Твердость сталь: Твёрдость — Википедия – методы измерения, шкалы HB, HRC, HV
методы измерения, шкалы HB, HRC, HV
Машиностроительные детали и механизмы, а также инструменты, предназначенные для их обработки, обладают набором механических характеристик. Немалую роль среди характеристик играет твердость. Твердость металлов наглядно показывает:
- износостойкость металла;
- возможность обработки резанием, шлифованием;
- сопротивляемость местному давлению;
- способность резать другой материал и прочие.


На практике доказано, что большинство механических свойств металлов напрямую зависят от их твердости.
Понятие твердости
Твердость материала – это стойкость к разрушению при внедрении во внешний слой более твердого материала. Другими словами, способность к сопротивлению деформирующим усилиям (упругой или пластической деформации).
Определение твердости металлов производится посредством внедрения в образец твердого тела, именуемого индентором. Роль индентора выполняет: металлически шарик высокой твердости; алмазный конус или пирамида.
После воздействия индентора на поверхности испытуемого образца или детали остается отпечаток, по размеру которого определяется твердость. На практике используются кинематические, динамические, статические способы измерения твердости.
В основе кинематического метода лежит составление диаграммы на основе постоянно регистрирующихся показаний, которые изменяются по мере вдавливания инструмента в образец. Здесь прослеживается кинематика всего процесса, а не только конечного результата.
Динамический метод заключается в следующем. Измерительный инструмент воздействует на деталь. Обратная реакция позволяет рассчитать затраченную кинетическую энергию. Данный метод позволяет проводить испытание на твердость не только поверхности, но и некоторого объема металла.
Статические методы – это неразрушающие способы, позволяющие определить свойства металлов. Методы основаны на плавном вдавливании и последующей выдержке в течение некоторого времени. Параметры регламентируются методиками и стандартами.
Прилагаемая нагрузка может прилагаться:
- вдавливанием;
- царапанием;
- резанием;
- отскоком.
Машиностроительные предприятия на данный момент для определения твердости материалов используют методы Бринелля, Роквелла, Виккерса, а также метод микротвердости.
На основе проводимых испытаний составляется таблица, в которой указываются материалы, прилагаемые нагрузки и полученные результаты.
Единицы измерения твердости
Каждый способов измерения сопротивления металла к пластической деформации имеет свою методику его проведения, а также единицы измерения.
Измерение твердости мягких металлов производится методом Бринелля. Данному способу подвергаются цветные металлы (медь, алюминий, магний, свинец, олово) и сплавы на их основе, чугуны (за исключением белого) и отожженные стали.
Твердость по Бринеллю определяется вдавливанием закаленного, отполированного шарика из шарикоподшипниковой стали ШХ15. Окружность шарика зависит от испытуемого материала. Для твердых материалов – все виды сталей и чугунов – 10 мм, для более мягких – 1 – 2 — 2,5 — 5 мм. Необходимая нагрузка, прилагаемая к шарику:
- сплавы железа – 30 кгс/мм2;
- медь и никель – 10 кгс/мм2;
- алюминий и магний – 5 кгс/мм2.
Единица измерения твердости – это числовое значение и следующий за ними числовой индекс HB. Например, 200 НВ.
Твердость по Роквеллу определяется посредством разницы приложенных нагрузок к детали. Вначале прикладывается предварительная нагрузка, а затем общая, при которой происходит внедрение индентора в образец и выдержка.
В испытуемый образец внедряется пирамида (конус) из алмаза или шарик из карбида вольфрама (каленой стали). После снятия нагрузки производится замер глубины отпечатка.
Единица измерения твердости – это условные единицы. Принято считать, что единица — это величина осевого перемещения конуса, равная 2 мкм. Обозначение твердости маркируется тремя буквами HR (А, В, С) и числовым значением. Третья буква в маркировке обозначает шкалу.
Методика отображает тип индентора и прилагаемую к нему нагрузку.
Тип шкалы | Инструмент | Прилагаемая нагрузка, кгс |
А | Конус из алмаза, угол вершины которого 120° | 50-60 |
В | Шарик 1/16 дюйма | 90-100 |
С | Конус из алмаза, угол вершины которого 120° | 140-150 |
В основном, используются шкалы измерения А и С. Например, твердость стали HRC 26…32, HRB 25…29, HRA 70…75.
Измерению твердости по Виккерсу подвергаются изделия небольшой толщины или детали, имеющие тонкий, твердый поверхностный слой. В качестве клинка используется правильная четырехгранная пирамида угол при вершине, которой составляет 136°. Отображение значений твердости выглядит следующим образом: 220 HV.
Измерение твердости по методу Шора производится путем замера высоты отскока упавшего бойка. Обозначается цифрами и буквами, например, 90 HSD.
К определению микротвердости прибегают, когда необходимо получить значения мелких деталей, тонкого покрытия или отдельной структуры сплава. Измерение производят путем измерения отпечатка наконечника определенной формы. Обозначение значения выглядит следующим образом:
Н□ 0,195 = 2800, где
□ — форма наконечника;
0,196 — нагрузка на наконечник, Н;
2800 – численное значение твердости, Н/мм2.
Твердость основных металлов и сплавов
Измерение значения твердости проводится на готовых деталях, отправляющихся на сборку. Контроль производится на соответствие чертежу и технологическому процессу. На все основные материалы уже составлены таблицы значений твердости как в исходном состоянии, так и после термической обработки.
Цветные металлы
Твердость меди по Бринеллю составляет 35 НВ, значения латуни равны 42-60 НВ единиц в зависимости от ее марки. У алюминия твердость находится в диапазоне 15-20 НВ, а у дюралюминия уже 70НВ.
Черные металлы
Твердость по Роквеллу чугуна СЧ20 HRC 22, что соответствует 220 НВ. Сталь: инструментальная – 640-700 НВ, нержавеющая – 250НВ.
Для перевода из одной системы измерения в другую пользуются таблицами. Значения в них не являются истинными, потому что выведены империческим путем. Не полный объем представлен в таблице.
HB | HV | HRC | HRA | HSD |
228 | 240 | 20 | 60.7 | 36 |
260 | 275 | 24 | 62.5 | 40 |
280 | 295 | 29 | 65 | 44 |
320 | 340 | 34.5 | 67.5 | 49 |
360 | 380 | 39 | 70 | 54 |
415 | 440 | 44.5 | 73 | 61 |
450 | 480 | 47 | 74.5 | 64 |
480 | 520 | 50 | 76 | 68 |
500 | 540 | 52 | 77 | 73 |
535 | 580 | 54 | 78 | 78 |
Значения твердости, даже если они производятся одним и тем же методом, зависят от прилагаемой нагрузки. Чем меньше нагрузка, тем выше показания.
Методы измерения твердости
Все методы определения твердости металлов используют механическое воздействие на испытуемый образец – вдавливание индентора. Но при этом не происходит разрушение образца.
Метод определения твердости по Бринеллю был первым, стандартизованным в материаловедении. Принцип испытания образцов описан выше. На него действует ГОСТ 9012. Но можно вычислить значение по формуле, если точно измерить отпечаток на образце:
HB=2P/(πD*√(D2-d2),
- где
Р – прикладываемая нагрузка, кгс; - D – окружность шарика, мм;
- d – окружность отпечатка, мм.
Шарик подбирается относительно толщины образца. Нагрузку высчитывают предварительно из принятых норм для соответствующих материалов:
сплавы из железа — 30D2;
медь и ее сплавы — 10D2;
баббиты, свинцовые бронзы — 2,5D2.


Условное изображение принципа испытания
Скачать ГОСТ 9012-59
Схематически метод исследования по Роквеллу изображается следующим образом согласно ГОСТ 9013.


Метод измерения твердости по Роквеллу
Итоговая приложенная нагрузка равна сумме первоначальной и необходимой для испытания. Индикатор прибора показывает разницу глубины проникновения между первоначальной нагрузкой и испытуемой h –h0.
Скачать ГОСТ 9013-59
Метод Виккерса регламентирован ГОСТом 2999. Схематически он изображается следующим образом.


Метод Виккерса
Математическая формула для расчета:
HV=0.189*P/d2 МПа
HV=1,854*P/d2 кгс/мм2
Прикладываемая нагрузка варьируется от 9,8 Н (1 кгс) до 980 Н (100 кгс). Значения определяются по таблицам относительно измеренного отпечатка d.


Метод Шора
Метод считается эмпирическим и имеет большой разброс показаний. Но прибор имеет простую конструкцию и его можно использовать при измерении крупногабаритных и криволинейных деталей.
Измерить твердость по Моосу металлов и сплавов можно царапанием. Моос в свое время предложил делать царапины более твердым минералом по поверхности предмета. Он разложил известные минералы по твердости на 10 позиций. Первую занимает тальк, а последнюю алмаз.
После измерения по одной методике перевод в другую систему весьма условен. Четкие значения существуют только в соотношении твердости по Бринеллю и Роквеллу, так как машиностроительные предприятия их широко применяют. Зависимость можно проследить при изменении диаметра шарика.
d, мм | HB | HRA | HRC | HRB |
2,3 | 712 | 85,1 | 66,4 | — |
2,5 | 601 | 81,1 | 59,3 | — |
3,0 | 415 | 72,6 | 43,8 | — |
3,5 | 302 | 66,7 | 32,5 | — |
4,0 | 229 | 61,8 | 22 | 98,2 |
5,0 | 143 | — | — | 77,4 |
5,2 | 131 | — | — | 72,4 |
Как видно из таблицы, увеличение диаметра шарика значительно снижает показания прибора. Поэтому на машиностроительных предприятиях предпочитают пользоваться измерительными приборами с однотипным размером индентора.
Твердость HRC. Число твердости инструментов и крепежа.
Выбирая инструмент для работы, мы сталкиваемся с такой его характеристикой как твердость, которая характеризует его качество. Чем выше этот показатель, тем выше его способность сопротивляться пластической деформации и износу при воздействии на обрабатываемый материал. Именно этот показатель определяет, согнется ли зуб пилы при распиловке заготовок, или какую проволоку смогут перекусить кусачки.
Метод Роквелла
Среди всех существующих методов определения твердости сталей и цветных металлов самым распространенным и наиболее точным является метод Роквелла.
Проведение измерений и определение числа твердости по Роквеллу регламентируется соответствующими документами ГОСТа 9013-59. Этот метод реализуется путем вдавливания в тестируемый материал инденторов – алмазного конуса или твердосплавного шарика. Алмазные инденторы используются для тестирования закаленных сталей и твердых сплавов, а твердосплавные шарики – для менее твердых и относительно мягких металлов. Измерения проводят на механических или электронных твердомерах.
Методом Роквелла предусматривается возможность применения целого ряда шкал твердости A, B, C, D, E, F, G, H (всего – 54), каждая из которых обеспечивает наибольшую точность только в своем, относительно узком диапазоне измерений.
Для измерения высоких значений твердости алмазным конусом чаще всего используются шкалы «А», «С». По ним тестируют образцы из закаленных инструментальных сталей и других твердых стальных сплавов. А сравнительно более мягкие материалы, такие как алюминий, медь, латунь, отожженные стали испытываются шариковыми инденторами по шкале «В».
Пример обозначения твердости по Роквеллу: 58 HRC или 42 HRB.
Впереди стоящие цифры обозначают число или условную единицу измерения. Две буквы после них – символ твердости по Роквеллу, третья буква – шкала, по которой проводились испытания.
(!) Два одинаковых значения от разных шкал – это не одно и то же, например, 58 HRC ≠ 58 HRA. Сопоставлять числовые значения по Роквеллу можно только в том случае, если они относятся к одной шкале.
Диапазоны шкал Роквелла по ГОСТ 8.064-94:
A | 70-93 HR |
B | 25-100 HR |
C | 20-67 HR |
Слесарный инструмент
Инструменты для ручной обработки металлов (рубка, резка, опиливание, клеймение, пробивка, разметка) изготавливают из углеродистых и легированных инструментальных сталей. Их рабочие части подвергают закаливанию до определенной твердости, которая должна находиться в пределах:
Ножовочные полотна, напильники | 58 – 64 HRC |
Зубила, крейцмессели, бородки, кернеры, чертилки | 54 – 60 HRC |
Молотки (боек, носок) | 50 – 57 HRC |
Монтажный инструмент
Сюда относятся различные гаечные ключи, отвертки, шарнирно-губцевый инструмент. Норму твердости для их рабочих частей устанавливают действующие стандарты. Это очень важный показатель, от которого зависит, насколько инструмент износостоек и способен сопротивляться смятию. Достаточные значения для некоторых инструментов приведены ниже:
Гаечные ключи с размером зева до 36 мм | 45,5 – 51,5 HRC |
Гаечные ключи с размером зева от 36 мм | 40,5 – 46,5 HRC |
Отвертки крестовые, шлицевые | 47 – 52 HRC |
Плоскогубцы, пассатижи, утконосы | 44 – 50 HRC |
Кусачки, бокорезы, ножницы по металлу | 56 – 61 HRC |
Металлорежущий инструмент
В эту категорию входит расходная оснастка для обработки металла резанием, используемая на станках или с ручными инструментами. Для ее изготовления используются быстрорежущие стали или твердые сплавы, которые сохраняют твердость в холодном и перегретом состоянии.
Метчики, плашки | 61 – 64 HRC |
Зенкеры, зенковки, цековки | 61 – 65 HRC |
Сверла по металлу | 63 – 69 HRC |
Сверла с покрытием нитрид-титана | до 80 HRC |
Фрезы из HSS | 62 – 66 HRC |
Примечание: Некоторые производители фрез указывают в маркировке твердость не самой фрезы, а материала, который она может обрабатывать.
Крепежные изделия
Существует взаимосвязь между классом прочности крепежа и его твердостью. Для высокопрочных болтов, винтов, гаек эта взаимосвязь отражена в таблице:
Болты и винты | Гайки | Шайбы | ||||||||||||||
Классы прочности |
8.8 |
10.9 | 12.9 |
8 |
10 |
12 |
Ст. | Зак.ст. | ||||||||
d<16 мм | d>16 мм | d<16 мм | d>16 мм | |||||||||||||
Твердость по Роквеллу, HRC | min | 23 | 23 | 32 | 39 | 11 | 19 | 26 | 29.2 | 20.3 | 28.5 | |||||
max | 34 | 34 | 39 | 44 | 30 | 36 | 36 | 36 | 23.1 | 40.8 |
Если для болтов и гаек главной механической характеристикой является класс прочности, то для таких крепежных изделий как стопорные гайки, шайбы, установочные винты, твердость не менее важна.
Стандартами установлены следующие минимальные / максимальные значения по Роквеллу:
Стопорные кольца до Ø 38 мм | 47 – 52 HRC |
Стопорные кольца Ø 38 -200 мм | 44 – 49 HRC |
Стопорные кольца от Ø 200 мм | 41 – 46 HRC |
Стопорные зубчатые шайбы | 43.5 – 47.5 HRB |
Шайбы пружинные стальные (гровер) | 41.5 – 51 HRC |
Шайбы пружинные бронзовые (гровер) | 90 HRB |
Установочные винты класса прочности 14Н и 22Н | 75 – 105 HRB |
Установочные винты класса прочности 33Н и 45Н | 33 – 53 HRC |
Относительное измерение твердости при помощи напильников
Стоимость стационарных и портативных твердомеров довольно высока, поэтому их приобретение оправдано только необходимостью частой эксплуатации. Многие мастеровые по мере надобности практикуют измерять твердость металлов и сплавов относительно, при помощи подручных средств.
Опиливание образца напильником – один из самых доступных, однако далеко не самый объективный способ проверки твердости стальных деталей, инструмента, оснастки. Напильник должен иметь не затупленную двойную насечку средней величины №3 или №4. Сопротивление опиливанию и сопровождающий его скрежет позволяет даже при небольшом навыке отличить незакаленную сталь от умеренно (40 HRC) или твердо закаленной (55 HRC).
Для тестирования с большей точностью существуют наборы тарированных напильников, именуемые также царапающий твердомер. Они применяются для испытания зубьев пил, фрез, шестерен. Каждый такой напильник является носителем определенного значения по шкале Роквелла. Твердость измеряется коротким царапанием металлической поверхности поочередно напильниками из набора. Затем выбираются два близко стоящие – более твердый, который оставил царапину и менее твердый, который не смог поцарапать поверхность. Твердость тестируемого металла будет находиться между значениями твердости этих двух напильников.
Переводная таблица твердости
Для сопоставления чисел твердости Роквелла, Бринелля, Виккерса, а также для перевода показателей одного метода в другой существует справочная таблица:
Виккерс, HV | Бринелль, HB | Роквелл, HRB |
100 | 100 | 52.4 |
105 | 105 | 57.5 |
110 | 110 | 60.9 |
115 | 115 | 64.1 |
120 | 120 | 67.0 |
125 | 125 | 69.8 |
130 | 130 | 72.4 |
135 | 135 | 74.7 |
140 | 140 | 76.6 |
145 | 145 | 78.3 |
150 | 150 | 79.9 |
155 | 155 | 81.4 |
160 | 160 | 82.8 |
165 | 165 | 84.2 |
170 | 170 | 85.6 |
175 | 175 | 87.0 |
180 | 180 | 88.3 |
185 | 185 | 89.5 |
190 | 190 | 90.6 |
195 | 195 | 91.7 |
200 | 200 | 92.8 |
205 | 205 | 93.8 |
210 | 210 | 94.8 |
215 | 215 | 95.7 |
220 | 220 | 96.6 |
225 | 225 | 97.5 |
230 | 230 | 98.4 |
235 | 235 | 99.2 |
240 | 240 | 100 |
Виккерс, HV | Бринелль, HB | Роквелл, HRC |
245 | 245 | 21.2 |
250 | 250 | 22.1 |
255 | 255 | 23.0 |
260 | 260 | 23.9 |
265 | 265 | 24.8 |
270 | 270 | 25.6 |
275 | 275 | 26.4 |
280 | 280 | 27.2 |
285 | 285 | 28.0 |
290 | 290 | 28.8 |
295 | 295 | 29.5 |
300 | 300 | 30.2 |
310 | 310 | 31.6 |
320 | 319 | 33.0 |
330 | 328 | 34.2 |
340 | 336 | 35.3 |
350 | 344 | 36.3 |
360 | 352 | 37.2 |
370 | 360 | 38.1 |
380 | 368 | 38.9 |
390 | 376 | 39.7 |
400 | 384 | 40.5 |
410 | 392 | 41.3 |
420 | 400 | 42.1 |
430 | 408 | 42.9 |
440 | 416 | 43.7 |
450 | 425 | 44.5 |
460 | 434 | 45.3 |
470 | 443 | 46.1 |
490 | - | 47.5 |
500 | - | 48.2 |
520 | - | 49.6 |
540 | - | 50.8 |
560 | - | 52.0 |
580 | - | 53.1 |
600 | - | 54.2 |
620 | - | 55.4 |
640 | - | 56.5 |
660 | - | 57.5 |
680 | - | 58.4 |
700 | - | 59.3 |
720 | - | 60.2 |
740 | - | 61.1 |
760 | - | 62.0 |
780 | - | 62.8 |
800 | - | 63.6 |
820 | - | 64.3 |
840 | - | 65.1 |
860 | - | 65.8 |
880 | - | 66.4 |
900 | - | 67.0 |
1114 | - | 69.0 |
1120 | - | 72.0 |
Примечание: В таблице приведены приближенные соотношения чисел, полученные разными методами. Погрешность перевода значений HV в HB составляет ±20 единиц, а перевода HV в HR (шкала C и B) до ±3 единиц.
При выборе инструмента желательно предпочесть модели известных производителей. Это дает уверенность в том, что приобретаемый продукт изготовлен с соблюдением технологий, а его твердость отвечает заявленным значениям.
Статьи о продукции 23.09.2019 16:32:41
«Какова твердость стали?» – Яндекс.Кью
Твердость стали зависит от многих факторов — это и содержание углерода, и наличие других элементов в сплаве (например, хрома, молибдена, никеля, азота), а еще твердость стали зависит от технологии ее создания.
Главный фактор твердости стали – это содержание в ней углерода. Низкоуглеродистые стали, которые содержать от 0,05 до 0,25% углерода, обычно мягкие, тогда как высокоуглеродистые стали, содержащие до 2% углерода, могут быть очень твердыми. Но конечная твердость зависит от режима термической обработки — например, закалка может увеличить твердость углеродистой стали в четыре раза.
Твердость стали можно определять разными методами — Бринелля, Виккерса, Шора, Роквелла. Каждый метод имеет свои особенности: например, по методу Шора твердость определяется по высоте отскока бойка, падающего на твердую поверхность с определнной высоты; а по методам Бринелля, Виккерса и Роквелла в поверхность под нагрузкой вдавливаются стальные или алмазные тела — инденторы (шарики, наконечники. пирамиды — для разных методов свое тело), и по отпечаткам на поверхности определяют твердость.
По методу Ровелла, для измерения твердости стали применяют три шкалы:
A – обозначается HRA, индентор – алмазный конус, диапазон измерений: 60-80 HRA. Применима к высокоуглеродистым легированным инструментальным сталям, а также твердым сплавам.
B – обозначается HRB, индентор – закаленный шарик, диапазон измерений: 35-100 HRB. Это уже стали средней твердости и сплавы цветных металлов.
C – обозначается HRC, индентор – алмазный конус, диапазон измерений: 20-90 HRC. Для сталей средней твердости.
Много теории и общих слов, а теперь приведу пример попроще для понимания, какова бывает твердость стали. Например, ножевых сталей с твердостью свыше 70HRC не существует. А на практике не встречается ножей из стали твердостью свыше 65HRC. Самыми распространенными и прекрасно используемыми являются ножи из дамасской стали с твердостью 56-62HRC.
Твердость металлов. Таблица твердости металлов
Для того чтобы детали и механизмы служили длительно и надежно, материалы, из которых они изготовлены, должны соответствовать необходимым условиям работы. Именно поэтому важно контролировать допустимые значения их основных механических показателей. К механическим свойствам относятся твердость, прочность, ударная вязкость, пластичность. Твердость металлов — первичная конструкционная характеристика.
Понятие
Твердость металлов и сплавов — это свойство материала создавать сопротивление при проникновении в его поверхностные слои иного тела, которое не деформируется и не разрушается при сопутствующих нагрузках (индентора). Определяют с целью:
- получения информации о допустимых конструкционных особенностях и о возможностях эксплуатации;
- анализа состояния под действием времени;
- контроля результатов температурной обработки.
От этого показателя частично зависят прочность и устойчивость поверхности к старению. Исследуют как исходный материал, так и уже готовые детали.
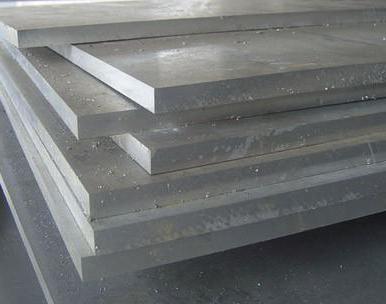
Варианты исследования
Показателем является величина, которая называется числом твердости. Существуют различные методы измерения твердости металлов. Наиболее точные исследования заключаются в использовании различных видов вычисления, инденторов и соответствующих твердомеров:
- Бринелля: суть работы аппарата – вдавливание шарика в исследуемый металл или сплав, вычисление диаметра отпечатка и последующее математическое вычисление механического параметра.
- Роквелла: используются шарик или алмазный конусный наконечник. Значение отображается на шкале или определяется расчётно.
- Виккерса: наиболее точное измерение твердости металла с применением алмазного пирамидального наконечника.
Для определения параметрических соответствий между показателями разных способов измерения для одного и того же материала существуют специальные формулы и таблицы.
Факторы, определяющие вариант измерения
В лабораторных условиях, при наличии необходимого ассортимента оборудования, выбор способа исследования осуществляется в зависимости от определенных характеристик заготовки.
- Ориентировочное значение механического параметра. Для конструкционных сталей и материалов с небольшой твердостью до 450-650 НВ применяют метод Бринелля; для инструментальных, легированных сталей и других сплавов – Роквелла; для твердосплавов – Виккерса.
- Размеры испытуемого образца. Особо маленькие и тонкие детали обследуются с помощью твердомера Виккерса.
- Толщина металла в месте замера, в частности, цементированного или азотированного слоя.
Все требования и соответствия задокументированы ГОСТом.
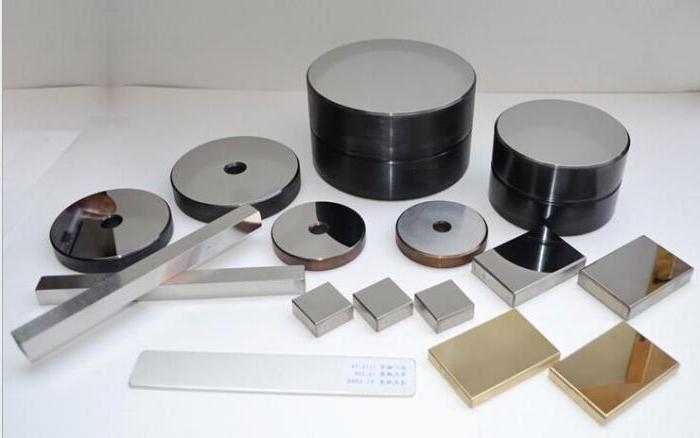
Особенности методики Бринелля
Испытания на твердость металлов и сплавов с помощью твердомера Бринелля проводятся со следующими особенностями:
- Индентор – шарик из легированной стали или из карбидо-вольфрамового сплава диаметром 1, 2, 2,5, 5 или 10 мм (гост 3722-81).
- Продолжительность статического вдавливания: для чугуна и стали – 10-15 с., для цветных сплавов – 30, также возможна длительность в 60 с., а в некоторых случаях – 120 и 180 с.
- Граничное значение механического параметра: 450 НВ при измерении стальным шариком; 650 НВ при использовании твердосплава.
- Возможные нагрузки. С помощью входящих в комплект грузов корректируется фактическая сила деформации на испытуемый образец. Их минимальные допустимые значения: 153,2, 187,5, 250 Н; максимальные – 9807, 14710, 29420 Н (гост 23677-79).
С помощью формул, в зависимости от диаметра выбранного шарика и от испытуемого материала, можно вычислить соответствующее допустимое усилие вдавливания.
Тип сплава | Математическое вычисление нагрузки |
Сталь, сплавы никеля и титана | 30D2 |
Чугун | 10D2, 30D2 |
Медь и медные сплавы | 5D2, 10D2, 30D2 |
Легкие металлы и сплавы | 2,5D2, 5D2, 10D2, 15D2 |
Свинец, олово | 1D2 |
Пример обозначения:
400HB10/1500/20, где 400HB – твердость металла по Бринеллю; 10 – диаметр шарика, 10 мм; 1500 – статическая нагрузка, 1500 кгс; 20 – период осуществления вдавливания, 20 с.
Для установления точных цифр рационально исследовать один и тот же образец в нескольких местах, а общий результат определять путем нахождения среднего значения из полученных.
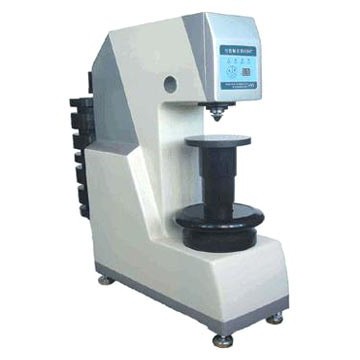
Определение твердости по методу Бринелля
Процесс исследования протекает в следующей последовательности:
- Проверка детали на соответствие требованиям (ГОСТ 9012-59, гост 2789).
- Проверка исправности аппарата.
- Выбор необходимого шарика, определение возможного усилия, установка грузов для его формирования, периода вдавливания.
- Запуск твердомера и деформация образца.
- Измерение диаметра углубления.
- Эмпирическое вычисление.
НВ=F/A,
где F – нагрузка, кгс или Н; A – площадь отпечатка, мм2.
НВ=(0,102*F)/(π*D*h),
где D – диаметр шарика, мм; h – глубина отпечатка, мм.
Твердость металлов, измеренная этим способом, имеет эмпирическую связь с вычислением параметров прочности. Метод точен, особенно для мягких сплавов. Является основополагающим в системах определения значений этого механического свойства.
Особенности методики Роквелла
Этот способ измерения был изобретен в 20-х годах XX века, более автоматизирован, чем предыдущий. Применяется для более твердых материалов. Основные его характеристики (ГОСТ 9013-59; гост 23677-79):
- Наличие первичной нагрузки в 10 кгс.
- Период выдержки: 10-60 с.
- Граничные значения возможных показателей: HRA: 20-88; HRB: 20-100; HRC: 20-70.
- Число визуализируется на циферблате твердомера, также может рассчитываться арифметически.
- Шкалы и инденторы. Известно 11 различных шкал в зависимости от типа индентора и предельно-допустимой статической нагрузки. Наиболее распространённые в использовании: А, В и С.
А: алмазный конусный наконечник, угол при вершине 120˚, общая допустимая сила статического влияния – 60 кгс, HRA; исследуются тонкие изделия, в основном прокат.
С: также алмазный конус, рассчитанный на максимальное усилие 150 кгс, HRC, применим для твердых и закаленных материалов.
В: шарик размером 1,588 мм, изготовленный из закаленной стали или из твердого карбидо-вольфрамового сплава, нагрузка – 100 кгс, HRB, используется для оценки твердости отожжённых изделий.
Шарикообразный наконечник (1,588 мм) применим для шкал Роквелла B, F, G. Также существуют шкалы E, H, K, для которых используется шарик диаметром 3,175 мм (ГОСТ 9013-59).
Количество проб, проделанных с помощью твердомера Роквелла на одной площади, ограничивается размером детали. Допускается повторная проба на расстоянии 3-4 диаметра от предыдущего места деформации. Толщина испытуемого изделия также регламентируется. Она должна быть не меньше увеличенной в 10 раз глубины внедрения наконечника.
Пример обозначения:
50HRC – твердость металла по Роквеллу, измерена с помощью алмазного наконечника, ее число равно 50.
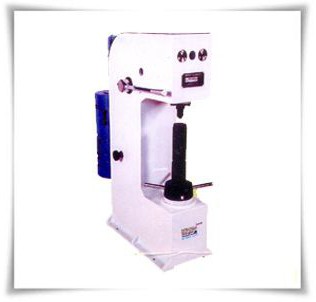
План исследования по методу Роквелла
Измерение твердости металла более упрощено, нежели для способа Бринелля.
- Оценка размеров и характеристик поверхности детали.
- Проверка исправности аппарата.
- Определение типа наконечника и допустимой нагрузки.
- Установка образца.
- Осуществление первичного усилия на материал, величиной в 10 кгс.
- Осуществление полного соответствующего усилия.
- Чтение полученного числа на шкале циферблата.
Также возможен математический расчет с целью точного определения механического параметра.
При условии использования алмазного конуса с нагрузкой 60 или 150 кгс:
HR=100-((H-h)/0,002;
при совершении испытания с помощью шарика под усилием 100 кгс:
HR=130-((H-h)/0,002,
где h – глубина внедрения индентора при первичном усилии 10 кгс; H – глубина внедрения индентора при полной нагрузке; 0,002 – коэффициент, регламентирующий величину перемещения наконечника при изменении числа твердости на 1 единицу.
Метод Роквелла является простым, но недостаточно точным. В то же время он позволяет измерять показатели механического свойства для твердых металлов и сплавов.
Характеристики методики Виккерса
Определение твердости металлов по данному способу наиболее просто и точно. Работа твердомера основана на вдавливании в образец алмазного пирамидального наконечника.
Основные особенности:
- Индентор: алмазная пирамида с углом при вершине 136°.
- Предельно допустимая нагрузка: для легированного чугуна и стали — 5-100 кгс; для медных сплавов — 2,5-50 кгс; для алюминия и сплавов на его основе — 1-100 кгс.
- Период выдержки статической нагрузки: от 10 до 15 с.
- Испытуемые материалы: сталь и цветные металлы с твердостью более 450-500 НВ, в том числе изделия после химико-термической обработки.
Пример обозначения:
700HV20/15,
где 700HV – число твердости по Виккерсу; 20 – нагрузка, 20 кгс; 15 – период статического усилия, 15 с.
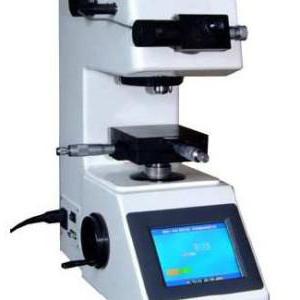
Последовательность исследования Виккерса
Порядок действий предельно упрощен.
- Проверка образца и аппаратуры. Особое внимание уделяется поверхности детали.
- Выбор допустимого усилия.
- Установка испытуемого материала.
- Запуск твердомера в работу.
- Чтение результата на циферблате.
Математический расчет по этому способу выглядит следующим образом:
HV=1,8544*(F/d2),
где F – нагрузка, кгс; d – среднее значение длин диагоналей отпечатка, мм.
Он позволяет измерять высокую твердость металлов, тонких и небольших деталей, при этом предоставляя высокую точность результата.
Способы перехода между шкалами
Определив диаметр отпечатка с помощью специального оборудования, можно с помощью таблиц определить твердость. Таблица твердости металлов – проверенный помощник в вычислении данного механического параметра. Так, если известно значение по Бринеллю, можно легко определить соответствующее число Виккерса или Роквелла.
Пример некоторых значений соответствия:
Диаметр отпечатка, мм | Метод исследования | ||||
Бринелля | Роквелла | Виккерса | |||
A | C | B | |||
3,90 | 241 | 62,8 | 24,0 | 99,8 | 242 |
4,09 | 218 | 60,8 | 20,3 | 96,7 | 218 |
4,20 | 206 | 59,6 | 17,9 | 94,6 | 206 |
4,99 | 143 | 49,8 | — | 77,6 | 143 |
Таблица твердости металлов составлена на основе экспериментальных данных и имеет высокую точность. Также существуют графические зависимости твердости по Бринеллю от содержания углерода в железоуглеродистом сплаве. Так, в соответствии с такими зависимостями, для стали с количеством карбона в составе равному 0,2% она составляет 130 НВ.
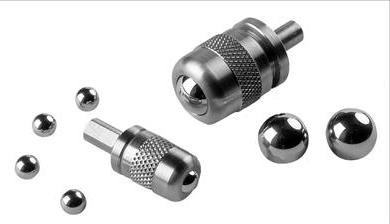
Требования к образцу
В соответствии с требованиями ГОСТов, испытуемые детали должны соответствовать следующим характеристикам:
- Заготовка должна быть ровная, твердо лежать на столе твердомера, ее края должны быть гладкими или тщательно обработаны.
- Поверхность должна иметь минимальную шероховатость. Должна быть отшлифована и очищена, в том числе с помощью химических составов. Одновременно, во время процессов механической обработки, важно предупредить образование наклепа и повышения температуры обрабатываемого слоя.
- Деталь должна соответствовать выбранному методу определения твердости по параметрическим свойствам.
Выполнение первичных требований – обязательное условие точности измерений.
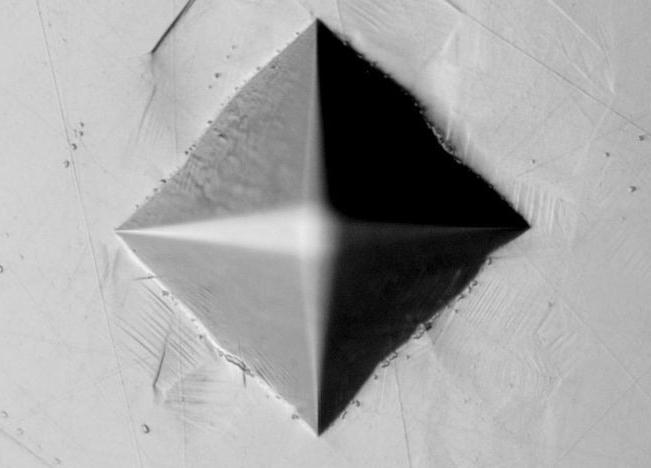
Твердость металлов — важное основополагающее механическое свойство, определяющее их некоторые остальные механические и технологические особенности, результаты предыдущих процессов обработки, влияние временных факторов, возможные условия эксплуатации. Выбор методики исследования зависит от ориентировочных характеристик образца, его параметров и химического состава.
«Какова твердость стали?» – Яндекс.Знатоки
Твердость стали зависит от многих факторов — это и содержание углерода, и наличие других элементов в сплаве (например, хрома, молибдена, никеля, азота), а еще твердость стали зависит от технологии ее создания.
Главный фактор твердости стали – это содержание в ней углерода. Низкоуглеродистые стали, которые содержать от 0,05 до 0,25% углерода, обычно мягкие, тогда как высокоуглеродистые стали, содержащие до 2% углерода, могут быть очень твердыми. Но конечная твердость зависит от режима термической обработки — например, закалка может увеличить твердость углеродистой стали в четыре раза.
Твердость стали можно определять разными методами — Бринелля, Виккерса, Шора, Роквелла. Каждый метод имеет свои особенности: например, по методу Шора твердость определяется по высоте отскока бойка, падающего на твердую поверхность с определнной высоты; а по методам Бринелля, Виккерса и Роквелла в поверхность под нагрузкой вдавливаются стальные или алмазные тела — инденторы (шарики, наконечники. пирамиды — для разных методов свое тело), и по отпечаткам на поверхности определяют твердость.
По методу Ровелла, для измерения твердости стали применяют три шкалы:
A – обозначается HRA, индентор – алмазный конус, диапазон измерений: 60-80 HRA. Применима к высокоуглеродистым легированным инструментальным сталям, а также твердым сплавам.
B – обозначается HRB, индентор – закаленный шарик, диапазон измерений: 35-100 HRB. Это уже стали средней твердости и сплавы цветных металлов.
C – обозначается HRC, индентор – алмазный конус, диапазон измерений: 20-90 HRC. Для сталей средней твердости.
Много теории и общих слов, а теперь приведу пример попроще для понимания, какова бывает твердость стали. Например, ножевых сталей с твердостью свыше 70HRC не существует. А на практике не встречается ножей из стали твердостью свыше 65HRC. Самыми распространенными и прекрасно используемыми являются ножи из дамасской стали с твердостью 56-62HRC.
Ножевые стали | Кузница Коваль
При выборе охотничьих, туристических, кухонных и ножей для повседневного использования (EDC), топоров или мачете, следует поближе познакомиться с материалом для изготовления режущей части этих изделий.
Очень важно знать, какими свойствами обладает марка стали, который используется в изделии. К таким свойствам относятся, в первую очередь, упругость, вязкость, способность держать заточку, устойчивость к коррозии, твердость и способность к доводке режущей кромки. При этом не следует также упускать из виду такие факторы, как пригодность стали для обработки и ее стоимость.
Ни одна сталь не может объединять в себе все положительные свойства. Углеродистая сталь, например, за счет мелкозернистой структуры легко затачивается, но при этом не очень устойчива к коррозии. Клинки из стали, изготовленной с применением метода порошковой металлургии, мало подвержены коррозии и хорошо сохраняют режущие свойства, но одновременно трудно поддаются доводке режущей кромки, поэтому процесс обработки такой стали очень трудоемок и стоит довольно дорого.
Стали, используемые для производства ножей, можно грубо разделить на две группы: углеродистые и легированные стали.
Углеродистые стали
В принципе, любая сталь, предназначенная для изготовления ножей, должна поддаваться закалке, для чего содержание углерода в ней должно быть не менее 0,5%. При содержании углерода свыше 1,7% сталь уже не поддается обработке ковкой. В углеродистых сталях практически отсутствуют другие составные элемента сплава, как, например, марганец, хром, ванадий, молибден.
Одним из свойств углеродистой стали является ее простота при термической обработке, то есть, имея относительно широкий температурный диапазон нагрева, эта сталь легко «прощает» погрешности мастера в процессе ковки и закалки. Углеродистая сталь хорошо поддается различным видам обработки в не закаленном состоянии (опиливание, сверление, шлифовка и т.д.), кроме того, легко затачивается. Благодаря мелкозернистой структуре карбидов железа лезвие из такой стали в результате заточки может быть очень острым.
Основным недостатком углеродистой стали является отсутствие коррозионной стойкости, что, правда, можно свести до минимума с помощью полировки поверхности изделия до блеска и, конечно, тщательного ухода. На практике это означает следующее: после эксплуатации ножа, его клинок необходимо очистить от грязи и слегка смазать маслом. Но даже самый лучший уход не может предотвратить образование на поверхности углеродистой стали серого налета и пятен, если клинок ножа входит в контакт с кислотами, например, с фруктовой кислотой при резке томатов или яблок, а также при соприкосновении с жирными кислотами, например, при резке жареного мяса.
Легированные стали
Легированные инструментальные стали являются идеальным материалом для изготовления ножей.
Все легированные стали имеют следующие положительные свойства: устойчивость к коррозии (если содержание хрома свыше 13%), твердость и способность сохранять режущие свойства. Выбор правильной стали зависит, в первую очередь, от того, для каких целей предназначен будущий нож.
Стали, изготовленные метолом порошковой металлургии (ПМ), отличаются значительно более высокой износостойкостью по сравнению со стандартными сталями, кроме того, они прекрасно поддаются закалке и одновременно сохраняют хорошую вязкость – три свойства, которые можно только пожелать ножевой стали. В последнее время эти стали все больше используются в ножевом производстве.
Технология изготовления стали с применением порошковой металлургии достаточно дорогостоящая. В ходе технологического процесса расплавленные составные элементы сплава распыляются в вакууме ИЛИ инертном газе, после чего, находясь в тестообразном состоянии, спрессовываются под высоким давлением и при высокой температуре. Благодаря этому процессу элементы сплава легко соединяются друг с другом, тогда как просто в расплавленном состоянии и при достаточно высокой концентрации смешать их уже невозможно. Это можно сравнить с солью и водой: соль хорошо растворяется в том или ином объеме воды до определенного предела насыщения; если добавлять соль далее, то растворяться она уже не будет. Кроме того, в ходе данного процесса твердые карбиды принимают форму мелких шариков почти одинакового размера, поэтому благодаря мелкозернистой структуре сталь, изготовленная с помощью данной технологии, хорошо полируется.
За счет большой вязкости и высокого сопротивления разрыву сталь ПМ имеет больший предел прочности лезвия на излом, чем обычные марки сталей. Это свойство позволяет подвергать такую сталь более высокой степени закалки, а это значит, что лезвие ножа может быть тоньше.
Совершенно очевидно, что сталь ПМ за счет ее трудоемкого производства дороже, чем сталь, созданная обычным литьем.
Вязкость и износостойкость данной марки стали в значительной степени затрудняют ее обработку, что приводит к повышенному износу инструментов и абразивных лент. Все эти факторы, соответственно, сказываются на стоимости ножа, изготовленного из этой супер стали.
С какой целью к железу добавляются легирующие элементы? Объясняется это довольно просто: железо подвергается закалке только в соединении с углеродом, поэтому, для того чтобы получить ту или иную марку стали, к железу добавляется углерод в различных количествах.
Существует ряд элементов, которые облагораживают сталь и коренным образом меняют ее свойства.
Углерод придает стали жесткость и вместе с железом и другими элементами образует карбиды – чрезвычайно твердые метало-углеродистые соединения.
Хром придает сплаву коррозионную стойкость: при содержании хрома не менее 13% сталь становится нержавеющей. Кроме того, хром повышает твердость и износостойкость стали.
Марганец придает материалу клинков зернистую структуру, которая, в свою очередь, способствует прочности ножа или инструмента из стали.
Кремний, также как и марганец, при ковке клинка ножа используется для придания ему крепости.
Ванадий, так же, как и тантал, никель, молибден, кобальт и вольфрам, повышает износостойкость и жесткость стали.
Ниже приводится подробное описание популярных марок стали, используемых для производства клинков туристических и охотничьих ножей, топоров, тяпок и мачете, а также складных ножей.
Российские стали для производства ножей:
Сталь Х12МФ. Из стали изготавливают профилировочные ролики сложных форм, секции кузовных штампов сложных форм, сложные матрицы при формовке листового металла, эталонные шестерни, накатные плашки, волоки, матрицы и пуансоны вырубных просечных штампов со сложной конфигурацией рабочих. Сталь Х12МФ хорошо зарекомендовала себя в изготовлении клинков для ножей. Неприхотливая, но удобная в работе сталь для изготовления ножевого инструмента. Сталь х12МФ отлично держит заточку, обладает высокой прочностью, хорошо держит режущую кромку. При попадании в агрессивную среду может покрыться налетом или на клинке ножа могут появятся темные пятна, поэтому нож из стали Х12МФ требует ухода. Нужно отметить, что многие производители льют булат на основе Х12МФ.
Состав стали марки Х12МФ: Углерод (С) 1,45 – 1,65 %, Марганец (Mn) 0,15 – 0,45 %, Хром (Cr) 11 – 12,5 %, Кремний (Si) 0,10 – 0,40 %, Молибден (Мо) 0,4 – 0,6 %, Ванадий (V) 0,15 – 0,3 %, Никель (Ni) 0,35 %, Фосфор (Р) 0,03 %.
Типичная твердость стали для ножей из Х12МФ по шкале Роквелла: 60 – 62HRc.
Аналоги стали для ножей марки Х12МФ в других странах: SLD (Япония), X155CrMo12.1 (Германия), SKD-11 (Швеция), D2 (США).
Посмотреть ножи из Х12МФ
Сталь 95Х18. 95Х18 – высоколегированная нержавеющая сталь для ножевого производства, обладающая высокой твердостью, стойкостью режущей кромки, высокой коррозионной стойкостью. Сталь 95Х18 считается одним из лучших материалов для изготовления клинковых изделий. В целом – одна из лучших сталей, применяемых для производства ножей по соотношению цена-качество. Промышленное предназначение стали 95Х18 – детали, к которым предъявляются требования высокой прочности и износостойкости и работающие при температуре до 500С или подвергающиеся действию умеренных и агрессивных сред.
Состав стали марки 95Х18: Углерод (С) 0,90 – 1,00 %, Марганец (Mn) 0,80 %, Хром (Cr) 17 – 19 %, Кремний (Si) 0,80 %, Фосфор (Р) 0,025 %.
Типичная твердость стали для ножей из 95Х18 по шкале Роквелла: 57 – 59Hrc.
Аналоги стали для ножей марки 95Х18 в других странах: AUS-8 (Япония), X90CrMoV18/1L4112 (Германия), 123C26 (Швеция), 440B (США).
Посмотреть ножи из 95Х18
Сталь 110Х18МШД. Это нержавеющая сталь мартенситного класса. Российская сталь производимая методом электрошлакового (ЭШП) и вакуумно-дугового (ВДП) переплава, с соответствующей маркировкой: 110Х18М-Ш и 110Х18М-ШД. Эта сталь нашла применение в подшипниках специального назначения и в ответственном хирургическом инструменте, так как к ней предъявляются требования высокой прочности и износостойкости. Наличие вредных примесей, таких как сера и фосфор меньше по сравнению с другими сталями для ножевого производства. При использовании стали 110Х18 в клинках ножей достигается превосходное сочетание режущих и прочностных свойств и коррозионной стойкости.
Состав стали марки 110Х18МШД: Углерод (С) 1,10 – 1,20 %, Марганец (Mn) 0,10 – 0,50%, Хром (Cr) 16,5 – 18 %, Молибден (Мо) 3,0 %, Никель (Ni) 0,5 %.
Типичная твердость стали для ножей из 110Х18МШД по шкале Роквелла: 58 – 61Hrc.
Аналоги стали для ножей марки 110Х18МШД в других странах: SUS440C (Япония), X105CrMo17/1,4125 (Германия), 19C27 (Швеция), 440C Crusible Metals (USA).
Посмотреть ножи из 110Х18МШД.
Сталь 65X13. Высоколегированная коррозионно-стойкая сталь. Весьма распространенная сталь для производства недорогих ножей, режущего инструмента, кухонных ножей, пил, съемных лезвий, скальпелей, лезвий бритв. Изначальное её предназначение – режущий инструмент, кухонные ножи, пилы, съёмные лезвия, скальпели, лезвия бритв. Поскольку из неё часто делают скальпели и другие медицинские инструменты, её ещё часто называют “медицинской”. В общем, сталь 65Х13 – достаточно неплохой вариант для недорогого рабочего и подарочного ножа.
Состав стали марки 65X13: Углерод (С) 0,65 %, Марганец (Mn) 0,40 %, Хром (Cr) 13 – 15 %, Кремний (Si) 0,30 %, Молибден (Мо) 0,02 – 0,1 %, Ванадий (V) 0,02 – 0,10 %, Никель (Ni) 0,25 – 0,40 %.
Типичная твердость стали для ножей из 65X13 по шкале Роквелла: 56 – 58HRc.
Аналоги стали для ножей марки 65X13 в других странах: 440A (США), AUS6 (Япония), X55CrMo14 (Германия), AEB-L (Швеция).
Посмотреть ножи из 65Х13.
Сталь 9ХС. Инструментальная легированная сталь российского производства, используется для изготовления различного рода инструментов. Из стали 9ХС производят: сверла, развертки, метчики, плашки, гребенки, фрезы, машинные штемпели, клейма для холодных работ. Ответственные детали, материал которых должен обладать повышенной износостойкостью, усталостной прочностью при изгибе, кручении, контактном нагружении, а также упругими свойствами. Сталь 9ХС относительно недавно сыскала большую популярность в охотничьих ножах ручной ковки. Нож из кованой стали 9ХС обладает хорошими режущими качествами и отлично держит заточку.
Состав стали марки 9ХС: Углерод (С) 0,85-0,95 %, Марганец (Mn) 0,30-0,60 %, Хром (Cr) 0,95 – 1,25 %, Кремний (Si) 1,20-1,60 %, Молибден (Мо) 0,20 %, Ванадий (V) 0,15 %, Никель (Ni) 0,35 %, Фосфор (Р) 0,03 %, Вольфрам (W) 0,2 %
Типичная твердость стали для ножей из 9ХС по шкале Роквелла: 60 – 63HRc.
Посмотреть ножи из 9ХС.
Сталь ХВ5. Хромовольфрамовая инструментальная легированная сталь. ХВ5 – одна из самых твердых инструментальных сталей. Из-за повышенной твердости ХВ5 называют “алмазной сталью”. Применяется сталь ХВ5 для инструментов, работающих с малыми скоростями резания при обработке металлов повышенной твердости (отбеленного чугуна, стекла, фарфора), а также при срезании стружки малого сечения. Кроме того из этой стали получаются прочнейшие ножи , которые по свои характеристикам, режущим свойствам и твердости оставляют далеко позади ножи из других углеродистых и легированных сталей. При правильной термообработке клинок из алмазной стали может иметь твердость до 69-70 HRc.
Состав стали марки ХВ5: Углерод (С) 1,3-1,35 %, Марганец (Mn) 0,10-0,30 %, Хром (Cr) 0,4 – 0,7 %, Кремний (Si) 0,10-0,30 %, Ванадий (V) 0,2 %, Вольфрам (W) 5%
Типичная твердость стали для ножей из ХВ5 по шкале Роквелла: 63 – 67HRc.
Посмотреть ножи из ХВ5.
Сталь У10. Инструментальная углеродистая сталь. Используется для производства инструмента, работающего в условиях, не вызывающих разогрева режущей кромки. Из стали У10 производят: метчики ручные, рашпили, надфили, пилы для обработки древесины, матрицы для холодной штамповки, гладкие калибры, топоры. Сталь У10 можно отнести к «классическому» клинковому материалу.
Состав стали марки У10: Углерод (С) 1,16 – 1,23 %, Марганец (Mn) 0,17 – 0,28 %, Хром (Cr) 0,2 %, Кремний (Si) 0,17 – 0,33 %, %, Никель (Ni) 0,2 %, Фосфор (Р) 0,02 %,
Типичная твердость стали для ножей из У10 по шкале Роквелла: 59 – 61HRc.
Посмотреть ножи из У10.
Сталь У8. Инструментальная углеродистая сталь. Используется для производства инструмента, работающего в условиях, не вызывающих разогрева режущей кромки. Из стали У8 производят: фрезы, зенковки, стамески, долота, пилы продольные и дисковые, накатные ролики, керны, отвертки, комбинированные плоскогубцы, боковые кусачки, топоры. Сталь У8, как и другие марки стали У можно отнести к «классическому» клинковому материалу.
Состав стали марки У10: Углерод (С) 0,76 – 0,83%, Марганец (Mn) 0,17 – 0,28 %, Хром (Cr) 0,2 %, Кремний (Si) 0,17 – 0,33 %, %, Никель (Ni) 0,2 %, Фосфор (Р) 0,02 %,
Типичная твердость стали для ножей из У10 по шкале Роквелла: 58 – 60HRc.
Посмотреть ножи из У8.
Сталь 65Г. Пружинно-рессорная сталь, легированная марганцем. Из стали 65Г производят: пружины, рессоры, упорные шайбы, тормозные ленты, фрикционные диски, шестерни, фланцы, корпусы подшипников, зажимные и подающие цанги и другие детали, к которым предъявляются требования повышенной износостойкости, а также детали, работающие без ударных нагрузок. Сталь 65Г не стойка к коррозии, недолго держит режущую кромку, но обладает высокой ударной вязкостью. В основном из этой стали изготавливают метательные ножи.
Состав стали марки У10: Углерод (С) 0,62 – 0,7 %, Марганец (Mn) 0,9 – 1,2 %, Хром (Cr) 0,25 %, Кремний (Si) 0,17 – 0,33 %, %, Никель (Ni) 0,25 %, Фосфор (Р) 0,02 %,
Типичная твердость стали для ножей из 65Г по шкале Роквелла: 55 – 58HRc.
Аналоги стали для ножей марки 65Г в других странах: 1066, 1566, G15660 (США), 66Mn4, Ck67 (Германия).
Посмотреть ножи из 65Г.
Импортные стали для производства ножей:
Сталь UDDEHOLM ElMAX. Elmax Superclean — порошковая инструментальная коррозионно-стойкая сталь концерна Bohler Uddeholm. Сталь ELMAX довольно давно присутствует на рынке и достаточно популярна при производстве клинков для ножей. По стойкости эта сталь для ножей несколько уступает стали M390 и приближается по свойствам к стали CPM S30V. Elmax безусловно можно отнести к передовым мировым сталям, изготовляемым методом порошковой металлургии. Имея повышенную чистоту, вязкость и карбиды небольшого размера сталь Elmax прекрасно держит заточку, устойчива к агрессивным средам.
Состав стали марки ElMAX: Углерод (С) 1,72 %, Хром (Cr) 17,8 %, Кремний (Si) 0,8 %, Молибден (Мо) 0,99 %, Ванадий (V) 2,99 %, Никель (Ni) 0,15 %, Вольфрам (W) 0,11 %, добавки редкоземельных металлов.
Типичная твердость стали для ножей из ELMAX по шкале Роквелла: 60 – 61HRc.
Посмотреть ножи из ELMAX.
Сталь UDDEHOLM VANADIS 10. Vanadis 10 — известная порошковая сталь от концерна Bohler Uddeholm с высоким содержанием ванадия, обладающая уникальным сочетанием отличной абразивной износостойкости и хорошей устойчивости к образованию сколов. Эта сталь производится с использованием процесса порошковой металлургии, что обеспечивает очень низкое содержание неметаллических включений. Uddeholm Vanadis 10 обладает хорошей обрабатываемостью и полиpуемостью, что, в сочетании с хорошей pазмеpной стабильностью при термообработке, обеспечивает неоспоримые преимущества для изготовителей режущего инструмента.
Uddeholm Vanadis 10 – это сталь, легированная
хромом, молибденом и ванадием, и обладающая
следующими характеристиками: чрезвычайно высокой абразивной
износостойкостью, высокой прочностью на сжатие, очень хорошей сквозной пpокаливаемостью, хорошей вязкостью, очень хорошей стабильностью при закалке, хорошей устойчивостью к вторичному отпуску.
Ножи из Vanadis 10 отличает высокая стойкостью к абразивному воздействию, высокая ударная прочность и вязкость, повышенная устойчивостью к образованию трещин сколов и заминов. Режущая кромка клинка очень долго не садиться и нож отлично держит заточку.
Состав стали марки VANADIS 10: Углерод (С) 2,9 %, Хром (Cr) 8 %, Кремний (Si) 0,5 %, Молибден (Мо) 1,5 %, Ванадий (V) 9,8 %, Вольфрам (W) 0,33 %, добавки редкоземельных металлов.
Типичная твердость стали для ножей из VANADIS 10 по шкале Роквелла: 62 – 64HRc.
Посмотреть ножи из VANADIS 10.
Сталь BOHLER M390 MICROCLEAN. Это коррозионностойкая мартенситная хромистая сталь получаемая методом порошковой металлургии. Большое содержание маленьких хорошо диспергированных карбидов Cr и Vв основном материале, содержащем, по крайней мере 12% хрома, дает следующие преимущества: наивысшая коррозионная стойкость, оптимальная износостойкость, превосходная полируемость. Благодаря своему составу и технологиям порошковой металлургии ножи из стали Böhler M390 имеют очень агрессивный рез, высокую износостойкость и отличную коррозийную устойчивость.
Состав стали марки BÖHLER M390 MICROCLEAN.: Углерод (С) 1,9 %, Хром (Cr) 20 %, Кремний (Si) 0,7 %, Молибден (Мо) 1 %, Марганец (Mn) 0,3 %, Ванадий (V) 4 %, Вольфрам (W) 0,6 %, добавки редкоземельных металлов.
Типичная твердость стали для ножей из M390 по шкале Роквелла: 61 – 64HRc.
Посмотреть ножи из M390.
Сталь BOHLER N695. Это мартенситная, хромистая нержавеющая сталь с высокой твердостью, износостойкостью и хорошей коррозионной стойкостью. Сталь N695 производится с использованием электрошлакового переплава. Является хорошей сталью для ножей, которым необходимо иметь не только стойкую режущую кромку, но и способность выдерживать ударные и боковые нагрузки на поворот и на излом.
Содержание примесей и легирующих добавок в сплаве для ножей марки N 695: Углерод (С) 1,05%, Кремний (Si) 0,4 %, Хром (Cr) 17 %, Молибден (Мо) 0,5 %, Марганец (Mn) 0,4 %.
Типичная твердость стали для ножей из N695 по шкале Роквелла: 57 – 60HRc.
Аналоги стали для ножей марки N695 в других странах: 440C, Z100CD17, SUS 440C, X105CrMo17, 5618, 5630.
Посмотреть ножи из N695.
Сталь BOHLER K340. Холодноштамповая инструментальная сталь концерна Böhler Uddeholm. Производится с использованием метода электрошлакового переплава (ЭШП). ЭШП обеспечивает уменьшение количества микро и макро сегрегации, а также чистоту и гомогенность структуры. Преимущества стали K340: гомогенная структура по всему объему заготовки; равномерные и минимальные изменения размеров; высокая вязкость, обеспечивающая широкий спектр областей применения; повышенный предел прочности на сжатие, особенно важный для тяжелонагруженных инструментов; улучшенная обрабатываемость, благодаря гомогенной структуре.
Состав стали марки K340: Углерод (С) 1,1 %, Хром (Cr) 8,3 %, Кремний (Si) 0,9 %, Молибден (Мо) 2,1 %, Ванадий (V) 0,5 %, Марганец (Mn) 0,4 %, добавки редкоземельных металлов.
Типичная твердость стали для ножей из K340 по шкале Роквелла: 59 – 62HRc.
Посмотреть ножи из K340.
Сталь D2. Это высокоуглеродистая хромистая инструментальная штамповая сталь. Сталь D2 имеет высокую стойкость к износу, компрессионным нагрузкам и абразивным воздействиям. Это одна из лучших и известнейших мировых сталей для производства ножей. Из стали D2 изготавливают ножи известные кампании из США и Японии. Ножи из этой стали отлично держат режущую кромку и имеют высокую коррозионную стойкостью. После термообработки твердость клинка из стали D2 находится в пределах 60-62 HRC.
Ножи из D2 практически не ржавеют, но поскольку сталь немного не дотягивает до нержавеющей (от 13% хрома), рекомендуется протирать клинки ножей и не оставлять на долго во влажных местах.
Состав стали марки D2: Углерод (С) 1,55 %, Марганец (Mn) 0,35 %, Хром (Cr) 11 – 12,5 %, Кремний (Si) 0,45 %, Молибден (Мо) 0,8 %, Ванадий (V) 0,8 %.
Типичная твердость стали для ножей из D2 по шкале Роквелла: 59 – 62HRc.
Аналоги стали для ножей марки D2 в других странах: Х12МФ (Россия), SLD (Япония), X155CrMo12.1 (Германия), SKD-11 (Швеция).
Посмотреть ножи из D2.
Что такое твердость стали? (ч.1)
Понятие твердости металлов раньше было известно только выпускникам технических вузов, рабочим машиностроительных заводов и мастерам кузнечного дела. В обиход современного ножемана этот термин вошел вместе с принятием закона об оружии и ГОСТов, которые приводят признаки, на основании которых нож может быть отнесен к холодному оружию.
Одним из обязательных признаков, по которым то или иное изделие относится к холодному оружию является твердость стали из которой выполнен клинок ножа (или как это называется в ГОСТе — боевая часть холодного оружия). И начиная с этого момента, найфоманы в России начали потихоньку почитывать справочники в которых приводятся характеристики разных сталей, пояснения в различии порошковых и ламинированных сталей, ну и конечно показатели твердости стали, те самые заметные HRC.
Если один автолюбитель сможет спросить другого о том, сколько «кубиков в движке», то продвинутый найфоман, посмотрев на характеристики полевого ножа в которых указано «57-59 HRC» может на полном серьезе определить, что это модель хлипковата для бушкрафта и ей место на кухне.
Данная статья в простой и понятной форме расскажет о том, что же за зверь такой HRC, откуда от взялся и зачем он вообще нужен.
Интересный факт: На американских и европейских сайтах в числе параметров, которые указывают продавцы или производители крайне редко встречается такой параметр, как твердость стали.
Законодательно этот вопрос никак не регулируется, вот и не нужен этот параметр обычному неискушенному покупателю.
Итак, что же нам нужно знать о твердости металлов?
Человек издревле столкнулся с понятием твердости материалов. А также достаточно быстро понял, что различные материалы отличаются друг от друга по твердости и прочности. Если ударить палкой по камню, то палка либо сломается, либо отскочит. Если ударить камнем по палке, то палка сломается. Если кокос упадет с дерева на галечный пляж, то разобьется. А если долго и старательно бить кремнем по более мягкому камню, то вполне себе можно изготовить голову для каменного топора.
Постепенно, в процессе эволюции наши с вами предки поняли, что различные материалы имеют различную твердость, и в зависимости от этой твердости обладают или не обладают нужными свойствами. Так родился способ определения твердости материла, посредством сравнения его с неким эталоном.
Так, хороший плотник может определить степень усушки бревна постукивая по нему киянкой, выполненной из дерева более твердой породы. Гончар с помощью специального молоточка может определить степень готовности глиняной посуды. Вольно или невольно, каждый из нас хоть раз в жизни прибегал к аналогичному способу определения твердости предмета.
Однако, самым распространенным методом определения твердости материала до недавнего времени был склерометрический метод. Склерометрия представляет собой физический процесс, когда проверяемый материал царапает (или царапается) некий эталонный образец. Если проверяемый материла царапает эталон — значит проверяемый материал тверже.
Если проверяемый материал не может оставить следа на эталоне и при этом сам легко царапается эталоном — значит проверяемый материал имеет твердость меньше чем у эталона. Сейчас такая процедура кажется нам смешной, но до недавнего времени, это был единственный способ определить твердость материала. А как еще древние шумеры могли определить, что можно наносить надписи острой палочкой на почти засохшую глину?
Вопрос с определением твердости материалов (особенно камней и металлов) остро встал в конце XVIII и начале XIX веков, с развитием геологии и началом расцвета машиностроения.
Именно к этому времени относится появление известной всем физикам и археологам «шкалы Мооса». Однако, первым кто предложил измерять твердость металлов посредством их сравнения с эталоном был французский естествоиспытатель середины XVIII века Рене Антуан Реомюр.
Реомюр активно проводил эксперименты, связанные с плавлением и обработкой металлов и поэтому перед ним остро стоял вопрос определения различных характеристик тех сплавов, которые он получал в процессе своих изысканий.
Его идеи подхватил и развил немецкий естествоиспытатель и геолог Карл Фридрих Христиан Моос. В 1811-м году он придумал систему эталонного сравнения минералов, которая теперь носит его имя. Примерно до середины XX века это шкалой активно пользовались разведывательные геологические партии по всему миру.
Шкала Мооса представляет собой сравнительную таблицу в которой указаны различные по твердости известные минералы и указана их твердость измеряемая в критериях:
- Царапается ногтем;
- Царапается медью;
- Царапается стеклом;
- Царапает стекло;
- Обрабатывается только алмазом.
К самому мягкому эталонному минералу относится таль, к самому твердому минералу отнесен алмаз. Твердость талька по шкале Мооса составляет «1», твердость алмаза составляет «10». Между тальком и алмазом по мере возрастания твердости расположены: гипс (твердость 2), кальцит (твердость 3), флюорит (твердость 4), апатит (твердость 5), ортоклаз (твердость 6), кварц (твердость 7), топаз (твердость 8), корунд (твердость 9). Такой простой способ определения твердости минералов оказался незаменим в полевых условиях.
Помимо шкалы Мооса, существуют другие способы определения твердости материалов, которые получили активное развитие в конце XIX и в начале XX века. Обычно выделяют четыре самых известных способа определения твердости металлов:
- Метод Бринелля;
- Метод Виккерса;
- Метод Шора;
- Метод Роквелла.
Забегая вперед, заметим: все эти методы похожи между собой, так как основаны на вдавливании эталонного образца в поверхность металла. Различаются только форма эталона, сила давления, формула расчета величины.
Элемент, который вдавливается в поверхность металла, называется «индентор». В качестве индентора могут использоваться стальной шарик (метод Бринелля), алмазный конус (метод Роквелла), алмазная пирамидка (методы Виккерса и Шора).