ΠΠ°ΠΊ ΡΠ΄Π΅Π»Π°ΡΡ ΡΠ°ΠΌΠΎΠ΄Π΅Π»ΡΠ½ΡΠ΅ ΡΠΈΡΠΊΠΈ: 403 β ΠΠΎΡΡΡΠΏ Π·Π°ΠΏΡΠ΅ΡΡΠ½ β ΠΠ΅Π»Π°Π΅ΠΌ ΡΠΈΡΠΊΠΈ ΡΠ°ΠΌΠΎΡΡΠΎΡΡΠ΅Π»ΡΠ½ΠΎ ΠΈΠ· ΠΏΠΎΠ΄ΡΡΡΠ½ΡΡ ΡΡΠ΅Π΄ΡΡΠ² β ΡΠ°Π·Π½ΡΠ΅ Π²Π°ΡΠΈΠ°Π½ΡΡ
ΠΠ°ΡΠ°Π»Π»Π΅Π»ΡΠ½ΡΠ΅ ΡΠ»Π΅ΡΠ°ΡΠ½ΡΠ΅ ΡΠΈΡΠΊΠΈ ΠΈΠ· ΡΠ²Π΅Π»Π»Π΅ΡΠ° ΡΠ²ΠΎΠΈΠΌΠΈ ΡΡΠΊΠ°ΠΌΠΈ
ΠΠ΄ΡΠ°Π²ΡΡΠ²ΡΠΉΡΠ΅, ΡΠ²Π°ΠΆΠ°Π΅ΠΌΡΠ΅ ΡΠΈΡΠ°ΡΠ΅Π»ΠΈ ΠΈΒ ΡΠ°ΠΌΠΎΠ΄Π΅Π»ΠΊΠΈΠ½Ρ!Π£Β ΠΌΠ½ΠΎΠ³ΠΈΡ ΠΈΡ Β ΠΠ°Ρ ΠΈΠΌΠ΅Π΅ΡΡΡ Π²Β ΡΠ°ΡΠΏΠΎΡΡΠΆΠ΅Π½ΠΈΠΈ ΠΌΠ°ΡΡΠ΅ΡΡΠΊΠ°Ρ, Π»ΠΈΠ±ΠΎ ΠΎΠ±ΠΎΡΡΠ΄ΠΎΠ²Π°Π½Π½ΡΠΉ Π³Π°ΡΠ°ΠΆ. ΠΒ ΠΎΠ΄Π½ΠΈΠΌ ΠΈΠ·Β ΡΠ°ΠΌΡΡ Π³Π»Π°Π²Π½ΡΡ ΠΈΠ½ΡΡΡΡΠΌΠ΅Π½ΡΠΎΠ² ΡΠ²Π»ΡΡΡΡΡ ΡΠΈΡΠΊΠΈ. ΠΒ ΡΡΠΎΠΈΠΌΠΎΡΡΡ Π΄Π°ΠΆΠ΅ ΡΡΠ°ΡΠ΅Π½ΡΠΊΠΈΡ , Π±ΡΠ²ΡΠΈΡ Π²Β ΡΠΏΠΎΡΡΠ΅Π±Π»Π΅Π½ΠΈΠΈ ΡΠΈΡΠΊΠΎΠ² Π²Π΅ΡΡΠΌΠ° Π²ΡΡΠΎΠΊΠ°.
ΠΒ Π΄Π°Π½Π½ΠΎΠΉ ΡΡΠ°ΡΡΠ΅, Π°Π²ΡΠΎΡ YouTube ΠΊΠ°Π½Π°Π»Π° Β«Workshop DiyΒ» ΡΠ°ΡΡΠΊΠ°ΠΆΠ΅Ρ ΠΠ°ΠΌ, ΠΊΠ°ΠΊ ΠΎΠ½Β ΠΈΠ·Π³ΠΎΡΠΎΠ²ΠΈΠ» ΠΏΡΠΎΡΡΡΠ΅ ΠΏΠ°ΡΠ°Π»Π»Π΅Π»ΡΠ½ΡΠ΅ ΡΠ»Π΅ΡΠ°ΡΠ½ΡΠ΅ ΡΠΈΡΠΊΠΈ ΠΈΠ·Β ΡΠ²Π΅Π»Π»Π΅ΡΠ°, ΠΈΒ Π΄ΡΡΠ³ΠΈΡ
Π΄ΠΎΡΡΡΠΏΠ½ΡΡ
ΠΌΠ°ΡΠ΅ΡΠΈΠ°Π»ΠΎΠ².

ΠΠ°ΡΠ΅ΡΠΈΠ°Π»Ρ.
βΒ Π‘ΡΠ°Π»ΡΠ½Π°Ρ ΠΏΠ»Π°ΡΡΠΈΠ½Π°
βΒ Π¨Π²Π΅Π»Π»Π΅Ρ
βΒ Π‘ΡΠ°Π»ΡΠ½ΡΠ΅ ΡΠ³ΠΎΠ»ΠΊΠΈ, ΠΊΠ²Π°Π΄ΡΠ°Ρ
βΒ Π‘ΡΠ°Π»ΡΠ½Π°Ρ ΡΠΏΠΈΠ»ΡΠΊΠ°, ΠΏΡΡΡΠΎΠΊ
βΒ ΠΠΎΠ»ΡΡ, Π³Π°ΠΉΠΊΠΈ, ΡΠ°ΠΉΠ±Ρ
βΒ ΠΡΡΠΎΠ·ΠΎΠ»ΡΠ½Π°Ρ ΠΊΡΠ°ΡΠΊΠ°
βΒ Π Π΅Π·ΠΈΠ½ΠΎΠ²ΡΠ΅ ΠΊΠΎΠ»ΡΡΠ°
βΒ ΠΠΈΡΠΎΠ».

ΠΠ½ΡΡΡΡΠΌΠ΅Π½ΡΡ, ΠΈΡΠΏΠΎΠ»ΡΠ·ΠΎΠ²Π°Π½Π½ΡΠ΅ Π°Π²ΡΠΎΡΠΎΠΌ.
βΒ ΠΠΎΠ»Π³Π°ΡΠΊΠ°
βΒ ΠΡΡΠ΅Π·Π½ΠΎΠΉ ΠΈΒ Π·Π°ΡΠΈΡΡΠ½ΠΎΠΉ Π΄ΠΈΡΠΊΠΈ
βΒ Π‘ΡΡΡΠ±ΡΠΈΠ½Ρ
βΒ Π¨ΡΡΡΠΏΠΎΠ²Π΅ΡΡ, ΡΠ²Π΅ΡΠ»Π° ΠΏΠΎΒ ΠΌΠ΅ΡΠ°Π»Π»Ρ
βΒ Π‘Π²Π°ΡΠΎΡΠ½ΡΠΉ Π°ΠΏΠΏΠ°ΡΠ°Ρ
βΒ Π£Π³ΠΎΠ»ΡΠ½ΠΈΠΊ, ΠΌΠ°ΡΠΊΠ΅Ρ, ΡΡΠ»Π΅ΡΠΊΠ°.
ΠΡΠΎΡΠ΅ΡΡ ΠΈΠ·Π³ΠΎΡΠΎΠ²Π»Π΅Π½ΠΈΡ.
ΠΠ»Ρ Π½ΠΈΠΆΠ½Π΅ΠΉ ΡΠ°ΡΡΠΈ ΠΎΡΠ½ΠΎΠ²Π°Π½ΠΈΡ ΠΌΠ°ΡΡΠ΅Ρ ΡΠ΅ΡΠΈΠ» ΠΈΡΠΏΠΎΠ»ΡΠ·ΠΎΠ²Π°ΡΡ Π²ΠΎΡ ΡΠ°ΠΊΡΡ ΡΡΠ°Π»ΡΠ½ΡΡ ΠΏΠ»Π°ΡΡΠΈΠ½Ρ, ΠΈΠΌΠ΅ΡΡΡΡ Π·Π°ΠΊΡΡΠ³Π»Π΅Π½Π½ΡΠΉ ΠΊΡΠ°ΠΉ.
Π‘Π°ΠΌΠΎ ΠΎΡΠ½ΠΎΠ²Π°Π½ΠΈΠ΅ Π±ΡΠ΄Π΅Ρ ΠΈΠΌΠ΅ΡΡ ΡΠ°Π·Π±ΠΎΡΠ½ΡΡ ΠΊΠΎΠ½ΡΡΡΡΠΊΡΠΈΡ, ΠΏΠΎΡΡΠΎΠΌΡ Π°Π²ΡΠΎΡ ΠΈΠ·Π³ΠΎΡΠ°Π²Π»ΠΈΠ²Π°Π΅Ρ Π΄Π²Π΅ Π±ΠΎΠΊΠΎΠ²ΡΠ΅ Π½Π°ΠΏΡΠ°Π²Π»ΡΡΡΠΈΠ΅, ΠΈΠ·Β ΡΠ³ΠΎΠ»ΠΊΠ°, Π·Π°ΡΠ΅ΠΌ Π·Π°ΠΊΡΡΠ³Π»ΡΠ΅Ρ ΠΊΡΠ°Ρ.
ΠΠ°ΠΏΡΠ°Π²Π»ΡΡΡΠΈΠ΅ ΡΠΈΠΊΡΠΈΡΡΡΡΡΡ ΠΊΒ ΠΎΡΠ½ΠΎΠ²Π°Π½ΠΈΡ Π³Π΅ΠΉΡΠ΅ΡΠ½ΡΠΌ Π·Π°Ρ Π²Π°ΡΠΎΠΌ, ΠΈΒ ΡΠ²Π΅ΡΠ»ΠΈΡΡΡ ΠΏΠΎΒ ΠΏΠ°ΡΠ΅ ΠΎΡΠ²Π΅ΡΡΡΠΈΠΉ Π²Β Π½ΠΈΡ ΠΈΒ ΠΎΡΠ½ΠΎΠ²Π°Π½ΠΈΠΈ. ΠΠ½ΠΈ ΠΏΡΠ΅Π΄Π½Π°Π·Π½Π°ΡΠ΅Π½Ρ Π΄Π»Ρ ΠΊΡΠ΅ΠΏΠ΅ΠΆΠ½ΡΡ Π±ΠΎΠ»ΡΠΎΠ².
Π¨Π²Π΅Π»Π»Π΅Ρ ΡΡΡΠ°Π½Π°Π²Π»ΠΈΠ²Π°Π΅ΡΡΡ ΠΌΠ΅ΠΆΠ΄Ρ Π½Π°ΠΏΡΠ°Π²Π»ΡΡΡΠΈΠΌΠΈ, ΠΈΒ Π²ΡΡΠ΅Π·Π°Π΅ΡΡΡ ΡΡΠ°Π»ΡΠ½Π°Ρ ΠΏΠ»Π°ΡΡΠΈΠ½Π°, ΠΊΠΎΡΠΎΡΠ°Ρ Π±ΡΠ΄Π΅Ρ Π²Π΅ΡΡ Π½Π΅ΠΉ ΡΠ°ΡΡΡΡ ΡΡΠ΅ΠΌΠ½ΠΎΠ³ΠΎ ΠΎΡΠ½ΠΎΠ²Π°Π½ΠΈΡ. ΠΠ°Π»Π΅Π΅ ΠΏΠ»Π°ΡΡΠΈΠ½Π° ΠΏΡΠΈΡ Π²Π°ΡΡΠ²Π°Π΅ΡΡΡ ΠΊΒ Π½Π°ΠΏΡΠ°Π²Π»ΡΡΡΠΈΠΌ.
ΠΠΎΡΠ»Π΅ ΠΏΡΠΎΠ²Π°ΡΠΈΠ²Π°Π½ΠΈΡ ΠΈΒ Π·Π°ΡΠΈΡΡΠΊΠΈ ΡΠ²ΠΎΠ², Π°Π²ΡΠΎΡ ΠΏΡΠΎΠ²Π΅ΡΡΠ΅Ρ Π½Π°Π»ΠΈΡΠΈΠ΅ Π»ΡΡΡΠ° ΠΌΠ΅ΠΆΠ΄Ρ ΡΠ²Π΅Π»Π»Π΅ΡΠΎΠΌ ΠΈΒ ΠΎΡΠ½ΠΎΠ²ΠΎΠΉ.

ΠΠ°ΡΡΠ΅Ρ Π²ΡΡΠ΅Π·Π°Π΅Ρ Π΄Π²Π΅ ΠΏΠ»Π°ΡΡΠΈΠ½Ρ, ΠΎΠ΄Π½Π° ΠΈΠ·Β Π½ΠΈΡ Π±ΡΠ΄Π΅Ρ ΡΡΠΎΠΏΠΎΡΠ½ΠΎΠΉ, Π²Β Π½Π΅ΠΉ Π²ΡΡΠ²Π΅ΡΠ»ΠΈΠ²Π°Π΅ΡΡΡ ΠΎΡΠ²Π΅ΡΡΡΠΈΠ΅ Π΄Π»Ρ Π²ΠΈΠ½ΡΠ°.
ΠΠ°Β ΡΡΠ°Π»ΡΠ½ΡΡ ΡΠΏΠΈΠ»ΡΠΊΡ Π½Π°ΠΊΡΡΡΠΈΠ²Π°ΡΡΡΡ Π½Π΅ΡΠΊΠΎΠ»ΡΠΊΠΎ Π³Π°Π΅ΠΊ, ΠΈΒ ΠΎΠ½ΠΈ ΠΏΡΠΈΠ²Π°ΡΠΈΠ²Π°ΡΡΡΡ ΠΊΠΎΒ Π²ΡΠΎΡΠΎΠΉ ΠΏΠ»Π°ΡΡΠΈΠ½Π΅.
ΠΡΠΎΠ²Π΅ΡΠΈΠ² ΡΠΎΠΎΡΠ½ΠΎΡΡΡ Π²ΠΈΠ½ΡΠ° ΠΈΒ ΡΠ²Π΅Π»Π»Π΅ΡΠ°, ΠΏΠ»Π°ΡΡΠΈΠ½Π° ΡΒ Π³Π°ΠΉΠΊΠ°ΠΌΠΈ ΠΏΡΠΈΠ²Π°ΡΠΈΠ²Π°Π΅ΡΡΡ ΠΊΒ Π½ΠΈΠΆΠ½Π΅ΠΉ ΡΠ°ΡΡΠΈ ΠΎΡΠ½ΠΎΠ²Π°Π½ΠΈΡ.

ΠΡΠ°ΠΊ, ΠΎΡΠ½ΠΎΠ²Π½ΡΠ΅ Π΄Π΅ΡΠ°Π»ΠΈ Π³ΠΎΡΠΎΠ²Ρ, ΠΌΠ°ΡΡΠ΅Ρ Π΄Π΅Π»Π°Π΅Ρ ΠΊΠΎΠ½ΡΡΠΎΠ»ΡΠ½ΡΡ ΡΠ±ΠΎΡΠΊΡ ΠΈΒ ΠΏΡΠΎΠ²Π΅ΡΠΊΡ ΡΠ°Π±ΠΎΡΠΎΡΠΏΠΎΡΠΎΠ±Π½ΠΎΡΡΠΈ.
ΠΠ΅ΡΠ΅Π΄Π½ΠΈΠ΅ ΡΠ°ΡΡΠΈ Π΄Π»Ρ Π³ΡΠ±ΠΎΠΊ Π²ΡΡΠ΅Π·Π°Π½Ρ ΠΈΠ·Β ΡΠΎΠ»ΡΡΠΎΠΉ ΡΡΠ°Π»ΡΠ½ΠΎΠΉ ΠΏΠ»Π°ΡΡΠΈΠ½Ρ, ΡΠ°ΠΊΠΎΠΉΒ ΠΆΠ΅ ΠΊΠ°ΠΊ ΠΈΒ Π²Β ΠΎΡΠ½ΠΎΠ²Π°Π½ΠΈΠΈ.

Π’Π΅ΠΏΠ΅ΡΡ ΠΎΠ½Β Π½Π°ΡΠΈΠ½Π°Π΅Ρ ΡΠ²Π°ΡΠΊΡ ΠΎΠ΄Π½ΠΎΠΉ ΠΈΠ·Β Π³ΡΠ±ΠΎΠΊ, ΠΈΒ ΠΏΡΠΎΠ²Π΅ΡΡΠ΅Ρ ΠΏΡΠ°Π²ΠΈΠ»ΡΠ½ΠΎΠ΅ ΡΠ°ΡΠΏΠΎΠ»ΠΎΠΆΠ΅Π½ΠΈΠ΅ ΠΏΠ»ΠΎΡΠΊΠΎΡΡΠ΅ΠΉ.
ΠΠ΅ΠΏΠ΅ΡΡΠΎΠΊ Π·Π°Π³ΠΈΠ±Π°Π΅ΡΡΡ ΠΏΡΠΈ ΠΏΠΎΠΌΠΎΡΠΈ ΠΌΠΎΠ»ΠΎΡΠΊΠ°, ΠΈΒ ΠΏΡΠΎΠ²Π°ΡΠΈΠ²Π°Π΅ΡΡΡ.
ΠΠ΅ΡΠ²ΠΎΠΉ Π°Π²ΡΠΎΡ ΡΠ΅ΡΠ°Π΅Ρ ΠΏΡΠΈΠ²Π°ΡΠΈΡΡ ΠΊΒ ΡΠ²Π΅Π»Π»Π΅ΡΡ ΠΏΠΎΠ΄Π²ΠΈΠΆΠ½ΡΡ Π³ΡΠ±ΠΊΡ.


Π‘ΠΎΠ΅Π΄ΠΈΠ½ΡΠ΅Ρ ΠΏΠ»ΠΎΡΠΊΠΎΡΡΠΈ Π³ΡΠ±ΠΎΠΊ ΠΌΠ΅ΠΆΠ΄Ρ ΡΠΎΠ±ΠΎΠΉ, ΠΈΒ ΠΏΡΠΈΠ²Π°ΡΠΈΠ²Π°Π΅Ρ Π½Π΅ΠΏΠΎΠ΄Π²ΠΈΠΆΠ½ΡΡ Π³ΡΠ±ΠΊΡ ΠΊΒ ΠΎΡΠ½ΠΎΠ²Π°Π½ΠΈΡ. Π’Π°ΠΊ ΠΎΠ½Β Ρ ΠΎΡΠ΅Ρ Π΄ΠΎΠ±ΠΈΡΡΡΡ ΠΌΠ°ΠΊΡΠΈΠΌΠ°Π»ΡΠ½ΠΎΠΉ ΡΠΎΡΠ½ΠΎΡΡΠΈ.
ΠΠ·Β ΡΡΠ°Π»ΡΠ½ΠΎΠ³ΠΎ Π»ΠΈΡΡΠ° Π²ΡΡΠ΅Π·Π°ΡΡΡΡ Π΄Π΅ΡΠ°Π»ΠΈ Π΄Π»Ρ ΠΏΡΠΈΠΆΠΈΠΌΠ½ΡΡ ΠΏΠ»Π°ΡΡΠΈΠ½, Π²Β Π½ΠΈΡ Π²ΡΡΠ²Π΅ΡΠ»ΠΈΠ²Π°ΡΡΡΡ ΠΎΡΠ²Π΅ΡΡΡΠΈΡ. ΠΠ°Β Π΄Π²ΡΡ ΠΏΠ»Π°ΡΡΠΈΠ½Π°Ρ Π²Β ΠΎΡΠ²Π΅ΡΡΡΠΈΡΡ Π½Π°ΡΠ΅Π·Π°Π΅ΡΡΡ ΡΠ΅Π·ΡΠ±Π° Π΄Π»Ρ ΠΏΡΠΈΠΆΠΈΠΌΠ½ΡΡ Π²ΠΈΠ½ΡΠΎΠ², Π°Β Π²Β Π΄Π²ΡΡ ΠΎΡΡΠ°Π²ΡΠΈΡ ΡΡ Π·Π΅Π½ΠΊΡΡΡΡΡ ΠΎΡΠ²Π΅ΡΡΡΠΈΡ.


ΠΡΠ°ΠΊ, Π°Π²ΡΠΎΡ ΡΡΡΠ³ΠΈΠ²Π°Π΅Ρ Π²ΠΈΠ½ΡΠΎΠΌ ΠΊΠΎΠ½ΡΡΡΡΠΊΡΠΈΡ, ΠΈΒ ΠΏΡΠΈΠ²Π°ΡΠΈΠ²Π°Π΅Ρ ΠΏΠ»Π°ΡΡΠΈΠ½Ρ ΡΒ ΡΠ΅Π·ΡΠ±ΠΎΠΉ ΠΊΒ Π²Π΅ΡΡ Π½Π΅ΠΉ ΡΠ°ΡΡΠΈ Π³ΡΠ±ΠΎΠΊ.


ΠΠΎΡΠ»Π΅ Π²ΡΠ΅Ρ ΡΠ²Π°ΡΠΎΡΠ½ΡΡ ΡΠ°Π±ΠΎΡ ΡΠ²Ρ ΠΈΒ ΠΏΠΎΠ²Π΅ΡΡ Π½ΠΎΡΡΠΈ Π΄Π΅ΡΠ°Π»Π΅ΠΉ Π·Π°ΡΠΈΡΠ°ΡΡΡΡ Π»Π΅ΠΏΠ΅ΡΡΠΊΠΎΠ²ΡΠΌ ΡΠ»ΠΈΡΠΎΠ²Π°Π»ΡΠ½ΡΠΌ Π΄ΠΈΡΠΊΠΎΠΌ.

ΠΠΎΡ Π²Β ΡΠ°ΠΊΠΎΠΉ Π³Π°ΠΉΠΊΠ΅ ΠΌΠ°ΡΡΠ΅Ρ Π²ΡΡΠ²Π΅ΡΠ»ΠΈΠ» ΠΎΡΠ²Π΅ΡΡΡΠΈΠ΅ Π΄Π»Ρ ΡΡΡΠ°Π³Π°, ΠΈΒ ΠΏΡΠΈΠ²Π°ΡΠΈΠ» Π΅Π΅Β ΠΊΒ ΠΊΡΠ°Ρ Π²ΠΈΠ½ΡΠ°.
ΠΒ Π²ΠΎΡ ΡΡΠ° ΠΏΠ»ΠΎΡΠΊΠΎΡΡΡ Π±ΡΠ΄Π΅Ρ ΡΠ»ΡΠΆΠΈΡΡ Π½Π΅Π±ΠΎΠ»ΡΡΠΎΠΉ Π½Π°ΠΊΠΎΠ²Π°Π»ΡΠ½Π΅ΠΉ.

ΠΠ°Π»Π΅Π΅ Π΄Π΅ΡΠ°Π»ΠΈ ΠΎΠΊΡΠ°ΡΠΈΠ²Π°ΡΡΡΡ Π°ΡΡΠΎΠ·ΠΎΠ»ΡΠ½ΠΎΠΉ ΠΊΡΠ°ΡΠΊΠΎΠΉ, ΠΎΠ΄Π½Π°ΠΊΠΎ Π½Π΅Β ΠΏΠΎΒ Π²ΡΠ΅ΠΌ ΠΏΠΎΠ²Π΅ΡΡ Π½ΠΎΡΡΡΠΌ.

ΠΠ°Β Π΄Π²ΡΡ ΡΡΠ΅ΠΌΠ½ΡΡ ΠΏΡΠΈΠΆΠΈΠΌΠ½ΡΡ ΠΏΠ»Π°ΡΡΠΈΠ½Π°Ρ Π½Π°Π½ΠΎΡΠΈΡΡΡ ΡΠ°Π·ΠΌΠ΅ΡΠΊΠ°, ΠΈΒ Π½Π°ΡΠ΅Π·Π°Π΅ΡΡΡ Π΄ΠΈΠ°Π³ΠΎΠ½Π°Π»ΡΠ½Π°Ρ Π½Π°ΡΠ΅ΡΠΊΠ°.
ΠΠΎΡΠ»Π΅ ΡΠ»ΠΈΡΠΎΠ²ΠΊΠΈ ΠΎΠ½ΠΈ ΠΏΡΠΈΠΎΠ±ΡΠ΅ΡΠ°ΡΡ Π·Π½Π°ΠΊΠΎΠΌΡΠΉ Π²ΡΠ΅ΠΌ Π²ΠΈΠ΄.
ΠΡΠ°ΠΊ, Π²ΡΠ΅ Π΄Π΅ΡΠ°Π»ΠΈ Π³ΠΎΡΠΎΠ²Ρ, ΠΈΒ Π·Π΄Π΅ΡΡ Π²ΠΈΠ΄Π½ΠΎ, ΠΊΠ°ΠΊΠΈΠ΅ ΠΈΠ·Β ΠΏΠΎΠ²Π΅ΡΡ Π½ΠΎΡΡΠ΅ΠΉ ΠΌΠ°ΡΡΠ΅Ρ ΡΠΏΠ΅ΡΠΈΠ°Π»ΡΠ½ΠΎ Π½Π΅Β ΠΎΠΊΡΠ°ΡΠΈΠ²Π°Π».
ΠΒ Π²Π΅ΡΡΡΠ°ΠΊΠ΅ ΠΎΠ½Β ΠΏΡΠΎΡΠ²Π΅ΡΠ»ΠΈΠ» Π½Π΅ΠΎΠ±Ρ ΠΎΠ΄ΠΈΠΌΡΠ΅ ΠΎΡΠ²Π΅ΡΡΡΠΈΡ Π΄Π»Ρ ΠΊΡΠ΅ΠΏΠ΅ΠΆΠ½ΡΡ Π±ΠΎΠ»ΡΠΎΠ². ΠΠΌΠΈ Π±ΡΠ΄Π΅Ρ ΠΎΠ΄Π½ΠΎΠ²ΡΠ΅ΠΌΠ΅Π½Π½ΠΎ ΡΡΡΠ½ΡΡΠΎ ΠΌΠ΅ΠΆΠ΄Ρ ΡΠΎΠ±ΠΎΠΉ ΠΎΡΠ½ΠΎΠ²Π°Π½ΠΈΠ΅, ΠΈΒ ΡΠΈΡΠΊΠΈ Π·Π°ΠΊΡΠ΅ΠΏΠ»Π΅Π½Ρ ΠΊΒ ΡΡΠΎΠ»Ρ.
ΠΠ²ΡΠΎΡ Π²ΡΡΠ°Π²ΠΈΠ» ΡΡΡΠ°Π³ Π²Β Π³ΠΎΠ»ΠΎΠ²ΠΊΡ Π²ΠΈΠ½ΡΠ°, ΠΈΒ Π½Π°Π½Π΅Ρ ΡΠΌΠ°Π·ΠΊΡ Π½Π°Β ΡΠ΅Π·ΡΠ±Ρ.


ΠΠ΅ΡΠ΅Π΄ Π²ΠΊΡΡΡΠΈΠ²Π°Π½ΠΈΠ΅ΠΌ Π²ΠΈΠ½ΡΠ° Π²Β Π³Π°ΠΉΠΊΠΈ ΠΎΡΠ½ΠΎΠ²Π°Π½ΠΈΡ, Π°Π²ΡΠΎΡ ΡΠ΄Π΅Π»Π°Π» Π²Β ΡΠ°ΠΊΠΎΠΉΒ ΠΆΠ΅ Π³Π°ΠΉΠΊΠ΅ Π΄Π²Π° ΠΎΡΠ²Π΅ΡΡΡΠΈΡ, ΠΈΒ Π½Π°ΡΠ΅Π·Π°Π» Π²Β Π½ΠΈΡ ΡΠ΅Π·ΡΠ±Ρ. ΠΠ°Β Π²ΠΈΠ½Ρ Π½Π°Π΄Π΅Π²Π°ΡΡΡΡ ΡΠ°ΠΉΠ±Ρ ΡΒ Π΄Π²ΡΡ ΡΡΠΎΡΠΎΠ½, Π°Β ΡΡΠ° Π³Π°ΠΉΠΊΠ° Π±ΡΠ΄Π΅Ρ ΡΠ΄Π΅ΡΠΆΠΈΠ²Π°ΡΡ Π²ΠΈΠ½Ρ Π²Β ΡΡΠΎΠΏΠΎΡΠ½ΠΎΠΉ ΠΏΠ»Π°ΡΡΠΈΠ½Π΅.
ΠΡΠ°ΠΊ, ΠΌΠ°ΠΊΡΠΈΠΌΠ°Π»ΡΠ½ΠΎΠ΅ ΡΠ°Π±ΠΎΡΠ΅Π΅ ΡΠ°ΡΡΡΠΎΡΠ½ΠΈΠ΅ ΠΌΠ΅ΠΆΠ΄Ρ Π³ΡΠ±ΠΊΠ°ΠΌΠΈ ΡΠΎΡΡΠ°Π²ΠΈΠ»ΠΎ ΡΡΡΡ Π±ΠΎΠ»Π΅Π΅ 200Β ΠΌΠΌ.

ΠΠ°ΠΆΠ°Π² ΠΏΡΠΎΡΠΈΠ»ΡΠ½ΡΡ ΡΡΡΠ±Ρ Π²Β ΡΠΈΡΠΊΠ°Ρ , Π°Π²ΡΠΎΡ ΠΏΡΠΎΠ²Π΅ΡΡΠ΅Ρ ΠΈΡ Β Π½Π°Β Π½Π°Π΄Π΅ΠΆΠ½ΠΎΡΡΡ, ΠΎΠ½ΠΈ Π²ΡΠ΄Π΅ΡΠΆΠΈΠ²Π°ΡΡ Π΄Π°ΠΆΠ΅ Π΅Π³ΠΎ Π²Π΅Ρ.

ΠΡΠ° Π½Π΅Π±ΠΎΠ»ΡΡΠ°Ρ ΠΏΠ»ΠΎΡΠ°Π΄ΠΊΠ° Π±ΡΠ΄Π΅Ρ ΡΠ»ΡΠΆΠΈΡΡ Π½Π΅Π±ΠΎΠ»ΡΡΠΎΠΉ Π½Π°ΠΊΠΎΠ²Π°Π»ΡΠ½Π΅ΠΉ. ΠΠΎΠ½Π΅ΡΠ½ΠΎ, Π½Π°Β Π½Π΅ΠΉ ΠΊΠΎΠ²Π°ΡΡ ΠΏΠΎΠ΄ΠΊΠΎΠ²Ρ Π½Π΅Π»ΡΠ·Ρ, Π°Β Π΄Π»Ρ Π½Π΅Π±ΠΎΠ»ΡΡΠΈΡ Π΄Π΅ΡΠ°Π»Π΅ΠΉ Π²ΠΏΠΎΠ»Π½Π΅ ΡΠ³ΠΎΠ΄ΠΈΡΡΡ.

Π’Π°ΠΊΠΆΠ΅ ΠΌΠ°ΡΡΠ΅Ρ ΡΠ΄Π΅Π»Π°Π» Π½Π΅Π±ΠΎΠ»ΡΡΡΡ Π΄ΠΎΡΠ°Π±ΠΎΡΠΊΡ ΡΡΡΠ°Π³Π°, ΠΎΠ½Β ΠΏΠ»ΠΎΡΠ½ΠΎ Π½Π°Π΄Π΅Π» Π½Π°Β Π½Π΅Π³ΠΎ Π΄Π²Π΅ ΡΠ΅Π·ΠΈΠ½ΠΊΠΈ ΡΒ Π΄Π²ΡΡ ΡΡΠΎΡΠΎΠ½ ΠΎΡΒ Π³ΠΎΠ»ΠΎΠ²ΠΊΠΈ Π²ΠΈΠ½ΡΠ°. ΠΠ½ΠΈ ΠΏΠΎΠ·Π²ΠΎΠ»ΡΡΡ ΡΠΈΠΊΡΠΈΡΠΎΠ²Π°ΡΡ ΡΡΡΠ°Π³ ΠΊΠ°ΠΊ Π²Β ΠΊΡΠ°ΠΉΠ½Π΅ΠΌ ΠΏΠΎΠ»ΠΎΠΆΠ΅Π½ΠΈΠΈ, ΡΡΠΎ Π½Π΅ΠΎΠ±Ρ ΠΎΠ΄ΠΈΠΌΠΎ Π΄Π»Ρ ΡΠΎΠ·Π΄Π°Π½ΠΈΡ ΠΌΠ°ΠΊΡΠΈΠΌΠ°Π»ΡΠ½ΠΎΠ³ΠΎ ΠΏΡΠΈΠΆΠΈΠΌΠ½ΠΎΠ³ΠΎ ΡΡΠΈΠ»ΠΈΡ. ΠΒ ΡΠ°ΠΊΠΆΠ΅ ΠΌΠΎΠΆΠ½ΠΎ Π·Π°ΡΠΈΠΊΡΠΈΡΠΎΠ²Π°ΡΡ ΡΡΡΠ°Π³ Π²Β ΡΠ΅Π½ΡΡΠ°Π»ΡΠ½ΠΎΠΌ ΠΏΠΎΠ»ΠΎΠΆΠ΅Π½ΠΈΠΈ, ΡΡΠΎ ΡΠ΄ΠΎΠ±Π½ΠΎ Π΄Π»Ρ Π±ΡΡΡΡΠΎΠ³ΠΎ Π²ΡΠ°ΡΠ΅Π½ΠΈΡ.
ΠΠΎΡ ΡΠ°ΠΊΠΈΠ΅ ΠΊΡΠ°ΡΠΈΠ²ΡΠ΅, ΠΈΒ Π΄ΠΎΡΡΠ°ΡΠΎΡΠ½ΠΎ ΡΠ΅ΡΡΠ΅Π·Π½ΡΠ΅ ΠΏΠ°ΡΠ°Π»Π»Π΅Π»ΡΠ½ΡΠ΅ ΡΠΈΡΠΊΠΈ ΠΏΠΎΠ»ΡΡΠΈΠ»ΠΈΡΡ ΡΒ Π°Π²ΡΠΎΡΠ°. ΠΡΠΈ ΠΆΠ΅Π»Π°Π½ΠΈΠΈ, ΠΈΡ Β ΠΌΠΎΠΆΠ½ΠΎ Π±ΡΠ΄Π΅Ρ ΡΠ΄Π΅Π»Π°ΡΡ ΠΏΠΎΠ²ΠΎΡΠΎΡΠ½ΡΠΌΠΈ, Π΄ΠΎΠ±Π°Π²ΠΈΠ² ΠΊΒ ΠΎΡΠ½ΠΎΠ²Π°Π½ΠΈΡ ΠΏΠΎΠ²ΠΎΡΠΎΡΠ½ΡΠΉ ΡΡΠΎΠ». ΠΡΠΎΠΌΠ΅ ΡΠΎΠ³ΠΎ, Π°Π²ΡΠΎΡ Π΄Π΅Π»Π°Π» ΠΎΡΠ½ΠΎΠ²Π°Π½ΠΈΠ΅ ΡΠ°Π·Π±ΠΎΡΠ½ΡΠΌ ΠΏΠΎΒ ΡΠΎΠΉ ΠΏΡΠΈΡΠΈΠ½Π΅, ΡΡΠΎ ΡΠ°ΠΊ ΠΌΠΎΠΆΠ½ΠΎ Π±ΡΠ΄Π΅Ρ Π»Π΅Π³ΠΊΠΎ Π΄ΠΎΠ±ΡΠ°ΡΡΡΡ Π΄ΠΎΒ Π³Π°Π΅ΠΊ, ΠΈΒ Π·Π°ΠΌΠ΅Π½ΠΈΡΡ ΠΈΡ Β Π½Π°Β Π±ΠΎΠ»Π΅Π΅ ΡΠ΅ΡΡΠ΅Π·Π½ΡΠ΅ Π²ΠΌΠ΅ΡΡΠ΅ ΡΒ Π²ΠΈΠ½ΡΠΎΠΌ.
ΠΠ»Π°Π³ΠΎΠ΄Π°ΡΡ Π°Π²ΡΠΎΡΠ° Π·Π°Β ΠΏΡΠΎΡΡΡΡ ΠΊΠΎΠ½ΡΡΡΡΠΊΡΠΈΡ ΠΎΠ΄Π½ΠΎΠ³ΠΎ ΠΈΠ· ΡΠ°ΠΌΡΡ Π½Π΅ΠΎΠ±Ρ ΠΎΠ΄ΠΈΠΌΡΡ ΠΏΡΠΈΡΠΏΠΎΡΠΎΠ±Π»Π΅Π½ΠΈΠΉ Π΄Π»Ρ ΠΌΠ°ΡΡΠ΅ΡΡΠΊΠΎΠΉ!
ΠΡΠ΅ΠΌ Ρ ΠΎΡΠΎΡΠ΅Π³ΠΎ Π½Π°ΡΡΡΠΎΠ΅Π½ΠΈΡ, ΡΠ΄Π°ΡΠΈ, ΠΈΒ ΠΈΠ½ΡΠ΅ΡΠ΅ΡΠ½ΡΡ ΠΈΠ΄Π΅ΠΉ!
ΠΠ²ΡΠΎΡΡΠΊΠΎΠ΅ Π²ΠΈΠ΄Π΅ΠΎ ΠΌΠΎΠΆΠ½ΠΎ Π½Π°ΠΉΡΠΈ Π·Π΄Π΅ΡΡ.
ΠΡΡΠΎΡΠ½ΠΈΠΊ
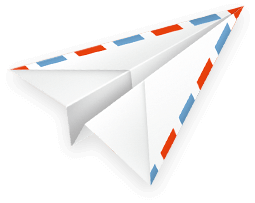
ΠΠΎΠ»ΡΡΠ°ΠΉΡΠ΅ Π½Π° ΠΏΠΎΡΡΡ ΠΏΠΎΠ΄Π±ΠΎΡΠΊΡ Π½ΠΎΠ²ΡΡ ΡΠ°ΠΌΠΎΠ΄Π΅Π»ΠΎΠΊ. ΠΠΈΠΊΠ°ΠΊΠΎΠ³ΠΎ ΡΠΏΠ°ΠΌΠ°, ΡΠΎΠ»ΡΠΊΠΎ ΠΏΠΎΠ»Π΅Π·Π½ΡΠ΅ ΠΈΠ΄Π΅ΠΈ!
*ΠΠ°ΠΏΠΎΠ»Π½ΡΡ ΡΠΎΡΠΌΡ Π²Ρ ΡΠΎΠ³Π»Π°ΡΠ°Π΅ΡΠ΅ΡΡ Π½Π° ΠΎΠ±ΡΠ°Π±ΠΎΡΠΊΡ ΠΏΠ΅ΡΡΠΎΠ½Π°Π»ΡΠ½ΡΡ Π΄Π°Π½Π½ΡΡ
Π‘ΡΠ°Π½ΠΎΠ²ΠΈΡΠ΅ΡΡ Π°Π²ΡΠΎΡΠΎΠΌ ΡΠ°ΠΉΡΠ°, ΠΏΡΠ±Π»ΠΈΠΊΡΠΉΡΠ΅ ΡΠΎΠ±ΡΡΠ²Π΅Π½Π½ΡΠ΅ ΡΡΠ°ΡΡΠΈ, ΠΎΠΏΠΈΡΠ°Π½ΠΈΡ ΡΠ°ΠΌΠΎΠ΄Π΅Π»ΠΎΠΊ Ρ ΠΎΠΏΠ»Π°ΡΠΎΠΉ Π·Π° ΡΠ΅ΠΊΡΡ. ΠΠΎΠ΄ΡΠΎΠ±Π½Π΅Π΅ Π·Π΄Π΅ΡΡ.Π’ΠΈΡΠΊΠΈ ΠΈΠ· ΠΌΠ΅ΡΠ°Π»Π»Π° ΡΠ²ΠΎΠΈΠΌΠΈ ΡΡΠΊΠ°ΠΌΠΈ

ΠΡΠΈΠ²Π΅Ρ Π²ΡΠ΅ΠΌ Π»ΡΠ±ΠΈΡΠ΅Π»ΡΠΌ ΡΠ°ΠΌΠΎΠ΄Π΅Π»ΠΎΠΊ. ΠΡΠΌΠ°Ρ ΠΌΠ½ΠΎΠ³ΠΈΠ΅ Π·Π½Π°ΡΡ, ΡΡΠΎ, Π½ΠΈ ΠΎΠ΄Π½Π° ΡΡΠΎΠ»ΡΡΠ½Π°Ρ ΠΌΠ°ΡΡΠ΅ΡΡΠΊΠ°Ρ Π½Π΅ ΠΎΠ±Ρ ΠΎΠ΄ΠΈΡΡΡ Π±Π΅Π· ΡΠΈΡΠΊΠΎΠ². ΠΡΠΎ ΠΎΡΠ΅Π½Ρ ΡΡΠ½ΠΊΡΠΈΠΎΠ½Π°Π»ΡΠ½ΡΠΉ ΠΈΠ½ΡΡΡΡΠΌΠ΅Π½Ρ Π΄Π»Ρ ΡΠΈΠΊΡΠΈΡΠΎΠ²Π°Π½ΠΈΡ Π΄Π΅ΡΠ°Π»ΠΈ ΠΏΡΠΈ ΡΠ°Π·Π»ΠΈΡΠ½ΡΡ Π²ΠΈΠ΄Π°Ρ ΠΎΠ±ΡΠ°Π±ΠΎΡΠΊΠΈ, Π° ΡΠ°ΠΊΠΆΠ΅ ΠΏΡΠΈΠΆΠΈΠΌΠ° Π²ΠΎ Π²ΡΠ΅ΠΌΡ ΡΠΊΠ»Π΅ΠΈΠ²Π°Π½ΠΈΡ. ΠΠ±ΡΡΠ½ΠΎ ΠΎΠ΄Π½Π° ΡΠ°ΡΡΡ ΡΠ²Π»ΡΠ΅ΡΡΡ ΠΏΠΎΠ΄Π²ΠΈΠΆΠ½ΠΎΠΉ, Π° Π΄ΡΡΠ³Π°Ρ ΠΆΠ΅ΡΡΠΊΠΎ Π·Π°ΠΊΡΠ΅ΠΏΠ»Π΅Π½Π° Π½Π° Π²Π΅ΡΡΡΠ°ΠΊΠ΅. ΠΠΎ ΠΊΠ°ΠΊ ΡΡΠΎ Π²ΠΎΠ΄ΠΈΡΡΡ, Π΄ΠΎΡΠΎΠ³ΠΎΠΉ ΠΈ ΠΊΠ°ΡΠ΅ΡΡΠ²Π΅Π½Π½ΡΠΉ ΠΈΠ½ΡΡΡΡΠΌΠ΅Π½Ρ ΡΡΠΎΠΈΡ Π±ΠΎΠ»ΡΡΠΈΡ Π΄Π΅Π½Π΅Π³, Π½Π΅ Π²ΡΠ΅ Π½Π°ΡΠΈΠ½Π°ΡΡΠΈΠ΅ ΡΠ»Π΅ΡΠ°ΡΠΈ ΠΈΠ»ΠΈ ΠΏΡΠΎΡΡΠΎ Π»ΡΠ±ΠΈΡΠ΅Π»ΠΈ ΠΏΠΎΠΌΠ°ΡΡΠ΅ΡΠΈΡΡ, ΠΌΠΎΠ³ΡΡ ΡΠ΅Π±Π΅ ΠΏΠΎΠ·Π²ΠΎΠ»ΠΈΡΡ ΡΠ°ΠΊΠΎΠ΅ ΡΠ΄ΠΎΠ²ΠΎΠ»ΡΡΡΠ²ΠΈΠ΅. ΠΠΌΠ΅Π½Π½ΠΎ ΠΏΠΎΡΡΠΎΠΌΡ Π±ΡΠ»ΠΎ ΠΏΡΠΈΠ½ΡΡΠΎ ΡΠ΅ΡΠ΅Π½ΠΈΠ΅ ΡΠ΄Π΅Π»Π°ΡΡ Π΄Π°Π½Π½ΡΠ΅ ΡΠΈΡΠΊΠΈ, ΡΠ΅ΠΌ ΡΠ°ΠΌΡΠΌ Π΄ΠΎΠΊΠ°Π·Π°ΡΡ, ΡΡΠΎ ΡΠ΄Π΅Π»Π°ΡΡ ΠΈΡ ΡΠ²ΠΎΠΈΠΌΠΈ ΡΡΠΊΠ°ΠΌΠΈ ΡΠ΅Π°Π»ΡΠ½ΠΎ ΠΈ ΡΡΠΎ Π±ΡΠ΄Π΅Ρ Π½ΠΈ ΡΡΡΡ Π½Π΅ Ρ ΡΠΆΠ΅ Π·Π°Π²ΠΎΠ΄ΡΠΊΠΈΡ , Π° Π² Π½Π΅ΠΊΠΎΡΠΎΡΡΡ ΠΏΠΎΠΊΠ°Π·Π°ΡΠ΅Π»ΡΡ Π΄Π°ΠΆΠ΅ Π»ΡΡΡΠ΅. ΠΠ°ΡΡΠ°ΡΡ Π½Π° ΠΌΠ°ΡΠ΅ΡΠΈΠ°Π»Ρ Π±ΡΠ΄ΡΡ Π² ΡΠ°Π·Ρ ΠΌΠ΅Π½ΡΡΠ΅, ΡΠ΅ΠΌ ΠΊΡΠΏΠΈΡΡ Π³ΠΎΡΠΎΠ²ΡΠ΅ ΡΠΈΡΠΊΠΈ, ΡΠ΅ΠΌ Π±ΠΎΠ»Π΅Π΅ Π½Π΅ Π½Π°Π΄ΠΎ Π·Π°Π±ΡΠ²Π°ΡΡ, ΡΡΠΎ Ρ Π½Π΅ΠΊΠΎΡΠΎΡΡΡ Π² ΠΌΠ°ΡΡΠ΅ΡΡΠΊΠΈΡ Π΅ΡΡΡ ΠΎΠ±ΡΠ΅Π·ΠΊΠΈ ΡΠ³ΠΎΠ»ΠΊΠΎΠ², ΠΎΡΡΠ°ΡΠΊΠΈ ΡΠ²Π΅Π»Π»Π΅ΡΠΎΠ² ΠΈ Π΄ΡΡΠ³ΠΈΠ΅ Π΄Π΅ΡΠ°Π»ΠΈ, ΠΊΠΎΡΠΎΡΡΠ΅ ΠΏΠΎΠΉΠ΄ΡΡ Π½Π° ΠΈΠ·Π³ΠΎΡΠΎΠ²Π»Π΅Π½ΠΈΠ΅ Π΄Π°Π½Π½ΠΎΠΉ ΡΠ°ΠΌΠΎΠ΄Π΅Π»ΠΊΠΈ.
Π ΡΠ°ΠΊΠΆΠ΅ Π²ΠΈΠ΄Π΅ΠΎ Π³ΡΡΠ½ΡΠΎΠ²ΠΊΠΈ ΠΈ ΠΏΠΎΠΊΡΠ°ΡΠΊΠΈ Π³ΠΎΡΠΎΠ²ΠΎΠ³ΠΎ ΡΠ°ΠΌΠΎΠ΄Π΅Π»ΡΠ½ΠΎΠ³ΠΎ ΠΈΠ½ΡΡΡΡΠΌΠ΅Π½ΡΠ°.
ΠΠ»Ρ ΡΠΎΠ³ΠΎ, ΡΡΠΎΠ±Ρ ΡΠ΄Π΅Π»Π°ΡΡ ΡΠΈΡΠΊΠΈ ΠΈΠ· ΠΌΠ΅ΡΠ°Π»Π»Π° ΡΠ²ΠΎΠΈΠΌΠΈ ΡΡΠΊΠ°ΠΌΠΈ, ΠΏΠΎΠ½Π°Π΄ΠΎΠ±ΠΈΡΡΡ:
* ΠΠΈΡΡ ΠΌΠ΅ΡΠ°Π»Π»Π° ΡΠΎΠ»ΡΠΈΠ½ΠΎΠΉ 12 ΠΌΠΌ ΠΈ 8 ΠΌΠΌ
* Π£Π³ΠΎΠ»ΠΎΠΊ 73 ΠΌΠΌ, ΡΠΎΠ»ΡΠΈΠ½Π° ΠΌΠ΅ΡΠ°Π»Π»Π° 8 ΠΌΠΌ
* Π Π΅ΡΡΠΎΡΠ°
* ΠΠ²Π΅ ΠΎΠ±ΠΎΠΉΠΌΡ ΠΏΠΎΠ΄ΡΠΈΠΏΠ½ΠΈΠΊΠ°
* ΠΠΈΠ½Ρ ΠΎΡ Π΄ΠΎΠΌΠΊΡΠ°ΡΠ° ΠΈΠ»ΠΈ ΠΆΠ΅ ΡΡΠ°ΡΡΡ
ΡΠΈΡΠΊΠΎΠ²
* ΠΠ°ΠΉΠΊΠ° Π²ΠΈΠ½ΡΠ°
* Π‘Π²Π°ΡΠΎΡΠ½ΡΠΉ Π°ΠΏΠΏΠ°ΡΠ°Ρ, ΡΠ²Π°ΡΠΎΡΠ½Π°Ρ ΠΌΠ°ΡΠΊΠ°, ΠΏΠ΅ΡΡΠ°ΡΠΊΠΈ
* Π‘ΡΡΡΠ±ΡΠΈΠ½Ρ
* ΠΡΠΎΡΠΈΠ»Ρ 20*40 ΠΌΠΌ
* ΠΠ»Π΅ΠΊΡΡΠΎΠ΄ΡΠ΅Π»Ρ, ΠΆΠ΅Π»Π°ΡΠ΅Π»ΡΠ½ΠΎ ΡΠ²Π΅ΡΠ»ΠΈΠ»ΡΠ½ΡΠΉ ΡΡΠ°Π½ΠΎΠΊ
* Π‘Π²Π΅ΡΠ»ΠΎ ΠΏΠΎ-ΠΌΠ΅ΡΠ°Π»Π»Ρ 6 ΠΌΠΌ
* Π¨Π°ΠΉΠ±Π° Ρ ΠΎΡΠ²Π΅ΡΡΡΠΈΠ΅ΠΌ Π±Π»ΠΈΠ·ΠΊΠΈΠΌ ΠΊ Π΄ΠΈΠ°ΠΌΠ΅ΡΡΡ Π²ΠΈΠ½ΡΠ°
* Π£Π³Π»ΠΎΡΠ»ΠΈΡΠΎΠ²Π°Π»ΡΠ½Π°Ρ ΠΌΠ°ΡΠΈΠ½ΠΊΠ° Ρ ΠΎΡΡΠ΅Π·Π½ΡΠΌ ΠΊΡΡΠ³ΠΎΠΌ
* Π¨ΠΏΠΈΠ»ΡΠΊΠ° Π΄ΠΈΠ°ΠΌΠ΅ΡΡΠΎΠΌ 6 ΠΌΠΌ
ΠΠΎΡ ΠΈ Π²ΡΠ΅, ΡΡΠΎ Π½ΡΠΆΠ½ΠΎ Π΄Π»Ρ ΠΈΠ·Π³ΠΎΡΠΎΠ²Π»Π΅Π½ΠΈΡ ΠΌΠΎΡΠ½ΡΡ ΡΠΈΡΠΊΠΎΠ² ΡΠ²ΠΎΠΈΠΌΠΈ ΡΡΠΊΠ°ΠΌΠΈ.
Π¨Π°Π³ ΠΏΠ΅ΡΠ²ΡΠΉ.
ΠΠ΅ΡΠ²ΡΠΌ Π΄Π΅Π»ΠΎΠΌ ΡΡΡΠ°Π½Π°Π²Π»ΠΈΠ²Π°Π΅ΠΌ ΠΎΠ±ΠΎΠΉΠΌΡ ΠΏΠΎΠ΄ΡΠΈΠΏΠ½ΠΈΠΊΠ° Π½Π° Π²ΠΈΠ½Ρ, ΠΊΠΎΡΠΎΡΠ°Ρ Π±ΡΠ΄Π΅Ρ ΡΠ»ΡΠΆΠΈΡΡ ΡΠΏΠΎΡΠΎΠΌ ΠΏΡΠΈ Π·Π°ΠΆΠΈΠΌΠ΅ ΡΠΈΡΠΊΠΎΠ².


ΠΠ΅ΡΠ°Π»Π» ΠΎΠ±ΠΎΠΉΠΌΡ Π΄ΠΎΡΡΠ°ΡΠΎΡΠ½ΠΎ ΠΏΡΠΎΡΠ½ΡΠΉ, ΡΡΠΎ ΠΈ Π½ΡΠΆΠ½ΠΎ Π΄Π»Ρ Π½Π°ΡΠ΅ΠΉ ΡΠ°ΠΌΠΎΠ΄Π΅Π»ΠΊΠΈ. Π Π±ΡΠ΄ΡΡΠ΅ΠΌ Π½Π° ΡΡΠΎΠΉ ΠΌΠ΅ΡΡΠΎ ΠΌΠΎΠΆΠ½ΠΎ ΡΡΡΠ°Π½ΠΎΠ²ΠΈΡΡ ΡΠΏΠΎΡΠ½ΡΠΉ ΠΏΠΎΠ΄ΡΠΈΠΏΠ½ΠΈΠΊ. ΠΠΎΠ·ΠΈΡΠΈΠΎΠ½ΠΈΡΡΠ΅ΠΌ ΠΎΠ±ΠΎΠΉΠΌΡ Π½Π° Π²ΠΈΠ½ΡΠ΅ ΠΌΠ°ΠΊΡΠΈΠΌΠ°Π»ΡΠ½ΠΎ ΡΠΎΠ²Π½ΠΎ, ΡΠ΄Π΅Π»Π°ΡΡ ΡΡΠΎ Π»ΡΡΡΠ΅ Π²ΡΠ΅Π³ΠΎ Π½Π° ΡΠΎΠΊΠ°ΡΠ½ΠΎΠΌ ΡΡΠ°Π½ΠΊΠ΅, Π·Π°ΠΆΠ°Π² Π²ΠΈΠ½Ρ Π² ΠΏΠ°ΡΡΠΎΠ½ ΠΈ ΡΡΡΠ°Π½ΠΎΠ²ΠΈΠ² ΡΠ΅Π·Π΅Ρ, Π²ΡΡΡΠ°Π²ΠΈΡΡ ΠΎΠ±ΠΎΠΉΠΌΡ ΠΏΠΎ Π½Π΅ΠΌΡ, ΠΏΠΎΡΠΈΡ ΠΎΠ½ΡΠΊΡ Π²ΡΠ°ΡΠ°Ρ ΠΏΠ°ΡΡΠΎΠ½ ΡΡΠ°Π½ΠΊΠ° ΠΈ ΠΏΡΠΈ Π½Π΅ΠΎΠ±Ρ ΠΎΠ΄ΠΈΠΌΠΎΡΡΠΈ ΠΏΠΎΡΡΡΠΊΠΈΠ²Π°ΡΡ Π΄Π»Ρ ΡΡΡΡΠ°Π½Π΅Π½ΠΈΡ ΠΎΡΠΊΠ»ΠΎΠ½Π΅Π½ΠΈΠΉ.

ΠΠΎΡΠ»Π΅ ΡΡΠΎΠ³ΠΎ ΠΏΡΠΈ ΠΏΠΎΠΌΠΎΡΠΈ ΡΠ²Π°ΡΠΎΡΠ½ΠΎΠ³ΠΎ Π°ΠΏΠΏΠ°ΡΠ°ΡΠ° ΠΏΡΠΈΠ²Π°ΡΠΈΠ²Π°Π΅ΠΌ ΠΎΠ±Π΅ Π΄Π΅ΡΠ°Π»ΠΈ Π½Π°ΠΌΠ΅ΡΡΠ²ΠΎ Π΄ΡΡΠ³ ΠΊ Π΄ΡΡΠ³Ρ. ΠΡΠΈ ΡΠ²Π°ΡΠΊΠ΅ ΡΠ°ΡΡΠ΅ΠΉ ΡΠΎΠ±Π»ΡΠ΄Π°ΠΉΡΠ΅ ΠΌΠ΅ΡΡ Π±Π΅Π·ΠΎΠΏΠ°ΡΠ½ΠΎΡΡΠΈ, Π½Π΅ Π·Π°Π±ΡΠ²Π°ΠΉΡΠ΅ ΠΎΠ΄Π΅Π²Π°ΡΡ ΠΊΡΠ°Π³ΠΈ, Π° ΡΠ°ΠΊΠΆΠ΅ Π·Π°ΡΠΈΡΠ½ΡΡ ΡΠ²Π°ΡΠΎΡΠ½ΡΡ ΠΌΠ°ΡΠΊΡ.
Π¨Π°Π³ Π²ΡΠΎΡΠΎΠΉ.
Π’Π΅ΠΏΠ΅ΡΡ Π½ΡΠΆΠ½ΠΎ ΡΠ΄Π΅Π»Π°ΡΡ Π½Π΅ΠΏΠΎΠ΄Π²ΠΈΠΆΠ½ΡΡ ΡΠ°ΡΡΡ ΡΠΈΡΠΊΠΎΠ², ΠΏΡΠΈ ΠΏΠΎΠΌΠΎΡΠΈ ΡΠ³Π»ΠΎΡΠ»ΠΈΡΠΎΠ²Π°Π»ΡΠ½ΠΎΠΉ ΠΌΠ°ΡΠΈΠ½ΠΊΠΈ ΠΎΡΠΏΠΈΠ»ΠΈΠ²Π°Π΅ΠΌ ΠΊΠ²Π°Π΄ΡΠ°Ρ 180 ΠΌΠΌ ΠΈΠ· Π»ΠΈΡΡΠ° ΠΌΠ΅ΡΠ°Π»Π»Π° ΡΠΎΠ»ΡΠΈΠ½ΠΎΠΉ 12 ΠΌΠΌ.

Π Π½Π΅ΠΌΡ ΠΏΡΠΈΠΌΠ΅ΡΡΠ΅ΠΌ ΠΎΡΡΠ΅Π·ΠΊΠΈ ΠΌΠ΅ΡΠ°Π»Π»Π° ΡΠΎΠ»ΡΠΈΠ½ΠΎΠΉ 8 ΠΌΠΌ ΠΏΠΎ Π²ΡΡΠΎΡΠ΅ ΡΠ³ΠΎΠ»ΠΊΠ°, ΠΊΠΎΡΠΎΡΡΠΉ Π±ΡΠ΄Π΅Ρ ΠΏΠΎΠ΄Π²ΠΈΠΆΠ½ΠΎΠΉ ΡΠ°ΡΡΡΡ ΡΠΈΡΠΊΠΎΠ², Π° ΡΠ²Π΅ΡΡ Ρ ΡΠ°ΡΠΏΠΎΠ»Π°Π³Π°Π΅ΠΌ Π»ΠΈΡΡ ΠΈΠ· 12-ΡΠΈ ΠΌΠΈΠ»Π»ΠΈΠΌΠ΅ΡΡΠΎΠ²ΠΎΠ³ΠΎ ΠΌΠ΅ΡΠ°Π»Π»Π°, Π²ΡΠ΅ ΡΡΠΈ Π΄Π΅ΡΠ°Π»ΠΈ ΡΠΈΠΊΡΠΈΡΡΠ΅ΠΌ ΠΊ ΡΠ³ΠΎΠ»ΠΊΡ ΠΏΡΠΈ ΠΏΠΎΠΌΠΎΡΠΈ ΡΡΡΡΠ±ΡΠΈΠ½Ρ.
ΠΠ»Ρ ΡΠΎΠ³ΠΎ, ΡΡΠΎΠ±Ρ ΠΏΡΠΈ ΡΠ²Π°ΡΠΊΠ΅ Π΄Π΅ΡΠ°Π»Π΅ΠΉ Π² ΠΎΠ΄Π½ΠΎ ΡΠ΅Π»ΠΎΠ΅ ΡΠ³ΠΎΠ»ΠΎΠΊ ΠΌΠΎΠ³ ΡΠ²ΠΎΠ±ΠΎΠ΄Π½ΠΎ ΠΏΠ΅ΡΠ΅ΠΌΠ΅ΡΠ°ΡΡΡΡ Π²Π½ΡΡΡΠΈ, Π½ΡΠΆΠ½ΠΎ ΠΏΠΎΠ΄Π»ΠΎΠΆΠΈΡΡ ΠΏΠ΅ΡΠ΅Π΄ ΡΡΠΈΠΌ ΠΊΠ°ΡΡΠΎΠ½ΠΊΡ Ρ ΡΡΠ΅Ρ ΡΡΠΎΡΠΎΠ½, ΡΠ΅ΠΌ ΡΠ°ΠΌΡΠΌ ΠΎΠ±Π΅ΡΠΏΠ΅ΡΠΈΠ² ΠΌΠΈΠ½ΠΈΠΌΠ°Π»ΡΠ½ΡΠΉ Π·Π°Π·ΠΎΡ Π΄Π»Ρ Π½ΠΎΡΠΌΠ°Π»ΡΠ½ΠΎΠΉ ΡΠ°Π±ΠΎΡΡ ΠΏΠΎΠ΄Π²ΠΈΠΆΠ½ΠΎΠ³ΠΎ ΠΌΠ΅Ρ Π°Π½ΠΈΠ·ΠΌΠ°.


Π’Π°ΠΊΠΆΠ΅ ΡΠ»Π΅Π΄ΠΈΡΠ΅, ΡΡΠΎΠ±Ρ ΠΏΡΠΈ ΡΠ²Π°ΡΠΊΠ΅ ΠΌΠ΅ΡΠ°Π»Π» Π½Π΅ Π²ΡΠ»Π΅Π· Π²ΠΎΠ²Π½ΡΡΡΡ, ΡΠ°ΠΊ ΠΊΠ°ΠΊ ΡΡΠΎ Π·Π°ΠΉΠΌΠ΅Ρ Π½Π΅ΠΌΠ°Π»ΠΎ Π²ΡΠ΅ΠΌΠ΅Π½ΠΈ Π½Π° ΠΈΡΠΏΡΠ°Π²Π»Π΅Π½ΠΈΠ΅.
Π¨Π°Π³ ΡΡΠ΅ΡΠΈΠΉ.
Π£ΡΡΠ°Π½Π°Π²Π»ΠΈΠ²Π°Π΅ΠΌ Π³Π°ΠΉΠΊΡ Π½Π° ΠΎΡΠ½ΠΎΠ²Π°Π½ΠΈΠΈ.


ΠΠ»Ρ ΡΡΠΎΠ³ΠΎ ΡΠ°Π·ΠΌΠ΅ΡΠ°Π΅ΠΌ ΠΌΠ΅ΡΡΠΎ, Π³Π΄Π΅ ΠΎΠ½Π° Π±ΡΠ΄Π΅Ρ ΠΏΡΠΈΠ²Π°ΡΠ΅Π½Π°, ΠΏΠΎΠ·ΠΈΡΠΈΠΎΠ½ΠΈΡΡΠ΅ΠΌ Π΅Π΅ ΠΏΠΎΡΠ΅ΡΠ΅Π΄ΠΈΠ½Π΅, ΡΠ΄Π΅Π»Π°Π² ΠΎΡΡΡΡΠΏ ΠΎΡ ΠΊΡΠ°Ρ ΠΎΠΊΠΎΠ»ΠΎ 5 ΠΌΠΌ. Π§ΡΠΎΠ±Ρ Π²ΠΈΠ½Ρ ΠΏΠ΅ΡΠ΅ΠΌΠ΅ΡΠ°Π»ΡΡ ΡΠΎΠ²Π½ΠΎ, ΠΏΠΎΠ΄ΠΊΠ»Π°Π΄ΡΠ²Π°Π΅ΠΌ ΠΏΠΎΠ΄ Π½Π΅Π³ΠΎ ΠΏΡΠΎΡΠΈΠ»Ρ Ρ ΡΠ°Π·ΠΌΠ΅ΡΠ°ΠΌΠΈ 20*40 ΠΌΠΌ ΠΈ ΠΏΡΠΈΡ Π²Π°ΡΡΠ²Π°Π΅ΠΌ ΡΠ²Π°ΡΠΊΠΎΠΉ Π³Π°ΠΉΠΊΡ ΠΊ ΠΎΡΠ½ΠΎΠ²Π°Π½ΠΈΡ, ΠΏΠΎΡΠ»Π΅ ΡΠ΅Π³ΠΎ ΡΠΆΠ΅ ΠΎΡΠ½ΠΎΠ²Π°ΡΠ΅Π»ΡΠ½ΠΎ ΠΏΡΠΎΠ²Π°ΡΠΈΠ²Π°Π΅ΠΌ.
ΠΠ»Ρ ΠΎΠ±ΡΠ°ΡΠ½ΠΎΠ³ΠΎ Ρ ΠΎΠ΄Π° Π² Π²ΠΈΠ½ΡΠ΅ Π½ΡΠΆΠ½ΠΎ ΠΏΡΠΎΡΠ²Π΅ΡΠ»ΠΈΡΡ ΠΎΡΠ²Π΅ΡΡΡΠΈΠ΅. Π‘Π΄Π΅Π»Π°ΡΡ ΡΡΠΎ Π»Π΅Π³ΡΠ΅ ΠΈ ΡΠΎΠ²Π½Π΅Π΅ Π±ΡΠ΄Π΅Ρ Π½Π° ΡΠ²Π΅ΡΠ»ΠΈΠ»ΡΠ½ΠΎΠΌ ΡΡΠ°Π½ΠΊΠ΅, Π½ΠΎ Π΅ΡΠ»ΠΈ Ρ Π²Π°Ρ Π΅Π³ΠΎ Π½Π΅Ρ, ΡΠΎ ΠΎΠ±ΡΡΠ½Π°Ρ Π΄ΡΠ΅Π»Ρ ΡΠΎΠΆΠ΅ ΠΏΠΎΠ΄ΠΎΠΉΠ΄Π΅Ρ. ΠΡΠ²Π΅ΡΡΡΠΈΠ΅ Π΄Π΅Π»Π°Π΅ΠΌ ΡΡΡΠΎΠ³ΠΎ ΠΏΠΎΡΠ΅ΡΠ΅Π΄ΠΈΠ½Π΅ Π²ΠΈΠ½ΡΠ°, ΡΠ²Π΅ΡΠ»ΠΎ Π² Π΄Π°Π½Π½ΠΎΠΌ ΡΠ»ΡΡΠ°Π΅ ΠΈΠΌΠ΅Π΅Ρ Π΄ΠΈΠ°ΠΌΠ΅ΡΡ 6 ΠΌΠΌ, Π² Π½Π΅Π³ΠΎ Π² Π΄Π°Π»ΡΠ½Π΅ΠΉΡΠ΅ΠΌ Π±ΡΠ΄Π΅Ρ ΡΡΡΠ°Π½ΠΎΠ²Π»Π΅Π½ ΡΠΏΠ»ΠΈΠ½Ρ ΡΠ°ΠΊΠΎΠ³ΠΎ ΠΆΠ΅ Π΄ΠΈΠ°ΠΌΠ΅ΡΡΠ°.
Π¨Π°Π³ ΡΠ΅ΡΠ²Π΅ΡΡΡΠΉ.
ΠΠ»Π°ΡΡΠΈΠ½Π° Π΄Π»Ρ ΡΠΏΠΎΡΠ° Π²ΠΈΠ½ΡΠ° Π΄ΠΎΠ»ΠΆΠ½Π° ΠΈΠΌΠ΅ΡΡ ΠΎΡΠ²Π΅ΡΡΡΠΈΠ΅ ΡΡΡΡ Π±ΠΎΠ»ΡΡΠ΅ Π΅Π³ΠΎ Π΄ΠΈΠ°ΠΌΠ΅ΡΡΠ°. Π Π΄Π°Π½Π½ΠΎΠΌ ΡΠ»ΡΡΠ°Π΅ ΡΠ²Π΅ΡΠ»Π° ΠΏΠΎ ΠΌΠ΅ΡΠ°Π»Π»Ρ Π½ΡΠΆΠ½ΠΎΠ³ΠΎ Π΄ΠΈΠ°ΠΌΠ΅ΡΡΠ° Π½Π΅ Π±ΡΠ»ΠΎ, ΠΏΠΎΡΡΠΎΠΌΡ Π±ΡΠ»ΠΎ ΡΠ΅ΡΠ΅Π½ΠΎ ΡΠ°ΡΠΏΠΈΠ»ΠΈΡΡ ΡΠ³Π»ΠΎΡΠ»ΠΈΡΠΎΠ²Π°Π»ΡΠ½ΠΎΠΉ ΠΌΠ°ΡΠΈΠ½ΠΊΠΎΠΉ 12-ΡΠΈ ΠΌΠΈΠ»Π»ΠΈΠΌΠ΅ΡΡΠΎΠ²ΡΡ ΠΏΠ»Π°ΡΡΠΈΠ½Ρ ΠΏΠΎΠΏΠΎΠ»Π°ΠΌ, Π° Π·Π°ΡΠ΅ΠΌ ΡΠ΄Π΅Π»Π°ΡΡ ΠΏΠΎΠ»ΡΠΊΡΡΠ³Π»ΡΠ΅ ΠΏΡΠΎΠΏΠΈΠ»Ρ ΡΠΎΠΉ ΠΆΠ΅ Π£Π¨Π, Π° ΡΠΆΠ΅ ΠΏΠΎΡΠΎΠΌ ΡΠ²Π°ΡΠΈΡΡ ΠΎΠ±ΡΠ°ΡΠ½ΠΎ.
ΠΠΈΠ½Ρ Π² ΡΠ±ΠΎΡΠ΅ Ρ ΡΠΏΠΎΡΠ½ΠΎΠΉ ΠΏΠ»Π°ΡΡΠΈΠ½ΠΎΠΉ Π²ΡΠ³Π»ΡΠ΄ΠΈΡ ΡΠ°ΠΊ.


ΠΠΎΠΌΠΈΠΌΠΎ ΠΎΠ±ΠΎΠΉΠΌ ΠΎΡ ΠΏΠΎΠ΄ΡΠΈΠΏΠ½ΠΈΠΊΠ° Π½ΡΠΆΠ½Π° ΡΠ°ΠΉΠ±Π° Π΄Π»Ρ ΠΎΠ±ΡΠ°ΡΠ½ΠΎΠ³ΠΎ Ρ ΠΎΠ΄Π° ΡΠΈΡΠΊΠΎΠ², Π΅Π΅ ΠΌΠΎΠΆΠ½ΠΎ ΡΠ΄Π΅Π»Π°ΡΡ ΡΠ°ΠΌΠΎΠΌΡ ΠΏΡΠΈ ΠΏΠΎΠΌΠΎΡΠΈ ΡΠΎΠΊΠ°ΡΠ½ΠΎΠ³ΠΎ ΡΡΠ°Π½ΠΊΠ°.
Π¨Π°Π³ ΠΏΡΡΡΠΉ.
ΠΡΠΈΠ²Π°ΡΠΈΠ²Π°Π΅ΠΌ Π½Π΅ΡΠΊΠΎΠ»ΡΠΊΠΈΠΌΠΈ ΡΠΎΡΠΊΠ°ΠΌΠΈ Π-ΠΎΠ±ΡΠ°Π·Π½ΡΡ ΡΠ°ΡΡΡ, ΠΊΠΎΡΠΎΡΡΡ Π΄Π΅Π»Π°Π»ΠΈ ΡΡΡΡ ΡΠ°Π½Π΅Π΅, ΠΊ ΠΎΡΠ½ΠΎΠ²Π°Π½ΠΈΡ ΡΡΡΠΎΠ³ΠΎ ΠΏΠΎΡΠ΅ΡΠ΅Π΄ΠΈΠ½Π΅, Π° ΡΠ°ΠΊΠΆΠ΅ ΠΏΡΠΈΠΆΠΈΠΌΠ½ΡΡ ΠΏΠ»Π°ΡΡΠΈΠ½Ρ ΠΊ ΠΏΠΎΠ΄Π²ΠΈΠΆΠ½ΠΎΠΉ ΡΠ°ΡΡΠΈ.
ΠΠ°ΠΊΠΈΠ΄ΡΠ²Π°Π΅ΠΌ ΡΠ°ΠΉΠ±Ρ ΡΠ½ΠΈΠ·Ρ ΠΈ ΠΏΡΠΎΡΠΎΠ²ΡΠ²Π°Π΅ΠΌ ΡΠΏΠΈΠ»ΡΠΊΡ, ΠΊΠΎΡΠΎΡΠ°Ρ Π½Π΅ Π΄Π°Π΅Ρ Π²ΠΈΠ½ΡΡ Π²ΡΠΉΡΠΈ ΠΏΡΠΈ ΠΎΡΠΊΡΡΡΠΈΠ²Π°Π½ΠΈΠΈ. ΠΠΎΡΠ»Π΅ ΡΡΠΎΠ³ΠΎ ΠΊΠ°ΡΠ΅ΡΡΠ²Π΅Π½Π½ΠΎ ΠΏΡΠΎΠ²Π°ΡΠΈΠ²Π°Π΅ΠΌ ΡΡΡΠΊΠΈ Π½Π΅ΠΏΠΎΠ΄Π²ΠΈΠΆΠ½ΡΡ Π΄Π΅ΡΠ°Π»Π΅ΠΉ.
ΠΠΎΡ ΡΠ°ΠΊ ΡΡΠΎ Π²ΡΠ³Π»ΡΠ΄ΠΈΡ.
Π Π²Π΅ΡΡ Π½Π΅ΠΉ ΡΠ°ΡΡΠΈ ΠΏΡΠΎΡΠ²Π΅ΡΠ»ΠΈΠ²Π°Π΅ΠΌ ΠΎΡΠ²Π΅ΡΡΡΠΈΠ΅, Π² Π΄Π°Π»ΡΠ½Π΅ΠΉΡΠ΅ΠΌ ΠΎΠ½ΠΎ ΠΏΡΠΈΠ³ΠΎΠ΄ΠΈΡΡΡ Π΄Π»Ρ ΡΡΡΠ°Π½ΠΎΠ²ΠΊΠΈ Π·Π°ΡΠΈΡΠ½ΠΎΠΉ ΡΠ΅Π·ΠΈΠ½Ρ, ΡΠ°ΠΊ ΠΊΠ°ΠΊ ΠΏΠΎΠΏΠ°Π΄Π°Π½ΠΈΠ΅ ΡΡΡΡΠΆΠΊΠΈ Π½Π° ΠΏΠΎΠ΄Π²ΠΈΠΆΠ½ΡΡ ΡΠ°ΡΡΡ, Π° Π² ΠΏΠΎΡΠ»Π΅Π΄ΡΡΠ²ΠΈΠΈ ΠΈ Π½Π΅ΠΏΠΎΠ΄Π²ΠΈΠΆΠ½ΠΎΠΉ, ΠΌΠΎΠΆΠ΅Ρ ΠΏΡΠΈΠ²Π΅ΡΡΠΈ ΠΊ Π·Π°ΠΊΠ»ΠΈΠ½ΠΈΠ²Π°Π½ΠΈΡ ΡΠΈΡΠΊΠΎΠ² ΠΈΠ»ΠΈ ΠΆΠ΅ ΡΡΠ»ΠΎΠΆΠ½ΠΈΡΡ Ρ ΠΎΠ΄ Π²ΠΈΠ½ΡΠ°. Π Π»ΡΠ±ΠΎΠΌ ΡΠ»ΡΡΠ°Π΅ ΡΡΠΎ Π½ΠΈΠΊΠ°ΠΊ Π½Π΅ ΠΏΠΎΠΌΠ΅ΡΠ°Π΅Ρ ΠΈ Π½Π΅ ΠΎΡΠ»Π°Π±ΠΈΡ ΠΊΠΎΠ½ΡΡΡΡΠΊΡΠΈΡ.


Π¨Π°Π³ ΡΠ΅ΡΡΠΎΠΉ.
ΠΠΎΡΠ° ΡΠ΄Π΅Π»Π°ΡΡ Π²Π΅ΡΡ Π½ΡΡ ΡΠ°ΡΡΡ ΡΠΈΡΠΊΠΎΠ². Π Π°Π·ΠΌΠ΅ΡΠ°Π΅ΠΌ Π½Π° Π»ΠΈΡΡΠ΅ ΡΠΎΠ»ΡΠΈΠ½ΠΎΠΉ 6 ΠΌΠΌ ΡΡΠΊΠΈΠ· Π² Π²ΠΈΠ΄Π΅ ΡΡΠ°ΠΏΠ΅ΡΠΈΠΈ ΠΈ ΠΏΡΠΈ ΠΏΠΎΠΌΠΎΡΠΈ ΡΠ³Π»ΠΎΡΠ»ΠΈΡΠΎΠ²Π°Π»ΡΠ½ΠΎΠΉ ΠΌΠ°ΡΠΈΠ½ΠΊΠΈ Π²ΡΡΠ΅Π·Π°Π΅ΠΌ ΡΠ΅ΡΡΡΠ΅ Π·Π°Π³ΠΎΡΠΎΠ²ΠΊΠΈ, Π΄Π²Π΅ ΠΈΠ· Π½ΠΈΡ Π±ΡΠ΄ΡΡ Π²ΡΡΠ΅, ΡΠ°ΠΊ ΠΊΠ°ΠΊ ΡΡΡΠ°Π½Π°Π²Π»ΠΈΠ²Π°ΡΡΡΡ Π±ΡΠ΄ΡΡ Π½Π° Π»ΠΈΡΡ ΠΌΠ΅ΡΠ°Π»Π»Π°, ΡΠΎΠ»ΡΠΈΠ½Π° ΠΊΠΎΡΠΎΡΠΎΠ³ΠΎ 12 ΠΌΠΌ.

ΠΠΎΠ³Π΄Π° Π²ΡΠ΅ ΡΠ΅ΡΡΡΠ΅ Π΄Π΅ΡΠ°Π»ΠΈ Π²ΡΠΏΠΈΠ»Π΅Π½Ρ, ΠΏΡΠΈΠ²Π°ΡΠΈΠ²Π°Π΅ΠΌ ΠΈΡ , Π½ΠΎ Π΄Π΅Π»Π°Π΅ΠΌ ΡΡΠΎ Π½Π΅ΠΌΠ½ΠΎΠ³ΠΎ ΠΏΠΎΠ΄ ΡΠ³Π»ΠΎΠΌ, ΡΡΠΎΠ±Ρ ΡΠ²Π΅Π»ΠΈΡΠΈΡΡ ΡΠΈΡΠΈΠ½Ρ Π³ΡΠ±ΠΎΠΊ, ΠΎΠ½Π° ΠΊ ΡΠ»ΠΎΠ²Ρ ΡΠ°Π²Π½Π° 140 ΠΌΠΌ. ΠΠ»Ρ ΡΠ΄ΠΎΠ±ΡΡΠ²Π° ΠΈ ΡΠΎΡΠ½ΠΎΡΡΠΈ ΠΌΠΎΠΆΠ½ΠΎ ΡΠ΄Π΅Π»Π°ΡΡ ΠΈΠ· ΠΏΡΠΎΡΠΈΠ»Ρ ΡΠ°Π±Π»ΠΎΠ½ Ρ Π½Π΅ΠΎΠ±Ρ ΠΎΠ΄ΠΈΠΌΡΠΌ ΡΠ³Π»ΠΎΠΌ, ΠΏΠΎ ΠΊΠΎΡΠΎΡΠΎΠΌΡ Π±ΡΠ΄ΡΡ ΠΏΡΠΈΠ²Π°ΡΠ΅Π½Ρ Π²ΡΠ΅ ΡΠ΅ΡΡΡΠ΅ ΡΠ°ΡΡΠΈ.
ΠΠΎΠ»ΠΆΠ½ΠΎ ΠΏΠΎΠ»ΡΡΠΈΡΡΡ ΠΏΡΠΈΠ±Π»ΠΈΠ·ΠΈΡΠ΅Π»ΡΠ½ΠΎ ΡΠ°ΠΊ.
Π¨Π°Π³ ΡΠ΅Π΄ΡΠΌΠΎΠΉ.
ΠΡΠΈΠ²Π°ΡΠΈΠ²Π°Π΅ΠΌ ΡΠ³ΠΎΠ»ΠΊΠΈ Π΄Π»Ρ ΡΡΡΠ°Π½ΠΎΠ²ΠΊΠΈ Π³ΡΠ±ΠΎΠΊ, Π΄Π»Ρ Π±ΠΎΠ»Π΅Π΅ ΡΠΎΡΠ½ΠΎΠ³ΠΎ ΠΏΠΎΠ·ΠΈΡΠΈΠΎΠ½ΠΈΡΠΎΠ²Π°Π½ΠΈΡ ΡΡΡΠ³ΠΈΠ²Π°Π΅ΠΌ ΠΈΡ ΡΡΡΡΠ±ΡΠΈΠ½ΠΎΠΉ, ΡΠ°ΠΊ Π³ΡΠ±ΠΊΠΈ Π±ΡΠ΄ΡΡ ΡΠΎΠ²Π½ΡΠ΅ ΠΏΠΎ ΠΎΡΠ½ΠΎΡΠ΅Π½ΠΈΡ Π΄ΡΡΠ³ ΠΊ Π΄ΡΡΠ³Ρ.
ΠΡΠΈΡΠ»ΠΎ Π²ΡΠ΅ΠΌΡ ΠΎΠ±ΡΠΈΡΡ ΠΏΠΎΠ΄Π²ΠΈΠΆΠ½ΡΡ ΠΈ Π½Π΅ΠΏΠΎΠ΄Π²ΠΈΠΆΠ½ΡΡ ΡΠ°ΡΡΠΈ, Π²Π΅ΡΡ Π½ΡΡ Π±ΡΠ΄Π΅Ρ ΡΠ΄Π΅Π»Π°Π½Π° ΠΈΠ· 12 ΠΌΠΌ , Π° Π±ΠΎΠΊΠΎΠ²ΠΈΠ½Π° ΠΈΠ· 6 ΠΌΠΌ Π»ΠΈΡΡΠ° ΠΌΠ΅ΡΠ°Π»Π»Π°. ΠΡΠ΅ Ρ ΠΎΡΠΎΡΠ΅Π½ΡΠΊΠΎ ΠΏΡΠΈΠ²Π°ΡΠΈΠ²Π°Π΅ΠΌ ΠΈ Π·Π°ΡΠΈΡΠ°Π΅ΠΌ ΠΏΡΠΈ ΠΏΠΎΠΌΠΎΡΠΈ ΠΌΠ΅ΡΠ°Π»Π»ΠΈΡΠ΅ΡΠΊΠΎΠΉ ΡΠ΅ΡΠΊΠΈ.
ΠΠ΅ Π·Π°Π±ΡΠ²Π°Π΅ΠΌ ΠΏΡΠΎ Π·Π°ΡΠΈΡΠ½ΡΠ΅ ΠΎΡΠΊΠΈ ΠΏΡΠΈ ΡΠ°Π±ΠΎΡΠ΅. Π’Π°ΠΊ Π²ΡΠ³Π»ΡΠ΄ΡΡ ΡΠΈΡΠΊΠΈ Ρ ΡΠ°Π·Π½ΡΡ ΡΡΠΎΡΠΎΠ½, Π΅ΡΠ΅ Π½ΡΠΆΠ½ΠΎ Π±ΡΠ΄Π΅Ρ ΠΏΡΠΈΠ²Π°ΡΠΈΡΡ 25-ΡΠ΅ ΡΠ³ΠΎΠ»ΠΊΠΈ, ΡΡΠΎΠ±Ρ ΡΠ±ΡΠ°ΡΡ ΠΎΡΡΡΡΠ΅ ΡΠ³Π»Ρ Π² ΠΌΠ΅ΡΡΠ°Ρ ΠΊΡΠ΅ΠΏΠ»Π΅Π½ΠΈΡ Π³ΡΠ±ΠΎΠΊ.


Π¨Π°Π³ Π²ΠΎΡΡΠΌΠΎΠΉ.
ΠΡΠ΅ΠΌΡ ΡΠ΄Π΅Π»Π°ΡΡ ΡΠ°ΠΌΠΈ Π³ΡΠ±ΠΊΠΈ ΡΠΈΡΠΊΠΎΠ², ΠΌΠ°ΡΠ΅ΡΠΈΠ°Π» Π΄Π»Ρ Π½ΠΈΡ Π±ΡΠ» Π²ΡΠ±ΡΠ°Π½ Π½Π΅ ΡΠ»ΡΡΠ°ΠΉΠ½ΠΎ, ΡΠ΅ΡΡΠΎΡΡ Π΄ΠΎΠ²ΠΎΠ»ΡΠ½ΠΎ ΠΏΡΠΎΡΠ½ΡΠ΅ ΠΈ ΠΈΠΌΠ΅ΡΡ ΡΠΎΠ»ΡΠΈΠ½Ρ 12 ΠΌΠΌ, ΡΡΠΎ Π² ΡΠ°ΠΌΡΠΉ ΡΠ°Π· Π΄Π»Ρ ΠΌΠΎΡΠ½ΠΎΠ³ΠΎ ΠΈΠ½ΡΡΡΡΠΌΠ΅Π½ΡΠ°. ΠΠ΅Π»Π°Π΅ΠΌ Π½Π°ΡΠ΅ΡΠΊΠΈ Π΄Π»Ρ Π±ΠΎΠ»Π΅Π΅ Π»ΡΡΡΠ΅Π³ΠΎ ΡΡΠ΅ΠΏΠ»Π΅Π½ΠΈΡ Π΄Π΅ΡΠ°Π»ΠΈ Π² Π±ΡΠ΄ΡΡΠΈΡ ΡΠΈΡΠΊΠ°Ρ ΠΏΡΠΈ ΠΏΠΎΠΌΠΎΡΠΈ Π£Π¨Π Ρ ΠΎΡΡΠ΅Π·Π½ΡΠΌ Π΄ΠΈΡΠΊΠΎΠΌ ΡΠΎΠ»ΡΠΈΠ½ΠΎΠΉ 1 ΠΌΠΌ.
ΠΠ½ΠΈΠΌΠ°Π½ΠΈΠ΅, ΡΠ°Π±ΠΎΡΠ°ΡΡ Ρ Π£Π¨Π Π±Π΅Π· Π·Π°ΡΠΈΡΡ Π½Π΅Π»ΡΠ·Ρ, Π½Π΅ ΡΠΈΡΠΊΡΠΉΡΠ΅ ΠΆΠΈΠ·Π½ΡΡ. ΠΠ°Π»Π΅Π΅ ΡΠ»Π΅Π΄ΡΠ΅Ρ ΠΏΡΠΈΠ²Π°ΡΠΈΡΡ Π³ΡΠ±ΠΊΠΈ ΠΊ ΡΠ³ΠΎΠ»ΠΊΠ°ΠΌ ΠΈ ΡΠΈΡΠΊΠΈ ΡΡΠΈΡΠ°ΠΉ Π³ΠΎΡΠΎΠ²Ρ.
Π’Π°ΠΊ Π²ΡΠ³Π»ΡΠ΄ΡΡ ΡΠΈΡΠΊΠΈ Π±Π΅Π· ΠΏΠΎΠΊΡΠ°ΡΠΊΠΈ.


Π¨Π°Π³ Π΄Π΅Π²ΡΡΡΠΉ.
Π’Π΅ΠΏΠ΅ΡΡ Π·Π°ΠΉΠΌΠ΅ΠΌΡΡ Π²Π½Π΅ΡΠ½ΠΈΠΌ Π²ΠΈΠ΄ΠΎΠΌ ΡΠΈΡΠΊΠΎΠ². Π‘Π½Π°ΡΠ°Π»Π° Π·Π°ΠΊΠ»Π΅ΠΈΠ²Π°Π΅ΠΌ ΠΌΠ΅ΡΡΠ°, ΠΊΠΎΡΠΎΡΡΠ΅ Π½Π΅ Π½ΡΠΆΠ½ΠΎ ΠΊΡΠ°ΡΠΈΡΡ, ΡΡΠΎ Π²ΠΈΠ½Ρ, Π³Π°ΠΉΠΊΠ°, Π³ΡΠ±ΠΊΠΈ ΠΈ ΡΡΠΊΠΎΡΡΡ. ΠΠΎΡΠ»Π΅ ΡΠΎΠ³ΠΎ, ΠΊΠ°ΠΊ Π²ΡΠ΅ Π½Π΅Π½ΡΠΆΠ½ΡΠ΅ Π΄Π»Ρ ΠΏΠΎΠΊΡΠ°ΡΠΊΠΈ Π΄Π΅ΡΠ°Π»ΠΈ Π·Π°ΠΊΠ»Π΅Π΅Π½Ρ ΠΌΠ°Π»ΡΡΠ½ΡΠΌ ΡΠΊΠΎΡΡΠ΅ΠΌ Π½Π°ΡΠΈΠ½Π°Π΅ΠΌ Π³ΡΡΠ½ΡΠΎΠ²Π°ΡΡ ΠΏΠΎΠ²Π΅ΡΡ Π½ΠΎΡΡΡ ΡΠΈΡΠΊΠΎΠ². Π Π΄Π°Π½Π½ΠΎΠΌ ΡΠ»ΡΡΠ°Π΅ ΠΈΡΠΏΠΎΠ»ΡΠ·ΠΎΠ²Π°Π»ΡΡ ΠΊΡΠ°ΡΠΊΠΎΠΏΡΠ»ΡΡ, Π½ΠΎ Π΅ΡΠ»ΠΈ Ρ Π²Π°Ρ Π΅Π³ΠΎ Π½Π΅Ρ, ΡΠ°ΠΊ ΠΆΠ΅ ΠΊΠ°ΠΊ ΠΈ ΠΊΠΎΠΌΠΏΡΠ΅ΡΡΠΎΡΠ°, ΡΠΎ Π±Π°Π»Π»ΠΎΠ½ΡΠΈΠΊ Π³ΡΡΠ½ΡΠΎΠ²ΠΊΠΈ ΠΊΡΠΏΠΈΡΡ Π½Π°ΡΡΠΎΠ»ΡΠΊΠΎ ΠΏΡΠΎΡΡΠΎ, ΠΊΠ°ΠΊ ΠΈ Ρ ΠΊΡΠ°ΡΠΊΠΎΠΉ.
ΠΠΎΠ³Π΄Π° ΡΠ»ΠΎΠΉ Π³ΡΡΠ½ΡΠ° Π²ΡΡΠΎΡ Π½Π΅Ρ ΠΌΠΎΠΆΠ½ΠΎ ΠΊΡΠ°ΡΠΈΡΡ ΡΠΈΡΠΊΠΈ Π² ΡΠ²Π΅Ρ, Π²Π°ΡΠΈΠ°Π½Ρ Ρ ΠΆΠ΅Π»ΡΠΎΠΉ ΠΊΡΠ°ΡΠΊΠΎΠΉ ΠΎΠΊΠ°Π·Π°Π»ΡΡ Π²Π΅ΡΡΠΌΠ° ΡΠ΄Π°ΡΠ½ΡΠΌ, Π° ΡΠ°ΠΌ ΡΠΆ ΠΊΠ°ΠΊ Π²Π°ΡΠ΅ΠΉ Π΄ΡΡΠ΅ ΡΠ³ΠΎΠ΄Π½ΠΎ. ΠΠΎ ΠΎΠΊΠΎΠ½ΡΠ°Π½ΠΈΠΈ ΠΏΠΎΠΊΡΠ°ΡΠΊΠΈ ΡΠΈΡΠΊΠΈ Π³ΠΎΡΠΎΠ²Ρ.
ΠΡΠ΅ΠΌΡ Π½Π° ΡΠ±ΠΎΡΠΊΡ ΡΠΎΡΡΠ°Π²ΠΈΠ»ΠΎ ΠΏΠΎΡΡΠ΄ΠΊΠ° Π΄Π²ΡΡ ΡΠ°Π±ΠΎΡΠΈΡ Π΄Π½Π΅ΠΉ, ΡΡΠΎ ΡΡΠΈΡΠ°Ρ ΠΎΠΏΡΠ°Π²Π΄Π°Π½Π½ΡΠΌ Π΄Π΅ΠΉΡΡΠ²ΠΈΠ΅ΠΌ, ΡΡΠΈΡΡΠ²Π°Ρ ΠΊΠ°ΠΊΠΈΠ΅ ΠΌΠΎΡΠ½ΡΠ΅ ΡΠΈΡΠΊΠΈ ΠΏΠΎΠ»ΡΡΠΈΠ»ΠΈΡΡ. Π’Π°ΠΊΠΆΠ΅ ΠΎΠ½ΠΈ Π½Π΅ Π»ΠΈΡΠ΅Π½Ρ ΠΏΠ»ΡΡΠΎΠ², Π·Π΄Π΅ΡΡ ΠΌΠΎΠΆΠ½ΠΎ Π·Π°ΠΆΠ°ΡΡ, Π½Π°ΠΏΡΠΈΠΌΠ΅Ρ, ΠΊΠ»Π°ΠΏΠ°Π½, ΡΠ°ΠΊ ΠΊΠ°ΠΊ ΠΏΠΎΠ΄ Π³ΡΠ±ΠΊΠ°ΠΌΠΈ Π΅ΡΡΡ Π½Π΅ΠΌΠ½ΠΎΠ³ΠΎ ΠΏΡΠΎΡΡΡΠ°Π½ΡΡΠ²Π° Π΄Π»Ρ ΡΠΈΠΊΡΠ°ΡΠΈΠΈ ΡΠ°ΠΊΠΈΡ Π΄Π΅ΡΠ°Π»Π΅ΠΉ, Π½Ρ Π° ΠΏΠΎΠ΄Π²ΠΈΠΆΠ½Π°Ρ ΠΏΠ΅ΡΠ΅Π΄Π½ΡΡ ΡΠ°ΡΡΡ Π΄Π°Π΅Ρ Π²ΠΎΠ·ΠΌΠΎΠΆΠ½ΠΎΡΡΡ Π·Π°ΠΆΠ°ΡΡ Π΄Π»ΠΈΠ½Π½ΡΡ Π΄Π΅ΡΠ°Π»Ρ Π²ΠΏΠ»ΠΎΡΡ Π΄ΠΎ ΠΏΠΎΠ»Π°, Π½Π΅ ΡΠΏΠΈΡΠ°ΡΡΡ Π² Π²Π΅ΡΡΡΠ°ΠΊ, ΠΊΠ°ΠΊ ΡΡΠΎ ΡΠ΄Π΅Π»Π°Π½ΠΎ Π² Π½Π΅ΠΊΠΎΡΠΎΡΡΡ Π·Π°Π²ΠΎΠ΄ΡΠΊΠΈΡ ΡΠΈΡΠΊΠ°Ρ .
ΠΠ° ΡΡΠΎΠΌ Ρ ΠΌΠ΅Π½Ρ Π²ΡΠ΅, Π²ΡΠ΅ΠΌ ΡΠΏΠ°ΡΠΈΠ±ΠΎ Π·Π° Π²Π½ΠΈΠΌΠ°Π½ΠΈΠ΅ ΠΈ ΡΠ΄Π°ΡΠ½ΡΡ ΡΠ°ΠΌΠΎΠ΄Π΅Π»ΠΎΠΊ.
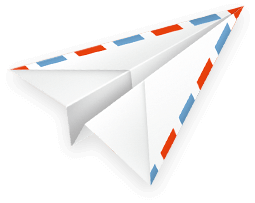
ΠΠΎΠ»ΡΡΠ°ΠΉΡΠ΅ Π½Π° ΠΏΠΎΡΡΡ ΠΏΠΎΠ΄Π±ΠΎΡΠΊΡ Π½ΠΎΠ²ΡΡ ΡΠ°ΠΌΠΎΠ΄Π΅Π»ΠΎΠΊ. ΠΠΈΠΊΠ°ΠΊΠΎΠ³ΠΎ ΡΠΏΠ°ΠΌΠ°, ΡΠΎΠ»ΡΠΊΠΎ ΠΏΠΎΠ»Π΅Π·Π½ΡΠ΅ ΠΈΠ΄Π΅ΠΈ!
*ΠΠ°ΠΏΠΎΠ»Π½ΡΡ ΡΠΎΡΠΌΡ Π²Ρ ΡΠΎΠ³Π»Π°ΡΠ°Π΅ΡΠ΅ΡΡ Π½Π° ΠΎΠ±ΡΠ°Π±ΠΎΡΠΊΡ ΠΏΠ΅ΡΡΠΎΠ½Π°Π»ΡΠ½ΡΡ Π΄Π°Π½Π½ΡΡ
Π‘ΡΠ°Π½ΠΎΠ²ΠΈΡΠ΅ΡΡ Π°Π²ΡΠΎΡΠΎΠΌ ΡΠ°ΠΉΡΠ°, ΠΏΡΠ±Π»ΠΈΠΊΡΠΉΡΠ΅ ΡΠΎΠ±ΡΡΠ²Π΅Π½Π½ΡΠ΅ ΡΡΠ°ΡΡΠΈ, ΠΎΠΏΠΈΡΠ°Π½ΠΈΡ ΡΠ°ΠΌΠΎΠ΄Π΅Π»ΠΎΠΊ Ρ ΠΎΠΏΠ»Π°ΡΠΎΠΉ Π·Π° ΡΠ΅ΠΊΡΡ. ΠΠΎΠ΄ΡΠΎΠ±Π½Π΅Π΅ Π·Π΄Π΅ΡΡ.Π ΡΡΠ½ΡΠ΅ ΡΠΈΡΠΊΠΈ ΡΠ²ΠΎΠΈΠΌΠΈ ΡΡΠΊΠ°ΠΌΠΈ

ΠΡΠΈΠ²Π΅Ρ Π²ΡΠ΅ΠΌ Π»ΡΠ±ΠΈΡΠ΅Π»ΡΠΌ ΡΠ°ΠΌΠΎΠ΄Π΅Π»ΠΎΠΊ. Π ΠΊΠ°ΠΆΠ΄ΠΎΠΉ ΠΌΠ°ΡΡΠ΅ΡΡΠΊΠΎΠΉ Π΄ΠΎΠ»ΠΆΠ½Ρ Π±ΡΡΡ ΡΠ»Π΅ΡΠ°ΡΠ½ΡΠ΅ ΡΠΈΡΠΊΠΈ, ΡΠ°ΠΊ ΠΊΠ°ΠΊ Π±Π΅Π· Π½ΠΈΡ Π½ΠΈΠΊΡΠ΄Π°, Π½ΠΎ Π±ΡΠ²Π°ΡΡ ΡΠ°ΠΊΠΈΠ΅ ΡΠ»ΡΡΠ°ΠΈ, ΠΊΠΎΠ³Π΄Π° Π½ΡΠΆΠ½ΠΎ Π·Π°ΡΠΈΠΊΡΠΈΡΠΎΠ²Π°ΡΡ Π΄Π΅ΡΠ°Π»Ρ ΠΏΡΠ΅ΠΈΠΌΡΡΠ΅ΡΡΠ²Π΅Π½Π½ΠΎ Ρ ΠΏΠ»ΠΎΡΠΊΠΎΠΉ ΡΠΎΡΠΌΠΎΠΉ, Π½Π°ΠΏΡΠΈΠΌΠ΅Ρ, ΠΏΡΠΈΠΆΠ°ΡΡ Π΄Π²Π° Π»ΠΈΡΡΠ° ΠΈ ΡΠ²Π°ΡΠΈΡΡ Π΄ΡΡΠ³ Ρ Π΄ΡΡΠ³ΠΎΠΌ, Π²ΠΎΡ ΠΊΠ°ΠΊ ΡΠ°Π· Π² ΡΡΠΎΠΌ ΡΠ»ΡΡΠ°Π΅ ΠΏΠΎΠΌΠΎΠ³ΡΡ ΡΡΡΠ½ΡΠ΅ ΡΠΈΡΠΊΠΈ. Π Π΄Π°Π½Π½ΠΎΠΉ ΡΡΠ°ΡΡΠ΅ Ρ ΡΠ°ΡΡΠΊΠ°ΠΆΡ, ΠΊΠ°ΠΊ ΡΠ΄Π΅Π»Π°ΡΡ ΡΡΡΠ½ΡΠ΅ ΡΠΈΡΠΊΠΈ ΡΠ²ΠΎΠΈΠΌΠΈ ΡΡΠΊΠ°ΠΌΠΈ, ΠΊΠΎΡΠΎΡΡΠ΅ Π½Π΅ ΠΏΠΎΡΡΠ΅Π±ΡΡΡ ΠΎΡ Π²Π°Ρ ΠΊΠ°ΠΊΠΈΡ -Π»ΠΈΠ±ΠΎ Π½Π°Π²ΡΠΊΠΎΠ², Π° ΡΠ°ΠΊΠΆΠ΅ Π·Π°ΡΡΠ°Ρ, ΡΠ°ΠΊΠΎΠ΅ ΠΏΡΠΈΡΠΏΠΎΡΠΎΠ±Π»Π΅Π½ΠΈΠ΅ ΠΌΠΎΠΆΠ΅Ρ ΠΏΠΎΠ·Π²ΠΎΠ»ΠΈΡΡ Π»ΡΠ±ΠΎΠΉ Π½Π°ΡΠΈΠ½Π°ΡΡΠΈΠΉ.
ΠΠ΅ΡΠ΅Π΄ ΡΠ΅ΠΌ, ΠΊΠ°ΠΊ ΠΏΡΠΎΡΠΈΡΠ°ΡΡ ΠΏΠΎΡΠ°Π³ΠΎΠ²ΡΡ ΡΠ±ΠΎΡΠΊΡ Π΄Π°Π½Π½ΠΎΠΉ ΡΠ°ΠΌΠΎΠ΄Π΅Π»ΠΊΠΈ, ΠΏΡΠ΅Π΄Π»Π°Π³Π°Ρ ΠΏΠΎΡΠΌΠΎΡΡΠ΅ΡΡ Π²ΠΈΠ΄Π΅ΠΎ, Π³Π΄Π΅ Π½Π°Π³Π»ΡΠ΄Π½ΠΎ ΠΏΠΎΠΊΠ°Π·Π°Π½ΠΎ, ΠΊΠ°ΠΊ ΠΈ ΠΈΠ· ΡΠ΅Π³ΠΎ ΡΠ΄Π΅Π»Π°ΡΡ ΡΠ°ΠΊΠΈΠ΅ ΡΡΡΠ½ΡΠ΅ ΡΠΈΡΠΊΠΈ, Π° ΡΠ°ΠΊΠΆΠ΅ ΠΈΡ ΡΠ΅ΡΡΠΈΡΠΎΠ²Π°Π½ΠΈΠ΅.
ΠΠ»Ρ ΡΠΎΠ³ΠΎ, ΡΡΠΎΠ±Ρ ΡΠ΄Π΅Π»Π°ΡΡ ΡΡΡΠ½ΡΠ΅ ΡΠΈΡΠΊΠΈ ΡΠ²ΠΎΠΈΠΌΠΈ ΡΡΠΊΠ°ΠΌΠΈ, ΠΏΠΎΠ½Π°Π΄ΠΎΠ±ΠΈΡΡΡ:
* ΠΡΠΎΡΠΈΠ»ΡΠ½Π°Ρ ΡΡΡΠ±Π° 20 ΠΌΠΌ ΠΈ 25 ΠΌΠΌ
* ΠΠ½ΠΊΠ΅ΡΠ½ΡΠΉ Π±ΠΎΠ»Ρ
* ΠΡΡΠ΅Π·Π½ΠΎΠΉ ΡΡΠ°Π½ΠΎΠΊ ΠΏΠΎ ΠΌΠ΅ΡΠ°Π»Π»Ρ ΠΈΠ»ΠΈ Π£Π¨Π
* Π‘Π²Π°ΡΠΎΡΠ½ΡΠΉ Π°ΠΏΠΏΠ°ΡΠ°Ρ, ΡΠ»Π΅ΠΊΡΡΠΎΠ΄Ρ
* ΠΠ°ΡΠΈΡΠ½ΡΠ΅ ΠΎΡΠΊΠΈ, ΠΊΡΠ°Π³ΠΈ, ΡΠ²Π°ΡΠΎΡΠ½Π°Ρ ΠΌΠ°ΡΠΊΠ°
* ΠΠΈΡΡ ΠΌΠ΅ΡΠ°Π»Π»Π° ΡΠΎΠ»ΡΠΈΠ½ΠΎΠΉ 3 ΠΌΠΌ
* ΠΠΎΡΡΠ½Π΅Π²ΠΎΠΉ ΠΏΠ°Π»Π΅Ρ
Π¨Π°Π³ ΠΏΠ΅ΡΠ²ΡΠΉ.
ΠΠ΅ΡΠ²ΡΠΌ Π΄Π΅Π»ΠΎΠΌ Π½ΡΠΆΠ½ΠΎ ΡΠ΄Π΅Π»Π°ΡΡ ΠΈΠ· ΠΏΡΠΎΡΠΈΠ»ΡΠ½ΡΠΉ ΡΡΡΠ± ΠΊΠ°ΡΠΊΠ°Ρ. ΠΡΠΈ ΠΏΠΎΠΌΠΎΡΠΈ ΡΠ³Π»ΠΎΡΠ»ΠΈΡΠΎΠ²Π°Π»ΡΠ½ΠΎΠΉ ΠΌΠ°ΡΠΈΠ½ΠΊΠΈ ΠΈΠ»ΠΈ ΠΎΡΡΠ΅Π·Π½ΠΎΠ³ΠΎ ΡΡΠ°Π½ΠΊΠ° ΠΏΠΎ ΠΌΠ΅ΡΠ°Π»Π»Ρ Π²ΡΡΠ΅Π·Π°Π΅ΠΌ ΡΠ°ΡΡΠΈ ΡΡΡΠ½ΡΡ
ΡΠΈΡΠΊΠΎΠ² ΠΈΠ· ΠΏΡΠΎΡΠΈΠ»ΡΠ½ΠΎΠΉ ΡΡΡΠ±Ρ 25 ΠΌΠΌ. Π ΠΈΡΠΎΠ³Π΅ Π΄ΠΎΠ»ΠΆΠ½ΠΎ ΠΏΠΎΠ»ΡΡΠΈΡΡΡ ΠΏΡΠΈΠΌΠ΅ΡΠ½ΠΎ ΡΠ°ΠΊ.

ΠΠΎΠ½ΡΡΡΡΠΊΡΠΈΡ ΠΌΠΎΠΆΠ½ΠΎ ΠΈΠ·ΠΌΠ΅Π½ΡΡΡ Π² Π·Π°Π²ΠΈΡΠΈΠΌΠΎΡΡΠΈ ΠΎΡ ΡΠ°Π·ΠΌΠ΅ΡΠΎΠ² Π·Π°ΠΆΠΈΠΌΠ°Π΅ΠΌΡΡ Π΄Π΅ΡΠ°Π»Π΅ΠΉ, Π° ΡΠ°ΠΊΠΆΠ΅ Π΄Π»ΠΈΠ½Ρ Π±ΠΎΠ»ΡΠ°, ΡΠ°ΠΊ ΠΊΠ°ΠΊ Ρ ΠΎΠ΄ ΠΏΡΠΈ ΡΡΠΎΠΌ ΡΠΎΠΆΠ΅ ΠΈΠ·ΠΌΠ΅Π½ΠΈΡΡΡ.
ΠΡΠΈ ΡΠ°Π±ΠΎΡΠ΅ Ρ ΡΠ³Π»ΠΎΡΠ»ΠΈΡΠΎΠ²Π°Π»ΡΠ½ΠΎΠΉ ΠΌΠ°ΡΠΈΠ½ΠΊΠΎΠΉ Π±ΡΠ΄ΡΡΠ΅ ΠΎΡΡΠΎΡΠΎΠΆΠ½Ρ, Π½Π΅ Π·Π°Π±ΡΠ²Π°ΠΉΡΠ΅ ΠΎ ΠΌΠ΅ΡΠ°Ρ Π±Π΅Π·ΠΎΠΏΠ°ΡΠ½ΠΎΡΡΠΈ, Π·Π°ΡΠΈΡΠ½ΡΠ΅ ΠΎΡΠΊΠΈ ΠΎΠ±ΡΠ·Π°ΡΠ΅Π»ΡΠ½Ρ, ΡΠ°ΠΊΠΆΠ΅ Π½Π΅ ΡΠ°Π±ΠΎΡΠ°ΠΉΡΠ΅ Ρ Π£Π¨Π Π±Π΅Π· Π·Π°ΡΠΈΡΡ Π΄ΠΈΡΠΊΠ°.
Π¨Π°Π³ Π²ΡΠΎΡΠΎΠΉ.
Π’Π΅ΠΏΠ΅ΡΡ Π½ΡΠΆΠ½ΠΎ ΡΠ΄Π΅Π»Π°ΡΡ ΠΏΠΎΠ΄Π²ΠΈΠΆΠ½ΡΡ ΡΠ°ΡΡΡ, Π΅Π΅ Π΄Π΅Π»Π°Π΅ΠΌ ΠΈΠ· ΠΏΡΠΎΡΠΈΠ»ΡΠ½ΠΎΠΉ ΡΡΡΠ±Ρ 20 ΠΌΠΌ, ΡΠΎΠ»ΡΠΈΠ½ΠΎΠΉ ΠΆΠ΅Π»Π°ΡΠ΅Π»ΡΠ½ΠΎ 1,5 ΠΈΠ»ΠΈ ΠΆΠ΅ 2 ΠΌΠΌ, Π² Π΄Π°Π½Π½ΠΎΠΌ ΡΠ»ΡΡΠ°Π΅ Π½Π°ΡΠ»Π°ΡΡ ΡΠΎΠ»ΡΠΊΠΎ 1,2 ΠΌΠΌ, ΡΡΠΎ Π½Π΅ ΠΎΡΠ΅Π½Ρ Ρ
ΠΎΡΠΎΡΠΎ, ΡΠ°ΠΊ ΠΊΠ°ΠΊ Π²Π°ΡΠΈΡΡ ΡΠ°ΠΊΠΎΠΉ ΠΌΠ΅ΡΠ°Π»Π» ΡΠ»ΠΎΠΆΠ½Π΅Π΅.



ΠΠ»ΠΈΠ½Ρ ΠΏΠΎΠ΄Π²ΠΈΠΆΠ½ΠΎΠΉ ΡΠ°ΡΡΠΈ Π΄Π΅Π»Π°Π΅ΠΌ ΡΠ°ΠΊΠΎΠΉ, ΡΡΠΎΠ±Ρ ΠΏΡΠΈ Π΅Π΅ ΠΌΠ°ΠΊΡΠΈΠΌΠ°Π»ΡΠ½ΠΎΠΌ Π²ΡΠ»Π΅ΡΠ΅ ΠΈΠ· ΡΡΡΠ±Ρ 25 ΠΌΠΌ Π±ΠΎΠ»ΡΡΠΈΡ Π»ΡΡΡΠΎΠ² Π½Π΅ Π½Π°Π±Π»ΡΠ΄Π°Π»ΠΎΡΡ, ΠΈΠ½Π°ΡΠ΅ ΠΏΡΠΈ Π·Π°ΠΆΠΈΠΌΠ΅ Π±ΡΠ΄ΡΡ Π±ΠΎΠ»ΡΡΠΈΠ΅ ΠΏΠ΅ΡΠ΅ΠΊΠΎΡΡ. ΠΠ°Π»Π΅Π΅ ΠΊ ΡΡΡΠ±Π΅ 25 ΠΌΠΌ ΠΏΡΠΈΠ²Π°ΡΠΈΠ²Π°Π΅ΠΌ Π³Π°ΠΉΠΊΡ, Π° Π½Π° Π³ΠΎΠ»ΠΎΠ²ΠΊΡ Π°Π½ΠΊΠ΅ΡΠ½ΠΎΠ³ΠΎ Π±ΠΎΠ»ΡΠ° ΠΏΡΠΈΠ²Π°ΡΠΈΠ²Π°Π΅ΠΌ ΠΏΠΎΡΡΠ½Π΅Π²ΠΎΠΉ ΠΏΠ°Π»Π΅Ρ, ΠΏΠΎΡΠ»Π΅ ΡΠ΅Π³ΠΎ Π½ΡΠΆΠ½ΠΎ Π±ΡΠ΄Π΅Ρ ΠΏΠΎΠ΄ΠΎΠ±ΡΠ°ΡΡ ΡΠΏΠΈΠ»ΡΠΊΡ ΠΈΠ»ΠΈ Π±ΠΎΠ»Ρ, ΠΊΠΎΡΠΎΡΡΠΌ ΠΈ Π±ΡΠ΄Π΅Ρ Π·Π°ΠΊΡΡΡΠΈΠ²Π°ΡΡ ΠΏΠΎΠ²ΠΈΠΆΠ½ΡΠΉ ΠΌΠ΅Ρ Π°Π½ΠΈΠ·ΠΌ. Π 20-ΠΎΠΉ ΠΏΡΠΎΡΠΈΠ»ΡΠ½ΠΎΠΉ ΡΡΡΠ±Π΅ ΠΏΡΠΈΠ²Π°ΡΠΈΠ²Π°Π΅ΠΌ Ρ ΠΎΠ΄Π½ΠΎΠΉ ΡΡΠΎΡΠΎΠ½Ρ Π»Π°ΠΏΠΊΡ ΠΈΠ· Π»ΠΈΡΡΠΎΠ²ΠΎΠ³ΠΎ ΠΌΠ΅ΡΠ°Π»Π»Π° ΡΠΎΠ»ΡΠΈΠ½ΠΎΠΉ 3 ΠΌΠΌ, Π° ΠΊ Π΄ΡΡΠ³ΠΎΠΌΡ ΠΊΠΎΠ½ΡΡ ΠΏΡΠΈΠ²Π°ΡΠΈΠ²Π°Π΅ΠΌ ΠΊΡΡΠ³Π»ΡΠΊ ΠΈΠ»ΠΈ ΡΠ°ΡΠΈΠΊ ΠΎΡ ΠΏΠΎΠ΄ΡΠΈΠΏΠ½ΠΈΠΊΠ°, ΠΊΡΠ΄Π° ΠΈ Π±ΡΠ΄Π΅Ρ Π΄Π°Π²ΠΈΡΡ Π±ΠΎΠ»Ρ Π² ΠΌΠΎΠΌΠ΅Π½Ρ ΠΏΡΠΈΠΆΠΈΠΌΠ°.




Π‘ΠΎΠ±Π»ΡΠ΄Π°ΠΉΡΠ΅ ΠΌΠ΅ΡΡ Π±Π΅Π·ΠΎΠΏΠ°ΡΠ½ΠΎΡΡΠΈ ΠΏΡΠΈ ΡΠ²Π°ΡΠΊΠ΅ Π΄Π΅ΡΠ°Π»Π΅ΠΉ, ΠΎΠ΄Π΅Π²Π°ΠΉΡΠ΅ Π·Π°ΡΠΈΡΠ½ΡΡ ΡΠ²Π°ΡΠΎΡΠ½ΡΡ ΠΌΠ°ΡΠΊΡ ΠΈ ΠΊΡΠ°Π³ΠΈ, ΡΡΠΎΠ±Ρ ΠΈΠ·Π±Π΅ΠΆΠ°ΡΡ ΠΎΠΆΠΎΠ³ΠΎΠ² ΠΈ Π½Π΅ ΡΠ»ΠΎΠ²ΠΈΡΡ «Π·Π°ΠΉΡΠΈΠΊΠΎΠ²»
Π¨Π°Π³ ΡΡΠ΅ΡΠΈΠΉ.
Π Π°Π½Π΅Π΅ Π²ΡΠΏΠΈΠ»Π΅Π½Π½ΡΠΉ ΠΊΠ°ΡΠΊΠ°Ρ ΡΠ²Π°ΡΠΈΠ²Π°Π΅ΠΌ Π² Π΅Π΄ΠΈΠ½ΠΎΠ΅ ΡΠ΅Π»ΠΎΠΌ, Π² ΠΈΡΠΎΠ³Π΅ Π΄ΠΎΠ»ΠΆΠ½ΠΎ ΠΏΠΎΠ»ΡΡΠΈΡΡΡ ΡΠ°ΠΊ.

Π‘Π²Π°ΡΠΎΡΠ½ΡΠ΅ ΡΠ²Ρ Π·Π°ΡΠΈΡΠ°Π΅ΠΌ ΠΏΡΠΈ ΠΏΠΎΠΌΠΎΡΠΈ ΡΠ³Π»ΠΎΡΠ»ΠΈΡΠΎΠ²Π°Π»ΡΠ½ΠΎΠΉ ΠΌΠ°ΡΠΈΠ½ΠΊΠΈ Ρ ΡΡΡΠ°Π½ΠΎΠ²Π»Π΅Π½Π½ΡΠΌ ΡΠ»ΠΈΡΠΎΠ²Π°Π»ΡΠ½ΡΠΌ ΠΊΡΡΠ³ΠΎΠΌ.
ΠΠ° Π½Π΅ΠΏΠΎΠ΄Π²ΠΈΠΆΠ½ΡΡ Π»Π°ΠΏΠΊΡ ΠΏΡΠΈΠ²Π°ΡΠΈΠ²Π°Π΅ΠΌ ΡΠ°ΠΊΠΎΠΉ ΠΆΠ΅ Π»ΠΈΡΡ ΠΌΠ΅ΡΠ°Π»Π»Π°. ΠΠ»Ρ Π±ΠΎΠ»ΡΡΠ΅ΠΉ ΡΠ΅ΠΏΠΊΠΎΡΡΠΈ ΠΌΠΎΠΆΠ½ΠΎ ΡΠ΄Π΅Π»Π°ΡΡ Π½Π° Π½ΠΈΡ Π½Π°ΡΠ΅ΡΠΊΠΈ, Π²ΠΎΡΠΏΠΎΠ»ΡΠ·ΠΎΠ²Π°Π²ΡΠΈΡΡ ΡΠ³Π»ΠΎΡΠ»ΠΈΡΠΎΠ²Π°Π»ΡΠ½ΠΎΠΉ ΠΌΠ°ΡΠΈΠ½ΠΊΠΎΠΉ.
Π¨Π°Π³ ΡΠ΅ΡΠ²Π΅ΡΡΡΠΉ.
Π’Π΅ΠΏΠ΅ΡΡ ΡΡΡΡΠΎΠΉΡΡΠ²ΠΎ ΠΏΠΎΠ»Π½ΠΎΡΡΡΡ Π³ΠΎΡΠΎΠ²ΠΎ, Π° Π·Π½Π°ΡΠΈΡ ΠΏΡΠΈΡΠ»ΠΎ Π²ΡΠ΅ΠΌΡ ΠΏΡΠΎΠ²Π΅ΡΠΈΡΡ Π΅Π³ΠΎ Π½Π° ΡΠ°Π±ΠΎΡΠΎΡΠΏΠΎΡΠΎΠ±Π½ΠΎΡΡΡ. ΠΡΠ±ΠΈΡΠ°Π΅ΠΌ Π΄Π΅ΡΠ°Π»Ρ, ΠΊΠΎΡΠΎΡΡΡ ΠΆΠ΅Π»Π°Π΅ΠΌ Π·Π°ΡΠΈΠΊΡΠΈΡΠΎΠ²Π°ΡΡ ΠΈ ΠΏΡΠΈ ΠΏΠΎΠΌΠΎΡΠΈ ΡΠΏΠΈΠ»ΡΠΊΠΈ, Π²ΡΡΠ°Π²Π»Π΅Π½Π½ΠΎΠΉ Π² ΠΏΠΎΡΡΠ½Π΅Π²ΠΎΠΉ ΠΏΠ°Π»Π΅Ρ Π½Π° Π±ΠΎΠ»ΡΠ΅ ΠΏΡΠΈΠΆΠΈΠΌΠ°Π΅ΠΌ ΠΏΠΎΠ΄Π²ΠΈΠΆΠ½ΡΡ ΡΠ°ΡΡΡ, Π² ΡΠ»Π΅Π΄ΡΡΠ²ΠΈΠΈ ΡΠ΅Π³ΠΎ Π½ΡΠΆΠ½Π°Ρ Π΄Π΅ΡΠ°Π»Ρ ΠΏΡΠΎΡΠ½ΠΎ ΡΠΈΠΊΡΠΈΡΡΠ΅ΡΡΡ, ΠΏΠΎΡΠ»Π΅ ΡΠ΅Π³ΠΎ Ρ Π½Π΅ΠΉ ΠΌΠΎΠΆΠ½ΠΎ ΡΠ°Π±ΠΎΡΠ°ΡΡ, Π²Π°ΡΠΈΡΡ, ΠΎΠ±ΡΠ°Π±Π°ΡΡΠ²Π°ΡΡ ΠΈΠ»ΠΈ Π΄Π΅Π»Π°ΡΡ ΠΊΠ°ΠΊΠΎΠ³ΠΎ-Π»ΠΈΠ±ΠΎ ΡΠΎΠ΄Π° ΡΠΊΠ»Π΅ΠΉΠΊΡ. ΠΠΎΠ΄Π²ΠΈΠΆΠ½Π°Ρ ΡΠ°ΡΡΡ ΡΠ°Π·ΠΆΠΈΠΌΠ°Π΅ΡΡΡ ΠΏΡΠΈ ΠΎΡΠ»Π°Π±Π»Π΅Π½ΠΈΠΈ Π½Π°ΡΡΠΆΠΊΠΈ Π±ΠΎΠ»ΡΠ° ΠΈ ΠΎΠ±ΡΠ°ΡΠ½ΠΎΠ³ΠΎ Ρ
ΠΎΠ΄Π° Π½Π΅ ΠΈΠΌΠ΅Π΅Ρ.
ΠΠ° ΡΡΠΎΠΌ Ρ ΠΌΠ΅Π½Ρ Π²ΡΠ΅, Π²ΡΠ΅ΠΌ ΡΠΏΠ°ΡΠΈΠ±ΠΎ Π·Π° Π²Π½ΠΈΠΌΠ°Π½ΠΈΠ΅ ΠΈ ΡΠ²ΠΎΡΡΠ΅ΡΠΊΠΈΡ ΡΡΠΏΠ΅Ρ ΠΎΠ².
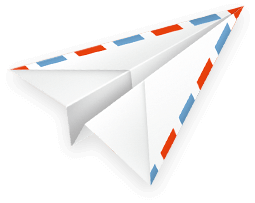
ΠΠΎΠ»ΡΡΠ°ΠΉΡΠ΅ Π½Π° ΠΏΠΎΡΡΡ ΠΏΠΎΠ΄Π±ΠΎΡΠΊΡ Π½ΠΎΠ²ΡΡ ΡΠ°ΠΌΠΎΠ΄Π΅Π»ΠΎΠΊ. ΠΠΈΠΊΠ°ΠΊΠΎΠ³ΠΎ ΡΠΏΠ°ΠΌΠ°, ΡΠΎΠ»ΡΠΊΠΎ ΠΏΠΎΠ»Π΅Π·Π½ΡΠ΅ ΠΈΠ΄Π΅ΠΈ!
*ΠΠ°ΠΏΠΎΠ»Π½ΡΡ ΡΠΎΡΠΌΡ Π²Ρ ΡΠΎΠ³Π»Π°ΡΠ°Π΅ΡΠ΅ΡΡ Π½Π° ΠΎΠ±ΡΠ°Π±ΠΎΡΠΊΡ ΠΏΠ΅ΡΡΠΎΠ½Π°Π»ΡΠ½ΡΡ Π΄Π°Π½Π½ΡΡ
Π‘ΡΠ°Π½ΠΎΠ²ΠΈΡΠ΅ΡΡ Π°Π²ΡΠΎΡΠΎΠΌ ΡΠ°ΠΉΡΠ°, ΠΏΡΠ±Π»ΠΈΠΊΡΠΉΡΠ΅ ΡΠΎΠ±ΡΡΠ²Π΅Π½Π½ΡΠ΅ ΡΡΠ°ΡΡΠΈ, ΠΎΠΏΠΈΡΠ°Π½ΠΈΡ ΡΠ°ΠΌΠΎΠ΄Π΅Π»ΠΎΠΊ Ρ ΠΎΠΏΠ»Π°ΡΠΎΠΉ Π·Π° ΡΠ΅ΠΊΡΡ. ΠΠΎΠ΄ΡΠΎΠ±Π½Π΅Π΅ Π·Π΄Π΅ΡΡ.Π΄Π΅ΡΠ΅Π²ΡΠ½Π½ΡΠ΅, ΠΈΠ· ΠΏΡΠΎΡΠΈΠ»ΡΠ½ΠΎΠΉ ΡΡΡΠ±Ρ ΠΈ ΠΌΠ΅ΡΠ°Π»Π»Π°
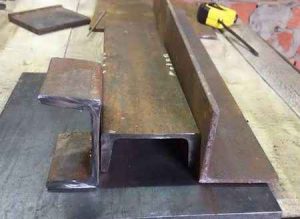
ΠΠ°ΠΊ ΡΠ΄Π΅Π»Π°ΡΡ ΡΠΈΡΠΊΠΈ ΡΠ²ΠΎΠΈΠΌΠΈ ΡΡΠΊΠ°ΠΌΠΈ
Π‘ΠΎΠ΄Π΅ΡΠΆΠ°Π½ΠΈΠ΅ ΡΡΠ°ΡΡΠΈ
ΠΠ±ΠΎΠΉΡΠΈΡΡ Π±Π΅Π· ΡΠΈΡΠΊΠΎΠ² ΠΎΡΠ΅Π½Ρ ΡΠ»ΠΎΠΆΠ½ΠΎ, Π²Π΅Π΄Ρ ΠΈΠΌΠ΅Π½Π½ΠΎ ΡΡΠΎ ΠΏΡΠΈΡΠΏΠΎΡΠΎΠ±Π»Π΅Π½ΠΈΠ΅ ΠΏΠΎΠ·Π²ΠΎΠ»ΡΠ΅Ρ Π½Π°ΠΊΡΠ΅ΠΏΠΊΠΎ Π·Π°ΡΠΈΠΊΡΠΈΡΠΎΠ²Π°ΡΡ ΡΡΠΎ-Π»ΠΈΠ±ΠΎ. ΠΠ΅Π²Π°ΠΆΠ½ΠΎ, ΡΡΠΎ ΠΏΡΠΈΡ ΠΎΠ΄ΠΈΡΡΡ Π΄Π΅Π»Π°ΡΡ, ΡΠ²Π΅ΡΠ»ΠΈΡΡ, ΡΠ΅Π·Π°ΡΡ ΠΈΠ»ΠΈ ΡΠ»ΠΈΡΠΎΠ²Π°ΡΡ β ΡΠΈΡΠΊΠΈ Π΄Π°ΡΡ Π²ΠΎΠ·ΠΌΠΎΠΆΠ½ΠΎΡΡΡ Π΄Π΅Π»Π°ΡΡ ΡΡΠΎ Π±ΡΡΡΡΠΎ ΠΈ Π³Π»Π°Π²Π½ΠΎΠ΅ Π±Π΅Π·ΠΎΠΏΠ°ΡΠ½ΠΎ.Π‘Π΅Π³ΠΎΠ΄Π½Ρ ΠΊΡΠΏΠΈΡΡ ΡΠΈΡΠΊΠΈ Π½Π΅ ΠΏΡΠΎΠ±Π»Π΅ΠΌΠ°, Π±ΡΠ»ΠΈ Π±Ρ Π΄Π΅Π½ΡΠ³ΠΈ ΠΈ ΠΆΠ΅Π»Π°Π½ΠΈΠ΅. ΠΠ΄Π½Π°ΠΊΠΎ ΠΌΠ½ΠΎΠ³ΠΈΠ΅ Π΄ΠΎΠΌΠ°ΡΠ½ΠΈΠ΅ ΠΌΠ°ΡΡΠ΅ΡΠ° Π½Π΅ ΠΎΡΡΠ°Π½Π°Π²Π»ΠΈΠ²Π°ΡΡΡΡ Π½Π° ΡΡΠΎΠΌ, ΠΎΠ½ΠΈ Π΄Π΅Π»Π°ΡΡ ΡΠΈΡΠΊΠΈ ΡΠ²ΠΎΠΈΠΌΠΈ ΡΡΠΊΠ°ΠΌΠΈ. ΠΠΌΠ΅Π½Π½ΠΎ ΠΎ ΡΠΎΠΌ, ΠΊΠ°ΠΊ ΡΠ΄Π΅Π»Π°ΡΡ ΠΏΡΠΎΡΡΡΠ΅, Π½ΠΎ ΡΠ΄ΠΎΠ±Π½ΡΠ΅ Π² ΡΠ°Π±ΠΎΡΠ΅ ΡΠΈΡΠΊΠΈ, Π±ΡΠ΄Π΅Ρ ΡΠ°ΡΡΠΊΠ°Π·Π°Π½ΠΎ Π² Π΄Π°Π½Π½ΠΎΠΌ ΠΎΠ±Π·ΠΎΡΠ΅ ΡΡΡΠΎΠΈΡΠ΅Π»ΡΠ½ΠΎΠ³ΠΎ ΠΆΡΡΠ½Π°Π»Π° samastroyka.ru.
Π Π°Π·Π»ΠΈΡΠ½ΡΠ΅ Π²Π°ΡΠΈΠ°Π½ΡΡ ΡΠ°ΠΌΠΎΠ΄Π΅Π»ΡΠ½ΡΡ ΡΠΈΡΠΊΠΎΠ²
Π’ΠΈΡΠΊΠΈ ΠΏΡΠ΅Π΄ΡΡΠ°Π²Π»ΡΡΡ ΡΠΎΠ±ΠΎΠΉ ΠΏΡΠΎΡΡΡΡ ΠΊΠΎΠ½ΡΡΡΡΠΊΡΠΈΡ, ΠΊΠΎΡΠΎΡΠ°Ρ ΡΠΎΡΡΠΎΠΈΡ ΠΈΠ· Π½Π΅ΡΠΊΠΎΠ»ΡΠΊΠΈΡ ΡΠ°ΡΡΠ΅ΠΉ. ΠΠ΄Π½Π° ΠΈΠ· Π½ΠΈΡ ΠΏΡΠΎΡΠ½ΠΎ ΡΠΈΠΊΡΠΈΡΡΠ΅ΡΡΡ ΠΊ ΡΡΠΎΠ»Π΅ΡΠ½ΠΈΡΠ΅, Π° Π²ΡΠΎΡΠ°Ρ ΡΠ²Π»ΡΠ΅ΡΡΡ ΠΏΠΎΠ΄Π²ΠΈΠΆΠ½ΠΎΠΉ. ΠΠΌΠ΅Π½Π½ΠΎ Π±Π»Π°Π³ΠΎΠ΄Π°ΡΡ ΡΡΠΎΠΌΡ ΡΠ΄Π°ΡΡΡΡ ΡΠ°Π·ΠΆΠ°ΡΡ ΡΠΈΡΠΊΠΈ ΠΈ Π·Π°ΠΆΠ°ΡΡ Π² Π½ΠΈΡ ΠΎΠ±ΡΠ°Π±Π°ΡΡΠ²Π°Π΅ΠΌΡΡ Π·Π°Π³ΠΎΡΠΎΠ²ΠΊΡ (Π΄Π΅ΡΠ°Π»Ρ).
Π‘Π°ΠΌΡΠ΅ ΠΏΡΠΎΡΠ½ΡΠ΅ ΡΠΈΡΠΊΠΈ Π΄Π΅Π»Π°ΡΡΡΡ ΠΈΠ· ΠΌΠ΅ΡΠ°Π»Π»Π°. ΠΠ°ΡΠΈΠ°Π½ΡΡ ΠΏΠΎΠΏΡΠΎΡΠ΅, Π΄Π»Ρ ΠΈΠ·Π³ΠΎΡΠΎΠ²Π»Π΅Π½ΠΈΡ ΡΠ°Π·Π»ΠΈΡΠ½ΡΡ ΡΠ°ΠΌΠΎΠ΄Π΅Π»ΠΎΠΊ, ΠΌΠΎΠΆΠ½ΠΎ ΡΠ΄Π΅Π»Π°ΡΡ, ΠΈΡΠΏΠΎΠ»ΡΠ·ΡΡ Π΄Π»Ρ ΡΡΠΈΡ ΡΠ΅Π»Π΅ΠΉ Π΄ΡΠ΅Π²Π΅ΡΠΈΠ½Ρ. ΠΡΠ°ΠΊ, ΡΠ°ΡΡΠΌΠΎΡΡΠΈΠΌ ΡΠ°ΠΌΡΠ΅ ΠΏΠΎΠΏΡΠ»ΡΡΠ½ΡΠ΅ Π²Π°ΡΠΈΠ°Π½ΡΡ ΡΠ°ΠΌΠΎΠ΄Π΅Π»ΡΠ½ΡΡ ΡΠΈΡΠΊΠΎΠ².
Π’ΠΈΡΠΊΠΈ ΠΈΠ· ΠΏΡΠΎΡΠΈΠ»ΡΠ½ΠΎΠΉ ΡΡΡΠ±Ρ β Π²ΠΏΠΎΠ»Π½Π΅ ΡΠ°ΠΊΠΎΠΉ ΡΠ΅Π±Π΅ ΡΠ΄Π°ΡΠ½ΡΠΉ Π²Π°ΡΠΈΠ°Π½Ρ ΠΈΠ·Π³ΠΎΡΠΎΠ²Π»Π΅Π½ΠΈΡ ΡΠΈΡΠΊΠΎΠ² ΡΠ²ΠΎΠΈΠΌΠΈ ΡΡΠΊΠ°ΠΌΠΈ, Π³Π΄Π΅ ΠΏΡΠΎΡΠΈΠ»ΡΠ½Π°Ρ ΡΡΡΠ±Π° Π²ΡΡΡΡΠΏΠ°Π΅Ρ Π² ΠΊΠ°ΡΠ΅ΡΡΠ²Π΅ Π½Π°ΠΏΡΠ°Π²Π»ΡΡΡΠ΅ΠΉ. Π Π½Π΅ΠΉ ΠΏΡΠΈΠ²Π°ΡΠ΅Π½Π° ΠΏΠΎΠ΄Π²ΠΈΠΆΠ½Π°Ρ ΡΠ°ΡΡΡ, ΠΊΠΎΡΠΎΡΠ°Ρ Π·Π°ΡΡΠ³ΠΈΠ²Π°Π΅ΡΡΡ ΠΏΡΠΈ ΠΏΠΎΠΌΠΎΡΠΈ ΡΠΏΠΈΠ»ΡΠΊΠΈ.
Π‘Π°ΠΌΠΎΠ΄Π΅Π»ΡΠ½ΡΠ΅ ΡΠΈΡΠΊΠΈ ΠΈΠ· ΠΌΠ΅ΡΠ°Π»Π»Π° β ΠΈΠΌΠ΅ΡΡ ΠΏΡΠΎΡΡΡΡ, Π½ΠΎ Π² ΡΠΎΠΆΠ΅ Π²ΡΠ΅ΠΌΡ ΠΎΡΠ΅Π½Ρ Π½Π°Π΄ΡΠΆΠ½ΡΡ ΠΊΠΎΠ½ΡΡΡΡΠΊΡΠΈΡ. Π‘ΡΠ°Π½ΠΈΠ½Π° ΡΠ°ΠΊΠΈΡ ΡΠΈΡΠΊΠΎΠ² Π²ΡΠΏΠΎΠ»Π½Π΅Π½Π° ΠΈΠ· ΡΠΎΠ»ΡΡΠΎΠ³ΠΎ ΠΌΠ΅ΡΠ°Π»Π° ΠΈ ΠΏΡΠΈΠΊΡΡΡΠΈΠ²Π°Π΅ΡΡΡ ΠΊ ΡΡΠΎΠ»Π΅ΡΠ½ΠΈΡΠ΅ ΡΠ»Π΅ΡΠ°ΡΠ½ΠΎΠ³ΠΎ Π²Π΅ΡΡΡΠ°ΠΊΠ°, ΠΏΠΎΡΡΠ΅Π΄ΡΡΠ²ΠΎΠΌ Π±ΠΎΠ»ΡΠΎΠ². Π‘ ΠΊΡΠ°Ρ ΡΡΠ°Π½ΠΈΠ½Ρ ΠΏΡΠΈΠ²Π°ΡΠΈΠ²Π°Π΅ΡΡΡ ΡΠΎΠ»ΡΡΠ°Ρ Π³Π°ΠΉΠΊΠ°, Π° ΡΠΎΠ»Ρ ΠΏΡΠΈΠΆΠΈΠΌΠ½ΠΎΠ³ΠΎ ΠΌΠ΅Ρ Π°Π½ΠΈΠ·ΠΌΠ° Π²ΡΠΏΠΎΠ»Π½ΡΠ΅Ρ Π΄Π»ΠΈΠ½Π½Π°Ρ ΡΠΏΠΈΠ»ΡΠΊΠ° Ρ ΠΏΡΠΈΠ²Π°ΡΠ΅Π½Π½ΡΠΌ Π½Π° ΠΊΠΎΠ½ΡΠ΅ Π½Π°Π±Π°Π»Π΄Π°ΡΠ½ΠΈΠΊΠΎΠΌ.
ΠΠ΅ΡΠ΅Π²ΡΠ½Π½ΡΠ΅ ΡΠΈΡΠΊΠΈ β ΡΠ°ΠΊΠΈΠ΅ ΡΠΈΡΠΊΠΈ ΡΠΎΠ±ΠΈΡΠ°ΡΡΡΡ ΠΈΠ· Π΄Π²ΡΡ Π΄Π΅ΡΠ΅Π²ΡΠ½Π½ΡΡ Π±ΡΡΡΠΊΠΎΠ², ΠΌΠ΅ΠΆΠ΄Ρ ΠΊΠΎΡΠΎΡΡΠΌΠΈ, ΡΠΎΠ±ΡΡΠ²Π΅Π½Π½ΠΎ, ΠΈ Π·Π°ΡΡΠ³ΠΈΠ²Π°Π΅ΡΡΡ ΠΎΠ±ΡΠ°Π±Π°ΡΡΠ²Π°Π΅ΠΌΠ°Ρ Π·Π°Π³ΠΎΡΠΎΠ²ΠΊΠ°. Π ΠΊΠ°ΡΠ΅ΡΡΠ²Π΅ Π·Π°ΡΡΠΆΠ½ΠΎΠ³ΠΎ ΠΌΠ΅Ρ Π°Π½ΠΈΠ·ΠΌΠ°, ΠΊΠ°ΠΊ ΠΈ Π²ΠΎ Π²ΡΠ΅Ρ ΠΏΡΠ΅Π΄ΡΠ΄ΡΡΠΈΡ ΡΠ»ΡΡΠ°ΡΡ , ΠΈΡΠΏΠΎΠ»ΡΠ·ΡΠ΅ΡΡΡ ΡΠΏΠΈΠ»ΡΠΊΠ° Ρ ΡΠ΅Π·ΡΠ±ΠΎΠΉ, ΠΈ Π³Π°ΠΉΠΊΠΈ ΠΏΠΎΠ΄Ρ ΠΎΠ΄ΡΡΠ΅Π³ΠΎ Π΄ΠΈΠ°ΠΌΠ΅ΡΡΠ°. Π§ΡΠΎΠ±Ρ Π³Π°ΠΉΠΊΠΈ Π½Π΅ ΠΏΡΠΎΠ΄Π°Π²ΠΈΠ»ΠΈ Π΄Π΅ΡΠ΅Π²ΡΠ½Π½ΡΠ΅ Π±ΡΡΡΠΊΠΈ, Ρ Π΄Π²ΡΡ ΡΡΠΎΡΠΎΠ½ ΡΠ°ΡΠΏΠΎΠ»Π°Π³Π°Π΅ΡΡΡ ΠΏΠΎ ΠΎΠ΄Π½ΠΎΠΉ ΠΌΠ΅ΡΠ°Π»Π»ΠΈΡΠ΅ΡΠΊΠΎΠΉ ΠΏΠ»Π°ΡΡΠΈΠ½Π΅.
ΠΠ°ΠΊΠΎΠΉ Π±Ρ Π²Π°ΡΠΈΠ°Π½Ρ ΠΈΠ·Π³ΠΎΡΠΎΠ²Π»Π΅Π½ΠΈΡ ΡΠΈΡΠΊΠΎΠ² ΡΠ²ΠΎΠΈΠΌΠΈ ΡΡΠΊΠ°ΠΌΠΈ Π²ΡΠ±ΡΠ°Π½ Π½Π΅ Π±ΡΠ», Π²Π°ΠΆΠ½ΠΎ ΠΏΠΎΠ½ΠΈΠΌΠ°ΡΡ, ΡΡΠΎ Π±Π΅Π· ΡΠ²Π°ΡΠΊΠΈ, ΠΏΡΠ°ΠΊΡΠΈΡΠ΅ΡΠΊΠΈ Π½Π΅ ΠΎΠ±ΠΎΠΉΡΠΈΡΡ. Π’Π°ΠΊΠΆΠ΅ ΠΏΠΎΡΡΠ΅Π±ΡΠ΅ΡΡΡ Π±ΠΎΠ»Π³Π°ΡΠΊΠ°, Π° Π² Π½Π΅ΠΊΠΎΡΠΎΡΡΡ ΡΠ»ΡΡΠ°ΡΡ ΠΈ ΡΠ΅Π·ΡΠ±ΠΎΠ½Π°ΡΠ΅Π·Π½ΠΎΠ΅ ΡΡΡΡΠΎΠΉΡΡΠ²ΠΎ, Π΅ΡΠ»ΠΈ ΠΈΡΠΏΠΎΠ»ΡΠ·ΡΡΡΡΡ ΠΊΠ°ΠΊΠΈΠ΅-ΡΠΎ Π½Π΅ΡΡΠ°Π½Π΄Π°ΡΡΠ½ΡΠ΅ ΡΠ΅Π·ΡΠ±ΠΎΠ²ΡΠ΅ ΡΠΎΠ΅Π΄ΠΈΠ½Π΅Π½ΠΈΡ.
ΠΠ°ΠΊ ΡΠ΄Π΅Π»Π°ΡΡ ΡΠΈΡΠΊΠΈ ΡΠ²ΠΎΠΈΠΌΠΈ ΡΡΠΊΠ°ΠΌΠΈ
Π§ΡΠΎΠ±Ρ ΡΠ΄Π΅Π»Π°ΡΡ ΠΏΡΠΎΡΠ½ΡΠ΅ ΠΈ Π½Π°Π΄ΡΠΆΠ½ΡΠ΅ ΡΠΈΡΠΊΠΈ, ΠΏΠΎΠ½Π°Π΄ΠΎΠ±ΡΡΡΡ ΡΠ»Π΅Π΄ΡΡΡΠΈΠ΅ ΠΌΠ°ΡΠ΅ΡΠΈΠ°Π»Ρ:
- Π‘ΡΠ°Π»ΡΠ½ΠΎΠΉ Π»ΠΈΡΡ, ΡΠΎΠ»ΡΠΈΠ½ΠΎΠΉ Π½Π΅ ΠΌΠ΅Π½Π΅Π΅ 10 ΠΌΠΌ;
- Π¨ΠΏΠΈΠ»ΡΠΊΠ° Π16;
- ΠΠ°ΠΉΠΊΠ° ΠΏΠΎΠ΄ ΡΠΏΠΈΠ»ΡΠΊΡ ΡΠΎΠΎΡΠ²Π΅ΡΡΡΠ²ΡΡΡΠ΅Π³ΠΎ Π΄ΠΈΠ°ΠΌΠ΅ΡΡΠ°.
ΠΠ· ΠΈΠ½ΡΡΡΡΠΌΠ΅Π½ΡΠΎΠ², ΠΏΡΠΈ ΠΈΠ·Π³ΠΎΡΠΎΠ²Π»Π΅Π½ΠΈΠΈ ΡΠ°ΠΌΠΎΠ΄Π΅Π»ΡΠ½ΡΡ ΡΠΈΡΠΊΠΎΠ², Π½Π΅ ΠΎΠ±ΠΎΠΉΡΠΈΡΡ Π±Π΅Π· ΡΠ²Π°ΡΠΎΡΠ½ΠΎΠ³ΠΎ Π°ΠΏΠΏΠ°ΡΠ°ΡΠ°, ΡΠ»Π΅ΠΊΡΡΠΎΠ΄ΠΎΠ² 3 ΠΌΠΌ, Π±ΠΎΠ»Π³Π°ΡΠΊΠΈ Ρ ΠΊΡΡΠ³ΠΎΠΌ ΠΏΠΎ ΠΌΠ΅ΡΠ°Π»Π»Ρ.
Π Π°ΡΡΠΌΠΎΡΡΠΈΠΌ ΠΏΡΠΎΡΠ΅ΡΡ ΠΈΠ·Π³ΠΎΡΠΎΠ²Π»Π΅Π½ΠΈΡ ΠΌΠ΅ΡΠ°Π»Π»ΠΈΡΠ΅ΡΠΊΠΈΡ ΡΠΈΡΠΊΠΎΠ² ΡΠ²ΠΎΠΈΠΌΠΈ ΡΡΠΊΠ°ΠΌΠΈ:
- Π ΠΏΠ΅ΡΠ²ΡΡ ΠΎΡΠ΅ΡΠ΅Π΄Ρ Π½ΡΠΆΠ½ΠΎ ΡΠ°Π·ΡΠ΅Π·Π°ΡΡ Π»ΠΈΡΡ ΠΏΠΎ ΡΠΎΡΠΌΠ΅ ΠΏΡΡΠΌΠΎΡΠ³ΠΎΠ»ΡΠ½ΠΈΠΊΠ°, ΡΡΠΎΠ±Ρ ΡΠ΄Π΅Π»Π°ΡΡ Π½Π΅ΠΏΠΎΠ΄Π²ΠΈΠΆΠ½ΡΡ ΡΡΠ°Π½ΠΈΠ½Ρ. ΠΠ΅ΡΠ°Π»Π» Π΄Π»Ρ ΡΡΠΈΡ ΡΠ΅Π»Π΅ΠΉ ΠΌΠΎΠΆΠ½ΠΎ ΠΈΡΠΏΠΎΠ»ΡΠ·ΠΎΠ²Π°ΡΡ ΠΈ ΡΠΎΠ½ΡΡΠ΅, ΡΠΎΠ»ΡΠΈΠ½ΠΎΠΉ 3-5 ΠΌΠΌ;
- ΠΠ°ΡΠ΅ΠΌ Π½Π΅ΠΎΠ±Ρ ΠΎΠ΄ΠΈΠΌΠΎ Π²ΡΡΠ΅Π·Π°ΡΡ ΠΏΡΡΠΌΠΎΡΠ³ΠΎΠ»ΡΠ½ΠΈΠΊ ΠΈΠ· Π±ΠΎΠ»Π΅Π΅ ΡΠΎΠ»ΡΡΠΎΠ³ΠΎ ΠΌΠ΅ΡΠ°Π»Π»Π°. ΠΡΡΠΌΠΎΡΠ³ΠΎΠ»ΡΠ½ΠΈΠΊ Π΄ΠΎΠ»ΠΆΠ΅Π½ ΠΈΠΌΠ΅ΡΡ Π½Π΅ΡΠΊΠΎΠ»ΡΠΊΠΎ ΠΌΠ΅Π½ΡΡΠΈΠ΅ ΡΠ°Π·ΠΌΠ΅ΡΡ, ΡΠ΅ΠΌ ΡΡΠ°Π½ΠΈΠ½Π°. ΠΠ½ ΠΏΡΠΈΠ²Π°ΡΠΈΠ²Π°Π΅ΡΡΡ ΠΊ Π½Π΅ΠΉ ΡΡΡΠΎΠ³ΠΎ ΠΏΠΎ ΡΠ΅Π½ΡΡΡ;
- ΠΠΎΡΠ»Π΅ ΡΡΠΎΠ³ΠΎ ΠΈΠ· ΡΠΎΠ½ΠΊΠΎΠ³ΠΎ ΠΌΠ΅ΡΠ°Π»Π»Π°, ΠΏΠΎ ΡΠ°Π·ΠΌΠ΅ΡΠ°ΠΌ Π²ΡΠΎΡΠΎΠ³ΠΎ ΠΏΡΡΠΌΠΎΡΠ³ΠΎΠ»ΡΠ½ΠΈΠΊΠ° Π²ΡΡΠ΅Π·Π°Π΅ΡΡΡ Π΅ΡΡ ΠΎΠ΄ΠΈΠ½, ΠΏΠΎ ΠΊΡΠ°ΡΠΌ ΠΊΠΎΡΠΎΡΠΎΠ³ΠΎ ΠΏΡΠΈΠ²Π°ΡΠΈΠ²Π°Π΅ΡΡΡ Π΄Π²Π΅ ΠΌΠ΅ΡΠ°Π»Π»ΠΈΡΠ΅ΡΠΊΠΈΠ΅ ΠΏΠΎΠ»ΠΎΡΠΊΠΈ ΡΠ±ΠΎΠΊΡ. ΠΡΠΎΡ ΠΏΡΡΠΌΠΎΡΠ³ΠΎΠ»ΡΠ½ΠΈΠΊ Π±ΡΠ΄Π΅Ρ ΠΏΠΎΠ΄Π²ΠΈΠΆΠ½ΠΎΠΉ ΡΠ°ΡΡΡΡ ΡΠ°ΠΌΠΎΠ΄Π΅Π»ΡΠ½ΡΡ ΡΠΈΡΠΊΠΎΠ²;
- ΠΠ°ΡΠ΅ΠΌ ΠΈΠ· ΡΠΎΠ»ΡΡΠΎΠ³ΠΎ ΠΌΠ΅ΡΠ°Π»Π»Π° ΡΠ»Π΅Π΄ΡΠ΅Ρ Π²ΡΡΠ΅Π·Π°ΡΡ Π΄Π²Π΅ ΠΏΠΎΠ»ΠΎΡΠΊΠΈ, ΠΊΠΎΡΠΎΡΡΠ΅ Π±ΡΠ΄ΡΡ ΡΠ»ΡΠΆΠΈΡΡ Π² ΡΠΎΠ»ΠΈ ΠΏΡΠΈΠΆΠΈΠΌΠ½ΡΡ ΡΠ»Π΅ΠΌΠ΅Π½ΡΠΎΠ². ΠΠΎΠ»ΠΎΡΠΊΠΈ ΠΌΠ΅ΡΠ°Π»Π»Π° ΠΏΡΠΈΠ²Π°ΡΠΈΠ²Π°ΡΡΡΡ Ρ ΠΊΡΠ°Ρ ΠΏΠΎΠ΄Π²ΠΈΠΆΠ½ΠΎΠΉ ΡΠ°ΡΡΠΈ ΠΈ Π½Π° ΠΊΠΎΠ½ΡΠ΅ ΡΠ°ΠΌΠΎΠΉ ΡΡΠ°Π½ΠΈΠ½Ρ;
- Π§ΡΠΎΠ±Ρ ΡΠΈΡΠΊΠΈ, ΡΠ΄Π΅Π»Π°Π½Π½ΡΠ΅ ΡΠ²ΠΎΠΈΠΌΠΈ ΡΡΠΊΠ°ΠΌΠΈ, Π·Π°ΡΠ°Π±ΠΎΡΠ°Π»ΠΈ, ΠΎΡΡΠ°ΡΡΡΡ ΠΏΡΠΈΠ²Π°ΡΠΈΡΡ Π³Π°ΠΉΠΊΡ Ρ Π΄ΡΡΠ³ΠΎΠ³ΠΎ ΠΊΠΎΠ½ΡΠ° ΠΏΠΎΠ΄Π²ΠΈΠΆΠ½ΠΎΠΉ ΡΠ°ΡΡΠΈ, ΠΏΠΎΡΠ»Π΅ ΡΠ΅Π³ΠΎ Π½Π°ΠΊΡΡΡΠΈΡΡ Π½Π° Π½Π΅Ρ ΡΠΏΠΈΠ»ΡΠΊΡ.
Π’Π°ΠΊΠΈΠΌ ΠΎΠ±ΡΠ°Π·ΠΎΠΌ, ΠΌΠΎΠΆΠ½ΠΎ ΡΡΠΊΠΎΠ½ΠΎΠΌΠΈΡΡ Π½Π° ΠΏΠΎΠΊΡΠΏΠΊΠ΅ Π·Π°Π²ΠΎΠ΄ΡΠΊΠΈΡ ΡΠΈΡΠΊΠΎΠ². ΠΡΠΎΠΌΠ΅ ΡΠΎΠ³ΠΎ, ΡΠ°ΠΌΠΎΠ΄Π΅Π»ΡΠ½ΡΠ΅ ΡΠΈΡΠΊΠΈ ΠΌΠΎΠ³ΡΡ ΠΈΠΌΠ΅ΡΡ ΡΠΎΠ²Π΅ΡΡΠ΅Π½Π½ΠΎ ΡΠ°Π·Π½ΡΠ΅ ΡΠ°Π·ΠΌΠ΅ΡΡ, ΠΊΠΎΡΠΎΡΡΠ΅ ΠΈΠ΄Π΅Π°Π»ΡΠ½ΠΎ ΠΏΠΎΠ΄Ρ ΠΎΠ΄ΡΡ ΠΏΠΎΠ΄ ΠΊΠ°ΠΊΠΈΠ΅-ΡΠΎ ΠΊΠΎΠ½ΠΊΡΠ΅ΡΠ½ΡΠ΅ Π·Π°Π΄Π°ΡΠΈ.
ΠΡΠ΅Π½ΠΈΡΡ ΡΡΠ°ΡΡΡ ΠΈ ΠΏΠΎΠ΄Π΅Π»ΠΈΡΡΡΡ ΡΡΡΠ»ΠΊΠΎΠΉ:Π‘Π°ΠΌΠΎΠ΄Π΅Π»ΡΠ½ΡΠ΅ Π±ΡΡΡΡΠΎΠ·Π°ΠΆΠΈΠΌΠ½ΡΠ΅ ΡΠΈΡΠΊΠΈ
ΠΡΠΏΠΎΠ»Π½ΡΡΡ ΠΎΠ΄Π½ΠΎΡΠΈΠΏΠ½ΡΡ ΡΠ°Π±ΠΎΡΡ ΠΏΠΎ ΠΎΠ±ΡΠ°Π±ΠΎΡΠΊΠ΅ ΠΌΠ½ΠΎΠΆΠ΅ΡΡΠ²Π° ΠΎΠ΄ΠΈΠ½Π°ΠΊΠΎΠ²ΡΡ Π΄Π΅ΡΠ°Π»Π΅ΠΉ Π² ΡΠΈΡΠΊΠ°Ρ Π½Π΅ΡΠ΄ΠΎΠ±Π½ΠΎ. ΠΡ Π²ΠΈΠ½Ρ ΠΏΡΠΈΡ ΠΎΠ΄ΠΈΡΡΡ ΠΏΠΎΠ΄ΠΎΠ»Π³Ρ Π·Π°ΠΊΡΡΡΠΈΠ²Π°ΡΡ ΠΈ Π²ΡΠΊΡΡΡΠΈΠ²Π°ΡΡ, Π½Π° ΡΡΠΎ ΡΡΠ°ΡΠΈΡΡΡΡ Π²ΡΠ΅ΠΌΡ. Π§ΡΠΎΠ±Ρ Π·Π°ΠΆΠΈΠΌΠ°ΡΡ ΠΈ ΡΠ½ΠΈΠΌΠ°ΡΡ Π·Π°Π³ΠΎΡΠΎΠ²ΠΊΠΈ Π±ΡΡΡΡΠ΅Π΅, ΠΌΠΎΠΆΠ½ΠΎ Π²ΠΎΡΠΏΠΎΠ»ΡΠ·ΠΎΠ²Π°ΡΡΡΡ ΡΠ°ΠΌΠΎΠ΄Π΅Π»ΡΠ½ΡΠΌΠΈ Π±ΡΡΡΡΠΎΠ·Π°ΠΆΠΈΠΌΠ½ΡΠΌΠΈ ΡΠΈΡΠΊΠ°ΠΌΠΈ ΡΡΡΠ°ΠΆΠ½ΠΎΠ³ΠΎ ΡΠΈΠΏΠ°. ΠΠ½ΠΈ Π½Π°ΡΡΡΠ°ΠΈΠ²Π°ΡΡΡΡ Π²ΠΈΠ½ΡΠΎΠΌ ΠΏΠΎΠ΄ Π½ΡΠΆΠ½ΡΡ ΡΠΎΠ»ΡΠΈΠ½Ρ Π΄Π΅ΡΠ°Π»Π΅ΠΉ, Π° ΠΏΠΎΡΠΎΠΌ Π΄ΠΎΠΆΠΈΠΌΠ°ΡΡ ΠΈΡ ΡΡΠΎΠΊΠΎΠΌ. ΠΠ²ΠΈΠ³Π°Ρ ΡΡΡΠ°Π³ΠΎΠΌ ΡΠΈΡΠΊΠΎΠ², ΠΌΠΎΠΆΠ½ΠΎ Π·Π° ΠΏΠ°ΡΡ ΡΠ΅ΠΊΡΠ½Π΄ ΠΎΡΠ²ΠΎΠ±ΠΎΠ΄ΠΈΡΡ ΠΎΠ΄Π½Ρ Π·Π°Π³ΠΎΡΠΎΠ²ΠΊΡ ΠΈ Π·Π°ΠΆΠ°ΡΡ Π²ΠΌΠ΅ΡΡΠΎ Π½Π΅Π΅ Π΄ΡΡΠ³ΡΡ.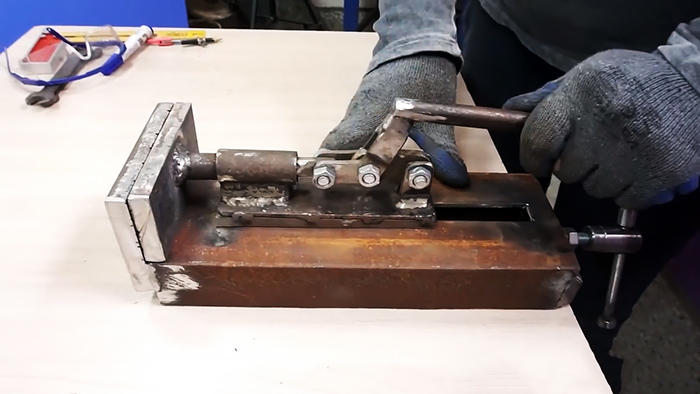
ΠΠ°ΡΠ΅ΡΠΈΠ°Π»Ρ:
- ΠΏΠΎΠ»ΠΎΡΡ ΠΈΠ»ΠΈ Π»ΠΈΡΡΠΎΠ²Π°Ρ ΡΡΠ°Π»Ρ 3 ΠΌΠΌ, 5 ΠΌΠΌ, 10 ΠΌΠΌ
- ΡΡΠ°Π»ΡΠ½ΡΠ΅ ΡΡΡΠ±Ρ d18-25 ΠΌΠΌ, 25-30 ΠΌΠΌ
- ΠΊΡΡΠ³Π»ΡΠΊ ΠΏΠΎΠ΄ Π²Π½ΡΡΡΠ΅Π½Π½ΠΈΠΉ Π΄ΠΈΠ°ΠΌΠ΅ΡΡ ΠΌΠ΅Π½ΡΡΠ΅ΠΉ ΡΡΡΠ±Ρ;
- ΠΌΠ°ΡΡΠΈΠ²Π½ΡΠΉ ΡΠ²Π΅Π»Π»Π΅Ρ;
- ΡΠΏΠΈΠ»ΡΠΊΠ° Π10;
- Π±ΠΎΠ»ΡΡ, Π³Π°ΠΉΠΊΠΈ, ΡΠ°ΠΉΠ±Ρ Π10.
ΠΠ·Π³ΠΎΡΠΎΠ²Π»Π΅Π½ΠΈΠ΅ ΡΠΈΡΠΊΠΎΠ²
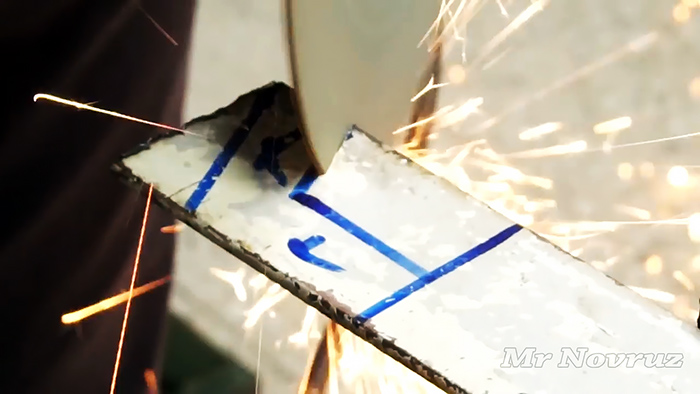
ΠΠ· ΠΏΠΎΠ»ΠΎΡΡ ΠΈΠ»ΠΈ Π»ΠΈΡΡΠΎΠ²ΠΎΠΉ ΡΡΠ°Π»ΠΈ Π²ΡΡΠ΅Π·Π°ΡΡΡΡ 2 Π-ΠΎΠ±ΡΠ°Π·Π½ΡΡ Π·Π°Π³ΠΎΡΠΎΠ²ΠΊΠΈ Ρ ΡΠ³Π»ΠΎΠΌ 110-120 Π³ΡΠ°Π΄ΡΡΠΎΠ², ΠΈ Π΄Π»ΠΈΠ½ΠΎΠΉ ΡΡΠΎΡΠΎΠ½ ΠΏΠΎ Π²Π½ΡΡΡΠ΅Π½Π½Π΅ΠΌΡ ΡΠ³Π»Ρ 4-5 ΡΠΌ. ΠΠ°Π»Π΅Π΅ ΠΎΠ½ΠΈ ΡΠΊΡΡΠ³Π»ΡΡΡΡΡ Π½Π° Π½Π°ΠΆΠ΄Π°ΠΊΠ΅ ΠΈ ΠΏΠΎΠ»Π½ΠΎΡΡΡΡ Π·Π°ΡΠΈΡΠ°ΡΡΡΡ.
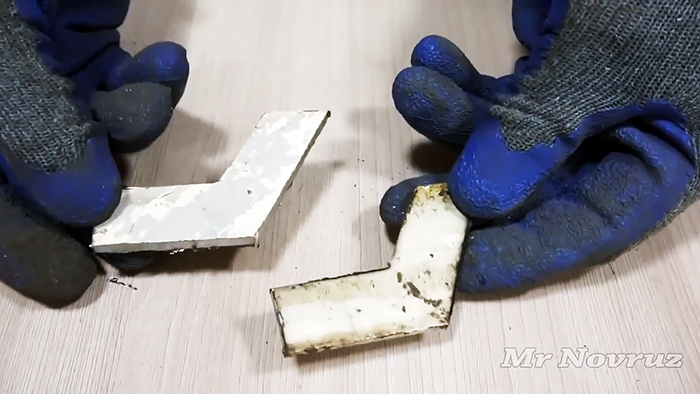
ΠΠ°Π³ΠΎΡΠΎΠ²ΠΊΠΈ ΡΠΊΠ»Π°Π΄ΡΠ²Π°ΡΡΡΡ Π²Π΄Π²ΠΎΠ΅ ΠΈ Π²ΠΌΠ΅ΡΡΠ΅ ΠΏΡΠΎΡΠ²Π΅ΡΠ»ΠΈΠ²Π°ΡΡΡΡ. ΠΠ΄Π½ΠΎ ΠΎΡΠ²Π΅ΡΡΡΠΈΠ΅ Π΄Π΅Π»Π°Π΅ΡΡΡ ΠΏΠΎ ΡΠ΅Π½ΡΡΡ, Π²ΡΠΎΡΠΎΠ΅ Ρ ΠΊΡΠ°Ρ. Π‘Π²Π΅ΡΠ»Π΅Π½ΠΈΠ΅ Π²ΠΌΠ΅ΡΡΠ΅ ΠΏΠΎΠ·Π²ΠΎΠ»ΡΠ΅Ρ ΡΠ΄Π΅Π»Π°ΡΡ ΠΈΡ Π°Π±ΡΠΎΠ»ΡΡΠ½ΠΎ ΠΎΠ΄ΠΈΠ½Π°ΠΊΠΎΠ²ΡΠΌΠΈ.
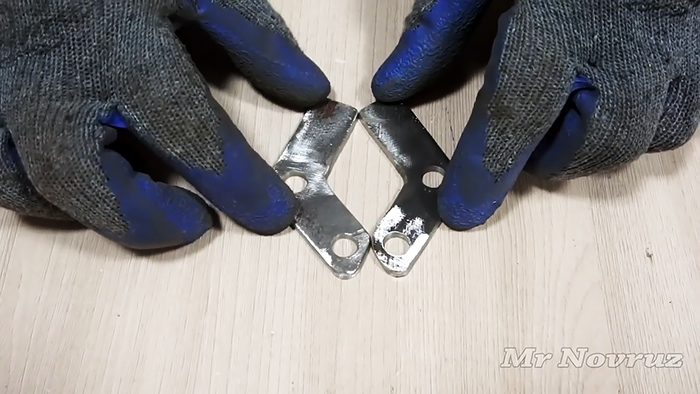
ΠΠ° ΡΡΠ°Π»ΡΠ½ΠΎΠΌ ΠΊΡΡΠ³Π»ΡΠΊΠ΅ Ρ ΠΊΡΠ°Ρ ΡΠ½ΠΈΠΌΠ°ΡΡΡΡ ΡΠΏΡΡΠΊΠΈ. Π ΠΏΡΠΎΡΠΎΡΠΊΠ΅ Π΄Π΅Π»Π°Π΅ΡΡΡ ΠΎΡΠ²Π΅ΡΡΡΠΈΠ΅, ΡΠ°ΠΊΠΈΠΌ ΠΆΠ΅ ΡΠ²Π΅ΡΠ»ΠΎΠΌ, ΡΡΠΎ ΠΈ Π½Π° Π-ΠΎΠ±ΡΠ°Π·Π½ΡΡ Π·Π°Π³ΠΎΡΠΎΠ²ΠΊΠ°Ρ .
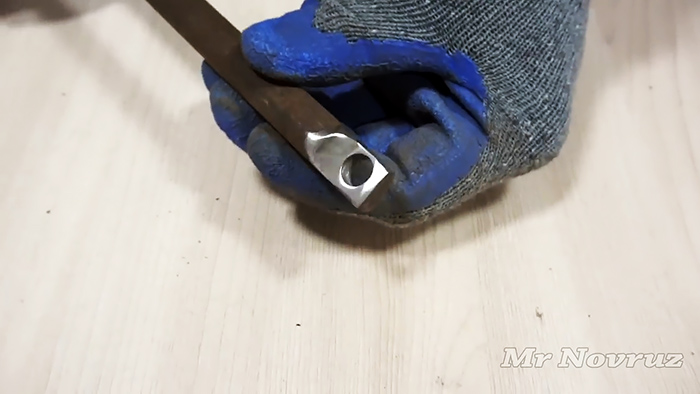
ΠΡ ΠΊΡΡΠ³Π»ΡΠΊΠ° ΠΏΠΎΡΡΠ΅Π±ΡΠ΅ΡΡΡ ΠΎΡΡΠ΅Π·ΠΎΠΊ 5-7 ΡΠΌ. ΠΠ½ ΡΠ°ΡΡΠΈΡΠ½ΠΎ Π²ΡΡΠ°Π²Π»ΡΠ΅ΡΡΡ Π² ΡΡΡΠ±ΠΊΡ Π΄Π»ΠΈΠ½ΠΎΠΉ 15 ΡΠΌ ΠΈ ΠΎΠ±Π²Π°ΡΠΈΠ²Π°Π΅ΡΡΡ Ρ Π½Π΅ΠΉ.
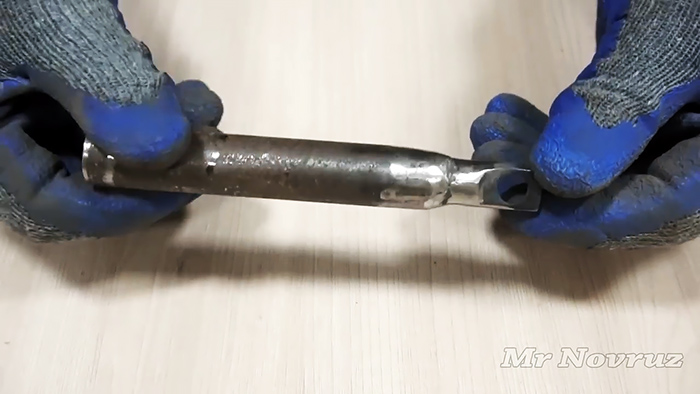
ΠΠ°ΡΠ΅ΠΌ ΠΊ ΠΊΡΡΠ³Π»ΡΠΊΡ ΡΠ΅ΡΠ΅Π· ΠΊΡΠ°ΠΉΠ½Π΅Π΅ ΠΎΡΠ²Π΅ΡΡΡΠΈΠ΅ Ρ ΠΏΠΎΠΌΠΎΡΡΡ Π±ΠΎΠ»ΡΠ° ΠΏΡΠΈΠΊΡΡΡΠΈΠ²Π°ΡΡΡΡ ΡΠ°Π½Π΅Π΅ ΡΠ΄Π΅Π»Π°Π½Π½ΡΠ΅ ΡΠ³ΠΎΠ»ΡΠ½ΠΈΠΊΠΈ.
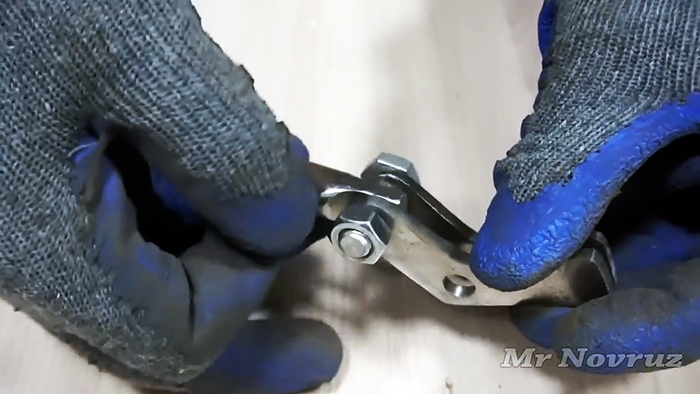
ΠΠ· Π±ΠΎΠ»Π΅Π΅ ΡΠΎΠ»ΡΡΠΎΠΉ Π»ΠΈΡΡΠΎΠ²ΠΎΠΉ ΡΡΠ°Π»ΠΈ Π½ΡΠΆΠ½ΠΎ Π²ΡΡΠ΅Π·Π°ΡΡ ΠΊΠΎΡΠΎΡΠΊΡΡ ΠΏΠΎΠ»ΠΎΡΡ Π΄Π»ΠΈΠ½ΠΎΠΉ 5-7 ΡΠΌ ΠΈ ΡΠΈΡΠΈΠ½ΠΎΠΉ 2-3 ΡΠΌ. ΠΠ΅ Π½ΡΠΆΠ½ΠΎ ΡΠΊΡΡΠ³Π»ΠΈΡΡ ΠΈ ΠΏΡΠΎΡΠ²Π΅ΡΠ»ΠΈΡΡ Ρ ΠΊΡΠ°Π΅Π² ΠΏΠΎ ΠΎΡΠ²Π΅ΡΡΡΠΈΡ.
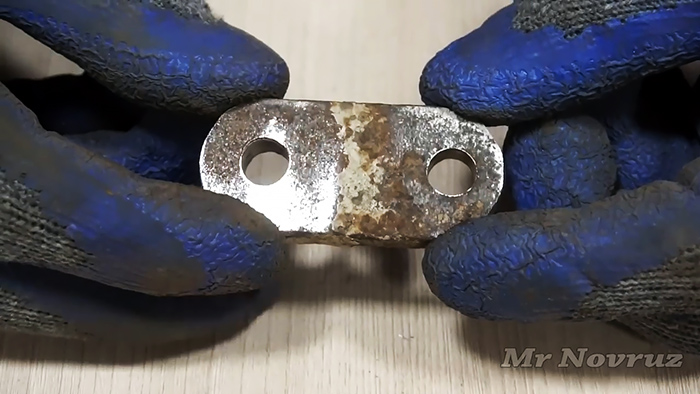
ΠΠΎΠ»ΡΡΠ΅Π½Π½Π°Ρ Π΄Π΅ΡΠ°Π»Ρ Π²ΡΡΠ°Π²Π»ΡΠ΅ΡΡΡ ΠΌΠ΅ΠΆΠ΄Ρ ΡΠ³ΠΎΠ»ΡΠ½ΠΈΠΊΠ°ΠΌΠΈ ΠΈ ΡΠΎΠ΅Π΄ΠΈΠ½ΡΠ΅ΡΡΡ Ρ Π½ΠΈΠΌΠΈ Π±ΠΎΠ»ΡΠΎΠΌ Ρ Π³Π°ΠΉΠΊΠΎΠΉ.
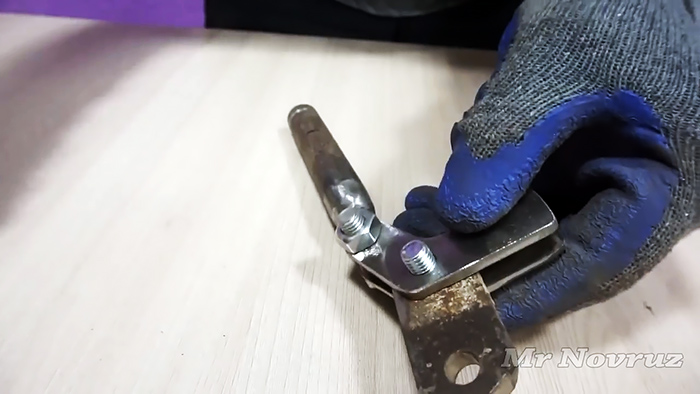
ΠΠ· ΠΏΠΎΠ»ΠΎΡΡ ΠΈΠ»ΠΈ ΡΡΠ°Π»ΡΠ½ΠΎΠ³ΠΎ Π»ΠΈΡΡΠ° Π²ΡΡΠ΅Π·Π°Π΅ΡΡΡ 2 ΠΏΡΠΎΡΡΠΈΠ½Ρ ΡΠΈΡΠΈΠ½ΠΎΠΉ 2-3 ΡΠΌ ΠΈ Π΄Π»ΠΈΠ½ΠΎΠΉ 3-4 ΡΠΌ. ΠΠ΄ΠΈΠ½ ΠΈΡ ΠΊΡΠ°ΠΉ Π·Π°ΠΊΡΡΠ³Π»ΡΠ΅ΡΡΡ, ΠΈ Π²ΠΎΠ·Π»Π΅ Π½Π΅Π³ΠΎ ΡΠ²Π΅ΡΠ»ΠΈΡΡΡ ΠΎΡΠ²Π΅ΡΡΡΠΈΠ΅.
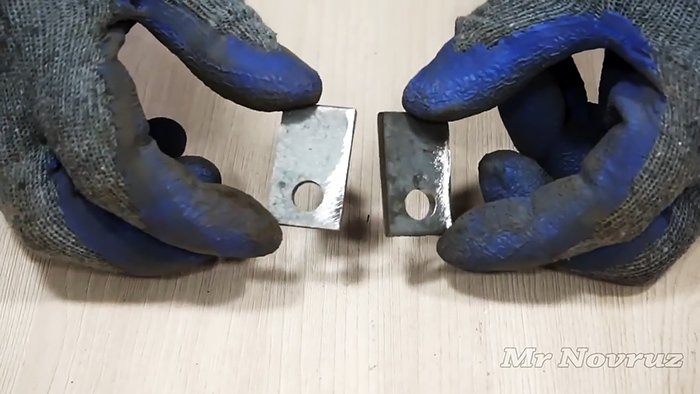
ΠΠ°ΡΠ΅ΠΌ ΠΏΡΠΎΡΡΠΈΠ½Ρ ΡΠΎΠ΅Π΄ΠΈΠ½ΡΡΡΡΡ Π±ΠΎΠ»ΡΠΎΠΌ Ρ ΠΏΡΠ΅Π΄ΡΠ΄ΡΡΠ΅ΠΉ ΠΏΠ»Π°ΡΡΠΈΠ½ΠΎΠΉ. ΠΡ ΠΏΠ»ΠΎΡΠΊΠΈΠ΅ ΠΊΡΠ°Ρ Π½ΡΠΆΠ½ΠΎ Π²ΡΡΡΠ°Π²ΠΈΡΡ Π½Π° ΠΏΠΎΠ»ΠΎΡΠ΅ 5Ρ 20 ΡΠΌ ΠΈ ΠΏΡΠΈΠ²Π°ΡΠΈΡΡ.
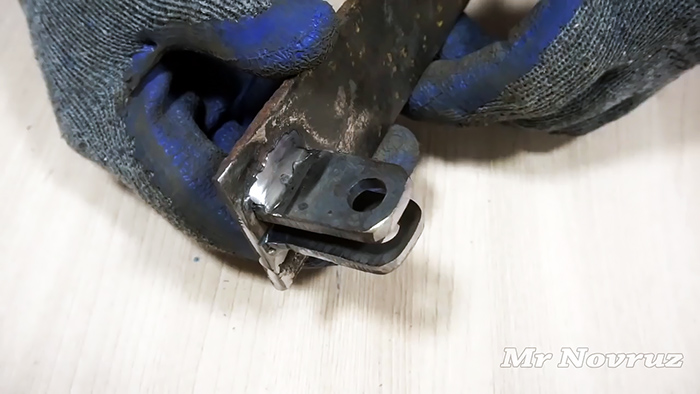
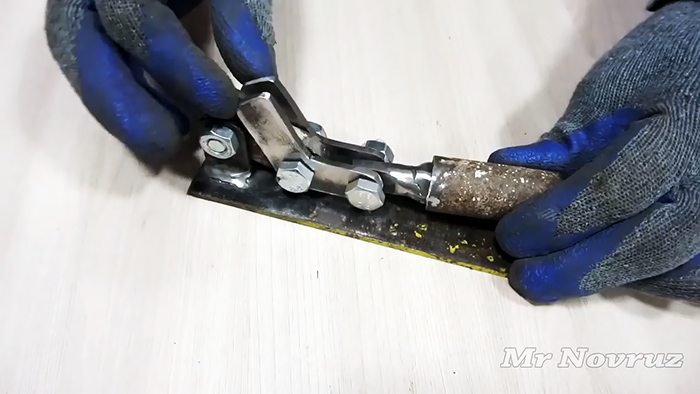
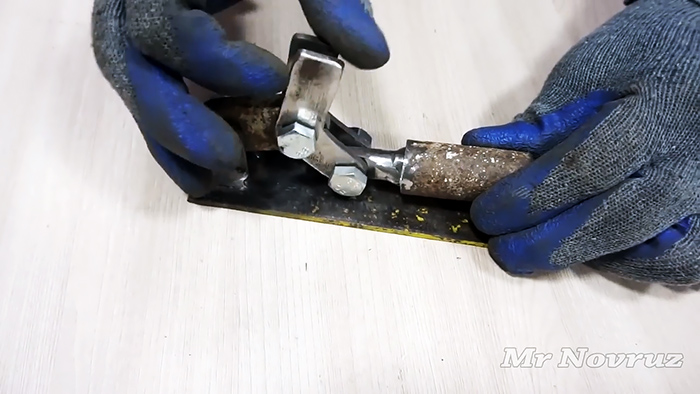
Π ΡΠ²ΠΎΠ±ΠΎΠ΄Π½ΠΎΠΌΡ ΠΊΡΠ°Ρ ΡΠ³ΠΎΠ»ΡΠ½ΠΈΠΊΠΎΠ² ΠΏΡΠΈΠ²Π°ΡΠΈΠ²Π°Π΅ΡΡΡ Π΄Π»ΠΈΠ½Π½ΡΠΉ ΡΡΡΠ°Π³. ΠΠ°ΡΠ΅ΠΌ ΠΊΡΡΠ³Π»ΡΠΊ Ρ ΡΡΡΠ±ΠΊΠΎΠΉ Π½Π° Π²ΡΠΎΡΠΎΠΌ ΠΊΡΠ°Ρ Π-ΠΎΠ±ΡΠ°Π·Π½ΡΡ Π·Π°Π³ΠΎΡΠΎΠ²ΠΎΠΊ Π²ΡΡΠ°Π²Π»ΡΠ΅ΡΡΡ Π² ΠΊΠΎΡΠΎΡΠΊΠΈΠΉ ΠΎΡΡΠ΅Π·ΠΎΠΊ ΡΡΡΠ±Ρ Π±ΠΎΠ»ΡΡΠ΅Π³ΠΎ Π΄ΠΈΠ°ΠΌΠ΅ΡΡΠ°. Π‘Π°ΠΌΠ° ΡΡΡΠ±Π° ΠΏΡΠΈΠ²Π°ΡΠΈΠ²Π°Π΅ΡΡΡ ΠΊ ΠΏΠΎΠ΄ΠΎΡΠ²Π΅ ΠΏΡΠΎΡΡΠΈΠ½ ΡΠ΅ΡΠ΅Π· ΠΏΡΠΎΡΡΠ°Π²ΠΊΡ. ΠΡΠ»ΠΈ Π²ΡΠ΅ ΡΠ΄Π΅Π»Π°Π½ΠΎ ΠΏΡΠ°Π²ΠΈΠ»ΡΠ½ΠΎ, ΡΠΎ ΠΏΡΠΈ Π΄Π²ΠΈΠΆΠ΅Π½ΠΈΠΈ ΡΡΡΠ°Π³Π° ΡΡΠΎΠΊ ΠΌΠ΅Ρ Π°Π½ΠΈΠ·ΠΌΠ° Π²ΡΠ΄Π²ΠΈΠ³Π°Π΅ΡΡΡ ΠΈ Π·Π°Π΄Π²ΠΈΠ³Π°Π΅ΡΡΡ.
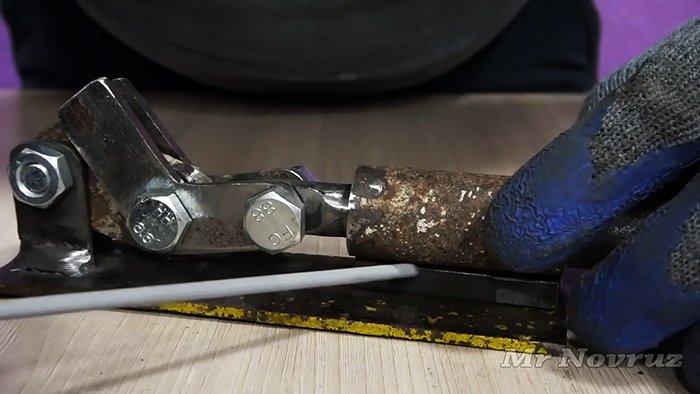
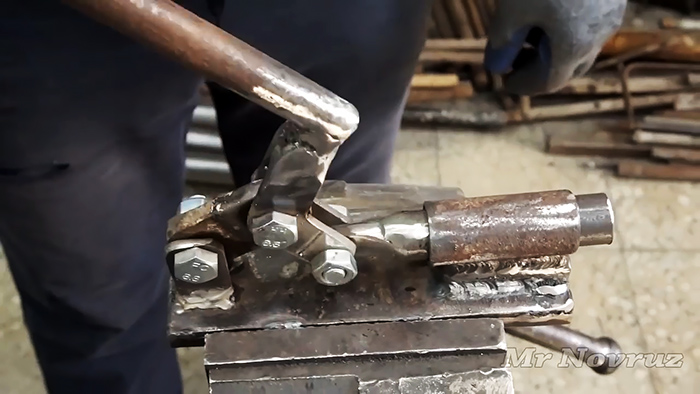
ΠΠ°Π»Π΅Π΅ Π±Π΅ΡΠ΅ΡΡΡ ΡΡΠ°Π»ΡΠ½ΠΎΠΉ ΡΠ²Π΅Π»Π»Π΅Ρ 30-50 ΡΠΌ Π² Π΄Π»ΠΈΠ½Ρ (Π·Π°Π²ΠΈΡΠΈΡ ΠΎΡ ΠΆΠ΅Π»Π°Π΅ΠΌΠΎΠ³ΠΎ ΡΠ°Π·ΠΌΠ΅ΡΠ° ΡΠΈΡΠΊΠΎΠ²).
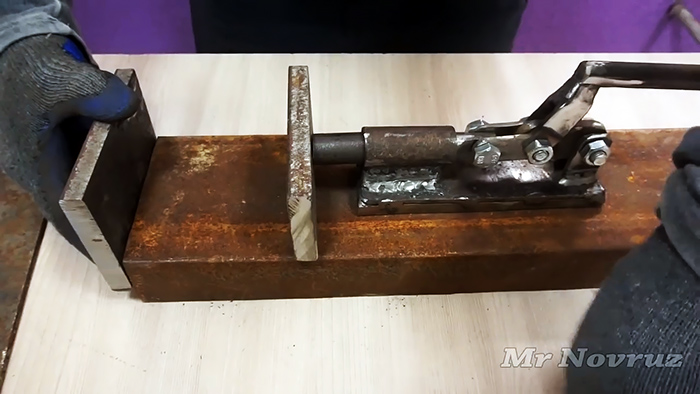
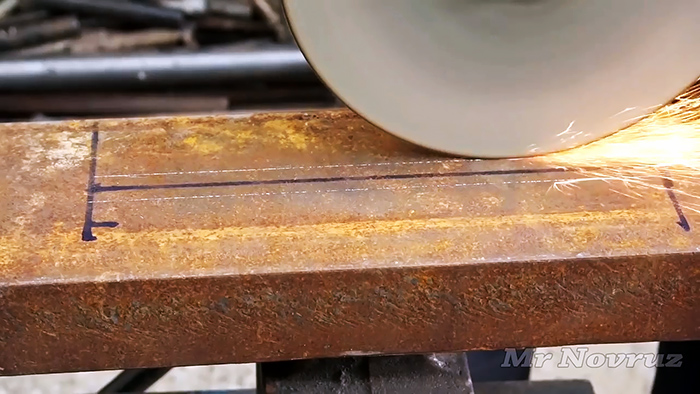
ΠΠΎ Π΅Π³ΠΎ ΡΠ΅Π½ΡΡΡ Π΄Π΅Π»Π°Π΅ΡΡΡ ΠΏΡΠΎΠ΄ΠΎΠ»ΡΠ½ΡΠΉ ΡΠ°Π·ΡΠ΅Π· ΠΏΠΎ ΡΠΈΡΠΈΠ½Π΅ Π³Π°ΠΉΠΊΠΈ Π10. ΠΠ°ΡΠ΅ΠΌ Π½Π° ΠΎΠ±ΡΠ°ΡΠ½ΠΎΠΉ ΡΡΠΎΡΠΎΠ½Π΅ ΠΏΠΎΠ΄ΠΎΡΠ²Ρ ΠΌΠ΅Ρ Π°Π½ΠΈΠ·ΠΌΠ° Ρ ΡΡΡΠ°Π³ΠΎΠΌ ΠΏΡΠΈΠ²Π°ΡΠΈΠ²Π°ΡΡΡΡ Π³Π°ΠΉΠΊΠΈ. ΠΠ»Π°Π³ΠΎΠ΄Π°ΡΡ ΡΡΠΎΠΌΡ ΠΎΠ½ ΠΌΠΎΠΆΠ΅Ρ ΡΠΊΠΎΠ»ΡΠ·ΠΈΡΡ ΠΏΠΎ Π²ΡΡΠ΅Π·Ρ ΡΠ²Π΅Π»Π»Π΅ΡΠ°, ΠΊΠ°ΠΊ ΠΏΠΎ Π½Π°ΠΏΡΠ°Π²Π»ΡΡΡΠ΅ΠΉ.
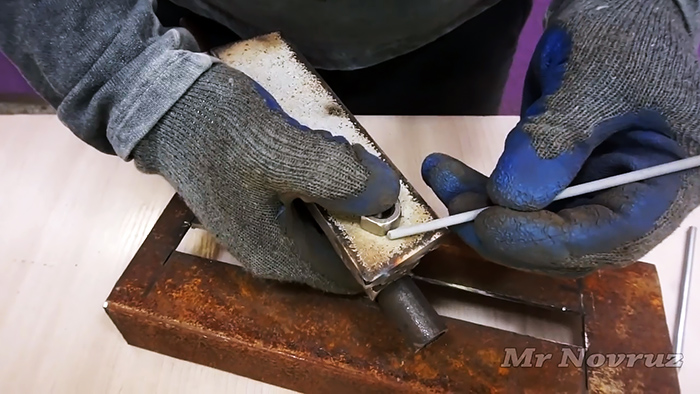
ΠΠ° ΡΠ»Π΅Π΄ΡΡΡΠ΅ΠΌ ΡΡΠ°ΠΏΠ΅ Π½ΡΠΆΠ½ΠΎ ΡΠ΄Π΅Π»Π°ΡΡ ΠΊΡΠ΅ΠΏΠ»Π΅Π½ΠΈΠ΅ ΡΡΡΠ°ΠΆΠ½ΠΎΠ³ΠΎ ΠΌΠ΅Ρ Π°Π½ΠΈΠ·ΠΌΠ°. ΠΠ»Ρ ΡΡΠΎΠ³ΠΎ Π²ΡΡΠ΅Π·Π°Π΅ΡΡΡ ΠΏΠΎΠ»ΠΎΡΠ°, Π² Π½Π΅ΠΉ Π΄Π΅Π»Π°ΡΡΡΡ ΠΎΡΠ²Π΅ΡΡΡΠΈΡ Π±ΠΎΠ»ΡΡΠ΅Π³ΠΎ Π΄ΠΈΠ°ΠΌΠ΅ΡΡΠ°, ΡΠ΅ΠΌ Π³Π°ΠΉΠΊΠΈ Π10.
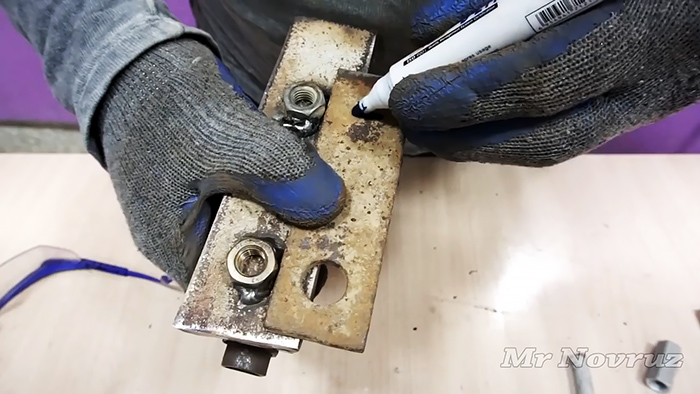
ΠΠ½Π° ΡΡΡΠ°Π½Π°Π²Π»ΠΈΠ²Π°Π΅ΡΡΡ Π½Π° ΠΎΠ±ΠΎΡΠΎΡΠ΅ ΡΠ²Π΅Π»Π»Π΅ΡΠ° Π½Π° Π³Π°ΠΉΠΊΠΈ ΠΎΡ ΠΏΠΎΠ΄ΠΎΡΠ²Ρ ΡΡΡΠ°Π³ΠΎΠ², Π·Π°ΡΠ΅ΠΌ ΡΠ²Π΅ΡΡ Ρ Π½Π°ΠΊΠ»Π°Π΄ΡΠ²Π°ΡΡΡΡ ΡΠ°ΠΉΠ±Ρ ΠΈ Π²ΠΊΡΡΡΠΈΠ²Π°ΡΡΡΡ ΠΊΠΎΡΠΎΡΠΊΠΈΠ΅ Π±ΠΎΠ»ΡΡ.
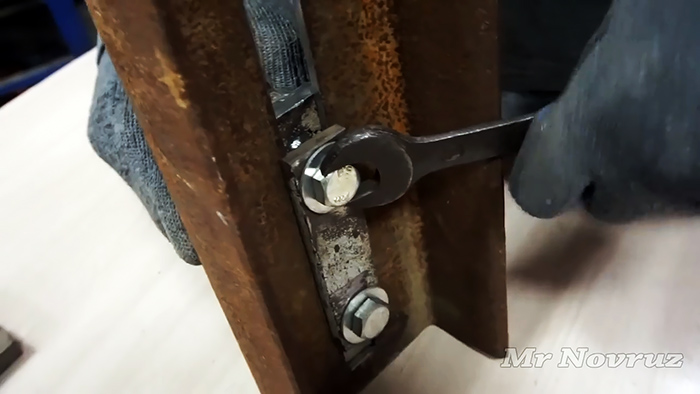
Π ΡΠ΅Π·ΡΠ»ΡΡΠ°ΡΠ΅ ΡΡΡΠ°ΠΆΠ½ΡΠΉ Π±Π»ΠΎΠΊ ΡΠΊΠΎΠ»ΡΠ·ΠΈΡ ΠΏΠΎ Π½Π°ΠΏΡΠ°Π²Π»ΡΡΡΠ΅ΠΉ, Π½ΠΎ Π½Π΅ Π²ΡΠΏΠ°Π΄Π°Π΅Ρ.

ΠΠ° ΡΡΠΎΠΊ ΠΈ ΠΏΠ΅ΡΠ΅Π΄Π½ΠΈΠΉ ΠΊΡΠ°ΠΉ ΡΠ²Π΅Π»Π»Π΅ΡΠ° ΠΏΡΠΈΠ²Π°ΡΠΈΠ²Π°ΡΡΡΡ ΡΡΠ°Π»ΡΠ½ΡΠ΅ ΠΏΠ»Π°ΡΡΠΈΠ½Ρ ΡΠ΅ΡΠ΅Π½ΠΈΠ΅ΠΌ 10 ΠΌΠΌ. ΠΡΠΎ Π³ΡΠ±ΠΊΠΈ ΡΠΈΡΠΊΠΎΠ², ΠΏΠΎΡΡΠΎΠΌΡ ΠΆΠ΅Π»Π°ΡΠ΅Π»ΡΠ½ΠΎ ΠΏΠ΅ΡΠ΅Π΄ ΠΏΡΠΈΠ²Π°ΡΠΊΠΎΠΉ Π½Π°ΡΠ΅Π·Π°ΡΡ Π½Π° Π½ΠΈΡ Π½Π°ΡΠ΅ΡΠΊΠΈ.
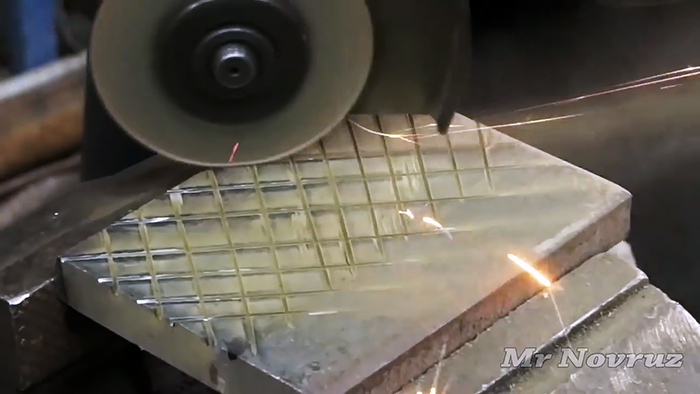
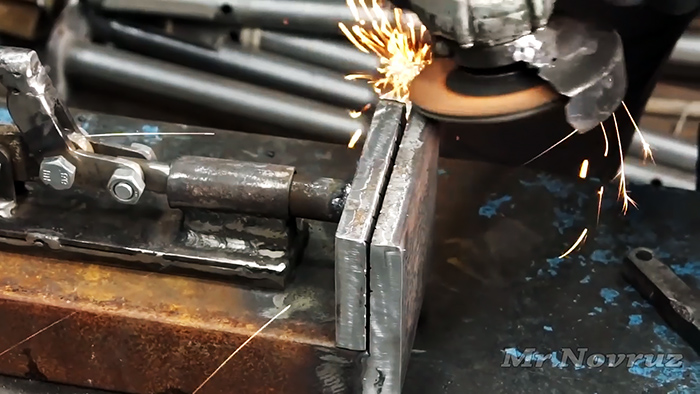
ΠΠ»Ρ ΠΏΠ΅ΡΠ΅ΠΌΠ΅ΡΠ΅Π½ΠΈΡ ΠΊΠ°ΡΠ΅ΡΠΊΠΈ Ρ ΡΡΡΠ°ΠΆΠ½ΡΠΌ ΠΌΠ΅Ρ Π°Π½ΠΈΠ·ΠΌΠΎΠΌ Π½Π° ΠΎΠ±ΡΠ°ΡΠ½ΠΎΠΉ ΡΡΠΎΡΠΎΠ½Π΅ ΡΠ²Π΅Π»Π»Π΅ΡΠ° ΠΊ ΡΠΈΠΊΡΠΈΡΡΡΡΠ΅ΠΉ ΠΏΠ»Π°ΡΡΠΈΠ½Π΅ ΠΏΡΠΈΠ²Π°ΡΠΈΠ²Π°Π΅ΡΡΡ Π΄Π»ΠΈΠ½Π½Π°Ρ Π³Π°ΠΉΠΊΠ°. ΠΠ° ΡΠΎΡΠ΅Ρ ΡΠ²Π΅Π»Π»Π΅ΡΠ° Π½Π°Π²Π°ΡΠΈΠ²Π°Π΅ΡΡΡ ΠΏΠΎΠ»ΠΎΡΠ° Ρ ΠΎΡΠ²Π΅ΡΡΡΠΈΠ΅ΠΌ ΠΏΠΎ ΡΠ΅Π½ΡΡΡ.
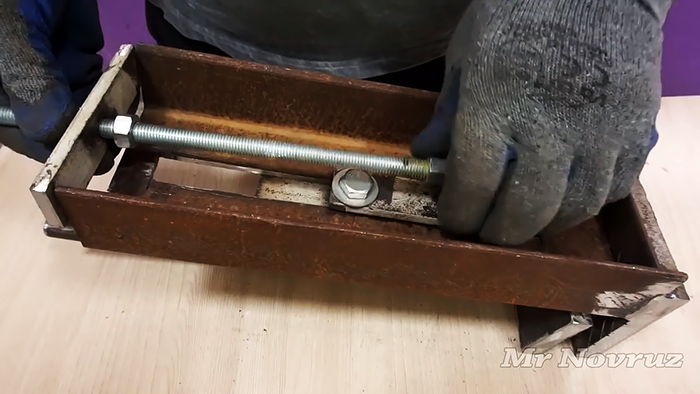
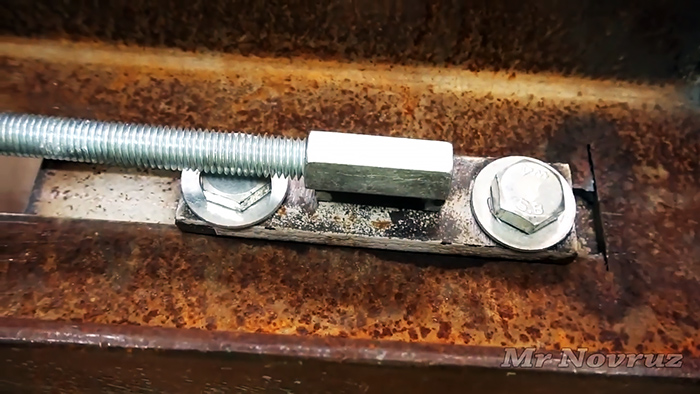
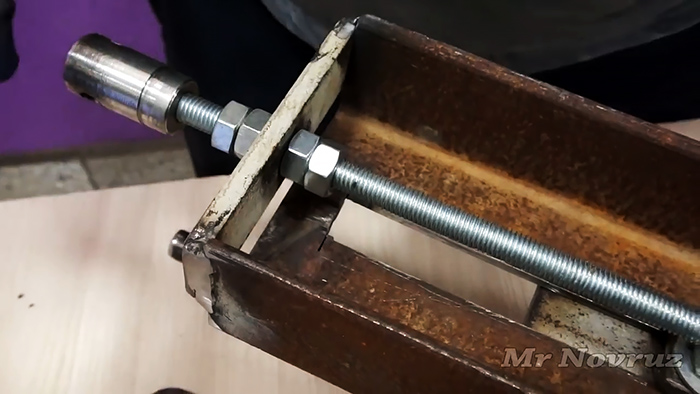
ΠΠ°ΡΠ΅ΠΌ ΡΠ΅ΡΠ΅Π· ΠΏΠ»Π°ΡΡΠΈΠ½Ρ Π² ΡΠΎΡΡΠ΅ ΡΠ²Π΅Π»Π»Π΅ΡΠ° Π² Π΄Π»ΠΈΠ½Π½ΡΡ Π³Π°ΠΉΠΊΡ Π½Π° ΠΊΠ°ΡΠ΅ΡΠΊΠ΅ Π·Π°Π²ΠΎΡΠ°ΡΠΈΠ²Π°Π΅ΡΡΡ ΡΠΏΠΈΠ»ΡΠΊΠ°. ΠΠ°ΠΆΠ½ΠΎ Π΅Π΅ Π·Π°ΡΠΈΠΊΡΠΈΡΠΎΠ²Π°ΡΡ Π² ΠΎΠ΄Π½ΠΎΠΌ ΠΏΠΎΠ»ΠΎΠΆΠ΅Π½ΠΈΠΈ. ΠΠ»Ρ ΡΡΠΎΠ³ΠΎ Π΄ΠΎ ΠΈ ΠΏΠΎΡΠ»Π΅ ΠΎΠΏΠΎΡΠ½ΠΎΠΉ ΠΏΠ»Π°ΡΡΠΈΠ½Ρ ΡΠ²Π΅Π»Π»Π΅ΡΠ° ΡΡΡΠ°Π½Π°Π²Π»ΠΈΠ²Π°Π΅ΡΡΡ ΠΏΠΎ 2 Π³Π°ΠΉΠΊΠΈ. Π ΡΠ°ΠΊΠΎΠΌ ΡΠ»ΡΡΠ°Π΅ Π²ΡΠ°ΡΠ°Ρ ΡΠΏΠΈΠ»ΡΠΊΡ Π·Π° ΡΡΠΊΠΎΡΡΠΊΡ, ΠΌΠΎΠΆΠ½ΠΎ Π±ΡΠ΄Π΅Ρ Π΄Π²ΠΈΠ³Π°ΡΡ ΠΊΠ°ΡΠ΅ΡΠΊΡ Ρ ΡΡΡΠ°Π³ΠΎΠΌ.
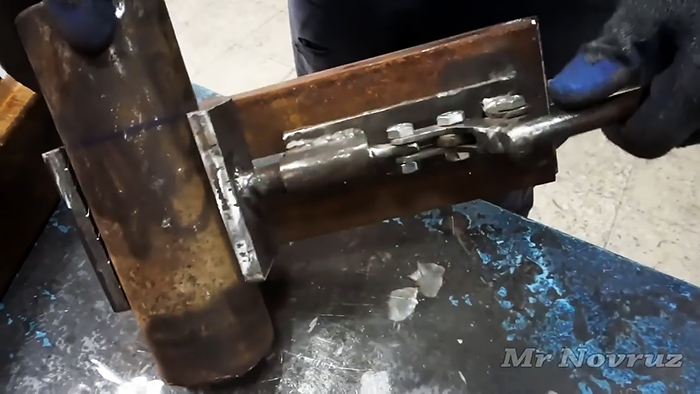
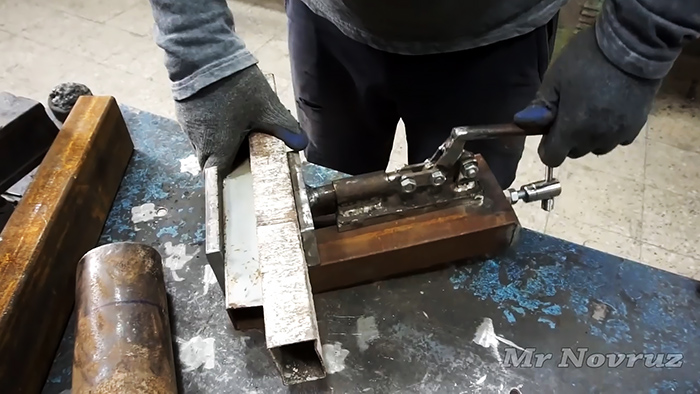
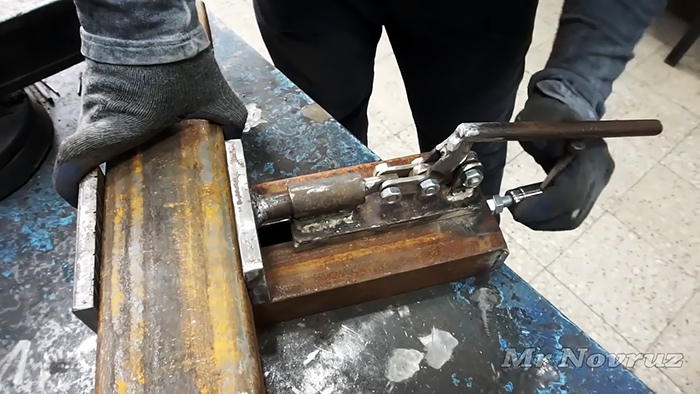
Π‘ΠΌΠΎΡΡΠΈΡΠ΅ Π²ΠΈΠ΄Π΅ΠΎ
ΠΠ°ΠΊ ΡΠ΄Π΅Π»Π°ΡΡ ΡΠΈΡΠΊΠΈ ΡΠ²ΠΎΠΈΠΌΠΈ ΡΡΠΊΠ°ΠΌΠΈ? Π§Π΅ΡΡΠ΅ΠΆΠΈ Ρ ΡΠ°Π·ΠΌΠ΅ΡΠ°ΠΌΠΈ
ΠΠ»Ρ ΡΠΈΠΊΡΠ°ΡΠΈΠΈ Π΄Π΅ΡΠ°Π»Π΅ΠΉ Π²ΠΎ Π²ΡΠ΅ΠΌΡ ΠΎΠ±ΡΠ°Π±ΠΎΡΠΊΠΈ Π½ΡΠΆΠ½Ρ ΡΠΏΠ΅ΡΠΈΠ°Π»ΡΠ½ΡΠ΅ ΡΠΈΠΊΡΠ°ΡΠΎΡΡ. Π‘Π΄Π΅Π»Π°ΡΡ ΡΠΈΡΠΊΠΈ ΡΠ²ΠΎΠΈΠΌΠΈ ΡΡΠΊΠ°ΠΌΠΈ ΡΠ°Π·Π½ΡΡ ΡΠ°Π·ΠΌΠ΅ΡΠΎΠ² Π½Π΅ΡΠ»ΠΎΠΆΠ½ΠΎ, ΠΏΠΎΡΡΠ΅Π±ΡΡΡΡΡ ΡΠ΅ΡΡΠ΅ΠΆΠΈ Ρ ΡΠ°Π·ΠΌΠ΅ΡΠ°ΠΌΠΈ, Π° ΡΠ°ΠΊΠΆΠ΅ ΡΠ΅Ρ Π½ΠΎΠ»ΠΎΠ³ΠΈΡΠ΅ΡΠΊΠ°Ρ ΠΏΠΎΡΠ»Π΅Π΄ΠΎΠ²Π°ΡΠ΅Π»ΡΠ½ΠΎΡΡΡ Π²ΡΠΏΠΎΠ»Π½Π΅Π½ΠΈΡ ΡΠ°Π±ΠΎΡ.
Π£ Π΄ΠΎΠΌΠ°ΡΠ½Π΅Π³ΠΎ ΠΌΠ°ΡΡΠ΅ΡΠ° Π² Π°ΡΡΠ΅Π½Π°Π»Π΅ ΠΎΠ±ΡΡΠ½ΠΎ ΠΌΠ½ΠΎΠ³ΠΎ ΡΠ°ΠΌΡΡ ΡΠ°Π·Π½ΡΡ ΠΈΠ½ΡΡΡΡΠΌΠ΅Π½ΡΠΎΠ². ΠΠ΄Π½Π°ΠΊΠΎ, ΡΡΡΠ΄Π½ΠΎ ΠΏΠ΅ΡΠ΅ΠΎΡΠ΅Π½ΠΈΡΡ ΡΠΎΠ»Ρ ΡΠΈΡΠΊΠΎΠ². ΠΡ ΠΈΡΠΏΠΎΠ»ΡΠ·ΡΡΡ Π΄Π»Ρ ΡΡΡΠ°Π½ΠΎΠ²ΠΊΠΈ Π΄Π΅ΡΠ°Π»Π΅ΠΉ ΡΠ°Π·Π½ΠΎΠ³ΠΎ ΡΠ°Π·ΠΌΠ΅ΡΠ°, ΠΏΠΎΡΡΠΎΠΌΡ Π² ΠΎΠ΄Π½ΠΎΠΉ ΠΌΠ°ΡΡΠ΅ΡΡΠΊΠΎΠΉ ΠΌΠΎΠ³ΡΡ ΠΏΡΠΈΡΡΡΡΡΠ²ΠΎΠ²Π°ΡΡ ΡΠΈΠΊΡΠΈΡΡΡΡΠΈΠ΅ ΠΏΡΠΈΡΠΏΠΎΡΠΎΠ±Π»Π΅Π½ΠΈΡ ΡΠ°Π·Π»ΠΈΡΠ½ΠΎΠ³ΠΎ Π²ΠΈΠ΄Π° ΠΈ ΠΊΠΎΠ½ΡΡΡΡΠΊΡΠΈΠ²Π½ΠΎΠ³ΠΎ ΠΈΡΠΏΠΎΠ»Π½Π΅Π½ΠΈΡ. Π ΠΌΠ΅ΡΠ°Π»Π»ΠΎΠΎΠ±ΡΠ°Π±ΠΎΡΠΊΠ΅ ΠΈΡΠΏΠΎΠ»ΡΠ·ΡΡΡ ΠΏΡΠ΅ΠΈΠΌΡΡΠ΅ΡΡΠ²Π΅Π½Π½ΠΎ ΠΌΠ΅ΡΠ°Π»Π»ΠΈΡΠ΅ΡΠΊΠΈΠ΅ ΠΈΠ·Π΄Π΅Π»ΠΈΡ, Π° Π΄Π»Ρ ΠΎΠ±ΡΠ°Π±ΠΎΡΠΊΠΈ Π΄ΡΠ΅Π²Π΅ΡΠΈΠ½Ρ ΡΠΈΡΠΎΠΊΠΎ ΠΏΡΠΈΠΌΠ΅Π½ΡΡΡ Π΄Π΅ΡΠ΅Π²ΡΠ½Π½ΡΠ΅ ΡΡΡΡΠΎΠΉΡΡΠ²Π°. ΠΠ΅ΠΊΠΎΡΠΎΡΡΠ΅ ΠΌΠ°ΡΡΠ΅ΡΠ° ΠΎΡΠ½Π°ΡΠ°ΡΡ ΡΠ²ΠΎΠΈ ΡΠ°Π±ΠΎΡΠΈΠ΅ ΡΡΠΎΠ»Ρ ΡΠ°ΠΌΠΎΠ΄Π΅Π»ΡΠ½ΡΠΌΠΈ ΡΠ»Π΅ΡΠ°ΡΠ½ΡΠΌΠΈ ΡΠΈΡΠΊΠ°ΠΌΠΈ. ΠΡΠ²Π°Π΅Ρ ΡΠ°ΠΊ, ΡΡΠΎ Π½ΡΠΆΠ΅Π½ ΡΠΏΠ΅ΡΠΈΠ°Π»ΡΠ½ΡΠΉ ΠΊΡΠ΅ΠΏΠ΅ΠΆΠ½ΡΠΉ ΠΈΠ½ΡΡΡΡΠΌΠ΅Π½Ρ.
ΠΠ»Π΅ΠΌΠ΅Π½ΡΡ ΡΠΈΡΠΊΠΎΠ²
ΠΠ°ΠΆΠΈΠΌΠ½ΠΎΠ΅ ΠΏΡΠΈΡΠΏΠΎΡΠΎΠ±Π»Π΅Π½ΠΈΠ΅ Π΄ΠΎΠ»ΠΆΠ½ΠΎ ΠΈΠΌΠ΅ΡΡ Π½Π΅ΡΠΊΠΎΠ»ΡΠΊΠΎ ΠΎΡΠ½ΠΎΠ²Π½ΡΡ ΡΠ»Π΅ΠΌΠ΅Π½ΡΠΎΠ²:
- Π³ΡΠ±ΠΊΠ° Π½Π΅ΠΏΠΎΠ΄Π²ΠΈΠΆΠ½Π°Ρ;
- Π³ΡΠ±ΠΊΠ° ΠΏΠΎΠ΄Π²ΠΈΠΆΠ½Π°Ρ;
- Π²ΠΈΠ½ΡΠΎΠ²ΠΎΠΉ ΠΌΠ΅Ρ Π°Π½ΠΈΠ·ΠΌ;
- ΡΠ³ΠΎΠ»ΠΎΠΊ ΠΏΠΎΠΏΠ΅ΡΠ΅ΡΠ½ΡΠΉ;
- ΡΠΊΠΎΠ±Π° ΠΏΠΎΠ΄Π²ΠΈΠΆΠ½ΠΎΠΉ Π³ΡΠ±ΠΊΠΈ;
- ΠΏΠΎΠ»Π·ΡΠ½;
- ΠΎΡΠ½ΠΎΠ²Π½Π°Ρ ΠΎΠΏΠΎΡΠ° (ΡΠ³ΠΎΠ»ΠΎΠΊ ΠΏΡΠΎΠ΄ΠΎΠ»ΡΠ½ΡΠΉ).
Π‘Ρ Π΅ΠΌΠ° ΡΠ°ΠΌΠΎΠ΄Π΅Π»ΡΠ½ΡΡ ΡΠΈΡΠΊΠΎΠ²
ΠΠΎΠ½ΡΡΡΡΠΊΡΠΈΠ²Π½ΠΎ ΡΠ΅ΡΠ΅Π½ΠΈΠ΅ Π·Π°ΠΆΠΈΠΌΠ° ΠΌΠΎΠΆΠ΅Ρ Π±ΡΡΡ ΡΠ°Π·Π»ΠΈΡΠ½ΡΠΌ. ΠΠ½ΠΎΠ³Π΄Π° Π² ΠΊΠ°ΡΠ΅ΡΡΠ²Π΅ ΠΈΡΡ ΠΎΠ΄Π½ΡΡ ΠΌΠ°ΡΠ΅ΡΠΈΠ°Π»ΠΎΠ² ΠΈΡΠΏΠΎΠ»ΡΠ·ΡΡΡ Π΄Π°ΠΆΠ΅ ΠΎΠ±ΡΡΠ½ΡΠ΅ ΠΏΠ°ΡΡΠ°ΡΠΈΠΆΠΈ.
Π‘Π°ΠΌΡΠ΅ ΠΏΡΠΎΡΡΡΠ΅ ΠΊΠΎΠ½ΡΡΡΡΠΊΡΠΈΠΈ
ΠΡΠΈΠ½ΡΡΠΎ ΠΎΠΏΡΠ΅Π΄Π΅Π»ΡΡΡ ΠΏΠΎ ΠΎΡΠΎΠ±Π΅Π½Π½ΠΎΡΡΡΠΌ ΡΡΡΡΠΎΠΉΡΡΠ²Π° ΡΠ»Π΅Π΄ΡΡΡΠΈΠ΅ Π²ΠΈΠ΄Ρ ΡΠΈΡΠΊΠΎΠ²:
- ΠΌΠ°ΡΡΠΈΠ²Π½ΡΠ΅ ΡΡΠ°ΡΠΈΠΎΠ½Π°ΡΠ½ΡΠ΅. Π’Π°ΠΊΠΈΠ΅ ΠΎΠ±ΡΡΠ½ΠΎ ΡΠ°Π·ΠΌΠ΅ΡΠ°ΡΡ Π½Π° ΠΎΠ΄Π½ΠΎΠΌ ΠΈΠ· ΡΠ³Π»ΠΎΠ² Π²Π΅ΡΡΡΠ°ΠΊΠ°. Π ΠΊΡΠ·Π½ΡΡ ΠΏΡΠΈΠ½ΡΡΠΎ ΡΡΡΠ°Π½Π°Π²Π»ΠΈΠ²Π°ΡΡ Π½Π° ΠΎΡΠ΄Π΅Π»ΡΠ½ΡΡ ΠΎΠΏΠΎΡΡ, ΡΡΡΠ°Π½ΠΎΠ²Π»Π΅Π½Π½ΡΡ Π½Π° ΠΌΠΎΡΠ½ΡΠΉ ΡΡΠ½Π΄Π°ΠΌΠ΅Π½Ρ;
- ΠΏΠΎΠ²ΠΎΡΠΎΡΠ½ΡΠ΅ ΠΌΠΎΠΆΠ½ΠΎ ΠΈΡΠΏΠΎΠ»ΡΠ·ΠΎΠ²Π°ΡΡ Ρ Π½Π΅ΡΠΊΠΎΠ»ΡΠΊΠΈΡ ΡΡΠΎΡΠΎΠ½. ΠΡΠΈ Π½Π΅ΠΎΠ±Ρ ΠΎΠ΄ΠΈΠΌΠΎΡΡΠΈ ΡΠ°ΡΠΏΠΎΠ»ΠΎΠΆΠ΅Π½ΠΈΠ΅ Π³ΡΠ±ΠΎΠΊ ΠΎΡΠΈΠ΅Π½ΡΠΈΡΡΡΡ Π² ΡΠ°Π·Π½ΡΡ Π½Π°ΠΏΡΠ°Π²Π»Π΅Π½ΠΈΡΡ ;
- ΠΌΠ°ΡΠΈΠ½Π½ΡΠ΅ ΠΏΡΠ΅Π΄ΡΡΠΌΠ°ΡΡΠΈΠ²Π°ΡΡ Π΄Π»Ρ ΠΈΡΠΏΠΎΠ»ΡΠ·ΠΎΠ²Π°Π½ΠΈΡ Π½Π° ΡΠ²Π΅ΡΠ»ΠΈΠ»ΡΠ½ΡΡ ΡΡΠ°Π½ΠΊΠ°Ρ . ΠΠΎΠΆΠ½ΠΎ ΡΠ°ΡΠΏΠΎΠ»Π°Π³Π°ΡΡ ΠΏΠΎΠ΄ΠΎΠ±Π½ΡΠ΅ ΠΈΠ·Π΄Π΅Π»ΠΈΡ Π½Π° ΡΡΠ΅Π·Π΅ΡΠ½ΡΡ ΡΡΠΎΠ»Π°Ρ , ΡΡΡΠΎΠ³Π°Π»ΡΠ½ΠΎΠΌ ΠΈΠ»ΠΈ Π΄ΠΎΠ»Π±Π΅ΠΆΠ½ΠΎΠΌ ΠΎΠ±ΠΎΡΡΠ΄ΠΎΠ²Π°Π½ΠΈΠΈ, Π° ΡΠ°ΠΊΠΆΠ΅ Π½Π° ΡΠ²Π°ΡΠΎΡΠ½ΡΡ Π»ΠΈΠ½ΠΈΡΡ ;
- ΠΊΠ»ΠΈΠ½ΠΎΠ²ΡΠ΅ ΠΎΡΠ»ΠΈΡΠ°ΡΡΡΡ ΡΠ΅ΠΌ, ΡΡΠΎ ΠΊΠΎΠ½ΡΡΡΡΠΊΡΠΈΡ ΠΈΠΌΠ΅Π΅Ρ ΡΠ²ΠΎΠ΅ΠΎΠ±ΡΠ°Π·Π½ΡΠΉ Π²ΠΈΠ΄. Π’Π°ΠΊΠΈΠ΅ ΡΠΈΠΊΡΠ°ΡΠΎΡΡ ΠΏΠΎΠ·Π²ΠΎΠ»ΡΡΡ ΡΠ°Π·Π²ΠΈΠ²Π°ΡΡ Π΄ΠΎΠ²ΠΎΠ»ΡΠ½ΠΎ Π±ΠΎΠ»ΡΡΠΈΠ΅ ΡΡΠΈΠ»ΠΈΡ ΠΏΡΠΈΠΆΠ°ΡΠΈΡ Π·Π°ΠΊΡΠ΅ΠΏΠ»ΡΠ΅ΠΌΡΡ Π΄Π΅ΡΠ°Π»Π΅ΠΉ;
- ΠΏΠ°ΡΠ°Π»Π»Π΅Π»ΡΠ½ΡΠ΅ ΠΊΠΎΠ½ΡΡΡΡΠΊΡΠΈΠΈ ΠΠΎΠΊΡΠΎΠ½Π°. ΠΡΠΎΠ±Π΅Π½Π½ΠΎΡΡΡΡ ΠΈΡ ΡΠ²Π»ΡΠ΅ΡΡΡ ΠΈΡΠΏΠΎΠ»ΡΠ·ΠΎΠ²Π°Π½ΠΈΠ΅ Π½Π΅ ΠΎΠ΄Π½ΠΎΠ³ΠΎ, Π° Π½Π΅ΡΠΊΠΎΠ»ΡΠΊΠΈΡ Π²ΠΈΠ½ΡΠΎΠ²ΡΡ Π·Π°ΠΆΠΈΠΌΠΎΠ². ΠΠ»ΠΈΠ½Π½ΠΎΠΌΠ΅ΡΠ½ΡΠ΅ Π΄Π΅ΡΠ°Π»ΠΈ Π² ΡΠ°Π·Π½ΡΡ ΡΠ°ΡΡΡΡ Π·Π°ΠΊΡΠ΅ΠΏΠ»ΡΡΡΡΡ Π² ΡΠ°Π·Π½ΡΡ ΡΠΎΡΠΊΠ°Ρ ;
- Π²Π΅ΡΡΠΈΠΊΠ°Π»ΡΠ½ΡΠ΅ ΠΈΡΠΏΠΎΠ»ΡΠ·ΡΡΡ Π΄Π»Ρ ΠΎΠ±ΡΠ°Π±ΠΎΡΠΊΠΈ ΠΈΠ·Π΄Π΅Π»ΠΈΠΉ, ΠΈΠΌΠ΅ΡΡΠΈΡ Π±ΠΎΠ»ΡΡΡΡ Π²ΡΡΠΎΡΡ. ΠΠΏΠΎΡΠ° ΠΏΠΎΠ΄ΠΎΠ±Π½ΡΡ ΡΠΈΡΠΊΠΎΠ² ΠΌΠΎΠΆΠ΅Ρ Π½Π°Ρ ΠΎΠ΄ΠΈΡΡΡΡ Π²Π½ΠΈΠ·Ρ, Π° Π·ΠΎΠ½Π° ΠΎΠ±ΡΠ°Π±ΠΎΡΠΊΠΈ ΡΠ°ΡΠΏΠΎΠ»Π°Π³Π°Π΅ΡΡΡ ΡΠ²Π΅ΡΡ Ρ.
Π Π°Π·ΡΠ°Π±ΠΎΡΠΊΠ° ΠΊΠΎΠ½ΡΡΡΡΠΊΡΠΈΠΈ ΡΠΈΡΠΊΠΎΠ²
Π§Π΅ΡΡΠ΅ΠΆ ΡΠ°ΠΌΠΎΠ΄Π΅Π»ΡΠ½ΡΡ ΡΠΈΡΠΊΠΎΠ²
ΠΡΠΈ ΠΆΠ΅Π»Π°Π½ΠΈΠΈ ΡΠ°ΠΌΠΎΡΡΠΎΡΡΠ΅Π»ΡΠ½ΠΎ ΠΈΠ·Π³ΠΎΡΠΎΠ²ΠΈΡΡ ΡΠΎΠ±ΡΡΠ²Π΅Π½Π½ΡΡ ΠΊΠΎΠ½ΡΡΡΡΠΊΡΠΈΡ, Π½Π΅ΠΎΠ±Ρ ΠΎΠ΄ΠΈΠΌΠΎ ΠΏΠΎΠ΄Π³ΠΎΡΠΎΠ²ΠΈΡΡ ΡΠ΅ΡΡΠ΅ΠΆΠΈ (ΡΡΠΊΠΈΠ·Ρ). ΠΠ° ΠΎΡΠ½ΠΎΠ²Ρ ΠΌΠΎΠΆΠ½ΠΎ Π²Π·ΡΡΡ ΠΊΠ°ΡΠ°Π½ΡΠ΅ ΡΠ³ΠΎΠ»ΠΊΠΈ, ΡΠ²Π΅Π»Π»Π΅ΡΡ, Π΄Π²ΡΡΠ°Π²ΡΡ. Π ΠΏΡΠΎΠΌΡΡΠ»Π΅Π½Π½ΡΡ ΡΡΡΡΠΎΠΉΡΡΠ²Π°Ρ ΠΈΡΠΏΠΎΠ»ΡΠ·ΡΡΡ ΡΡΠ³ΡΠ½Π½ΠΎΠ΅ Π»ΠΈΡΡΠ΅. ΠΠ΅Π±ΠΎΠ»ΡΡΠΈΠ΅ ΠΏΠΎ ΡΠ°Π·ΠΌΠ΅ΡΡ ΠΌΠΎΠ³ΡΡ ΠΈΠ·Π³ΠΎΡΠ°Π²Π»ΠΈΠ²Π°ΡΡΡΡ ΠΈΠ· ΡΠ²Π΅Π»Π»Π΅ΡΠ°.
Π‘Π°ΠΌΠΎΠ΄Π΅Π»ΡΡΠΈΠΊΠΈ ΠΈΡΠΏΠΎΠ»ΡΠ·ΡΡΡ ΡΠ°Π·Π½ΡΠ΅ Π²ΠΈΠ΄Ρ Π΄ΡΠ΅Π²Π΅ΡΠΈΠ½Ρ ΠΈΠ»ΠΈ ΠΌΠ΅ΡΠ°Π»Π»ΠΎΠΏΡΠΎΠΊΠ°Ρ.
ΠΠ΅ΡΠ΅Π²ΡΠ½Π½Π°Ρ ΠΊΠΎΠ½ΡΡΡΡΠΊΡΠΈΡ
Π ΡΠΎΡΡΠ°Π²Π΅ ΠΈΠ·Π΄Π΅Π»ΠΈΠΉ ΠΈΠ· Π΄Π΅ΡΠ΅Π²Π° ΠΈΡΠΏΠΎΠ»ΡΠ·ΡΡΡ ΠΌΠ΅ΡΠ°Π»Π»ΠΈΡΠ΅ΡΠΊΠΈΠ΅ ΡΠ»Π΅ΠΌΠ΅Π½ΡΡ:
- Π²ΠΈΠ½Ρ. ΠΡΠΈΠΌΠ΅Π½ΡΡΡ ΡΠΏΠΈΠ»ΡΠΊΠΈ ΡΠΎ ΡΡΠ°Π½Π΄Π°ΡΡΠ½ΠΎΠΉ ΡΠ΅Π·ΡΠ±ΠΎΠΉ. ΠΡΠ»ΠΈ Π² Π½Π°Π»ΠΈΡΠΈΠΈ Π΅ΡΡΡ Π΄ΠΎΠΌΠΊΡΠ°Ρ, ΡΠΎ Π² ΡΠ°Π·ΡΠ°Π±Π°ΡΡΠ²Π°Π΅ΠΌΠΎΠΌ ΠΈΠ·Π΄Π΅Π»ΠΈΠΈ Π±ΡΠ΄Π΅Ρ ΠΈΡΠΏΠΎΠ»ΡΠ·ΠΎΠ²Π°ΡΡΡΡ ΠΏΡΡΠΌΠΎΡΠ³ΠΎΠ»ΡΠ½Π°Ρ ΡΠ΅Π·ΡΠ±Π°;
- Π³Π°ΠΉΠΊΠ°. ΠΠ΅ ΠΏΠΎΠ΄Π±ΠΈΡΠ°ΡΡ ΠΏΠΎΠ΄ ΠΈΠΌΠ΅ΡΡΠΈΠΉΡΡ Π·Π°ΠΆΠΈΠΌΠ½ΠΎΠΉ Π²ΠΈΠ½Ρ;
- ΠΊΡΠ΅ΠΏΠ΅ΠΆΠ½ΡΠ΅ ΡΠ»Π΅ΠΌΠ΅Π½ΡΡ ΠΈΡΠΏΠΎΠ»ΡΠ·ΡΡΡ Π΄Π»Ρ ΠΏΡΠΈΠ΄Π°Π½ΠΈΡ ΠΆΠ΅ΡΡΠΊΠΎΡΡΠΈ.
ΠΠ΅Π³ΠΊΠΎΡΡΠ΅ΠΌΠ½Π°Ρ ΠΊΠΎΠ½ΡΡΡΡΠΊΡΠΈΡ
ΠΠΎ ΠΈΡΠΏΠΎΠ»Π½Π΅Π½ΠΈΡ ΡΡΡΡΠΎΠΉΡΡΠ²Π° ΠΌΠΎΠ³ΡΡ Π±ΡΡΡ:
- ΡΡΠ°ΡΠΈΠΎΠ½Π°ΡΠ½ΡΠΌΠΈ ΡΠΈΡΠΊΠ°ΠΌΠΈ, ΡΠ°Π·ΠΌΠ΅ΡΠ°Π΅ΠΌΡΠ΅ ΠΏΠΎΡΡΠΎΡΠ½Π½ΠΎ Π½Π° ΠΎΠ΄Π½ΠΎΠΌ ΠΌΠ΅ΡΡΠ΅;
- ΠΏΠ΅ΡΠ΅Π½ΠΎΡΠ½ΡΠΌΠΈ (Π»Π΅Π³ΠΊΠΎΡΡΠ΅ΠΌΠ½ΡΠΌΠΈ) ΡΠΈΡΠΊΠ°ΠΌΠΈ. ΠΡ ΠΌΠΎΠΆΠ½ΠΎ Π±ΡΡΡΡΠΎ ΡΠ½ΡΡΡ, ΡΠ»ΠΎΠΆΠΈΡΡ Π² ΡΡΠ°Π½ΡΠΏΠΎΡΡΠ½ΠΎΠ΅ ΡΡΠ΅Π΄ΡΡΠ²ΠΎ Π΄Π»Ρ Π²ΡΠΏΠΎΠ»Π½Π΅Π½ΠΈΡ ΡΠ°Π±ΠΎΡ ΠΏΠΎ ΠΌΠ΅ΡΡΡ Π²ΡΠΏΠΎΠ»Π½Π΅Π½ΠΈΡ ΡΠ΅ΠΌΠΎΠ½ΡΠ°.
ΠΠΎΡΠ°Π³ΠΎΠ²ΡΠ΅ ΡΠ΅Ρ Π½ΠΎΠ»ΠΎΠ³ΠΈΠΈ ΠΈΠ·Π³ΠΎΡΠΎΠ²Π»Π΅Π½ΠΈΡ Π΄Π΅ΡΠ΅Π²ΡΠ½Π½ΡΡ ΡΠΈΡΠΊΠΎΠ² Π² Π΄ΠΎΠΌΠ°ΡΠ½ΠΈΡ ΡΡΠ»ΠΎΠ²ΠΈΡΡ
ΠΠΎΠ½ΡΡΡΡΠΊΡΠΈΡ Π΄Π»Ρ Π²Π΅ΡΡΡΠ°ΠΊΠ°
Π Π΄ΠΎΠΌΠ°ΡΠ½ΠΈΡ ΡΡΠ»ΠΎΠ²ΠΈΡΡ ΡΠΈΡΠΊΠΈ Π΄Π»Ρ Π²Π΅ΡΡΡΠ°ΠΊΠ° ΠΈΠ·Π³ΠΎΡΠ°Π²Π»ΠΈΠ²Π°ΡΡΡΡ Π² ΡΠ»Π΅Π΄ΡΡΡΠ΅ΠΉ ΠΏΠΎΡΠ»Π΅Π΄ΠΎΠ²Π°ΡΠ΅Π»ΡΠ½ΠΎΡΡΠΈ.
ΠΠ·Π³ΠΎΡΠΎΠ²Π»Π΅Π½ΠΈΠ΅ Π΄Π΅ΡΠ΅Π²ΡΠ½Π½ΡΡ ΡΠΈΡΠΊΠΎΠ², ΡΡΡΠ°Π½Π°Π²Π»ΠΈΠ²Π°Π΅ΠΌΡΡ Π½Π° ΡΡΠΎΠ»Π΅
ΠΡΡΠ³Π°Ρ ΠΊΠΎΠ½ΡΡΡΡΠΊΡΠΈΡ ΠΈΡΠΏΠΎΠ»ΡΠ·ΡΠ΅ΡΡΡ Π² ΡΡΠΎΠ»ΡΡΠ½ΠΎΠΌ ΠΏΡΠΎΠΈΠ·Π²ΠΎΠ΄ΡΡΠ²Π΅. ΠΡΠΎΡ Π²ΠΈΠ΄ ΠΊΡΠ΅ΠΏΠ΅ΠΆΠ° ΡΡΡΠ°Π½Π°Π²Π»ΠΈΠ²Π°Π΅ΡΡΡ Π½Π° ΡΡΠΎΠ»Π΅. ΠΡ Π΄ΠΎΠΏΠΎΠ»Π½ΠΈΡΠ΅Π»ΡΠ½ΠΎ ΠΌΠΎΠΆΠ½ΠΎ ΡΠΊΡΠ΅ΠΏΠΈΡΡ Ρ ΠΏΠΎΠΌΠΎΡΡΡ ΡΡΡΡΠ±ΡΠΈΠ½.
![]() | ΠΠΎΡΠΎΠ²Π°Ρ ΠΏΠ»Π°ΡΡΠΈΠ½Π° Ρ ΠΎΡΠ²Π΅ΡΡΡΠΈΠ΅ΠΌ Γ 20 ΠΌΠΌ. |
![]() | ΠΡΠΏΠΎΠ»Π½Π΅Π½ΠΈΠ΅ Π΄ΠΎΠΏΠΎΠ»Π½ΠΈΡΠ΅Π»ΡΠ½ΡΡ ΠΏΡΠΎΠΏΠΈΠ»ΠΎΠ². |
![]() | ΠΠΎΡΠΎΠ²ΠΎΠ΅ ΠΈΠ·Π΄Π΅Π»ΠΈΠ΅ ΠΈΡΠΏΠΎΠ»ΡΠ·ΡΠ΅ΡΡΡ Π΄Π»Ρ ΡΠΈΠΊΡΠ°ΡΠΈΠΈ Π·Π°Π³ΠΎΡΠΎΠ²ΠΎΠΊ ΠΏΡΠΈ ΠΈΠ·Π³ΠΎΡΠΎΠ²Π»Π΅Π½ΠΈΠΈ Π½Π΅Π±ΠΎΠ»ΡΡΠΈΡ ΡΠΊΡΠ»ΡΠΏΡΡΡ ΠΈΠ· Π΄ΡΠ΅Π²Π΅ΡΠΈΠ½Ρ ΠΌΡΠ³ΠΊΠΈΡ ΠΏΠΎΡΠΎΠ΄. |
ΠΡΠΎΡΡΡΠ΅ Π΄Π΅ΡΠ΅Π²ΡΠ½Π½ΡΠ΅ ΡΠΈΡΠΊΠΈ
![]() | ΠΠΎΠ»ΡΡ Π8 ΠΈΡΠΏΠΎΠ»ΡΠ·ΡΡΡΡΡ Π΄Π»Ρ ΡΡΡΠ°Π½ΠΎΠ²ΠΊΠΈ Π±ΡΡΡΠΊΠΎΠ². |
![]() | ΠΠ΅ΠΏΠΎΠ΄Π²ΠΈΠΆΠ½Π°Ρ Π³ΡΠ±ΠΊΠ° ΠΌΠΎΠΆΠ΅Ρ ΡΡΡΠ°Π½Π°Π²Π»ΠΈΠ²Π°ΡΡΡΡ Π² Π½Π΅ΡΠΊΠΎΠ»ΡΠΊΠΈΡ ΠΏΠΎΠ»ΠΎΠΆΠ΅Π½ΠΈΡΡ . ΠΠΎΡΡΠΎΠΌΡ Π² ΡΠΈΡΠΊΠ°Ρ ΠΌΠΎΠΆΠ½ΠΎ ΡΠΈΠΊΡΠΈΡΠΎΠ²Π°ΡΡ Π΄Π΅ΡΠ°Π»ΠΈ ΡΠ°Π·Π½ΠΎΠΉ ΡΠΈΡΠΈΠ½Ρ. |
![]() | Π’ΠΈΡΠΊΠΈ Π³ΠΎΡΠΎΠ²Ρ. ΠΠΌΠΈ ΠΌΠΎΠΆΠ½ΠΎ ΠΏΠΎΠ»ΡΠ·ΠΎΠ²Π°ΡΡΡΡ Π΄Π»Ρ ΡΠ°Π±ΠΎΡΡ Ρ Π΄Π΅ΡΠ΅Π²ΡΠ½Π½ΡΠΌΠΈ Π·Π°Π³ΠΎΡΠΎΠ²ΠΊΠ°ΠΌΠΈ. |
ΠΠ·Π³ΠΎΡΠΎΠ²Π»Π΅Π½ΠΈΠ΅ ΡΠΈΡΠΊΠΎΠ² ΠΈΠ· ΠΌΠ΅ΡΠ°Π»Π»Π°
ΠΠ°Π»ΠΎΠ³Π°Π±Π°ΡΠΈΡΠ½ΡΠ΅ ΡΡΠ°Π½ΠΎΡΠ½ΡΠ΅ ΡΠΈΡΠΊΠΈ
![]() | ΠΡΠΎΠΈΠ·Π²ΠΎΠ΄ΠΈΡΡΡ ΠΏΠΎΠ΄Π³ΠΎΠ½ΠΊΠ° Π΄Π΅ΡΠ°Π»Π΅ΠΉ ΠΏΠΎ ΠΌΠ΅ΡΡΡ. |
![]() | ΠΡΠΈΠ²Π°ΡΠΈΠ² ΠΏΠ»Π°ΡΡΠΈΠ½Ρ, ΠΏΠΎΠ»ΡΡΠ°ΡΡ Π½Π΅Π±ΠΎΠ»ΡΡΠΈΠ΅ ΡΠΈΡΠΊΠΈ. |
![]() | ΠΡΠΎΠ²Π΅ΡΡΠΈ ΠΏΡΠΎΠ±Π½ΠΎΠ΅ ΠΈΡΠΏΠΎΠ»ΡΠ·ΠΎΠ²Π°Π½ΠΈΠ΅ ΠΌΠΎΠΆΠ½ΠΎ, Π·Π°ΠΊΡΠ΅ΠΏΠΈΠ² ΡΠΈΡΠΊΠΈ Π½Π° ΡΡΠΎΠ»Π΅. |
![]() | Π€ΠΈΠΊΡΠ°ΡΠΈΡ Π΄Π΅ΡΠ°Π»Π΅ΠΉ Π²ΡΠΏΠΎΠ»Π½ΡΠ΅ΡΡΡ Π½Π°Π΄Π΅ΠΆΠ½ΠΎ. |
Π’ΠΈΡΠΊΠΈ ΠΈΠ· ΡΠ²Π΅Π»Π»Π΅ΡΠ°
ΠΠ°ΡΡΠ΅ΡΠ° ΠΏΡΠ΅Π΄Π»Π°Π³Π°ΡΡ ΠΌΠ½ΠΎΠ³ΠΎ ΡΠ°Π·Π½ΠΎΠΎΠ±ΡΠ°Π·Π½ΡΡ ΠΊΠΎΠ½ΡΡΡΡΠΊΡΠΈΠΉ ΡΠ°ΠΌΠΎΠ΄Π΅Π»ΡΠ½ΡΡ ΡΠΈΡΠΊΠΎΠ². ΠΠΎΠΆΠ½ΠΎ ΠΏΠΎΠ΄ΠΎΠ±ΡΠ°ΡΡ ΠΏΠΎΠ΄Ρ ΠΎΠ΄ΡΡΠΈΠΉ Π²Π°ΡΠΈΠ°Π½Ρ, ΠΊΠΎΡΠΎΡΡΠΉ Π½Π΅ΡΠ»ΠΎΠΆΠ½ΠΎ ΠΏΠΎΠ²ΡΠΎΡΠΈΡΡ.
[autor_bq]
Π‘Π°ΠΌΠΎΠ΄Π΅Π»ΡΠ½ΡΠ΅ ΡΠΈΡΠΊΠΈ ΠΈΠ· ΠΌΠ΅ΡΠ°Π»ΠΎΠ»Π»ΠΎΠΌΠ°

ΠΡΠΈΠ²Π΅ΡΡΡΠ²ΡΡ Π»ΡΠ±ΠΈΡΠ΅Π»Π΅ΠΉ ΠΏΠΎΠΌΠ°ΡΡΠ΅ΡΠΈΡΡ, ΡΠ΅Π³ΠΎΠ΄Π½Ρ ΠΌΡ ΡΠ°ΡΡΠΌΠΎΡΡΠΈΠΌ, ΠΊΠ°ΠΊ ΠΈΠ·Π³ΠΎΡΠΎΠ²ΠΈΡΡ ΡΠ°ΠΊΡΡ ΠΏΠΎΠ»Π΅Π·Π½ΡΡ Π² Π±ΡΡΡ Π²Π΅ΡΡ ΠΊΠ°ΠΊ ΡΠΈΡΠΊΠΈ. ΠΠ²ΡΠΎΡ ΡΠ΅ΡΠΈΠ» ΡΠΎΠ±ΡΠ°ΡΡ ΡΠ°ΠΌΠΎΠ΄Π΅Π»ΠΊΡ ΠΈΠ· ΠΈΠΌΠ΅ΡΡΠ΅Π³ΠΎΡΡ ΠΌΠ΅ΡΠ°Π»Π»ΠΎΠ»ΠΎΠΌΠ°, ΠΏΠΎΠ»ΡΡΠΈΠ»ΠΎΡΡ Π²ΡΠ΅ Π°ΠΊΠΊΡΡΠ°ΡΠ½ΠΎ ΠΈ Π½Π°Π΄Π΅ΠΆΠ½ΠΎ. ΠΠΎΠ½Π΅ΡΠ½ΠΎ, Π½Π° ΠΏΠ΅ΡΠ²ΡΠΉ Π²Π·Π³Π»ΡΠ΄ Π½Π΅ ΠΎΡΠ΅Π½Ρ Π½Π°Π΄Π΅ΠΆΠ½ΠΎ ΡΠ΄Π΅Π»Π°Π½ Π²ΠΈΠ½ΡΠΎΠ²ΠΎΠΉ ΡΠ·Π΅Π», ΡΡΡ ΠΈΡΠΏΠΎΠ»ΡΠ·ΠΎΠ²Π°Π»ΡΡ ΠΎΠ±ΡΡΠ½ΡΠΉ ΡΠ΅Π·ΡΠ±ΠΎΠ²ΠΎΠΉ ΡΡΠ΅ΡΠΆΠ΅Π½Ρ ΠΈ Π³Π°ΠΉΠΊΠΈ, Π² ΡΠΎ Π²ΡΠ΅ΠΌΡ ΠΊΠ°ΠΊ Π² ΠΊΠ°ΡΠ΅ΡΡΠ²Π΅Π½Π½ΡΡ ΡΠΈΡΠΊΠ°Ρ ΠΈΡΠΏΠΎΠ»ΡΠ·ΡΠ΅Ρ Π²Π°Π» Ρ Π·Π°ΠΊΠ°Π»Π΅Π½Π½ΠΎΠΉ ΡΡΠ°Π»ΡΡ, Π° ΡΠ΅Π·ΡΠ±Π° ΠΈΠΌΠ΅Π΅Ρ ΠΎΡΠΎΠ±ΡΠΉ ΡΠ°Π³. Π’Π΅ΠΌ Π½Π΅ ΠΌΠ΅Π½Π΅Π΅, ΡΠΈΡΠΊΠΈ ΠΏΡΠ΅ΠΊΡΠ°ΡΠ½ΠΎ ΡΠΆΠΈΠΌΠ°ΡΡ ΠΊΡΡΠΎΠΊ ΠΏΡΠΎΡΠΈΠ»ΡΠ½ΠΎΠΉ ΡΡΡΠ±Ρ, ΡΠ°ΠΊ ΡΡΠΎ Π΄Π΅ΡΠΆΠ°ΡΡ ΠΏΡΠ΅Π΄ΠΌΠ΅ΡΡ ΠΎΠ½ΠΈ ΡΠΌΠΎΠ³ΡΡ Π²ΠΏΠΎΠ»Π½Π΅ Π½Π΅ΠΏΠ»ΠΎΡ ΠΎ. ΠΠ° ΡΠΈΡΠΊΠ°Ρ ΡΠ°ΠΊΠΆΠ΅ ΠΈΠΌΠ΅Π΅ΡΡΡ Π½Π΅Π±ΠΎΠ»ΡΡΠ°Ρ Π½Π°ΠΊΠΎΠ²Π°Π»ΡΠ½Ρ. ΠΡΠ»ΠΈ Π²Π°Ρ Π·Π°ΠΈΠ½ΡΠ΅ΡΠ΅ΡΠΎΠ²Π°Π» ΠΏΡΠΎΠ΅ΠΊΡ, ΠΏΡΠ΅Π΄Π»Π°Π³Π°Ρ ΠΈΠ·ΡΡΠΈΡΡ Π΅Π³ΠΎ Π±ΠΎΠ»Π΅Π΅ Π΄Π΅ΡΠ°Π»ΡΠ½ΠΎ!
ΠΠ°ΡΠ΅ΡΠΈΠ°Π»Ρ ΠΈ ΠΈΠ½ΡΡΡΡΠΌΠ΅Π½ΡΡ, ΠΊΠΎΡΠΎΡΡΠ΅ ΠΈΡΠΏΠΎΠ»ΡΠ·ΠΎΠ²Π°Π» Π°Π²ΡΠΎΡ:
Π‘ΠΏΠΈΡΠΎΠΊ ΠΌΠ°ΡΠ΅ΡΠΈΠ°Π»ΠΎΠ²:
— ΡΠ²Π΅Π»Π»Π΅Ρ;
— ΡΠ³ΠΎΠ»ΠΎΠΊ;
— Π»ΠΈΡΡΠΎΠ²ΠΎΠ΅ ΠΆΠ΅Π»Π΅Π·ΠΎ;
— ΡΠ΅Π·ΡΠ±ΠΎΠ²ΠΎΠΉ ΡΡΠ΅ΡΠΆΠ΅Π½Ρ, Π³Π°ΠΉΠΊΠΈ;
— ΡΡΠ°Π»ΡΠ½ΠΎΠΉ ΡΡΠ΅ΡΠΆΠ΅Π½Ρ Π΄Π»Ρ ΡΡΡΠΊΠΈ;
— ΠΊΡΠ°ΡΠΊΠ° ΠΏΠΎ ΠΌΠ΅ΡΠ°Π»Π»Ρ.

Π‘ΠΏΠΈΡΠΎΠΊ ΠΈΠ½ΡΡΡΡΠΌΠ΅Π½ΡΠΎΠ²:
— Π±ΠΎΠ»Π³Π°ΡΠΊΠ° Ρ ΠΎΡΡΠ΅Π·Π½ΡΠΌΠΈ ΠΈ ΡΠ»ΠΈΡΠΎΠ²Π°Π»ΡΠ½ΡΠΌΠΈ Π½Π°ΡΠ°Π΄ΠΊΠ°ΠΌΠΈ;
— Π΄ΡΠ΅Π»Ρ ΠΈΠ»ΠΈ ΡΠ²Π΅ΡΠ»ΠΈΠ»ΡΠ½ΡΠΉ ΡΡΠ°Π½ΠΎΠΊ;
— ΡΠ²Π°ΡΠΎΡΠ½ΡΠΉ Π°ΠΏΠΏΠ°ΡΠ°Ρ;
— ΠΌΠ°ΡΠΊΠ΅Ρ, ΡΡΠ»Π΅ΡΠΊΠ°.
ΠΡΠΎΡΠ΅ΡΡ ΠΈΠ·Π³ΠΎΡΠΎΠ²Π»Π΅Π½ΠΈΡ ΡΠΈΡΠΊΠΎΠ²:
Π¨Π°Π³ ΠΏΠ΅ΡΠ²ΡΠΉ. ΠΠΎΠ΄Π³ΠΎΡΠΎΠ²ΠΊΠ° ΠΌΠ°ΡΠ΅ΡΠΈΠ°Π»ΠΎΠ²
ΠΠΎΠ΄Π²ΠΈΠΆΠ½Π°Ρ ΡΠ°ΡΡΡ ΡΠΈΡΠΊΠΎΠ² ΠΈΠ·Π³ΠΎΡΠΎΠ²Π»Π΅Π½Π° ΠΈΠ· ΠΊΡΡΠΊΠ° ΡΠ²Π΅Π»Π»Π΅ΡΠ°, Π° Π΄Π»Ρ ΠΈΠ·Π³ΠΎΡΠΎΠ²Π»Π΅Π½ΠΈΡ ΠΎΡΠ½ΠΎΠ²Ρ Π°Π²ΡΠΎΡ ΠΈΡΠΏΠΎΠ»ΡΠ·ΠΎΠ²Π°Π» ΡΠΎΠ»ΡΡΠΎΠ΅ Π»ΠΈΡΡΠΎΠ²ΠΎΠ΅ ΠΆΠ΅Π»Π΅Π·ΠΎ. Π§ΡΠΎΠ±Ρ ΠΏΠΎΠ»ΡΡΠΈΡΡ ΠΎΡΠ½ΠΎΠ²Ρ Π½ΡΠΆΠ½ΡΡ
ΡΠ°Π·ΠΌΠ΅ΡΠΎΠ², Π°Π²ΡΠΎΡ ΡΠ²Π°ΡΠΈΠ» Π»ΠΈΡΡΡ Π²ΠΌΠ΅ΡΡΠ΅.
Π ΠΊΠ°ΡΠ΅ΡΡΠ²Π΅ Π½Π°ΠΏΡΠ°Π²Π»ΡΡΡΠ΅ΠΉ Π΄Π»Ρ ΡΠ²Π΅Π»Π»Π΅ΡΠ° (Π΄Π²ΠΈΠΆΡΡΠ΅ΠΉΡΡ ΡΠ°ΡΡΠΈ) Π°Π²ΡΠΎΡ ΠΈΡΠΏΠΎΠ»ΡΠ·ΠΎΠ²Π°Π» Π΄Π²Π° ΡΠ³ΠΎΠ»ΠΊΠ° ΠΈ Π»ΠΈΡΡΠΎΠ²ΠΎΠ΅ ΠΆΠ΅Π»Π΅Π·ΠΎ. ΠΡΠ±Ρ Π°Π²ΡΠΎΡ ΠΈΠ·Π³ΠΎΡΠΎΠ²ΠΈΠ» ΠΈΠ· ΡΠ³ΠΎΠ»ΠΊΠ°, ΠΎΠ½ΠΈ ΠΏΠΎΡΠΎΠΌ Π΄ΠΎΠΏΠΎΠ»Π½ΠΈΡΠ΅Π»ΡΠ½ΠΎ Π±ΡΠ»ΠΈ ΠΎΠ±Π²Π°ΡΠ΅Π½Ρ Π»ΠΈΡΡΠΎΠ²ΡΠΌ ΠΆΠ΅Π»Π΅Π·ΠΎΠΌ.
ΠΡΠ΅ ΡΠΎΡΡΠ°Π²Π»ΡΡΡΠΈΠ΅ Π½Π°ΡΠ΅Π·Π°Π΅ΠΌ ΠΈ ΠΎΡΠΈΡΠ°Π΅ΠΌ Π΄ΠΎ Π±Π»Π΅ΡΠΊΠ° Π±ΠΎΠ»Π³Π°ΡΠΊΠΎΠΉ Ρ ΡΠ΅ΡΠΎΡΠ½ΠΎΠΉ Π½Π°ΡΠ°Π΄ΠΊΠΎΠΉ.

Π¨Π°Π³ Π²ΡΠΎΡΠΎΠΉ. Π‘Π±ΠΎΡΠΊΠ° ΠΎΡΠ½ΠΎΠ²Ρ
Π‘ΠΎΠ±ΠΈΡΠ°Π΅ΠΌ ΠΎΡΠ½ΠΎΠ²Ρ, ΡΠΏΠ΅ΡΠ²Π° ΠΊ ΠΏΠ»Π°ΡΡΠΈΠ½Π΅ ΠΏΡΠΈΠ²Π°ΡΠΈΠ²Π°Π΅ΠΌ ΡΠ΄Π²ΠΎΠ΅Π½Π½ΡΠ΅ Π³Π°ΠΉΠΊΠΈ, ΠΊΠ°ΠΊ Π°Π²ΡΠΎΡ, ΡΡΠ΄Π° Π±ΡΠ΄Π΅Ρ Π·Π°Π²ΠΎΡΠ°ΡΠΈΠ²Π°ΡΡΡΡ ΡΠ΅Π·ΡΠ±ΠΎΠ²ΠΎΠΉ ΡΡΠ΅ΡΠΆΠ΅Π½Ρ. ΠΠ°Π΅ΠΊ Π½Π΅ Π»ΠΈΡΠ½ΠΈΠΌ Π±ΡΠ΄Π΅Ρ ΡΠ΄Π΅Π»Π°ΡΡ 3, Π° ΡΠΎ ΠΈ 4 ΡΡΡΠΊΠΈ, ΡΠ²Π°ΡΠΈΡΡ Π²ΡΠ΅ Π½ΡΠΆΠ½ΠΎ Π½Π°Π΄Π΅ΠΆΠ½ΠΎ, ΡΠ°ΠΊ ΠΊΠ°ΠΊ ΡΡΠΎΡ ΡΠ·Π΅Π» ΠΎΡΠ΅Π½Ρ ΠΎΡΠ²Π΅ΡΡΡΠ²Π΅Π½Π½ΡΠΉ ΠΈ ΡΡΠ΄Π° ΠΏΡΠΈΡ ΠΎΠ΄ΡΡΡΡ Π±ΠΎΠ»ΡΡΠΈΠ΅ Π½Π°Π³ΡΡΠ·ΠΊΠΈ. Π ΡΠ΅Π»ΠΎΠΌ Π²Π°ΡΠΈΡΡ Π³Π°ΠΉΠΊΠΈ Π½Π΅ ΠΆΠ΅Π»Π°ΡΠ΅Π»ΡΠ½ΠΎ, ΡΠ°ΠΊ ΠΊΠ°ΠΊ ΠΌΠ΅ΡΠ°Π»Π» ΡΡΠ°Π½ΠΎΠ²ΠΈΡΡΡ ΠΌΡΠ³ΡΠ΅.
ΠΠ°ΡΠ΅ΠΌ ΡΡΡΠ°Π½Π°Π²Π»ΠΈΠ²Π°Π΅ΠΌ Π½Π° ΠΎΡΠ½ΠΎΠ²Ρ ΡΠ²Π΅Π»Π»Π΅Ρ ΠΈ ΠΏΠΎ Π±ΠΎΠΊΠ°ΠΌ ΠΏΡΠΈΠ²Π°ΡΠΈΠ²Π°Π΅ΠΌ Π½Π°ΠΏΡΠ°Π²Π»ΡΡΡΠΈΠ΅, Π² Π½Π°ΡΠ΅ΠΌ ΡΠ»ΡΡΠ°Π΅ ΡΡΠΎ ΡΠ³ΠΎΠ»ΠΊΠΈ. Π¨Π²Π΅Π»Π»Π΅Ρ Π΄ΠΎΠ»ΠΆΠ΅Π½ Π»Π΅Π³ΠΊΠΎ Π΄Π²ΠΈΠ³Π°ΡΡΡΡ ΠΌΠ΅ΠΆΠ΄Ρ Π½Π°ΠΏΡΠ°Π²Π»ΡΡΡΠΈΠΌΠΈ, Π½ΠΎ ΠΈ Π»ΡΡΡΠΎΠ² Π±ΠΎΠ»ΡΡΠΈΡ Π±ΡΡΡ Π½Π΅ Π΄ΠΎΠ»ΠΆΠ½ΠΎ. Π‘Π²Π΅ΡΡ Ρ Π½Π°Π΄ ΡΠ²Π΅Π»Π»Π΅ΡΠΎΠΌ ΠΏΡΠΈΠ²Π°ΡΠΈΠ²Π°Π΅ΠΌ ΠΏΠ»Π°ΡΡΠΈΠ½Ρ ΠΌΠ΅ΠΆΠ΄Ρ ΡΠ³ΠΎΠ»ΠΊΠ°ΠΌΠΈ, ΠΏΠΎΠ»ΡΡΠ°Π΅ΡΡΡ ΡΠ²ΠΎΠ΅Π³ΠΎ ΡΠΎΠ΄Π° ΡΡΡΠ±Π°, Π² ΠΊΠΎΡΠΎΡΠΎΠΉ Π΄Π²ΠΈΠΆΠ΅ΡΡΡ ΡΠ²Π΅Π»Π»Π΅Ρ.
Π¨Π°Π³ ΡΡΠ΅ΡΠΈΠΉ. ΠΡΠ±Ρ
ΠΠ΅ΠΏΠΎΠ΄Π²ΠΈΠΆΠ½ΡΡ Π³ΡΠ±Ρ ΠΏΡΠΈΠ²Π°ΡΠΈΠ²Π°Π΅ΠΌ ΠΊ ΠΎΡΠ½ΠΎΠ²Π΅, Π² ΠΊΠ°ΡΠ΅ΡΡΠ²Π΅ ΠΌΠ°ΡΠ΅ΡΠΈΠ°Π»Π° Π°Π²ΡΠΎΡ ΠΈΡΠΏΠΎΠ»ΡΠ·ΡΠ΅Ρ ΠΊΡΡΠΎΠΊ ΡΠ³ΠΎΠ»ΠΊΠ°. ΠΡ Π° ΠΏΠΎΠ΄Π²ΠΈΠΆΠ½ΡΡ Π³ΡΠ±Ρ ΠΏΡΠΈΠ²Π°ΡΠΈΠ²Π°Π΅ΠΌ ΠΊ ΠΊΠΎΠ½ΡΡ ΡΠ²Π΅Π»Π»Π΅ΡΠ°. Π’ΠΎΡΠ΅Ρ ΡΠ²Π΅Π»Π»Π΅ΡΠ° Π·Π°Π²Π°ΡΠΈΠ²Π°Π΅ΠΌ ΠΏΠ»Π°ΡΡΠΈΠ½ΠΎΠΉ ΠΈΠ· ΡΠΎΠ»ΡΡΠΎΠ³ΠΎ ΠΆΠ΅Π»Π΅Π·Π°, Π² Π½Π΅ΠΉ Π΄ΠΎΠ»ΠΆΠ½ΠΎ ΠΈΠΌΠ΅ΡΡΡΡ ΠΎΡΠ²Π΅ΡΡΡΠΈΡ Π΄Π»Ρ ΡΠ΅Π·ΡΠ±ΠΎΠ²ΠΎΠ³ΠΎ Π²Π°Π»Π°. ΠΡΠ° ΠΏΠ»Π°ΡΡΠΈΠ½Π° Π±ΡΠ΄Π΅Ρ ΡΠ»ΡΠΆΠΈΡΡ ΡΠΏΠΎΡΠΎΠΌ Π΄Π»Ρ ΡΠ΅Π·ΡΠ±ΠΎΠ²ΠΎΠ³ΠΎ Π²Π°Π»Π°.
ΠΠ°Π»Π΅Π΅ Π³ΡΠ±Ρ Π½ΡΠΆΠ½ΠΎ ΡΠΊΡΠ΅ΠΏΠΈΡΡ, Π²ΡΡΠ΅Π·Π°Π΅ΠΌ ΠΈΠ· ΡΠΎΠ»ΡΡΠΎΠ³ΠΎ Π»ΠΈΡΡΠΎΠ²ΠΎΠ³ΠΎ ΠΆΠ΅Π»Π΅Π·Π° ΡΡΠ΅ΡΠ³ΠΎΠ»ΡΠ½ΠΈΠΊΠΈ ΠΈ ΠΏΡΠΈΠ²Π°ΡΠΈΠ²Π°Π΅ΠΌ Π½Π° ΡΠ²ΠΎΠΈ ΠΌΠ΅ΡΡΠ°. Π‘Π²Π°ΡΠ½ΡΠ΅ ΡΠ²Ρ ΠΏΠΎ ΠΌΠ΅ΡΠ΅ Π²ΠΎΠ·ΠΌΠΎΠΆΠ½ΠΎΡΡΠΈ Π·Π°ΡΠΈΡΠ°Π΅ΠΌ, ΡΡΠΎΠ±Ρ Π²ΡΠ΅ Π²ΡΠ³Π»ΡΠ΄Π΅Π»ΠΎ Π°ΠΊΠΊΡΡΠ°ΡΠ½ΠΎ.
Π¨Π°Π³ ΡΠ΅ΡΠ²Π΅ΡΡΡΠΉ. Π Π°Π±ΠΎΡΠΈΠΉ Π²Π°Π»
ΠΠ΅Π»Π°Π΅ΠΌ ΡΠ°Π±ΠΎΡΠΈΠΉ Π²Π°Π», Π² Π½Π°ΡΠ΅ΠΌ ΡΠ»ΡΡΠ°Π΅ ΡΡΠΎ ΡΠ΅Π·ΡΠ±ΠΎΠ²ΠΎΠΉ ΡΡΠ΅ΡΠΆΠ΅Π½Ρ. ΠΠ°ΠΊΡΡΡΠΈΠ²Π°Π΅ΠΌ Π½Π° Π²Π°Π» Π΄Π²Π΅ Π³Π°ΠΉΠΊΠΈ ΠΈ ΡΠ²Π°ΡΠΈΠ²Π°Π΅ΠΌ ΠΈΡ ΠΌΠ΅ΠΆΠ΄Ρ ΡΠΎΠ±ΠΎΠΉ, Π° ΡΠ°ΠΊΠΆΠ΅ ΠΏΡΠΈΠ²Π°ΡΠΈΠ²Π°Π΅ΠΌ ΠΊ Π²Π°Π»Ρ. ΠΠ°ΡΠ΅ΠΌ ΡΡΠ° Π΄Π΅ΡΠ°Π»Ρ ΡΠ»ΠΈΡΡΠ΅ΡΡΡ Π±ΠΎΠ»Π³Π°ΡΠΊΠΎΠΉ, ΡΡΠΎ Π±ΡΠ΄Π΅Ρ ΡΠΏΠΎΡ Π²Π°Π»Π°. Π ΠΊΠΎΠ½ΡΡ Π²Π°Π»Π° ΠΏΠ΅ΡΠΏΠ΅Π½Π΄ΠΈΠΊΡΠ»ΡΡΠ½ΠΎ ΠΏΡΠΈΠ²Π°ΡΠΈΠ²Π°Π΅ΡΡΡ Π³Π°ΠΉΠΊΠ°, ΡΡΠΎ Π±ΡΠ΄Π΅Ρ ΡΡ ΠΎ Π΄Π»Ρ ΡΡΡΠΊΠΈ. Π ΠΊΠ°ΡΠ΅ΡΡΠ²Π΅ ΡΡΡΠΊΠΈ ΠΈΡΠΏΠΎΠ»ΡΠ·ΡΠ΅ΠΌ ΡΡΠ°Π»ΡΠ½ΠΎΠΉ ΡΡΠ΅ΡΠΆΠ΅Π½Ρ, ΡΠ°ΠΊ ΠΊΠ°ΠΊ ΠΆΠ΅Π»Π΅Π·Π½ΡΠΉ Π±ΡΠ΄Π΅Ρ Π³Π½ΡΡΡΡΡ.
Π’Π°ΠΊΠΆΠ΅ Π½Π° Π²Π°Π»Ρ Π΄ΠΎΠ»ΠΆΠ΅Π½ Π±ΡΡΡ Π²Π½ΡΡΡΠ΅Π½Π½ΠΈΠΉ ΡΠΏΠΎΡ, ΠΊΠΎΡΠΎΡΡΠΉ Π±ΡΠ΄Π΅Ρ ΠΎΡΠ²Π΅ΡΠ°ΡΡ Π·Π° ΡΠ°Π·Π΄Π²ΠΈΠ³Π°Π½ΠΈΠ΅ Π³ΡΠ±, Π½Π°ΠΊΡΡΡΠΈΠ²Π°Π΅ΠΌ Π³Π°ΠΉΠΊΡ Π½Π° Π²Π°Π» ΠΈ ΠΏΡΠΈΠ²Π°ΡΠΈΠ²Π°Π΅ΠΌ Π΅Π΅. ΠΠΎΡ ΠΈ Π²ΡΠ΅, Π²Π°Π» Π³ΠΎΡΠΎΠ², ΠΎΡΡΠ°Π»ΠΎΡΡ Π΅Π³ΠΎ ΡΠΌΠ°Π·Π°ΡΡ Π΄Π»Ρ ΠΏΡΠΎΠ΄ΠΎΠ»ΠΆΠΈΡΠ΅Π»ΡΠ½ΠΎΠ³ΠΎ ΡΡΠΎΠΊΠ° ΡΠ»ΡΠΆΠ±Ρ ΠΈ ΡΠΈΡΠΊΠΈ ΠΌΠΎΠΆΠ½ΠΎ ΡΠΎΠ±ΡΠ°ΡΡ. ΠΠ½ΠΈ ΡΠΆΠ΅ ΡΠ°Π±ΠΎΡΠ°ΡΡ, Π½ΠΎ ΡΡΠ΅Π±ΡΡΡ Π΄ΠΎΡΠ°Π±ΠΎΡΠΊΠΈ.
Π¨Π°Π³ ΠΏΡΡΡΠΉ. ΠΠ°ΠΊΠ»Π°Π΄ΠΊΠΈ Π½Π° Π³ΡΠ±Ρ
ΠΠ΅Π»Π°Π΅ΠΌ Π½Π°ΠΊΠ»Π°Π΄ΠΊΠΈ, Π±Π»Π°Π³ΠΎΠ΄Π°ΡΡ ΠΊΠΎΡΠΎΡΡΠΌ ΠΏΡΠ΅Π΄ΠΌΠ΅ΡΡ Π±ΡΠ΄ΡΡ Π½Π°Π΄Π΅ΠΆΠ½ΠΎ ΡΠ΄Π΅ΡΠΆΠΈΠ²Π°ΡΡΡΡ Π² ΡΠΈΡΠΊΠ°Ρ . ΠΠ»Ρ Π½Π°ΠΊΠ»Π°Π΄ΠΎΠΊ ΡΠ΅ΠΊΠΎΠΌΠ΅Π½Π΄ΡΠ΅ΡΡΡ Π½Π°ΠΉΡΠΈ ΡΠ³Π»Π΅ΡΠΎΠ΄ΠΈΡΡΡΡ ΡΡΠ°Π»Ρ, ΡΠ°ΠΊ ΠΊΠ°ΠΊ ΠΎΠ±ΡΡΠ½ΠΎΠ΅ ΠΆΠ΅Π»Π΅Π·ΠΎ ΠΌΡΠ³ΠΊΠΎΠ΅ ΠΈ ΡΡΠ°Π»ΡΠ½ΡΠ΅ Π΄Π΅ΡΠ°Π»ΠΈ Π±ΡΠ΄ΡΡ ΠΏΠ»ΠΎΡ ΠΎ Π΄Π΅ΡΠΆΠ°ΡΡΡΡ Π² ΡΠΈΡΠΊΠ°Ρ . ΠΡΡΠ΅Π·Π°Π΅ΠΌ Π΄Π²Π΅ Π΄Π΅ΡΠ°Π»ΠΈ ΠΈ Π΄Π΅Π»Π°Π΅ΠΌ Π½Π° Π½ΠΈΡ Π½Π°ΡΠ΅ΡΠΊΠΈ ΠΊΡΠ΅ΡΡ-Π½Π°ΠΊΡΠ΅ΡΡ. Π ΠΈΡΠΎΠ³Π΅ ΠΏΠΎΠ»ΡΡΠ°Π΅ΠΌ ΠΎΡΠ»ΠΈΡΠ½ΡΠ΅ Π½Π°ΠΊΠ»Π°Π΄ΠΊΠΈ, ΡΠ²Π΅ΡΠ»ΠΈΠΌ ΠΎΡΠ²Π΅ΡΡΡΠΈΡ ΠΈ ΠΏΡΠΈΠΊΡΡΡΠΈΠ²Π°Π΅ΠΌ ΠΈΡ Π²ΠΈΠ½ΡΠΈΠΊΠ°ΠΌΠΈ ΠΊ Π³ΡΠ±Π°ΠΌ. ΠΠ»Ρ ΠΏΡΠΎΡΡΠΎΡΡ Π°Π²ΡΠΎΡ ΠΏΡΠΈΠ²Π°ΡΠΈΠ» ΠΊ Π³ΡΠ±Π°ΠΌ Π³Π°ΠΉΠΊΠΈ.
Π¨Π°Π³ ΡΠ΅ΡΡΠΎΠΉ. ΠΠ±ΡΠΈΠ²ΠΊΠ° Π΄Π»Ρ Π³ΡΠ± ΠΈ Π½Π°ΠΊΠΎΠ²Π°Π»ΡΠ½Ρ
ΠΡΠ±Ρ Π°Π²ΡΠΎΡ ΡΠ΅ΡΠΈΠ» Π΄ΠΎΠΏΠΎΠ»Π½ΠΈΡΠ΅Π»ΡΠ½ΠΎ ΠΎΠ±ΡΠΈΡΡ Π»ΠΈΡΡΠΎΠ²ΡΠΌ ΠΆΠ΅Π»Π΅Π·ΠΎΠΌ, Π±Π»Π°Π³ΠΎΠ΄Π°ΡΡ ΡΠ΅ΠΌΡ Π²ΡΠ΅ ΠΊΡΠ°ΡΠΈΠ²ΠΎ ΡΠΌΠΎΡΡΠΈΡΡΡ, Π° Π³ΡΠ±Ρ Π΄ΠΎΠΏΠΎΠ»Π½ΠΈΡΠ΅Π»ΡΠ½ΠΎ ΡΠΊΡΠ΅ΠΏΠ»Π΅Π½Ρ. ΠΠΎΡΠ»Π΅ Π·Π°ΡΠΈΡΡΠΊΠΈ ΡΠ²Π°ΡΠ½ΡΡ ΡΠ²ΠΎΠ² Π²ΡΠ΅ Π²ΡΠ³Π»ΡΠ΄ΠΈΡ ΠΊΠ°ΠΊ ΡΠ΅Π»ΡΠ½ΠΎΠ΅ ΠΈΠ·Π΄Π΅Π»ΠΈΠ΅.
ΠΠ΅Π»Π°Π΅ΠΌ Π΄Π»Ρ ΡΠΈΡΠΊΠΎΠ² ΠΈ Π½Π°ΠΊΠΎΠ²Π°Π»ΡΠ½Ρ, ΠΊΠΎΡΠΎΡΠ°Ρ ΠΏΠΎΠ·Π²ΠΎΠ»ΠΈΡ Π²ΡΡΠ°Π²Π½ΠΈΠ²Π°ΡΡ Π΄Π΅ΡΠ°Π»ΠΈ ΠΈ ΡΠ°ΠΊ Π΄Π°Π»Π΅Π΅. Π‘Π²Π°ΡΠΈΠ²Π°Π΅ΠΌ Π΅Π΅ ΠΈΠ· ΡΠΎΠ»ΡΡΠΎΠ³ΠΎ Π»ΠΈΡΡΠΎΠ²ΠΎΠ³ΠΎ ΠΆΠ΅Π»Π΅Π·Π°. Π Π·Π°Π²Π΅ΡΡΠ΅Π½ΠΈΠΈ ΡΠΈΡΠΊΠΈ Ρ
ΠΎΡΠΎΡΠΎ Π·Π°ΡΠΈΡΠ°Π΅ΠΌ Π΄ΠΎ Π±Π»Π΅ΡΠΊΠ°, ΡΠ±ΠΈΡΠ°Π΅ΠΌ Π½Π΅ΡΠΎΠ²Π½ΠΎΡΡΠΈ.
Π¨Π°Π³ ΡΠ΅Π΄ΡΠΌΠΎΠΉ. ΠΠ°Π²Π΅ΡΡΠ΅Π½ΠΈΠ΅
Π Π·Π°Π²Π΅ΡΡΠ΅Π½ΠΈΠΈ ΠΊΡΠ°ΡΠΈΠΌ ΡΠΈΡΠΊΠΈ ΠΊΡΠ°ΡΠΊΠΎΠΉ ΠΏΠΎ ΠΌΠ΅ΡΠ°Π»Π»Ρ, ΡΠ΅ΠΏΠ΅ΡΡ ΠΆΠ΅Π»Π΅Π·ΠΎ Π½Π΅ Π±ΡΠ΄Π΅Ρ ΡΠΆΠ°Π²Π΅ΡΡ, Π° ΡΠΈΡΠΊΠΈ Π±ΡΠ΄ΡΡ ΠΎΡΠ»ΠΈΡΠ½ΠΎ Π²ΡΠ³Π»ΡΠ΄Π΅ΡΡ. Π Π°Π±ΠΎΡΠΈΠΉ Π²Π°Π» ΠΎΠ±ΡΠ·Π°ΡΠ΅Π»ΡΠ½ΠΎ ΡΠΌΠ°Π·ΡΠ²Π°Π΅ΠΌ, ΡΠ΅ΠΏΠ΅ΡΡ ΡΠΈΡΠΊΠΈ ΡΠ°Π±ΠΎΡΠ°ΡΡ Π»Π΅Π³ΠΊΠΎ, Π° ΡΠ΅Π·ΡΠ±Π° ΠΈΠ·Π½Π°ΡΠΈΠ²Π°Π΅ΡΡΡ Π½Π΅ ΡΠ°ΠΊ Π±ΡΡΡΡΠΎ.
Π’ΠΈΡΠΊΠΈ Π³ΠΎΡΠΎΠ²Ρ, Π² ΠΊΠ°ΡΠ΅ΡΡΠ²Π΅ ΡΠΊΡΠΏΠ΅ΡΠΈΠΌΠ΅Π½ΡΠ° Π°Π²ΡΠΎΡ ΡΠΆΠΈΠΌΠ°Π΅Ρ ΠΊΡΡΠΎΠΊ ΠΏΡΠΎΡΠΈΠ»ΡΠ½ΠΎΠΉ ΡΡΡΠ±Ρ. ΠΠ°ΠΊΡΠΈΠΌΠ°Π»ΡΠ½ΠΎ Π³ΡΠ±Ρ ΡΠΈΡΠΊΠΎΠ² ΡΠ°Π·Π΄Π²ΠΈΠ³Π°ΡΡΡΡ Π΄ΠΎ 30 ΡΠΌ. Π½Π°ΠΊΠΎΠ²Π°Π»ΡΠ½Ρ ΡΠ°ΠΊΠΆΠ΅ ΡΠ°Π±ΠΎΡΠ°Π΅Ρ ΠΎΡΠ»ΠΈΡΠ½ΠΎ. ΠΠ° ΡΡΠΎΠΌ ΠΏΡΠΎΠ΅ΠΊΡ ΠΎΠΊΠΎΠ½ΡΠ΅Π½, Π½Π°Π΄Π΅ΡΡΡ, Π²Π°ΠΌ ΡΠ°ΠΌΠΎΠ΄Π΅Π»ΠΊΠ° ΠΏΠΎΠ½ΡΠ°Π²ΠΈΠ»Π°ΡΡ. Π£Π΄Π°ΡΠΈ ΠΈ ΡΠ²ΠΎΡΡΠ΅ΡΠΊΠΈΡ
Π²Π΄ΠΎΡ
Π½ΠΎΠ²Π΅Π½ΠΈΠΉ, Π΅ΡΠ»ΠΈ ΡΠ΅ΡΠΈΡΠ΅ ΠΏΠΎΠ²ΡΠΎΡΠΈΡΡ ΠΏΠΎΠ΄ΠΎΠ±Π½ΠΎΠ΅. ΠΠ΅ Π·Π°Π±ΡΠ²Π°ΠΉΡΠ΅ Π΄Π΅Π»ΠΈΡΡΡΡ Ρ Π½Π°ΠΌΠΈ ΡΠ²ΠΎΠΈΠΌΠΈ ΠΈΠ΄Π΅ΡΠΌΠΈ ΠΈ ΡΠ°ΠΌΠΎΠ΄Π΅Π»ΠΊΠ°ΠΌΠΈ!
ΠΡΡΠΎΡΠ½ΠΈΠΊ
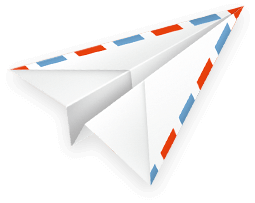
ΠΠΎΠ»ΡΡΠ°ΠΉΡΠ΅ Π½Π° ΠΏΠΎΡΡΡ ΠΏΠΎΠ΄Π±ΠΎΡΠΊΡ Π½ΠΎΠ²ΡΡ ΡΠ°ΠΌΠΎΠ΄Π΅Π»ΠΎΠΊ. ΠΠΈΠΊΠ°ΠΊΠΎΠ³ΠΎ ΡΠΏΠ°ΠΌΠ°, ΡΠΎΠ»ΡΠΊΠΎ ΠΏΠΎΠ»Π΅Π·Π½ΡΠ΅ ΠΈΠ΄Π΅ΠΈ!
*ΠΠ°ΠΏΠΎΠ»Π½ΡΡ ΡΠΎΡΠΌΡ Π²Ρ ΡΠΎΠ³Π»Π°ΡΠ°Π΅ΡΠ΅ΡΡ Π½Π° ΠΎΠ±ΡΠ°Π±ΠΎΡΠΊΡ ΠΏΠ΅ΡΡΠΎΠ½Π°Π»ΡΠ½ΡΡ Π΄Π°Π½Π½ΡΡ
Π‘ΡΠ°Π½ΠΎΠ²ΠΈΡΠ΅ΡΡ Π°Π²ΡΠΎΡΠΎΠΌ ΡΠ°ΠΉΡΠ°, ΠΏΡΠ±Π»ΠΈΠΊΡΠΉΡΠ΅ ΡΠΎΠ±ΡΡΠ²Π΅Π½Π½ΡΠ΅ ΡΡΠ°ΡΡΠΈ, ΠΎΠΏΠΈΡΠ°Π½ΠΈΡ ΡΠ°ΠΌΠΎΠ΄Π΅Π»ΠΎΠΊ Ρ ΠΎΠΏΠ»Π°ΡΠΎΠΉ Π·Π° ΡΠ΅ΠΊΡΡ. ΠΠΎΠ΄ΡΠΎΠ±Π½Π΅Π΅ Π·Π΄Π΅ΡΡ.