeven J. D. Damascus steel, part I: Indian wootz steel // Metallography. — 1987. — Vol. 20. — P. 145—151.
- Verhoeven J. D., Jones L. L. Damascus steel, part II: Origin of the damask pattern Original // Metallography. — 1987. — Vol. 20. — P. 153—180.
- Verhoeven J. D., Baker H. H., Peterson D. T. et al. Damascus steel, part III: The Wadsworth-Sherby mechanism // Materials Characterization. — 1990. — Vol. 24. — P. 205—227.
- Peterson D. T., Baker H. H., Verhoeven J. D. Damascus Steel: Characterization of one Damascus Steel Sword // Materials Characterization. — 1990. — Vol. 24. — P. 355—374.
- Figiel L. S. On Damascus Steel. — Atlantis Arts Press, 1991. — 145 pp. — ISBN 0-9628711-1-7, 978-0-96-287111-5.
- Verhoeven J. D., Pendray A. H. Experiments To Reproduce the Pattern of Damascus Steel Blades // Materials Characterization. — 1992. — Vol. 29. — P. 195—212.
- Verhoeven J. D., Pendray A. H., Berge P. M. Studies of Damascus Steel Blades: Part I. Experiments on reconstructed blades // Materials Characterization. — 1993. — Vol. 30. — № 3. — P. 175—186.
- Verhoeven J. D., Pendray A. H., Berge P. M. Studies of Damascus Steel Blades: Part II. Destruction and Reformation of the Pattern // Materials Characterization. — 1993. — Vol. 30. — № 3. — P. 187—200.
- Verhoeven J. D. The Mystery of Damascus Blades // Scientific American. — 2001. — Vol. 284. — № 1. — P. 74—79.
- Reibold M., Paufler P., Levin A. A. et al. Carbon nanotubes in an ancient Damascus sabre // Nature. — 2006. — Vol. 444 (7117). — P. 286.
- Verhoeven J. D. Pattern Formation in Wootz Damascus Steel Swords and Blades // Indian Journal of History of Science. — 2007. — Vol. 42. — № 4. — P. 559—574.
- Федосов С. А. Исследование сварочной дамасской стали современной выделки // Металлург. — 2007. — № 12. — С. 64—74 (краткое изложение).
Пружинная сталь — Википедия
Материал из Википедии — свободной энциклопедии
Пружинная сталь — это низколегированный сплав, среднеуглеродистая или высокоуглеродистая сталь с очень большим пределом текучести. Это позволяет изделиям из пружинной стали возвращаться к исходной форме несмотря на значительный изгиб и скручивание.
Большинство пружинных сталей (как те, что используются в автомобилях) закалены и отпущены до значения 45 по шкале C Роквелла.
Кремний является ключевым компонентом большинства пружинных стальных сплавов. В США самой часто используемой пружинной сталью является ASTM A228 (0.80-0.95 % углерода), которая также известна под названием «музыкальная проволока» («music wire») или «пианинная проволока» («piano wire»).[1]
В России основными марками рессорно-пружинной стали являются марки 60Г, 65Г и другие, с содержанием углерода 0,5-0,9 %.
Класс по SAE (класс по ASTM) | Состав | Предел текучести | Максимальная твёрдость (HRC) | Комментарии |
---|---|---|---|---|
1074/1075[2] | 50 | Бесчешуйная воронёная сталь | ||
5160 (A689)[3] | 669 МПа | 63 | Хромово-кремниевая пружинная сталь; устойчива к усталости | |
9255 | 1.50-1.80 % Si, 0.70-1.00 % Mn и 0.52-0.60 % C | |||
301 Spring-tempered нержавеющая сталь (A666)[4] | 1014 МПа | 42 |
Применяется для изготовления пружин и тому подобных изделий, например, торсионов и рессор. Из-за устойчивости к изломам и трещинам пружинная сталь также широко используется при производстве металлических шпаг для сценических сражений. Пружинная сталь это один из самых популярных материалов при изготовлении отмычек по причине эластичности и гибкости. Также используется для фортепианных струн и пружинных хомутов.
- ↑ Oberg, Jones, Horton, Ryffel, 2000, p. 286.
- ↑ McMaster-Carr catalog (116th ed.), McMaster-Carr, с. 3630, <http://www.mcmaster.com/#catalog/116/3630>. Проверено 3 сентября 2010.
- ↑ McMaster-Carr catalog (116th ed.), McMaster-Carr, с. 3632, <http://www.mcmaster.com/#catalog/116/3632>. Проверено 3 сентября 2010.
- ↑ McMaster-Carr catalog (116th ed.), McMaster-Carr, с. 3662, <http://www.mcmaster.com/#catalog/116/3662>. Проверено 3 сентября 2010.
- ГОСТ 14959-79. Прокат из рессорно-пружинной углеродистой и легированной стали. Технические условия.
- ГОСТ 9389-75 Проволока стальная углеродистая пружинная. Технические условия.
- Oberg, Erik; Franklin D. Jones; Holbrook L. Horton; Henry H. Ryffel; Franklin D. Jones, Holbrook L. Horton, and Henry H. Ryffel. Machinery’s Handbook (неопр.) / Christopher J. McCauley, Riccardo Heald, and Muhammed Iqbal Hussain. — 26th edition. — New York: Industrial Press Inc, 2000. — ISBN 0-8311-2635-3.
История производства и использования железа — Википедия
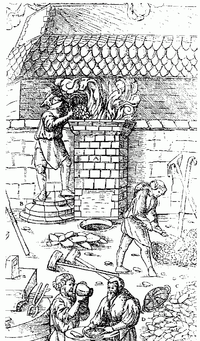
История производства и использования железа берёт своё начало в доисторической эпохе, скорее всего, с использования метеоритного железа. Выплавка в сыродутной печи применялась в XII веке до н. э. в Индии, Анатолии и на Кавказе. Также отмечается использование железа при выплавке и изготовлении орудий и инструментов в 1200 году до н. э. в Африке южнее Сахары[2][3]. Уже в первом тысячелетии до н. э. использовалось кованое железо (англ. Wrought iron). Об обработке железа упоминается в первой книге Библии (Быт. 4:22).
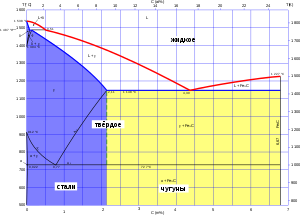
Материал, в обиходе называемый «железом», как правило, является сталью или чугуном и представляет собой сплав железа (Fe), как химического элемента, с углеродом (C). Кроме железа и углерода сплав содержит незначительные количества других химических элементов.
При концентрации углерода в сплаве менее 0,3 % получается мягкий пластичный тугоплавкий (температура плавления железа 1539 °C) сплав, за которым и закрепляется название его основного ингредиента — железа. Представление о том железе, с которым имели дело наши предки, сейчас можно получить, исследовав механические свойства гвоздя.
При концентрации углерода в сплаве от 0,3 до 2,14 % сплав называется «сталью». В первозданном виде сталь походит по своим свойствам на железо, но, в отличие от него, поддается закалке: при резком охлаждении после нагрева до определённых температур сталь приобретает большую твёрдость — замечательное достоинство, однако, почти совершенно сводимое на нет приобретённой в процессе той же закалки хрупкостью.
При концентрации углерода в сплаве свыше 2,14 % сплав называется «чугуном». Чугун — хрупкий легкоплавкий сплав, пригодный для литья, но не поддающийся обработке ковкой. Чугун насыщен графитовыми включениями, делающими его неоднородным и механически непрочным. Температура плавления чугуна варьируется от 1150 до 1300 °C.
Технологии производства и обработки железа и сплавов[править | править код]
Для производства железа исторически применялось несколько технологий, которые сложно расположить в хронологическом порядке.
Метеоритное железо[править | править код]
Использование железа началось намного раньше, чем его производство. Иногда люди находили куски серовато-чёрного металла, попавшие на Землю с метеоритами — метеоритное железо, использовали их для изготовления оружия: перековывали в кинжалы или наконечники копий. Метеоритное железо было более прочным и пластичным, чем бронза, и дольше «держало» остроту лезвия. Поскольку железные метеориты содержали железоникелевый сплав, можно предположить, что качество некоторых уникальных кинжалов могло соперничать с современным ширпотребом[4]. Однако, та же уникальность приводила к тому, что такое оружие оказывалось не на поле боя, а в сокровищнице очередного правителя.
Сыродутная печь[править | править код]
Первым устройством для получения железа из руды стала одноразовая сыродутная печь (сыродутный горн, домница). Несмотря на наличие недостатков способ получения железа с использованием такой печи долгое время оставался единственным способом получения железа из руды. На Руси появление первых домниц относят к IX веку[5].
Впервые железо научились обрабатывать народы Анатолии. Древние греки считали, что открывателями железа был народ халибов. В литературе этот народ назывался устойчивым выражением «отец железа». Слово «сталь» на греческом языке («Χάλυβς») происходит от этого этнонима.
«Железная революция» началась на рубеже I тысячелетия до нашей эры в Ассирии. Железные мечи научились изготавливать представители Гальштатской культуры. С VIII века до нашей эры сварочное железо быстро стало распространяться в Европе, в III веке до нашей эры оно вытеснило бронзу в Галлии, во II веке новой эры появилось в Германии, а в VI веке уже широко употреблялось в Скандинавии; племенами же, проживающими на территории будущей Руси — киммерийцами, а позже скифами и сарматами — железо использовалось ещё до н. э.. В Японии железный век наступил только в VII веке нашей эры.
Известный популяризатор науки Айзек Азимов так описывает историю перехода человечества из бронзового века в железный[6]:
![]() | Где-то около XV—XIV вв. до н. э. техника выплавки и науглероживания железа была разработана в кавказских предгорьях в Урарту. Эта страна находилась тогда под властью Хеттского царства, которое находилось на высшей точке своей мощи. Хеттские цари тщательно охраняли монополию на новую технику, ибо понимали её важность. Вначале получали только маленькие партии железа, и в течение нескольких столетий оно стоило порой в сорок раз дороже серебра. Но ещё до того, как выплавку можно было увеличить, а хеттам — этим воспользоваться, им пришёл конец. Хеттское царство было разрушено во время беспорядков, последовавших за движением «народов моря», и хеттская монополия на железо была нарушена. Технология выплавки железа быстро распространялась в том числе, конечно, в Ассирию, которая граничила с «железным царством» Урарту. Торговля железом восстановила процветание Ассирии. Открылся путь для новых завоеваний. Вторгшиеся в Грецию дорийские племена обладали железным оружием, именно поэтому они так легко покорили вооруженных бронзой ахейцев. Было железо и у «народов моря», и, когда филистимляне захватывали ханаанское побережье, в сражениях они использовали железное оружие, Но они были не настолько глупы, чтобы раскрывать секрет выплавки железа. Пока им удавалось хранить эту техническую тайну, израильтянам приходилось обороняться более примитивным оружием. Благодаря железу филистимляне не только легко закрепились на побережье, но и обложили данью ближайшие к ним племена. Около двух веков (до прихода к власти Давида в 1013 году до н. э.) им удавалось господствовать над более многочисленными израильскими племенами. | ![]() |
Первым шагом в зарождающейся чёрной металлургии было получение железа путём восстановления его из окиси. Болотная руда перемешивалась с древесным углём и закладывалась в печь. При высокой температуре, создаваемой горением угля, углерод начинал соединяться не только с атмосферным кислородом, но и с тем кислородом, который был связан с атомами железа.
После выгорания угля в печи оставалась так называемая «крица» — комок пористого восстановленного железа с примесью большого количества шлаков. Крицу потом снова разогревали и подвергали обработке ковкой, выколачивая шлак из железа. Полученный брусок железа (в котором всё же оставалось 2—4 % шлака) назывался «кричной болванкой». Долгое время ковка была основным процессом в технологии производства железа, причём, с приданием изделию формы она была связана в последнюю очередь. Ковкой получался сам материал.
Сварное оружие[править | править код]
Сталь производилась уже из готового железа путём насыщения углеродом последнего. При высокой температуре и недостатке кислорода углерод, не успевая окисляться, пропитывал железо. Чем больше было углерода, тем твёрже оказывалась сталь после закалки.
Как можно было заметить, ни один из перечисленных выше сплавов не обладает таким свойством, как упругость. Железный сплав может приобрести это качество, только если в нём возникает чёткая кристаллическая структура, что происходит, например, в процессе застывания из расплава. Проблема же древних металлургов заключалась в том, что расплавить железо они не могли. Для этого требуется разогреть его до 1540 °C, в то время как технологии древности позволяли достичь температур в 1000‑1300 °C. Вплоть до середины XIX века было невозможно расплавить железо и сталь с содержанием углерода менее 0,4 %, так как плавкость железных сплавов снижается по мере уменьшения концентрации углерода.
Таким образом ни железо, ни сталь сами по себе для изготовления оружия не годились. Орудия и инструменты из чистого железа выходили слишком мягкими, а из чистой стали — слишком хрупкими. Потому, чтобы изготовить, например, меч, приходилось делать «бутерброд» из двух пластин железа, между которыми закладывалась стальная пластина. При заточке мягкое железо стачивалось и появлялась стальная режущая кромка.
Такое оружие, сваренное из нескольких слоёв с разными механическими свойствами, называлось сварным. Общими недостатками этой технологии являлись излишняя массивность и недостаточная прочность изделий. Сварной меч не мог пружинить, вследствие чего неизбежно ломался или гнулся при ударе о непреодолимую преграду.
Отсутствием упругости недостатки сварного оружия не исчерпывались. В дополнение к упомянутым недостаткам, его, например, невозможно было «толком» заточить. Железу можно было придать какую угодно остроту (хотя и стачивалось оно быстро), но и тупилась мягкая режущая кромка из железа почти мгновенно. Сталь же точиться не желала — режущая кромка крошилась. Здесь налицо полная аналогия с карандашами — мягкий грифель легко сделать острым, но он сразу затупится, а твёрдый до особой остроты не доведёшь — десять раз сломается. Так что, бритвы приходилось делать из железа и затачивать заново ежедневно.
В целом же сварное оружие не превосходило остротой столовый нож. Уже одно это обстоятельство требовало делать его достаточно массивным для придания удовлетворительных рубящих свойств.
Единственной мерой, позволяющей достичь сочетания остроты и твёрдости в рамках технологии сварки, была закалка изделия уже после его заточки. Применим же этот метод становился в случае, если стальная режущая кромка приваривалась просто к железному обуху, а не заключалась в «бутерброд» из железа. Либо после заточки могли быть закалены клинки, у которых железный сердечник покрывался снаружи сталью. Недостатком такого метода было то, что заточка оказывалась возможна лишь однажды. Когда стальное лезвие повреждалось и тупилось, весь клинок приходилось перековывать.
Тем не менее именно освоение техники сварки — несмотря на все её недостатки — произвело настоящий переворот во всех сферах человеческой деятельности и привело к огромному возрастанию производительных сил. Сварные орудия были вполне функциональны и, при том, общедоступны. Только с их распространением каменные орудия оказались окончательно вытеснены, и наступил век металла.
Железные орудия решительно расширили практические возможности человека. Стало возможным, например, строить рубленные из брёвен дома — ведь железный топор валил дерево уже не в три, как медный, а в 10 раз быстрее, чем каменный. Широкое распространение получило и строительство из тёсаного камня. Он, естественно, употреблялся и в эпоху бронзы, но большой расход сравнительно мягкого и дорогого металла решительно ограничивал такие эксперименты. Значительно расширились также и возможности земледельцев.
Булатная сталь и дамаск[править | править код]
Увидеть железо жидким металлурги смогли только в XIX веке, однако ещё на заре железной металлургии — в начале I тысячелетия до нашей эры — индийские мастера сумели решить проблему получения высокоуглеродистой стали с композитной структурой. Такую сталь называли булатом, но из-за сложности изготовления и отсутствия необходимых материалов в большей части мира эта сталь так и осталась индийским секретом на долгое время.
Более технологичный путь получения упругой стали, при котором не требовались ни особо чистая руда, ни графит, ни специальные печи, был найден в Китае во II веке нашей эры. Сталь перековывали до двенадцати раз, при каждой ковке складывая заготовку вдвое, в результате чего получался отличный оружейный материал, называемый «дамаском», из которого, в частности, делались японские катаны (мечи). Количество слоёв стали рассчитывается по формуле A=2Nx{\displaystyle A=2^{N}x}, где N{\displaystyle N} — количество проковок, а x{\displaystyle x} — изначальное количество видов (слоёв) стали, сковываемой в «бутерброд». При каждой ковке количество слоёв удваивалось, а после 12 проковок количество слоёв достигало 4096, и слои становились неразличимы.
Штукофен[править | править код]
Более высокую, по сравнению с сыродутной печью, ступень в развитии чёрной металлургии представляли собой постоянные высокие печи, называемые в Европе штукофенами. Это действительно была высокая печь — с четырёхметровой трубой для усиления тяги. Мехи штукофена «качались» уже несколькими людьми, а иногда и водяным двигателем. Штукофен имел дверцы, через которые раз в сутки извлекалась крица.
Изобретены штукофены были в Индии в начале первого тысячелетия до новой эры. В начале нашей эры они попали в Китай, а в VII веке вместе с «арабскими» цифрами арабы заимствовали из Индии и эту технологию. В конце XIII века штукофены стали появляться в Германии и Чехии (а ещё до того были на юге Испании) и в течение следующего века распространились по всей Европе.
Производительность штукофена была несравненно выше, чем сыродутной печи — в день он давал до 250 кг железа, а температура в нём оказывалась достаточна для науглероживания части железа до состояния чугуна. Однако штукофенный чугун при остановке печи застывал на её дне, смешиваясь со шлаками, а очищать металл от шлаков умели тогда только ковкой, но как раз ей-то чугун и не поддавался. Его приходилось выбрасывать.
Иногда, впрочем, штукофенному чугуну пытались найти какое-то применение. Например, древние индусы отливали из грязного чугуна гробы, а турки в начале XIX века — пушечные ядра. Трудно судить, сколь хорошими были гробы, но ядра из него получались невысокого качества.
Ядра для пушек из железистых шлаков в Европе отливали ещё в конце XVI века. Из литой брусчатки делались дороги. В Нижнем Тагиле до сих пор сохранились здания с фундаментами из литых шлаковых блоков[7].
Блауофен[править | править код]
Металлурги давно заметили связь между температурой плавления и выходом продукта — чем выше была температура, тем большую часть содержащегося в руде железа удавалось восстановить. Потому рано или поздно им приходила мысль улучшить штукофен — добавить предварительный подогрев воздуха и увеличить высоту трубы. В середине XV века в Европе появились печи нового типа — блауофены, которые сразу преподнесли сталеварам неприятный сюрприз.
Более высокая температура действительно значительно повысила выход железа из руды, но она же повысила и долю железа науглероживающегося до состояния чугуна. Теперь уже не 10 %, как в штукофене, а 30 % выхода составлял чугун — «свиное железо», ни к какому делу не годное. В итоге, выигрыш часто не окупал модернизации.
Блауофенный чугун, как и штукофенный, застывал на дне печи, смешиваясь со шлаками. Он выходил несколько лучшим, так как его самого было больше, следовательно, относительное содержание шлаков выходило меньше, но продолжал оставаться малопригодным для литья. Чугун, получаемый из блауофенов, оказывался уже достаточно прочен, но оставался ещё очень неоднородным. Из него выходили только предметы простые и грубые — кувалды, наковальни, пушечные ядра.
Кроме того, если в сыродутных печах могло быть получено только железо, которое потом науглероживалось, то в штукофенах и блауофенах внешние слои крицы оказывались состоящими из стали. В блауофенных крицах стали было даже больше, чем железа. С одной стороны, это было хорошо, но вот отделить сталь от железа оказалось весьма затруднительно. Содержание углерода становилось трудно контролировать. Только долгой ковкой можно было добиться однородности его распределения.
В своё время, столкнувшись с этими затруднениями, индусы не стали двигаться дальше, а занялись тонким усовершенствованием технологии и пришли к получению булата. Но индусов в ту пору интересовало не количество, а качество продукта. Европейцы, экспериментируя с чугуном, скоро открыли передельный процесс, поднявший металлургию железа на качественно новый уровень.
Доменная печь[править | править код]
Следующим этапом в развитии металлургии стало появление доменных печей. За счёт увеличения размера, предварительного подогрева воздуха и механического дутья, в такой печи всё железо из руды превращалось в чугун, который расплавлялся и периодически выпускался наружу. Производство стало непрерывным — печь работала круглосуточно и не остывала. За день она выдавала до полутора тонн чугуна. Перегнать же чугун в железо в горнах было значительно проще, чем выколачивать его из крицы, хотя ковка все равно требовалась — но теперь уже выколачивали шлаки из железа, а не железо из шлаков.
Хотя найденные в Китае чугунные изделия восходят к V веку до нашей эры[8], самые ранние доменные печи, производящие чугун в «чушках» (слитках), который мог переплавляться в очищенный чугун в вагранках, датируются III—II веками до нашей эры. Подавляющее большинство обнаруженных ранних мест доменного производства относятся к периоду после введения государственной монополии на соль и железорудную промышленность в 117 году до нашей эры (период правления императора У-ди, 141—87 до н. э.) в эпоху династии Хань (202 год до нашей эры — 220 год нашей эры). Большинство железоделательных мест, открытых до 117 года до нашей эры, занимались лишь литьём из заготовок, выплавленных в доменных печах в других районах, отдалённых от населённых пунктов[9][10].
В Европе доменные печи впервые были применены на рубеже XV—XVI веков. На Ближнем Востоке и в Индии эта технология появилась только в XIX веке (в значительной степени, вероятно, потому, что водяной двигатель из-за характерного дефицита воды на Ближнем Востоке не употреблялся). Наличие в Европе доменных печей позволило ей обогнать в XVI веке Турцию если не по качеству металла, то по валу. Это оказало несомненное влияние на исход борьбы, особенно когда оказалось, что из чугуна можно лить пушки.
Георгий Агрикола так описывает средневековую технологию плавки[11]:
![]() | Обычай выдающихся плавильщиков, умеющих управлять четырьмя элементами (имеются в виду земля, воздух, огонь и вода — вне цитаты), таков. Они смешивают в правильных пропорциях руды, содержащие земли, и загружают их в печи. Затем льют нужное количество воды и умело управляют движением воздуха, поступающего из мехов, забрасывая руду туда, где огонь горит с наибольшей силой. Мастер равномерно обрызгивает водой внутреннее пространство печи, слегка увлажняя древесный уголь с тем, чтобы к нему приставали мелкие частицы руды; иначе эти частицы приводятся в движение силой дутья и огня и уносятся вместе с дымом. | ![]() |
Также Агрикола верно объясняет необходимость изменения конструкции печи в зависимости от типа руд[11]:
![]() | Так как природа руд, подлежащих плавке, бывает различной, плавильщикам приходится устраивать горн то выше, то ниже и устанавливать трубу, куда вводятся насадки мехов под меньшим или большим углом для того, чтобы дутье при надобности было более или менее сильным. Если руды нагреваются и плавятся легко, то для работы плавильщиков необходим низкий горн, а труба должна быть установлена под небольшим углом, чтобы дутье было легкое. Наоборот, если руды нагреваются и плавятся медленно, то требуется высокий горн, а труба должна быть установлена с крутым уклоном, чтобы обеспечить сильное дутье. Для руд этого рода нужна весьма горячая печь, в которой сначала расплавляются шлаки, штейны или легкоплавкие камни для того, чтобы руда не могла пригореть к поду горна и закрыть выпускное отверстие. | ![]() |
Передельный процесс[править | править код]
С XVI века в Европе получил распространение так называемый передельный процесс в металлургии — технология, при которой железо ещё при получении за счёт высокой температуры плавления и интенсивного науглероживания перегонялось в чугун, а уже затем, жидкий чугун, освобождаясь от лишнего углерода при отжиге в горнах, превращался в сталь.
Из передельной стали уже можно было изготавливать кривые мечи (например, сабли), чего не позволяла сделать сварная технология.
Применение угля, коксование, пудлингование, горячее дутьё[править | править код]
С начала XVII века европейской кузницей стала Швеция, производившая половину железа в Европе. В середине XVIII века её роль в этом отношении стала стремительно падать в связи с очередным изобретением — применением в металлургии каменного угля.
Прежде всего надо сказать, что до XVIII века включительно каменный уголь в металлургии практически не использовался — из-за высокого содержания вредных для качества продукта примесей, в первую очередь — серы. С XVII века в Англии каменный уголь, правда, начали применять в пудлинговочных печах для отжига чугуна, но это позволяло достичь лишь небольшой экономии древесного угля — большая часть топлива расходовалась на плавку, где исключить контакт угля с рудой было невозможно.
Потребление же топлива в металлургии уже тогда было огромно — домна (доменная печь) пожирала воз угля в час. Древесный уголь превратился в стратегический ресурс. Именно изобилие дерева в самой Швеции и принадлежащей ей Финляндии позволило шведам развернуть производство таких масштабов. Англичане, имевшие меньше лесов (да и те были зарезервированы для нужд флота), вынуждены были покупать железо в Швеции до тех пор, пока не научились использовать каменный уголь. Его ввёл в употребление в XVII веке Клемент Клерк и его мастера кузнечных дел и литья.
С 1709 году в местечке Коулбрукдейл Абрахам Дарби, основатель целой династии металлургов и кузнецов, использовал кокс для получения чугуна из руды в доменной печи. Из него поначалу делали лишь кухонную утварь, которая отличалась от работы конкурентов лишь тем, что её стенки были тоньше, а вес меньше. В 1750-х годах сын Дарби (Абрахам Дарби II) построил ещё несколько домен, и к этому времени его изделия были ещё и дешевле, чем изготовленные на древесном угле. В 1778 году внук Дарби, Абрахам Дарби III, из своего литья построил в Шропшире знаменитый Железный мост, первый мост в Европе, полностью состоящий из металлических конструкций.
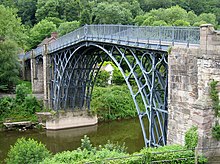
Для дальнейшего улучшения качества чугуна в 1784 году Генри Корт разработал процесс пудлингования. Среди многих металлургических профессий того времени, пожалуй, самой тяжелой была профессия пудлинговщика. Пудлингование было основным способом получения железа почти на протяжении всего XIX века. Это был очень тяжёлый и трудоёмкий процесс. Работа при нём шла так. На подину пламенной печи загружались чушки (слитки) чугуна; чушки расплавляли. По мере выгорания из металла углерода и других примесей температура плавления металла повышалась, и из жидкого расплава начинали «вымораживаться» кристаллы довольно чистого железа. На подине печи собирался комок слипшейся тестообразной массы. Рабочие-пудлинговщики приступали к операции накатывания крицы при помощи железного лома. Перемешивая ломом массу металла, они старались собрать вокруг лома комок, или крицу, железа. Такой комок весил до 50—80 кг и более. Крицу вытаскивали из печи и подавали сразу под молот — для проковки с целью удаления частиц шлака и уплотнения металла[7].
Рост производства и улучшение качества английского металла к концу XVIII века позволило Великобритании полностью отказаться от импорта шведского и российского железа. Развернулось сооружение каналов, позволявших перевозить уголь и металлы.
С 1830 по 1847 год производство металла в Англии возросло более чем в 3 раза. Применение горячего дутья при плавке руды, начавшееся в 1828 году, втрое сократило расход топлива и позволило использовать в производстве низшие сорта каменного угля, С 1826 по 1846 год экспорт железа и чугуна из Великобритании увеличился в 7,5 раза[12].
Конвертерное производство и мартеновские печи[править | править код]
В 1856 году Генри Бессемер получил патент на новую технологию производства стали (бессемеровский процесс). Он изобрёл конвертер — устройство, в котором сквозь жидкий чугун, получаемый в доменных печах, продувался воздух. В конвертере происходит выгорание углерода, растворённого в железе, что позволяет получать сталь в существенно больших количествах, чем это было ранее доступно.
Альтернативой применения конвертера на протяжении XX века являлась мартеновская печь, в которой также происходило дожигание углерода. К концу XX века мартеновские печи стали очевидно устаревшей технологией и были вытеснены кислородно-конвертерным производством стали.
В середине XX века был изобретён турбодетандер, позволяющий снизить затраты на производство кислорода. Кислород стал достаточно дешёвым, чтобы получить массовое применение в сталелитейной промышленности. Продувка расплавленного чугуна кислородом существенно разогревает металл, что упрощает производство (железо не «вымораживается», а остаётся жидким), позволяет также в конвертер сбрасывать металлолом для переплавки, а также в ряде случаев улучшает качество металла за счёт отсутствия растворённого в металле азота.
Электрометаллургия[править | править код]
Способность постоянного электрического тока восстанавливать металлы была обнаружена ещё в самом начале XIX века, однако отсутствие мощных источников электроэнергии ограничивало применение этих процессов лабораторными исследованиями. Появление в начале XX века мощных электростанций позволило создать промышленные технологии электрометаллургии. Изначально такие процессы применялись для производства цветных металлов, но к середине XX века пришли и в чёрную металлургию. Широкое применение нашли процессы электрической рудовосстанавливающей плавки, при которой железная руда, смешенная с незначительным количеством углерода, подвергается воздействию мощной электрической дуги, где происходит электрическое восстановление железа на катоде и выгорание примесей на аноде. Таким способом удаётся получить чугун высокого качества, сократить расход кислорода и снизить уровень выбросов углекислого газа. Передельные электрометаллургические процессы дают возможность плавить чугун в вакууме, в среде защитного газа, в присутствии химически активных легирующих элементов, что позволяет получать легированные стали высокого качества и специальные стали (жаропрочные, радиационно стойкие). Стали, получение которых возможно только электрометаллургическими процессами называют электросталями.
Восстановление водородом[править | править код]
Доменные печи и конвертерное производство является достаточно современным, но весьма грязным для экологии процессом. При том, что большая часть железа получается в кислородно-конвертерном производстве, велики и выбросы углекислого и угарного газов в атмосферу. Модной альтернативой становится прямое восстановление железа из руды водородом. При этом образующиеся частички железа расплавляются в электрических печах, после чего добавляется углерод и получается сталь.
Кузнецы-любители[править | править код]
Первыми производство железных изделий организовали кузнецы-любители — обычные крестьяне, промышлявшие таким ремеслом в свободное от обработки земли время. Кузнец сам находил «руду» (болотная руда вблизи ржавого болота или красный песок), сам выжигал уголь, сам строил сыродутную печь и выплавлял железо, сам ковал, сам обрабатывал.
Умение мастера на данном этапе закономерно было ограничено выковыванием изделий самой простой формы. Инструментарий же его состоял из мехов, каменных молота и наковальни и точильного камня. Железные орудия производились с помощью каменных инструментов.
Если удобные для разработки залежи руды имелись поблизости, то и целая деревня могла заниматься производством железа, но такое было возможным только при наличии устойчивой возможности выгодного сбыта продукции, чего практически не могло быть в условиях натурального хозяйства.
При такой организации производства железа, никогда не удавалось за его счёт полностью покрыть все потребности в самом простом оружии и самых необходимых орудиях труда. Из камня продолжали изготавливаться топоры, из дерева — гвозди и плуги. Металлические доспехи оставались недоступными даже для вождей. Концентрация железных изделий составляла всего порядка 200 граммов на душу населения[источник не указан 1152 дня].
На таком уровне доступности железа находились в начале нашей эры наиболее отсталые племена среди бриттов, германцев и славян. В XII‑XIII веке прибалты и финны сражаясь с крестоносцами пользовались ещё каменным и костяным оружием. Все эти народы умели уже делать железо, но ещё не могли получить его в необходимом количестве.[источник не указан 1152 дня]
Профессиональные кузнецы[править | править код]
Следующим этапом развития чёрной металлургии были профессиональные кузнецы, которые всё ещё сами выплавляли металл, но на добычу железоносного песка и выжигания угля чаще уже отправляли других мужиков — в порядке натурального обмена. На этом этапе кузнец, обычно, уже имел помощника-молотобойца и как-то оборудованную кузницу.
С появлением кузнецов концентрация железных изделий возрастала в 4‑5 раз. Теперь уже каждый крестьянский двор мог быть обеспечен персональным ножом и топором. Возрастало и качество изделий. Кузнецы профессионалы, как правило, владели техникой сварки и могли вытягивать проволоку. В принципе, такой умелец мог получить и дамаск, если знал как, но производство дамаскового оружия требовало такого количества железа, что не могло ещё быть сколько-то массовым.
В XVIII-XIX веках деревенские кузнецы умудрялись даже изготовлять стволы к нарезному оружию, но в этот период они уже пользовались оборудованием, которое сделали не сами. Некоторого масштаба перенос ремесленного производства из города в деревню становился возможным на таком этапе развития города, когда стоимость даже довольно сложного оборудования оказывалась незначительной.
Средневековые же деревенские кузнецы сами делали свои орудия труда. Как умели. Поэтому рядовой мастер обычно преуспевал в изготовлении предметов простой плоской формы, но положительно затруднялся, когда требовалось изготовить трёхмерное изделие, или состыковать несколько изделий между собой — что, например, требовалось для создания надёжного шлема. Изготовить же такое сложное изделие, как спусковой механизм для арбалета, деревенскому кузнецу было непосильно — для этого ведь потребовались бы даже измерительные устройства.
Не было у кустарных кузнецов и специализации — и мечи, и иголки, и подковы делал один и тот же мастер. Более того, во все времена сельские кузнецы были заняты в первую очередь именно изготовлением наиболее необходимых односельчанам простейших производственных и бытовых орудий, но не оружия.
Впрочем, последнее отнюдь не отменяет того обстоятельства, что в примитивных культурах даже самый заурядный кузнец считался несколько сродни колдуну, хотя, более адекватно его можно уподобить художнику. Выковывание даже обычного меча было настоящим искусством.
Теоретически всё выглядело просто: надо только наложить одна на другую три полоски металла, проковать их, и клинок готов. На практике, однако, возникали проблемы — с одной стороны надо было добиться прочной сварки и даже взаимопроникновения слоев, а с другой, нельзя было нарушать равномерность толщины слоя (а она-то и была — с лист бумаги) и, тем более, допустить, чтобы слой разорвался. А, ведь, обработка производилась тяжёлым молотом.
До разделения труда между городом и деревней годовое производство железа не превышало 100 граммов в год на человека, форма изделий была очень простой, а качество — низким, и, когда описывается вооружение какого-нибудь варяга, систематически упускается из вида, что речь идёт об оружии вождя, откопанном в его кургане. Варвары, которым курганы не полагались, вооружались существенно проще. На данном уровне развития производительных сил (характерном, например, для галлов, франков, норманнов, Руси X века) тяжёлое вооружение могло иметься только у аристократии — не более одного воина в броне на 1000 человек населения.
На новый уровень металлообрабатывающая промышленность вступила только тогда, когда стало возможным разделение труда и возникновение специальностей. Мастер железо покупал, причём уже нужного качества, покупал инструменты, необходимые по его профилю, и нанимал подмастерьев. Если уж он и делал ножи, то сдавал их на реализацию ящиками. Если делал мечи, то не по два в год, а по четыре в неделю. И, естественно, обладал большим опытом в их изготовлении.
Но для возникновения специализации непременно требовался город — хоть на несколько тысяч жителей — чтобы мастер мог всё купить и продать. Даже очень крупные призамковые посёлки (а их население тоже иногда достигало нескольких тысяч человек) не давали такой возможности — ведь в них не только ничего не производилось на продажу в другие поселения, но и отсутствовал даже внутренний товарообмен.
Чем более был развит обмен, тем больше могло быть мастеров и их специализаций, сформироваться разделение труда. Но для значительного развития обмена требовались деньги и сравнительная стабильность.
Ещё больший прогресс мог быть достигнут организацией мануфактуры, но вокруг неё требовалось выстроить уже 50-тысячный город, и наличие ещё нескольких таких же поблизости.
Тем не менее, даже после сосредоточения ремесленного производства в городах, колоритная фигура кузнеца оставалась непременным элементом пасторального ландшафта вплоть до начала, а кое-где и до середины XX века. Долгое время крестьяне просто не имели возможности покупать городские изделия. На ранних этапах развития обмена квалифицированные ремесленники обслуживали только господствующие классы — в первую очередь военные сословия.
После распространения штукофенов[править | править код]
Кустарное производство железа, однако, перестало практиковаться сразу после распространения штукофенов. Кузнецы начали покупать железо в слитках, а ещё чаще — железный лом, на предмет перековки мечей на орала.
Когда же развитие товарности хозяйства сделало ремесленные изделия доступными широким массам, кузнецы ещё долго занимались починкой сделанных в городах орудий.
Параллельно с решением организационных моментов улучшение методов обработки металлов требовало и совершенствования техники. Поскольку же основным методом была ковка, то усовершенствованию подлежали в первую очередь молоты.
Дело было в том, что, если ковка осуществлялась ручным молотом, то и размер изделия оказывался ограничен физическими возможностями кузнеца. Человек был способен отковать деталь весом не более нескольких килограммов. В большинстве случаев этого оказывалось достаточно, но при изготовлении, скажем, деталей осадных машин без механического молота, приводимого в движение водяным колесом, мулами или рабочими, было уже не обойтись.
Проблема выковывания массивных (до нескольких центнеров) деталей была решена ещё в античности, но в период средних веков она обрела новую остроту, так как крицы, получаемые из штукофенов, тоже нельзя было отковать кувалдой.
Конечно, можно было делить их на небольшие части, но, при этом, в каждой оказалось бы своё, причём неизвестное, содержание углерода, а потом, для изготовления мало-мальски крупного изделия полученные куски пришлось бы сковывать обратно.
Всё это было крайне невыгодно. Ковать крицу надо было целиком. Потом
Живая сталь — Википедия
«Жива́я сталь» (англ. Real Steel) — американский фантастический боевик режиссёра Шона Леви, вдохновленный рассказом Ричарда Мэтисона «Сталь» (в русском переводе — «Стальной человек»)[3]. Главную роль в фильме сыграл Хью Джекман, а в качестве продюсеров выступили Шон Леви, Сьюзэн Монтфорд и Дон Мёрфи[4]. Мировая премьера фильма состоялась 6 сентября 2011 года в Париже в кинотеатре Гран-Рекс[5]. В США и России картина вышла в прокат 7 октября[6].
В России фильм разрешён для показа зрителям, достигшим 12 лет. В США фильм не рекомендуется смотреть детям до 13 лет[7].
Действие истории разворачивается в будущем, в 2020 году, когда традиционные боксёрские поединки и другие боевые искусства утратили зрительский интерес и свою актуальность из-за недостаточной жестокости, и были заменены гладиаторскими боями с участием роботов, управляемых людьми.
Главный герой — Чарли Кентон (Хью Джекман), бывший боксер, живущий у дочери своего умершего тренера Бейли Таллет (Эванджелин Лилли), принимает участие в боях роботов, терпя одно поражение за другим и всё глубже увязая в долгах. Попутно он узнает, что умерла его бывшая жена, оставив их сына Макса Кентона (Дакота Гойо) сиротой. Продав право на опеку над мальчиком более состоятельным родственникам покойной супруги, он берет Макса на время под свою опеку, «чтобы наладить отношения отца и сына», а также для получения дополнительных денег.
Он снова участвует в боях, покупая на вырученные деньги одного из лучших роботов — Нойзи Боя с голосовым управлением, где терпит очередное фиаско из-за того, что, даже не ознакомившись с доступными приёмами, как выразился Макс, просто «выкрикивал то, что круче звучит». В поисках деталей на нового робота Чарли с сыном идут на свалку, где Макс, упав с обрыва, находит бракованного, но целого робота второго поколения, по имени «Атом». Этот устаревший робот был создан не для боёв, а как спарринг-партнёр, он не может атаковать, но зато хорошо держит удар и имеет редкую «функцию тени», позволяющей повторять любые движения человека. Макс решает с помощью Атома участвовать в нелегальных боях роботов и заработать немного денег.
В первом же бою Атом побеждает и выясняется, что он очень стойкий робот. Макс, установив голосовой контроль от Нойзи Боя на Атома, предлагает Чарли научить через «функцию тени» Атома боксерскому стилю. Так, побеждая в боях, Атом становится участником турнира «Живая сталь», а Чарли и Макс сближаются. После победы над профессиональным роботом «Твин Ситис» Макс вызывает на бой Фарру Лемкову (Ольга Фонда) — миллиардершу, для которой Так Машидо (Карл Юн), легендарный создатель боевых роботов, собрал Зевса — непобедимого робота, чемпиона «Живой стали». После дерзкого вызова Макса, для Лемковой начинается «Пиар-кошмар», и через некоторое время она принимает вызов.
Затем на Чарли и Макса неожиданно нападают бизнесмены, которым Чарли задолжал, и избивают их, забрав все деньги. Беспокоясь за сына, Чарли отдаёт его официальным опекунам, чтобы обезопасить. Но после разговора с Бейли, он меняет решение и уговаривает их отпустить Макса с ним на турнир, и они соглашаются.
Во время боя Зевс, атакуя Атома, наносит ему серьёзные повреждения, разрушив систему голосового контроля. Макс уговаривает Чарли бороться с Зевсом через «функцию тени» Атома. Дождавшись, пока у Зевса закончится заряд энергии, Чарли наносит серию сокрушительных ударов. Чемпион «Живой Стали» начинает проигрывать, и за пульт управления Зевса садится сам Так Машидо. Несмотря на это, Атом отправляет Зевса в нокдаун, но тому удается подняться. Зевс побеждает по очкам, но это сокрушительный провал для компании Фарры Лемковой. Атома провозглашают Народным чемпионом, а Чарли признаётся Максу, что привязался к нему.
- «Fast Lane» — Bad Meets Evil
- «Here’s A Little Something For» — Beastie Boys
- «Miss The Misery» — Foo Fighters
- «The Enforcer» — 50 Cent
- «Nine Thou» — Styles of Beyond
- «Make Some Noise» — The Crystal Method feat. Yelawolf
- «Till I Collapse» — Eminem feat. Nate Dogg
- «One Man Army» — The Prodigy & Tom Morello
- «Give It A Go» — Timbaland feat. Veronica
- «I’m Your Daddy» — Weezer
- «The Midas Touch» — Tom Morello
- «Why Try» — Limp Bizkit
- «Torture» — Rival Sons
- «All My Days» — Alexi Murdoch
- «Kenton» — Danny Elfman
- «The Wings of Icarus» — Celldweller
- «You’ll Be Under My Wheels» — The Prodigy
Первый трейлер фильма появился в декабре 2010 года[8]. В мае 2011 года DreamWorks выпустила второй трейлер. 19 сентября Джекман появился на WWE Raw, чтобы прорекламировать фильм[9]. 24 сентября на Первом канале вышел выпуск программы «Прожекторперисхилтон» с участием Джекмана, в котором актёр рассказывал о фильме[10].
Поисковик Bing прорекламировал фильм в своём блоге, а в фильме замечен логотип «bing»[11].
Фильм получил смешанные отзывы кинокритиков. На Rotten Tomatoes 60 % рецензий являются положительными, средний рейтинг составляет 5,9 из 10[12]. Сайт Metacritic дал фильму оценку в 56 баллов из 100 на основе 32 обзоров[13]. Роджер Эберт оценил фильм в 3 звезды из 4-х[14].
Фильм вошёл в число номинантов на премию «Оскар» за лучшие визуальные эффекты[15].
В ноябре 2016 года стало известно, что ведётся проработка сиквела «Живая сталь 2»[16]. Сценаристом продолжения является Джон Гэйтинс[17]. Стивен Спилберг подключился в качестве исполнительного продюсера фильма[18].
Обсуждение:Сталь — Википедия
Глупая война правок. Я прекрасно знаю, что в Википедии это спор решен и что правильно писать «на Украине», но остаюсь на стороне анонимного участника, который пытался пропихнуть версию с «В». Я живу в Украине и всегда пишу и встречаю (в книгах, прессе) версию «в Украине». Признаю, что в России ситуация может быть другой, но это выглядит довольно смешно и глупо. Но согласен, холивар устраивать смысла нет. Ink 19:54, 13 декабря 2010 (UTC)
Вна Украине — пишут «в», в России — «на». Соответственно — в русском разделе википедии пишут по-русски. А не по-украински…
- По правилам русского языка, правильно писать «на Украине». HarDNoxぎ¿ 19:37, 13 июня 2015 (UTC)
Господа, существующее определение стали можно подогнать любое г… на основе железа с примесью углерода до 2,14% Потому-то и есть гостированные ограничения по количеству примесей. Кроме того, не все стали ковкие! Яркий пример сталь ХВГ, которая не куется, потому что очень хрупкая. Еще, при указывании верхнего предела по содержанию углерода указывайте уже и нижний предел, а то норот подумает, что железо с 0,005% углерода тоже сталь. Предлагаю следующее определение: Сталь — это сплав железа с углеродом с содержанием углерода от 0,01% до 2,14% (на практике до 2%), а также содержанием постоянных примесей: серы до 0,04%, фосфора до 0,04%, марганца до 0,8% и кремния до 0,08%.
Далее. Следует перечислить виды классиикации стали, описать хотябы виды обычной углеродистой стали по структуре, та в конце концов, описание стали нужно начинать с диаграммы железо-углерод!
Статью писал безграмотный студент-двоишник 2-го курса машиностроительного вуза —213.227.245.156 12:34, 5 апреля 2012 (UTC)
Изменяю определение стали[править код]
Совершенно безграмотное определение стали. Сталь вовсе не обязана быть твердым раствором (эвтектика — не твердый раствор) или иметь эвтектическое превращение (низкоуглеродистые стали — доэевтектические). Поэтому меняю определение. Chivesud 20:14, 19 августа 2013 (UTC)
не хватает истории появления стали, развития производства стали 213.87.122.208 11:21, 6 сентября 2013 (UTC) Жорик
Очень хреновая статья.[править код]
Господа металлурги, у кого есть день-другой свободного времени? Пожалуйста… Абсолютно с Вами согласен. Хрень полная.217.118.83.166
Электротермический способ[править код]
«до 800 кВт / ч на 1 т стали»
Энергия получается не делением, а умножением мощности (кВт) на время (час): кВт•час. Лучше словом: киловатт-час. Леонид 87.99.93.122 12:21, 14 декабря 2015 (UTC)
«Кодовый символ». Наверное, всё же условный знак (или усл. обозначение). Текст, случаем, не из школьного учебника «перетяпан», в большей своей части? Yury Tarasievich 06:28, 3 января 2016 (UTC)
…до 1991 учитывает РСФСР или СССР? Yury Tarasievich 06:28, 3 января 2016 (UTC)
Пункты 3 и 7 называются одинаково: «Производство стали»
213.141.146.181 18:39, 2 февраля 2016 (UTC)
Я удивляюсь вам, господа мелаллурги. Посвятить столько места и усилий на устаревшие методы — мартеновский, бессемеровский, томасовский… Только читателя путаете. Может кто не ленивый может их обработать, чтобы историческая значимость была отмечена, а большая часть букв (совершенно ненужных) была выкинута?
Chivesud (обс.) 17:58, 22 октября 2017 (UTC)
Быстрорежущая сталь — Википедия
Быстроре́жущие ста́ли — легированные стали, предназначенные главным образом для изготовления металлорежущего инструмента, работающего при высоких скоростях резания.
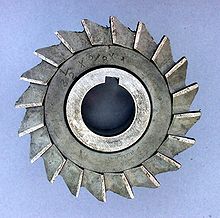
Быстрорежущая сталь должна обладать высокими сопротивлением разрушению, твёрдостью (в холодном и горячем состояниях) и красностойкостью.
Высокими сопротивлением разрушению и твердостью в холодном состоянии обладают и углеродистые инструментальные стали. Однако инструмент из них не в состоянии обеспечить высокоскоростные режимы резания. Легирование быстрорежущих сталей вольфрамом, молибденом, ванадием и кобальтом обеспечивает горячую твердость и красностойкость стали.
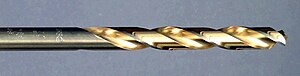
Для обточки деталей из дерева, цветных металлов, мягкой стали резцы из обычной твердой стали были вполне пригодны, но при обработке стальных деталей резец быстро разогревался, скоро изнашивался и деталь нельзя было обтачивать со скоростью больше 5 м/мин[1].
Барьер этот удалось преодолеть после того, как в 1858 году Р. Мюшетт получил сталь, содержащую 1,85 % углерода, 9 % вольфрама и 2,5 % марганца. Спустя десять лет Мюшетт изготовил новую сталь, получившую название самокалки. Она содержала 2,15 % углерода, 0,38 % марганца, 5,44 % вольфрама и 0,4 % хрома. Через три года на заводе Самуэля Осберна в Шеффилде началось производство мюшеттовой стали. Она не теряла режущей способности при нагревании до 300 °C и позволяла в полтора раза увеличить скорость резания металла — 7,5 м/мин.
Спустя сорок лет на рынке появилась быстрорежущая сталь американских инженеров Тэйлора и Уатта. Резцы из этой стали допускали скорость резания до 18 м/мин. Эта сталь стала прообразом современной быстрорежущей стали Р18.
Ещё через 5—6 лет появилась сверхбыстрорежущая сталь, допускающая скорость резания до 35 м/мин. Так, благодаря вольфраму было достигнуто повышение скорости резания за 50 лет в семь раз и, следовательно, во столько же раз повысилась производительность металлорежущих станков.
Дальнейшее успешное использование вольфрама нашло себе применение в создании твердых сплавов, которые состоят из вольфрама, хрома, кобальта. Были созданы такие сплавы для резцов, как стеллит. Первый стеллит позволял повысить скорость резания до 45 м/мин при температуре 700—750 °C. Сплав вида, выпущенный Круппом в 1927 году, имел твердость по шкале Мооса 9,7—9,9 (твердость алмаза равна 10).
В 1970-х годах в связи с дефицитом вольфрама быстрорежущая сталь марки Р18 была почти повсеместно заменена на сталь марки Р6М5 (так называемый «самокал», самозакаливающаяся сталь), которая, в свою очередь, вытесняется безвольфрамовыми Р0М5Ф1 и Р0М2Ф3.
Характеристики быстрорежущих сталей[править | править код]
Горячая твердость[править | править код]
При нормальной температуре твердость углеродистой стали даже несколько выше твердости быстрорежущей стали. Однако в процессе работы режущего инструмента происходит интенсивное выделение тепла. При этом до 80 % выделившегося тепла уходит на разогрев инструмента. Вследствие повышения температуры режущей кромки начинается отпуск материала инструмента и снижается его твердость.
После нагрева до 200 °C твердость углеродистой стали начинает быстро падать. Для этой стали недопустим режим резания, при котором инструмент нагревался бы выше 200 °C. У быстрорежущей стали высокая твердость сохраняется при нагреве до 500—600 °C. Инструмент из быстрорежущей стали более производителен, чем инструмент из углеродистой стали.
Красностойкость[править | править код]
Если горячая твердость характеризует то, какую температуру сталь может выдержать, то красностойкость характеризует, сколько времени сталь будет выдерживать такую температуру. То есть насколько длительное время закаленная и отпущенная сталь будет сопротивляться разупрочнению при разогреве.
Существует несколько характеристик красностойкости. Приведем две из них.
Первая характеристика показывает, какую твердость будет иметь сталь после отпуска при определенной температуре в течение заданного времени.
Второй способ охарактеризовать красностойкость основан на том, что интенсивность снижения горячей твердости можно измерить не только при высокой температуре, но и при комнатной, так как кривые снижения твердости при высокой температуре и комнатной идут эквидистантно, а измерить твердость при комнатной температуре, разумеется, гораздо проще, чем при высокой. Опытами установлено, что режущие свойства теряются при твердости 50 HRC при температуре резания, что соответствует примерно 58 HRC при комнатной. Отсюда красностойкость характеризуется температурой отпуска, при которой за 4 часа твердость снижается до 58 HRC (обозначение K4р58).
Марка стали | Температура отпуска, °C | Время выдержки, час | Твердость, HRCэ |
---|---|---|---|
У7, У8, У10, У12 | 150—160 | 1 | 63 |
Р9 | 580 | 4 | |
У7, У8, У10, У12 | 200—220 | 1 | 59 |
Р6М5К5, Р9, Р9М4К8, Р18 | 620—630 | 4 |
Сопротивление разрушению[править | править код]
Кроме «горячих» свойств, от материала для режущего инструмента требуются и высокие механические свойства; под этим подразумевается сопротивление хрупкому разрушению, так как при высокой твердости (более 60 HRC) разрушение всегда происходит по хрупкому механизму. Прочность таких высокотвердых материалов обычно определяют как сопротивление разрушению при изгибе призматических, не надрезанных образцов, при статическом (медленном) и динамическом (быстром) нагружении. Чем выше прочность, тем большее усилие может выдержать рабочая часть инструмента, тем большую подачу и глубину резания можно применить, и это увеличивает производительность процесса резания.
Химический состав быстрорежущих сталей[править | править код]
Марка стали | C | Cr | W | Mo | V | Co |
---|---|---|---|---|---|---|
Р0М2Ф3 | 1,10—1,25 | 3,8—4,6 | — | 2,3—2,9 | 2,6—3,3 | — |
Р6М5 | 0,82—0,90 | 3,8—4,4 | 5,5—6,5 | 4,8—5,3 | 1,7—2,1 | < 0,50 |
Р6М5Ф2К8 | 0,95—1,05 | 3,8—4,4 | 5,5—6,6 | 4,6—5,2 | 1,8—2,4 | 7,5—8,5 |
Р9 | 0,85—0,95 | 3,8—4,4 | 8,5—10,0 | < 1,0 | 2,0—2,6 | — |
Р18 | 0,73—0,83 | 3,8—4,4 | 17,0—18,5 | < 1,0 | 1,0—1,4 | < 0,50 |
Изготовление и обработка быстрорежущих сталей[править | править код]
Быстрорежущие стали изготавливают как классическим способом (разливка стали в слитки, прокатка и проковка), так и методами порошковой металлургии (распыление струи жидкой стали азотом)[3]. Качество быстрорежущей стали в значительной степени определяется степенью её прокованности. При недостаточной проковке изготовленной классическим способом стали наблюдается карбидная ликвация.
При изготовлении быстрорежущих сталей распространенной ошибкой является подход к ней как к «самозакаливающейся стали». То есть достаточно нагреть сталь и охладить на воздухе, и можно получить твердый износостойкий материал. Такой подход абсолютно не учитывает особенности высоколегированных инструментальных сталей.
Перед закалкой быстрорежущие стали необходимо подвергнуть отжигу. В плохо отожженных сталях наблюдается особый вид брака: нафталиновый излом, когда при нормальной твердости стали она обладает повышенной хрупкостью.
Грамотный выбор температуры закалки обеспечивает максимальную растворимость легирующих добавок в α-железе, но не приводит к росту зерна.
После закалки в стали остается 25—30 % остаточного аустенита. Помимо снижения твердости инструмента, остаточный аустенит приводит к снижению теплопроводности стали, что для условий работы с интенсивным нагревом режущей кромки является крайне нежелательным. Снижения количества остаточного аустенита добиваются двумя путями: обработкой стали холодом или многократным отпуском[3]. При обработке стали холодом её охлаждают до −80…−70 °C, затем проводят отпуск. При многократном отпуске цикл «нагрев — выдержка — охлаждение» проводят по 2—3 раза. В обоих случаях добиваются существенного снижения количества остаточного аустенита, однако полностью избавиться от него не получается.
Принципы легирования быстрорежущих сталей[править | править код]
Высокая твердость мартенсита объясняется растворением углерода в α-железе. Известно, что при отпуске из мартенсита в углеродистой стали выделяются мельчайшие частицы карбида. Пока выделившиеся карбиды ещё находятся в мельчайшем дисперсном рассеянии (то есть на первой стадии выделения при отпуске до 200 °C), твердость заметно не снижается. Но если температуру отпуска поднять выше 200 °C, происходит рост карбидных выделений, и твердость падает.
Чтобы сталь устойчиво сохраняла твердость при нагреве, нужно её легировать такими элементами, которые затрудняли бы процесс коагуляции карбидов. Если ввести в сталь какой-нибудь карбидообразующий элемент в таком количестве, что он образует специальный карбид, то красностойкость скачкообразно возрастает. Это обусловлено тем, что специальный карбид выделяется из мартенсита и коагулирует при более высоких температурах, чем карбид железа, так как для этого требуется не только диффузия углерода, но и диффузия легирующих элементов. Практически заметная коагуляция специальных карбидов хрома, вольфрама, молибдена, ванадия происходит при температурах выше 500 °C.
Красностойкость создается легированием стали карбидообразующими элементами (вольфрамом, молибденом, хромом, ванадием) в таком количестве, при котором они связывают почти весь углерод в специальные карбиды, и эти карбиды переходят в раствор при закалке. Несмотря на сильное различие в общем химическом составе, состав твердого раствора очень близок во всех сталях, атомная сумма W+Mo+V, определяющая красностойкость, равна примерно 4 % (атомн.), отсюда красностойкости и режущие свойства у разных марок быстрорежущих сталей близки. Быстрорежущая сталь, содержащая кобальт, превосходит по режущим свойствам остальные стали (он повышает красностойкость), но кобальт очень дорогой элемент.
В советских и российских марочниках сталей марки быстрорежущих сталей обычно имеют особую систему обозначений и начинаются с буквы «Р» (rapid — быстрый). Связано это с тем, что эти стали были изобретены в Англии, где такую сталь называли «rapid steel». Цифра после буквы «Р» обозначает среднее содержание в ней вольфрама (в процентах от общей массы, буква В пропускается). Затем указывается после букв М, Ф и К содержание молибдена, ванадия и кобальта. Инструменты из быстрорежущей стали иностранного производства обычно маркируются аббревиатурой HSS (High Speed Steel), а также HSSE (кобальтовая сталь).
Сравнение твёрдости быстрорежущих сталей с кобальтом и сталей без кобальта в зависимости от температуры.В последние десятилетия использование быстрорежущей стали сокращается в связи с широким распространением твёрдых сплавов. Из быстрорежущей стали изготавливают в основном концевой инструмент (метчики, свёрла, фрезы небольших диаметров) В токарной обработке резцы со сменными и напайными твердосплавными пластинами почти полностью вытеснили резцы из быстрорежущей стали.
По применению отечественных марок быстрорежущих сталей существуют следующие рекомендации.
- Сталь Р9 рекомендуют для изготовления инструментов простой формы, не требующих большого объёма шлифовки, для обработки обычных конструкционных материалов. (резцов, фрез, зенкеров).
- Для фасонных и сложных инструментов (для нарезания резьб и зубьев), для которых основным требованием является высокая износостойкость, рекомендуют использовать сталь Р18 (вольфрамовая).
- Кобальтовые быстрорежущие стали (Р9К5, Р9К10) применяют для обработки деталей из труднообрабатываемых коррозионно-стойких и жаропрочных сталей и сплавов, в условиях прерывистого резания, вибраций, недостаточного охлаждения.
- Ванадиевые быстрорежущие стали (Р9Ф5, Р14Ф4) рекомендуют для изготовления инструментов для чистовой обработки (протяжки, развёртки, шеверы). Их можно применять для обработки труднообрабатываемых материалов при срезании стружек небольшого поперечного сечения.
- Вольфрамомолибденовые стали (Р9М4, Р6М3) используют для инструментов, работающих в условиях черновой обработки, а также для изготовления протяжек, долбяков, шеверов, фрез.
- ↑ Мезенин Н. А. Занимательно о железе. — М.: «Металлургия», 1972. — 200 с.
- ↑ Марочник сталей и сплавов / В. Г. Сорокин, А. В. Волосникова, С. А. Вяткин, и др. Под общ. ред. В. Г. Сорокина. — М.: Машиностроение, 1989. — 640 с.
- ↑ 1 2 Гуляев А. П. Металловедение. Учебник для втузов. 6-е изд., перераб. и доп. — М.: «Металлургия», 1986. — 544 с.
- Технология конструкционных материалов. Под ред. А. М. Дальского. — М.: «Машиностроение», 1958.